1. Introduction
Colombia is the fourth largest palm oil producer in the world (after Indonesia, Malaysia and Thailand) and the first in Latin America, reaching yields of 3.8 tons of crude oil per hectare as of 2017, for a total production of 1627462 tons [1]. In 2018, production showed a positive variation of 0.2%, compared to the previous year [2]. During the processing of oil palm (Elaeis guineensis) fruits, large quantities of biomass residues are generated among them bunches, mesocarp fiber and kernel shells (mesocarp), the latter in proportions of 0.1 - 0.4 tons/tons of crude oil [3]. Some studies have found that oil palm residues have considerable amounts of carbon, 43% to 51% of weight (%wt.), and fixed carbon, ranges from 30 to 39%wt., which categorizes them as materials with great potential to be converted into carbon-rich biochar [4].
Oil palm kernel shells are a high hardness material, composed of 49.8% lignin, 30.4% cellulose and 12.7% hemicellulose [5]. Elemental and proximate analysis shows that it is made up of 41.9% carbon, 5.4% hydrogen, <1% nitrogen and 40.5% oxygen. In addition, it contains 11.2% moisture, 79% volatiles, 1.4 ash, 30.9% fixed carbon and a calorific value of 22.5 MJ/kg [6]. In Colombia about 67% of the total kernel shells are used as fuel for boilers and the remaining, 33%, is used for charcoal generation, compost, among others. However, obtaining biotechnological products from biomass residues such as biochar, used to remediate and increase soil fertility [7-9], remove pollutants in water [10, 11], mitigate climate change [12], is a topic of global interest.
The biochar is a carbon-rich solid obtained through reductive thermal processing or pyrolysis of biomass from various sources [13], in the absence or low presence of oxygen. The pyrolysis process occurs in the temperature range of 400-1200 °C, although the product yield depends on various operating parameters, generally low temperatures and longer residence time (slow pyrolysis) favor char production [14]. In addition to biochar, volatile materials are generated in the process that can be further condensed in liquid phase (bio-oil) and the remaining so-called "non-condensable" synthesis gases, such as CO, CO2, CH4 and H2 [15], all contain exploitable energy potential.
The characteristics of biochar derived from palm kernel shells produced under slow pyrolysis conditions have been evaluated. Elemental and proximate analyses show that it consists of 48.6% carbon, 5.6% hydrogen and 38.7% oxygen [16]. In addition, it is made up of 30.3% volatile material, 7.6% ash and moisture content 2.3%. Also, it contains 73.1% fixed carbon and higher calorific value 27.5 MJ kg-1 [17].
Moreover, thermodynamic studies based on energy and exergy analysis are basic principles to determine the exergy-economic cost in the production of materials. For this purpose, the input fuel costs and capital expenditures must be contrasted to determine the unit costs of the product, being an essential activity to evaluate the performance, efficiency and establish the optimization of the process [18]. The use of methods such as the SPECO method proposed by Lazzaretto & Tsatsaronis (2006) [19], allows the calculation of losses occurring at the system level (input, output, raw material and by-product flows), and also facilitates the evaluation of the energy process, so that the full cost of biochar generation can be deduced.
There are studies that show technoeconomic and economic analysis of biochar production such as those developed by Shabangu & Lehmann (2014) [20], Campbell & Naughton (2018) [21], Sahoo & Mani (2019) [22] and Lee & Ng (2020) [23]. Likewise, Harsono and Mohd (2013) [24] carried out the energy and economic balance of biochar production based on oil palm residues. Recently, Heredia and Peralta (2018) [25], determined the thermo-economic cost of biochar production taking into account the exergy in the process. However, studies showing the exergy cost or cost of the useful energy required for biochar production are not known to the best of our knowledge. Based on the above, the objective of this research was to determine the exergy-economic cost of the production of biochar, made from palm kernel shell, under conditions of slow pyrolysis at experimental and pilot scale.
2. Materials and methods
This research was carried out in the department of Cesar, Colombia. For the development of this paper, it was necessary to apply the theories of analysis to an experimental system and a pilot system, thus establishing the main components for scaling, according to the requirements of the type of system. It is important to mention that the experimental equipment seeks to maximize with precision the biochar formation at a high cost of resources; in pilot equipment it is necessary to control the resources, even if the biochar formation yields are lowered.
2.1. Equipment description and operation
As shown in Fig. 1, the experimental self-fired furnace consists of a logic controller (b), which allows controlling the flow of electrical energy, establishing the heating ramps and verifying the internal temperature of the furnace by means of the thermocouple (f). This is followed by the horizontal heating furnace (c), internally insulated with fiberglass and asbestos, composed of 12 parallel resistors insulated with refractory ceramic; it also has a cylindrical reactor with a diameter of 0.06 m and a height of 0.7 m, with a volumetric capacity of 0.002 m3. The pyrolysis process is carried out in this reactor, initially by introducing the biomass material (oil palm kernel shell), then the flow of nitrogen from the nitrogen gas cylinder (a), which allows the formation of an inert atmosphere to generate an incomplete combustion process. Once the pyrolysis process is finished, the biochar is extracted directly from the reactor while the gases evacuate to the gas collector (d), where the condensation process takes place, then the non-condensable gases evacuate through a duct to the chimney (e). For the operation of the equipment an electrical voltage of 110 V is required.
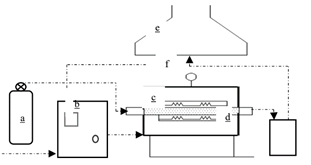
Source: Prepared by the authors.
Figure 1 Components of the experimental furnace. Experimental self-fired furnace. a) Nitrogen gas cylinder, b) Logic controller, c) Horizontal heating furnace, d) Gas collector, e) Chimney, and f) Thermocouple.
Fig. 2 shows the pilot furnace consisting of a junction box (b) which allows the distribution of electrical power. Next, there is the logic controller (c) and the vertical heating furnace (d). The latter is jacketed and thermally insulated with glass wool. It has a space reserved for the retort, where the three U-shaped heaters are installed, each with a power of 1.5 kW, connected in parallel, located on a refractory ceramic support. The retort, made of stainless steel (like the rest of the furnace), has a capacity for 150 kg of load and has the thermocouple (f) installed. Likewise, the thermal reactor is 0.2 m in diameter and 0.8 m in height, for a total volume of 0.03 cm3. It also has a tar collector (e) which has two functions, one is the TGA equipment and the other is the balance of tars, the collector has an input for tars coming from the furnace and an output for volatiles. The furnace can reach temperatures close to 873.2 K. The equipment requires an electrical voltage of 220 V.
2.2. Experimental tests
Five experimental tests were carried out for the production of biochar in each unit under slow pyrolysis conditions using oil palm kernel shells, which were previously dried at room temperature and with a particle size in the range of 0.15 - 200 mm. The operating conditions applied in each unit are shown in Table 1, these vary depending on the capacity and operation of the equipment.
Table 1 Operating conditions affecting internal and external variables.
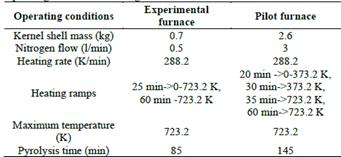
Source: Prepared by the authors.
On the other hand, the energy requirements to establish the temperature ramps in each equipment are different, because the temperature increase needs are also different, as shown in Figs. 3 and 4, in which it is shown that the controls are very efficient because they maintain the heating rate.

Source: Prepared by the authors.
Figure 3 Temperature ramps used in the experimental furnace. Heating ramp of the experimental furnace. Experimental.: Real heating ramp inside the furnace, Theorical R.: Programmed ramp.
Mass balance
The mass balance in each unit was carried out by applying Eq. 1, the inputs are given by the mass of the kernel shells (ṁC) and the mass of the nitrogen gas (ṁN2), while the outputs are represented by the mass of the biochar (ṁB), the mass of the condensable and non-condensable gases (ṁG) and the mass of the nitrogen gas (ṁN). ṁH2O corresponds to the mass of water contained in the kernel shells.
ṁC y ṁB were determined by gravimetry, the mass of the kernel shells introduced in each oven are shown in Table 1 ṁH2O was estimated by applying ASTM D 7582-15, ṁG was calculated by the difference between the masses of the shells, biochar and water. Meanwhile, ṁN2 was calculated by applying the ideal gas equation, taking into account that the gas is maintained at a pressure of 1.02 atm and at room temperature (301.2 K). Additionally, a thermogravimetric analysis (TGA) was performed on the shells and biochar, using a Q500 V6.7 Build 203 thermo-gravimetric analyzer.
2.4. Energy balance
The energy balance was performed by applying Eq. 2, where (
) is the electrical power supplied to each piece of equipment, (
) is the flow of energy transformed into heat that remains in the system. The energy coming out of the system is given by the fluxes of energies absorbed by biochar (
), condensable and non-condensable gases (
), nitrogen (
) and water
.
The furnace electrical power
is 0.5 kW during 1.4 hours. The pilot furnace requires an electrical potential of 3.4 kW, the equipment does not consume energy during internal temperature regulation, therefore, the actual electrical consumption time is 1.9 hours. Furthermore, the 𝜕Q/ 𝜕t corresponds to the heat change in the furnace chamber, corresponding to the sum of
,
,
and
; Eq. 3 was applied to calculate these values, where m is the mass flow of compound i, 𝐶 𝑃 is the specific heat of compound i, and ΔT is the temperature differential; additionally, the enthalpy of evaporation at 100 °C is added to the heat of water. The specific heat of each element was taken from a technical report made by the company TECSOL (2011) [26]. For determining
it was considered that nitrogen had a behavior of an ideal gas, taking into account that the gas enters the systems with a pressure of 15 psi.
In addition,
was calculated with the differential between the electrical energy supply and the sum of the energies absorbed by biochar, gases, water and nitrogen, as shown in Eq. 4.
Additionally, the energy efficiency (nw) in each furnace was calculated by applying Eq. 5. Taking into account that the energy absorbed by the shells (wC) is equal to the total sum of the flow of energy absorbed by the biochar and the gases (
), the equivalent of the amount of energy in the form of heat adsorbed by these (Q).
2.5.Exergy analysis
The exergy of the gases (EG) was calculated by applying Eq. 6, where w E is the energy of the gases and S0 is the initial entropy of the gases. The average entropy of the gases was determined by literature review using the Thermodynamics book by Cengel & Boles (2012) [27], taking into account that the process generates mainly CO2, CH4, CO, H2 and N2.
The exergy of biochar (E B ) was determined by Eq. 7.
The exergy efficiency (n E ) was obtained by applying Eq. 8.
2.6. Exergetic cost of biochar
The exegetical cost of biochar (C R ) is given by Eq. 9, where (C H ) is the technical cost of use, maintenance and operation of equipment, (w E ) the energy consumed by the equipment (C C ) the cost of acquisition of the kernel shells which includes the cost of transportation and purchase of the material, Q C l the energy of the kernel shells which was calculated by Eq. 3, taking into account that C P =1.4 kJ/kg.K, data obtained from [26], and that ΔT= 695.2 K.
The cost of electricity in the residential, industrial and governmental sectors was obtained using the average energy tariff in some Colombian departments, information provided by the Mining and Energy Planning Unit (UPME). The cost of the equipment and the nitrogen cylinder was consulted directly in the purchase invoices, after which the prices were projected using the average Colombian CPI. The cost of the kernel shells was determined taking into account that 1 ton of the material can cost between $15000 and $40000, values reported by Garcia et al. (2010), so an average was made and a projection was made at the current price.
3. Results and discussions
3.1. Mass balance
The resources and products of the pyrolysis process in each unit are shown in Table 2. In the experimental furnace, 32.8% of the kernel shells is converted into biochar, 9.1% into water vapor and 58.1% into gases and oils. On the other hand, in the pilot furnace, 44.6% of the kernel shells is converted into biochar, 9.1% into water vapor and 46.2% into gases and oils. From the foregoing, it can be deduced that the pyrolysis conditions in the pilot furnace favor the production of biochar and gas almost equally, unlike the experimental furnace where the production of biochar is much lower than that of the gases, with a differential of 25%.
3.2. TGA analysis of oil palm kernel shells
The TGA curve for palm kernel shells is shown in Fig. 5, which shows that there are four stages of decomposition or mass loss of the material at different temperature ranges. The first mass loss (9.4%) occurs in a temperature range of 25-175 °C, resulting from the reduction of moisture and the decomposition of a small part of hemicellulose in the form of light volatile material [17]. The second loss (24.1%) occurs between 200 - 300 °C, as a consequence of total decomposition of hemicellulose. Followed by this, 25.1% is lost between 300 - 400 °C which corresponds to the decomposition of cellulose and lignin, reaching the highest degradation at 342.3 °C. Between 400 to 600 °C, carbonization of the material occurs, producing Cx, CO, CO2 and H2 in the form of tars and non-condensable gases [28]. On the other hand, in the same figure it can be observed that at a temperature of 342.3°C the material reaches the maximum degradation rate equivalent to 3.8%.
3.3. TGA analysis of biochar
The thermogravimetric analysis of the biochar is shown in Fig. 6. Four stages of decomposition are observed, where small losses of mass are evidenced as a consequence of the loss of moisture and degradation of the labile carbon. The first loss (6.1%) occurs between 25-125 °C, the second loss (2.9%) occurs between 125- 275 °C, the third loss (3.5%) is generated between 275-350 °C and finally (11.1%) occurs between 350 - 600 °C. On the other hand, in the same figure three peaks are observed where the maximum degradation rates occur, the first occurs at a temperature of 256. 7 °C, the second at 338.2 °C and the third at 541.5 °C.
3.4. Energy balance
The resources, products and energy losses in the pyrolysis process of both systems are shown in Table 3. From this it can be concluded that the biochar generated in the experimental furnace and the pilot furnace retained 0.5 and 2.9% respectively of the total energy entering each system.
Using the information shown in Table 2, the electrical energy efficiency of both systems was calculated. In the experimental furnace the energy efficiency is 3.2%, while in the pilot furnace it is 14.6%, the above results show that the equipment is characterized by low energy efficiency, which indicates that there is a lot of energy loss possibly due to heat transfer to the external environment or due to the type of material that makes up the equipment. It is important to clarify that the efficiency calculated above does not correspond to the electrical energy transformed into heat, but to the overall energy efficiency of the system.
3.5.1 3.5.1. Exergy of the gases
In the experimental furnace, 0.04 kg of gases are produced, which contain 37.6 kJ of exergy, while in the pilot furnace the exergy content of 1.2 kg of gases is 1137.5 kJ.
3.5.2 Exergy of biochar
The exergy of biochar in the experimental furnace is equal to 29.5 kJ, while in the pilot furnace the exergy of biochar is equal to 1356.7 kJ.
3.5.3 3.5.3. Exergetic efficiency
According to the results obtained, the equipment has low exergetic efficiency; in the case of the experimental furnace, the exergetic efficiency is 2.5%, while in the pilot furnace it is 10.8%. The results indicate that the exergetic efficiency of the equipment is low. There is a high and significant loss of energy during its heating, in addition the gases acquire a large part of it, which can be of great benefit when trying to optimize the process with their recirculation.
3.5.4 3.5.4. Exergetic cost of biochar production
To determine the exergetic cost of biochar, it was necessary to know the prices of each piece of equipment and of the resources for pyrolysis. Table 4 contains the prices in Colombian pesos projected for the year 2020.
Below, Table 5 shows the cost of energy consumed by each piece of equipment during pyrolysis. This cost was determined in six departments of Colombia, taking into account three sectors: residential, industrial and governmental. In general, the cost of biochar is lower when it is produced in the industrial sector. However, in the departments of Cesar and Atlántico, the cost increases if it occurs in the governmental sector, while in the departments of Cundinamarca, Magdalena, Santander, and Risaralda, the cost increases in the residential sector.
In addition to the above, the technical costs related to the use, maintenance and operation of the experimental furnace and the pilot furnace during pyrolysis are $ 1400 and $ 2400 respectively. On the other hand, the cost of 0.02 and 0.3 kg of nitrogen required for pyrolysis in the experimental furnace and pilot furnace is $ 16755.5 and $ 32394 respectively. On the other hand, the cost of 0.07 and 2.6 kg of kernel shells is equivalent to $ 3.2 and $ 119.6 respectively. In addition, the energy in the form of heat absorbed by 0.02 and 0.25 kg of kernel shells during the transformation to biochar and gases in the experimental furnace and the pilot furnace is 69.2 and 2494.2 kJ, respectively.
Considering the previous results, it was determined that the exogenous economic cost of 0.02 kg of biochar produced in the department of Cesar, in an governmental area using the experimental furnace is 896.8 $ kJ/kJ; while the exogenous economic cost of 1.2 kg of biochar produced in the pilot furnace in the same place is 238.4 $kJ/kJ. In order to Table 6, shows the exergo economic cost of the production of 1 kg of biochar in both equipments. It can be seen that the exergy cost of biochar production varies depending on the place and sector where it is carried out, as well as the type of furnace. In this case, the production of biochar in the experimental kiln is more costly in exergy terms than in the pilot furnace.
4. Conclusions
Exergy studies are an essential tool to know the energy and exergy content of the resources and products of a thermal system process, as well as the operation and efficiency of the equipment. However, the mass content and the energy and exergy characteristics of pyrolysis products may vary depending on the operating conditions and the type of equipment used.
The excergoeconomic cost of biochar production varies according to the equipment, the operating conditions and the place where the process is carried out. The production cost biochar in the experimental furnace under slow pyrolysis conditions involves high energy consumption compared to larger scale processes. Therefore, it may be necessary to take advantage of the heat and energy contained in the gases, either through bioenergy production or heat recirculation.