1 Introduction
The development of biopolymers of biology base and in addition of being biodegradable has increased, being an alternative to polymers from petroleum [1] and currently a great interest in these biopolymers and also in thermoplastics; one of them is polylactic acid (PLA) due to its easy processability, biocompatibility, and above all due to its obtaining, which is obtained from renewable sources [2]. PLA has attracted a great attention in all areas where a is required a polymer with good mechanical strength and good degradability [3]. Among the main characteristics of this thermoplastic polymer is your biocompatibility with other materials, considering that is a biocompatible polymer and does not produce toxic effects in the environment, which makes it a natural option for the development of new products [4]. However, PLA has some limitations such as its fragility and its low resistance to heat, limiting to some degree the use of this material in certain areas such as biomedicine [1]. For the previously mentioned reason, the study of this material has improved related to sustainable synthesis regarding the development of production routes and especially to a dynamic mechanical study of the material obtained [5].
Polylactic acid is a thermoplastic type aliphatic polyester generated from lactic acid (see Fig. 1) and which can be obtained by various methods of polycondensation of lactic acid (see Fig. 2) and ring opening lactide polymerization (ROP); and the renewable resources products such as starch are a source of extraction [6]. PLA can be synthesized using different catalysts, there are nowadays polymerization studies with more than 100 organometallic catalysts of tin, zinc, aluminium, manganese, among other metals [7].
The PLA precursor molecule (lactide) is produced by microbial fermentation of glucose and obtained from biomasses with high content of lactose or sucrose [8] ; for the previously mentioned reason, the study of obtaining of PLA from biomass has received more attention in lasts years.
PLA has been seen very well in the area of biomedicine, it is used in prostheses, implants, among others, however, in the area of engineering, it is not of adequate interest due to its low thermomechanical properties, such as its low ductility, low thermal distortion temperature, high sensitivity to humidity, but it has an advantage that is its high degradability in different types of hydrolysis [2-9]. To make up for its low mechanical properties, the dosage of this polymer has been studied with various materials such as polysaccharides, biopolymers and nanoparticles thanks to its biocompatibility that it have [10].The Second generation biodegradable polyesters are the most attractive to dose with PLA [11], being the biopolymers derived from the polyxydroxyalkanoates, a family of biopolyesters more attractive in dosages with other polymers, this due to its adjustable mechanical properties and high biodegradability [12].
Other polymers that have been studied are thermoplastic aliphatic polyesters that are an important family of biodegradable polymers and very promising for the replacement of polymers of oil origin [13-14]; within this family there are the polybutylene succinate (PBS) and the polybutylene succinate adipate (PBSA) which are materials with mechanical properties very similar to conventional polymers. [14]. The production of PBS and PBSA is relatively low considering that the obtaining is through of diacids and diols obtaining satisfactory mechanical properties such as flexibility and resistance to impact, differing between them in that PBSA has a lower crystallinity being more susceptible to degradation [15]. In especial the PBSA, being an aliphatic polyester, is a main candidate to be used in food packaging due to its biodegradability [16]. The PBSA has other important characteristics such as the processing capacity, so it can be processed by blown fusion and even injection molded so it can be applied to different technical fields [17]. The PBSA (see Fig. 3) can be synthesized by polycondensation of the 1,4-butanediol and in the presence of succinic and adipic acids, thus obtaining good mechanical properties very similar to polyethylene and polypropylene [18-20]; it can also be synthesized by transesterification from 1,4-butanediol and dimethyl esters of succyanate (SA) and the adipic acid. (AA) [21].
This paper aims at presenting a study of the behavior of a dosage between the PLA and the PB SA and also to determine which is the appropriate processing process for this mixture. It should be mentioned that PLA was extracted from potato residues and PLA was obtained by ring opening polymerization (ROP) of lactide. It must be noted that this several doses were carried out and each one underwent hardness tests as well as dynamic mechanical tests; all with the objective of establishing the best dose of PLA / PBSA and determining the best use of this material.
2 Materials and methods
In this investigation it is divided into two phases; The first one consists of obtaining the PLA from the starch and by means of ring opening polymerization (ROP) the PLA is obtained, followed by dosages of the PLA obtained with the PBSA type Bionolle 30011 commercial grade.
2.1 Obtaining polylactic acid (PLA)
The PLA was obtained by polymerizing of lactic acid in polylactic, and for this, the synthesis of lactic acid was carried out by fermentation of starch (which is a substrate with a high content of carbohydrates).
2.1.1. Lactic fermentation
The objective of this type of fermentation is to obtain lactic acid and for this was used as a substrate the starch that was extracted from potato residues. The extraction of the starch was carried out according to the method established by Holden [22], which consists of various processes such as: washing, cutting, crushing, settling, decanting, drying, grinding, and storage. This extracted starch is subjected to fermentation that consisted first of all of the activation of the bacteria Lactobacillus Delbreuckii Bulgaricus that belong to the Gram-negative lactic acid (BAL) bacterias and awas cquired from the AGROALIMENTAR company. For this activation, were taken 2.5 g of the bacteria and was placed in 250 ml of nutrient agar previously prepared and sterilized, subsequently covered, sealed and placed in an oven at 30 °C for 24 hours, later the bacteria were seeded, with the help of a piece of platinum, in petri dishes and with nutrient agar, to then be identified using the Gram staining technique [23]. For the preparation of the substrate (starch) it was prepared weighing 1000 g with 1000 ml of LAB008 nutrient agar; this nutritive agar was prepared by weighing 13 g of agar in 1000 ml of distilled and autoclaved water at 120 °C and 1 atm pressure, then was added and homogenized 250 ml of the previously activated bacteria and to substrate solution and nutrient agar already prepared. This solution was left to stand for 15 days at a temperature of 19 °C and a pH of 6, to subsequently recover the lactic acid by distillation at a temperature of 90 °C, and the resulting solution was analyzed by spectroscopy FTIR.
2.1.2. Lactic acid polymerization
The lactic acid obtained was polymerized by the ring opening method (ROP) [24], which consisted of taking 100 ml of lactic acid and adding 5 ml of sulfuric acid as a catalyst 60% at temperature of 80 °C for 30 min under stirring, all this in an improvised polymerization experimental system (see Fig. 4). It was left to react for a time of 9 hours and in each lapse of two hours was added 5 ml of sulfuric acid and it was increased to a temperature of 120 ° C whit the objective to obtain the transformation of the dimer lactide.
To the obtained lactide, 3.5 g were added of iron (II) chloride and 50 ml of ethyl alcohol to 95%, at a temperature of 60 ° C for 24 hours; so subsequently that the ethanol was removed by evaporation at a temperature of 78 ° C, also it was filtered and dried at a temperature of 70 ° C until constant weight. And likewise, the product obtained was identified by spectroscopy FTIR.
2.2 Dosage of polymeric material PLA /PBSA
For the mixing of these two biopolymers was carried out on twin screw extruder "mod. LTE-26-40", consisting of 10 sections of 104 mm each one, equipped with a heating system and cooling; in addition, the extruder screws are modulated in order to be able to orient "kneading". The technical characteristics to which the extruder worked are detailed in Table 1.
Under these conditions, were made mixtures of PLA obtained from potato starch and PBSA Bionolle 3001 purchased from Highpolimer Co. Ltd. Japan; to obtain granules and later by compression molding at a temperature of 190 ° C and for 5 minutes were obtained sheets of 170 x 170 mm with a thickness of 4 mm.
For the formulations of this mixture, its are considered yours fluidity indexes and dosages are recorded from 5, 10, 15, 22, 30, 40, 60, and 79.5% of PBSA (see Table 2). In the formulation was added 0.5% of VRX crodamide as a lubricant.
Table 2 Dosages of PLA - PBSA for the extruder.
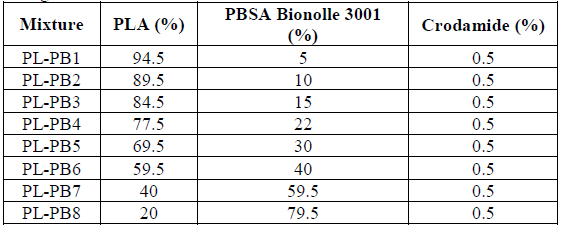
*Where PLA (polylactic acid) and PBSA (polybutylene sucyanate adipate) and also PL - PB are the mixtures that were made.
Source: The author.
2.2.1. Extruded conditions
The extrusion process was carried out at different temperatures and in the different samples, that is, from the PL-PB1 sample to the PL-PB3 it was carried out under certain conditions of temperature as shown in Table 3.
2.3 Instrumental techniques for characterizing the PLA - PBSA mixture
For the samples analysis, different instrumental methods are used to visualize the PLA-PBSA mixtures behavior in different dosages.
2.3.1. Thermogravimetric Analysis (TGA)
This method identifies the material's thermal stability since it can visualize the variation in weight of a polymeric material during heating. With the mentioned heating and specific temperatures, thermal degradation of the material occurs, which is evidenced by "thermogravimetric" curves that describe the material weight loss linked to temperature [25,26]. This thermogravimetric analysis was carried out with a thermobalance model Q500 TGA system by TA Instruments. The sample amount used was 10 mg placed in a platinum crucible at a temperature ranging between 35 °C and 900 °C. The instrument was previously calibrated with pure standards. It was then heated at a controlled and default rate of 1 °C min-1 when weight loss is greater than 2 mg s-1 and 20 ° C min-1 when weight loss is less than 1 mg s-1. The test was carried out in a 35 ° to 600 °C nitrogen chamber and on-air between 600 ° to 900 °C, keeping the constant flows of 50 ml/min.
2.3.2. Differential Sweep Analysis (DSC)
This technique is part of the thermal analysis methods used to characterize polymers' physical properties, in which a property sample is controlled concerning its time or temperature, while the temperature sample changes on a scheduled basis. The DSC allows obtaining thermal information of the analyzed material by heating or cooling it at various controlled temperatures. In particular, the thermal transitions in polymeric materials are determined, including changes in thermal capacity after changes in the state of the material [27-29].
This analysis was performed with a differential scanning calorimeter (DSC) of TA (DSC Q 2000), which was previously calibrated with an indium standard (with a purity of 99.9% at melting temperature Tf = 156.4 °C and melting enthalpy of 28.4 J / g). The sample weighed 10 mg and was placed in an Al crucible with 40 ml capacity. It was then hermetically sealed with an Al cap and finally placed on the calorimeter scale. The heat treatment used for analysis and the crosslinking kinetics of samples was as follows:
First heating: from -70 to 200 °C at 10 °C/min
Cooling: from 200 to -70 °C to 10 ° C/min
Second heating: from -70 to 200 °C at 10 °C/min
The atmosphere is kept inert by a constant flow of nitrogen of 50 ml /min.
2.3.3. Fourier Transform Infrared spectroscopy (FTIR)
This analysis consists of equipment use containing an interferometer that allows scanning all the frequencies present in the IR radiation generated by the grid or prism system. This scan is carried out by a mirror, which, when mobilized, introduces a difference in the optical path giving rise to an interference with the ray reflected by its fixed mirror. In this way, an interferogram is obtained that marks the intensity in a time domain. [30].
The instrument used to characterize the samples was a CARY 660 FTIR spectrophotometer (From Agilent Technologies), and the analysis was performed at a temperature of 25 °C in dry air. Given the samples nature, measurements were performed in attenuated reflectance with a diamond crystal pike and a 45 ° ZnSe arrangement with single reflection. The interferometer generates an interference spectrum in the presence of the beam splitter.
2.3.4. Flow Index Measurement (MFI)
This index represents the fluidity capacity of a polymer under constant pressure and temperature conditions. This analysis is an indicator or tool for quality control of polymers due to its ease of operation. The MFI is quantified by the melt flow defined as the extruded polymer's weight in a specific time (usually 10 minutes). [31]. Method A of ISO 1133 "Determination of the melt flow rate (MFR) and the volumetric melt flow rate (MVR) of thermoplastics" was used. The test was carried out on a Melt Flow Indexer equipment at a temperature of 230 °C at a constant pressure of 10.0 kg molten polymer. The material melt compression occurred in 4 more 1 minutes of permanence at the test temperature. The polymer in the molten state under pressure generated a cylindrical mass flow cut every 5 seconds. The test duration was controlled in 25 minutes, and subsequently, each sample was weighed. In general, experimental conditions for extruded polymer samples should be between 10 mm and 20 mm in length without defects (porosity).
2.3.5 Hardness Determination "SHORE"
It can be derived that the hardness is inversely proportional to the penetration of a punch and is dependent highly on the elasticity modulus and the viscoelastic properties of the material. [32]. To perform this test norm ASTM D2240 "Standard Test Method for Rubber Property -Durometer Hardness" was used, using a CV-SH type durometer and samples with a thickness of 6 mm as indicated in a standard. The tests are performed at an ambient temperature of 23 ± 1 °C in a rigid horizontal plane (to avoid errors), to which stress is applied at a constant speed and perpendicular to the surface for 15 seconds; this procedure was performed at five different points at a distance of 6 mm.
2.3.6. Mechanical Thermo-dynamic Analysis (DMTA)
The test objective is to know the polymeric materials' properties such as glass transition temperature and temperature as a function of frequency expressed in stress curves, characterized by the polymer chain's molecular movement [33]. In this test, a sinusoidal deformation at a constant amplitude is applied, and frequency modulates with respect to time, and from the response sample, a complex modulus can be obtained [34]. The tests were carried out with a Tritec DMTA model 2000 DMA equipment (Triton Technology), applying the conditions shown in Table 4. Also, the geometric measurements that the sample had for this analysis are specified in the same table.
3 Results
3.1 Obtaining the PLA
Employing the potato starch fermentation process as a substrate and using bacterium "Lactobacillus Delbreuckii Bulgaricus" as a fermenting medium for 15 days resulted in a dark yellow phase mixture and another with gelatinous consistency with the characteristic smell of ferment. Subsequently, undergoing distillation and controlled temperatures to recover lactic acid, which was later analyzed in the FTIR spectrum.
3.1.1 Iinfrared spectroscopy analysis FTIR of lactic acid
The FTIR spectrum of the synthesized lactic acid is shown in Fig. 5; The most important peaks are noted; the first is a peak with a signal at 3274.47 cm-1, a band belonging to the stretch of the OH bond and, also identified a signal at 1638.14 cm-1 which is assumed to be the stretch of the carbonyl group (C = O), so correct synthesis was verified.
3.1.2. Polymerization of lactic acid into polylactic acid (PLA)
To obtain polylactic acid, lactide dimer was first obtained, which was subsequently polymerized by ROP with ferrous chloride as catalyst and ethanol, resulting in a white polymer where excess alcohol was later eliminated, resulting in a gray-colored polymer. The resulting polymer underwent thermogravimetric tests and FTIR spectroscopy.
3.1.2.1 Analysis of polylactic acid by infrared spectroscopy FTIR
A synthesized polylactic acid analysis by FTIR was performed, in which some spectrum singularities were observed (see Fig. 6). A 1746.64 cm-1 signal is observed attributed to the carbonyl group stretching (C = O); two signals in 2990 and 2950 cm-1 attributed to the methyl group asymmetric stretching (- CH3) and at 1381.46 cm-1 a symmetrical deformation of this methyl group. Another important signal observed in this spectrum is at 1180.53 cm-1, belonging to the asymmetric stretch of the C-O bonds; concluding that the polymerization has been carried out effectively.
3.1.2.2. Thermogravimetric Analysis (TGA) of polylactic acid
Fig. 7 shows analysis performed on obtained PLA; we can observe that on a temperature of 213, 73 °C, weight loss of 98.18% begins, and at the process ends at around 500 °C, there is a remnant of 0.51% weight, leaving residues of 0.1884% (0.01884 mg) and this percentage is attributed to the unreacted catalyst.
3.2 Characterization and analysis of the PLA - PBSA dosages
As explained in the methodology section, various PLA and PBSA mixtures' analysis and characterization were performed using TGA, DSC, FTIR, MFI, Shore Hardness, and DMTA analysis.
3.2.1. TGA Analysis of PLA dosages - PBSA
The Table 5 summarizes the thermogravimetric analysis results on the mixtures PL-PB1 to PL - PB8 with specifications indicated in Table 2. The table shows weight loss temperatures and the percentage of waste that remains after the mixture's thermal degradation. Regarding PLA weight loss; As the temperature increases, weight loss decreases ascribing to the PLA; however, the percentage of residues increases since it is attributable to the catalyst that has not reacted.
3.2.2 Differential Scanning Calorimetric Analysis (DSC)
As explained in the methodology section, in the DSC analysis, three thermal treatments were performed on the samples at different temperatures: heating, cooling, and reheating to study and analyze the temperatures of fusion, glass transition, and crystallization. These parameters are evidenced in Tables 6, where a DSC summary analysis is presented for each sample.
Table 6 Main results of the Differential Scan Analysis (DSC) - First heating.
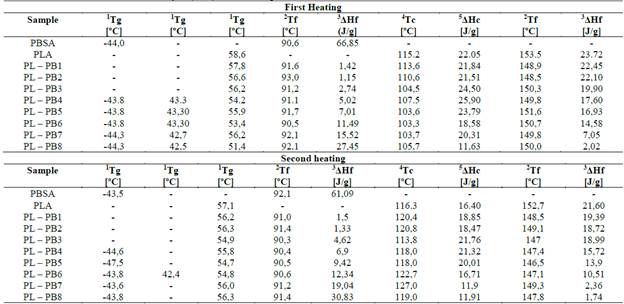
1Tg = transition initial temperature, 2Tf = melting peak temperature, 3AHf = fusion enthalpy, 4Tc = crystallization peak temperature, 5AHc = crystallization enthalpy
Source: The author
The tables show that adding low amounts of PSBA has high crystallization temperature (see Table 6); however, the crystallization enthalpies are somewhat dispersed, the PL-PB4 sample has a high enthalpy of crystallization and a temperature of 107.5 °C; this means that the addition of PBSA gives it a more significant crystalline character attributed to the fact that PBSA is semi-crystalline. Another important characteristic observed in the data obtained is that crystallization enthalpies, when cooled, are slightly lower than those from the first heating, which indicates that the PBSA in the mixture with the PLA does not crystallize effectively because the PLA being amorphous influences the crystallization of the mix. Furthermore, as the amount of PBSA in the mixture decreases, the fusion temperatures (Tf) in the first heating are slightly higher than the second heating; these characteristics may be attributed to the thermal properties of the PBSA (especially the melting point) are lower compared to the PLA
3.2.3. Flow Index Analysis (MFI)
Table 7 details the flow index results applied to the dosages PL - PB1 up to PL - PB8. The analysis compared to undosed polymers (extracted) PLA and PBSA (bionelle 3001); This procedure shows fluidity index of the samples have higher values (greater than 3.4 g/10min) than the undosed polymers; this is due to the dosages contained in crodamide VRX, which influences increasing the fluency index.
3.2.4. "Shore" hardness test
The Shore D hardness test showed that the samples are relatively rigid; this is shown in Table 8, where it can be seen that when the sample contains more significant amounts of PBSA, the hardness of the sample decreases, and this is because the PBSA is less rigid and therefore more elastic compared to PLA which is more rigid
Table 8 "Shore" D Hardness Analysis (ASTM D2240).
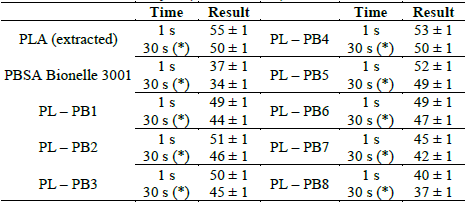
(*): The reading of the hardness value "Shore" D is repeated for 30 seconds of the permanence of the mass sample.
Source: The author.
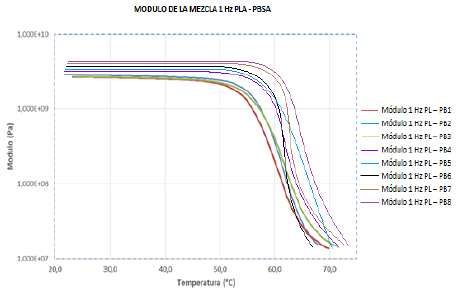
Source: The author.
Figure 8 Performance of modules E resulting from the temperature for IGB1, 2, and 3 mixtures obtained by DMTA.
Table 7 details the flow index results applied to the dosages PL - PB1 up to PL - PB8. The analysis compared to undosed polymers (extracted) PLA and PBSA (bionelle 3001); This procedure shows fluidity index of the samples have higher values (greater than 3.4 g/10min) than the undosed polymers; this is due to the dosages contained in crodamide VRX, which influences increasing the fluency index.
3.2.5. Thermo-Dynamic Mechanical Analysis (DMTA)
Fig. 8 shows the analysis DMTA of the dosages, which represent the hardness analysis "Shore" D. The following graph shows that as the PBSA increases in the mixture module E increases with temperature (see Fig. 8). This figure also shows that at temperatures above 50 ° C the samples PL - PB2 up to PL - PB8 are slightly higher than the PL-B1sample. In general, the PBSA increase is observed in the sample giving it a viscoelastic character; also observed that in temperature ranges of 50 and 60 ° C, a slope is mainly influenced by the decrease in PLA presence in the mixture
4 Discussion
In the dosing of a copolymer (PBSA) with a linear aliphatic polyester (PLA) carried out in this assignment, thermo-mechanical properties of said materials have been modified, especially in the PLA's crystallinity; we can see these properties are diminished due to the PBSA presence; considering that at a higher amount of PBSA the crystallinity decreases (see Table 8) and up to 50% of its initial value. In work carried out by Zuluaga [35], the polymerization process is controlled by the degree of crystallinity since the reaction parameters such as temperature, pressure, reaction time, and catalyst can be controlled, resulting in a polymer of different molecular weights. According to Migliaresi [36], PLA with lower molecular weights reaches almost constant crystallinity values , and, according to this author, the molecular weight is influenced by the presence of the isomers (L and D).
Perelló's work [37] assures that mechanical properties and crystallinity depend on molecular weight and indicates that semi-crystalline PLA has high rigidity. When contrasted with our study, it shows that it starts from a mixture with relatively high hardness, and as the amount of PBSA increases, the hardness decreases, so we can say that the mixture behaves in an amorphous way.
On the other hand, the biopolymer use can be analyzed from a fluidity index standpoint; Table 8 shows low values of this index are obtained, and according to Shea [38], polymers or materials with low fluidity index can be processed by extrusion and thermoforming. The fluidity index, being a rheological test, indicates that the fluidity of a polymeric material gives us the idea of the polymer structure. Sanchez [39] explains this index is related to molecular weight and length of the polymer chain and is dependent on the polymerization type carried out; in this sense, long-chain polymers will have high mechanical properties and need a significant amount of energy to be able to unwind and therefore, will be more resistant and vice versa; however, the fluidity index is inversely proportional to the chain length, that is, the shorter the chain length and low molecular weights will have higher melt index; for this reason, our study obtained a low melt index, assuming a polymer with a high molecular chain.
5 Conclusions
With the information obtained in this investigation, it is possible to have a clear vision of the effects of dosing PLA with PBSA, and the following conclusions were obtained:
Polymerization employing the ring-opening method (ROP) to get PLA is a good alternative since in this study, a 70% PLA was obtained, being a highly effective method; however, it is relatively expensive due to reaction time and acid costs.
The PLA shows stability up to 80 °C, and subsequently presents a degradation at a temperature higher than 214 °C; it has a weight loss of around 98% (see Fig. 8). This stability present in the sample influences the type of polymerization carried out; that being said, the PLA type (semi-crystalline or amorphous) obtained depends on the type of polymerization applied.
The dosage's thermal, rheological, and mechanical study shows that it has a proper fluidity and elasticity to be used in various industrial sectors. However, it also indicates that the addition of PBSA improves its mechanical and elastic characteristics and physically becomes less transparent; this is due to a crystalline phase's presence concerning the PLA that was initially amorphous. In addition to this, as the PBSA amount increases, the hardness decreases, not significantly; therefore, its flow index decreases (shown in Tables 8 and 9), so the presence of PBSA has a significant influence because it is crystalline.
According to the information obtained in this study, it does not imply that the PLA-PBSA mixture serves to carry out extrusion or thermoforming processes, and this due to its low fluidity index, so it cannot be inferred that formulation is appropriate. Still, in general, the mixture is useful for the mentioned processes