1. Introducción
La industria de manufactura se caracteriza por estar compuesta por una amplia gama de operaciones con gran consumo de energía y baja eficiencia, lo cual la hace tener un potencial considerable para el ahorro de energía y la mitigación de emisiones a través de evaluaciones acertadas sobre su eficiencia energética con el fin de mejorar su rendimiento 1. El sector manufacturero comprende algunos de los más grandes consumidores de energía y emisores de carbono en el mundo. Este sector representa aproximadamente el 33% del uso de energía primaria y 38% de las emisiones de CO2 a nivel mundial según cifras presentadas por la EIA (U.S Energy Information Administration) 1,2. Para el caso particular de los procesos de mecanizado (es decir, taladrado, torneado o fresado, etc.) se ha informado de una eficiencia máxima del 30% 2. En general, se espera que el sector industrial crezca durante las próximas décadas generando un incremento en la demanda de procesos de mecanizado, y también se magnificará el consumo de energía y emisión de carbono consecuentemente 3. La falta de estudios profundos en la identificación de las variables que logren relacionar la calidad del proceso de manufactura con su consumo energético hace que el impacto económico dentro del sector se vea altamente afectado. La medición y el monitoreo del consumo de energía son una medida eficaz para proporcionar datos para respaldar operaciones confiables en cualquier organización. En ingeniería mecánica, estos datos son útiles para: (a) establecer objetivos de desempeño ambiental, (b) reducir el consumo de energía en los procesos de fabricación mecánica, (c) utilizar medidas de eficiencia en los procesos de fabricación, (d) comprender cómo cumplir los requisitos del cliente por parte de los proveedores. Para controlar el uso de la energía en una planta de fabricación mecánica, el consumo de energía debe ser medido y cuantificado en los procesos reales de producción; partiendo del conocimiento de cómo influyen en este las variables que intervienen en el proceso, para así poder juzgar y evaluar dicho consumo específico con miras de lograr un ahorro de energía práctico 1.
Las investigaciones sobre el modelamiento, optimización, monitoreo, medición, ahorro y evaluación de la energía presentan vacíos debido a la complejidad y variedad de los procesos de fabricación mecánica que dificultan establecer un método de estudio sistémico, por lo que es necesario evaluar en dichos procesos como las variables del mecanizado influyen en el consumo de energía. Adicionalmente el concepto y la connotación del rendimiento energético de la fabricación mecánica no están claros, y su marco y los indicadores relacionados son imperfectos, no se tiene una metodología estandarizada que ayude a evaluar el rendimiento energético en la industria de fabricación mecánica y, además, como mejorarlo 4. En la industria de mecanizado el consumo de energía es responsable de una parte sustancial de la carga ambiental por lo que es imperativo evaluar los parámetros de mecanizado identificando su incidencia en el consumo de energía 5,6. La reducción del consumo de energía es una consideración esencial en la fabricación sostenible; y en la industria manufacturera se requiere una técnica de optimización basada en la selección de condiciones de corte sostenibles. Naturalmente, la medición y el seguimiento al consumo de energía es el primer paso hacia el análisis y ahorro energético, y así promover el mecanizado eficiente 2.
En el pasado, las operaciones de corte de metales se han optimizado principalmente en función de consideraciones económicas y tecnológicas, sin la dimensión medioambiental. Es fundamental mejorar la tasa de producción y la calidad de corte al tiempo que se mitiga el efecto de la fabricación en el medio ambiente. En los procesos de mecanizado, las variables de optimización más utilizadas son la tasa de arranque de material, la rugosidad superficial, la fuerza de corte, la vida útil de la herramienta y el consumo de energía 7-11. En estudios previos se ha evidenciado la fuerte correlación entre algunas de las anteriores variables, es así que, la mejora de una variable de salida en el proceso de mecanizado no siempre es posible sin afectar alguna otra variable y para reducir el consumo de energía del proceso de corte, tanto la rugosidad de la superficie como la tasa de remoción de material deben considerarse al mismo tiempo 5.
Sihag y Singh realizaron una revisión de literatura sobre el consumo de energía en centros de mecanizado e identificaron los criterios más utilizados en la literatura especializada para la clasificación del consumo de energía 2, estos son: el consumo de energía del husillo y del proceso de remoción del material, el consumo de energía debido a la operación para la fabricación del producto (llamado energía directa) incluyendo el consumo de energía de la herramienta de corte, el refrigerante y material de la pieza de trabajo (llamado energía indirecta) (Este criterio también es propuesto en 6). También se considera el consumo de energía en el proceso de corte (remoción neta de material) y el consumo de energía de la maquina al estar encendida (motores, actuadores, centro de control, etc.), y finalmente, el consumo de energía considerando el estado operativo general de la máquina, esto es: puesta en marcha, arranque, aceleración-desaceleración, marcha en vacío, corte de aire, corte, cambio de herramienta y ajuste, entre otros.
Sihag y Singh evidenciaron que el consumo de energía de los centros de mecanizado no solo se asocia al proceso de remoción de material y, que, por el contrario, la complejidad de su estructura y la cantidad de variables que intervienen en el proceso hacen de la optimización del consumo de energía una necesidad y gran reto académico e industrial. Previamente al estudio de Sihag y Singh, Behrendt y otros 6, habían cuantificado y jerarquizado la potencia total requerida por el proceso de mecanizado. Li y otros en 4 proponen la clasificación del consumo de energía del proceso de mecanizado en tres etapas: Etapa de espera, etapa de corte en aire (cuando no hay carga aplicada a la herramienta) y etapa de corte (cuando el movimiento de la herramienta se traduce en remoción de material). En la Figura 1 se presenta el perfil de potencia en un proceso convencional. Li y otros proponen además tres enfoques para disminuir el consumo de energía en el proceso de mecanizado: 1) balance entre los objetivos económicos y los objetivos sustentables del proceso de mecanizado. 2) mejora en la planificación de los procesos integrando la optimización de los parámetros de corte y 3) mejora en la planificación de los procesos integrando la optimización de la ruta de corte 4,12.
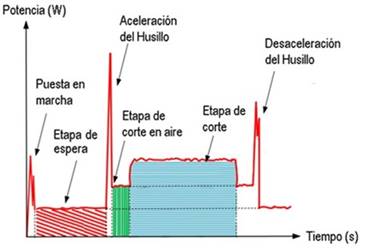
Fuente: Adaptado de Li et al. 13
Figura 1 Gráfico de potencia instantánea durante el proceso de corte CNC.
Dentro del análisis realizado por Behrendt et al.6 se identifica que a nivel tecnológico la optimización de los parámetros de corte y la optimización de la ruta de corte son los dos enfoques que presentan un mayor espectro de intervención dado que no involucra el cambio de la operatividad intrínseca del centro de mecanizado o el impacto ambiental de la extracción y disposición de las materias primas a ser mecanizadas. Entre los parámetros de corte estudiados se encuentran: la velocidad del husillo, la profundidad y ancho del corte, la velocidad de avance, etc. 4; estos parámetros se han relacionado con los niveles de consumo de energía de acuerdo con el tipo de ataque de las herramientas de corte y el ángulo de incidencia en el material, encontrando que la energía de fricción es aproximadamente la mitad de la energía de corte para todos los rangos de velocidad 6,8,14.
También se han relacionado el esfuerzo cortante, la energía de fricción 14 y la rugosidad 15; con lo que se puede inferir que es muy elevada la cantidad de variables y parámetros del proceso de mecanizado que tienen una influencia directa en el consumo energético y una alta interdependencia entre ellos, lo que indica que predecir el consumo es cada vez más complejo y sugiere la necesidad de estudios sistemáticos que ayuden a identificar las variables de mayor impacto. Behrendt et al.6, midieron la potencia para el tiempo de espera o stand by de ocho diferentes centros de mecanizado clasificados según su capacidad de procesamiento (Ver Figura 2). En dicho estudio se evidenció el alto consumo de energía de todos los componentes del centro aun cuando la herramienta no tiene una carga aplicada sobre ella, es decir, no se está removiendo material.
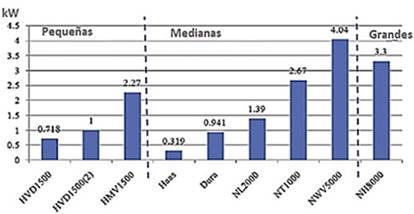
Fuente: Adaptado de Behrendt et al.6.
Figura 2 Consumo de diferentes centros de mecanizado en la etapa de espera (standby).
Se propone, por lo tanto, que para realizar un análisis comparativo entre centros de mecanizado o entre rutas de mecanizado considerar solo la potencia relacionada a la etapa de corte. Las variables a considerar en dicha etapa son la velocidad de corte, avance y profundidad las cuales conducen a una buena precisión en los modelos de predicción 5,16-20; pero es necesario aumentar la cantidad de datos experimentales 5,15. Los estudios centrados solo en el corte son importantes porque este parámetro influye directamente en la calidad superficial de la pieza mecanizada.
Un gran número de estudios consideraron la optimización de los parámetros de corte como una estrategia importante para mejorar significativamente la eficiencia en el mecanizado, estos parámetros deben seleccionarse cuidadosamente de tal modo que se logre maximizar la vida útil de la herramienta, la calidad del producto terminado y el mínimo consumo de energía posible. En el presente trabajo mediante un diseño experimental factorial se desarrolla un análisis de la influencia de los parámetros de corte, esto es: profundidad de corte, velocidad del husillo y velocidad de avance sobre el consumo energético y la calidad superficial, en dos centros de mecanizado. Los centros de mecanizado a comparar fueron: el CNC de cinco ejes Leadwell V-40iT® y la Hass UMC-750.
2. Metodología
2.1. Centros de mecanizado
Para el presente estudio se implementaron el mismo set de experimentos en dos centros de mecanizado diferentes: el centro de mecanizado de cinco ejes Leadwell V-40iT® ubicado en el Instituto Tecnológico de Medellín (denotado en el presente estudio así: ITM), el cual cuenta con unas especificaciones eléctricas de 18.5 KW de potencia máxima en el husillo, tensión de entrada CA (3 fases) a 440VCA, una carga (3 fases) de 35A. El segundo centro utilizado fue el centro de mecanizado de cinco ejes Haas UMC-750, con unas especificaciones eléctricas de 22,4 Kw de potencia máxima en el husillo, tensión de entrada CA (3 fases) de 220VCA-baja y 440VCA-alta, una carga (3 fases) de 70A-baja y 35A-alta, ubicado en la Institución Universitaria Pascual Bravo en Medellín (denotado en el presente estudio IUPB). Para ambos centros se realizó el programa de mecanizado utilizando el software Sprutcam® con postprocesador para el diseño de la ruta de mecanizado.
2.2. Diseño de experimentos
Con el propósito de identificar los efectos principales de las diferentes condiciones operacionales sobre las variables de salida se utilizó un diseño experimental con un enfoque factorial. Las variables o factores controlables empleados en este estudio para evaluar su efecto sobre la rugosidad y el consumo de energía fueron: profundidad de corte, PC (mm), velocidad del husillo, VH (RPM) y velocidad de avance, VA (mm/min). Las variables de salida o de respuesta fueron el consumo energía (Wh) y la rugosidad (Ra: media aritmética de valores absolutos del perfil de rugosidad, µm). El consumo de energía se obtuvo integrando la potencia en el intervalo de tiempo de la etapa de corte de cada experimento. Se seleccionaron cinco niveles para VH y VA y cuatro niveles para PC, teniendo un total de 100 tratamientos (ej. 4x5x5). Este set experimental se implementó en cada centro de mecanizado sin realizar réplicas por tratamiento, para un total de 200 corridas experimentales. En la Tabla 1 se presentan los factores y niveles utilizados en los experimentos.
Los factores controlables del proceso fueron el material de trabajo (acero SAE 1045), la herramienta de corte y la programación, los factores no controlables del proceso fueron fluctuaciones eléctricas y vibraciones externas. El material mecanizado seleccionado fue el Acero SAE 1045 con una dureza de Brinell de 190. La composición química del material mecanizado se presenta en la Tabla 2 y la herramienta de corte seleccionada fue una fresa de ½ in de carburo de tungsteno sin recubrimiento, marca Master Cut.
Para ambos centros de mecanizado se utilizó la prensa de sujeción Vertex y una boquilla de montaje tipo BT40, dicho montaje puede observarse en la Figura 3. Para la medición del consumo de energía se utilizó un Fluke modelo 1732 de conexión directa en voltaje y por campo magnético en amperaje a las líneas de ingreso del centro de mecanizado, esta señal registra todo el proceso según se presentó en la Figura 1 anteriormente, sin embargo, para el procesamiento de los datos y el análisis de resultados solo se consideró la etapa de corte. Finalmente, para la medición en la calidad del acabado superficial se utilizó un rugosímetro portátil por contacto, marca TMTeck Modelo TMR 200 con una resolución de 0.001µm.
Tabla 1 Tabla de parámetros de proceso de mecanizado evaluados en el proyecto.
Factor | Unidad | Nombre | Nivel | |||
---|---|---|---|---|---|---|
2 | 3 | 4 | 5 | |||
Profundidad de corte | Mm | PC | 1 | 1,5 | 2 | 2,5 |
Velocidad de Husillo | RPM | VH | 950 | 1187,5 | 1425 | 1662,5 |
Velocidad de avance | mm/min | VA | 134 | 167,5 | 201 | 234,5 |
Fuente: Elaboración propia
Tabla 2 Composición química Acero SAE 1045
Elemento | Carbono | Molibdeno | Fosforo | Azufre |
---|---|---|---|---|
Wt% | 0.43-0.50 | 0.6-0.9 | 0,4 | 0,05 |
Fuente: Elaboración propia
3. Resultados
En la Figura 4 se presenta la influencia de los tres factores de entrada (profundidad de corte, velocidad de avance y velocidad del husillo) sobre los parámetros de respuesta para el centro de mecanizado IUPB. En las Figuras 4a y 4c se puede observar que, para variaciones de la profundidad de corte y la velocidad del husillo, respectivamente, se obtienen valores entre 20 y 50 Wh para el consumo de energía y alrededor de 0.4 y 2.5 µm sin poderse identificar una tendencia según la variación de los factores de entrada. Para el caso de la velocidad de avance (ver Figura 4b) la rugosidad sigue reportando valores en el mismo intervalo anterior, pero se identifica un menor consumo de energía para altas velocidades de avance y un mayor consumo de energía para bajas velocidades de avance.
En la Figura 5 se presenta la variación de los parámetros de salida en función de los factores de entrada para el centro de mecanizado ITM. Para el factor de profundidad de corte se observa un incremento de la rugosidad para una profundidad de corte de 1.5 mm, también se observa una disminución de la rugosidad al aumentar el consumo de energía (ver Figura 5a), esta misma relación se observa para la velocidad del husillo (ver Figura 5c). En la Figura 5b se observa la inferencia de la velocidad de avance del centro Leadwell (ITM) con una tendencia similar para el centro de mecanizado Haas (IUPB), donde se disminuye la rugosidad a medida que el consumo de energía aumenta y viceversa, y se aumenta el consumo de energía con bajas velocidades de avance. Para el centro de mecanizado ITM se tiene un intervalo de consumo de energía entre 40 y 90 Wh y un intervalo de rugosidad entre 0.5 y 3.5 µm. Se hace notar que a mayor velocidad de avance menor consumo de energía para ambos centros de mecanizado.
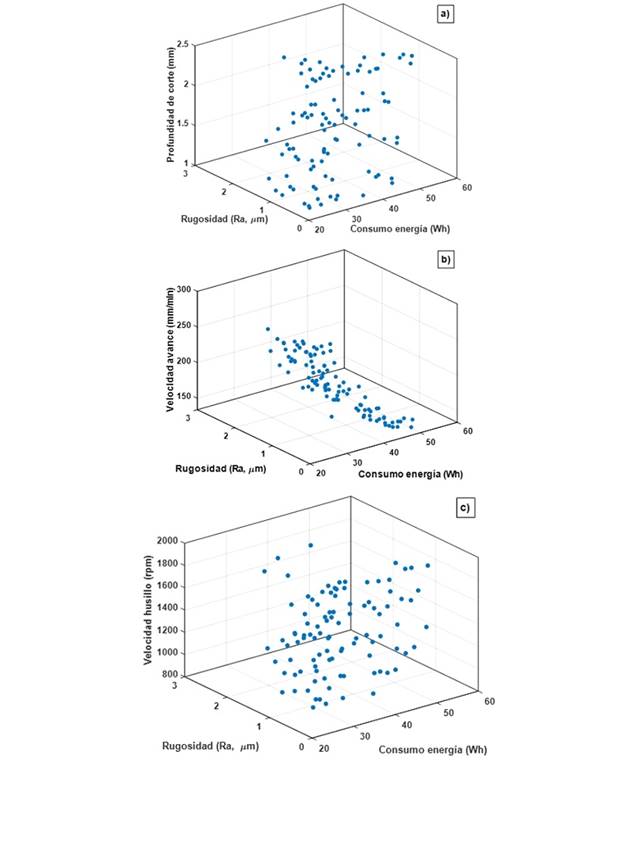
Fuente: Elaboración propia
Figura 4 Influencia de los factores de entrada sobre la rugosidad y el consumo de energía para el centro de mecanizado IUPB.
Con el propósito de corroborar la relación entre la velocidad de avance y el consumo de energía, se presenta en la Figura 6 el consumo de energía y la rugosidad para los dos centros de mecanizado, ilustrando el menor y el mayor nivel de la velocidad de avance, 134 y 268 (mm/min) respectivamente. Los resultados presentados en la Figura 6 son para una profundidad de corte de 1mm la cuál es el nivel inferior del factor. Se evidencia que, aunque se varíe la velocidad del husillo, el factor que más influencia tiene en el consumo de energía es la velocidad de avance. El centro de mecanizado Haas (IUPB) pasa de un consumo medio de 47.34Wh a un consumo medio de 24.87Wh aumentando la velocidad de avance. De igual manera, el centro de mecanizado Leadwell (ITM) pasa de un consumo medio de 85.14Wh a 42.03Wh.
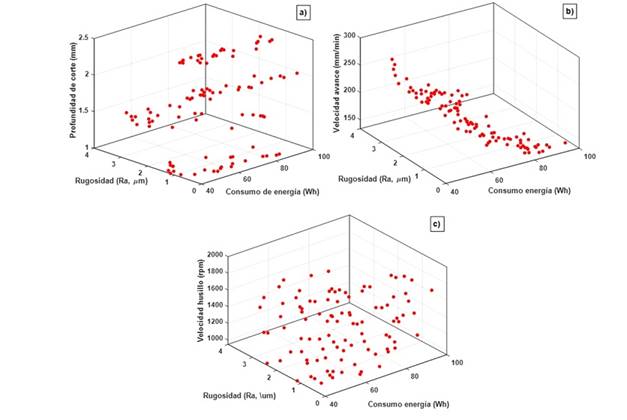
Fuente: Elaboración propia
Figura 5 Influencia de los factores de entrada sobre la rugosidad y el consumo de energía para el centro de mecanizado ITM.
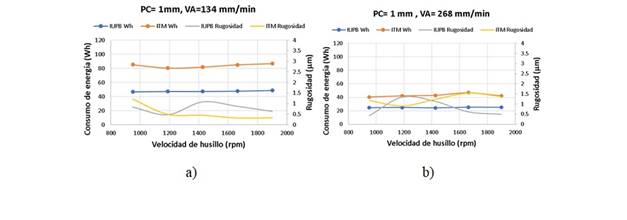
Fuente: Elaboración propia
Figura 6 Consumo de energía y rugosidad para una profundidad de corte de 1 mm a) Velocidad de avance de 134 mm/min. b) Velocidad de avance de 268 mm/min.
En la Figura 7 se presenta un análisis similar al de la Figura 6 pero para el mayor nivel del factor de profundidad de corte equivalente a 2.5 mm. Al igual que en la Figura 6, en la Figura 7, se evidencia que el incremento en la velocidad de avance da como resultado la disminución del consumo de energía. Esta relación entre la velocidad de avance y el consumo de energía está dada, principalmente, por la disminución del tiempo de mecanizado disminuyendo así el tiempo de consumo de potencia del centro. El centro de mecanizado Haas (IUPB) pasa de 50.55Wh de consumo medio a 28.32Wh. Para el centro de mecanizado Leadwell (ITM) la variación va de 86.75Wh a 45.13Wh en el incremento de VA. Dado que pasa los cuatro experimentos (Figura 6 y Figura 7) no se evidencia una variación significativa en la rugosidad de las piezas obtenidas se recomienda trabajar con mayores valores de velocidad de avance para condiciones operaciones similares a las consideradas en el estudio. Los resultados obtenidos indican una muy leve influencia de la velocidad de avance en la calidad del acabado superficial, a diferencia de lo que reporta la literatura donde se expone que es la relación velocidad del husillo y velocidad de avance los factores de mayor influencia en la calidad superficial de la pieza 21,22.
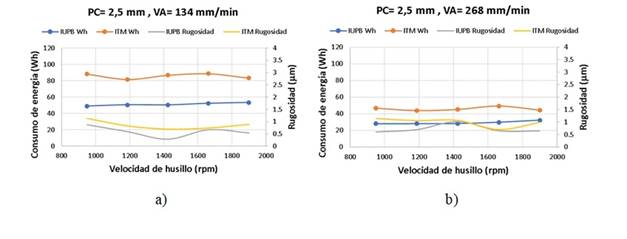
Fuente: Elaboración propia
Figura 7 Consumo de energía y rugosidad para una profundidad de corte de 2.5 mm a) Velocidad de avance de 134 mm/min. b) Velocidad de avance de 268 mm/min.
En la Figura 8 se observa cómo la variación en la profundidad de corte afecta significativamente la rugosidad estabilizando sus valores en los dos centros de mecanizado para todos los niveles de la velocidad del husillo.
En las figuras anteriores se han analizado los efectos independientes entre los factores de entrada y los parámetros de salida, sin embargo, por la naturaleza del fenómeno y, por lo tanto, por la estructura del diseño experimental los factores presentan una interacción entre ellos que da como resultado los efectos de los parámetros de salida.
En la Figura 9 se presenta un análisis de interacción por pares para los tres factores de entrada sobre cada parámetro de salida para el centro de mecanizado Haas. Las Figuras 9a, 9b y 9c presentan los gráficos de interacción con respecto al consumo de energía y las Figuras 9d, 9e y 9f con respecto a la rugosidad. El propósito del análisis de interacción es identificar el efecto conjunto de dos o más factores de entrada sobre la variable dependiente o parámetro de salida.
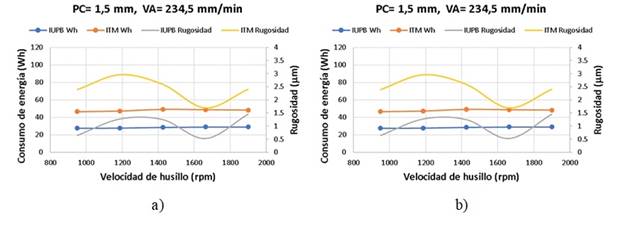
Fuente: Elaboración propia
Figura 8 Consumo de energía y rugosidad para una a) Velocidad de avance de 234.5 mm/min. a) profundidad de corte de 1.5 mm. b) profundidad de corte de 2 mm.
Las figuras se interpretan mediante el entrecruzamiento (o corte) de las líneas de los diferentes niveles de un factor, así, si existen entrecruzamientos se puede establecer que existe una interacción entre los factores para los diferentes niveles. La existencia de interacciones entre factores indica que el análisis del efecto de cada factor individual dependerá de los niveles en los que se encuentre los demás factores (con los que exista interacción) a la hora de observar o analizar dicho efecto.
En la Figura 9a se observa que los diferentes niveles de la velocidad del husillo se cortan predominantemente para valores bajos de la profundidad de corte, evidenciando que existe un efecto entre dichos factores y que la velocidad del husillo condiciona el efecto de la profundidad de corte en el consumo medio de energía. Para valores elevados de la profundidad de corte (PC=2mm o PC= 2.5mm) la interacción disminuye y aumenta el consumo de energía. En la Figura 9b y 9c se observa que sí existe una interacción entre la velocidad del husillo y la velocidad de avance al igual que la profundidad de corte y la velocidad de avance, sin embargo, estas dos interacciones son menos marcadas ya que presentan menos cortes entre líneas.
De lo anterior se puede concluir que existe un efecto más independiente entre la velocidad de avance con los otros factores respecto al consumo de energía, también se puede observar que el consumo de energía medio disminuye cuando aumenta la velocidad de avance como se ha identificado en las figuras anteriores. Para el caso de la interacción entre los factores respecto a la rugosidad se observa que para todos los factores existe una evidente interacción entre pares (ver Figura 9d, >, 9e y 9f). Este resultado indica que el efecto marginal de cada nivel de los factores o variables de entrada debe considerar los niveles de los demás factores involucrados en el análisis. En otras palabras, analizar el efecto de cada factor sobre la rugosidad de manera aislada no sería adecuado.
En la Figura 10 se presentan los gráficos de interacción para el centro de mecanizado Leadwell -ITM. En este caso también se presenta un efecto de interacción entre la velocidad del husillo y la profundidad de corte sobre el consumo de energía (ver Figura 10a). El incremento del consumo de energía se da al aumentarse la profundidad de corte para todos los niveles de la velocidad del husillo que presenta el centro de mecanizado Haas (ver Figura 9a) también se observa el mismo comportamiento para el centro de mecanizado Leadwell el consumo de energía. Observando la rugosidad se continúa observado la presencia de una interacción entre los factores para todos los niveles. Sin embargo, y a diferencia del centro de mecanizado Haas, la interacción entre la velocidad del husillo y la profundidad de corte (ver Figura 10e) y, además, la interacción entre la profundidad de corte y la velocidad de avance (ver Figura 10f) son menos marcadas, disminuyendo el condicionamiento mutuo entre dichos factores y sus respectivos niveles respecto a la rugosidad. Cabe resaltar la disminución de la rugosidad para elevados valores de la profundidad de corte (PC=2 y PC= 2.5) como se observa en la Figura 5a).
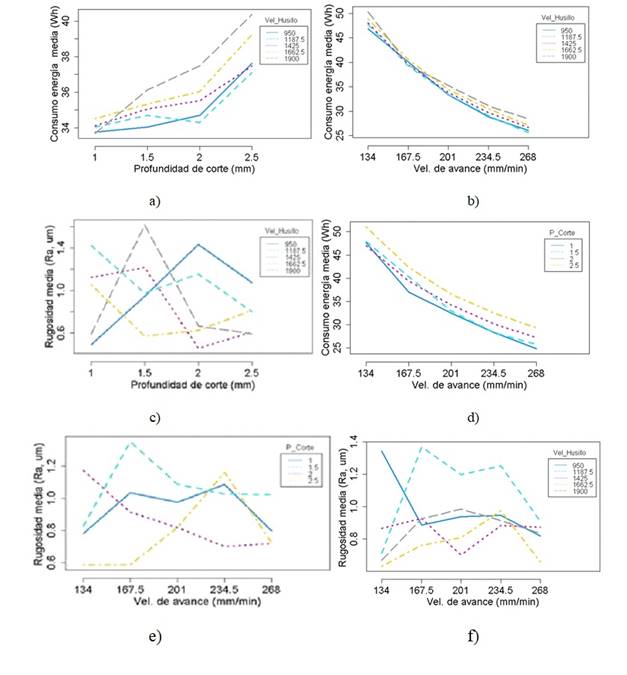
Fuente: Elaboración propia.
Figura 9 Análisis de interacción entre los factores de entradas y los parámetros de salida para el centro de mecanizado Haas - IUPB.
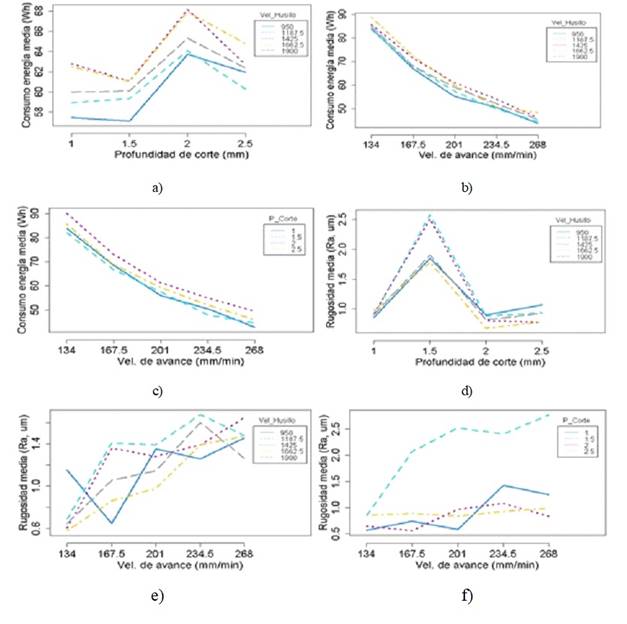
Fuente: Elaboración propia
Figura 10 Análisis de interacción entre los factores de entradas y los parámetros de salida para el centro de mecanizado Leadwell - ITM.
El desempeño de las herramientas de corte es otro factor considerado en los estudios de consumo energéticos en centros de mecanizado. La duración de la herramienta de corte en función de las variables operacionales son un parámetro clave para hacer del proceso de mecanizado más eficiente. Para el presente estudio el consumo de las herramientas de corte no fue un parámetro analizado debido a que cada experimento se realizó con una fresa nueva y el tiempo de las pruebas fue muy corto (entre 47 y 115 segundos).
En la Figura 11 se presenta el antes y el después de una herramienta de corte utilizada en el centro de mecanizado Haas de la IUPB con las condiciones experimentales de PC=2.5 mm, VH=1900 RPM y VA=268 mm/min. En la Figura 11b se detalla una pequeña fractura y un leve desgate en el borde de ataque, sin embargo, la herramienta podría ser utilizada para un nuevo proceso de mecanizado sin interferir significativamente en la calidad del proceso.
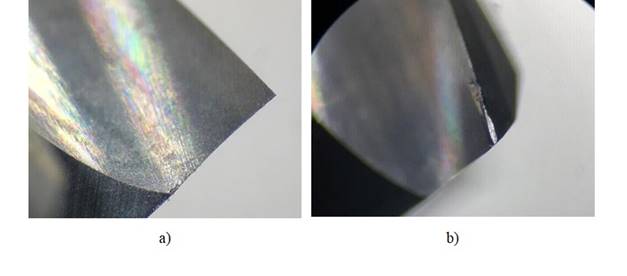
Fuente: Elaboración propia.
Figura 11 Detalle de las herramientas a) antes del proceso de mecanizado b) después del proceso de mecanizado.
Finalmente, y considerando los resultados previamente descritos, se pudo evidenciar la influencia que tiene el parámetro velocidad de avance sobre el consumo de energía, puesto que este parámetro tiene una relación directa con el tiempo de mecanizado. De igual manera, a bajas profundidades de corte el consumo energético de los centros de mecanizado se redujo considerablemente. Debido a lo anterior se recomienda controlar la velocidad de avance y la profundidad de corte si el objetivo es optimizar el consumo de energía de los centros de mecanizado.
4. Conclusiones
En este artículo se presenta un análisis descriptivo de los resultados obtenidos en un experimento donde se estudia la influencia de tres factores controlables (profundidad de corte, velocidad del husillo y velocidad de avance) sobre dos variables respuesta o de salida (la calidad del proceso de mecanizado, o rugosidad, y el consumo de energía) para dos centros de mecanizado: el centro Haas UMC-750 y el centro Leadwell V-40iT®. Los diferentes análisis desarrollados evidenciaron que el factor que tiene una mayor incidencia en consumo de energía en ambos centros de mecanizado es la velocidad de avance, lográndose observar reducciones en el consumo de hasta 50% para el aumento de la velocidad de avance. Este resultado se debe en gran medida a que dicho factor determina el tiempo de duración del proceso de mecanizado. Adicionalmente, se encuentra un efecto de interacción relevante entre la profundidad de corte y la velocidad del husillo sobre el consumo de energía.
De igual manera, se encuentran efectos de interacción (por pares) entre todos los factores sobre el acabado superficial, medido mediante la caracterización del parámetro de rugosidad Ra (um). Se evidenció que todos los factores tienen una interacción marcada para todos los niveles, y, en particular, se identificó que la profundidad de corte influencia considerablemente la rugosidad. Dichas interacciones señalan la importancia de la interdependencia de los efectos de los factores involucrados y se recomienda no realizar análisis aislados o marginales de estos factores. Teniendo claro que los tres factores considerados en el presente estudio interactúan para generar un cambio en los parámetros de salida, se concluye que la experimentación realizada no revela la influencia directa de la velocidad del husillo en el consumo de energía y acabado superficial.
Dado que los resultados y análisis presentados son de carácter descriptivo, se deja como trabajo futuro un análisis estadístico más elaborado de los resultados obtenidos con el experimento presentado. Considerando que sólo una réplica por tratamiento fue realizada un análisis de varianza (ANOVA) Bayesiano sería el más indicado para esta situación. Con este tipo de análisis, además de cuantificar efectos principales (marginales) e interacciones, también permitiría la identificación de las condiciones óptimas de operación para cada centro de maquinado para los factores estudiados en este trabajo.