Introducción
Ha sido estimado que no existirán suficientes productos forestales en el mercado para 2030, por lo que los esfuerzos se han centrado en el manejo eficiente, reúso de productos y desechos de lignocelulosa [1]. Una posibilidad de mejorar la economía circular es usar diferentes materiales de desecho y productos de diferentes sectores [2]; la ventaja de usar materiales reciclados no sólo ofrece un menor precio, sino que es más eco-efectivo que disponerlos [2]. Los residuos del corte de madera, han sido comúnmente tratados como desecho y existe un problema para su disposición. Actualmente las fibras recuperadas son utilizadas para producir productos de papel, material de construcción y bioplásticos [1]. Fibras como el cáñamo, yute y bambú han sido estudiados debido a sus propiedades mecánicas [3], así como abeto, pino, eucalipto, arce, haya y roble se incluyen generalmente como harinas embebidas en matrices poliméricas [4].
Los materiales compuestos son un material multifase que consiste de un material matriz con una fase de refuerzo, es decir, en el caso de los materiales WPC, generalmente se usa la madera como refuerzo en forma de harina [5], y fibras [1,2,6]. Los compositos madera plástico (WPC) son materiales amistosos ambientalmente debido a que la fuente del material puede ser materiales vírgenes o reciclados, que permiten reducir los costos de manufactura, energía y el consumo de materiales vírgenes [6]. Los materiales compuestos madera plástico, han sido utilizados en aplicaciones de exteriores como cubiertas, revestimientos y marcos de ventanas, donde el material está expuesto a la humedad, a las acciones de congelación-descongelación y a los rayos ultravioleta [6], así como en aplicaciones de interiores en partes de edificios que han mejorado sus propiedades en relación con materiales convencionales [7].
El uso de WPC ha crecido rápidamente debido al incremento en aplicaciones en la construcción, componentes automotrices, industria del mueble y diversos bienes industriales y del consumidor [1,3,8]. Tan solo en China el desarrollo de este mercado se ha triplicado entre 2010 y 2012 [2]; los materiales han atraído diferentes investigaciones debido a su bajo costo de producción, densidad del material y propiedades mecánicas apropiadas para aplicaciones generales, combinadas con su renovabilidad [9,10].
Previamente han sido desarrollados materiales WPC, elaborados a partir de mezclas de polietileno y polipropileno [11,12], fenol-formaldehído [5], polipropileno [13,14], polietileno de alta y baja densidad [15,20], policloruro de vinilo [21], policloruro de vinilo con quitosana [22], polietileno de alta densidad [23], polibutileno succinato [24], polihidroxialcanoato [8], y plástico reciclado [11]. Algunas de las ventajas asociadas con el uso de fibras naturales como refuerzo incluyen esfuerzo mecánico específico alto, propiedades aislantes térmicas, biodegradabilidad, compostabilidad [25], fácilmente disponibles a bajo costo [26], mientras que sus limitantes incluyen la incompatibilidad de las fibras con las matrices poliméricas [3], la tendencia a formar agregados durante el proceso, un alto contenido de grupos hidroxilo lo que favorece la absorción de humedad [27], composición compleja de polisacáridos [28], temperaturas de proceso limitadas y baja resistencia al fuego [3]. La incompatibilidad entre las fibras es debida principalmente a su naturaleza hidrofílica y por ende a la presencia de los grupos hidroxilo y otros grupos polares. Cuando estas fibras son combinadas con matrices poliméricas de naturaleza hidrofóbica, se produce una débil adhesión y delaminación [29].
El álamo (Populus spp) y sus híbridos han sido considerados como una alternativa de fuente de madera, debido a su rápida tasa de crecimiento y su fácil reproducción; representan una de las más abundantes especies en Norte América. Tan sólo en Canadá se estima que ocupan cerca del 50% de la superficie boscosa. Actualmente, la madera de álamo es utilizada principalmente como fibra para pulpa y en la industria de papel, sus productos ingenieriles se enfocan en aglomerado para construcción, madera de capas sujetas con adhesivos y materiales compuestos. Es un material compuesto que consiste principalmente de tres polímeros: celulosa, hemicelulosa y lignina [30].
La policaprolactona (PCL) fue uno de los primeros polímeros sintetizados por el grupo de Carothers en 1930. Se hizo comercialmente disponible debido a los esfuerzos por identificar polímeros sintéticos que pudieran ser degradados por microorganismos. La PCL puede ser preparada seguida de una polimerización por apertura del anillo; usando una variedad de catalizadores [31], tiene una temperatura de transición vítrea de -60 ºC y una temperatura de fusión de 60-70 ºC, con una tasa de biodegradación más lenta que otros polímeros biodegradables [32]. Los WPC son plásticos resistentes al ataque fúngico, no obstante, una de sus mayores problemáticas es que son muy susceptibles a degradación biológica, por este motivo, se evita su uso donde haya agua presente [4].
El objetivo de la presente investigación es obtener un material compuesto de PCL/harina de álamo para así evaluar su uso potencial como material para el diseño industrial, a partir de sus propiedades mecánicas, de degradación hidrolítica y por radiación ultravioleta.
Materiales y métodos
Para esta investigación se utilizó aserrín de madera obtenido por medio de un proceso de molido, para obtener una harina fina de madera. Se utilizó Policaprolactona de alta densidad (Sigma-Aldrich, 440744). La Policaprolactona fue molida, cribada con cedazo y se realizaron composiciones 80/20 y 75/25 harina de álamo/Policaprolactona. El tamaño promedio de las fibras o harina utilizado fue de 237,79 µm. Se tomaron 70 mediciones utilizando el software EM Wizard directamente en la micrografía y se obtuvo la media aritmética.
Las composiciones fueron sometidas a calor en un horno a 80 ºC durante una hora. Se utilizó un microscopio electrónico de barrido por emisión de campo JEOL JSM7000F para observar la estructura y porosidad de las muestras. Se utilizó un espectrofotómetro FTIR-ATR (Nicolet 6700) a 100 escaneos y una resolución de 16 cm- 1, en el cual fueron analizadas las muestras sin preparación previa. Se realizaron dos grupos de prueba, uno de ellos fue sometido a luz ultravioleta por 24 horas, y el otro grupo no. Ambos grupos fueron sometidos a degradación hidrolítica en una solución amortiguadora de fosfato en diferentes periodos de tiempo (1, 2, 3, 4, 5 y 6 semanas). Cada muestra fue sumergida en 5 mL de solución amortiguadora por triplicado. Una vez transcurrido el periodo de tiempo, las muestras eran extraídas y secadas en estufa de vacío a temperatura ambiente. La degradación fue calculada por comparación de peso antes y después de la prueba.
Posteriormente fue realizada la prueba de humedabilidad y retención de agua por triplicado a 1, 2, 3, 4 y 5 horas. Para esta prueba se utilizó agua destilada, en vasos de precipitados de 40 mL se añadió 5 mL de agua y se sumergió 1 trozo del compuesto previamente pesado por cada vaso. Se dejaron de 1 a 5 horas. Pesando cada hora la muestra, para calcular el nivel de absorción que este tuvo. A la par se hizo lo mismo con trozos de madera virgen para hacer un comparativo de la absorción entre la madera y nuestro compuesto Las muestras entonces eran pesadas, y se calculó la humedabilidad como un porcentaje del peso de las películas. La tasa de adsorción fue determinada por medio del método gravimétrico. Se realizó barrido de temperatura de -100 °C a 100 °C a 5 °C/cm en una geometría de flexión en tres puntos. El tamaño de las muestras fue de: 12,7 mm de ancho x 30 mm de largo x 3 mm de espesor. También se realizó la prueba de esfuerzo- deformación a 40 °C también de flexión en 3 puntos. Como método para generar la propuesta de diseño se utilizó la metodología de Karana [33], orientado por materiales para la generación de esta propuesta de valor aprovechando las propiedades.
Resultados
Se puede considerar que la absorción de agua es uno de los principales parámetros dimensionales de la inestabilidad de un WPC, debido a las características hidrofílicas y a las partículas de harina de madera ricas en grupos -OH [24]. Esta absorción de agua es atribuida tanto a la porosidad de las muestras como a la humedad que puede ser captada por las partículas de madera. En la Figura 1, se puede apreciar, que los materiales compuestos mostraron uniformidad en la matriz, en la que no resultaron visibles las partículas de madera, y se pudo apreciar escasa porosidad. Esto resultó similar tanto para las muestras 75/25 (Figura 1a), como para las 80/20 (Figura 1b).
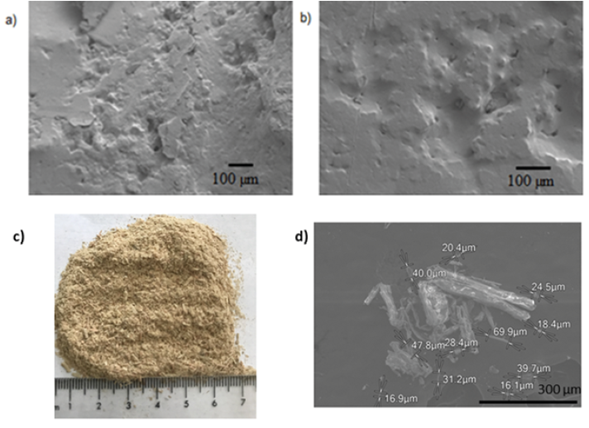
Figura 1 Micrografías de SEM de a) 75/25, b) 80/20 policaprolactona/harina de álamo, c) fotografía de harina de álamo y d) micrografía de la harina de álamo.
La Figura 2 muestra las vibraciones de los grupos OH correspondientes a las partículas de madera alrededor de 3350 cm- 1 [34]. El enlace asimétrico de estiramiento CH2 de la policaprolactona fue encontrado en 2943 cm- 1, en 1728 cm- 1 se encontró el estiramiento carbonilo, en 1237 cm- 1 el enlace de estiramiento O-C-O [35]. De acuerdo con lo observado, los resultados sugieren interacción del grupo carbonilo de la PCL y el enlace de estiramiento O-C-O con los grupos OH de la madera.
De acuerdo con el análisis realizado en las pruebas de biodegradación (Figura 3ay3b), se pudo observar que el material sufre una degradación en su peso mínima, de menos del 0,05 % a seis semanas, tanto con las muestras expuestas a radiación (Figura 3a), como las que no fueron sometidas a este tratamiento (Figura 3b).
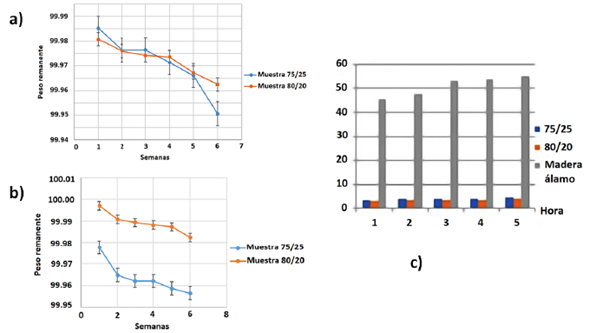
Figura 3 a) Muestras 75/25 y 80/20 harina de álamo/policaprolactona expuestas a 24 horas de luz UV y b) muestras 75/25 y 80/20 sin tratamiento de radiación, sujetas a degradación hidrolítica por 6 semanas y c) porcentaje de humedad captada por las muestras de madera de álamo y las composiciones 80/20 y 75/25 harina de álamo/Policaprolactona.
Esto puede ser atribuido a las características hidrofóbicas de la policaprolactona que son aprovechadas en la elaboración del WPC [36]. Esta prueba se realizó para comparar el efecto de la luz UV sobre los WPC en relación con su degradación hidrolítica, y los resultados mostraron que los materiales compuestos sufren una degradación mínima, a pesar de que las muestras fueron sometidas a 24 horas de radiación UV. Este tiempo es muy superior al utilizado en otros experimentos en donde el tiempo es menor a 1 hora [32].
Para determinar la durabilidad del material compuesto la capacidad de absorción de agua, es un parámetro indispensable, debido a que la humedad causa fallas interfaciales en las partículas de madera [37]. Esta capacidad de absorción es un resultado de la porosidad de superficie y la absorción de las partículas de madera principalmente en este material, debido a que la Policaprolactona es un material con una hidrofobicidad elevada [38]. Fue corroborado por medio de las micrografías de SEM (Figura 1ay1b), que el material compuesto no muestra una porosidad significativa, lo que favorece la no captación de humedad.
Los bajos porcentajes de captación de agua de las muestras, comparados con las muestras de madera, así como la saturación de humedad que se puede apreciar en la tendencia mostrada a lo largo del tiempo de prueba (Figura 3c), permite sugerir que el material compuesto sólo permite captar un porcentaje menor al 5 % del peso del material compuesto, lo que implica que las fibras de madera no pueden captar humedad debido a la protección de la matriz polimérica. Es importante destacar que, en otros estudios, esta tendencia de estabilidad de absorción de humedad, se presenta en periodos más largos de tiempo, como 90 días [24]. Es importante señalar que el tipo de comportamiento mostrado, indica la hidrofobicidad de la muestra. La humedad de las muestras pudo ser adquirida a través de los grupos OH de la muestra, los huecos entre la matriz polimérica y la harina de madera, el volumen libre de polímero o los huecos generados por la misma humedad [24]. Esto permite verificar que la Policaprolactona mejora las propiedades del compuesto ya que los resultados muestran que las moléculas de agua, no son tan atraídas por el material, como por otras fibras previamente utilizadas [8]. Esto contrasta con la hidrofilicidad de las fibras naturales que generalmente provocan una alta absorción que causa una adhesión débil y una rugosidad de superficie no adecuada en condiciones de humedad [3]. En esencia, ha sido considerado que el proceso de absorción de agua en la madera está relacionado con el rompimiento y reorganización de los componentes lignocelulósicos de la madera, lo que permite la interacción de sus enlaces hidrógeno con los grupos hidroxilos [24,39].
El análisis de flexión es comúnmente desarrollado para medir el módulo y esfuerzo de flexión de todo tipo de materiales y productos. Este tipo de prueba permite medir el esfuerzo de flexión y el módulo de flexión para compuestos, plásticos, cerámicos y concreto [40]. La Figura 4 muestra las curvas esfuerzo-deformación para los materiales compuestos. El módulo de Young obtenido en las muestras es significativamente mayor al reportado por otros autores, como Tiwari et al.[35], cuyo rango oscila de 22 a 38 MPa para nanofibras y los reportados por Esmaeilzadeh et al.[41], para nanocompuestos de 38 MPa a 94 MPa. A diferencia de otro tipo de materiales compuestos, en las muestras no ocurre fluctuación de esfuerzo antes de alcanzar el máximo valor [42]. Después de alcanzar el esfuerzo máximo las curvas caen, e inmediatamente después las muestran arrojan un ligero comportamiento plástico antes de romperse, presentando un esfuerzo de flexión de 1,02 MPa y 1,902 MPa para las muestras 80/20 y 75/25 respectivamente. Este comportamiento puede proceder de las interacciones químicas débiles que ocurren entre los materiales que componen la muestra. No obstante, esta información sugiere que las propiedades mecánicas de las muestras mejora con el aumento de la proporción de Policaprolactona en la muestra.
Con respecto al barrido de temperatura para las muestras, en ambos casos se encontró una conducta similar, especificando que en la muestra 75/25 dio como resultado Tm = 52,02 ºC, y en la muestra 80/20 tenemos una Tm = 63,07 ºC, lo que sugiere que la interacción con la harina de madera aumenta la temperatura de fusión del material compuesto (Figura 5). Esto coincide con lo reportado previamente, en donde se había reportado que el Tm para la Policaprolactona se encontraba alrededor de 52 ºC [43]. Estos son resultados positivos con temperaturas de proceso, ya que otras investigaciones han encontrado temperaturas de fusión de este tipo de materiales arriba de 140 ºC [44].
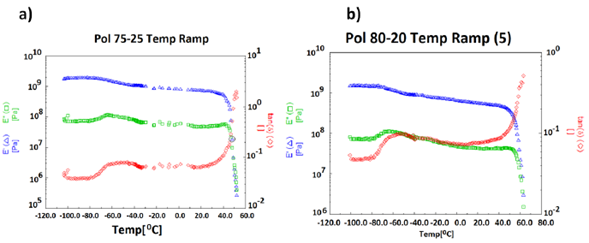
Figura 5 Barrido de temperatura para las muestras a) 75/25 y b) 80/20 Policaprolactona/harina de álamo.
De acuerdo con las propiedades del material, se realizó una propuesta de valor enfocada a los sanitarios de un hogar. Esta propuesta se basa en las tendencias de diseño expuestas en la feria de diseño ISH 2019, en la cual se expuso el uso de materiales alternos y sustentables en el diseño de sanitarios. La propuesta de valor tiene como mercado meta a familias de 2 a 6 personas que cuenten con un sanitario y tengan como necesidad el ahorro de espacio en el sanitario. El producto, cuenta con un cajón y una repisa inferior para el posicionamiento de los artículos que usan diariamente en los sanitarios. Finalmente, esta propuesta de valor fue generada en el software Rhinoceros 4.1 y se renderizó de forma visual en Autodesk 3DS Max versión 2018 (Figura 6).
Conclusiones y/o recomendaciones
Durante la presente investigación fue desarrollado exitosamente un material compuesto madera- plástico, con características de hidrofobicidad que no limitan su uso en ambientes húmedos. De igual manera, las propiedades mecánicas mostradas por los materiales compuestos permiten identificarlos con gran potencial para su uso en desarrollo de productos. Los autores hemos propuesto una posible aplicación del mismo, que esperamos pueda ser útil para apreciar las ventajas del material compuesto.