Services on Demand
Journal
Article
Indicators
-
Cited by SciELO
-
Access statistics
Related links
-
Cited by Google
-
Similars in SciELO
-
Similars in Google
Share
Revista Facultad de Ingeniería Universidad de Antioquia
Print version ISSN 0120-6230On-line version ISSN 2422-2844
Rev.fac.ing.univ. Antioquia vol.38 no.1 Medellín Jan./Jun. 2006
Estudio comparativo de dos tecnologías de mecanizado rápido; Coproinmold y sinterizado selectivo por láser
Milton Coba Salcedo a , Esther Serres Moliner b
a Universidad Politécnica de Cataluña. Escuela Técnica Superior de Ingenieros Industriales de Barcelona, ETSEIB-UPC. Avenida Diagonal 647. CP. 08028. Departamento de Ingeniería Mecánica. Laboratorio de Tecnología de Fabricación.
b ASCAMM PLUS, Servicios Tecnológicos S. L., Applus + Materiales y Procesos Industriales. Campus Universidad Autónoma de Barcelona. A. C. 18. C. P. 08193. Barcelona, España
(Recibido el 1.º de marzo de 2005. Aceptado el 15 de mayo de 2006)
Resumen
Las tecnologías de mecanizado rápido, adoptan las técnicas de prototipado rápido y las aplican en la fabricación de utillajes, especialmente moldes para la industria de inyección de plásticos. Las investigaciones sobre las técnicas de mecanizado rápido, muestran cómo estas han ido ganando mayor importancia, y ya se posiciona como una seria alternativa a los métodos de mecanizado convencional. En este artículo, se comparan dos importantes técnicas de mecanizado rápido tomando como base datos experimentales del acabado superficial, calidad dimensional, ciclo de vida, costos y tiempo de desarrollo de los utillajes.
---------- Palabras clave: mecanizado rápido, mecanizado indirecto, mecanizado directo, Coproinmold, sinterizado selectivo por láser (SLS).
A comparative study of two rapid tooling technologies; Coproinmold – Selective Laser Sintering
Abstract
Rapid tooling (RT) is the technology that implements rapid prototyping (RP) techniques in the fabrication of tools and molds, especially for injection of plastics.
Recently, RT has gained importance to the point that it is already considered to be a viable alternative to the methods of conventional machining. Two important techniques of RT are compared in this paper. This comparison is based on experimental data on the surface texture, dimensional quality, life cycle, costs and time of development of the tooling.
---------- Key words: Rapid tooling (RT), Indirect tooling, Direct tooling, Coproinmold, selective laser sintering (SLS).
Introducción
La tecnología de prototipado rápido ha mejorado con el paso de los últimos 10 años; una de las principales ventajas del prototipado rápido en la manufactura, es poder verificar un diseño en sólo cuestión de horas después de completar sus detalles en CAD [1]. Esto ha incidido en la disminución del tiempo de desarrollo de los productos.
Sin embargo, una de las principales limitaciones del prototipado rápido es que a pesar de lo rápido de la manufactura, a menudo no se puede obtener el prototipo en el material requerido para el producto final. Además, el proceso de construcción del prototipo, hace que las propiedades mecánicas de este sean, de alguna manera, diferentes que las del producto manufacturado por el proceso de producción final [2]. La tecnología de mecanizado rápido, esencialmente, adopta las técnicas de prototipado rápido y las aplica en la fabricación de utillajes y matrices. Se originó de la necesidad de mejorar los modelos de prototipado rápido en términos de su rendimiento. El mecanizado rápido se hace cada día más popular en la fabricación no sólo como una alternativa al prototipado rápido, sino especialmente en la producción de series cortas en las que no se justifica una inversión en máquinas de mecanizado convencional [3]. Los métodos de construcción de utillajes para la producción en serie de un determinado número de partes, han sido divididos por la mayoría de los investigadores en dos grupos [4-5], mecanizado indirecto (indirect tooling) y mecanizado directo (direct tooling) (figura 1).
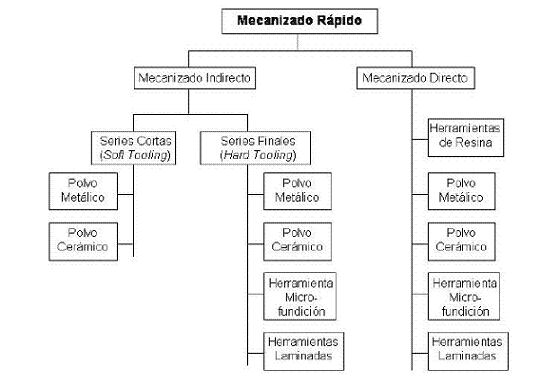
Figura 1 Clasificación de los métodos de rapid tooling [5]
El mecanizado indirecto es una técnica alternativa a las formas tradicionales de hacer utillajes. Estos métodos son poco costosos, con períodos cortos de desarrollo lo que permite la validación del utillaje y la introducción de cambios antes que se haga muy costoso. En el mecanizado indirecto, se crea un negativo usando alguna tecnología de prototipado rápido, este negativo se hace en materiales como silicona, resina epoxy o metal blando. De aquí se crea el inserto del utillaje prototipo por un método de mecanizado rápido. El objetivo de estos métodos es llenar el vacío entre el prototipado rápido y el mecanizado directo, buscando conseguir la producción de utillajes de series cortas. El amplio rango de técnicas de mecanizado indirecto hace difícil determinar cuál es el método más apropiado para un proyecto específico. Los métodos de mecanizado indirecto para la producción de insertos de utillajes necesitan como mínimo un proceso intermedio de prototipado rápido para la elaboración de una réplica; esto puede resultar en una pérdida de precisión, y puede incrementar el tiempo de construcción del molde [6].
Los métodos de mecanizado directo, permiten la producción de insertos capaces de sobrevivir a algunas decenas o docenas de miles de ciclos de producción. En estos procesos el utillaje se crea directamente por una técnica de mecanizado directo (figura 1). La durabilidad o expectativa de vida de los insertos producidos por este método varían significativamente dependiendo del material y el método empleado.
Bases del estudio
Como parte del proyecto “Estudio para la optimización y mejora de la tecnología Coproinmold” el cual se describió en el primero de estos dos artículos, se realizó el estudio comparativo de las tecnologías de mecanizado rápido: Coproinmold y sinterizado selectivo por láser (SLS). El estudio se centró en contrastar el acabado superficial, el acabado dimensional, el coste, tiempo de ejecución y el número de piezas inyectadas (durabilidad del molde).
Para la realización de dicho estudio, se fabricaron moldes con piezas tipo y se utilizaron moldes fabricados para diferentes empresas. De esta manera, se obtuvo información muy valiosa de moldes para piezas con diferentes grados de complejidad que actualmente demanda el mercado.
Experimentación
Se diseñaron, a partir del programa de modelizado CAD SolidWorks, dos geometrías que se utilizaron para el estudio, con el fin de diseñar:
Los insertos de estereolitografía que serían los negativos de las improntas metálicas generadas a través de la tecnología Coproinmold.
Los ficheros CAD.SLS para generar los insertos a partir de la tecnología de sinterizado selectivo por láser.
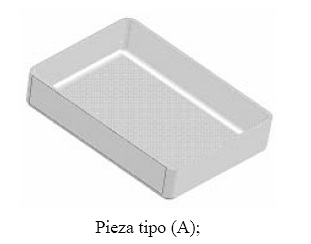
Figura 2 Detalle de la pieza tipo “tapa”
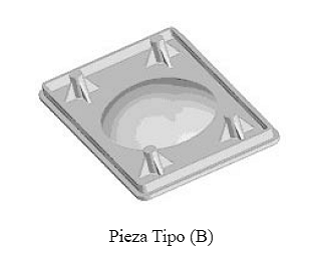
Figura 3 Detalle de la pieza tipo base
Se definieron una serie de cotas para evaluar la planitud exterior, planitud interior, error en el eje X y error en el eje Y.
Para hacer el estudio de la calidad superficial de las dos tecnologías, se tomaron las medidas de los valores de rugosidad, para los parámetros Ra (desviación media aritmética del perfil de rugosidad) y Rt (altura total del perfil de rugosidad) [7].
Además se incluyeron otras variables tecnológicas de comparación como; el tiempo de vida, el
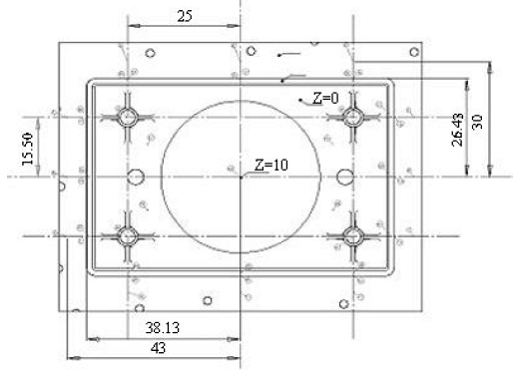
Figura 4 Cotas definidas para la pieza base
tiempo de desarrollo y el costo de desarrollo, en particular por el interés que pueden tener para sus aplicaciones industriales [6].
Antes de proceder al estudio comparativo de las dos tecnologías, en el siguiente apartado se describe de manera muy breve el proceso de obtención del inserto metálico mediante las dos tecnologías.
Descripción de las tecnologías
La tecnología Coproinmold está clasificada como una tecnología de mecanizado rápido del tipo mecanizado indirecto, pues se crea un negativo del modelo a generar por métodos de prototipado rápido, mientras la tecnología de sinterizado selectivo por láser es una tecnología de mecanizado rápido del tipo mecanizado directo ya que las piezas son generadas directamente de un fichero CAD.
Tecnología Coproinmold
La tecnología Coproinmold consiste básicamente en el proceso de deposición electrolítica de capas metálicas, sobre un prototipo de estereolitografía que hace las veces de negativo del molde a generar [8].
El proceso se realiza en dos fases; primero se sumerge el prototipo ya preparado en un baño de níquel sulfatado durante los días especificados para que se produzca la electrodeposición de la capa metálica de níquel (figura 5).
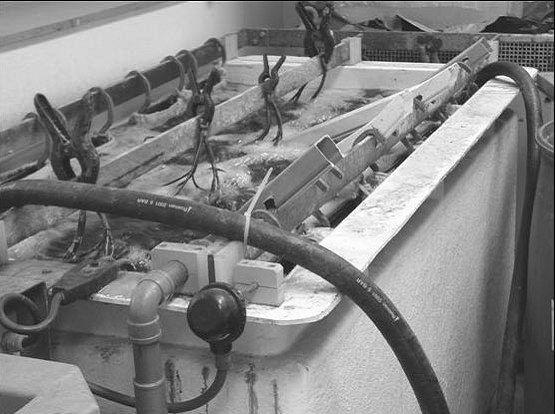
Figura 5 Baño de níquel sulfatado
Una vez cumplido este tiempo se pasa a un baño de cobre ácido durante unos días para que se produzca la electrodeposición de la capa de cobre, de esta forma se obtiene la capa de impronta metálica (figura 6).
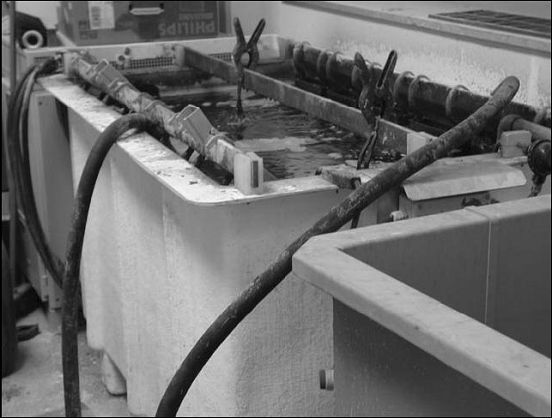
Figura 6 Baño de cobre ácido
Una vez pasado el tiempo determinado para que se produzca la metalización de la capa, se procede a la extracción de las plataformas con los prototipos. Se retira todo el material polimérico, producto del inserto de estereolitografía y se procede a rellenar el inserto metálico con viruta de aluminio y un polímero que al solidificarse proporciona consistencia mecánica y conductividad térmica al inserto final (figura 7).
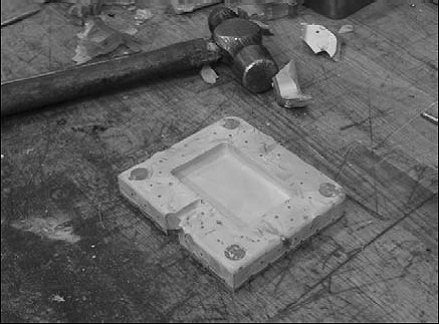
Figura 7 Inserto final
Tecnología de sinterizado selectivo por láser (SLS)
Mediante esta tecnología se pueden obtener los insertos del molde de manera directa por adición de materiales.
Se deposita una capa de polvo, de unas décimas de milímetro, en una cuba que se ha calentado a una temperatura ligeramente inferior al punto de fusión del polvo; seguidamente un láser CO2 sinteriza el polvo en los puntos seleccionados, a partir de un fichero. SLS va creando capa a capa los objetos tridimensionales, mediante la fusión selectiva de las partículas de polvo, utilizando el calor generado por el láser.
Estas se van fundiendo, uniéndose a la capa anterior por lo que encajan perfectamente al diseño realizado en CAD. A medida que se funden las capas, las piezas van cogiendo forma en el interior de la máquina (figura 8). Una vez terminado el proceso, sólo falta limpiar la pieza y ya está preparada para su posterior tratamiento.
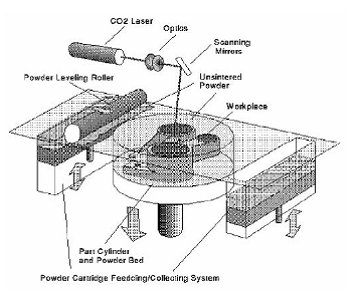
Figura 8 Esquema del funcionamiento de la máquina SLS
La pieza obtenida se introduce en un horno de sinterización controlado por PLC que ejecuta un ciclo de temperaturas hasta alcanzar en la última etapa de la curva del programa una temperatura aproximada de 1.100 °C. En este estado de la rampa de temperatura se produce el infiltrado del bronce en el poro creado en el quemado del aglutinante (burn out), y al mismo tiempo se produce la sinterización del acero.
Con el inserto obtenido se realizan las tareas de posprocesado: mecanizado final, pulido, etc. y se obtiene un molde de características similares a los moldes de acero o aluminio utilizados en la industria de los plásticos (figura 9).
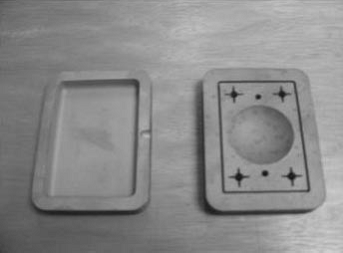
Figura 9 Insertos SLS-pieza tapa y pieza base
La tecnología SLS permite el uso de materiales termofusibles y, por tanto, la creación de prototipos en materiales plásticos, elastómeros y metales. Es esta última opción la que hace posible la creación de figuras metálicas para moldes de inyección [9].
Estudio comparativo entre los insertos metálicos obtenidos con la tecnología Coproinmold y los obtenidos con sinterizado selectivo por láser
En la tabla 1 podemos observar el coste medio y el tiempo medio necesario para fabricar un molde prototipo. Los moldes se fabricaron a partir de elementos modulares estándar y la obtención de los insertos metálicos (cavidad y punzón) se realizó mediante las tecnologías Coproinmold y SLS.
El cálculo del coste y el tiempo de fabricación se han hecho a partir de una estimación media entre diferentes moldes prototipo con varios grados de complejidad, fabricados con las dos tecnologías (tabla 1).
Tabla 1 Estudio comparativo del coste de las dos tecnologías
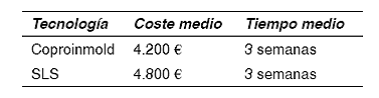
En segundo lugar se centró el estudio en la calidad del inserto obtenido y en consecuencia en la calidad de la pieza final de plástico. Al igual se hizo para calcular las respuestas en el diseño de experimentos, se verificó el acabado dimensional (tablas 2 y 3) y el acabado superficial de diferentes insertos (tablas 4 y 5).
Tabla. 2 Análisis dimensional del error promedio para el grado de complejidad A
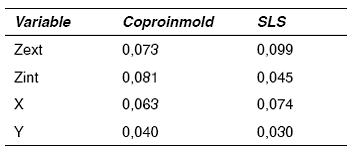
Tabla 3 Análisis dimensional del error promedio para el grado de complejidad B
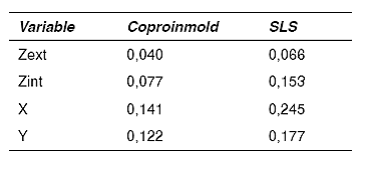
El acabado dimensional se calculó a partir de unas cotas definidas en puntos estratégicos del inserto (nivelado del partaje y de zonas interiores del inserto, cotas X y Y de las paredes exteriores de la figura, etc.). A partir de estas cotas tipo para diferentes moldes, tanto de SLS como de Coproinmold, se efectuó una media ponderada de todas ellas. Estos valores comunes para todos los insertos, permitieron realizar el estudio comparativo entre las dos tecnologías a partir del cálculo de los errores para cada cota (error = cota nominal - cota real). En la tabla 2 y tabla 3 se muestra todos estos valores del análisis comparativo separado en dos grados de complejidad para cada una de las tecnologías (Coproinmold vs. SLS).
Los errores obtenidos para las piezas de complejidad A no son significativos ya que ningún aumento supera 0,1 mm. En cambio para las piezas de complejidad B, estos errores son más significativos. En este caso, los errores obtenidos con la tecnología Coproinmold son menores respecto a los obtenidos con la tecnología SLS.
Para realizar los diferentes cálculos de la rugosidad se utilizó la máquina de medir rugosidades y perfiles. En cuanto se obtenían los diferentes insertos se procedía al cálculo de la rugosidad Ra y Rt previo a las operaciones de pulido. Al no incluir estas operaciones de pulido manuales antes del cálculo de la rugosidad, permitía garantizar la “no distorsión” de los resultados, ya que la persona encargada de realizar el pulido de los insertos no siempre era la misma, y en el caso que lo fuera, no lo efectuaría siempre de la misma manera. Por lo tanto, los resultados obtenidos no corresponden al acabado final de la pieza inyectada pero permiten realizar una comparación real entre las dos tecnologías y da una idea del tiempo que el pulidor tendrá que emplear en preparar los insertos para obtener un buen acabado superficial.
Por otro lado, debido a la diferencia de complejidad de forma de las piezas que se analizaron, se diferenciaron dos niveles de complejidad calculado a partir del factor de forma.
En las tablas 4 y 5 se muestran los valores medios de Ra y Rt de las dos tecnologías.
Tabla 4 Valores de rugosidad Ra
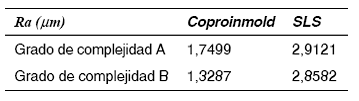
En este caso los resultados obtenidos también son mejores para los insertos obtenidos con la tecnología coproinmold.
Tabla 5 Valores de rugosidad Rt
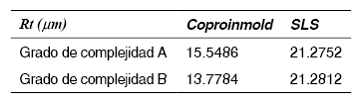
Por último se evaluó la durabilidad del molde teniendo en cuenta el número máximo aproximado de piezas de plástico inyectadas por cada molde prototipo (tabla 6). La durabilidad del molde variaba en cada caso dependiendo de los diferentes parámetros empleados en los procesos de fabricación del inserto, de los parámetros de inyección así como del tipo de material a inyectar. Aún dependiendo de todos estos valores, las diferencias entre las dos tecnologías fueron notables. En la tabla 6 se muestran estos datos orientativos que denota esta diferencia.
Tabla 6 Valores de durabilidad del molde
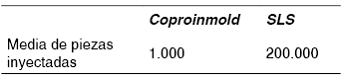
Los insertos fabricados con la tecnología Coproinmold, aproximadamente a partir de las 1.000 piezas inyectadas, presentaban desgastes en diferentes partes del molde.
En algunas partes de la figura de los insertos se pudieron observar desprendimientos de la capa superior de níquel. Este defecto era más notable en los moldes con paredes verticales que no habían sido perfectamente pulidas y denotaba problemas de adherencia entre las dos capas metálicas de níquel y cobre. Dependiendo de las condiciones de inyección y del tipo de material inyectado, en algunos casos, incluso se llegaron a deformar algunas partes del molde.
Los problemas de desgaste, de desprendimiento de capa y de deformación en los diferentes insertos les hacían perder su capacidad de repetitibilidad y de precisión y en consecuencia disminuía la durabilidad del molde prototipo fabricado con la tecnología Coproinmold.
En los insertos fabricados con la tecnología SLS los resultados fueron muy superiores a los obtenidos con la tecnología Coproinmold, se detectaban problemas de desgaste, deformación y falta de precisión a partir de las docientas mil piezas inyectadas aproximadamente.
Conclusiones
Se puede observar que la tecnología Coproinmold es superior en diferentes aspectos en relación con la de sinterizado: coste, acabado dimensional y superficial. Sin embargo, se evidenciaron desventajas como la durabilidad del molde y el hecho de no poder mecanizar los insertos una vez fabricados. En la evaluación de las características de cada una de estas técnicas rapid tooling, se han introducido variables tecnológicas que puedan servir para comparar desde distintos rangos cual puede tener una mejor aplicación, de acuerdo a cada necesidad, es evidente que las dos tecnologías son igualmente válidas, cada una para un determinado rango del mercado de moldes prototipo para la inyección de diferentes piezas de plástico.
Referencias
1. S. Ashley, “From CAD art to rapid metal tools”, Mechanical Engineering, N.º 3. 1997. pp. 82-87. [ Links ]
2. P. Hilton, “Making the leap to rapid tool making”, Mechanical Engineering, N.º 7. 1995. pp. 75-76. [ Links ]
3. A. P. Nyaluke, D. An, H. R. Leep, H. R. Parsaeci “Rapid prototyping: Applications in academia institutions and industry”. Computers Ind. Eng. Vol. 29. 1995.pp. 345-349. [ Links ]
4. D. T. Pham, S. S. Dimov. Rapid prototyping and rapid tooling the key enablers for rapid manufacturing. Proc. Inst. Mech. Engrs. Vol. 217. 2003. pp. 1-23. [ Links ]
5. X. Plantá, “Nuevas Técnicas de Fabricación Rápida de Moldes Prototipo”. Revista Plásticos Universales, N.º 58.1999. p.1. [ Links ]
6. K. Chua, K. H. Hong, S.L. Ho. Rapid tooling technology. Part 1. A comparative study”. The Int. J. of Advan. Manufact. Technol. Vol. 15. 1999. pp. 604-608. [ Links ]
7. ISO 4287, Especificación Geométrica de Productos (GPS), Calidad Superficial: Método del Perfil; términos, definiciones y parámetros del estado superficial. Génova-Suiza. ISO. 1997 [ Links ]
8. M. Coba, E. Serres, “Tecnologías de fabricación rápida: Optimización y mejora de la tecnología de mecanizado rápido – Coproinmold”. Revista Facultad de Ingeniería- Universidad de Antioquia. Vol. 36. 2006. pp. 7-20. [ Links ]
9. J. A. Rodríguez, Sistemas de Prototipado Rápido. Notas Master en Diseño y Desarrollo de Nuevos Productos. UPC. 2001. pp. 1-33. [ Links ]
* Autor de correspondencia. Teléfono: +34+93 405 40 14, fax: +34+93 567 20 01, correo electrónico: milton.fabian.coba@upc.edu (M. Coba Salcedo).