Introduction
Nowadays, first-generation biomass is commonly used to obtain biofuels in order to address the increasing global energy demand and partially substitute fossil fuels. For example, vegetable oils from oil palm plantations or rapeseed in Europe are employed to produce biodiesel, and plants rich in fermentable sugars such as corn, cereals, and sugarcane are processed to produce bioethanol (Jin, Yang, Poe, and Huang, 2018; Kajaste, 2014; Ubando, Felix, and Chen, 2020). However, the exploitation of this type of biomass entails a problem, since it competes for the use of land and, in traditional agriculture, these products are feedstock, which increases and volatilizes their price (Damartzis and Zabaniotou, 2011; Lapkin etal., 2014). Besides, we live in an era of human dominance that has altered biogeochemical carbon, nitrogen, phosphorus, and water cycles (Carey, Yang, McNamara, and Mayer, 2016) and affected agricultural productivity, as well as the quality and fertility of the soil.
The most widely-recommended raw material to produce different types of high value-added products is second-generation biomass (2G). These include the more affordable and widely available lignocellulosic residues from agro-industrial activities. If 2G is not valorized, it will often be disposed of in sanitary landfills, used like a low quality fuel, or returned to the field as a fertilizer (Loffler et al., 2010; Zondervan, Nawaz, de Haan, Woodley, and Gani, 2011). As a result, the production costs of fuels and/or chemicals obtained from it are lower than those from first-generation biomass or energy crops (Bentsen, Felby, and Thorsen, 2014; Damartzis and Zabaniotou, 2011; Demirbas, 2010a; Ekman, Wallberg, Joelsson, and Borjesson, 2013). Additionally, this type of biomass does not have the same problems of its first-generation counterpart, since it is nonedible (Ubando et al., 2020).
This type of recovery is carried out at facilities known as biorefineries, which provide a conversion process with different products (energy, food/fodder, materials, chemicals, etc.) with ideally zero waste production (Carey et al., 2016; Martinez, Kok, and Ng, 2018; Ubando et al., 2020). This enables the recovery of nutrients to produce fertilizers by extracting high value-added phytochemicals (e.g., caffeine, polyphenols, and saponins, etc.) (Carey etal., 2016; Esquivel and Jiménez, 2012; Murthy and Madhava Naidu, 2012). Such waste is later used as a source of electrical energy, fuel, and/or chemicals in general (methanol) by means of a thermochemical treatment (gasification). In Colombia, a few industries have adopted this concept and recover this type of active or functional principles because their content in vegetable raw material is relatively low (Lapkin et al., 2014). Furthermore, if the energy in second-generation biomass, which is not efficiently recovered to make other functional products, given that it is generally employed as fertilizer or low-quality fuel (Bilhat Chala, Sajid Latif, 2015; Lapkin et al., 2014; Salinas Rios et al., 2014; Torres-Mancera et al., 2011), all its potential for adding value is wasted and it becomes an environmental issue (Hughes et al., 2014).
However, this type of facilities has to be studied in more detail, because the biomass supply chain could be noncontinuous and stable due to the fact that agro-industrial wastes are usually collected after the harvesting agricultural crops, and many of them have a seasonality nature, which affects the logistics and operation of the biorefinery. Therefore, the challenge is to manage biomass availability and storage in order to maintain a continuous in situ operation and production (Yue et al., 2014).
Biomass
First, it should be clarified that biomass is any organic material that can constitute the main raw material of a biorefinery, and it is classified into four types according to its origin (Maity, 2015):
Energy crops (corn, sugarcane, oil palm, etc.)
Agro-industrial waste (palm kernel, coffee pulp, etc.)
Wastes from tree pruning, gardening, etc.
Municipal and industrial waste
Second-generation or type II biomass is a renewable source of energy and it corresponds to the biodegradable fraction of products, wastes and residues of agriculture, forestry, cattle raising and related industries, as well as the above-mentioned fraction of municipal and industrial wastes (Bentsen et al., 2014; Loffler et al., 2010; Martinez et al., 2018). Additionally, biomass is the only renewable resource that can be transformed into gas, liquid and/or solid fuels by physical, thermal, thermochemical and/or biological processes (see Figure 1) (Balagurumurthy, Singh, Ohri, and Prakash, 2015; Escalante Hernández, Orduz Prada, Zapata Lesmes, Cardona Ruiz, and Duarte Ortega, 2010; ISAGEN, 2005).
In Colombia, there are many sources of residual biomass as a result of its agricultural vocation (Escalante Hernández et al., 2010; Hernández A., 1994) and the amount of agro-industrial waste from crops are of great socioeconomic importance in the country (see Figure 2). Such waste can be turned into a great opportunity to generate high value-added chemicals and/or electrical energy (Ekman et al., 2013).
These agro-industrial wastes are based on organic polymers such as lignin and cellulose. Due to a structure composed of carbohydrate chains, this kind of biomass is highly oxygenated in comparison with conventional fossil fuels, including liquid hydrocarbons and carbon. Nevertheless, its main constituent is carbon (Virmond, Rocha, Moreira, and José, 2013). Even though this renewable resource employed as raw material to produce energy, chemicals, and fuels will not satisfy humanity's needs in the short term, it will open the possibility of being a more sustainable and environmentally-friendly society through the concept of biorefineries (Clark, 2007).
Biorefineries
This type of facility is firmly based on the principles of sustainable use of land and green raw materials, environmentally-friendly technologies, and energy self-sufficiency, among others (Gil-Montenegro, Arocha-Morales, Rojas-Pérez, and Narvàez-Rincón, 2019; Kamm, Schonicke, and Hille, 2016). It can transform biomass and/or biologic materials into fuels, chemicals, pharmaceutics, energy, and even food and animal feed (Demirbas, 2009, 2010b; Ekman et al., 2013; Kamm et al., 2016; Loffler et al., 2010) (see Figure 3). These multiproduct platforms are designed and operated embracing the previously described sustainability principles and considering the features of the biomass, the sub products, and final products in terms of biochemical and chemical composition in order to find the best technologies and/or conversion routes that generate the most added value, profitability, and the least negative impact on the environment (Kamm et al., 2016; Maity, 2015).
Although Figure 3 and Table 1 describe several types of biorefineries, the differences between them are the type of treatment or conversion route that the biomass follows (thermal, biological or chemical), the production technologies, the characteristics of the raw materials, and their final products (Demirbas, 2009, 2010b; Kamm and Kamm, 2004; Loffler et al., 2010). Particularly, biorefineries that convert biomass into fuels, high value-added chemicals, electricity, and heat can generally be divided into two types: thermochemical and biological (Joglekar, Pathak, and Mandavgane, 2019; Parajuli et al., 2015). Thus, the types of biorefinery and the associated products are shown in Table 1.
Table 1 Classification of biorefineries according to their conversion route
Biorefinery | Path | Products |
---|---|---|
Biosyngas-based | Thermochemical | Syngas, hydrogen, methanol, dimethyl ether, diesel (Fischer-Tropsch) |
Pyrolysis-based | Thermochemical | Bio-oils, fuels, diesel, and hydrogen, among others |
Hydrothermal reforming | Thermochemical | Hydrocarbon compounds, chemicals, diesel and fuels |
Fermentation-based | Biological | Bioethanol |
Oil from vegetable species | Chemical | Biodiesel, diesel, and gasoline |
Source: Demirbas, 2010b
The operation, functionality, and characteristics of a biorefinery are usually compared to those of an oil refinery (Ariel, Alzate, Camilo, Toro, and Peña, 2018; Carey et al., 2016; Maity, 2014) because they work in a similar way, and a great portion of the products obtained from this fossil material, or their substitutes, can be manufactured from biomass (Kamm and Kamm, 2004; Kamm etal., 2016; Loffler et al., 2010). However, the most important difference is that oil refineries use a non-renewable resource (petroleum), while biorefineries use a renewable option (biomass) (Ariel et al., 2018; Carey et al., 2016; Haro, Ollero, Perales, and Vidal-Barrero, 2013).
Currently, there is another concept or industry like a biorefinery that seeks to mitigate environmental damage and use resources in a sustainable and rational way: polygeneration. Using this concept enables producing power and high-quality, high value-added chemical products through the efficient transformation of mainly non-renewable natural resources, such as carbon or natural gas. Therefore, this type of systems and biorefineries is considered to be the future of chemical and electrical power generation industries (Gangadharan, Zanwar, Zheng, Gossage, and Lou, 2012; Loffler et al., 2010).
The possibility of making a wide range of products greatly depends on the availability and characteristics of the biomass, its chemical composition of raw materials, and the technologies used for their transformation and energy recovery (Ekman et al., 2013; Maity, 2015; Zondervan et al., 2011). Industries that can apply several technologies and processes to transform a raw material (carbon and natural gas for polygeneration plants and biomass for biorefineries) provide a greater economic profit, rational and optimal use of resources, higher energy efficiency, less polluting emissions, and less negative effects on the environment (Kachrimanidou et al., 2015). To enjoy these benefits, the optimal operating conditions of a plant have to be carefully determined. Nevertheless, these conditions or operating parameters must not be generalized, because this type of facilities should be planned and adjusted to economic characteristics related to the market, the availability of resources, and the features of the raw materials associated with the plant's location (Demirbas, 2009; Leduc, Lundgren, Franklin, and Dotzauer, 2010; Loffler et al., 2010).)
Some literature and studies try to formulate, plan, and determine the best operating conditions for a plant that manufactures several types of products from renewable and non-renewable sources by simulating chemical processes and generating mathematical models and sensitivity analyses. These works try to model the operation of a plant in different situations. In general, they change market prices of raw materials, products, technologies and transformation. The operating parameters obtained from the development and solution of the models and simulations aim to guarantee the economic sustainability of the plant (Buragohain, Mahanta, and Moholkar, 2010b; Demirbas, 2009; Ekman et al., 2013; Zondervan et al., 2011). In some cases, they also minimize negative effects on the environment and the society (Gangadharan et al., 2012; Ng, Andiappan, Chemmangattuvalappil, and Ng, 2015).
Although plants or facilities of this kind have been widely studied in economic terms (Ng et al., 2015), their flexibility and capacity to respond to external disturbances have not been examined (Meerman, Ramírez, Turkenburg, and Faaij, 2012; Ngan et al., 2020; Sadhukhan et al., 2018). Furthermore, the economic and environmental costs of conventional technologies to manufacture a certain product are not usually compared to those of a novel alternative such as biorefineries. This is the case of a work that reports that the efficient energy recovery of nitrogen from a source of waste biomass at a biorefinery could reduce the existing dependence on the Haber-Bosch process, which uses between 1 and 2% of the total energy consumed world-wide (Carey et al., 2016). Thus, it avoids the consumption of natural resources, energy, and emissions harmful to human health that are associated with this process, which enables to obtain the fixed nitrogen needed to fertilize soils devoted to agriculture. Additionally, there is a considerable number of articles that deal with energy recovery from second-generation biomass under the concept of biorefinery. Nevertheless, they have not extensively discussed or considered the possibility of extracting high value-added biochemical and phytochemicals form raw biomass and, at the same time, produce fuels, electricity, and chemicals in general (Folmer, 2014; Lapkin et al., 2014), as can be confirmed in the work by Hughes et al. (2014).
Since Colombia is an agricultural country, the implementation of this type of concepts and methods entails a great challenge and opportunity for sustainable development, since niche markets such as pharmaceutics and cosmetics demand novel, functional, efficient, natural, and/or biobased ingredients (Departamento Nacional de Planeación DNP-DDRS Ministerio de Agricultura y Desarrollo Rural, Ministerio de Ambiente, Vivienda y Desarrollo Territorial Ministerio de
Comercio, Social, Exteriores, and Colciencias, 2011; Parajuli et al., 2015). The global market of special biochemical products (e.g., enzymes, flavors and fragrances, biopesticides, thickening agents, plant growth promotors, essential amino acids, and vitamins) based on biomass currently amounts to several billion US dollars per year, and it grows from 10 to 20% annually (Parajuli et al., 2015).
Phytochemical extraction and production of high value-added chemicals
There are two types of metabolites in biomass: primary and secondary. The first kind includes macromolecular compounds, such as polysaccharides (lignin and cellulose); the second (low-content) consists of waxes, oils, terpenes, and sterols. These components are highly relevant in biorefineries because they are functional and, in many cases, present biological activity (Clark et al., 2006; Herrero and Ibañez, 2018; Moncada, Aristizábal, and Cardona, 2016).
The extraction of secondary metabolites and the manufacture of natural products are gaining traction in the food, cosmetics, and pharmaceutical industries because final consumers are increasingly interested in biobased products of organic and sustainable nature that embrace the principles of green chemistry (Bergs et al., 2013; Herrero and Ibañez, 2018; Hughes et al., 2014). Moreover, the current trend in the field of profitable and sustainable recovery of waste biomass from agro-industrial processes (e.g., the coffee agroindustry) is exploiting the bioactive fractions and/or precursors of chemical compounds of general interest such as polyphenols, lipids, and carbohydrates, thus generating added value throughout the production chain (Ariel et al., 2087; Burniolfigols, Cenian, Skiadas, and Gavala, 2016). Figure 4 presents the block diagram of a proposed biorefinery that includes phytochemical extraction in the operation.
Biorefineries usually transform the entire biomass into fuels or plattform chemicals, and do not take advantage of secondary metabolites. In Figure 4, a proposed biorefinery is shown. It considers a novel procedure: phytochemical extraction prior to the thermochemical processes. The main advantage is that bioactive chemicals from secondary metabolites have the best market price per weight of material, since they are employed as raw materials in high-value industries such as pharmaceutic, cosmetic or human wellness industries.
The extraction method depends on the type of biomass (Ariel et al., 2018). Therefore, to have a sustainable and profitable operation, two questions should be addressed: What is the influence of the conditions of the process on the efficiency of the sequential or direct extraction of the target chemical fractions? And how does the scale of the process affect its performance? (Trivedi etal., 2016).
There are many well-known extraction techniques nowadays. Some of the most popular are solid-liquid, liquid-liquid, acid-base, and ultrasound and microwave-assisted extraction (Rombaut, Tixier, Bily, and Chemat, 2014a; Segneanu, Cziple, and Vlazan, 2013). Other techniques use pressurized fluids such as solvents; this is the case of supercritical fluids and pressurized liquids, among others (Herrero and Ibañez, 2018; Yeoh, Chong, Azahan, and Rahman, 2013). Nevertheless, the latter are associated with high investment costs, although, real economic evaluations of the process (including large-scale simulations) have not been carried out in most cases (Herrero and Ibañez, 2018).
In leaching extraction, the main issue is to find the most adequate solvent that enables the extraction of the phytochemicals of interest from biogenic raw material (Aristizábal-Alzate, 2016; C. E. Aristizábal, Vargas, and Alvarado, 2017; Herrero and Ibañez, 2018). However, the choice of solvents must be guided by a technical framework that includes key factors to achieve high efficiency (e.g., selectivity of the extraction, viscosity of the solvent, surface tension, cellular location of the target compound, and the part of the plant to be used as biomass (Bergs et al., 2013), among others) and observes the principles of green chemistry (Chemat, Vian, and Cravotto, 2012; Ghandi, 2014). For example, a numerical technique to select the solvent was proposed by Aristizábal (2016). It considers the Hansen solubility parameters of the secondary metabolites of interest and different solvents, as well as the affinity and the improvement of the performance of the solid-liquid extraction process. Table 2 below provides general information on some agro-industrial wastes, and the type of biorefinery that could be used to recover their energy, and possible high value-added products of industrial interest.
Biomass resulting from extraction processes is forwarded to thermochemical treatment, chemical or biological hydrolysis, and/or fermentation to obtain other high value-added chemicals (Moncada et al., 2016). Thus, byproducts are recycled, sustainability and profitability are increased, and the emission of pollutants by the biorefinery is reduced (Clark, 2007; Kajaste, 2014; Kamm et al., 2016). However, the recommendation in this case is a thermochemical process because traces of solvents used during phytochemical extraction may inhibit the growth of microorganisms, which would be counterproductive for a biological treatment (Lapkin et al., 2014). Furthermore, biofuels obtained from second-generation biomass have not been commercialized due to the low efficiencies and high costs of the equipment (Virmond et al., 2013). Besides, thermochemical methods use all components of the biomass (biodegradable and non-biodegradable fractions) without a pre-treatment stage, and they take from seconds to hours to produce hydrocarbons, value-added chemicals, and electricity, compared to biochemical processes that take days to complete the biotransformation and use microorganisms to turn the organic and biodegradable material only into alcohols and biogas by anaerobic digestion. Additionally, the slightest change in the composition of the biomass could produce functionality failures and undesired production due to changes in the metabolic route (Singh, Krishna, Mishra, Kumar, and Bhaskar, 2016). Therefore, the next section will describe thermochemical routes: gasification, methanol production, and the Fischer-Tropsch process. It can then be coupled with phytochemical extraction.
Gasification
The objective of this thermochemical treatment is to produce a mixture of CO, CO2, H2 and CH4 known as syngas (Molino, Chianese, and Musmarra, 2016; Pacioni et al., 2016; Pereira, Da Silva, De Oliveira, and Machado, 2012). The chemical reactions in this process take place in an environment with a limited amount of oxygen or another kind of oxidizing agent (air, steam, and a mixture of them) (Heidenreich and Foscolo, 2015; Richardson, Drobek, Julbe, Blin, and Pinta, 2015; Ramirez Rubio, Sierra, and Guerrero, 2011). During gasification, the biomass fed to the system is partially oxidized. This endothermal process, which occurs at high temperatures (500-1400 °C) and atmospheric pressures up to 33 bar (Ahmad, Zawawi, Kasim, Inayat, and Khasri, 2016), also needs a heat supply (Molino et al., 2016). Below, Figure 5 illustrates the gasification process and its different stages. It also shows the inputs and outputs of this treatment.
The material fed to the equipment (biomass, in this case) should contain an amount of water content below 35%. Water contents between 25 and 60% directly affect the efficiency of the gasifier, which results in energy losses (Ahmad et al., 2016).
Syngas can be used for several purposes such as heat and electrical energy generation. Furthermore, synthesis gas is employed to produce fuels through the Fischer-Tropsch process, methanol through the Lurgi-Ruhrgas process, and dimethyl ether and formaldehyde (Ahmad et al., 2016; Clifford, 2015; Moncada et al., 2016; Pacioni et al., 2016). Nevertheless, the quality of Syngas should be considered when used as raw material to produce energy and/or the previously mentioned chemicals, since it is affected by several factors, conditions, and operating parameters such as:
i) Type of gasifier
ii) Operating temperature
iii) Particle size of the raw material
iv) Gasifying agent
Since the most desirable product is a synthesis gas rich in CO and H2 to be used as chemical platform, temperatures in the 1200-1300 °C range allow the formation of these compounds and avoid the formation of methane. Specifically, particle sizes below 0,3 mm favor the production of CO, H2f and CH4, and reduce that of CO2. However, particle sizes under 0,15 mm affect the performance of H2 production. To select the gasifying agent, several studies demonstrated that a mixture of oxygen and vapor produces higher concentrations of CO and H2 in the syngas (63,27-72,56%) than using air (52,19-63,31%) (Ahmad et al., 2016).
Table 3 presents, as an example, the composition of a synthesis gas obtained from the gasification of Colombian agro-industrial waste as a function of the variation of the vapor/biomass ratio. It indicates that the initial characteristics of the biomass influence the final composition of the syngas and, depending on the selection of the gasifying agent and biomass ratio, this gas can be enriched or impoverished in one or several of its constituents. For example, we can observe that, regardless of the type of biomass, when the amount of water vapor is increased with respect to the biomass, the content of hydrogen (H 2) rises and carbon monoxide (CO) falls. Therefore, special attention must be paid when the input gasification parameters are set because, depending on the final use of the syngas, they should meet a certain composition, much more so if Syngas is recovered during the catalytic synthesis of other chemical compounds.
Table 3 Comparison of syngas composition (%v/v) and its calorific value over 1,123 K (850 °C) for different vapor/biomass ratios (weight fraction)
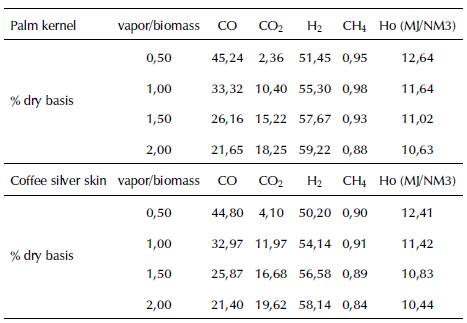
Source: Garcia, 2011
There are two types of phenomenological models that theoretically describe the behavior of the gasification process. The first kind includes 1D, 2D, or 3D kinetic models (depending on the space coordinates) that predict in more detailthe phenomenon, the evolution of the species, and the thermal and dynamic state of the process in the space conditions under consideration, due to the application of chemical kinetics, the description of the transport phenomena, and the balances between matter, energy, and momentum. The second type of model is related to chemical equilibrium, which can be divided into two groups: stoichiometric and non-stoichiometric methods (Costa, La Villetta, and Massarotti, 2015; Garcia, 2011; Rodrigues, Muniz, and Marcilio, 2016). Nevertheless, the second kind requires a number of kinetic parameters, determined through experimentation, that can range from a few to thousands depending on the selected gasification equipment, operating conditions, and kind of biomass (Garcia, 2011). The main reactions in the gasification process are illustrated in Table 4.
In addition, thermodynamic equilibrium or 0D models require less information and are valuable because they can predict the thermodynamic limits of a gasification system, regardless of the type of gasifier. As a result, they are simple, adequate to study the influence of operating parameters on the composition of the syngas (Hian, Saleh, and Abdul Samad, 2016; Rodrigues et al., 2016; Ruggiero and Manfrida, 1999), but they are only valid under chemical equilibrium conditions (Rodrigues et al., 2016). Other approaches involve Neural Networks and Computational Fluid Dynamics (CFD) (Costa et al., 2015; George, Arun, and Muraleedharan, 2016; La Villetta, Costa, and Massarotti, 2017).
Syngas: chemical platform to generate added value
As previously mentioned, the goal of a biorefinery is to integrate processes in order to simultaneously produce chemicals, fuels, and electricity that generate the optimum economic benefit (Ariel et al., 2018; Parajuli et al., 2015). For that purpose, processes and technologies that ensure the plant's sustainability and versatility in the long term should be integrated by incorporating different processing units in a modular way (C. Aristizábal, 2016). The following subsections describe some of the routes selected to exploit syngas and thus generate added value from its transformation into fuels, chemicals, and/or thermal energy (Bai, Liu, Lei, Li, and Jin, 2015; Rauch, Hrbek, and Hofbauer, 2014).
Catalytic synthesis of methanol
Methanol, or methyl alcohol (CH3OH), is one of the few chemical substances produced in megatons and traded in international commodity markets (Cooper, 2010). This alcohol is the precursor of a great variety of chemical compounds, such as formaldehyde (70%), methyl tert-butyl ether (20%), and acetic acid. Italso is an excellentfuel because of its octane rating of 113, the gasoline/methanol mixture (90/10) can increase the octane number of gasoline up to 130, and the engines that work with reach an efficiency of about 43% (Bozzano and Manenti, 2016). Besides being used to produce biofuels, it holds an approximately 10% share of total raw materials involved in this process, and it can be used to manufacture dimethyl ether, a chemical compound with the potential to compete with the consumption of conventional diesel (Bansode and Urakawa, 2014; Gangadharan et al., 2012; Pontzen, Liebner, Gronemann, Rothaemel, and Ahlers, 2011). Methyl alcohol would favor the transition from fossil to natural resources (Bozzano and Manenti, 2016).
Methanol can be manufactured through the catalytic reaction between CO, H2, and CO2 (Cooper, 2010). The conventional processes to produce this substance from synthesis gas or syngas are carried out in a multitubular fixed-bed reactor with a pellet-shaped Cu-ZnO-Al2O3 catalyst operating in gas phase (Hamelinck and Faaij, 2002; Holmgren, Berntsson, Andersson, and Rydberg, 2012; Leduc et al., 2010; Narvaez, Chadwick, and Kershenbaum, 2014). As this is a highly exothermal process, a cooling system should be implemented because high temperatures affect the useful life of the catalyst and, therefore, the reactor's performance. Table 5 below presents the main suppliers of methanol synthesis technologies and their operating conditions.
The equipment that produces methanol is fed syngas with a 2:1 ratio of hydrogen to carbon monoxide (Gangadharan et al., 2012; Gao et al., 2008; Holmgren et al., 2012). In addition, two other chemical pathways take place to generate methanol: either the CO2 reacts with hydrogen to form methanol and water, or there is a shift reaction (see Table 6).
Table 6 Chemical reactions and equations of the methanol production process
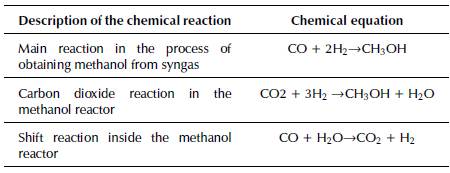
Source: Yusup, Phuong Anh, and Zabiri, 2010 and Riaz, Zahedi, and Klemeˇs, 2013
The kinetics of the chemical reactions involved in the process of catalytic synthesis of methanol is the following (Riaz etal., 2013):
Where,
In this proposed mathematical model, r denotes the reaction rate; f, fugacity; T, temperature; and R, the ideal gas constant.
The chemical synthesis processes that use catalysts (such as the production of methanol with copper-based catalysts) are very sensitive to the presence of sulfur and carbon dioxide (Holmgren et al., 2012). These compounds must be removed; otherwise, syngas conversion is restricted, and operating costs increase due to the continuous replacement of the catalyst due to poisoning, aging, or reduction of its active sites. Another issue found in industrial-scale methanol synthesis is the limitation imposed by the thermodynamic equilibrium. Therefore, many efforts are focused on developing technologies that expand methanol production by removing subproducts with selective membranes. However, for this purpose, mathematical and optimization models should be created to compare their efficiencyand functionality to traditional methods.
To purify methanol, a distillation tower can be used to remove the greatest possible number of impurities that may affect its quality, value, or simply the subsequent processes which use this product as raw material. This is thecase of the production of dimethyl ether (DME), another potential substitute of diesel (Gangadharan et al., 2012; Pontzen et al., 2011; Ravaghi-Ardebili and Manenti, 2015).
Fischer-Tropsch process
This process was developed by German inventors Franz Fischer and Hans Tropsch in the 1920's to produce liquid hydrocarbons (Buragohain et al., 2010b; Damartzis and Zabaniotou, 2011). It is a catalytic technique by which synthesis gas (CO + H2), also known as syngas, is transformed into a mixture of hydrocarbons: olefins, paraffins, waxes, and oxygenated products (synthetic fuels) or naphtha, a precursor in gasoline production (Arsalanfar et al., 2012; Buragohain et al., 2010b; Damartzis and Zabaniotou, 2011). The product obtained from this process greatly depends on the temperature, operating pressure, and the type of catalyst in use (Damartzis and Zabaniotou, 2011), which is generally made of metals in Group VIII such as iron (Fe), cobalt (Co), nickel (Ni), and ruthenium (Ru) (Arsalanfar et al., 2012). Equation (9) illustrates the general chemical reaction that represents this process:
A conventional catalyst based on cobalt (Co) enables the production of paraffinic diesel oils and, despite being expensive, it presents high activity at low temperatures and a ratio of H2/CO or stoichiometric number (SN) value of 2, which extends the useful life of the catalyst and prevents deactivation due to sintering or ageing (Buragohain, Mahanta, and Moholkar, 2010a; Kim, Jun, Joo, Han, and Song, 2009). Additionally, a Fe-based catalyst has also been developed to produce hydrocarbons, namely olefinic gasolines extracted from syngas with a substoichiometric H2/CO ratio, i.e., less than 2 (Buragohain et al., 2010a). Figure 6 presents a diagram of syngas production and exploitation through the Fischer-Tropsch process. Furthermore, it shows some of the conditions and characteristics of this catalytic transformation process of syngas into fuels:
The main Fischer-Tropsch reactions can be divided into five basic steps:
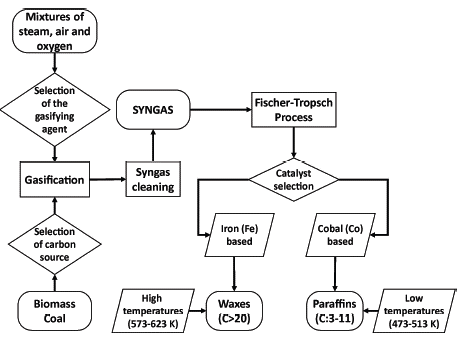
Source: Authors
Figure 6 Diagram of syngas production and exploitation by catalytic Fischer-Tropsch.
Adsorption of CO on the surface of the catalyst
Start of the polymerization by formation of a methyl radical (by dissociation of CO and hydrogenation)
Polymerization by condensation (addition of CO and H2, and water release)
Termination
Product desorption
The chemical equations of the reactions in a Fischer-Tropsch process are detailed in Table 7. Reaction 7 represents the transformation of the syngas into the products of interest: fuels with a number of carbon (C) atoms greater than 5.
Kinetics depend on the selected type of catalyst. For that reason, Table 8 reports the parameters of two power-law kinetics. The first one corresponds to a Fischer-Tropsch (FT) process with a catalyst based on Co and supported by Alumina (Co/Al2O3); the second one is based on Fe.
Table 8 Kinetic model parameters for the Fischer-Tropsch process with Cobalt (Co) and iron (Fe) catalysts
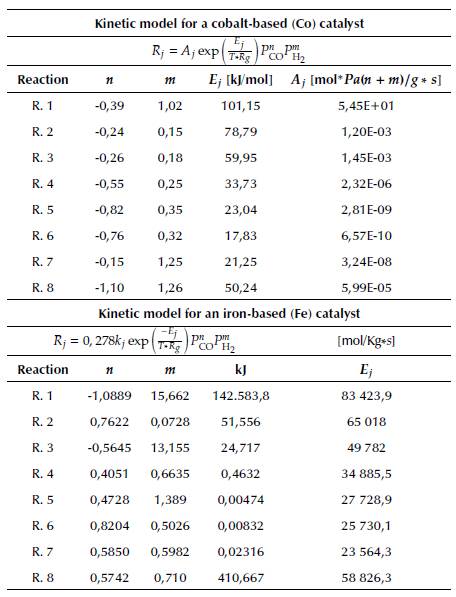
Source: Moazami, Wyszynski, Rahbar, Tsolakis, and Mahmoudi, 2017) and (Rahimpour, Jokar, and Jamshidnejad, 2012.
Moreover, Table 9 summarizes the chemical reactions of a mechanism that involves a Fischer-Tropsch process with a catalyst based on cobalt (Co), iron (Fe), and manganese (Mn).
In turn, Table 10 presents the model and kinetic parameters for this mechanism.
Table 9 Chemical reaction mechanism for a Fischer-Tropsch process with a Co-Fe-Mn catalyst
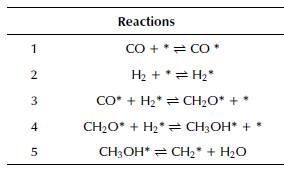
Source: Authors
Throughout history, four main types of industrial reactors have been used to produce Fischer-Tropsch reactions (Steynberg, Dry, Davis, and Breman, 2004):
Fixed packed-bed tubular reactor: SASOL (South African Synthetic Oil Ltd) call its reactor of this type Arge, which operates at 220-260 °C and 20-30 bar.
Circulating bed reactor: Named Synthol by SASOL, it operates at 350 ° C and 25 bar. It mostly produces olefinic gasoline.
Fluidized bed reactor: SASOLAdvanced Synthol, similar to Synthol in terms of operation but smaller for the same production capacity.
Slurry reactor: The catalyst is suspended in a liquid (often waxes produced by the same reaction) through which synthesis gas is bubbled. Generally, these reactors work at low temperatures to produce a maximum of products with high molecular weight.
Table 10 Model and kinetic parameters with a catalyst based on cobalt (Co), iron (Fe) and manganese (Mn)Summary of operating conditions of syngas valorization processes
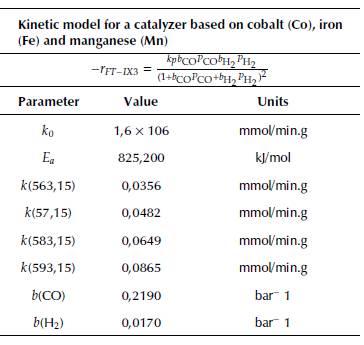
Source: Arsalanfar et al., 2012.
Table 11 summarizes some of the operating considerations and parameters to valorize syngas through thermochemical and catalytic processes and thus obtain thermal energy, electricity, fuels, and high value-added chemical compounds.
Table 11 Operating conditions of syngas valorization processes

Source: aManenti, Adani, Rossi, Bozzano, and Pirola, 2016; Riaz, Zahedi, and Klemes, 2013 and bRauch et al., 2014.
Conclusions
The exploitation of second-generation biomass and the integration of phytochemical extraction and thermochemical processes such as gasification at a biorefinery are great alternatives to address the energy crisis and the demand for materials for different industries. This is possible because this kind of facilities are conditioned to abide by sustainability and green chemistry parameters; they are viable as long as they consider the social, environmental, and economic conditions, characteristics, and particularities of their area of influence, so that their implementation truly becomes a driver of industrial development and the production of natural ingredients, highly functional bioproducts, chemicals, fuels, and energy to promote development and well-being.
Few studies in this field consider the phytochemical extraction process from biomass, and they process the entire biomass matrix through thermochemical and biological treatments. Therefore, the proposed biorefinery considers all the value of biomass, due to the extraction of high value-added chemicals such as phytochemicals, and, simultaneously, bytransforming the residual biomass from the extraction into fuel or platform.
Theoretical models for the extraction of phytochemicals and kinetic models for thermochemical processes allow to find the best operating conditions for a biorefinery thorugh computer simulation, thus saving resources in chemical reagents and chemical processes.
Colombia has an agricultural vocation and a remarkably abundant, yet diverse source of biomass. Consequently, the country is currently searching for alternatives that improve profitability in this sector and differentiation in world-wide markets by generating added value. A profitable and sustainable exploitation of biological and genetic resources should be focused on extracting natural high-value ingredients found in this diversity and important sources of waste biomass, such as agro-industrial activities. To support the production and operation costs of the plant, the available biomass must be used rationally, and the greatest possible number of products should be manufactured. However, due to the low content of this type of substances in vegetable matrices, such processing should be conducted at facilities, like biorefineries, that guarantee an efficient extraction and a comprehensive exploitation of this renewable resource.