1. Introduction
Solid lubricant coatings have attracted significant attention in recent years, as they can drastically reduce material wear rate and surface friction in an extensive range of sliding environments [1-4]. Among different types of materials used in solid lubricant applications, transition-metal dichalcogenides (TMDs) (sulfides, selenides or tellurides of tungsten, molybdenum and niobium) have been regarded as being of major importance for applications, including solid lubricants, in the aeronautic and aerospace industry [5]. For instance, one of the most widely used TMDs is tungsten disulfide (WS2), due to its high thermal stability (~500 °C in air) and low friction coefficient (between 0.02 and 0.06) [6,7]. Because of these outstanding properties, WS2 can be considered as a suitable material for applications where low friction (lubricity) at high temperatures is required [8]. On the other hand, the hexagonal structure of WS2 comprises S-W-S atomic planes joined by covalent bonds into layers, with Van der Waals forces acting as weak interlaminar bonds that give WS2 its lubricant behavior [6,7,9]. This structure graphite -like hexagonal layered structure makes WS2 a very suitable material for solid lubricant applications [10]
The magnetron sputtering technique is commonly used in coatings deposition technology, since it displays greater advantages compared to other methods. These advantages result in the possibility of obtaining highly precise thicknesses and to achieve material stoichiometry control [2]. In spite of these advantages, Polcar and Cavaleiro [11] stated that the magnetron sputtering technique has disadvantages for TMD coatings production, including: a highly-disorganized structure (exhibiting low orientation in the (0002) plane); extremely high sensitivity to environmental attacks; high porosity; and poor mechanical properties. These conditions affect performance of the material when used as a lubricant. A possible alternative for improving the material deposition performance by magnetron sputtering involves doping with other metallic and/or non-metallic elements [6-8,11-14]. Such doping can increase film density, adhesion and hardness. For instance, Scharf et al. [6] produced and characterized Ti-doped WS2 coatings using co-sputtering for solid lubricant applications. The team found a decrease in the friction coefficient when low Ti quantities were added to WS2 coatings. Furthermore, the addition of small, calculated amount of Ti also decreased oxides formation in high-humidity, high-temperature applications [15,16]
An important property to analyze when materials are exposed to moisture, high temperatures and aggressive environments is corrosion resistance In nanocrystalline materials, corrosion resistance depends on several factors such as the concentration of the alloying element; production conditions; microstructure; and environmental conditions [17]. Of the few studies on WS2-Ti, not many are dedicated to the characterization of its corrosion resistance properties. WS2-Ti corrosion resistance characteristics can be correlated with its composition and tribological properties, such as adherence and friction coefficient.
In this study, the effect of Ti doping in WS2 compounds was analyzed. A chemical composition, friction coefficient, adhesion, and corrosion resistance of Ti-WS2 analysis, depending on Ti cathode power applied, was conducted. The observed properties were compared with the performance of steel and undoped WS2.
2. Materials and methods
WS2 and Ti-doped WS2 (WS2-Ti) thin films were deposited on silicon and AISI 304 stainless steel substrates using a magnetron sputtering AJA ATC 1500 system. Coatings were produced using WS2 (99.95%) and Ti (99.99%) targets with a 2-inch diameter. The sputtering system was first pumped down to 1 x10-4 Pa. Then, an Argon-based plasma cleaning process was performed for 15 min to eliminate impurities that were not removed during the previous sample cleaning. A non-reactive atmosphere of Ar was used at a working pressure of 0.4 Pa. The WS2 cathode was maintained at a constant power of 2.5 W/cm2, whereas the power of Ti cathode was set at 0, 0.25, 0.5, 0.75, 1 and 1.25 W/cm2. The elemental composition was investigated using a Philips XL 30 TMP scanning electron microscope, applying a standard Energy Dispersive Spectroscopy-EDS technique at 20 keV and 200x.
The coatings’ atomic bonds were characterized by Raman spectroscopy, using a Nicolet Almega XR visible dispersive Raman microscope which included an Olympus BX51 microscope. A 532-nm laser (green-visible) at 80% power was used. The thin films’ thickness was determined using a KLA Tencor D100 profilometer, obtaining an average value of 500 nm for the films set. Scratch adhesion testing was performed using NANOVEA IBIS-Technology equipment, which includes a Rockwell C diamond indenter with a 200-μm radius, 35 N of maximum load and a distance of 2.5 mm. Corrosion resistance measurements were conducted using electrochemical impedance spectroscopy (EIS) with a Potentiostat-Galvanostat Gamry series G instrument, using 3.5 wt% NaCl as the electrolyte. A calomel electrode was used as a reference electrode, with a graphite counter electrode and the coating as the work electrode, in a range between 105 and 0.01 Hz and an open-circuit time potential of 1800 seconds. Curves obtained were analyzed using the Gamry Echem Analyst software, where polarization resistance, Rp, and the equivalent circuit were determined.
2. Results
3.1. EDS analysis
Titanium, tungsten, and sulfur sample quantifications are listed on Table 1. As expected, as the power of the Ti cathode was increased, the atomic percentage of Ti was also increased, at the expense of the W percentage. Furthermore, the %S remained approximately constant. The materials did not show the expected stoichiometry (Ti-WS2), since %S is not exactly the sum %Ti + %W. The deficiency in %S is due to the great energy amount required by Ar+ to impact the WS2 cathode. According to Banerjee and Chattopadhyay [18], this high energy requirement results in an enhanced dissociation of WS2 molecules, also reflected in the sulfur deficiency of the material.
3.2. Raman analysis
Fig. 1 shows the µ-Raman spectrum for undoped samples of WS2. In this figure, bands corresponding to W-S bonds at 352 cm-1 and 415 cm-1 were identified. These bands belong to the E2g mode of W+S movement in the x-y plane and the A1g mode of the S movement in the z axis [19]. Bands at 695 cm-1 and 805 cm-1 were also observed [20]; the band at 695 cm-1 corresponds to the O-W-O stretching mode of WO3 • nH2O, and the band at 805 cm-1 is assigned to the asymmetric stretching mode of oxygen bridges νa (O-W-O) [21,22]. Finally, the band observed at 518 cm-1 corresponds to the vibrational mode of Si [23]. O-W-O bands exist due to the material exhibiting orientations in basal planes that are perpendicular to the substrate surface (1-type films). This orientation allows exposure of the structure’s lateral faces to the environment. Then, these points exhibit activation because of the dangling bonds at cell edges [23], acting as recombination sites and centers for electrochemical corrosion [24].
Fig. 2 shows µ-Raman spectra for doped samples. It is possible to deduce from these spectra that due to the inclusion of Ti in the material, a significant change was induced in the WS2 structure. Evidence supports this is caused by the high sensitivity of Raman spectroscopy to crystalline structure variations [25]. These changes are reflected in the disappearance of the main bands at 352 cm-1 and 415 cm-1 of the E2g and A1g modes. The introduction of Ti in the WS2 lattice can block the free movement of W and S, while also inducing a phase transition. Ti doping in transition metal dichalcogenides is also responsible for structure reordering and amorphization when spinodal segregation is achieved [6, 7]. As Ti percentage increases, a steeper slope of the 200 cm-1 and 450 cm-1 bands was observed for samples deposited at a Ti cathode power density of 0.75, 1 and 1.25 W/cm2, indicating continuous material reordering and crystallization. This was corroborated by TEM images [14], which evidenced that including titanium in the structure makes it amorphous; increasing its content leads to nanocomposite form organization of the structure.
3.3. Scratch test analysis
Fig. 3(a) presents the Drag coefficient (DCof) as a function of distance for undoped WS2 samples. When a significant change occurs in the DCof-distance curve slope, a perpendicular line is traced until it intersects the load distance plot. The intersection point is then projected to the load axis to determine the critical load of the coating/substrate system. Initial fluctuations of DCof were caused during an initial stage of surface roughness polishing. As distance and load increase, the curve is stabilized. Two slope changes corresponding to adhesive and cohesive failures at critical loads of 11.5 N and 18 N respectively were observed. The image of the track obtained at 10x (Fig. 3(b)) shows a cohesive failure at 0.8 mm represented by a plastic deformation typical of laminar solids. Adhesive failures occurred at a distance of 1.3 mm, where applied load was great enough to generate film spallation.
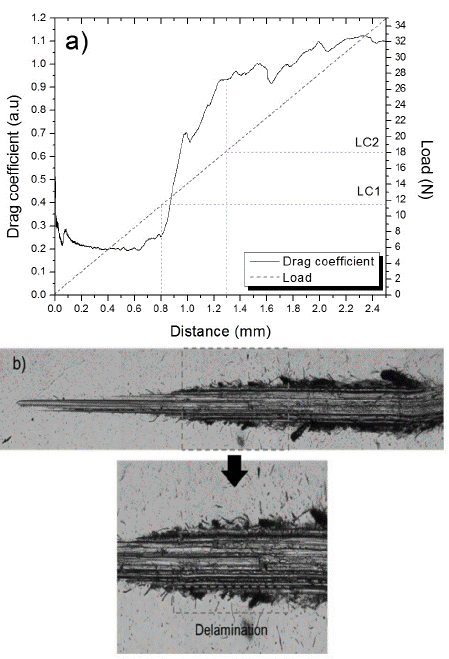
Source: The authors
Figure 3 Scratch test (a) Drag coefficient, Load depending on the distance (b) 10x micrograph of scratch track.
The critical load dependence on Ti cathode power can be observed in Fig. 4(a). Abrupt changes in critical load are evidenced at 18 N and 7 N for undoped and WS2-Ti 0.25 W samples, respectively. This decrease is caused by the inclusion of Ti in the WS2 structure, which produces numerous micro-deformations and phase transitions (Fig. 4(b)). These changes contribute to stress accumulation, causing premature coating damage.
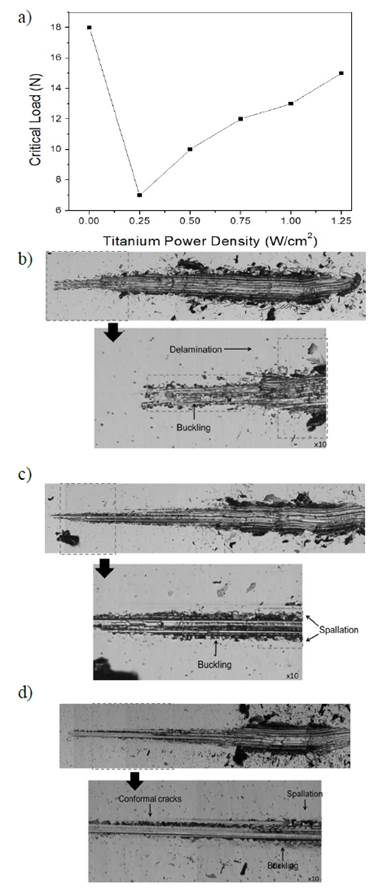
Source: The authors
Figure 4 a) Dependence of critical load (Lc) on titanium cathode power density, b) 10x micrograph of scratch track WS2-Ti 0.25 W, c) WS2-Ti 0.75 W and d) WS2-Ti 1.25 W.
For samples deposited at power density levels greater than 0.25 W/cm2, a progressive increase in critical load is observed. This is attributed to the following factors: (i) substrate-coating interface changes, leading to improved interaction between these and therefore increased adhesion; and (ii) an increase in hardness due to Ti doping. Changes in the coatings’ characteristic failure mechanism were then observed during the scratch test, where samples exhibited buckling or spallation-type failures or a mixture of these failure types (buckling spallation) along the track (Figs. 4(b), 4(c), 4(d)). These failures were more evident as the Ti concentration increased, consistent with an increase in the fragility of coatings [26,27].
Nevertheless, it is important to note that critical load values for doped samples are lower than those observed for undoped coatings, indicating an apparent increase in hardness and in fragility of the material were caused as a consequence of the residual stress brought about by the dopant. These combinations of effects forced the samples to fail more easily, which decreases critical load values [26]. A similar behavior (an increase in the hardness and in the critical load of doped WS2) is presented by Nossa and Cavaleiro [12]. They studied the mechanical properties, namely hardness and adhesion, of W-S coatings doped with nitrogen and carbon. Films were deposited using RF magnetron sputtering. Hardness and critical load of adhesion (Lc) values for undoped films were 0.6 ± 0.04 GPa and 5.2 N, respectively. Nevertheless, as the doping increased, the hardness and adhesion of the material increased considerably, reaching maximum values of 4.6 ± 0.3 GPa and 36.6 N for nitrogen and 5.4±0.2 GPa and 50 N for carbon. The authors attributed this behavior to the densification of the films, a phenomenon that promotes an increase in hardness and therefore an increase in critical load.
3.4. EIS analysis
Electrochemical impedance spectroscopy (EIS) testing was conducted to study the corrosion resistance behavior of steel, WS2 and WS2-Ti films. Results were determined by calculating polarization resistance (Rp) values and the equivalent circuit. Nyquist diagrams are shown in Fig. 5(a); experimentally obtained semicircles were observed, and these curves were used to carry out an adjustment using Gamry Analyst software Echem, yielding polarization resistance (Rp) values for each material. Resulting values are presented in Table 2.
The fitting was obtained from an equivalent circuit included in the software database. For these samples, the fitting was performed using a circuit containing a CPE (constant phase element), as shown in Fig. 5(b). The circuit is composed of Ru and Rp resistances, where Rp is parallel with an element that can work as a resistor or capacitor (CPE), which works here as a capacitor, completing a basic circuit impedance. The obtained Rp values showed low dispersion levels, as did the values for Ru, which corresponds to the resistance of a 3.5% NaCl solution with an average value of 26.67 ± 3.14 Ω [28, 29]. The low dispersion results are indicators of the validity of the results and the quality of the prepared solution.
As evidenced by the Rp values, the increase in corrosion resistance of steel following the addition of a WS2 layer was observed; this is explained by the formation of a WO3 layer in the film, seen in Raman spectroscopy, which protects the exposed surface against electrolyte attacks. However, when Ti is included in the samples, a large reduction in corrosion resistance is observed, even at significantly lower concentrations and in pure samples, as is the case of the WS2-Ti0.25 W/cm2 and WS2-Ti0.5 W/cm2 samples, respectively. This behavior is caused by increased stress and recrystallization processes generated as a result of the inclusion of Ti in the WS2 structure [6,14], creating active sites and film defects that in turn increase the strength of electrolyte attacks [30]. However, when the material contains a higher Ti concentration (WS2-Ti0.75), the observed increase in corrosion resistance was even superior to that of the pure sample. The corrosion resistance increases along with Ti content in the material, due to structural rearrangement at these Ti percentages [14], generating a film with few defects and greater density [12]. In addition, the characteristic behavior of Ti possibly allows the formation of a thin layer of TiO2, which helps inhibit the attack of the solution and improves the corrosion resistance [31].
3. Conclusions
The μ-Raman spectroscopy results for the WS2 sample showed major bands corresponding to the A1g and E2g modes. Additionally, bands corresponding to WO3 indicating the formation of oxides on the surface of the WS2 were observed. When the material is doped structural changes are reflected in the elimination of the main bands; this is caused by the distortion of Ti included in the lattice, preventing free movement of tungsten and sulfur, or because of a phase change.
Scratch test results showed changes in the tribological properties of the material as a result of doping. Furthermore, increasing Ti contents in the samples resulted in progressive failures of brittle materials. A decrease in critical load values following doping was observed because the maximum value of doped samples (WS2-Ti1.25 Lc = 15 N) was lower compared to that of the pure sample (Lc = 18 N).
Electrochemical impedance spectroscopy (EIS) results indicated an increase in corrosion resistance of the substrate with the addition of a WS2 layer. The presence of WO3 on the surface, evidenced by Raman results, contributes to protection from the solution. At higher Ti concentration levels, there was a considerable increase in corrosion resistance due to recrystallization processes in the material, increased material densification, reduction in the number of defects, and the number of active sites in the film, which helped avoid solution-related attacks. Furthermore, Ti was capable of forming an oxide layer helped to protect against corrosion.