Introducción
En el municipio de Sabana de Torres se encuentra una planta de tratamiento de gas natural llamada “PG-PSC”; dicha planta incorpora un sistema de recuperación y separación de hidrocarburos del gas natural, en el que se utiliza varsol como medio absorbente, el cual es calentado en dos hornos de combustión de llama directa.
El varsol pobre es bombeado a la torre de absorción, allí, la corriente es utilizada como medio absorbente para retener los hidrocarburos (propanos, butanos, pentanos y pesados) que se encuentran en una corriente de gas natural rico que se alimenta en contracorriente. Luego, el varsol enriquecido con estos hidrocarburos pasa a una etapa de separación que se lleva a cabo en una torre desetanizadora en la cual se despojan los más livianos (metano y etano); después, este fluido es enviado a una torre de fraccionamiento en la que se recuperan los hidrocarburos más pesados; posteriormente, la corriente sale por el fondo de la torre y se separa en dos corrientes nuevas, una de ellas es enviada a los hornos de llama directa para ser calentada y alimentada a la torre de fraccionamiento, y la otra es utilizada como aceite térmico en los rehervidores de las demás unidades de proceso para ser posteriormente bombeada a la torre de absorción e iniciar el proceso nuevamente (Figura 1).
Los hornos de llama directa fueron instalados en la década de los sesenta. Dichos equipos han estado operando de forma continua desde su puesta en marcha. Su alto requerimiento operativo en el transcurso del tiempo y el escaso mantenimiento comparado con su demanda operacional pudieron haber afectado gradualmente su desempeño y eficiencia.
Debido a que se desconoce el desempeño operativo actual de los hornos se decidió realizar un estudio técnico y, de esta forma, presentar opciones de mejora que podrían aumentar su eficiencia en términos de ahorro de gas combustible, además, se presentan ventajas de cada una de las alternativas que podrían impactar positivamente el desempeño de los hornos en estudio.
Metodología
El estudio operativo de los hornos de llama directa se llevó a cabo realizando una compilación de información en campo (en el sitio) sobre su estructura, el registro histórico de los datos operacionales y una verificación visual de la operación de los mismos, y en paralelo se hizo una contextualización con los avances de ingeniería que han tenido este tipo de equipos.
La compañía suministró información con respecto a la composición del fluido de trabajo (varsol), composición y variables operacionales de transporte del gas combustible, comportamiento térmico de los hornos (termografías), parámetros de diseño de los equipos y datos operacionales monitoreados por el sistema SCADA. Posteriormente, se depuró la información compilada con el fin de capturar los datos más relevantes asociados directamente a la eficiencia operativa de los equipos en relación al consumo de gas combustible y con dicha información, se plantearon opciones que permitieran mejorar la eficiencia de los hornos, basados en tres posibles causas que la impactan.
Factores que impactan la eficiencia
Estado del aislamiento térmico y/o las paredes de los equipos. El aislamiento térmico cumple una tarea de gran importancia en equipos de intercambio de calor puesto a que este permite disminuir las pérdidas de calor hacia el entorno y aprovechar así en mayor proporción el calor destinado al cambio de temperatura del fluido de trabajo [1]. Asimismo, la integridad de las mismas repercute sobre las pérdidas de calor; el óxido aumenta la emisividad de las superficies metálicas facilitando la disipación de calor hacia el ambiente.
En ausencia de fallas en el aislamiento térmico, las termografías presentarían mínimas variaciones en la escala de temperaturas de las paredes de los equipos, es decir, una coloración semejante en toda la superficie. No obstante, el aislamiento térmico al interior de los hornos se ha deteriorado con el tiempo, lo que se evidenció por zonas en las que hay un cambio abrupto de coloración (temperaturas) como se observó en las imágenes termográficas (puntos calientes) (Figura 2). Adicionalmente, en las caras externas se constata que hay zonas que han sido afectadas por el óxido [2].
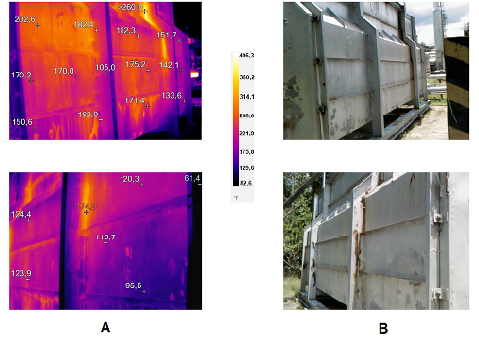
Fuente: planta de gas PG-PSC.
Figura 2 Vista termográfica (A) y natural del lado frontal del horno (B).
Temperatura de la corriente de aire alimentada. La temperatura de entrada de la corriente de aire al sistema juega un papel crucial en la distribución del calor generado por la combustión a través del equipo [3].
Basados en el libro “Waste Heat Reduction and Recovery for Improving Furnace Efficiency, Productivity and Emissions Performance” [4], precalentar la corriente de aire aumentaría notoriamente la eficiencia del proceso, ya que el calor generado por la reacción de combustión sería aprovechado significativamente en el aumento de la temperatura de los productos y no en la transformación de los reactivos, adicionalmente, es un proceso que no requiere un sistema complejo de equipos.
A nivel comercial, se utilizan tres equipos para llevar a cabo el precalentamiento:
Recuperador de calor: un recuperador es un equipo que sirve como medio de intercambio de calor entre los gases de chimenea y la corriente de aire entrante. La corriente caliente se hace fluir a través del equipo para permitir así el intercambio de calor desde los gases de chimenea hacia la corriente de aire frío aumentando así su temperatura [5].
Regenerador de calor: un regenerador corresponde a un equipo que permite almacenar el calor proveniente de una corriente caliente para ser posteriormente utilizado en el calentamiento de un fluido de interés. Los gases de chimenea se hacen fluir a través del equipo con el fin de cargar sus baterías de almacenamiento, luego, la corriente de aire es alimentada absorbiendo a su paso el calor almacenado aumentando así su temperatura. Como hay que cargarlo para que absorba y almacene la energía térmica, es necesario el uso de dos regeneradores; mientras uno se carga el otro ya ha sido cargado y puede calentar la corriente de aire entrante de forma continua [5].
Calentador con resistencias: es un equipo que en su interior tiene un sistema de resistencias que mediante la utilización de energía eléctrica aumentan la temperatura del fluido que lo atraviesa. El aire es capturado de la atmósfera por el equipo, luego se hace fluir a través de su interior, allí, las resistencias lo calientan para ser posteriormente alimentado al sistema [6].
Flujo de la corriente de aire alimentada al sistema. Estequiométricamente existe una cantidad de oxígeno mínimo que debe ser alimentado al equipo para que la reacción de combustión se lleve a cabo en su totalidad. De dicho flujo depende de que el combustible alimentado pueda ser aprovechado por completo. Sin embargo, una alimentación excesiva de aire podría ocasionar pérdidas del calor generado por la combustión, debido a que este está compuesto predominantemente por nitrógeno el cual no reacciona y, finalmente, parte del calor disponible tendría que ser utilizado para su calentamiento [7]. Actualmente, los hornos están absorbiendo aire directamente de la atmósfera a través de los Venturi que se encuentran instalados en su parte inferior. Gracias a sus planos iniciales, se identificó que los equipos trabajan con un 20 % de exceso de aire con respecto al flujo de combustible alimentado.
Síntesis de oportunidades de mejora
Sustituir o reparar parcial o totalmente el aislamiento térmico y/o las paredes de los hornos. Con el fin de evidenciar el estado del aislamiento térmico de los hornos, se recomienda realizar un estudio completo del mismo para definir su estado actual y llevar a cabo las reparaciones necesarias del mismo para garantizar su correcto funcionamiento, permitiendo así reducir las pérdidas de calor con el entorno.
Para el caso de los puntos calientes, las zonas más afectadas por el óxido deberían ser recubiertas con pintura anticorrosiva disminuyendo así la emisividad de los más críticos y aumentando la vida útil de los equipos [8].
Escoger el espesor y el material adecuado para aislar las paredes de los equipos no asegura que las pérdidas de calor con el entorno vayan a desaparecer, sin embargo, dichas pérdidas se pueden reducir entre el 10 % y el 25 %. A pesar de que los equipos se encuentren correctamente aislados, siempre existirán unas pérdidas aproximadas entre el 2 % y el 5 % del calor total del sistema [9].
Precalentar la corriente de aire alimentada. El proceso de combustión genera cambios de temperatura lo cual hace que haya pérdidas de calor (parte del calor generado es utilizado para calentar los reactivos y/o los productos); por esto, se recomienda precalentar la corriente de aire alimentado por alguno de los mecanismos anteriormente mencionados, permitiendo así aprovechar en mayor proporción el calor generado lo cual conlleva a una combustión más eficiente [3].
Ajustar el flujo de entrada de aire. Actualmente, el equipo trabaja internamente con un 20 % en exceso de aire con respecto al combustible alimentado; por esto, se recomienda calibrar los Venturi con el fin de asegurar un exceso del mismo que no repercuta negativamente en la eficiencia del proceso.
Resultados
Para analizar el comportamiento de la transferencia de calor desde la reacción de combustión hacia la corriente de varsol se utilizó el software de simulación de procesos Aspen Hysys ® (Figura 3) con las consideraciones enunciadas en la Figura 4. Para esto, se calcularon por separado el calor neto generado por la reacción de combustión y el calor absorbido por el fluido de trabajo.
Para cada uno de estos, se utilizó una distribución diferente de equipos puesto a que la reacción de combustión involucra dos calores sensibles y un calor latente, mientras el cambio de temperatura de la corriente de varsol involucra únicamente un calor sensible.
Para el cálculo del calor neto generado por la reacción de combustión y el calor absorbido por la corriente de varsol se tuvieron en cuenta las siguientes condiciones respectivamente.
El calor neto calculado para el proceso de combustión fue de 11 500 000 kJ/h y el calor absorbido por la corriente de varsol fue de 8 090 000 kJ/h obteniendo una eficiencia del 69.98 % (la eficiencia inicial de los equipos era del 78 %).
Discusión de resultados
Análisis de las alternativas propuestas Reparar parcial o totalmente el aislante térmico y/o las paredes de los hornos. Para los hornos en estudio, el realizar estos mantenimientos correctivos podría teóricamente aumentar su eficiencia a valores cercanos a su eficiencia original, es decir, se obtendría un incremento desde 69,98 % a un máximo de 78 %.
Actualmente, el equipo está consumiendo 1,156e7 kJ/h (10 957 MMBtu/h) (con una eficiencia del 69,69 %) si se implementa esta alternativa pasaría a consumir entre 1,093e7 kJ/h (10,362 MMBtu/h) y 1,037e7 kJ/h (9831 MMBtu) (para eficiencias del 74 % y 78 % respectivamente); teniendo en cuenta que el valor comercial del MMBtu para el gas natural que se utiliza en la planta es de 5,2 USD y que existiría una reducción en el consumo de energía de entre 630 000 kJ/h (0,595 MMBtu/h) hasta 1 190 000 kJ/h (1126 MMBtu/h); se esperaría un ahorro de entre 27 103,44 USD y 51 309,07 USD por año, dicho ahorro, se asociaría a la disminución del consumo de gas combustible.
No se tuvo en cuenta el costo de las intervenciones necesarias para la reparación total o parcial del aislamiento térmico de los hornos, además, se deberán realizar estudios adicionales con el fin de definir su estado actual y el tiempo de recuperación de la inversión.
Precalentar la corriente de aire alimentada. La eficiencia actual del horno es aproximadamente del 69,98 %, si se implementa esta alternativa con base en el estado de los hornos, su desgaste y trayectoria operacional (más de 50 años de operación) se esperaría un aumento de entre 9 % y 12 % [10], es decir, su eficiencia podría aumentar entre el 79,04 % y el 81,98 %.
Actualmente, el equipo está consumiendo 1,156e7 kJ/h (10,957 MMBtu/h) si se implementa esta alternativa pasaría a consumir entre 1,024e7 kJ/h (9,709 MMBtu/h) y 9,867e6kJ/h (9353 MMBtu/h) (para eficiencias de 78,98 % y 81,98 % respectivamente); teniendo en cuenta que el valor comercial del MMBtu para el gas natural que se utiliza en la planta es de 5,2 USD y que existiría una reducción en el consumo de energía de entre 1 320 000 kJ/h (1,248 MMBtu/h) hasta 1 693 000 kJ/h (1,604 MMBtu/h); se esperaría un ahorro de entre 56 856,52 USD y 73 049,23 USD por año, dicho ahorro, se asociaría a la disminución del consumo de gas combustible.
Adicionalmente, se recomienda utilizar un regenerador para llevar a cabo dicho proceso puesto a que este permite aprovechar el calor de los gases de chimenea y funciona en continuo. Para analizar su costo de instalación, transporte e implementación se sugiere llevar a cabo un estudio técnico para definir dichos costos.
Ajustar la cantidad de aire alimentado. Para llevar a cabo dicha tarea los tubos Venturi presentes en las entradas por las cuales fluye el aire hacia el interior de los equipos deberán ser calibrados con la finalidad que la cantidad alimentada de aire garantice el requerimiento de oxígeno estequiométrico de la reacción y, a su vez, haya un exceso de entre el 3 % y 15 % [11].
Actualmente, la eficiencia del equipo es del 69,98 % y está consumiendo 1,156e7 kJ/h (10,957 MMBtu/h) si se implementa esta alternativa la eficiencia aumentaría entre 3,06 % y 11,62 % (estos valores para excesos del 15 % y 3 % respectivamente), por lo tanto, para suplir el requerimiento actual de calor, pasaría a consumir entre 1,107e7kJ/h (10,498 MMBtu/h) y 9,914e6 kJ/h (9,397 MMBtu/h) (para eficiencias de 73,04 % y 81,60 % respectivamente); teniendo en cuenta que el valor comercial del MMBtu para el gas natural que se utiliza en la planta es de 5,2 USD y que existiría una reducción en el consumo de energía de entre 490 000 kJ/h (0,456 MMBtu/h) hasta 1 646 000 kJ/h (1,56 MMBtu/h); se esperaría un ahorro de entre 20 899,59 USD y 71 064,14 USD por año, dicho ahorro, se asociaría a la disminución del consumo de gas combustible.
Conclusiones
Si se adecúa el proceso con alguna de las alternativas de ahorro planteadas anteriormente, se podría esperar un ahorro mínimo de 20 899,56 USD por año y máximo 76 049,23 USD por año debido a la reducción en el consumo de gas natural, posterior a las inversiones requeridas para las adecuaciones mencionadas.
Teniendo en cuenta las alternativas planteadas, la adecuación que requeriría menor intervención para el proceso sería la tercera (modificar la cantidad de aire alimentado al sistema) puesto, a que su implementación solo requiere calibrar los tubos Venturi permitiendo una entrada de entre el 3 % y el 15 % (2 698 kscfd y 3 013 kscfd) de aire en exceso con respecto al gas natural alimentado. Reparar parcial o totalmente el aislante térmico y/o las paredes de los hornos, ajustar la cantidad de aire alimentado y precalentar la corriente de aire alimentado permitirían aumentar la eficiencia del proceso hasta 8,02 %, 11,62 % y 12 % respectivamente. No obstante, para el caso de estudio, el ajuste del aire alimentado seria la alternativa que requeriría menor intervención para el proceso.