Introdução
No Brasil, o crescimento da população, e o aumento do consumo de materiais poliméricos e do agronegócio são índices vinculados com o desenvolvimento económico. No entanto, a geração de resíduos cresce paralelamente a ritmo acelerado, e as políticas de adequação e reaproveitamento ainda são tímidas, gerando a consequência, sérios problemas ambientais. O açaí (Euterpe olerácea) é uma espécie típica da região da várzea amazônica, e seu fruto, é popularmente consumido na forma de suco por possuir grande valor energético, alta concentração de fibra alimentar e excelentes propriedades antioxidantes [1]. No estado do Pará, principal produtor nacional da fruta, a produção entre os anos de 2015 e 2018 aumentou em 43,80%, atingindo-se 1 430 239 toneladas [2]. Por outro lado, o consumo da polpa e derivados chegou, em 2018 ao valor de mercado de R$ 84 619 780,83 através da exportação somente para os Estados Unidos (principal consumidor). Considerando que, 85% p do fruto é a biomassa residual, observa- se que paralelo à produção da polpa tem-se a produção massiva do resíduo biológico. A fibra de açaí, que recobre o caroço tem cerca de 80 µm de diâmetro e comprimento de 20 mm. Possui uma composição de lignina de 33% p (similar à que possui a fibra de coco), igual quantidade de celulose (33% p), 37% de hemicelulose, 7% de material solúvel em água e 1% de material solúvel em solventes orgânicos [3]. O uso das fibras do caroço do açaí, como material de reforço tem apresentado bons resultados, visto que fatores como baixa densidade, natureza não-abrasiva, baixo consumo de energia, biodegradabilidade e menor impacto ambiental tem incentivado cada vez mais a sua aplicação em diversas áreas. Rowell et al. [4] e Lima Junior [5] concluíram que as fibras de açaí incrementam de forma satisfatória a resistência à tração em compósitos de cimentos Portland. Também, com o aumento do teor da fibra no compósito, a absorção da água também aumenta, o que impacta positivamente as propriedades de biodegradabilidade.
A lignina é uma macromolécula proveniente do tratamento físico-químico da biomassa lignocelulósica. Esta constituída por compostos alifáticos e aromáticos. Sua estrutura é amorfa, com grupos funcionais que lhe atribuem propriedades hidrofílicas e hidrofóbicas ao mesmo tempo. Este componente comunica propriedades recalcitrantes nas plantas. A lignina é reconhecida, atualmente como um biopolímero com alta estabilidade térmica, biodegradabilidade, poder antioxidante e rigidez. Tradicionalmente usada como fonte geradora de energia, nas usinas de produção de etanol, estudos recentes visualizam o potencial desta fibra como reforço de polímeros. Menezes [6] concluiu que a lignina é adequada para substituir parcialmente o fenol, oriundo do petróleo nas resinas fenólicas. A resina alternativa mostrou altos valores de módulo de armazenamento quando comparada com a resina padrão e ainda, requer menor tempo de cura. Tortola et al. [7], Janković et al. [8] e Kai et al. [9] demonstraram que a lignina pura assim como seus compósitos com hidroxipatita e PLA respectivamente, possuem boa compatibilidade tanto em cultivos de células animais como em células troco humanas. Propriedades como estas, permitem projetar os scaffolds de formas complexas facilitando a integração do tecido vivo com a peça e o crescimento das novas células. Kai et al. [9] estabeleceram uma metodologia de síntese do copolímero PLA/Lignina (Kraft), via abertura do anel do lactide, onde as cadeias aromáticas da lignina foram enxertadas nas extremidades e no centro da estrutura principal do PLA em crescimento. Desta forma, os autores encontraram que além de incrementar as propriedades mecânicas do PLA, a lignina ainda comunicou poder antioxidante ao produto final. Poteau et al.[10], Azadfar et al.[11], Morandim - Giannetti et al. [12] e Domenek et al.[13] estudaram, respectivamente o poder antioxidante de ligninas extraídas de diversas fontes (como palhas de trigo e aveia) sobre o polipropileno. Os autores demonstraram que os componentes fenólicos da lignina eram os responsáveis da atividade antioxidante dos polímeros.
Os polímeros de PMMA e PLA destacam-se como biomateriais, por suas propriedades de biodegradabilidade, biocompatibilidade em meio biológico e pela absorção. A rota clássica de síntese exige agitação contínua dos reagentes em solução orgânica, em um reator batch e controle restrito da temperatura do processo com o tempo [14,15].
A introdução de fibras na matriz do polímero duro e quebradiço podem melhorar a biodegradabilidade, a estabilidade térmica e a reciclabilidade [16-19]. Durante a construção de um compósito a adesão interfacial entre a fibra e a matriz polimérica é fundamental para se conseguir propriedades melhoradas com respeito aos constituintes individuais. Considerando que, parte do esforço aplicado será transferido desde a matriz para a fase dispersa, para conseguir propriedades mecânicas altas, a adesão interfacial também deve ser alta [19]. A adesão interfacial pode ser promovida através da adição de agentes compatibilizantes no conjunto, como os óleos vegetais. Estas substâncias, além de serem ambientalmente amigáveis apresentam ésteres de trigliceróis, os quais têm afinidades pelos polímeros e pelos grupos hidroxilas e fenólicos presentes nas fibras. Em um estudo de Oliveira [20], sobre compósitos de Biopolietileno de alta densidade (BPEAD), reforçados com fibras de carauá foi concluído que os compósitos preparados com óleo de mamona (CO - ácido ricinoléico) apresentaram maior resistência ao impacto para uma composição de BPEAD/15 % CO/15 % fibra. Isto, porque a presencia do óleo viabilizou as interações entre os grupos -OH, assim como a interação dos grupos apolares presentes no polímero e no óleo. De acordo com Huang e Zhang [21], compósitos poliméricos com fibra de madeira requerem de compatibilização, visto que a falta deste reduz as propriedades mecânicas do material, pela formação de aglomerados. Por outro lado, Poletto et al.[22] registraram que a adição de 2% de óleo natural, em compósitos de polipropileno reciclado, reforçados com madeira produz uma melhora nas propriedades térmicas e mecânicas do produto, comparáveis com aqueles compósitos onde foi utilizado 2% de anidrido maleico como compatibilizante.
Adicionalmente à compatibilização, o tratamento da fibra com solução aquosa de hidróxido de sódio (NaOH) é reconhecido como um método simples e barato de pré-tratamento para obter propriedades melhoradas do compósito final. A função principal deste pré-tratamento é uniformizar a superfície da fibra devido à eliminação de microvazios. Desta forma, a capacidade de transferência de tensão entre as células melhora, porque a razão de aspecto aumenta, fazendo que a área da superfície da fibra aumente. Comportamentos térmicos e mecânicos dos compósitos foram melhorados significativamente com o tratamento da fibra com 5% de NaOH [23,24].
Neste trabalho foi considerado o ácido ricinoléico para promover a compatibilização entre a fibra do caroço do açaí e da lignina do bagaço de cana- de-açúcar com os polímeros de PLA e PMMA. Também, foi realizado o tratamento químico com 5% NaOH sobre a fibra de açaí, para promover a adesão interfacial durante a construção das membranas via moldagem por solução. Propriedades físicas e mecânicas como absorção de água dos compósitos e módulo de Young permitiram avaliar e apontar futuras aplicações dos materiais construídos.
Metodologia experimental Materiais e métodos preparativos
A Tabela 1 resume as características principais dos materiais utilizados para a construção das membranas. O PMMA-56 (nome fantasia) foi sintetizado pelo próprio autor no Laboratório de Otimização, Projeto e Controle Avançado (LOPCA) da Faculdade de Engenharia Química da Universidade Estadual de Campinas (FEQ/ UNICAMP), como descrito em [14,25]. Para a construção das membranas, o polímero foi seco e triturado até um tamanho de 500 μm. O PLA2003D (designação do fabricante), em pellet foi seco em estufa convencional durante 2 h a 90 °C antes do uso. A lignina do bagaço de cana-de-açúcar foi fornecida pelo Laboratório Nacional de Bio- renováveis do Centro Nacional de Pesquisa em Energia e Materiais LNBr/CNPEM, também, antes do uso, foi seca a 105 °C por 24 h. A biomassa residual do açaí foi fornecida por um produtor da localidade de São Luis do Maranhão-Brasil e, no Laboratório de Materiais Engenharia de Processos da Universidade Federal do Maranhão (LaMEP/ UFMA), foi realizado o processo de limpeza e purificação de acordo com o método registrado em Lima Junior [5]. Posteriormente, foi realizada a retirada manual das fibras do caroço e, na sequência, foram lavadas em água fervente por 15 a 30 min para retirar os açúcares e impurezas residuais, e secas a 105 °C por 24 h. As fibras secas passaram por uma etapa de moenda e classificação de tamanho, em peneiras padronizadas. A Figura 1 apresenta, respectivamente os caroços lavados e secos e a fibra purificada e seca. Paralelamente, parte da fibra, lavada e seca foi submetida a pré- tratamento alcalino com NaOH, de acordo com o procedimento relatado em Gehlen [26]. Assim, as fibras foram submersas na solução alcalina (5% p NaOH) na proporção 7,5:1 (g/L) durante 24 h, e depois foram lavadas e secas. O óleo de rícino, o NaOH e o clorofórmio foram usados como fornecidos.
Tabela 1 Materiais utilizados para a construção das membranas poliméricas
Material | Fonte | Características |
---|---|---|
PMMA-56 | Fabricação própria LOPCA/ FEQ/UNICAMP | Polímero triturado; Diâmetro médio 500 μm Mw ? 214 000; P 1,5; IV 0,46 dl/g. |
PLA2003D | NatureWorks | Biopolímero usado para embalagem de alimentos. Mw = 200.000 g/mol, Mn = 155.000 g/mol, Tf = 210 °C e Tg = 55 e 58 °C, Conteúdo do isómero D = 3,5%, Índice de Fluidez = 2,9 g/10min. |
Lignina do bagaço de cana-de-açúcar | Fornecida pelo LNBr/ CNPEM | Resíduo da hidrólise ácida e deslignificação alcalina do bagaço de cana-de-açúcar. Diâmetro médio 40 μm (MESH 325/400) |
Fibra do caroço de açaí (in natura) | Extração própria (LaMEP/CCET/UFMA) | Fibra natural extraída mecanicamente do caroço do fruto de açaí (Euterpe olerácea). Diâmetro médio 460 μm (MESH 35/40) |
Fibra do caroço de açaí (pré-tratada) | Extração própria (LaMEP/CCET/UFMA) | Fibra pré-tratada com solução 5% NaOH. Diâmetro médio 460 μm (MESH 35/40) |
Óleo de rícino | Farmax 100 % | ID 12223, contém 70 - 77% dos triglicerídeos do ácido ricinoléico. |
Clorofórmio | Isofar | Pureza 99,8 %; PM 119,38 |
Hidróxido de sódio (NaOH) | Merck | Pureza 99% PA, em lentilhas 99% |
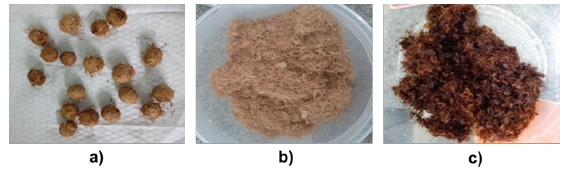
Figura 1 Biomassa extraída do despolpamento do fruto do açaí; a) Caroço com fibra purificada e seca; b) Fibra lavada e seca retirada manualmente do caroço; c) Fibras de açaí após tratamento com NaOH.
Preparação das membranas dos compósitos poliméricos com a biomassa lignocelulósica As membranas foram construídas pelo método de moldagem por solução (solvent casting) em clorofórmio. As soluções foram preparadas em três estágios: inicialmente, foi solubilizado o polímero em 50 mL de clorofórmio durante 24 h, seguidamente, foi adicionado o compatibilizante e deixado em repouso durante mais 24 h, finalmente, a fibra foi adicionada à mistura e aguardado integração por mais 24 h, sob agitação magnética. Após a solubilização, a mistura foi despejada em placas de vidro petri de 90x15 mm para facilitar a evaporação do solvente (vide Figura 2).
Os intervalos de composição de polímero, biomassa e compatibilizante estudados foram definidos a partir de estúdios anteriores do próprio autor [27], e considerando os resultados registrados em Oliveira [20]. A Tabela 2 resume as grandezas inicialmente exploradas para a preparação das membranas.
O número de corpos de prova para a avaliação da influência dos fatores: Composição de polímero, composição da fibra e composição de compatibilizante, sobre as variáveis resposta (propriedades físico-química e mecânicas dos compósitos) foram definidos com base em planejamentos fatoriais fracionários e completos com ponto central [28]. Um total de quatro planejamentos foram realizados para esta tarefa, sendo dois para o conjunto PMMA/ lignina/Compatibilizante e PMMA/Fibra de açaí/ compatibilizante, e dois para o conjunto PLA/ lignina/compatibilizante e PLA/Fibra de açaí/ compatibilizante como registrados nas Tabelas A.1 a A.4 do Anexo A. A avaliação estatística foi realizada com o auxílio do software Statistica 7.0.
Tabela 2 Intervalo de composição dos componentes utilizados para a preparação das membranas poliméricas.
Componente | Intervalo de composição (% p/v)* |
---|---|
Polímero PLA2003D | 8 - 12 |
Polímero PMMA-56 | 8 - 12 |
Fibra de açaí in natura | 2 - 3 |
Fibra de açaí pré-tratada | 2 - 3 |
Lignina | 1 - 5 |
Compatibilizante (óleo de rícino) | 5 - 20 |
Caracterização físico-química e mecânica das membranas construídas
Analise de absorção de água dos compósitos. Os ensaios de absorção foram realizados de acordo com a norma ASTM D5229 [29]. O procedimento para a coleta de dados consistiu de duas etapas: Na etapa 1, as amostras foram submetidas a processo de secagem a 55 °C durante 53 h continuas, controlado pela mudança de massa, até se atingir um equilíbrio ou saturação de 0,020 %. Posteriormente, foram tomadas as dimensões das amostras e na sequência, guardadas em um dessecador antes de iniciar o processo de absorção. Na etapa 2, as amostras, já secas foram colocadas em contado com o ambiente úmido (câmera de vapor), a temperaturas entre (22 - 24) °C, durante três semanas, e foi monitorado o ganho de massa até o equilíbrio (0,020%).
A partir da Equação 1 foi calculada a porcentagem de absorção de água a cada intervalo de tempo
Onde Wi é massa da amostra no tempo i e Wb é a massa de referência da amostra, isto é, aquela determinada após o processo inicial de secagem.
Avaliação Mecânica. Ensaio de tração. Os ensaios foram realizados em uma máquina universal de ensaios marca BIOPDI II, modelo coluna dupla de bancada-100kN, pertencente ao Laboratório de caracterização de materiais do curso de Design/UFMA. Para a construção dos corpos de prova foi seguido o protocolo indicado na norma ISO 527-5 [30] e BS ISSO 527-3 [31], usando a célula de força de 2000 kgf e uma taxa de 5 mm/min. Dados coletados de força aplicada versus posição permitiram calcular o modulo de Young, deformação e ductilidade do material (% Alongamento). A Figura 2 apresenta, na sequencia os estágios de preparação das membranas e construção dos corpos de prova para a realização dos ensaios de tração.
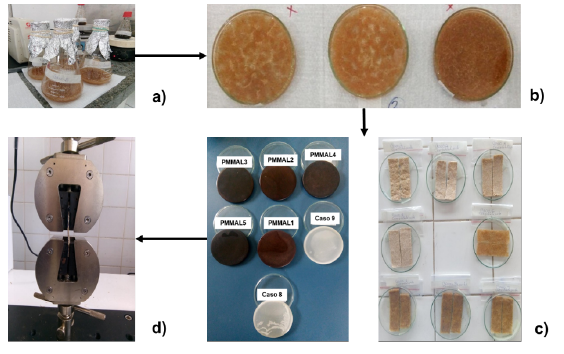
Figura 2 Estágios de preparação, construção e análise mecânica das membranas poliméricas reforçadas com fibras. a) Dissolução dos componentes, b) Moldagem, c) Membranas e corpos de prova, d) Ensaio de tração.
Microscopia eletrônica de varredura (MEV). A distribuição da carga de biomassa (fibra ou lignina) na matriz polimérica, na região da ruptura foi visualizada nas amostras submetidas aos ensaios de resistência à tração. As amostras foram fixadas em stubs com auxílio de fita, e metalizadas na superfície com ouro-paládio. Seguidamente foram visualizadas no microscópio eletrônico de varredura, Modelo TM 3030 da Marca Hitachi, pertencente ao laboratório de Materiais Dentários/ Programa de Pós-Graduação em Odontologia (UFMA).
Resultados e Discussão
Caracterização mecânicas dos materiais Membranas PMMA/Lignina do bagaço de cana- de-açúcar/compatibilizante
Para estas membranas, os fatores variaram em concentrações de 8 a 12% p/v para o PMMA-56, de 1 a 5% p/v para a lignina e de 5 a 10% p/v para o Óleo de Rícino. A matriz de planejamento resultou em 5 casos, identificados na Tabela A.1 do Anexo A. Também, no final da tabela são listados mais 5 casos tomados de referência, onde a membrana é constituída somente de polímero e compatibilizante.
A partir da análise estatística foi possível constatar que somente a composição de lignina e de polímero tem influência significativa nos valores de módulo de Young, (para um nível de confiança de 92%). Observou-se que um aumento na composição de lignina no compósito diminuía o módulo de Young (efeito negativo), no entanto, um aumento na composição de polímero, aumenta o módulo de Young do compósito (efeito positivo). No caso da composição de compatibilizante, o efeito isolado deste fator não teve nenhuma influência significativa, na faixa de composição estudada. Considerando estes resultados, foi gerado o Gráfico de Superfície de resposta para uma composição constante de 5% p/v de compatibilizante (vide Anexo B.1), onde pôde-se verificar que a composição ótima do compósito, com o qual se atinge o maior módulo de Young, foi aquela constituída por 9 a 12% p/v de PMMA, e 1 a 2,5% p/v de Lignina.
A Figura 3, apresenta as variações do comportamento do módulo de Young com as composições dos componentes. O melhor caso corresponde a PMMAL2, com a maior composição de PMMA e mínima composição de lignina e compatibilizante, por outro lado, o pior caso foi para PMMAL3 com menor concentração de PMMA e compatibilizante, e maior concentração de lignina. Este comportamento pode ser atribuído aos seguintes eventos: a) À matriz polimérica possuir maior rigidez e elasticidade do que a fase dispersa, desta forma, uma formulação com maior composição do polímero sempre resultará em altos valores de módulo de Young. b) Descontinuidades da face dispersa na matriz, o que diminui a transferência do esforço aplicado, reduzindo a tensão máxima suportada. Estas descontinuidades podem ser atribuídas à orientação das fibras, onde, em fibras curtas, é impossível de se prever, como apontado em De Lemos e Martins [32]. c) Ao limiar de composição PMMA/Lignina, visto que, o gráfico de superfície de resposta revelou que a composição útil da lignina está limitada a 1% no compósito; acima deste valor, o Módulo de Young diminuiu fortemente e, esta queda, foi amenizada pelo aumento do PMMA e compatibilizante.
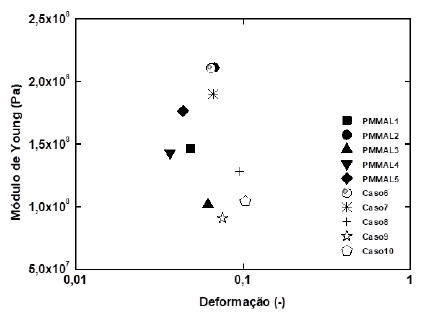
Figura 3 Variação do módulo de Young com a composição de lignina e compatibilizante, nas membranas de PMMA/Lignina/compatibilizante.
É altamente provável que existam fenômenos interfaciais (concorrência) gerados pela natureza destes componentes, visto que ambos, o PMMA e a Lignina são altamente elásticos e duros. Quando a tensão é aplicada, é de se esperar que a carga seja transferida para as regiões mais próximas da superfície e continue até a matriz e interface lignina/polímero, no entanto, o que os resultados mostraram indicou que quando a lignina supera o 1% p/v, a transferência de carga até a matriz não sucede completamente, assim, a resistência da membrana é definida em função da contribuição que a lignina comunica ao conjunto. Com respeito à ductilidade das membranas, todos os casos sem lignina mostraram uma maior deformação na ruptura. Por outro lado, aqueles casos com a lignina apresentaram maior modulo de Young (PMMAL2 versus o Caso 7; PMMAL4 versus Caso 9; PMMAL5 versus Caso 10), o que demostra o poder de rigidez deste material no polímero.
Membranas de PMMA/Fibra de açaí/ compatibilizante. A Tabela A.2 (do anexo A) registra as composições das membranas construídas para o estudo das variáveis resposta. Considerando que, as variáveis mais significativas sobre a resposta continuaram sendo as composições de polímero e da fibra, para a determinação da composição ótima da fibra na membrana, a concentração de compatibilizante foi fixada em 5% p/v, e com auxílio do gráfico de superfície de resposta (vide Anexo B.2 a) e b)) foram definidos os valores de 10 a 12% p/v de PMMA e de 2 a 3,4% p/v de Fibra de açaí in natura para as membranas PMMA /fibra de açaí in natura/ compatibilizante. Por outro lado, as composições de 9,5 a 12% p/v de PMMA e 2 a 3,0% p/v de Fibra de açaí pré-tratada foram definidas para as membranas de PMMA/fibra de açaí pré-tratada/ compatibilizante.
A seguir, a Figura 4 mostra a variação do módulo de Young em função da deformação, observando- se que os valores mais altos de módulo de Young foram obtidos para as membranas reforçadas com as fibras pré-tratadas. Pode-se destacar a membrana 1PMMAa1, constituída por 8% p/v de PMMA-56, 2% p/v de Fibra de açaí pré-tratada e 5% de compatibilizante. Em compensação o pior caso foi a membrana 5PMMAb5 constituída por 10% PMMA-56, 3% fibra de açaí in natura e 7,5% compatibilizante.
Analisando o efeito do compatibilizante, pode- se observar que o módulo de Young decresce nos casos superiores a 5% (Casos 1PMMAa1, 4PMMAa4, 5PMMAa5, 1PMMAb1, 4PMMAb4, 5PMMAb5), este comportamento foi previsto pela análise estatística, através da qual pôde- se definir uma composição máxima de 5%. O compatibilizante diminui a tensão interfacial e aumenta a adesão formando micro-pontes entre as faces, no entanto esta função irá depender da quantidade adicionada à mistura [33].
Ao comparar o efeito do pré-tratamento da fibra sobre a resistência final do compósito, os resultados não permitiram delinear uma tendência definida, toda vez que, tanto para os casos constituídos pelas fibras in natura e pré-tratadas foram obtidos valores médios e baixos do módulo de Young, e deformação máxima de 10%. Como já apontado previamente em [26,32,34], o tratamento da fibra com soluções alcalinas de NaOH elimina as impurezas, reduz os microvazios tornando as fibras mais uniformes e rugosas, o que aumenta a aderência com a matriz. No entanto, este tratamento reduz a quantidade de lignina na fibra, devido à alta solubilidade da hemicelulose no meio alcalino. Pelos resultados obtidos, para estas membranas pode-se concluir que a maior afinidade entre a matriz e a fibra compensou os efeitos negativos do pré-tratamento.
Quando se analisa a composição da fibra na membrana, pode-se perceber que para uma mesma composição de compatibilizante, uma redução na composição da fibra (de 4% p/v para 2% p/v) resultou em uma diminuição significativa do módulo de Young de 17% p/v para o conjunto 3PMMAa3 (com fibra pré-tratada) e 21% p/v para o compósito 3PMMAb3 (com fibra in natura). Isto demonstra que houve uma transferência eficiente dos esforços aplicados para a fase dispersa.
Por outro lado, houve uma significativa redução do alongamento (ductilidade) na ruptura com o porcentual de fibra adicionada; como observado na Figura 4, para todas as amostras sem fibras (Casos 6 a 10) a porcentagem de deformação na ruptura foi superior (maior do que 10% p/v para o Caso 10). Isto permitiu concluir que para este sistema, a introdução das fibras resulta em materiais mais resistentes.
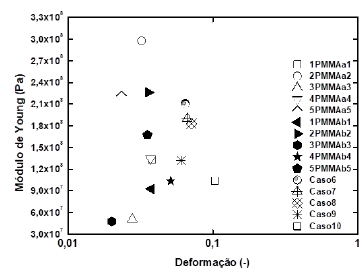
Figura 4 Variação do módulo de Young com a composição de fibra de açaí e compatibilizante nas membranas de PMMA/fibra de açaí/compatibilizante.
No gráfico de tensão versus deformação, da Figura 5 observou-se que o pré-tratamento promoveu a adesão interfacial o que favoreceu a resistência mecânica, toda vez que as membranas construídas com a fibra pré-tratada apresentaram valores maiores de módulo de Young no ato da ruptura. Por fim, em todos os casos com a fibra in natura houve uma maior elongação.
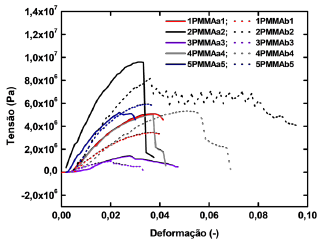
Figura 5 Influência do pré-tratamento nas membranas PMMA/fibra de açaí/compatibilizante. Membranas nomeadas com a_n° no final foram construídos com a fibra pré-tratada, e as nomeadas com b_n° no final foram construídas com a fibra in natura.
Membranas PLA/Lignina/Compatibilizante. Para estas membranas as composições usadas foram 16% p/v de compatibilizante, 1 a 3% p/v de lignina e 8 a 12% p/v de polímero. A matriz de planejamento resultou em 5 casos, identificados na Tabela A.3. Também, no final da tabela são listados mais 3 casos tomados de referência, onde as membranas são constituídas somente de polímero e compatibilizante. Por fim, também são registrados mais 5 casos sem compatibilizante, visando avaliar a necessidade de uso do mesmo, visto que, a lignina cumpriria a função integradora na matriz polimérica. Da mesma forma que nas membranas de PMMA, a avaliação estatística revelou que o efeito combinado das composições de polímero e lignina tiveram maior influência sobre os valores da variável resposta (Figura B.3). Na Figura 6 é destacada a influência da lignina na resistência à tração das membranas, onde a composição de polímero é constante no seu valor mínimo (8% p/v). O melhor caso apresentado foi aquele com a menor composição de lignina (Ensaio1 com 1% p/v). Como comentado previamente, este resultado indica que o limiar de composição da lignina é de 1% p/v, acima desse valor, a adesão interfacial matriz/fase dispersa é reduzida produzindo uma ineficiente transmissão dos esforços para o polímero. Na Figura 7, quando a composição de polímero é a máxima (12 % p/v), pôde-se observar que o aumento na composição de lignina de 1% p/v (Ensaio2) para 5% p/v (Ensaio4), aumenta a resistência a tração. O melhor caso obtido foi para a formulação com a menor composição de lignina e sem compatibilizante (Ensaio2SC), o que pode indicar que o caráter dual da lignina (hidrofílica e hidrofóbica) favorece a adesão dos componentes. A formulação sem lignina (PLA2) gerou a menor resistência, o que confirma que, a presença desta comunica dureza ao material.
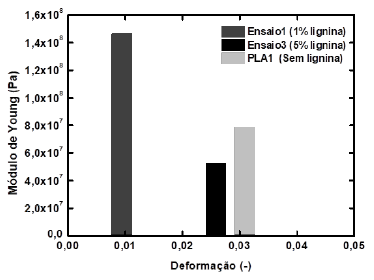
Figura 6 Modulo de Young versus composição de lignina para 8% p/v de PLA e 16% de compatibilizante, nas membranas de PLA/lignina/compatibilizante.
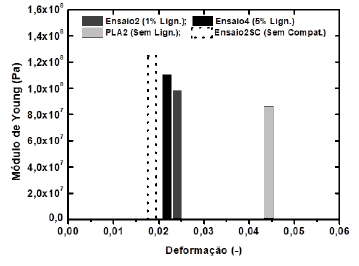
Figura 7 Modulo de Young versus composição de lignina para 12% p/v de PLA e 16% de compatibilizante, nas membranas de PLA/lignina/compatibilizante.
Na Figura 8, os resultados correspondem às membranas com às composições médias de polímero e lignina, (10% p/v e 3% p/v respectivamente), com e sem compatibilizante. Os resultados deste grupo confirmam que, nos compósitos com PLA e lignina é possível obter um material com alta resistência a tração, dispensando o uso de compatibilizante na formulação, como se observa para o Ensaio5SC.
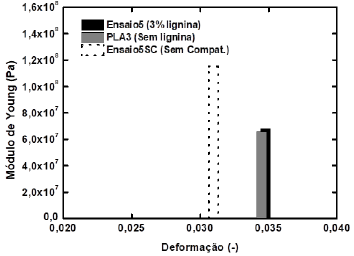
Figura 8 Modulo de Young versus composição de lignina para 10% p/v PLA e 16% p/v de compatibilizante, nas membranas de PLA/lignina/compatibilizante.
Na Figura 9, são comparados os casos com a maior composição de polímero (12% p/v) e lignina (5 % p/v) com e sem compatibilizante. Novamente, para estes compósitos, o melhor caso apresentou- se para aquele sem compatibilizante na formulação (Ensaio 4SC). Também, estes resultados reafirmam que a presença de lignina aumenta a resistência do compósito em todas as composições do polímero (maior resistência à tração no Ensaio4 com 5 % p/v de lignina comparada como caso PLA4 sem lignina). Pode-se concluir assim, que é possível construir membranas sem a necessidade de inclusão de um compatibilizante, resultado interessante quando se pensa na economia da fabricação.
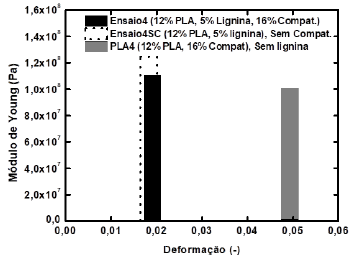
Figura 9 Modulo de Young versus composição de lignina para a composição máxima de polímero (12%) e lignina (5%) e 16% de compatibilizante, nas membranas de PLA/Lignina/Compatibilizante.
Membranas PLA/Fibra do caroço de açaí / Compatibilizante. Os casos de estudo definidos para estas membranas são descritos na Tabela A.4. Com ajuda dos gráficos de superfície de reposta, foi possível estabelecer as faixas de composição ótima em 16 % p/v de compatibilizante, (9,5 a 12) % p/v de PLA e (2,0 a 2,6) % p/v de fibra, in natura. Por outro lado, nas membranas com a fibra pré-tratada a composição ótima destas atingiu (2,0 a 3,0) % p/v de fibra. Pode-se observar que a matriz polimérica é mais receptiva a uma quantidade maior de fibra pré-tratada, o qual indica que o pré-tratamento teve um efeito positivo na interface matriz-fibra.
A Figura 10 compara os valores de Módulo de Young dos casos estudados, observando-se uma resistência um pouco maior nas membranas com a fibra in natura que pode ser explicada pela maior presença da lignina, no entanto, as membranas com a fibra pré-tratada mostraram uma maior elongação na ruptura, o que é conveniente quando se pensa na construção de geometrias complexa com este material.
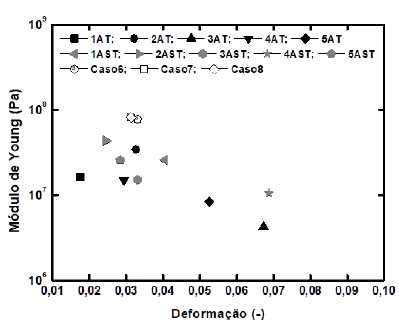
Figura 10 Variação do módulo de Young com a composição de fibra de açaí (in natura e pré-tratada), nos compósitos de PLA/fibra de açaí/16% compatibilizante.
As membranas com a fibra pré-tratada foram menos suscetíveis a rompimento durante a aplicação. Por fim, pode-se perceber que as membranas de PLA com as fibras oferecem uma menor resistência à tensão quando comparadas com as misturas sem as fibras (5AT e %AST versus Caso6, Caso7 e Caso8). Também, observou-se que os valores de resistência destes materiais são menores quando comparados com as membranas de PMMA. Este comportamento pode ser explicado por fenômenos de superfície na interface matriz/fibra, que envolve a natureza dos polímeros participantes. Embora estudos aprofundados são merecidos, pode-se afirmar que o caráter hidrofílico do PLA interfere na integração das fibras.
Ensaio de absorção de água
A absorção de água em compósitos com fibras vegetais se deve, principalmente à natureza hidrofílica da fibra e aos defeitos (cavidades) que surgem naturalmente durante a construção do compósito. As Figuras 11 e 12 apresentam a evolução da porcentagem de absorção de água para as amostras analisadas. A exceção dos casos 2AST e 2AT, todas atingiram o equilíbrio de absorção a partir das 100 h de análise.
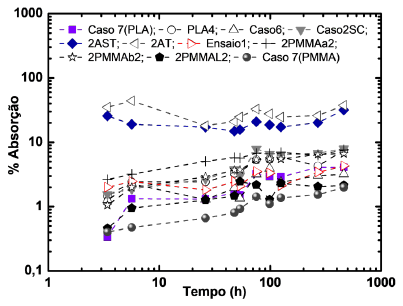
Figura 11 Variação da porcentagem de absorção com o tempo para os compósitos de PLA e PMMA com lignina e fibras de açaí in natura e pré-tratada.
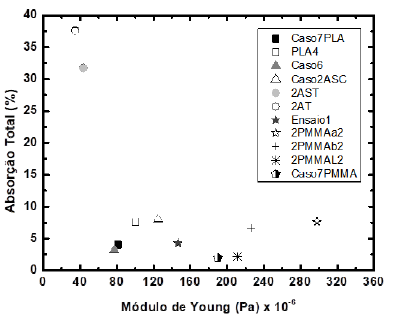
Figura 12 Relação entre o módulo de Young e a porcentagem de absorção total para os compósitos de PLA e PMMA com lignina e fibras de açaí in natura e pré-tratada.
As amostras, constituídas pelos polímeros sem fibras, Caso6 (10 % p/v PLA + 16% p/v compatibilizante), Caso7(PMMA) (12 % p/v PMMA e 5 % p/v de compatibilizante) e do caso 2PMMAL2 apresentaram os menores porcentagem de absorção, como era de se esperar, visto que estes materiais têm pouca afinidade com a água. O caso 2PMMAL2, se destacou em valores altos de Módulo de Young, o qual indica que houve uma forte adesão entre a fibra e a matriz.
A maioria dos compósitos, com fibras in natura e pré-tratadas apresentaram porcentagens de absorção abaixo de 10%, os quais são valores comparáveis com os encontrados na literatura para compósitos de polímero com fibras naturais. Sanches et al. [37] registraram porcentagens de absorção de 10,57% em compósitos de poliéster/ fibras de bagaço de cana-de-açúcar in natura, e 3,35% para compósitos de poliéster/fibras de bagaço de cana-de-açúcar, pré-tratada com NaOH.
Valores de porcentagens de absorção, fora do esperado (acima de 30%) foram encontrados para as membranas de igual composição de PLA e fibra do caroço de açaí, in natura e pré-tratada, 2AST e 2AT, respectivamente. Este comportamento pode ser atribuído à falta de adesão fibra-polímero, o que também pôde ser corroborado pelos valores inferiores de Módulo de Young dentro do conjunto de amostras analisadas. Por outro lado, comparando estas duas amostras, se observa que houve uma maior absorção de água na membrana com a fibra pré-tratada, contudo, o comportamento esperado era uma menor absorção devido à maior interação fibra-matriz promovida pelo pré- tratamento. Uma justificativa razoável para este comportamento é que pelo pré-tratamento foi reduzida a composição de lignina e hemicelulose, o que diminuiu a resistência da fibra.
Analisando as amostras do Caso7(PMMA) e do caso 2PMMAL2, observa-se que a porcentagem de absorção aumentou na membrana com a lignina. Considerando que a inserção de água no compósito diminui a estabilidade da integração polímero-fibra, pode-se inferir que a introdução da lignina aumenta a velocidade de biodegradação do compósito. Por outro lado, a introdução da lignina além de promover a absorção de umidade, ainda aumentou a resistência a tração do compósito em um 11%, o que demonstra o potencial deste compósito para aplicações de engenharia exigentes e ambientalmente amigáveis.
Um resultado similar foi conseguido nos casos PLA4 (12% p/v PLA), 2AST e 2AT para os quais se observou um aumento de 7,56% para 31,75% e 37,6% respectivamente, na porcentagem de absorção das membranas com fibras com respeito ao polímero puro. Cabe ressaltar que a diminuição na resistência à tração pela introdução da fibra foi bastante significativa de 57% para o compósito 2AST e de 66% para o compósito 2AT com respeito ao polímero puro.
Ensaios de microscopia eletrônica de varredura (MEV)
De acordo com as imagens microscópicas da Figura 13, as partículas de lignina apresentam formatos diversos, mas predominam os arredondados. Por outro lado, as fibras de açaí separadas do caroço são longitudinais, de espessura regular rugosa, com cavidades, tipo canais na parede secundária onde são alojados plasmodesmos (visualizados como pequenas esferas brilhantes na Figura 14). De acordo com Cruz Pessoa et al.[3] os plasmodesmos podem permanecer após o desprendimento manual ou mecânico da fibra do caroço. Um resultado interessante é observado na Figura 14b, para a fibra pré-tratada, onde pode-se perceber que tanto a superfície da fibra e os plasmodesmos permaneceram inalterados após o pré-tratamento. Por fim, os diâmetros das fibras visualizadas oscilam entre (52,8 - 101) μm, dimensões comparáveis com aquelas registradas em [3] (550 μm), [5] (80 μm) e em [38] (270 μm). As Figuras 15, e b) apresentam as micrografias dos polímeros somente com o compatibilizante, observando- se uma estrutura regular, com predominância da fase polimérica e alguns agrupamentos característicos do compatibilizante. As faces dos polímeros reforçados mostraram inclusões regulares arredondadas, especialmente naquelas constituídas pela lignina (Figura 16). Observa- se, na fratura, que estas partículas estão uniformemente distribuídas o que indica que a resistência mecânica na membrana foi resultado do efeito combinado da matriz e da fase dispersa. No caso das membranas reforçados com as fibras de açaí (Figura 17), observa-se que estas também estão uniformemente distribuídas, e no ponto de fratura, as fibras apresentaram uma deformação na conformação estrutural, de cilíndrica para laminar. Este comportamento demonstra que parte dos esforços suportados na matriz foram também comunicados para a face dispersa até o final do ensaio.
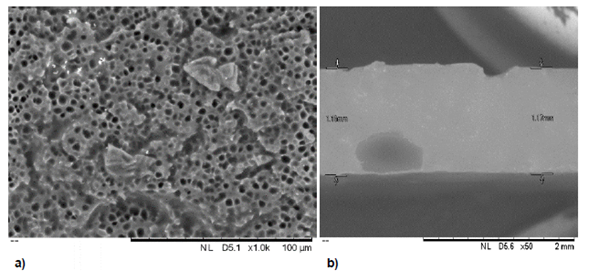
Figura 15 Micrografias da área transversal no ponto da fratura dos polímeros compatibilizados sem biomassa. a) Caso 7 da Tabela A.1 (12% PMMA+ 5 % compatibilizante); b) Caso6 da Tabela A.4 (10% PLA + 16% compatibilizante).
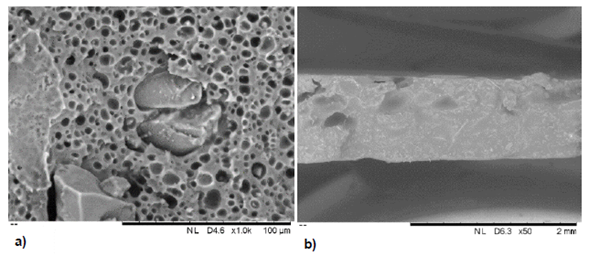
Figura 16 Micrografias da área transversal no ponto da fratura das membranas reforçadas com a lignina. a) PMMA-L2 (12% PMMA+ 1% lignina + 5% compatibilizante) da Tabela A.1; b) Ensaio 1 (8% PLA+ 1% lignina + 16% compatibilizante) da Tabela A.3.
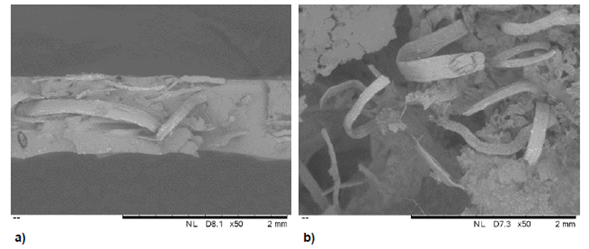
Figura 17 Micrografias da área transversal no ponto da fratura das membranas reforçadas com fibras de açaí. a) Amostra 2PMMA-b2, da Tabela A.2 (8% PMMA+ 4% Fibra do caroço do açaí in natura + 5% compatibilizante); b) Amostra 2AT, da Tabela A.4 (12% PLA+ 2% fibra de açaí pré-tratada + 16% compatibilizante).
Conclusões
A avaliação mecânica das membranas de PMMA/ Lignina/Compatibilizante, mostraram que o limiar de composição da lignina foi de 1% p/v, acima deste valor, o Módulo de Young diminuiu fortemente e, esta queda, foi amenizada pelo aumento do PMMA e compatibilizante. As membranas com lignina apresentaram maior resistência mecânica, assim, este reforço é interessante quando o objetivo é reduzir a carga polimérica no compósito final. Nas membranas de PMMA/Fibra de açaí/ Compatibilizante, o limiar de composição da fibra in natura foi superior do que das fibras pré- tratadas, no entanto, as membranas construídas com estas últimas apresentaram maior resistência mecânica, promovida pelo tratamento superficial da fibra, o que favoreceu a adesão interfacial. Por outro lado, para as membranas de PLA/ Lignina/Compatibilizante, uma composição de 1% p/v é ótima para reforçar a resistência da matriz polimérica, também, é possível construir as membranas sem a necessidade de inclusão de um compatibilizante, resultado interessante quando se pensa na economia da fabricação. Nas membranas PLA/Fibra/compatibilizante, o pré-tratamento da fibra teve um efeito positivo pois uma maior composição da fibra pôde ser integrada na matriz. Para estas membranas, a fibra pré-tratada comunicou uma maior elongação na ruptura, o que é vantajoso quando se pensa na construção de peças com geometrias complexas. A maioria das membranas com fibras in natura e pré-tratadas absorveram até um 10% de umidade.
Valores bem menores de 10% foram encontrados para as membranas construídas com PMMA, o qual se justifica pela maior hidrofobicidade do polímero. Membranas de PMMA com lignina, atingiram maiores porcentagem de absorção quando comparadas com o polímero puro, no entanto, a lignina aumentou a resistência a tração do compósito em um 11%. Este comportamento permitiu inferir que a introdução da fibra aumenta a velocidade de biodegradação do compósito mantendo a resistência mecânica da matriz polimérica.
As imagens da MEV confirmaram que o pré- tratamento alcalino das fibras de açaí não alterou a morfologia das mesmas, toda vez que tanto a superfície da fibra e os plasmodesmos permaneceram inalterados. Por outro lado, no momento da fratura mecânica, as cargas nos compósitos se conservaram uniformemente distribuídas indicando que a resistência mecânica do compósito foi resultado do efeito combinado da matriz e da fase dispersa.