Studies on the spatial distribution of acoustic discomfort are essential for improving the work environment, especially in evaluating the salubrity which operators and helpers will be subjected to the operation of a micro-tractor whose work rotation is 2400 rpm. Fernandes and Morata (2002) cite that physical agents such as noise, heat, vibration, pressure, radiation, and chemical agents such as smoke, dust, gases, and vapors, are some of the environmental stressors which are found in several workplaces.
Arcoverde et al. (2011) emphasize the importance of studies about noise levels in agricultural operations for the real need of adopting prevention to minimize noise effects and improve comfort and safety.
Bistafa (2018) conceptualizes noise as a sound without harmony, in general of a negative connotation, in other words, in most cases it can be classified as an undesirable way sonorously, standing out as one of the occupational risk agents.
Previous studies have evaluated the noise emitted by agricultural machines through geostatistics, but for the adjustment of the semivariogram, these studies used the spherical model (Ferraz et al., 2013; Júnior et al., 2014) and the Gaussian model (Missio et al., 2015; Pimenta et al., 2012; Spadim et al., 2015). However, these mentioned models may not represent the noise behavior correctly, being necessary to adjust these models as a periodic function or sinusoidal function, as the Wave model used by Gonçalves et al. (2019).
In addition, the Statistical Process Control (SPC) was another tool used to analyze these data. SPC is a simple tool, and its effectiveness is witnessed by a repetition physically established in industries around the world. Therefore, it is possible to control significant characteristics of the product and the process in real-time, guaranteeing quality levels at a cost supported by the market (Nomelini et al., 2009).
Among the main tools of the SPC, the control graphs stand out. They are among the most used when it comes to monitoring processes. According to Werkema (1995), the interpretation of control graphs is made through non-random patterns. Therefore, this work aimed to illustrate and discuss such patterns based on statistical and probabilistic concepts.
According to Nomelini et al. (2009), SPC is a robust methodology developed to effectively control product quality and production processes, using statistics to analyze the process's limitations. SPC application in noise emitted analysis by agricultural machinery is hardly found in scientific research, highlighting the importance of this study.
It is also noted that the mitigation of the noise problem is linked to reducing the intensity of the same source, reducing the exposure time, or using individual protective equipment. Thus, it is essential to know the reality of the machine under study in terms of noise to plan the best strategy to combat the problem.
Given the exposure, the aim of this study was to use geostatistics and Statistical Process Control (SPC) from individual charts to map and characterize the magnitude of the spatial variability of noise emitted by a micro-tractor, to identify healthy zones for workers.
MATERIALS AND METHODS
The experiment was developed at the Federal University of Lavras (UFLA), Lavras, Minas Gerais, Brazil. In this study, a micro-tractor with a nominal power of 11 kW (15 hp) was evaluated, whose year of manufacture was 2007. Its working rotation is 2400 rpm. The tractor had a coupled trailer, which did not have any driver.
The noise level rating of this agricultural machine was carried out in which the ambient temperature was between -5 and 30 °C and the air velocity was less than 5.0 m s-1. For the measurement of noise propagated by the tractor, a digital decibel meter model dec 460 was used to measure the noise level emission, the description of which is based on a sound pressure level measuring instrument with instantaneous reading and peak reading, automatic scale, and frequency weighting in A and C. There is a measurement of 35 to 130 dB (A) and internal calibrator in terms of the measurement scale.
Readings were taken at an average height of the operator's ear, at points distributed in a regular 2×2 m sampling grid. Totaling 441 sampling points around the agricultural machine in stationary operation (Figure 1). These samples were later used in descriptive statistics. A spatial coordinate was arbitrated in meters where the central point (0, 0) corresponded to the point where the agricultural machine remained in operation during all collection. The central point (0, 0) corresponded to the operator's seat (Figure 1).
The spatial dependence of the noise emitted by the micro-tractor placed in the operation regime was analyzed through adjustment of classic semivariogram by the Ordinary Least Squares (OLS) method and the Wave model. The classic semivariogram was estimated by Equation 1:
Where N (h) is the number of experimental pairs of observations, Z(xi) and Z(xi+h) and separated by a distance h, the semivariogram is represented by the graph γ(h) estimated semivariance for distance h. From the adjustment of a mathematical model to the calculated values of γ(h), the coefficients of the theoretical model are estimated for the semivariogram called the nugget effect, C0; threshold, C0+C1 and the reach, a, as described by Vieira et al. (1983).
In Equation 2, the theoretical model adjusted to the experimental semivariogram utilized for the research is the Wave model (Mota, 2008; Gonçalves et al., 2019).
Where is the contribution, a is the range, and h is the distance between the points observed.
Equation 2 represents periodic variations, which indicate non-monotonic growth of the semivariance with distance, presenting models with and without threshold (Andriotti, 2004). These non-monotonic structures can have reduced wave amplitudes, be isotropic, and be anisotropic (Carvalho et al., 2004). Another analysis that must be carried out is based on the relationship between theoretical and practical scope. According to Chilès and Delfiner (2012), the practical range of the Wave model is reached when the h is approximately equal to 4.5a.
For the geostatistical analysis, R was used as a statistical computer system with GeoR package (Ribeiro Júnior and Diggle, 2001). SURFER 15.2 software was used to plot the maps. The values recommended by ABNT (2021) were used for the evaluation of admissible levels. NR 15 norm defines a time limit for workers to be exposed to continuous or intermittent noise that will not harm their health.
In addition to the geostatistical analysis, the noise data emitted by this micro-tractor was evaluated through process control charts (SPC). Control charts also present complementary criteria for quality analysis. Including a sequence of points occurrence, upward downward trends, shifting in the process cyclic patterns, points plotted close to the control limits and clustering around the mainline (Szekut et al., 2018). Civardi (2017) suggested a sequence of steps to analyze the control charts: build experimental control limits after data collection according to the sampling plan; verify that all points are within the control limits and no random configuration is being performed. If these two conditions are met, it can be said that the process is under statistical control, and the next step is to assess the capacity of the process; if there are points outside the control limits and/or some non-random configuration, it may conclude that the process is out of the state of statistical control. In this case, special reasons that caused each point should be identified.
For the composition of individual letters in the SPC, the Minitab 19 software was used. Because of this, it was separated into five stages consecutively. Such stages were formed to facilitate the analysis of the data obtained in the sample grid. From these data, stage 1 was developed from radius 0 to 4 m; stage 2 was created from radius 4 to 8 m, stage 3 was set from radius 8 to 12 m, stage 4 was made from radius 12 to 16 m and the stage 5 consisted of a radius of 16 to 20 m.
RESULTS AND DISCUSSION
The descriptive statistics of the noise emitted by the studied tractor are shown in Table 1. Analyzing the minimum and maximum limits, the coefficient of variation, and the average noise, it was possible to observe a variation in the data. However, this analysis does not demonstrate the spacial position of the lowest and highest values of noise emitted by the tractor, therefore geostatistical studies are required.
The geostatistical analysis of the noise levels emitted by the micro-tractor in the operating regime can be noted in Table 2. Thus, it is observed that the semivariogram (Table 2; Figure 2) and its parameters (nugget effect, "C0"; contribution, "C1"; sill, "C0 + C1"; and range, "a") were obtained by the Ordinary Least Squares method (OLS - ordinary least square) and by the Wave model (Figure 2). By analyzing Figure 2 and also observing Table 2, the practical range of the spatial distribution of the noise emitted by this machine was 13.94 m, which implies that to this distance, the variable under study is influenced through space.
Table 2 Methods, models, and parameters estimated the experimental semivariogram to the noise level emitted by a tractor.

It is observed in Figure 3 that the alarming values of the noise emitted by the micro-tractor, above 85 dB (A), for daily exposure of 8 h (ABNT, 2021) are seen, in general, up to 6 m of distance around the tractor in operation regime. Note that in the center of the map (0,0), where the operator is positioned, the measured noise level was 91.20 dB (A), represented by the red color. This value can be considered high for daily exposure. The regulatory standard (NR 15) Ordinance 3,214/78 Ministry of Labor and Employment (MTbE) establishes that the maximum noise level allowed for 8 h of daily exposure is 85 dB(A). Above this limit, noise and disturbing human activities can cause serious damage to health (Silva et al., 2004).
The approximate value of the maximum noise 91.0 dB (A), was observed at point (0, -2), which was measured near the micro-tractor (noise emitting source), represented by the red color in the map. According to ABNT (2020), the permitted limit was exceeded for a daily exposure of 8 h in all cases evaluated. In this way, it was noted that both the operator of the evaluated tractor and the helper for the agricultural operation would be subjected to the harmful effects of the noise emitted by this machine.
It was found that operators need to wear hearing protection, that is, personal protective equipment (PPE). Therefore, the farther from the tractor, the more the color of the spots becomes bluish, which indicates the decrease in the noise level, thus becoming more appropriate for workers and not requiring the use of PPE. However, it is noted that even so, all workers involved in the operation of this machine use PPE. The minimum noise value produced by this tractor was about 59.0 dB (A) observed at point (-12, -20), that is, the furthest from the emitting source point.
Furthermore, observing the ABNT (2020) it is noted that the rural or similar employer must adopt ergonomic principles that aim at adapting working conditions to the psychophysiological characteristics of workers, to provide improvements in comfort conditions and safety at work, and also provides for the use of hearing protection, in this case, hearing protectors for activities with noise levels harmful to health.
Although the agricultural activity in Brazil is the most important since the colonial period until the middle of the 20th century, it had a significant advance for employees only from the Federal Constitution of 1988 in the seventh's article, where it guarantees rights to rural workers as well as urban workers and include unemployment insurance, the minimum wage, the severance pay for the length of service, the extra salary and the 8 h working day. Recently, ABNT (2020) presented progress for rural workers. It came to make the planning and development of agriculture, livestock, forestry, and aquaculture activities compatible with the safety and health of workers. With regard to ergonomics and safety in the use of agricultural machinery, this standard states that "all machines, equipment, implements, furniture, and tools must provide the worker with conditions of good posture, visualization, movement, and operation".
The majority of motocultivators use air-cooled single-cylinder engines. They are typically powered by diesel, with a four-stroke thermodynamic cycle and power ranging between 7,457 and 14,914 W. The total displacement varies between 250 and 500 (cm³) with a maximum operating regime between 3000 and 3800 rpm (Márquez, 2012). In addition, when Gomes et al. (2013) evaluated the increase of motor rotation, they observed that this operation could cause an increase in the sound power level, but only at extreme speeds (2,200 rpm).
The values of the noise emitted by the studied machinery above 85 dB (A), for daily exposure of 8 h NR 15 (ABNT, 2021), are visualized in the operation regime, in general, up to 2 m on the right side and the front and 4 m at the rear and 2 m at the left side of the machine (Figure 4). The maximum noise emission value found in the tractor understudy was 91.20 dB(A), in the operator's seat (Figure 4). Thus, according to NR 15 (ABNT, 2021), the maximum exposure allowable daily is 3 h and 30 min. Thus, it is always recommended to use ear protectors when operating this tractor.
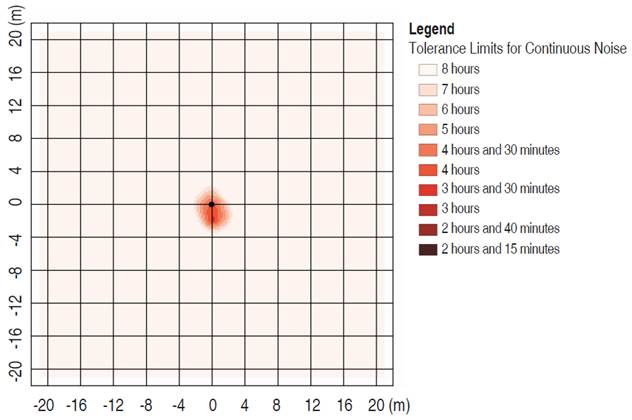
Figure 4 Map of the spatial distribution of the time of exposure to noise emitted by the tractor studied.
In Figure 5, the values related to noise levels obtained near the operator's ear are presented. At the front of the tractor, there was a similarity in the values of noise emitted by the tractor, indicating the noise emitted predominantly by the engine; however, only people located at distances greater than 4 m do not need to use PPE for shifts of 8 h.
Figure 6 shows the control chart of the averages of noise level variable. It may be that the process is controlled, it means that the points at the upper and lower control limits (UCL and LCL) show that the process suffered variations from common causes. Furthermore, there are probably more points below the control limits for the micro-tractor studied, which show that the operation of this machinery was closer to the control.
When the points outside these limits are observed, it is noted that these data were generated by incorrect data collection procedures or manufacturing years (Civardi, 2017). In contrast, when it comes to the sequences found, the main sequence pattern is when 7 (seven) or more consecutive points appear on just one side, below or above the midline (gray line). These sequences are more difficult to detect since it is necessary to analyze if the special causes will improve or harm the process (Nomelini et al., 2009).
In Figure 6, this phenomenon did not occur in the analysis of the individual control chart of the machinery under study. It is considering that the periodicity is a detectable configuration in the long term. The points are distributed as a curve that has an alternating up and downtrend. This variation can be associated, for example, with interference variability.
An individual control chart was chosen to be used as an evaluation parameter along with geostatistical data. The individual control chart (Figure 6) shows that across all single value/observation relationships, evaluated across 441 collected points, some points are outside the control limit. It can be seen that through the points collected, the value of the highest noise peak in the experiment was 91.2 dB (A), as shown in Table 1.
Still, analyzing the control chart present in Figure 6, it is possible to observe the convergence of the distribution values around the average and note that most of these values are close to their respective stages during the process. The points distribution is explained according to the coefficients of asymmetry and kurtosis with positive values, in which the distribution of values tended to be more to the left and more flattened. Therefore, in a positively asymmetric distribution, the tendency is for positive deviations to be much more significant than the negative ones. Concerning the behavior of the tail being more flattened, it is linked to the kurtosis value of the distribution, which is greater than 0.263 (Table 1), the distribution is flatter than the normal curve of the same area, and it is said to be a platicurtic curve. (Sindelar et al., 2014).
The individual control chart confirms that there were outliers in this case, as there were peaks in values within the subgroup and it was affecting the sample amplitude. Statistically, outliers are considered data outside the standard of the studied population; in this case, these data are considered interference peaks, which occur due to the influence of some external factor (Silva, 2019).
To sum up, Figures 3, 4, 5, and 6 illustrate the spatial distribution of noise that this machine may generate. These maps, based on the values recommended by NR 15 (ABNT, 2021) have fundamental importance for the management of acoustic health during the use of the agricultural machine, as they facilitate the understanding of the risks caused by noise exposure.
CONCLUSIONS
It was possible to characterize the structure and magnitude of spatial dependence of noise level emitted by the micro-tractor using the Wave model and its spatial distribution map through kriging.
The process has been studied in detail by the process control charts (SPC). It allowed identifying special causes according to variations in the process. Thus, it was possible to develop maps of the noise level emitted by the studied micro-tractor such as Spatial distribution map, Map of the spatial distribution of the time of noise exposure, and Map of necessity to use or not a Personal Protective Equipment (PPE), contributing to the management of acoustic health during the operation of the studied tractor.
For further studies, it is recommended to use a decibel meter and a dosimeter to improve the analyses. Also, it is useful to do this kind of study in other agricultural tractors, machines, and implements.