Services on Demand
Journal
Article
Indicators
-
Cited by SciELO
-
Access statistics
Related links
-
Cited by Google
-
Similars in SciELO
-
Similars in Google
Share
Ingeniería y competitividad
Print version ISSN 0123-3033
Ing. compet. vol.17 no.1 Cali Jan./June 2015
Mitigación de defectos en productos manufacturados
Mitigation of defects in products manufactured
Alexander D. Pulido-Rojano*
E-mail: apulido3@unisimonbolivar.edu.co
Carlos A. Bocanegra-Bustamante**
E-mail: cbocaneg2@cuc.edu.co
* Departamento de Ingeniería Industrial, Universidad Simón Bolívar, Barranquilla, Colombia
** Departamento de Ingeniería Industrial Universidad de la Costa. Barranquilla, Colombia.
Eje temático: INGENIERÍA INDUSTRIAL/INDUSTRIAL ENGINEERING
Recibido: Mayo 04 de 2014
Aceptado: Febrero 6 de 2015
Resumen
La presente investigación propone un proceso de mejora continua en el que se combinan herramientas estadísticas de calidad, como los gráficos de control, el diagrama de Pareto y el diagrama causa-efecto y el proceso de gestión de riesgo contenido en la Norma Técnica Colombiana-NTC 5254 e ISO 31000, con el objetivo de reducir los defectos que se puedan presentan en un sistema productivo de transformación. La propuesta busca ser una guía para combinar herramientas de calidad y normas de gestión teniendo en cuenta siempre las condiciones de operación de la compañía. El proceso de mejora propuesto inicia con la identificación de los productos y operaciones que representa un eslabón crítico para la organización dentro de su línea de producción y culmina con la revisión y monitoreo de las acciones propuesta para mitigar las fuentes de no conformidades identificadas. Se muestra la forma de implementar eficazmente el proceso de gestión de riesgos en sistemas productivos y de manufactura.
Palabras clave: Condiciones de operación, herramientas de calidad, proceso de gestión del riesgo.
Abstract
This paper proposes a process of continuous improvement in which some statistical tools of quality (Control charts, the Pareto diagram and the cause-effect diagram) and risk management process contained in the NTC 5254 and ISO 31000 are used. The objective is to propose a set of simple steps to reduce the defects that occur in a production system. The proposal seeks to be a guide for combining quality tools and management standards while taking into account the operating characteristics of the company. The proposed improvement process starts with the identification of products and processes critical to the organization within its product line and ends with review and monitoring of the actions proposed to mitigate the sources of nonconformities identified. It seeks to show how to implement a process of risk management in production systems and manufacturing.
Keywords: Operating conditions, quality tools, risk management process.
1. Introducción
La preocupación de las organizaciones por ofrecer un mejor producto o servicio las obliga al uso de un gran número de normas de cumplimiento y herramientas de tipo estadístico para mejorar y alcanzar una calidad óptima, satisfaciendo necesidades y cumpliendo en gran medida las expectativas de sus clientes y/o usuarios (ISO 9000, 2005). Las herramientas estadística de calidad han sido ampliamente utilizadas para ayudar al funcionamiento de sistemas de producción y al cumplimiento de requisitos de especificaciones de productos y servicios (Cachutt et al, 2008; Díaz et al, 2009; Pineda et al, 2011; Lee Ho et al, 2013); siendo implementadas por entidades para demostrar su compromiso y su orientación hacia la mejora continua (Peach, 2001). Por otra parte, la gestión de riesgos ha sido de vital importancia en el sector financiero (Arbeláez, 2006; Botín et al, 2011), en la Gestión de proyectos (Gasca Hurtado, 2010; López et al, 2011; Martínez et al, 2012; Espinosa et al, 2012), en salud y seguridad (Pérez-Vidal et al, 2012) y en la tecnología de información (Gómez et al, 2010).
Los inconvenientes surgen cuando es necesario combinar técnicas estadísticas con normas de gestión para el cumplimiento de estándares de calidad a nivel nacional e internacional. La interacción toma mayor importancia cuando se requiere que las decisiones sean sustentadas por un conocimiento y análisis pleno de la información en los niveles directivos, tácticos y operativos.
Teniendo en cuenta, bajo el marco de las consultas bibliográficas realizadas, que son pocas la evidencias de la implementación de un enfoque de riesgos en sistemas productivos, esta investigación presenta la integración de algunas herramientas de estadística de calidad, como los gráficos de control, el diagrama de Pareto y el diagrama causa-efecto y el despliegue del proceso de gestión de riesgos contenido en las normas NTC 5254 e ISO 31000, todo enmarcado en un proceso de mejora continua. Este proceso pretende identificar y mitigar potenciales fuentes de desviación de especificaciones de producto, armonizando filosofías de trabajo con normas nacionales e internacionales de gestión. El proceso de mejora fue aplicándolo a una empresa del sector industrial ubicada en la ciudad de Barranquilla. Dedicada a la transformación de vidrio y aluminio para ventanería y puertas.
2. Metodología
En el proceso de mejora propuesto se han establecido los pasos a seguir con el fin de implementarlo en cualquier proceso productivo. Las etapas van desde la identificación y descripción de los productos y operaciones que se desean monitorear hasta la revisión y seguimiento de las acciones propuestas para mitigar las causas de desviaciones en el producto, riesgos y no conformidades identificadas en el proceso de fabricación. (Figura (1)). Asimismo, buscando orientar y dar claridad en el desarrollo del proceso de mejora, se describen cada una de las etapas.
Identificación y descripción: En esta primera etapa, se identifican las operaciones y los productos críticos a los cuales se les realizara monitoreo. Se realiza una descripción detallada de las etapas productivas, actividades, métodos de trabajo y recursos utilizados en las operaciones. Lo anterior, buscando identificar posibles riesgos y casusas de no conformidades. Esta etapa es crucial en la implantación del proceso de mejora, ya que sus resultados se convertirán en las entradas para las siguientes fases.
Implementación y Clasificación: Mediante la implementación de las herramientas estadísticas de calidad anteriormente mencionadas, se clasifican las causas de no conformidades en el producto y los riesgos detectados en cada uno de las operaciones identificadas para el monitoreo. Adicionalmente se ponen en marcha los instrumentos para el seguimiento y control estadísticos de los procesos, y por último, se identifican datos de ocurrencia de los riesgos y no conformidades. Las herramientas implementadas en esta etapa dependerán de tipo de proceso que se esté analizando, es decir, se pueden añadir u omitir la utilización de alguna de ellas si quien implementa el proceso de mejora lo considera necesario.
Análisis: En esta fase, se realiza un análisis estadístico completo a las operaciones y productos monitoreados con base en los datos de ocurrencia obtenidos en la etapa anterior (Implementación y clasificación). El análisis realizado como resultado de la implementación de las herramientas estadísticas son de vital importancia para el diagnóstico de las operaciones hasta este punto. Nos permiten reconocer que productos y operaciones son mucho más críticas en la línea de producción.
Mitigación: Con el propósito de reducir los riesgos y no conformidades detectadas en el proceso productivo, en esta etapa se propone el despliegue del proceso de gestión de riesgos según las normas NTC 5254 e ISO 31000. En este proceso de gestión (Siguiendo un enfoque PHVA) se valoran, analizan y tratan los riegos o causas de no conformidades identificados en la etapa de identificación y descripción. Asimismo, se identifican las acciones de contención, reacción y prevención que se pondrán en marcha para mitigar la ocurrencia de los mismos.
Monitoreo y revisión: Tratándose de un proceso de mejora continua, en esta fase se realiza monitoreo y revisión a la efectividad de las acciones propuestas mediante los instrumentos de seguimiento y control estadísticos implementados, observando el comportamiento del proceso y datos de ocurrencia de no conformidades. Esto se realiza con el propósito de proponer nuevas acciones en caso que las propuestas inicialmente no han sido efectivas o actualizar el sistema en la etapa de identificación de nuevos riesgos.
Para mayor claridad, en la sección 3 será presentado un caso de estudio en donde se evidenciará la ejecución del proceso de mejora propuesto paso a paso.
3. Resultados y análisis
En el desarrollo y validación del proceso propuesto, descrito en la sección anterior, se identificó como marco de aplicación una empresa fundada en Barranquilla-Colombia, dedicada a la fabricación y transformación del vidrio y el aluminio. Los resultados fueron los siguientes:
3.1 Identificación y descripción
Para la validación del proceso de mejora propuesto nos concentramos en el estudio y análisis de la línea de producción del vidrio, la cual está compuesta por ocho subprocesos u operaciones de trasformación: Corte, Pulido Rectilíneo, Pulido Curvo-Bisel, Perforado-Boqueteado, Lavado-Secado, Diseño, Sandblasting y Templado. El flujograma de la línea de producción se muestra en la Figura (2). Para efectos de resumir los resultados obtenidos de todo el despliegue del proceso de mejora, se presentaran las salidas de su aplicación al subproceso u operación de Corte. Similares resultados fueron obtenidos en los restantes subprocesos.
En este primer paso se identificaron las operaciones y herramientas de trabajo utilizadas en la operación de Corte. Se logró determinar los aspectos particulares que son relevantes en el subproceso y las etapas secuenciales en la actividad de corte del vidrio. Además, se pudieron identificar y analizar las causas de no conformidades y riesgos relacionados con las condiciones de operación actual en la línea de producción. Esta información fue tomada de primera mano al realizar un seguimiento continuo al proceso y fue hecho por los analistas de Calidad de la Propia compañía.
3.2 Implementación y clasificación
En esta segunda etapa se implementan las herramientas de estadísticas ya mencionadas. El objetivo de esta fase es la clasificación cualitativa de los riegos o causas y el análisis cuantitativo de las no conformidades provocados por dichas causas o riegos. Para lo anterior, se utiliza el diagrama causa-efecto propuesto por Ishikawa en 1943 para clasificar la fuente de los riesgos y causas de no conformidades detectadas en la etapa de identificación y descripción para el proceso de Corte, tipificándolas en el enfoque 6 Ms (Montgomery, 2009). Ver resultados en Tabla 1 y Figura (3).
También, se implementa el diagrama de Pareto para conocer la frecuencia en la ocurrencia de las no conformidades o defectos en el vidrio, como por ejemplo, ralladuras, fisuras, quiebres, cortes inadecuados, escarchas, entre otros (ver Tabla 2). El propósito del diagrama de Pareto es priorizar las no conformidades o defectos y reconocer si el subproceso es críticos en la línea productiva, relacionándolo siempre con la fuente o causa que ha provocado su ocurrencia. El diagrama de Pareto se muestra en la Figura (7).
Asimismo, como instrumento de monitoreo se utiliza la carta de control "c", la cual sirve para verificar si el número de defectos por área en una lámina de vidrio es estable en las condiciones de operación actual. Esta herramienta se utiliza para el seguimiento de todos los subprocesos u operaciones en la elaboración de vidrio y permite realizar el seguimiento a los defectos que no se pueden medir de manera cuantitativa y que afectan la conformidad del producto (ver Figura (4), (5) y (6)). Para el cálculo de los límites de control se tomaron 40 muestras de producto en cada subproceso y se cuantificaron los defectos encontrados en cada una de ellas. Para determinar el tamaño de la muestra, partiendo de una implementación inicial de los diagramas de control para los diferentes subprocesos, algunos especialistas sugieren que el tamaño debe ser lo suficientemente grande para tener una oportunidad aproximada del 50% de detectar un corrimiento o anomalía en el proceso de alguna cantidad especificada (Montgomery, 2009). La evidencia de esta aplicación se muestra en la Figura (8). Los defectos para 40 muestras obtenidas de forma aleatoria del subproceso de corte se presentan en la Tabla 3.
Luego del procedimiento requerido para el cálculo de los límites de Control inferior, Central y superior, el resumen de los resultados son presentados en las Ecuaciones (1), (2) y (3), respectivamente.
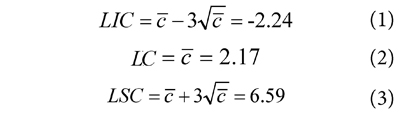
3.3 Análisis
Teniendo en cuenta la clasificación de las no conformidades mediantes el diagrama causas efecto, el análisis de ocurrencia de los defectos priorizadas a través de diagrama de Pareto y el control estadístico de por medio de los diagramas de control "c".
Se observa que para el subproceso de corte aproximadamente el 93% de las no conformidades corresponden a defectos de escarchas y bordes no uniformes, ocasionados frecuentemente por fuentes de mano de obra y los métodos de trabajo utilizados en el proceso. También se evidencia que el máximo de defectos por unidad de producto es de 6 con una media de 2.17.
3.4 Mitigación
Se realiza, bajo el enfoque general de la norma NTC 5254:2007 y el proceso de Gestión del Riesgo incluido en la ISO 31000:2009, el tratamiento y gestión de los riesgos y Causas de no conformidades identificadas en la fase de identificación y descripción (ver tabla 1). En la Figura (9) se presenta el ciclo correspondiente al proceso de gestión de riesgos según la norma NTC 5254 e ISO 31000.
La Gestión de riesgo y causas de no conformidades implica el establecimiento de todos aquellos elementos de infraestructura y culturales idóneos y la aplicación de un método sistemático y lógico para establecer el contexto, identificar, evaluar, tratar, monitorear y comunicar los riegos asociados con cualquier actividad, función o proceso en una manera que permita a las organizaciones minimizar perdidas y maximizar ganancias (NTC-5254, 2007) (ISO 31000, 2009). A continuación se exponen las diferentes etapas del proceso de Gestión de Riesgo desarrollado en la etapa de mitigación.
Identificación del contexto: El contexto está determinado por los productos y operaciones ya identificados en la etapa de identificación y descripción del proceso de mejora, las etapas y actividades del proceso productivo y por el establecimiento de los criterios de riegos cuyo impacto afectaran la imagen corporativa, calidad del producto, costos y los tiempos de producción o entrega. En la tabla 4 se muestra los criterios utilizados en este caso de estudio.
Identificación de los riesgos: La identificación de los riesgos, en términos de que puede suceder y como se presenta, se encuentran enmarcada en la información recolectada en la etapa de identificación y descripción del proceso de mejora propuesto (ver tabla 1).
Análisis de Riesgos: Se mide la posibilidad de ocurrencia del riesgo y su consecuencia con base en la matriz de calificación y análisis de riesgo (Tabla 5). La evaluación será el producto del valor asignado a la posibilidad y la gravedad de cada riesgo. Como podemos observar en la tabla 5 para cada nivel de consecuencias o gravedad del riesgo en un rango de uno a cinco, se presentaran efectos en los costos de producción, tiempos de entrega y calidad del producto. La información de los valores de ocurrencia y criterios de importancia del riesgo fueron suministrados y coordinados por el personal de experiencia de la empresa involucrados directamente con el procesos.
Evaluación del Riesgo: Para determinar qué tan prioritario es un riesgo, nos remitimos a la matriz de calificación y análisis de riesgo (Tabla 5). Observando las diferentes calificaciones del riesgo y su categoría, teniendo en cuenta su posibilidad dentro de un rango de uno a cinco. En este caso, los riesgos pueden ser clasificados como muy bajos, bajos, moderados, altos o muy altos.
Tratamiento de los Riesgos: En esta fase se crea la herramienta "Matriz de Diagnosis - Contención - Reacción - Prevención" (Tabla 6) (Aplicación subproceso de Corte) con el objetivo de proponer y poner en marcha las acciones necesarias para mitigar los Riesgos de mayor prioridad vistos en tabla 1.
La herramienta propuesta (Tabla 6), busca minimizar el impacto de los riesgos o causas que dan origen a las no conformidades en el producto. Por medio de diferentes acciones en cada fase de elaboración se pretende reducir la posibilidad de ocurrencia y cualquier consecuencia negativa que pueda resultar con la presencia de riesgos. Su resultado se reflejará en la reducción en la ocurrencia de los riesgos y no conformidades en el producto.
Esta herramienta, es construida en un documento MS-Excel y su estructura representada secuencialmente muestra: Los riesgos causantes de no conformidades identificados en los diferentes subprocesos y que afectan el producto. Se describen, en ella, en qué consisten y como se presentan dichos riesgos. Posteriormente, se muestra la valoración de riesgo dando valores de posibilidad de ocurrencia y gravedad, con el objetivo de concentrar la atención en aquellos riesgos cuyo valor sean los más altos porque representan mayores consecuencias en el deterioro de la calidad, consumo de recursos y retrasos en los tiempos de producción y entrega.
Seguidamente, se proponen acciones de contención, reacción y prevención en caso de ocurrencia de los riesgos. Esto permitirá al operario de cualquier subproceso tomar decisiones en tiempo real y poder prevenir o contener resultados de mayor gravedad.
3.5 Monitoreo y revisión
Con el objetivo de mantener el buen funcionamiento del proceso de mejora propuesto, la recolección de muestras para la actualización de las herramientas de análisis en la línea de producción de vidrio se realizará como máximo cada dos días. Esto permitirá identificar cualquier tipo de causa no natural que afecte el proceso o por otra parte reconocer si las acciones propuestas para mitigar los riegos son efectivas e incluirlas definitivamente en el proceso.
Asimismo, la actualización de los riesgos en cada uno de los subprocesos se debe realizar en un período no mayor a 90 días laborales, luego de haber implementado la acción o acciones necesarias para reducir o eliminar dichos riesgos, permitiendo identificar nuevas causas de no conformidades. En caso de que las acciones se han efectivas y se logre eliminar o reducir manera definitiva los riesgos ya identificados, la gerencia debe guardar registros de los resultados obtenidos aportando a la temática de las lecciones aprendidas dentro de la organización.
4. Conclusiones
Se ha presentado un proceso de mejora continua para la identificación, tratamiento, mitigación y monitoreo de defectos en productos manufacturados. En su desarrollo se pudo armonizar herramientas estadísticas de calidad con normas nacionales e internacionales de gestión de riesgos.
Durante la validación del proceso se logró identificar falencias en cada uno de los subproceso en la línea de transformación de vidrio en una empresa industrial de la ciudad de Barranquilla-Colombia. Además, se plantearon soluciones encaminadas a mitigar las causas o riesgos generadores de no conformidades en el producto monitoreado. Los resultados de la aplicación se presentaron para la operación de corte de vidrio y como logró fundamental, se implementaron las mejoras necesarias para aminorar la ocurrencia de los riesgos identificados, pudiéndose tomar el mejor curso de acción teniendo en cuenta las condiciones de operación de la empresa.
La utilización de herramientas de análisis como el Diagrama de Causa-efecto, Diagramas de Control y Diagrama de Pareto, ayudó a procesar y darle sentido a los datos recolectados, contribuyendo al análisis y conocimiento de las operaciones. Además, las herramientas implementadas permiten identificar cualquier cambio positivo o negativo en el subproceso debido al tratamiento de los riesgos o por causas no naturales.
Asimismo, el diseño e implementación de la herramienta "Matriz de Diagnosis - Contención - Reacción - Prevención", fundamentada en la norma NTC 5254:2007 e ISO 31000:2009 para la gestión del riesgo, nos permitió proponer acciones para prevenir las causas o desviaciones no deseadas. Esta herramienta permite concentrar la atención en aquellos que riesgos que fuesen más significativos para la operación.
Adicionalmente, podemos concluir que mediante el despliegue del proceso de gestión de riegos en sistemas productivos se logran proponer fácilmente actividades orientadas a que el operario responsable del subproceso tome decisiones en tiempo real. Esto buscando prevenir o contener resultados no deseados durante la transformación del producto. Teniendo en cuenta que el proceso solo se aplicó en un entorno industrial, como avance y proyecciones se sugiere aplicarlo en un ambiente de servicios y/o en procesos productivos que requieran la utilización de diferentes tipos de diagramas de control o instrumento para el monitoreo de los procesos.
5. Referencias
Australian/New Zealand Standard ISO 31000. (2009/11/20). AS/NZ ISO 31000 Risk Management. Principles and Guidelines. Sidney, Australia: Standards Australia and Standards New Zealan, Gestión de Riesgos (Comité Técnico Mixto OB-007). Recovered 15/05/2015 http://sherq.org/31000.pdf [ Links ]
Arbeláez, J.C., Ceferino, L., y Betancur, C. (2006). Riesgo operacional: reto actual de las entidades financieras. Revista Ingenierías Universidad de Medellín, 5 (9), 97-110. [ Links ]
Botín, J., Guzmán, R., & Smith, M. (2011). A methodological model to assist in the optimization and risk management of mining investment decisions. Journal Dyna, 78 (170), 221-226. [ Links ]
Cachutt, C., Illada, R. A., Barreto, J. R., y Pinto, F. E. (2008). Análisis de los procesos de fabricación en una empresa manufacturera mediante gráficos de control integrado. Revista Universidad, Ciencia y Tecnología, 12 (49), 235-246. [ Links ]
Díaz, E., Díaz, C., Flores, L., y Heyser, S. (2009). Estudio de la Variabilidad de Proceso en el Área de Envasado de un Producto en Polvo. Revista Información tecnológica, 20 (6), 105-113. [ Links ]
Espinosa, F., Dias, A., & Salinas, G. (2012). Un procedimiento para evaluar el riesgo de la innovación en la gestión del mantenimiento industrial. Ingeniare, Revista chilena de ingeniería, 20 (2), 242-254. [ Links ]
Gasca-Hurtado, G. P. (2010). Estudio de similitud del proceso de gestión de riesgos en proyectos de outsourcing de software: utilización de un método. Revista Ingenierías Universidad de Medellín, 9 (17), 119-130. [ Links ]
Gómez, R., Pérez, D., Donoso, Y., & Herrera, A. (2010). Metodología y gobierno de la gestión de riesgos de tecnologías de la información. Revista de Ingeniería, 31(1), 109-118. [ Links ]
ISO 9000 (International Standardization for Organization) (2005). Basic concepts and language. Ginebra, Suiza. [ Links ]
Lee-Ho, L., & Costa Quinino, R. (2013). An attribute control chart for monitoring the variability of a process. Journal ELSEVIER (Int. J. Production Economics), 145 (1), 263-267. [ Links ]
López, C., & Salmerón, J. (2011). Ranking risks in ambient intelligence projects. Journal of applied research and technology, 9 (3), 419-429. [ Links ]
Martínez, G., Moreno, B., & Rubio, M. (2012). Gestión del riesgo en proyectos de ingeniería. El caso del campus universitario pts. Universidad de Granada (España). Journal Dyna, 79 (173), 7-14. [ Links ]
Montgomery, C. D. (2009). Introduction to Statistical Quality Control (6 ed.) New York, USA: John Wiley & Sons, Inc. [ Links ]
NTC-5254 (Norma Técnica Colombiana). (2007). Directrices para la Gestión de Riesgos. Bogotá, Colombia: ICONTEC. [ Links ]
Peach, R. W. (2001) Manula de ISO (3 ed.) México D.F., México: McGraw Hill. [ Links ]
Pérez-Vidal, A., Amézquita-Marroquín, C. P., & Torres-Lozada, P. (2012). Identificación y priorización de peligros como herramientas de la gestión del riesgo en sistemas de distribución de agua potable. Revista Ingeniería y Universidad, 16 (2), 449-469. [ Links ]
Pineda, U., Estrada, M., & Parra, C. M. (2011). Aplicación del modelo Servqual y herramientas de ingeniería de la calidad para la planificación del servicio en la Biblioteca Central de la Universidad de Antioquia. Revista Interamericana de Bibliotecología, 34 (3), 243-255. [ Links ]
Poveda-Orjuela, P., & Lopez-Giraldo, M. (2010). Configuración de herramientas guía para la gestión integral de riesgos de inocuidad según ISO 31000 e ISO 22000 (vol. 1). Barranquilla, Colombia: Ediciones Uninorte. [ Links ]
Revista Ingeniería y Competitividad por Universidad del Valle se encuentra bajo una licencia Creative Commons Reconocimiento - Debe reconocer adecuadamente la autoría, proporcionar un enlace a la licencia e indicar si se han realizado cambios. Puede hacerlo de cualquier manera razonable, pero no de una manera que sugiera que tiene el apoyo del licenciador o lo recibe por el uso que hace.