Introducción
A lo largo de la historia de humanidad, los materiales han desempeñado un papel crucial en la evolución y la creación de nuevos productos que satisfagan las necesidades del ser humano, pero, al mismo tiempo, el aumento en el consumo de estos productos ha generado un aumento acelerado de residuos a nivel mundial. En el caso de Colombia, se estima que se producen aproximadamente 30.000 toneladas de residuos sólidos al día, de los cuales 92 % son llevados a rellenos sanitarios y únicamente un 5 % es reutilizado. Esto se traduce en un deterioro ambiental, debido a que el mal manejo de estos residuos contamina el agua, el aire y el suelo, produciendo enfermedades e infecciones que atentan directamente contra el ser humano. Esta problemática también ha evidenciado la necesidad de explotar racionalmente los recursos y crear nuevos objetos a partir de los desechos producidos 1. En este mismo orden, la celulosa residual obtenida de la producción de empaquetaduras para la industria automotriz es desechada, contribuyendo de este modo a la generación de más residuos. Esta investigación tiene como objetivo principal alargar el ciclo de vida del material, utilizándolo para el mejoramiento de materiales basados en caucho natural. Se realizaron diferentes mezclas de caucho y celulosa, con diferentes granulometrías, y estas fueron analizadas mediante ensayos de flexión, abrasión, tensión y desgarre, con el fin de conocer las propiedades del material.
Los polímeros 2 presentan ventajas como la resistencia, la dureza y la habilidad para absorber energía. Además, son ligeros e implican bajos costos en su fabricación. Por el lado de las desventajas, cabe mencionar la baja resistencia a altas temperaturas, la fragilidad a baja temperatura, la baja resistencia al desgaste, abrasión y la baja resistencia a radiaciones ultravioleta, gama y nuclear 3. Entre los polímeros se encuentran los elastómeros 4, cuya principal característica es que pueden ser estirados muchas veces su propia longitud para luego recuperar su forma original sin una deformación permanente. En esta familia se encuentra el poliisopreno, o caucho natural, proveniente del árbol de Hevea Brasiliensis 5. El caucho natural contiene carbono (C) e hidrogeno (H) en su composición química, en la relación atómica de 5 a 8 respectivamente (C3H8)n 6.
Por otro lado, se encuentran los cauchos originados por la industria del petróleo, tales como el polibutadieno, el poliisobutileno y los poliuretanos 7. El caucho natural o poliisopreno, debido a sus excelentes propiedades, puede ser usado en aplicaciones en la industria naval y la aeronáutica, entre muchas otras más 8. Sin embargo, las propiedades físicas y químicas del caucho dependen no solo de su formulación, sino también de diferentes factores como las condiciones de reticulación. En el caso del caucho natural, también son de importancia los factores geográficos, el clima y la humedad del lugar donde se encuentre el árbol de donde se extrae el látex 9.
Por otro lado, mediante la adición de azufre (generalmente) como componente activo de la reticulación (proceso también conocido como entrecruzamiento), los sistemas de vulcanización se clasifican en mono-, di- o polisulfídicos, que representan los tipos de puentes generados en el sistema y aportan propiedades diferentes al caucho vulcanizado. Así mismo, se requiere el uso de cargas o aditivos para el proceso de vulcanización, tales como el negro de humo, la sílice y el carbonato de calcio, en diferente granulometría para originar propiedades fisicomecánicas propias en cada sistema de mezcla. La calidad y las propiedades de los elastómeros dependerán del volumen utilizado de caucho, los vulcanizantes, los plastificantes, los antioxidantes, los acelerantes, los activadores, los retardadores, los rellenos y los ingredientes de la mezcla y sus cantidades de n partes del material por 100 partes en peso del caucho, conocido usualmente como phr (Parts per Hundred Rubber) 10.
Por otro lado, la celulosa residual, en adelante CR (C6 H10 O5), es obtenida a partir de los resíduos que genera la industria de los empaques de motos en Medellín. Generalmente, estas fibras naturales de celulósicas pueden ser extraídas de diferentes tipos de plantas, las cuales han sido utilizadas en la industria automotriz, papelera y de construcción, entre otras 11.
Materiales y métodos
El caucho natural utilizado en esta investigación fue el caucho TSR-10 producido en Colombia. La celulosa residual fue suministrada por la empresa Empaques Gasko, dedicada a fabricar empaquetaduras para motos. El caucho natural TSR-10 y el sistema de vulcanización fueron tablasuministrados y preparados en las instalaciones de la empresa Montesuelas, ubicada en Medellín. En primera instancia, la celulosa fue procesada en una máquina trituradora, con el fin de disminuir su tamaño a malla ASTM 325 (45 micrones). Los materiales utilizados en el sistema de mezcla están citados en la Tabla I. Se utilizó caucho natural TSR-10, viscosidad Money 70-90. Para la realización de las muestras, se prepararon cuatro mezclas diferentes, variando el porcentaje de residuo de celulosa. El proceso de masticación se llevó a cabo por 15 minutos, y el proceso de vulcanización a 160° C por 5 minutos. Las cantidades del sistema de vulcanizado se encuentran en phr
Para la producción de los compuestos, se mezclaron caucho natural, el sistema de vulcanización y los residuos de celulosa en un mezclador de rodillos de cámara abierta durante 20 minutos a 60° C y fricción 1,0:1,25. Posteriormente, se adicionaron los agentes vulcanizantes a la mezcla. Las proporciones de materiales (reactivos) utilizados para la preparación compuesta están citados en la Tabla I, dónde la cantidad de 225 phr de sílice funge como sistema de refuerzo. Posteriormente, los compuestos se prensaron térmicamente a 5 toneladas y 160° C durante su respectivo tiempo óptimo de vulcanización (t90) de 5 minutos, obtenido mediante la técnica de reometría, la cual es propia del sistema de mezcla de Montesuelas. Luego de triturar la celulosa proveniente del sistema de descarte de la empresa, se procedió a realizar el picado y el posterior tamizado para obtener las diferentes granulometrías, tal y como se observa en la Tabla II.
El material en análisis está enfocado en la industria del calzado, razón por la cual las pruebas preliminares para continuar con la investigación se centraron en los siguientes cinco métodos de caracterización:
Resistencia a la tensión: se utilizó la máquina universal de ensayos, en la cual se realzaron análisis en triplicado, siguiendo los parámetros de la Norma ASTM D-412 12.
Resistencia a la abrasión: se evaluó utilizando un dispositivo de tambor cilíndrico y una máquina de abrasión (Maqtest). El cilindro debe tener un diámetro de 150 ± 0,2 mm y una longitud de unos 500 mm, así como girar a una frecuencia de 40 ± 1 min - 1. Las muestras fueron preparadas según ASTM D 5963-97 (método A), en tres repeticiones para cada compuesto, implementando muestras cilíndricas con diámetros de 16 ± 0,2 mm y un espesor de 6 mm. Las pruebas se llevaron a cabo a lo largo de 40 m (ruta de fricción) bajo fuerza aplicada de 5 N, según la norma UNE-ISO 4649:2013 (método A). Los resultados se expresan por la pérdida por abrasión en mm3 , es decir, la pérdida en peso dividida por la densidad del material; entre menor sea el resultado, mayor resistencia a la abrasión tiene el elastómero.
Ensayo de flexión para suelas: se realizó en un flexómetro de suelas (marca Maqtest, modelo C115), siguiendo la Norma UNE-EN ISO 20344:2012, numeral 8.4.2. En esta técnica se evalúa el rendimiento de la suela del calzado en una cantidad determinada de ciclos durante 72 horas continuas, sin romperse o marcar una línea de rotura.
Resistencia al desgarro: esta prueba se llevó a cabo en una máquina universal de ensayos (marca Lloyd Instruments, modelo EZ 20). Con esta técnica se mide la resistencia a que se propague una grieta bajo los esfuerzos que ha de soportar un elemento en servicio o en el propio proceso de fabricación. La fuerza se aplica perpendicularmente a la dirección de propagación del desgarro, y los resultados se expresan por el valor mediano de la tensión del desgarro, el cociente de la fuerza, medida en N y el espesor de la probeta medido en mm. La unidad SI correspondiente es N/mm.
Densidad relativa de cada mezcla en g/cm3 , el ensayo se realizó siguiendo los parámetros de la Norma UNE-ISO 2781:2015 (método A), con agua destilada a 23 2° C.
Resultados
En primer lugar, se llevó a cabo la trituración de los residuos provenientes del sistema de descarte, para lo cual se utilizó un molino triturador de plásticos industrial. Posteriormente, el material fue tamizado en un equipo electromecánico; el proceso se realizó en varias sesiones de 15 minutos y se utilizaron 100 g de material en cada sesión de tamizado. En la Fig. 1 se evidencia la presentación inicial de los residuos hasta el proceso de tamizado. Las mallas utilizadas y la granulometría se mencionan en la Tabla II. Con estas se realizaron cuatro diferentes mezclas (A, B, C y D). La mezcla de la celulosa y el sistema de vulcanización fue llevada a cabo en un molino industrial de cilindros abierto.
Luego de realizadas las mezclas en el molino de cilindros, se tomaron las muestras de suela de calzado, utilizando molde cerrado y termo-conformado a una temperatura de 160 °C por 5 minutos, tiempo determinado por el sistema de mezcla en la empresa de calzado (elementos ilustrados en la Fig. 2). De esta manera se generaron las probetas para análisis de flexión.
Densidad relativa
La Tabla III muestra las densidades de la masa de las tres probetas con las cuales fueron calculadas, entre otras, la densidad relativa de la muestra A, producto del promedio del peso de la muestra al aire y sumergida en agua. Se hace evidente la poca variabilidad en los datos de las diferentes muestras (Tabla IV), teniendo en cuenta que los cuerpos de prueba fueron elaborados con el mismo sistema de vulcanización. La poca variabilidad observada en los datos puede deberse a la diferencia de material durante la elaboración de las probetas.
Resistencia a la abrasión
La determinación de la resistencia a la abrasión se realizó utilizando un dispositivo de tambor giratorio UNE-ISO 4649:2013 (método A), donde una pieza de la mezcla se desliza sobre una lámina abrasiva (de grado abrasivo específico) a una presión definida. Luego de esto se calculan la pérdida de masa y volumen de la pieza y se comparan con la de un compuesto de referencia sometido a un ensayo en las mismas condiciones.
En la Fig. 3 se ilustran el molde y el material al momento de realizar el proceso.
Con base en los resultados mencionados en la Tabla V, se observa que la mezcla con el mejor índice de resistencia a la abrasión fue la muestra C, dato que corresponde al bajo porcentaje de estiramiento registrado en el análisis de tensión, el cual está relacionado con la baja movilidad de las cadenas poliméricas y un alto valor de rigidez de la muestra, posiblemente producto de la interacción entre las partículas de celulosa y la matriz de caucho natural. Dado que los datos de resistencia a la abrasión son positivos dentro de este análisis, un número menor de 100 IAR indica una naja resistencia a la abrasión, en comparación con el caucho patrón. De igual manera, es de resaltar que, dentro del sistema de vulcanización, no existen sistemas de refuerzo como lo son habitualmente el negro de humo o la sílice, con los cuales aumenta la resistencia a la abrasión 13, 14.
Ensayo de flexión de suelas
El ensayo de flexión para suelas se realizó en un flexómetro de suelas marca Masqtest modelo C115 serial 44. La prueba consistió en realizar una incisión normalizada a las suelas, a través de todo el espesor rectangular y luego someterla a un número determinado de flexiones repetidas (30.000) de 90° y luego medir el incremento de la incisión, en la figura 4 se ilustra el montaje de los cuerpos de prueba en el equipo de ensayo.
En el caso del ensayo de flexión, para cada muestra se analizaron tres probetas como análisis preliminar de la investigación. Los resultados obtenidos luego de los 30.000 ciclos de flexión se presentan en la Tabla VI. Estos valores son promisorios, pues se obtuvieron valores similares a los de las mezclas internas de la empresa. Aun así, no hay valores publicados con los cuales comparar estas pruebas, lo cual demuestra que este campo aún se encuentra poco explorado y difundido con respecto a la ciencia de los elastómeros y su caracterización en el sector del calzado.
Tabla VI Comparativa de resultados del análisis de flexión en suelas fabricadas con residuos de celulosa
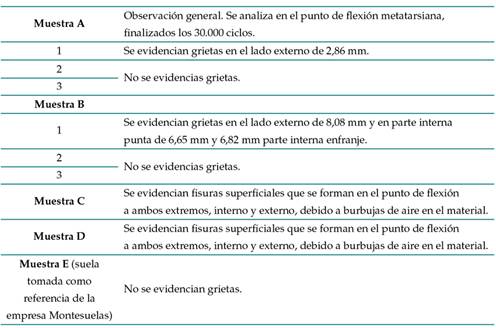
De acuerdo con los resultados presentados, se identificó que las muestras que mejor se comportaron finalizados los 30.000 ciclos fueron la muestra A, realizada con partículas inferiores a 600 µm, y la muestra B, con partículas inferiores a 850 µm, puesto que hubo un mayor porcentaje positivo en el que no se evidenciaron grietas. En las mezclas C y D, a pesar de las burbujas de aire que se presentaron en el material, solo se evidenciaron fisuras superficiales en la muestra. Con base en lo anterior, y tomando como la muestra principal la suela E (suela promedio), fabricada por la empresa Montesuelas, se corrobora que las muestras que mejor se comportaron en comparación con esta fueron la A y la B, puesto que hubo un mayor porcentaje en el que no se evidenciaron grietas, igualando de este modo su comportamiento al de la muestra E.
Análisis de tensión y deformación
Las propiedades de resistencia a la tracción para las mezclas se determinaron según la prueba estándar para propiedades de tracción de plásticos de la marca universal de ensayos Lloyd Instruments (modelo EZ 20), a una velocidad de deformación de 500 50 mm/min. Se inició el ensayo observando la distancia entre las marcas de referencia. Se registró la fuerza de elongación especificada para la prueba y el momento de ruptura.
Los resultados obtenidos se muestran en la Tabla VII. Se observó que la resistencia a la tensión incrementa de acuerdo con la reducción en la granulometría utilizada: entre más finos los residuos de la celulosa, mejor el comportamiento, tanto en la tensión como en el porcentaje de elongación hasta la ruptura. Al mismo tiempo, se observó que, a medida que aumentaba la cantidad de celulosa agregada, aumentaba la resistencia a la tensión, efecto reportado por otros autores hasta cantidades de 30 phr 15, 16, teniendo en cuenta que esto se aplicó en torno al 20 % de residuos sin agentes de refuerzo. Los datos obtenidos fueron positivos para las granulometrías i.e., cercanas a los 600 µm, con un tamaño promedio de 15 micras.
Resistencia al desagarro
El ensayo para determinar la resistencia al desgarro se llevó a cabo en una máquina universal de ensayos marca Lloyd Instruments (modelo EZ 20) y se basó en someter a tracción una probeta rectangular que presenta un corte parcial central desde uno de sus lados, para luego registrar la fuerza media ejercida durante la separación de la probeta.
Se evidencia que no solo la granulometría, sino también la cantidad de celulosa influyen en el resultado. En la investigación sobre caucho natural reforzado con biomasas renovables 17, la resistencia al desgarre va disminuyendo a medida que aumenta el porcentaje de bagazo. En nuestro caso, se presenta una pequeña variación: la resistencia al desgarre se ve afectada en principal medida por la granulometría de la celulosa. En la muestra C, elaborada con la granulometría menor, se presenta un menor comportamiento en comparación con las muestras B y C (mayores de 600 µm pero menores de 850 µm), según se observó en los análisis de resistencia a la rasgadura, la dureza, la abrasión y la tensión.
Dureza shore A
Este ensayo se realizó en las condiciones sugeridas por la norma ISO 23529 para materiales elastoméricos a 10 N de fuerza aplicada. Uno de los objetivos fue obtener información relevante entre la densidad relativa y sus posibles alteraciones con las partículas de refuerzo y el sistema de vulcanizado. De esta forma fue posible focalizar las posibles aplicaciones a nivel industrial.
Se identificó que la mezcla B, que contiene un 14 % de CR, obtuvo el mayor valor de dureza, presentando una media de 70 shore A, lo que indica, que entre más alto sea el porcentaje de CR añadido a la mezcla, mayor será su dureza. Además, tomando como referencia otras investigaciones similares, se notó que, en el caso de un material compuesto a partir de celulosa y poliestireno expandido residual, la mezcla con 11 % de CR presentó una media de 60, i.e., resultados similares que corroboran que, a mayor cantidad de celulosa, mayor dureza 18.
Conclusiones
A través de los resultados, es posible concluir que la granulometría más adecuada para las mezclas es la de menor tamaño, i.e., las partículas entre 600 y 850 µm presentaron la mejor relación con el sistema de vulcanización utilizado que las que contaban con una granulometría superior.
La resistencia al desgarre permitió observar una reducción lineal correlacionada con el incremento en la granulometría del residuo.
La mayor resistencia a la abrasión fue reportada por la muestra con el tamaño de partícula intermedio, posiblemente debido a la mejor interacción entre los constituyentes, mecanismo que favoreció la mejor distribución de cargas durante el ensayo.
Haciendo un análisis general, se evidencia que el residuo presentó buenas propiedades, específicamente frente a la flexión de la suela, y que podría ser utilizado como sistema de carga en el sector del calzado. Además, se presentó el efecto adicional de la trasmisión del color del residuo a la muestra, el cual, a simple vista, fue homogéneo y no mostró distorsión durante las pruebas.
Es necesario profundizar en la caracterización de este residuo industrial y su aplicación en el sector del caucho para obtener información sobre su posible influencia en las propiedades fisicomecánicas, pero, sin dudas, esta es una gran posibilidad de uso del residuo, dados sus buenos resultados en esta investigación preliminar.