1. INTRODUCTION
Produced water from oil and gas industry may include water injected during extraction operations in the form of high-pressure steam [1], [2]. Depending on whether natural gas, shale gas or crude oil is being produced, the water has particular characteristics [3]. These waters generally contain high amounts of hydrocarbons (oil and greases), dissolved solids, inorganic and toxic compounds, and naturally occurring radioactive materials (NORMs), as well as microorganisms. This water is re-utilized in different processes, including reinjection for enhanced oil recovery, hydraulic fracturing or final disposal on natural water sources [4].
For the control and / or elimination of native microorganisms present in produced water (including SRB and APB, it is possible to use both physical and chemical methods. Chemical methods are mainly based on chemical biocides, often combining physical removal type membranes or filters [2]. However, long term applications of biocide have translated into decreased efficiency of bacteria elimination, mainly due to factors such as high organic material levels in water, inactivation of the chemical product by reaction with other molecules, and possible emergence of genes resistant to antimicrobial products used in biocide formulations.
Once injected into the well, the biocide performance will decrease due to chemical interaction with the reservoir, high temperature and pressure conditions, and possible self-polymerization reactions [5].
On the other hand, control of these bacterial populations in injection waters can be performed by means of other physical, chemical and/ or biological strategies. Among these, the most widely reported are micro-filtration or osmosis, depending on the flow and quality of the water; use of high temperatures such as pasteurization, and oxidation by the use of ozone or chlorine, or treatment by radiation with germicidal ultraviolet light.
For almost a century, the germicidal effect of ultraviolet light at specific wavelengths has been well known. In recent years, the use of ultraviolet radiation has increased given the benefits that it offers against chemical disinfection, as it does not alter chemical and physical water properties, does not add toxic compounds or precursors to water, and is effective against any microorganism, including bacteria, fungi, yeasts, algae and even viruses in short-time treatments [6],[7],[8].
Germicidal ultraviolet or ultraviolet C irradiation (UV-C) in the electromagnetic spectrum is near a wavelength of 254 nm. This radiation causes cell death when it is directly exposed and producing DNA damage to the cells (Figure 1). The most frequent DNA damage is the appearance of pyrimidine cyclobutene dimers and pyrimidone-pyrimidine photoproducts, where two adjacent pyrimidines are covalently linked. It is also possible to find adjacent junctions of strongly bound thymine. These molecular processes produce failures to transcribe and translate efficiently the DNA into proteins and cellular replication, which ends up leading to cell death [9].
Not all bacteria die with the same amount of ultraviolet dose. The sensitivity varies and a microorganism can be better protected and more resistant than others. The UV dose required depends on the type of bacteria. For example, E. coli requires a dose of 5-6 mWs/cm2 for a LOG 1 reduction (90%). In theory, a UV dose of 18 mWs/cm2 (3 times the LOG-1 value) should produce a LOG 3 reduction (99.99%). However, in practice, the number of suspended solids and changes in transmittance (T), affect the UV dose theoretical value [10]. The different uses of water may require different application doses, based on the type of microorganisms and the correct elimination rate [11]. For injection water systems with low turbidity (approximately 1-50 NTU), the efficiency of bacteria removal with UV treatment depends on the quality and turbidity level of the water. Hence, it is recommended to carry out specific tests for each application case and determine the relationship between the variables that influence the process such as suspended solids (turbidity), bacteria titer, residence time, fluid flow and homogenization.
These variables are material in treatment efficiency and must be particular to each case study. Hypothetically, in water with high turbidity, caused by solids and/or bacteria, the flows must be reduced or the residence time increased, and require adequate homogenization to reach the desired treatment efficiency. In Figure 2, the phenomenon of self-shadow or radiation blockage by high amount of suspended solids in the water can be observed.
There is another phenomenon in the genetic material damage caused by UV-C, which is the self-repair due to the light effect. The production of reparative photolysis enzymes in the damaged areas frequently allows replication of DNA, and transcription and translation of RNA, and depending on the exposure time, the generation of cells without associated mutations is possible. However, this process occurs mainly in the presence of light. The aim of this study was to evaluate the use of UV-C radiation as a physical strategy complementary to the current processes used for the control of sulfate-reducing and acid-producing bacteria present in injection water from the oil & gas industry [10],[11].
2. EXPERIMENTAL DEVELOPMENT
The UV-C radiation effect was evaluated on SRB at laboratory scale in Petri dishes to find out the adequate exposure time. Therefore: triplicate tests of an agar plate were first spread with samples containing sulfate reducing bacteria and then, petri dishes were exposed to UV-C radiation (lamp 20 cm distant from the petri dish) at different times (10-120 seconds).
Next, a design of the UV system in continuous process was operated for treatment of injection water. Figure 3 is a schematic design of the UV system for water treatment.
A prototype was built containing an inlet water plug connecting the UV lamp column, using different hydraulic residence times (HRT), ranging from 1 to 20 min (Equation 1). A column operative working volume of 1360 mL was used, and a variable inflow was set to obtain several HRT values and assess the efficiency of UV-C radiation treatments.
HRT = V / Q
Equation 1. Hydraulic residence time
Where:
V: is the effective volume of the water column or container (mL)
Q: is the inlet flow to the column (mL/ min)
HRT: is the real time of water exposure to UV radiation (min)
The lamp used was a low-pressure tubular type with 8W of power and a wavelength emission of 253 nm. The radiation dose or intensity used in experiments was 2mWs/cm2.
Treatment Efficiency:
Specific culture media were used to enumerate SRB and APB (Postgate B and Red phenol culture broth, respectively) by using the serial dilution method to assess the radiation performance. In addition, SRB was analyzed by quantitative PCR (qPCR) matching the dsrA gene fragment; this gene is specific for SRB bacteria and the method allows to accurately quantify the bacteria titer present in a water sample The experimental assays were carried out using water with greases and oils (G&O) of 32 ±0.2 ppm, total suspended solids (TSS) of 70 ± 0.5 ppm, and a turbidity of 15 NTU. Injection water without biocide from a water treatment system of Ecopetrol field was used for all experiments.
3 ANALYSIS OF RESULTS
Initially, UV-C treatment tests were carried out with different exposure times on culture plates to find the ranges of treatment times in the continuous system. Figure 4 shows the results after exposure to UV-C of a SRB consortium Isolated from production water from a Colombian oil field.
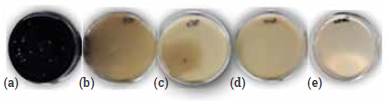
Figure 4 Effect of UV-C on culture plates to different exposure time: (a) No exposure; (b) 10 seconds; (c) 30 seconds; (d) 60 seconds; (e) 120 seconds.
It is observed that with 60 seconds of direct radiation exposure (50 cm away from the lamp to the plate), microbial growth is inhibited by 100%. These tests were carried out to determine the shortest effective time for treatment; however, it Is important to point out that the dynamic fluid conditions are different from the plate culture (static condition). Real conditions (industrial water treatment systems and its autochthonous mlcrobiota) may need more exposure time due to suspended solids present In the sample. Figure 5 shows the laboratory scale system used in the treatment of Injection water from a Colombian oil field.
According to equation 1, the input flow of the system was modified to evaluate different exposure times to UV-C radiation.
UV-C TREATMENT
The results of the treatment at different exposure times are shown in Tables 1 and 2. SRB and APB counts were made before starting the treatment. The control treatment corresponds to 20 minutes inside the system without radiation application, sampling at the inlet and the column outlet. Other treatments correspond to different times of radiation exposures, withdrawing samples before and after the UV-C treatment. Tables 2 and 3 show bacterial counts at different times of UV-C exposure of the injection water:
Table 1 Effect of different exposure times on microbial growth of SRB determined by serial dilution method
Exposure time (minutes) | Sample site | |
---|---|---|
Bacterial titer (cells/ml) | ||
Inlet | Outlet | |
Control (20 min) | 1000 | 1000 |
1 min | 1000 | 10 |
2.5 min | 1000 | <10 |
5 min | 1000 | <10 |
10 min | 1000 | <10 |
20 min | 1000 | <10 |
Table 2 Effect of different exposure times on microbial growth of SRB determined by qPCR method
Exposure time (minutes) | Sample site | |
---|---|---|
Bacterial titer (cells/ml) | ||
Inlet | Outlet | |
Control (20) | 32110±55 | 38012±38 |
1 | 21541±32 | 154±11 |
2.5 | 33215±41 | 10±1 |
5 | 45201±15 | ND* |
10 | 35200±29 | ND* |
20 | 15647±38 | ND* |
ND*: Not detected
Control tests in continuous mode have no radiation exposures, but these controls were performed with a HRT of 20 minutes to set the most critical condition in the different treatments. Treatments at shorter UV-C radiation exposure times (1 min) display a bacterial growth reduction from 1000 to 10 cells/mL, showing removal efficiencies of SRBs of 99%. Other UV-C radiation treatments (2.5 to 20 min of exposure) achieved 99-100% of SRB removal efficiency (Tables 1 and 2). Figure 6 shows the results of the SRB and APB growth cultured in serial dilution with twice the exposure to UV-C (2 and 10 minutes) versus the control without exposure to treatment. There is no growth observed in any of the culture media for either of the two treatments applied.
ADVANTAGES:
Wang et al [12] in 2005 carried out an economic analysis of this technology (UV-C treatment) for oil and gas industry water. The results obtained from this study indicate that the cost of the UV treatment of 12,000 hours (1.4 years), including investment costs, depreciation, electricity, maintenance, cleaning and operation amounts to US$ 0.008 per cubic meter (m3) of treated water, while the average cost of chemicals biocides is US$0.035 per m3 of treated water (US$ 879 per ton at a continuous dose of 40 ppm) In summary, UV-C technology could be roughly 1/5 of the cost of applying chemical products. UV treatment represents an alternative clean strategy for treatment of Injection water, which does not generate secondary contamination, restrictions of use near natural and surface water, production of any corrosion type, nor films or thickening forming in water nor Incompatibility with other applied chemicals or with secondary recovery polymers.
A further advantage is that when biocidal chemicals are used time-kill tests must be performed in advance to determine the appropriate dose and exposure time. In addition, several product evaluations must also be performed for each field and aimed for best in class products. However, these biocides are generating microbial resistance, which forces new strategies of biocide application such as product rotation or dose Increasing to reduce this risk. Additionally, with the use of UV radiation, operating conditions such as exposure time and water turbidity should be standardized, but they are always simpler and easily operated variables [13,14],Moreover, Kai Song et al. [15], have reported the use of LED bulbs for substantial improving on the efficiency of UV radiation as a strategy for eliminating bacteria: as this offers the possibility of using different wavelengths (UV-C: UV-B and UV-A ) in the same treatment, which is an advantage that cannot be achieved when using mercury lamps.
CONCLUSIONS
Treatment with UV-C light of injection water containing TSS and G&O at different exposure times led to an efficient control of the main bacterial populations (SRB and APB) associated with biocorrosion and souring.
By using two different but complementary methodologies for both microbial detection and enumeration, it was possible to evaluate the cell viability of these bacteria after exposure to UV-C treatment.
qPCR allowed quantification of a greater microbial diversity than the culture media although it did not reflect the state of the post-treatment cell. However, the results of both methods showed that the UV-C treatment is highly efficient to eliminate SRB and APB from injection water in minutes (2-10), offering a very interesting possible solution to microbial influenced corrosion risk in oil and gas industry facilities.
It is suggested to continue this investigation on a pilot scale, and verify its efficiency, added to installation, maintenance and operation cost of this strategy, which could eventually replace or alternate the use of chemicals applied to water.