INTRODUCCIÓN
La técnica de emisión acústica (EA) es ampliamente utilizada como una valiosa herramienta en ensayos no destructivos para el control, detección y posicionamiento de diferentes defectos en recipientes a presión, tanques de almacenamiento de hidrocarburos, pérdidas en válvulas y cañerías, descargas tipo corona en transformadores de alta tensión, rotura de fibra y matriz de materiales compuesto tipo FVRP y FCRP, análisis de propagación de fracturas en hormigón, etc. Esta técnica consiste en la detección y análisis de las ondas elásticas resultantes de la liberación de energía durante un corto periodo de tiempo, donde la emisión proviene de una fuente (o suceso) que es excitada de alguna manera. Ejemplo de este fenómeno es la liberación de energía potencial elástica durante el avance de una fractura frágil. Parte de esa energía liberada por la fisura se propaga a través del cuerpo fracturado en forma de onda de tensión elástica, donde eventualmente llega a un transductor piezoeléctrico que permite adquirir la señal de EA para su registro y posterior análisis. En particular, la propagación de una fractura se caracteriza por ser una emisión de tipo discreta, es decir temporalmente determinada.
Otra forma de utilizar la EA está relacionada con el monitoreo indirecto de procesos; con ellas se evalúa el desarrollo y evolución, por ejemplo, del corte de un material respecto de variables como el avance, velocidad de corte, material y condición del herramental, entre otras. Este tipo de EA, al igual que los procesos de fricción y erosión, genera señales que no están claramente determinadas en función del tiempo y tienden más bien a ser continuas con transitorios a lo largo del proceso. Dentro de la caracterización de las señales de EA se pueden parametrizar diferentes aspectos de la onda recibida como la duración, la amplitud máxima, el número de cuentas, la energía MARSE, la frecuencia promedio, el centroide de frecuencia, el tiempo de excursión hasta la amplitud máxima (denominado rise time) y el valor RMS de la EA, entre otros parámetros. Algunos de estos valores se calculan a partir del momento que la señal sobrepasa un valor arbitrario denominado umbral, el cual es fijado por el operador del equipo en función de su conocimiento y experiencia.
Existen trabajos que analizan el monitoreo de procesos de corte ortogonal, por ejemplo en metales, donde se asocia el RMS de la señal de EA con ciertas condiciones durante el torneado. Dornfeld y Kannatey-Asibu (1980), y Saini y Park (1996), generaron modelos empíricos y analíticos asociando este valor (RMS de EA) en función de variables como deformación plástica del material cortado, flujo de viruta, avance y r. p. m. Otros análisis, como el de Grabec y Leskovar (1977), también incluyen distribución del espectro de frecuencia de la señal de EA respecto del avance, r. p. m. y profundidad de corte. Jemielniak y Otman (1997) estudian el análisis de la curtosis y oblicuidad (skewness) de la distribución del parámetro RMS de EA, donde se muestra una buena sensibilidad para detectar la rotura catastrófica de la herramienta.
Para el taladrado de materiales compuestos en fibra de carbono y resina epoxi, Mascaro, Gibiat, Bernadou y Esquerre (2005) relacionan el espectro de frecuencia durante este proceso y muestran que la banda de frecuencia concerniente a la rotura de la matriz y de las fibras no varía con el cambio de geometría del herramental, la velocidad de taladrado y el avance. Además, indican que la energía de la señal de la EA es sensible al desgaste de la herramienta, lo que revela que eventualmente este parámetro podría ser utilizado para el control de su estado. Trabajos más recientes utilizan parámetros secundarios como la potencia media de la EA, los cuales funcionan como indicadores del estado de las brocas en perforados de metales (Gómez, Hey, Ruzzante y D'Attellis, 2010; Gómez 2012).
La perforación, desde un punto de vista mecánico, es un proceso complejo de modelar debido a la cantidad de variables que se deben considerar, a saber: geometría del cortador (Rajabov et al., 2012), cantidad de filos, tipo de mecanismo de corte, desintegración del material, forma de remoción, lubricación, temperatura, r. p. m., fuerza de avance (FA), etc. Se deben considerar también las características del material a ser cortado, que modifica la interacción herramienta/material en perforación de materiales rocosos (Bourgoyne et al., 1991) y, por tanto, también produce una modificación de la dinámica del proceso de corte relacionada con el tipo de material, constantes elásticas, fragilidad, ductilidad, dureza, granulometría, densidad, nivel de saturación de líquido y condiciones de tensión del ambiente que lo rodea, ya que diferentes entornos de confinamiento (equiaxial, po-liaxial, nivel de tensión deviatoria, etc.) modifican el comportamiento ante la fractura para un mismo material (Peng y Zhang, 2007).
La información obtenida durante el moni-toreo de procesos es cuantiosa. Para poder representar la evolución de estos procedimientos estocásticos es necesario el registro de grandes volúmenes de información donde la utilización de parámetros es una forma económica de resumir el comportamiento de la señal, siempre a coste de perder información. Los parámetros de EA sujetos a análisis pueden ser varios, y deben ser seleccionados en función del peso que tienen a la hora de describir el proceso que se desea monitorear. Es una práctica recomendada adicionar a los parámetros de la EA alguna variable adicional perteneciente al control del proceso, como por ejemplo la variación de la fuerza de avance en el perforado, la temperatura, la presión, u otro indicador dinámico para correlacionar la información de la EA. Esto determina que la cantidad de variables que se debe manejar sea alta y convierta al análisis de la condición de proceso en un problema de características multiparamétrico, en donde los puntos máximos o mínimos del sistema se encuentran posiblemente en combinaciones no lineales entre estas variables.
Allí la matemática, los métodos de cálculo actuales y la tecnología se conjugan para proveer formas de análisis que reúnen varias de las características necesarias para modelar estos sistemas (Everson y Cheraghi, 1999; Philippidis, Nikolaidis y Anastassopoulos, 1998).
Para el presente trabajo, se utiliza una red neuronal de tipo Kohonen o mapa autoorganizado (SOM, por su sigla en inglés) el cual tiene la capacidad de crear una grilla planar (mapa) con neuronas que se agrupan para clasificar diferentes tipos de información según reglas de aprendizaje específicas.
Este tipo de red fue utilizada con éxito en diferentes aplicaciones, como la detección de fisuras en fabricación de mosaicos (Barrera, Carreón y Ruiz, 2005); clasificación de origen de aceites de oliva y medición de la reactividad de enlaces químicos (Zupan y Gasteiger, 1993); mejora de las características de las señales (relación señal ruido) de la EA en el control de desgaste de herramientas de micro maquinado (Chen y Liao, 2003); análisis de modos de falla en materiales compuestos (Godin, Huguet y Gaertner, 2005); tratamiento de imágenes y señales en general; entre otras variadas aplicaciones (Kohonen, 2001).
METODOLOGÍA
Sistema de perforación: El sistema de perforación posee un equipo hidráulico con regulación de avance de 120 bar de potencia, con 1000 mm de recorrido y propulsado con un motor de 4 hp trabajando hasta 3000 r. p. m., el cual está conectado a una caja reductora y a un variador de velocidad para controlar la velocidad de rotación de la broca (figura 1a). El herramental de perforación se compone de cuerpo tubular de 1600 mm de longitud, donde en su extremo se fija la broca de perforación (figura 1b). de 65 mm diámetro con dos filos de carburo de tungsteno y un ángulo de punta de 162°. Adicionalmente, se cuenta con sistema de inyección de agua para la lubricación y extracción de material cortado. Este prototipo está adaptado para instrumentar directamente la broca de perforación (herramienta rotante) y obtener la señal de EA procedente del proceso de corte que se desarrolla en el extremo del cortador.
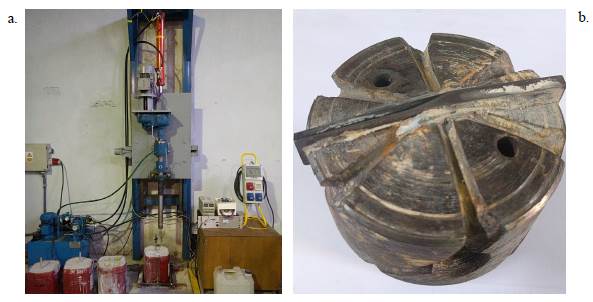
Fuente: elaboración propia.
Figura 1 a. Sistema completo de perforación con control de velocidad, central hidráulica, y herramienta de perforación. b. Detalle de la broca con cuerpo realizado en SAE 4140, dos filos de carburo de tungsteno y salidas de fluido.
Probetas de material multicapa: Las probetas ensayadas son paralelepípedos de 320x320 mm de base y 400 mm de altura, compuestas por capas de material geológico (rocas) de diferentes características colocadas en forma de estratos (figura 2a). Una vez definidos es-tos estratos (capas de rocas), se cementaron con material en una proporción 3:0,8:0,2 de arena, cemento y cal, respectivamente. Estas unidades consolidadas conforman una muestra de ensayo sobre la cual se pueden realizar 4 perforaciones simétricas, como se observa en la figura 2b. Además, cada una de la muestras fue instrumentada con una guía de ondas con el fin de obtener la EA del proceso de perforación por un camino alternativo al de la columna de perforación y comparar así su desempeño.
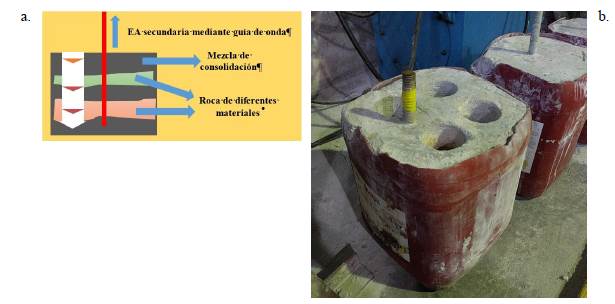
Fuente: elaboración propia.
Figura 2 a. Croquis de la composición de las probetas donde se observan los diferentes estratos y la guía de onda que los atraviesa. b. Probeta con cuatro perforaciones y guía de onda cementada.
Las probetas construidas de esta manera presentan gran heterogeneidad geométrica respecto del espesor de cada estrato, así como en el tallado para la conformación de cada capa (figura 3a, b y c). Esto produce que cada una de las probetas y de las perforaciones realizadas sean únicas e irrepetibles
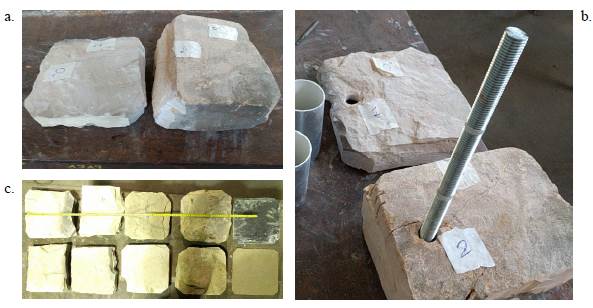
Fuente: elaboración propia.
Figura 3 a. Dos tipos diferentes de estratos con variación apreciable de espesor, b. Estratos con perforación para guía de ondas colocada, c. Diferentes estratos utilizados para ensamblar las probetas (arenisca, caliza y pizarra) y su tallado para montaje dentro de cada probeta
En la tabla 1. se detallan las composiciones de los dos tipos de probetas ensayadas para el presente trabajo. La muestra M1 contiene dos tipos de rocas sedimentarias de diferente tamaño de grano y material constituyente. El primer estrato pertenece a un tipo de roca determinado como arenisca, debido a su tamaño de grano, comparable con la sílice y observable a ojo desnudo. Este produce una fractura rugosa que, en general, se propaga por el material de unión de sus granos.
La segunda muestra utilizada está dentro de las llamadas lutitas, siendo específicamente esta una caliza. Son rocas sedimentarias de grano más fino que las areniscas, y esta en particular, se compone mayoritariamente por material producto de la sedimentación de moluscos marinos. Este tipo fractura en forma de escama paralela al sentido de deposición de sus elementos constitutivos. Debido a que es más densa que la arensica, si bien es menos dura que esta, es de más difícil taladrado debido al tamaño y densidad en la deposición de sus minerales.
La muestra M2 consiste en una composición de material cementicio con dos capas alternadas de roca metamórfica denominada pizarra; es densa (tamaño de grano muy fino), con placas de mica alineadas en sentido paralelo a la laminación. A su vez, se fractura en planos de debilidad paralelos a la laminación, con fracturas suaves o sedosas.
Sistema de emisión acústica: Para la adquisición y procesamiento de los datos se utilizó un sistema de EA de la marca Physical Acoustics Corporation (PAC), modelo DISP-4 de 4 canales, con capacidad de adquisición de parámetros característicos de la EA y formas de onda. Las señales fueron tomadas con dos sensores (uno en la probeta y otro en la broca) marca PAC modelo WD de banda ancha, con preamplificadores externos modelo 2/4/6 con ganancia ajustada en 20 dB para el sensor montado sobre la broca, y en 40 dB para el sensor montado en la probeta, El equipo se manejó en una PC con el software AE Win, Entre los parámetros medidos se registraron: amplitud, RMS, energía MARSE, cuentas, rise time, frecuencia media, centroide de frecuencia, duración, etc,
Arquitectura de red neuronal utilizada para análisis de probeta M2: La arquitectura de la red neuronal Kohonen creada consta de 400 neuronas dispuestas en forma de grilla toroidal de 20x20 neuronas, con una cantidad de cuatro vecinos por neurona y una función topológica de ajuste de vecindad tipo gaussiana, El criterio de la neurona ganadora se definió así: "la entrada más parecida al peso de una neurona resulta como ganadora", con ajuste de pesos por datos y por época, y con una duración de entrenamiento de 400 épocas, El error de mezclado y de norma alcanzado en la etapa de entrenamiento fue del 5,9 % y 0,09, respectivamente. La red fue entrenada y simulada con un vector dato (VD) multiparamétrico de 5 componentes [Amplitud, energía MARSE, RMS, rise time, frecuencia promedio], extraído de la señal de EA de la broca y proveniente de la perforación. La cantidad de VD utilizados fue de 400 para el entrenamiento y 196 para la predicción. Estos VD fueron seleccionados gráficamente respecto de las señales de EA, pertenecientes a la perforación de las dos rocas de pizarra (513 VD) y al material cementicio (83 VD) para la probeta M2.
Desarrollo del ensayo: Las probetas M1 y M2 fueron taladradas en cuatro sectores, tomando señales representativas de cada proceso. El tiempo de taladrado en estos ensayos en particular promedió los 1800 s. La EA se adquirió de manera paralela sobre la herramienta (canal 1) y la probeta (canal 2), con el fin de comprar señales y comprobar el correcto funcionamiento de la instrumentación de la herramienta giratoria de perforación. Una vez taladradas las probetas M1 y M2, se analizó la información parametrizada. En la probeta M1 se caracterizaron las zonas de las interfaces respecto de las diferentes rocas taladradas, mientras que para la probeta M2 se utilizaron algunos de los parámetros de EA para entrenar y simular mediante una RNK, luego de un posprocesamiento de la señal que comprende selección de los datos, etiquetado y normalización, además del análisis de correlación entre variables.
RESULTADOS
Para la probeta M1, en la figura 4a,b,c,d,e,f. se ilustran los parámetros amplitud [dB], energía MARSE [µv.s/cuentas] (área medida respecto de la evolvente de la señal rectificada de EA) y RMS [v] de la EA para los canales 1 y 2. Se observa que el sistema montado directamente sobre la herramienta de trabajo recibe una potencia de señal de mayor amplitud (6 a 8 veces) que la señal obtenida a través de la probeta. Esto posiblemente sea debido a que las ondas ultrasónicas encuentran en el metal del cuerpo de la broca una conexión directa con el proceso y un camino con mucha menor atenuación que a través de las interfaces de la roca, cuyo material es más dispersivo y atenuante. El análisis de la amplitud muestra que es bastante difícil detectar las variaciones entre diferentes zonas de estas probetas compuestas por estos tres elementos. Por otro lado, los parámetros de energía MARSE y el valor RMS de la EA muestran zonas de variación más marcadas respecto de la amplitud para diferentes partes del ensayo de la muestra M1.
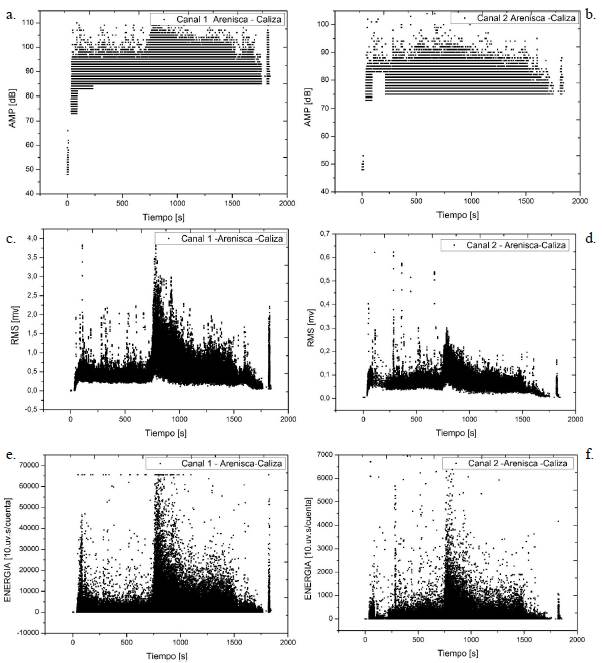
Fuente: elaboración propia.
Figura 4a,b,c,d,e,f, Muestra una marcada variación de los parámetros de EA en función de los estratos perforados. a y b. Parámetro RMS de EA medido sobre el canal 1 (broca de perforación) y canal 2 (guía de onda colocada dentro de la probeta). c y d. Parámetro de energía MARSE para canales 1 y 2, respectivamente
Estas variaciones pueden ser relacionadas (mediante análisis del material cortado y posición de la punta de la herramienta) con las correspondientes interfaces rocosas contra las cuales se fue encontrando el cortador de carburo. Estas interfaces están marcadas en la figura 5. y corresponden a:
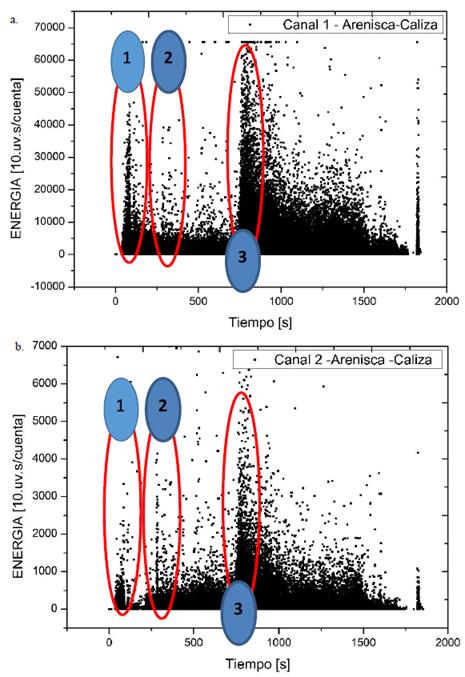
Fuente: elaboración propia.
Figura 5 Marcación de zonas de interfaz identificadas mediante a. Energía MARSE para canal 1. b. Energía MARSE para canal 2
Zona 1: inicio del proceso de taladrado sobre material de cementación de la probeta.
Zona 2: fin de zona 1 e inicio del taladrado de roca tipo arenisca.
Zona 3: fin de elemento cementación e inicio de taladrado de roca tipo caliza.
Estas zonas características de inestabilidad se observan cuando la broca hace un cambio de interfaz entre diferentes materiales geológicos y se pueden relacionar al progresivo avance del cortador dentro del nuevo material que comienza a cortar.
Al inicio de cambio de interfaz, la velocidad de corte de la punta de la broca es cero (0) y crece radialmente hacia el diámetro de esta, de manera que el primer contacto entre el cortador y la nueva interfaz se produce casi por indentación, más que por corte del material. Una vez que el cortador ingresó plenamente dentro del nuevo material, el corte se hace más estable y equilibrado, lo cual disminuye la tasa de emisión y la energía de la señal, y baja su amplitud máxima.
La comparación entre los canales 1 y 2 indicaría que la atenuación producida por el sustrato rocoso actúa como un filtro natural; así se disminuye la intensidad de la señal, en general, y las de alta frecuencia, en particular, ya que la atenuación es función creciente con la frecuencia. Esto permite tener una señal más limpia en la que se observan los cambios de interfaz de manera más clara. En contrapartida, parte de la información recibida por este canal puede ser perdida durante este efecto de filtrado natural.
Aquella proveniente de la herramienta de corte se muestra altamente correlacionada con la de la guía de onda de la probeta, mostrando que este canal de medición es representativo de las variaciones del proceso, con la ventaja de que no se necesita colocar una guía de onda por cada probeta a ensayar, ya que la cadena de medición es siempre la misma.
Para la probeta M2 -conformada por dos capas de roca pizarra cementadas-, también se pueden detectar estas interfaces, a medida que con la perforación se atraviesan los diferentes sustratos (figura 6).
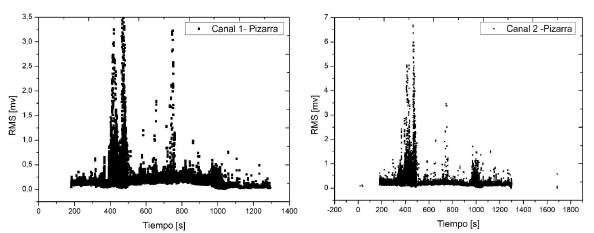
Fuente: elaboración propia.
Figura 6 Medición del parámetro RMS de la EA para probeta M2 de roca pizarra, canal 1 y canal 2, respectivamente.
La señal de EA proveniente de la instrumentación de la herramienta (canal 1) fue seleccionada en función de los gráficos para el proceso de entrenamiento y predicción de la RNK (figura 6). Estos tramos de información se etiquetaron como pizarra uno (P1), para el primer estrato de pizarra; pizarra dos (P2), para el segundo estrato, y finalmente, el elemento de consolidación, que se encuentra sobre, debajo y en medio de las capas, se nombró cementicio (C). Estas etiquetas sirvieron para evaluar el desempeño de la red en la clasificación, durante el entrenamiento y posteriormente en la predicción.
Los resultados del mapa de entrenamiento de Kohonen de la figura 7a. muestran una separación en clases de las señales pertenecientes al material C, respecto de los estratos de pizarra P1 y P2. Adicionalmente, la red tuvo la capacidad de diferenciar las señales provenientes de las dos rocas del mismo tipo de material metamórfico (P1 y P2), pero de diferente profundidad. Los resultados mostrados en la figura 7b. corresponden a la simulación realizada en el mapa ya entrenado.
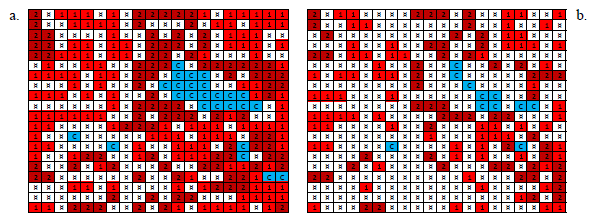
Fuente: elaboración propia.
Figura 7a Mapa de Entrenamiento de RNK para probeta M2 donde figuran P1, P2 y C. Figura 7b: Mapa de simulación y clasificación para probeta M2 con datos desconocidos por la RNK
Estos datos nunca fueron procesados por la red hasta el momento de la simulación, y fueron clasificados con un error de mezclado y de norma inferior al 5 % y 0,04, respectivamente. Se respetan las zonas topológicas delimitadas por las neuronas que clasifican los datos de las señales C respecto de las de P1 y P2. También se observa la formación de subclúster entre P1 y P2, a pesar de ser el mismo material.
CONCLUSIONES
Los resultados indican que la EA tiene la capacidad de proveer información útil para distinguir diferentes materiales geológicos durante el proceso de perforación a esta escala.
El parámetro de amplitud máxima de la EA no muestra claramente los cambios de la dinámica de corte que se suceden en los estratos, mientras que la energía MARSE y el RMS de la señal muestran transitorios relacionados con el cambio de material que se está perforando, posiblemente debido a la progresiva penetración del cortador en este.
La composición intrínseca de la probeta de material geológico filtra naturalmente la señal de EA, produciendo que las señales registradas por la guía de ondas dentro de la probeta sean de menor amplitud que las registradas directamente sobre la broca. Ambas señales mostraron una alta correlación de eventos, lo cual valida la utilización de la instrumentación sobre la broca como método para el monitoreo del proceso.
Con la información paramétrica de EA proveniente de la broca se logró entrenar y simular una RNK que mostró capacidad de clasificar la información perteneciente a cada tipo de material por separado, con un error de mezcla inferior al 5 %.