Introducción
La problemática de los materiales a base de petroquímicos ha tomado fuerza a nivel mundial, presentándose en el año 2018 una producción global de 359 millones de toneladas, esto debido a su versatilidad y fácil manipulación para los sectores de la industria (Miranda, 2023). La Organización de las Naciones Unidas (ONU) informó que solo el 9 % del plástico usado en el mundo se recicla (Redacción ambiente, 2024), por lo que otra de las opciones es la fabricación de plásticos biodegradables para disminuir esta alta producción.
El plástico convencional proveniente del petróleo se convierte en un material que tarda muchos años para descomponerse en condiciones ambientales de temperatura, humedad, rayos UV, etc. (Gupta et al., 2022), y solo se fraccionan en partículas más pequeñas llamados microplásticos, generando una amenaza ambiental por su dificultad para ser retirados de los diversos ecosistemas (Castañeta et al., 2020). Por esta razón, actualmente se busca remplazar estos plásticos por materiales que posean la capacidad de descomponerse en un tiempo no mayor a 6 meses por la acción enzimática de microrganismos (bacterias, hongos, algas) bajo condiciones normales del medio ambiente (Cortez et al., 2022).
Una de las alternativas son los biopolímeros, debido al bajo costo de las materias primas para su obtención, su alta disponibilidad y carácter renovable, propiedades que le permiten competir con el petróleo. Entre los polímeros basados en recursos renovables se encuentra el almidón, como el de yuca, judías y papas, utilizados para la elaboración de materiales biodegradables (Chen et al., 2023; Zhang et al., 2023). Las películas obtenidas a partir de algunos almidones como el de maíz han reportado 90 % de degradación en 90 días, otros del 48.7 % en 15 días, comparado con las bolsas de polietileno del 6.96 % en 90 días (Folino, 2020; Marichelvam, 2019); sin embargo, su naturaleza hidrofílica ha afectado de forma negativa las propiedades mecánicas, de barrera y térmicas, lo que ha dado origen a estudios sobre modificaciones al almidón (físicas, químicas o enzimáticas) o mezclas con otros polímeros (celulosa, policaprolactona (PCL), PLA, etc.) (Bangar et al., 2022). Así, una de las mezclas prometedoras es entre el almidón y el PLA por su carácter renovable y biodegradable (Arboleda et al., 2015).
Si bien los materiales biodegradables se han estudiado y analizado hasta su punto de producción, actualmente se reportan pocas investigaciones sobre el tiempo de vida útil de los pellets para obtener las películas biodegradables con las propiedades mecánicas óptimas de resistencia, color, flexibilidad, etc. Es así como se ha mezclado el almidón con diferentes plastificantes como glicerol, sorbitol, entre otros (Schmitt et al., 2015), y se ha hecho uso de recubrimientos y adición de extractos con el fin de alargar el tiempo de vida útil de los pellets, ya que su carácter hidrofílico afecta las propiedades y la producción de materiales biodegradables (Cutz et al., 2023). Además, otros factores que inciden son el tiempo de almacenamiento, el tipo de empaque y la humedad del ambiente, los cuales cambian las propiedades de los pellets y afectan la procesabilidad para la obtención de películas biodegradables, tecnología que la sociedad y la industria de los plásticos requiere.
Por lo anterior, el objetivo de esta investigación es determinar el tiempo de vida útil de los pellets a partir de TPS y PLA para obtener películas biodegradables a diferentes condiciones de almacenamiento. El diseño se basó en estudios de almacenamiento realizados a diferentes productos (Graham et al., 2017; Lee y Robertson, 2021), donde se determinó utilizar diferentes tipos de empaques y humedad relativa, y así evaluar cómo estas condiciones afectan las propiedades mecánicas de las películas obtenidas de la procesabilidad de los pellets almacenados.
Materiales
Métodos
Obtención del almidón termoplástico (TPS) y los pellets
El almidón se mezcló con glicerol en una proporción 66.5 % y 33.5 %, respectivamente, para obtener el TPS y PLA con TPS en una proporción de 40 % y 60 %, respectivamente. La mezcla fue plastificada en un extrusor de doble tornillo marca Leistritz modelo Micro-27 (Estados Unidos) con tornillos de 27 mm de diámetro y una relación L/D de 40:1. La velocidad del tornillo fue de 200 rpm. El perfil de temperatura de las zonas del extrusor desde la alimentación hasta el dado se fijó en 100-135-135- 135-130-150-165-165-160-154 °C. Se empleó un dado de cordón con tres orificios de 3 mm de diámetro.
El material se transportó a través de una banda con ventilación y posteriormente se cortó en pellets de 3 mm de largo.
Almacenamiento de los pellets
Los pellets obtenidos se almacenaron en tres tipos de empaques: bolsa de papel (empaque 1), bolsa de polietileno (empaque 2) y bolsa de celulosa multicapa (empaque 3). El material empacado se almacenó a 20 °C bajo tres condiciones diferentes de humedad relativa 10 %, 26 % y 70 %. Se empleó silica gel, cloruro de magnesio y cloruro de sodio, respectivamente, para proporcionar las humedades requeridas. El almacenamiento se realizó durante 75 días. El procesamiento de los pellets para la obtención de las películas flexibles se realizó en los días 0, 8, 20, 40 y 75.
Proceso de obtención de la película utilizando el extrusor de película soplada
Los pellets obtenidos se llevaron al extrusor de tornillo sencillo Thermo Scientific Haake Polylab OS (Alemania) equipado con un barril de 19 mm, un tornillo con 19 mm de diámetro y relación de compresión de 3:1. La velocidad del tornillo fue 35 rpm. El perfil de temperatura llevado a cabo desde la zona de alimentación hasta el dado de soplado fue de 130-155-170-155 °C. Se empleó una matriz de soplado con una apertura de 70 μm y un juego de rodillos para estandarizar el espesor de la película flexible.
Evaluación de propiedades mecánicas de tensión
A las películas flexibles obtenidas se les evaluó el esfuerzo, porcentaje de deformación y módulo de Young. Las muestras se calibraron de acuerdo con la norma técnica ASTM D882-10 utilizando un Pie de Rey digital (Absolute DigImatic modelo CD-6” CSX-B) y un medidor de espesor (Mitutoyo thicknes gage 7326s, Japón). Se empleó una máquina universal de ensayos (Shimadzu modelo EZ-Test EZL), con una velocidad de cabezal de 100 mm/min, con una celda de carga de 500 N, velocidad de recolección de datos de 500 puntos por segundo y una distancia entre mordazas de 50 mm.
Propiedades de barrera de los tres tipos de empaque
Para la permeabilidad a oxígeno (oxígeno extra seco grado 2.6, Cryogas -UN I072 - NTC 2462) se cortaron 3 muestras de cada tipo de empaque utilizado para almacenar los pellets de forma circular con 80 mm de diámetro, que se colocaron en un medidor de permeabilidad a gases (Gas Permeability Tester Perme VAC-VBS, Labthink, China) dentro de una celda de transmisión de gas, formando una semibarrera entre dos cámaras; la cámara inferior se llevó a una presión estable de vacío por 3 h, pasado este tiempo el gas se alimentó en la cámara superior a una mayor presión y se dejó pasar por la película. La diferencia de presión provocó que el gas permee a través de la muestra desde la cámara de mayor presión hacia la de baja presión. Las mediciones se realizaron por triplicado.
Resultados
Propiedades mecánicas de tensión de las películas obtenidas a partir de los pellets almacenados
En la Figura 1 se presentan las gráficas del esfuerzo para los 9 tratamientos de un corte longitudinal de las películas obtenidas a partir de los pellets almacenados a diferentes condiciones. Se observó que el empaque 3 presenta mayor variación con respecto a los otros dos tipos de empaque, debido a que, los pellets almacenados a la humedad del 70 % en un tiempo mayor a 8 días pierden sus propiedades de extrusión, como el porcentaje de humedad que paso de 0.466 % a 2.233 %. La película que se obtuvo era pegajosa y blanda como se observa en la Figura 5, por esta razón no fue posible obtener una muestra para medir sus propiedades mecánicas; el mismo comportamiento se evidenció a la humedad del 26 % a los 40 días de almacenamiento, como se puede ver en la Figura 1. Las películas obtenidas con los pellets almacenados al 10 % de humedad relativa presentaron un comportamiento inestable, ya que el esfuerzo se mantuvo en el día 8, después, esta propiedad disminuyó hasta el día 40 y luego ocurrió un leve aumento a través del tiempo.
Las películas obtenidas de los pellets almacenados en los empaques 1 y 2 presentaron comportamientos mecánicos similares a las humedades del 70 % y 26 %, con una disminución en el esfuerzo en los días 8 y 20, y en el día 40 ocurrió un aumento de esta propiedad con tendencia a mantenerse. Las películas de los pellets almacenados en los empaques 1 y 2 a la humedad del 10 % sufrieron un comportamiento similar hasta el día 40 con respecto al esfuerzo, después, para el empaque 1, se presentó una disminución de esta propiedad, mientras que en el empaque 2 aumentó.
El comportamiento anteriormente descrito con respecto a la propiedad del esfuerzo lo presentó los cortes transversales de las películas obtenidas, como se observa en la Figura 2, excepto para las muestras almacenadas en el empaque 3 a la humedad del 10 %, donde el esfuerzo disminuyó hasta el día 8 y se trató de mantener hasta el día 75.
En la Figura 3 se muestra la deformación que presenta un corte longitudinal de las películas a partir de los pellets almacenados a diferentes condiciones de almacenamiento. Se observó que las películas de los pellets almacenados a la humedad al 26 % en los empaques 1 y 2, y la muestra del empaque 2 a la humedad del 10 %, presentaron un comportamiento de aumento en la deformación hasta el día 20, y después inició una disminución con tendencia a estabilizarse; en cambio, en las muestras a la humedad del 70 % con el empaque 1 y 2, y la muestra a la humedad del 10 % con empaque 2, ocurrió un aumento de esta propiedad mecánica hasta el día 8, luego disminuyó y comenzó a estabilizarse hasta el día 75.
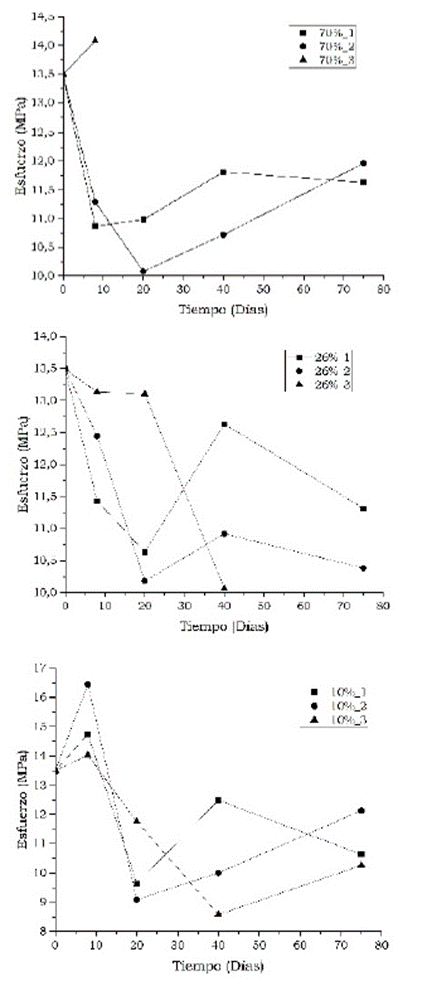
Figura 1 Propiedades mecánicas de esfuerzo del corte longitudinal de las películas. Humedad relativa: 70 %, 26 % y 10 %. Tipo de empaque 1, 2 y 3.
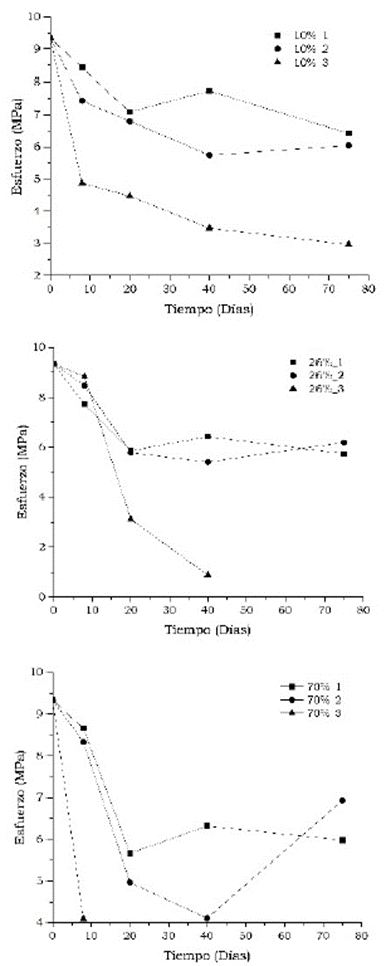
Figura 2 Propiedades mecánicas de esfuerzo del corte transversal de las películas. Humedad relativa: 70 %, 26 % y 10 %. Tipo de empaque 1, 2 y 3.
En la Figura 4 se muestra el comportamiento de la propiedad de deformación de un corte transversal de las películas a partir de los pellets almacenados. Se observó que las muestras almacenadas en el empaque 3, en las humedades de 70 % y 10 %, tuvieron una disminución de esta propiedad a los 8 días, a los 20 días la muestra a la humedad del 10 % comenzó a aumentar y a los 75 días ocurrió una disminución; efecto contrario ocurrió con la muestra a la humedad del 26 % utilizando el mismo empaque, donde aumentó la deformación a los 8 días, pero luego empezó a disminuir hasta los 40 días. Este comportamiento también se puede observar para las muestras a la humedad 70 % en el empaque 1 y 2, con la diferencia que se logró obtener la muestra del día 75, donde las películas obtenidas de los pellets almacenados en el empaque 2 presentaron un aumento mayor de la deformación comparada al empaque 1.
Los cortes transversales de las películas a partir de los pellets almacenados a las humedades del 26 % y 10 % en los empaques 1 y 2 presentaron un comportamiento similar de aumento de la deformación hasta el día 20. En el día 40 para las muestras del empaque 2 a las humedades del 26 % y 10 % la deformación disminuyó, y hasta el día 75 se estabilizó; por su parte, las muestras del empaque 1 a las humedades del 26 % y 10 % en el día 40 aumentaron esta propiedad y en el día 75 sufrieron una disminución.
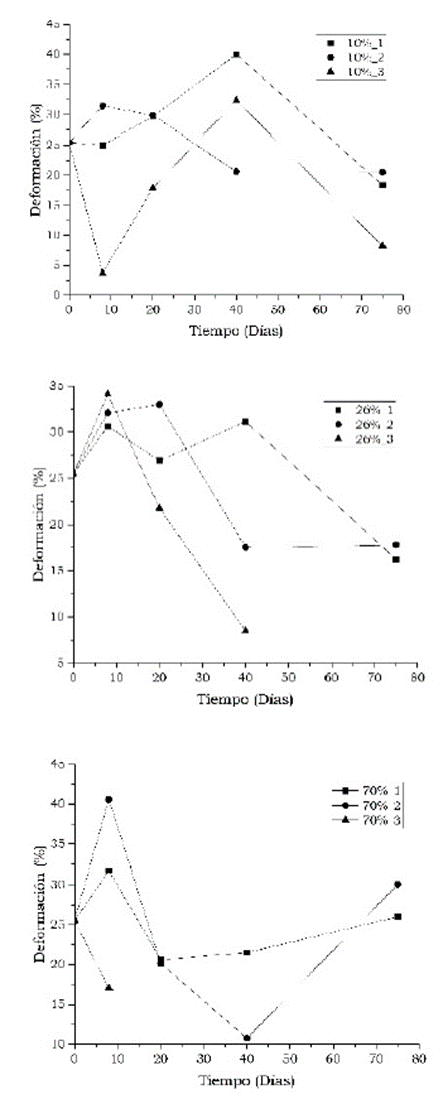
Figura 3 Propiedades mecánicas de deformación del corte longitudinal de las películas. Humedad relativa: 70 %, 26 % y 10 %. Tipo de empaque 1, 2 y 3.
Efecto del tipo de empaque, tiempo de almacenamiento y humedad en la vida útil de los pellets
De acuerdo con el análisis estadístico, se observó que los dos factores con mayor influencia en la vida útil de los pellets fueron: el tipo de empaque y el tiempo de almacenamiento, que presentaron una diferencia significativa en las propiedades mecánicas de tensión de las películas obtenidas (p<0.05), por lo cual se obtuvieron 15 tratamientos, los cuales se presentan en la Tabla 1.
Tabla 1 Nomenclatura para cada tratamiento a un tiempo de almacenamiento y tipo de empaque específico
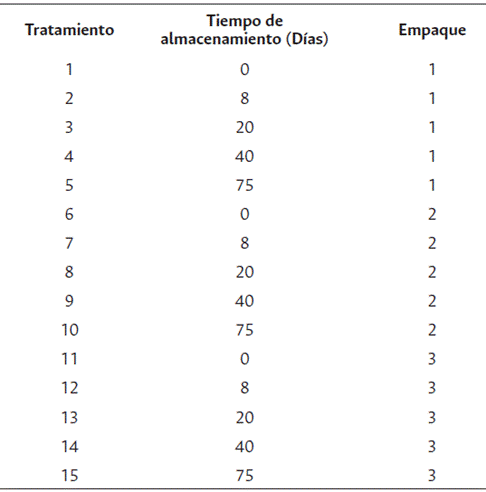
Los cortes transversales de las películas a partir de pellets almacenados hasta el día 20 y utilizando el empaque 1 o 2 mostraron un porcentaje de deformación similar a la muestra del día 0, debido que no se presentó una diferencia significativa (Figura 6). Con respecto al esfuerzo, al utilizar el empaque 1 fue posible mantener esta propiedad sin variación significativa hasta el día 8.
Por otro lado, en la Figura 7 se observa que los cortes longitudinales de las películas presentaron un porcentaje de deformación similar a la muestra del día 0 al utilizar el empaque 2 hasta los 75 días. Con respecto al esfuerzo, es similar a la película del día 0 utilizando el empaque 1 hasta el día 40 o utilizando el empaque 2 hasta el día 8.
Propiedades de barrera de los tres tipos de empaque
Los empaques 1 y 2 utilizados para almacenar los pellets para este estudio presentaron una permeancia de 7.632e-12 mol/m2*s*Pa, y 4.2937e-13mol/m2*s*Pa, respectivamente. El empaque 2 al ser celulosa multicapa presentó una permeabilidad mayor, comparado con empaques que tienen otros componentes incluida la celulosa. Estudios han reportado una permeancia entre 2.59 y 2.70e-11 mol/ m2*s*Pa para aquellas películas elaboradas con un determinado porcentaje de celulosa, por lo que, entre mayor contenido de celulosa, mayor permeabilidad del empaque (Palechor et al., 2023).
Discusión
Con respecto a la deformación, y como se puede ver en las Figuras 3 y 4, se evidenció que algunos tratamientos presentan unas variaciones en esta propiedad, debido a que una de las materias primas para obtener las películas flexibles biodegradables es el almidón, polímero natural que sufre dos cambios en su estructura una vez se somete a un proceso de gelatinización, donde los gránulos de almidón se hinchan debido a una energía adicional suministrada, formando un estado desordenado de alta energía (Chang et al., 2021). Estos materiales biodegradables presentan desventajas en sus propiedades mecánicas por el proceso de retrogradación que sufre el almidón, lo que ocasiona microfisuras frágiles mientras ocurre el reordenamiento de la cadena intermolecular o intramolecular, conduciendo a una disminución en su rendimiento y valor de aplicación (Guo et al., 2023).
El aumento del porcentaje de deformación en algunos tratamientos se puede deber a la plastificación, proceso que ocurre después de la retrogradación, donde existe una adsorción de humedad generando que la tensión en la punta de la microfisura rompa la estructura de las películas, lo que da como resultado un aumento en la fluidez de las moléculas de almidón y, por consiguiente, las películas presentan un aspecto más blando, pegajoso y una mayor deformación antes de su ruptura (Guo et al., 2023). Algunos estudios reportan que la adsorción de humedad posiblemente sea causa del almidón termoplástico (TPS), debido a que su estructura presenta grupos hidroxilos que actúan como aceptores y/o donantes de protones, aumentando el potencial de interactuar con la humedad del ambiente (Mina, 2021).
El comportamiento de los tratamientos con respecto al esfuerzo de los cortes transversal y longitudinal de las películas, posiblemente se deba al proceso de retrogradación del almidón que se genera después de que ha conseguido una estructura amorfa por el proceso de gelatinización, donde inicia una reconstrucción estructural del almidón, pero no hasta un estado anterior a la gelatinización. La retrogradación es un proceso continuo, que se puede dividir en dos etapas: a corto y largo plazo. Como se observó en el análisis estadístico, el tiempo de almacenamiento es uno de los factores con mayor influencia en las propiedades mecánicas de las películas. Probablemente, el tiempo requerido para que ocurran esas dos etapas esté relacionado con el tiempo de almacenamiento del almidón.
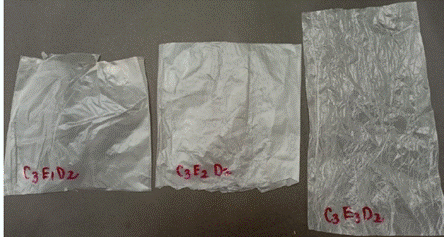
Figura 5 Películas obtenidas a partir de los pellets almacenados a una humedad del 70 % por 8 días, en empaques 1 (a), 2 (b) y 3 (c).
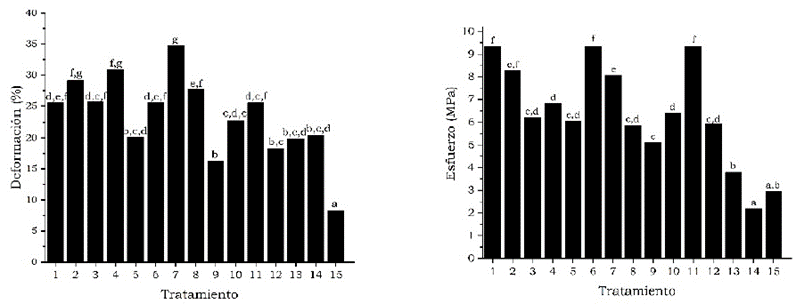
Figura 6 Efecto del tipo de empaque y tiempo de almacenamiento en las propiedades mecánicas de tensión de un corte transversal de las películas. Las diferencias de letras de la (a - g) indica diferencias significativas (p<0.05).
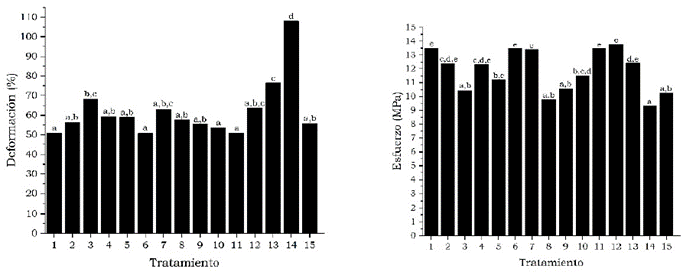
Figura 7 Efecto del tipo de empaque y tiempo de almacenamiento en las propiedades mecánicas de tensión de un corte longitudinal de las películas. Las diferencias de letras de la (a - e) indica diferencias significativas (p<0.05).
La primera etapa, (1) A corto plazo (desde las primeras horas hasta varias decenas de horas), se debe principalmente a la recristalización de la amilosa, como se evidencia en las Figuras 1 y 2 de esfuerzo, donde los primeros 8 días de almacenamiento ocurrió un cambio del esfuerzo en cada uno de los tratamientos, lo cual posiblemente obedezca a este fenómeno. La segunda, (2) A largo plazo (días), es causada principalmente por la recristalización de la amilopectina, la cual a su vez se puede dividir en dos procesos: la repolimerización entre cadenas de la estructura de doble hélice y el empaquetamiento de las dobles hélices de las cadenas de almidón (Chang et al., 2021; Taguchi et al., 2023). Este fenómeno se podría evidenciar en las Figuras 1 y 2 de esfuerzo, donde después de los 20 días de almacenamiento, en la mayoría de los tratamientos, el esfuerzo comienza a tener un comportamiento estable y con variaciones mínimas (Zhai et al., 2022)
Estudios similares han reportado que este proceso del almidón se debe a la estructura lineal de la amilosa y ramificada de la amilopectina, de la cual la amilosa tiene una mejor capacidad de reordenamiento, donde requiere relativamente poco espacio para ordenarse, en comparación con la estructura ramificada de la amilopectina que limita su movilidad después de la gelatinización y requiere más tiempo para formar una estructura ordenada (Chang et al., 2021; Taguchi et al., 2023).
Otros de los cambios observados con respecto al esfuerzo de algunos tratamientos es la disminución del esfuerzo en el tiempo con respecto a la muestra sin almacenar. Estudios han reportado que las películas de almidón nativo tienen una mayor resistencia a las películas almacenadas, las cuales han sufrido un proceso de retrogradación; esto puede deberse a que después de la retrogradación de la película se forma una estructura cristalina más alta a través de los enlaces de hidrógeno entre las amilopectinas, además, el agua ligada internamente se convierte en agua libre y luego se volatiliza en el proceso de retrogradación, disminuyendo el contenido de agua en las películas lo que resulta en una reducción de la resistencia de la atracción (Guo et al., 2023).
Por otro lado, el tipo de empaque donde se almacena los pellets es un factor que influye en las propiedades mecánicas de las películas. El tipo de empaque se considera un componente importante para conservar las características de un producto, debido a que una de sus funciones es la protección contra los factores externos (Yin et al., 2022). Los pellets son materiales susceptibles a la humedad, por lo que se determinó que el empaque 3 no es un tipo de empaque ideal, ya que a una humedad del 70 % es posible almacenar el producto por 8 días máximo, y a una humedad del 26 %, hasta 40 días, en comparación con los empaques 1 y 2, los cuales lograron conservar los pellets hasta 75 días.
Por otra parte, el empaque 3 no resistió la prueba de permeabilidad al oxígeno, posiblemente debido a la alta porosidad, alta capacidad de absorción de líquidos y al ser un material higroscópico debido a los grupos hidroxilo que presenta (Oshani et al., 2023). Por el contrario, los empaques 1 y 2 presentaron un coeficiente de permeancia al oxígeno similar, lo que posiblemente permitió que las muestras con estos tipos de empaque no tuvieran un contacto de forma acelerada con la humedad, factor que está ligado con la plastificación y retrogradación del almidón cuando es almacenado.
De acuerdo con el análisis estadístico, no existió diferencia significativa entre el empaque 1 y 2, por lo cual existen dos posibilidades de empacado. La diferencia persiste en que el empaque 1 proviene de una materia prima de fuente natural, de celulosa, la cual ha tenido varias investigaciones sobre sus propiedades como una posible alternativa para reemplazar los plásticos derivados del petróleo, por ejemplo, el polietileno, debido a su disponibilidad, capacidad de renovación y biodegradabilidad (Huang et al., 2022; Souza et al., 2022).
Estudios han reportado que las películas obtenidas a partir de celulosa ofrecen una excelente capacidad antibacteriana, actividades antioxidantes, notable protección UV, así como una barrera confiable contra el vapor de agua y el oxígeno (He et al., 2023). Estas se han utilizado para empacar lirio de Lanzhou, generando una inhibición a las actividades de las enzimas oxidativas y conservando las características de calidad del producto (Ren et al., 2023). Por otra parte, se ha demostrado que la celulosa mejora las propiedades mecánicas, propiedades de barrera y resistencia al agua para la obtención de películas (Jiang et al., 2022).
Conclusiones
Mediante el estudio se logró definir que el tipo de empaque y el tiempo de almacenamiento son factores que influyen en la vida útil de los pellets a partir de yuca termoplástico para obtener las películas flexibles. Se encontró que pueden existir dos tipos de empaques para el almacenamiento de los pellets: celulosa multicapa y polietileno, y que pueden almacenarse desde una humedad del 10 % hasta el 70 %, conservando las propiedades de los pellets por aproximadamente 75 días a una humedad del 26 %, ya que la diferencia del esfuerzo mecánico de las películas obtenidas a partir de los pellets almacenados fue de aproximadamente 5 MPa y el porcentaje de deformación presentó un aumento de aproximadamente 20 % con respecto a la muestra control, mientras que para el empaque de papel, a los 8 días de almacenamiento, no fue posible obtener películas con características similares al control.