1. INTRODUCCIÓN
En Colombia (Suramérica), el número de plantas de tratamiento de gas (TG) ha aumentado rápidamente en los últimos años. De acuerdo con el Reglamento Único de Transporte de Colombia (Resolución 071 [1]), el gas natural extraído se debe tratar para su posterior transporte hasta obtener un contenido de dióxido de carbono (CO2) y sulfuro de hidrógeno (H2S) inferiores a 2% mol y 4 ppm, respectivamente. El proceso de absorción con aminas es uno de los más utilizados en las plantas de TG para la eliminación de estos compuestos ácidos, donde usualmente se emplea una torre de absorción [2]. La metildietanolamina (MDEA) es una amina terciaria muy utilizada en este proceso. La etapa de regeneración tiene 4 etapas principales: expansión, filtración, calentamiento y regeneración. La desorción del CO2 se produce en la última etapa del proceso en un separador, donde el CO2 se libera a la atmósfera [3]. De esta manera, estas plantas liberan altas cantidades de CO2 que podrían ser capturadas [4] y utilizadas en varias aplicaciones, con el fin de proporcionar una alternativa para reducir las emisiones de gases de efecto invernadero (GEI) [5].
Sin embargo, las condiciones de captura dependen de las concentraciones de CO2 y la presión de la corriente, y se requerirán tecnologías diferentes para el funcionamiento óptimo en términos de energía y costo. Por ejemplo, para una corriente de gas que contiene elevadas cantidades de agua saturada, se requiere la remoción de esta agua [6]. Para ello, la deshidratación con trietilenglicol (TEG) es el proceso más utilizado en la industria del petróleo y el gas (O&G), que se combina con un proceso de adsorción para la remoción de agua remanente [7]. Por otra parte, esta corriente viaja con H2S que puede eliminarse mediante un proceso de absorción con MDEA [2]. Este solvente es selectivo para eliminar H2S y los requerimientos energéticos para su regeneración son bajos [3].
Por otro lado, los procesos criogénicos pueden producir corrientes de CO2 altamente puras, pero deben considerar el uso de refrigeración y alto consumo de energía [8]. Los tamices moleculares también se pueden usar como desecantes para deshidratar las corrientes de CO2 [9]. Los adsorbentes como cloruro de calcio (CaCl2), silicatos de aluminio y tamices moleculares se pueden usar como desecantes consumibles para deshidratar CO2.
El propósito de este estudio fue establecer un diseño de proceso que permita la purificación del CO2 emitido a la atmósfera desde el sistema de endulzamiento de gas natural en plantas de TG para su posterior comercialización. Esto con el fin de ofrecer una alternativa para reducir las emisiones de GEI y generar un mecanismo de desarrollo limpio en el proceso de una planta de TG. En la industria alimenticia, el CO2 se puede utilizar en bebidas carbonatadas y como fluido supercrítico, requiriendo una pureza de entre 99,5 y 99,9% mol. Por esta razón, se simularon diferentes configuraciones y combinaciones de etapas de proceso, utilizando ProMax como simulador de procesos, para determinar la tecnología más adecuada considerando la recuperación y pureza de CO2, fácil operación y costo.
2. MATERIALES Y MÉTODOS
2.1 Planta de tratamiento de gas
En este estudio se analizó una planta de TG con una capacidad de 11780 sm3/h localizada en la ciudad de Neiva, Colombia (latitud: 2,934484 y longitud: 75,2804). Esta planta libera 1177 sm3/h de CO2 a la atmósfera, y tiene un proceso de ocho etapas descrito en la Figura 1. La primera etapa es un separador trifásico primario [1], donde se obtienen tres corrientes: agua, hidrocarburos pesados y gas agrio. La compresión mediante el uso de compresores reciprocantes es la segunda etapa (2). El endulzamiento de gas es la tercera etapa (3) y se compone de bombas centrífugas, tanque flash, intercambiador de placas, válvulas de control de nivel y temperatura, torres de contacto y regeneración. El sistema de glicol es la cuarta etapa (4), también basado en la absorción química, que elimina el agua del gas para prevenir la formación de hidratos. La siguiente etapa (5) es el sistema de ajuste de punto de rocío, donde se efectúa la licuefacción del gas utilizando los principios de Joule Thompson y refrigeración mecánica, para disminuir el contenido de compuestos pesados (C3+). El sistema de fraccionamiento es la etapa posterior (7), donde una torre deetanizadora separa el remanente de CH4 y etano de la corriente líquida proveniente del sistema de ajuste de punto de rocío; para cumplir con el parámetro de concentración de etano (<6% mol). El gas que se obtiene en el sistema de punto de rocío y en el tope de la torre deetanizadora se envía como gas de venta; mientras que los líquidos pasan a una torre de estabilización de condensados (8), y en esta se generan gas licuado de petróleo (LPG) y líquidos de gas natural (LGN).
2.2 Caracterización de la corriente de CO2 a purificar
Se tomaron muestras de la corriente de gas ácido de la torre de regeneración del sistema de endulzamiento de la planta de TG (corriente de CO2 en la Figura 1). Las condiciones de operación de la torre de regeneración de amina en el momento del muestreo fueron, en promedio, 115 °C en los fondos, 97 °C en la parte superior y 62 kPa de presión. Las muestras de gas ácido se analizaron en un cromatógrafo de gases 7890 A GC 2010 (Agilent, USA) equipado con una columna capilar de tipo fibra de vidrio (50 m de longitud, 0,53 mm de diámetro interno, 0,5 µm de espesor de película), conectada a un detector de ionización de llama (FID); y dos columnas tipo acero inoxidable (50 m, 0,5 µm, Agilent, USA) rellenas con tierra de diatomeas, conectadas a un detector de conductividad térmica (TCD). Además, se midió la humedad y la concentración de H2S en la corriente de gas ácido con un sistema Dragger (Colombia) usando el principio de medición colorimétrica.
2.3 Simulación de los procesos de purificación de CO2
La purificación de CO2 se simuló utilizando tres procesos: (1) eliminación de H2S por absorción con aminas, (2) deshidratación con TEG y (3) sistema criogénico Ryan Holmes para remoción de compuestos livianos (metano-etano). Cada tecnología se explica a continuación.
2.3.1 Proceso 1: Eliminación de H2S por absorción con aminas
La amina utilizada para este proceso fue MDEA, que se tomó del sistema de endulza-miento de la planta de TG (proceso 3 en la Figura 1), que normalmente funciona con un flujo de 0,23 m3/min, pero puede trabajar con 0,19 m3/ min sin aumentar la carga ácida de la solución. Por tanto, se tomaron 0,037 m3/min de MDEA del sistema principal de amina y se recircularon al proceso de purificación de CO2, para eliminar H2S de la corriente de gas ácido (corriente de CO2 en la Figura 1). Ambos procesos, primario y secundario, se simularon usando ProMax (Versión 3.2, Bryan Research Engineering). El paquete termodinámico para el endulzamiento de amina fue Soave-Redlich-Kwong (SRK), el cual predice las propiedades de la fase líquida por el modelo de líquido de reacción electrolítica (ELR) y las propiedades de la fase de vapor utilizando las ecuaciones de estado de Soave-Redlich-Kong (SRK) [10]. La Figura 2 muestra el sistema simulado. La corriente de CO2 entra en una torre de contacto (S1) de 6 etapas teóricas; estas son las mismas etapas teóricas de la torre real del proceso de endulzamiento de la planta de TG. Se tomaron las mismas etapas teóricas porque un número menor de etapas disminuye el tiempo de residencia y, por tanto, la absorción de H2S. La relación de etapas reales a etapas ideales fue de 3, según el modelo cinético TSWEET de ProMax, que busca un tiempo de residencia apropiado del líquido en la columna.
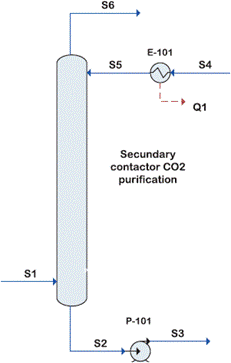
Figura 2 Diagrama de flujo del proceso diseñado en ProMax para la absorción de H2S. Las líneas azules continuas representan corrientes de materia y las líneas rojas punteadas representan corrientes de energía. Notación del equipo: P: Bomba, E: Intercambiador de calor.
De acuerdo con la Figura 2, la solución de amina de la planta de proceso de amina primaria se enfría y entra en la parte superior de la torre (S5). La amina en el fondo de la torre se envía a la etapa de amina primaria a regenerar (S3). Este proceso es posible debido a que la solución de amina usada se toma del proceso principal de endulzamiento de la planta de estudio y esto disminuye el costo de implementar un sistema de regeneración para esta tecnología. Este proceso de configuración se estableció así para conseguir la eliminación del H2S de la corriente de CO2.
2.3.2 Proceso 2: Deshidratación con TEG
La Figura 3 muestra el proceso requerido para reducir el agua en la corriente de CO2. El paquete de propiedades termodinámicas utilizado fue la ecuación de estado de Redlich-Kwong modificada por Soave, que puede describir las fases líquidas y de vapor y es adecuada para sustancias polares [9]. ProMax recomienda para el proceso de deshidratación, que la pureza típica del TEG después de la regeneración sea de 98,7% p/p y la temperatura del regenerador de glicol está limitada por la degradación térmica del TEG (204 °C). Martínez[9] mostró que las bandejas de burbujas en un sistema TEG/gas tienen un 25% de eficiencia total. En consecuencia, las etapas teóricas se dividieron por la eficiencia global para el cálculo de las etapas reales, obteniendo 28 etapas reales.
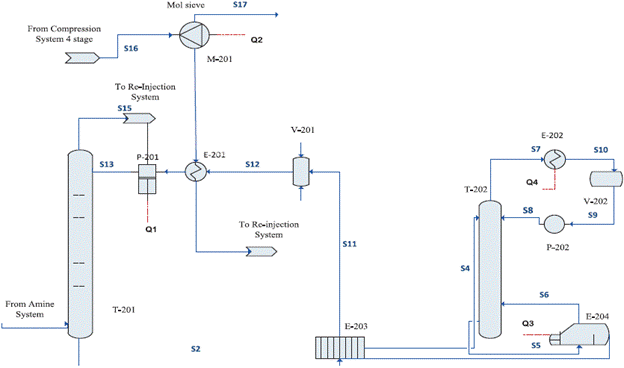
Figura 3 Diagrama de flujo del proceso diseñado en ProMax para deshidratación. Las líneas azules continuas representan corrientes de materia y las líneas rojas punteadas representan corrientes de energía. Notación del equipo: P: Bomba, E: Intercambiador de calor, V: Vasija, M: Mol Sieve, T: Torre.
En la Figura 3, el gas entra por el fondo de la torre (desde el sistema de amina de la Figura 2) y el TEG entra en la parte superior (S13). El glicol rico (S2) sale del fondo de la torre y pasa a través de un intercambiador de placas (glicol rico/pobre), donde intercambia calor con el glicol pobre para aumentar la temperatura. La solución de glicol regenerado (S12) pasa a través del intercambiador de calor de placas y luego se enfría con el gas de proceso y vuelve a la etapa de absorción (S13). Por su lado, el gas parcialmente saturado sale de la parte superior de la torre (S15). El gas a alta presión vuelve a circular a la etapa de deshidratación (S16), y a continuación, pasa a través del tamiz molécular. El diseño de un sistema de deshidratación con desecantes implica: la cantidad requerida de desecante, el diámetro y la longitud del lecho y el suministro de calor necesario para la regeneración del lecho (S17). La vasija V-201 cumple la función de sistema Make-up, que se usa en el proceso en planta para realizar las reposiciones de glicol, cuando se generan pérdidas por arrastre o para aumentar la concentración de glicol en la mezcla.
2.3.3 Proceso 3: Sistema criogénico Ryan Holmes
La Figura 4 muestra el diagrama de flujo del proceso Ryan Holmes, en el que el gas seco entra a alta presión y libre de agua. La torre de fraccionamiento tiene 6 etapas teóricas y 24 etapas reales. El paquete termodinámico utilizado fue Peng-Robinson. Esta ecuación de estado da resultados similares a los de Soave, sin embargo, es más precisa para predecir las densidades de los compuestos en fase líquida, especialmente no polares [11]. El gas sufre una caída de presión y pasa a través del intercambiador de calor, donde la temperatura cae a -40 °C (Sr2). Después de esto, pasa a una torre de fraccionamiento, donde los compuestos orgánicos volátiles como metano y etano se separan (Sr5) y el CO2 sale en la parte inferior como líquido (Sr10).
2.4 Recuperación y pureza de CO2
La eficiencia de cada sistema se determinó mediante un balance de masa en cada tecnología, dadas las entradas y salidas. Se evaluó la recuperación de CO2, de acuerdo con la ecuación 1, donde los flujos están en kmol/h, y la pureza de dicha corriente se contrastó con el valor requerido en la industria alimenticia, de mínimo 99,95% mol.
2.5 Costos de operación
La evaluación de la factibilidad económica de cada planta simulada se realizó mediante una evaluación económica clase V, de acuerdo a la American Association of Cost Engineers [12]. Estas evaluaciones generalmente se realizan para evaluar proyectos en etapa de concepto y producir estimaciones de costos totales con una precisión de predicción de entre 30 y 50%. Todas las estimaciones de costos se relacionan como costos de capital (Capex). Los costos de cada proceso se estimaron teniendo en cuenta todos los equipos y los servicios auxiliares. Por ejemplo, para estimar el costo de las bombas se tuvo en cuenta el tipo rotativo y alternativo. Para el costo de las torres de absorción, el diámetro y el número de placas teóricas. Y para el costo de los intercambiadores de calor, el área de transferencia de calor y la energía interna [13]. Los cálculos de CAPEX se realizaron siguiendo la metodología descrita por Seider y col. [14], donde para cada tecnología se estimó el costo total y los servicios auxiliares asociados. Los cálculos de la torre de absorción en el proceso de deshidratación se realizaron mediante la metodología reportada por [9]. Los costos estimados se actualizaron a 2016 usando una tasa promedio de incremento de 1,2% anual del producto interno bruto (PIB) reportado por el banco mundial [15].
3. RESULTADOS Y ANÁLISIS
3.1 Caracterización experimental de la corriente de CO2
Debido a las variaciones en la concentración del gas de entrada a la planta de (TG), se realizaron varias mediciones del subproducto de CO2 del proceso de endulzamiento en un mes para encontrar las mejores condiciones de funcionamiento, flujo no perturbado, cambios de presión y concentración en el flujo de entrada que entra a la planta de gas. Los resultados de tres muestras típicas se muestran en la Tabla 1. La variación en la concentración de las muestras depende de las condiciones de funcionamiento del sistema de regeneración en la planta de TG, porque cuando la temperatura aumenta en la parte superior de la torre, se genera un arrastre de amina en la corriente de CO2 emitida, debido a la desestabilización de la planta. De este modo, se seleccionó la muestra 1, que contenía 92% mol de CO2, 6,4% mol de agua y 276 ppm de H2S (esta composición se tomó como corriente de entrada para el proceso de purificación). Estas condiciones corresponden a los tiempos más estables de la planta sin que se hayan presentado perturbaciones en el proceso que pudieran alterar la medición.
3.2.1 Proceso 1: Eliminación de H2S por absorción con aminas
Se empleó absorción con MDEA para eliminar el H2S que viajaba con la corriente de CO2 a la salida del sistema de endulzamiento de gas, utilizando la composición de la muestra 1 de la Tabla 1 y el proceso descrito en la Figura 2. Se estudiaron dos variables de proceso, la temperatura del solvente y la presión del gas de entrada a la torre de contacto. Utilizando ProMax, se varió la temperatura del solvente entre 21 y 60 °C y la presión de gas entre 138 y 379 kPa. Los resultados se muestran en la Figura 5. El punto más alto de recuperación y pureza de CO2, y la eliminación de H2S, se obtuvo a 21 °C y 138 kPa, estas condiciones de operación favorecen la reacción exotérmica entre la amina y el H2S. La presión en el gas de entrada y la temperatura del solvente afectaron inversamente la absorción de H2S. La temperatura del solvente que entra a la torre de contacto debe ser 10 °C mayor que la temperatura del gas, para evitar la condensación de hidrocarburos [16]. Sin embargo, en este caso, y considerando que la corriente de gas tiene una alta concentración de compuestos ácidos, la temperatura del solvente podría reducirse a 23 °C. Para este caso, se verificó la viscosidad del solvente para determinar a qué temperatura dejaría de fluir, lo que ocurrió a 15 °C.
3.2.2 Proceso 2: Sistema de deshidratación con TEG
El contenido de agua en la corriente de CO2 mostrado en la Tabla 1, se eliminó por deshidratación con TEG, de acuerdo con el proceso de la Figura 3. Para ello, se varió la temperatura del rehervidor de la torre de destilación entre 149 y 204 °C, hasta alcanzar la concentración de TEG más alta en la torre de regeneración. De esta manera, se obtuvo una mayor absorción de agua libre en el gas debido a que, a mayor concentración de glicol en la solución regenerada, mayor su capacidad de absorción. Adicionalmente, para eliminar la cantidad de agua total de la corriente de gas, se incluyó un tamiz molecular a la salida del tope de la torre contactora del sistema de des-hidratación, donde el gas pasó a través del lecho adsorbente y retuvo selectivamente las moléculas de agua, hasta llevar la concentración de agua a 0% mol en la corriente S17 [6].
3.2.3 Proceso 3: Sistema criogénico Ryan Holmes
La tecnología Ryan Holmes de la Figura 4 se empleó para purificar el CO2 por procesos criogénicos. La Figura 6 muestra el efecto de variar la temperatura y la presión de la corriente de entrada al proceso sobre la recuperación y pureza de CO2. Para obtener la máxima recuperación de CO2 en la parte inferior de la torre, se requirió una presión de 2758 kPa y una temperatura en el condensador de -40 °C. Para la torre de fraccionamiento, se establecieron 6 etapas teóricas, teniendo en cuenta las condiciones de diseño definidas en el simulador de procesos (ProMax) para procesos criogénicos. El aumento del número de las etapas de la torre no varió la recuperación de CO2 ni el perfil de la torre, ya que este proceso estaba en su máximo punto operativo. El método CDC (condensación y destilación criogénica) se ha empleado para la eliminación de CO2 en mezclas de CH4/CO2 y otros gases usados en la recuperación de hidrocarburos de fuentes naturales. Este proceso requiere un consumo elevado de energía cuando la concentración de CO2 en los gases de entrada es baja [8].
3.3 Recuperación y pureza de CO2 de las tecnologías simuladas
El objetivo de este estudio fue proponer un proceso de purificación de la corriente de CO2 desechada en los sistemas de endulzamiento de gas, que permita su posterior uso en la industria alimenticia, donde el CO2 debe tener una pureza superior al 99,95%. La Tabla 2 muestra los resultados de máximas recuperación y pureza de CO2 obtenidos con cada tecnología, además de su comparación con otras tecnologías reportadas. El Proceso 1: Eliminación de H2S por absorción con aminas arrojó valores de pureza y recuperación de CO2 considerablemente elevadas. El Proceso 2: Deshidratación con TEG, que incluyó un tamiz molécular, entregó una pureza de CO2 de 99,81%, con una recuperación de 99,74%. La adsorción con tamiz molécular se ha reportado con recuperaciones del 95% [17], superadas en este estudio por su combinación con un sistema de absorción con TEG. Las mayores recuperación y pureza de CO2 se obtuvieron con el Proceso 3: Sistema criogénico Ryan Holmes (99,91 y 99,90%, respectivamente). La recuperación del Proceso 3 se ha reportado como superior al 95% y produce CO2 líquido de alta pureza [17]. Sin embargo, ninguna de las tecnologías alcanzó los estándares requeridos por la industria alimenticia de manera aislada. Por ello, se diseñaron combinaciones para aumentar la pureza de la corriente de CO2. La combinación (1) integró los procesos 1 y 2, finalizados con un proceso de compresión. Esta combinación arrojó una corriente de CO2 con una pureza de 99.83% y una recuperación de 99,85%, debido a la combinación de la absorción y la adsorción. La capacidad del sistema de absorción depende de la saturación de gas de TEG; sin embargo, la combinación del sistema de deshidratación y el tamiz molecular es significativamente eficaz en la purificación. No obstante, la combinación aún no entrega una corriente lo suficientemente pura para la industria alimenticia. Esta corriente podría ser usada en el recobro mejorado del petróleo en campos de la misma planta de gas [2]. Finalmente, la combinación 2, que incluye los tres sistemas simulados, permite obtener una corriente de CO2 con la pureza requerida por la industria alimenticia en la fase líquida. Además, el CO2 producido en fase gaseosa se puede comercializar para usos de menor pureza.
La flexibilidad operacional de las tres tecnologías se analizó con base en las condiciones de operación de los procesos diseñados. La Tabla 2 muestra dos niveles de flexibilidad operacional: moderada y baja. Los procesos 1 y 2 presentan flexibilidad moderada debido a que el control de las condiciones de operación es relativamente sencillo por la experiencia de la industria O&G en estos sistemas. Mientras que, en sistemas criogénicos como el Ryan Holmes, se requerirá una mayor supervisión debido a la manipulación de fluidos supercríticos, lo que la cataloga con una flexibilidad operacional baja.
3.4 Costos de inversión
La Tabla 2 muestra los costos de inversión de capital (CAPEX) de las tecnologías y sus combinaciones. Los valores se presentan como costo total en dólares (USD) y normalizados por tonelada de CO2 tratada [5]. Se observa que el aumento de pocos puntos porcentuales en la pureza del CO2 requiere aumentos en las inversiones de capital de más de un orden de magnitud. La combinación 1, aunque no logra la pureza requerida para la industria alimenticia, puede producir un CO2 apto para su reinyección en los pozos de petróleo y otros usos para diferentes industrias a un costo competitivo [20], con un valor de 37 USD/tCO2. Los procesos que involucraron el sistema criogénico mostraron altos costos debido a los procesos de compresión y secado de gas a bajas temperaturas, donde el CO2 obtenido está en fase líquida. La combinación 2 es 31% más costosa que la combinación 1, pero entrega el CO2 requerido.
De esta manera, la corriente de CO2 emitida en las plantas de endulzamiento de gas puede tratarse por una combinación de sistemas de absorción con MDEA para retirar el H2S, de deshidratación con TEG para retirar la humedad y de purificación final por un proceso criogénico Ryan Holmes. Esta combinación de procesos tendría unos costos de inversión cercanos a 53 USD/ tCO2, para un CO2 que puede comercializarse a valores superiores a 5000 USD/tCO2. La tecnología de Oxy-combustión de CO2 ha reportado costos de 52 USD/tCO2, similar al resultante de la combinación 2. De la misma manera, la combinación 1 arroja un valor de 37 USD/tCO2, menor comparada con las tecnologías mencionadas, con un CO2 de pureza apta para variadas aplicaciones [20].
4. CONCLUSIONES
En este trabajo se simularon tres procesos para la purificación del CO2 emitido en una planta de tratamiento de gas natural. El Proceso 1, consistente de la eliminación de H2S por absorción con aminas, produjo una pureza y una recuperación de CO2 de 98,72 y 94,02%, respectivamente. El Proceso 2: Deshidratación con TEG combinado con tamiz molecular, entregó una pureza de CO2 de 99,81% y una recuperación de 99,74%. El Proceso 3: Sistema criogénico Ryan Holmes entregó una recuperación y una pureza de CO2 de 99,91 y 99,90%, respectivamente. Debido a que ninguna tecnología por sí sola entregó el objetivo de pureza de CO2 de 99,95% mol para su uso en la industria alimenticia, se ensayaron diferentes combinaciones. La combinación de las tres tecnologías permite obtener un CO2 al 99.95% mol en la fase líquida del proceso. Los costos de las tecnologías oscilaron entre 4 y 53 USD/tCO2, relacionados directamente con la pureza obtenida.
De esta manera, la purificación del CO2 emitido en plantas de endulzamiento de gas natural por la combinación de sistemas de endulzamiento con MDEA, deshidratación con TEG y sistema criogénico Ryan Holmes, puede entregar corrientes de CO2 de alta pureza (99,99%) que puede ser usado en la industria alimenticia, con un costo de inversión comparable a otras tecnologías de captura de CO2 (53 USD/tCO2).