Vinasse is a liquid residue resulting from the distillation process from molasses or fermented sugarcane juice (Saccharum officinarum) to obtain ethanol in the production of rum, tequila, brandy, cachaça or bioethanol (Aristizábal 2015). In the liquor industry, for every liter of ethanol produced, 12 to 15 L of vinasse is obtained as a residue. Vinasse is a brown liquid with a low pH, sweet odor, and high content of dissolved and suspended organic matter (Conadesuca 2016).
García and Rojas (2006) indicate that vinasse contains soluble inorganic substances such as potassium and calcium, organic substances resulting from the metabolic process of yeasts and other microorganisms, alcohol and residual sugars, some insoluble organic substances, and volatile organic substances. The presence of high content of organic matter, potassium, and calcium, as well as moderate amounts of nitrogen and phosphorus, make it a highly polluting waste for water (Rajagopal et al. 2014), and its effects include a decrease in luminosity, photosynthetic activity and dissolved oxygen. It also causes eutrophication of water, contributes to an increase in insect and vector populations, resulting in the development of diseases.
There are different types of technologies for the handling and use of distillery vinasse. García and Rojas (2006) and Leal et al. (2003) studied the potential use of vinasse and concluded that, due to the presence of elements such as calcium, magnesium, sodium, potassium, zinc, and copper in adequate quantities, in addition to compounds and plant constituents such as free fatty acids, carbohydrates, amino acids, proteins, lipids, sugars among others, it can be combined with raw materials in order to produce animal feed.
Giraud and Rodríguez (2023) physicochemically characterized the vinasse and evaluated some alternative uses using the Hierarchical Analytical Process Method (AHP), where they considered the evaluated physicochemical potential, ease of production, utility in the market, and environmental contribution of the possible products as criteria; in the same way, they took into account as alternatives for the use of vinasse, liquid fertilizer (fertigation), pellet fertilizers, organic matter for the production of biogas and feed for livestock. The alternative recommended by consensus of the experts according to the AHP methodology was the feed for small animals and birds, accrediting as a key factor the high potential of the vinasse at the level of its physical-chemical characterization, particularly for its contribution of vegetable protein, fat, nutrients, and organic acids.
Likewise, previous studies indicate that the use of vinasse as part of the feed formulation for broilers increases their live weight and the efficiency of nutrient utilization by increasing digestibility and absorption, the latter attributed in part to the high contribution of B vitamins (Hidalgo et al. 2009; Rodríguez and Garcés 2015).
The design of feed for broilers is based on two aspects: 1) the need in Venezuela for an accessible source of protein such as chicken meat (Encovi 2022), and 2) the study by Hidalgo et al. (2009) shows that vinasse improves the immune system of chickens, which can be an important contribution since December 2022, Venezuelan poultry production has been impacted by a crisis of avian influenza (OPS 2023).
The Venezuelan poultry sector consists mainly of private companies that operate medium to large facilities for the production of chicken meat and eggs. On the other hand, within the diversity of breeds for broilers, there is the Cobb breed. In this breed, it is important to differentiate according to the commercial purpose between the male (meat production) and the female (egg production). They are characterized by their excellent growth rate with low-cost diets. Broiler diets are formulated to provide the energy and nutrients essential for broiler health and production efficiency. The basic nutritional components that birds require are water, amino acids, energy, vitamins, and minerals (Pronavicola 2018).
Based on what has been indicated, this study seeks to design a feed for broilers as an alternative use for vinasse. This approach would contribute to less management of this material as an environmental benefit and provide a lower-cost feed as an agro-industrial benefit.
MATERIALS AND METHODS
The study proposes the design of a feed for broilers considering vinasse in its formulation, including: 1) the formulation of the product, 2) the design of the production process for the feed, and 3) a proposal to evaluate the efficacy of the product in the bird growth.
Product formulation for broilers
Three formulations were designed according to the stage of the bird’s feeding plan (Table 1), taking as a reference the diet for a) EB 34 hybrid chickens used in the study by Hidalgo et al. (2009), b) laying hens of the Lohmann-Brown genetic line of Organización El Tunal (2023), and c) Japanese quails from the trial by Martins et al. (2017).
Table 1 Formulations designed for broiler feeding according to their different stages in the feeding program.
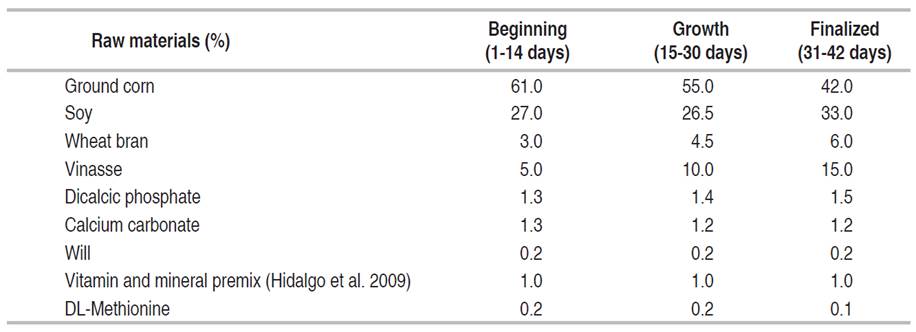
The broiler feed formulation was developed based on an extensive literature review and consultations with experts on the subject, resulting in a formulation for each stage of the poultry feeding program that meets the nutritional requirements of broilers, as shown in Table 1.
The amount of vinasse in the formulation is increased as the bird grows. The main physicochemical characteristics of this ingredient being those presented in Table 2. The amount of nutrients such as nitrogen, potassium, phosphorus, calcium, iron, and manganese, which are required in broiler feed for its proper development, stand out in the composition of the vinasse used in the study (Vásquez 2018).
According to Hidalgo et al. (2009), the inclusion of vinasse in the feed favors the feed conversion ratio, which means a reduction in costs by substituting ingredients such as molasses and cane juice. Additionally, vinasse is easy to produce and does not require any prior treatment before its inclusion in the preparation of the food.
Conversely, nitrogen-adjusted metabolizable energy (MI) was calculated for each formulation to quantify the total energy contribution (Table 3). The results indicate that the reported values remain within the recommended range for achieving optimal broiler growth performance, as reported by Torres (2018).
Design of the production process for food
The broiler feed production process involves eight phases: raw material reception, storage, raw material cleaning, grinding, mixing, sieving, pelletizing, and packaging. To test this design, future researchers must consider the bromatological analysis of the product in its different presentations, then verify the nutritional composition, and the presence of possible contaminants, to know its physicochemical properties, and rule out any microbiological contamination.
Figure 1 shows the diagram of the proposed manufacturing process of a broiler feed.
Process description
The process begins with the receipt and storage of dry macro ingredients and vitamins in separate silos, while the vinasse is received in tanker trucks and stored in a closed tank. The macro ingredients are cleaned to remove impurities and then screened to optimize the grinding process. Material with a size between 1.0 and 3.5 mm is transported directly to the weighing hopper, while larger particles of this size are crushed in a hammer mill. Material smaller than 1.0 mm in size is stored in a flour silo, as recommended for crumb and pellet feeds (Arbor Acres 2018). Vitamins and minerals are ground to a particle size of less than 3.5 mm, except for calcium carbonate which is supplied in particles of 2.0 to 4.0 mm (ISA Poultry 2010).
The macro-ingredients, vitamins, and vinasse are weighed and added to the industrial mixer according to the feed in the feeding stage to be produced to obtain a homogeneous mixture of the feed. If the feed is produced in crumbs, it goes directly to a packing scale (feed for the initiation stage), in case the feed is required in mini pellets or pellets, it continues the production line. In the latter case, the coarse powder is heat-treated (maximum 80 °C) by adding steam to a spiral conveyor belt. The increase in temperature reduces the percentage of moisture in the powder and additionally, together with the pressure of the pelletizer, the pellet is compacted in a better way, increasing its density and therefore its quality.
Once heat-treated, the hot powder is turned into pellets in the pellet machine to the desired diameter and then left to stand in a counter-current cooler. The final product is passed through a rotary sieve to ensure the desired particle size, weighed, and packaged in bird feed bags.
Proposal to evaluate the efficacy of the product in the growth of birds
The testing phase aims to provide an assessment of broiler feed that includes vinasse in its formulation, based on its impact on growth, feed conversion ratio, and overall health of the birds.
It is proposed to carry out the test in a chicken farm located in the state of Carabobo, Venezuela, where the average temperature is 31 °C, and there is a relative humidity of 59% (González 2017); the lighting and ventilation of the shed must be adequate (Pronavicola 2018). It includes a manual three-phase feeding system, ad libitum, with 60 male chicks of the Cobb breed, and an experimental design of completely randomized blocks (Gutiérrez 2015), distributed in two equal groups: a control group and another with the formulated feed. Each group is subdivided into three (subgroups of 10 chickens) to consider the repetitions of the trial covering the three stages of the poultry feeding program: initiation from 1 to 14 days, growth from 15 to 30 days, and termination from 31 to 42 days (Vásquez 2018).
During the trial, the supply of vinasse is proportional to the percentage indicated according to the stage of the feeding program in Table 1 and the amount of feed is fixed according to the nutritional needs of the breed, distributed in four daily rations. Before starting the trial, both groups of animals (control and formulated feed) are weighed to determine the average starting weight, and the feeding carcass is cleaned to ensure accuracy in the evaluation. Throughout the trial, feed is weighed before and after feeding to the animals to measure product acceptance and calculate the feed conversion ratio. At the end of each growth stage and before changing the feed ratio, the animals are weighed again on an empty stomach to determine the final weight. It is recommended at the end of the trial (42 days) to slaughter ten animals from each group to determine the total yield in carcass, breast, thighs and legs, viscera, and abdominal fat.
In Venezuela, poultry farms are located in the coastal area (western, central, and eastern) due to their proximity to both the ports through which most inputs arrive and the cities that are centers of consumption (Álvarez 2014). Based on this, the state of Carabobo is proposed as a site to carry out the testing phase of the formulated food. Additionally, the farm must have adequate lighting and ventilation conditions that allow the desired development of the broiler.
Before starting the feed testing phase, researchers must select 60 healthy chicks with 1 day of life. Likewise, during the development of the test, they must consider the vaccination plan required to maintain the birds’ health (Pronavicola 2018). Variables of interest are 1) the weight of the chicken before and after eating, 2) the weight of the chicken at the beginning and end of each feeding stage, and 3) the weight of the food consumed; With these variables, the aim is to calculate the acceptance of the product, the feed conversion ratio, and the growth of the chicken in the different stages of feeding, with which it can be defined as whether or not the formulated product meets the desired objective, that is, that the vinasse within the formulation of the feed for broiler feeding is beneficial.
CONCLUSION
The study shows that it is possible to design a broiler feed containing vinasse that meets the essential nutritional requirements. The amount of vinasse used in the feed aligns with the recommended daily dietary intake for broilers, which falls between 12,351.06 to 14,025.78 kJ•kg-1. A production process was developed for the feed in three different forms (initiation, growth, and completion), integrated into the standard broiler feed production line, and made ready for introduction to the market.
For future research, it is suggested to conduct a test phase to evaluate the effectiveness of the feed, as well as an economic study to assess its feasibility for broilers. It is also recommended to carry out field trials with varying proportions of vinasse in broiler feed, involving different genetic lines and/or other poultry species, to expand the scope of the study and provide practical application insights.