Introduction
Recently, studies have centered on nanomaterials with magnetic behavior that have different applications in physics, chemistry, and medicine due to their optical properties, as well as in other fields (Blanco-Gutiérrez, et al., 2013; Kisan, et al., 2014; Blanco-Gutiérrez, et al., 2010; López-Ruiz, et al., 2012; Muñoz, et al., 2013). They are also used as a contrast in vascular diagnostic imaging (Bakenecker, et al., 2020), like temperature sensors in MRI (Hankiewicz et al., 2019), and as an alternative treatment for patients with cancerous tumors through magnetic fluid hyperthermia (MFH) (Benhal, et al., 2019). In environmental remediation, their ability to retain metals and contaminants, such as chromium VI in contaminated water resulting from the corrosion caused by the stainless-steel present in nuclear reactor shells, has been tested as well, which is vital given the risk it represents for the environment and human health (Ismail, et al., 2019). Similarly, they have proven useful to detect Salmonella in milk quickly and efficiently (Jin, et al., 2020) and in the processing of cooking oil waste to make biodiesel using magnetic nanoparticles as a catalyst (Touqeer, et al., 2020).
Magnetic nanoparticles can be obtained by chemical and physical methods (Wang & Zhang, 2020), using a hydrothermal method based on low-temperature coprecipitation (Chellappa & Vijayalakshmi, 2019), or by self-combustion (Sontu, et al., 2018).
Within the wide variety of magnetic nanoparticles, iron oxides such as magnetite Fe3O4 and maghemite Fe2O3 stand out due to their stability and accessibility. Magnetite is stable in the pH range between 8 and 14 in an environment where no oxidation is present. The composition has a ratio of 2:1 of Fe3+ and Fe2+ ions whereas if the process is carried out in a potentially oxidizing environment what maghemite is obtained (Toma, et al., 2016).
In the present study, we compared three chemical methods for obtaining magnetic Fe nanoparticles, each of them with a different degree of difficulty. We specifically compared their effectiveness in obtaining a homogeneous morphology and nanometric scale and an adequate elemental composition, i.e., with no contamination of the precursor elements of the process and with a highly crystalline structure.
One of the synthesis methods discussed in our study was coprecipitation in an aqueous medium without temperature, which has a medium-level complexity and can be carried out in a standard laboratory. This method was used by Arévalo, et al. (2017) with a great variety of precursors, such as polymeric surfactants, polyvinyl alcohol, and others, and they achieved a high level of reliability in the synthesis of particles with nanometric dimensions and spinel structure, which is characteristic of magnetite. Other researchers obtained similar results when using this method with different precursors (Houshiar, et al., 2014; Iranmanesh, et al., 2018; Raeisi-Shahraki, et al., 2012).
The second synthesis method we analyzed was the obtention of magnetic Fe nano-particles by using ferrous sulfate as the main precursor for coprecipitation at a constant temperature of 90°C. A similar process using the same main precursor but a different chemical synthesis method was conducted by Tao, et al. (2020). In their study, they made the physicochemical analysis of the sustainable production of Fe2O3 nanoparticles from the reduction of ferrous sulfate with coke, thereby optimizing the sulfur recycling process resulting from the obtention of white titanium (Ren, et al., 2017). The third method we explored was coprecipitation without temperature where the precursor is an alternative element such as iron filings obtained from nails or wires and immersed in an acidic medium, such as vinegar, for a period of 12 to 24 hours (Toma, et al., 2016).
Materials and methods
Nanoparticles were obtained through three synthesis methods which we describe below:
Synthesis method 1
In this method, we used coprecipitation in an aqueous medium without temperature mixing the Fe2+ and Fe3+ precursors in an alkaline medium (Toma, et al., 2016). First, we prepared two solutions in distilled water in beakers: one with 1.079 M de FeSO4 7H2O and another with 2.1458 M de FeCl3 6H2O. These two solutions were then mixed using a mechanical agitator with a polymer impeller at 1000 rpm for 5 minutes. Subsequently, we prepared a solution with 0.3 M de NaOH in distilled water and added it to the previously made mixture, we then incorporated the three solutions and stirred again at 1000 rpm until the initially orange mixture changed to black, after which we continued to stir for another 15 minutes. Once the mechanical agitation finished, magnetic nanoparticles (MNP) were separated using a neodymium magnet, subsequently decanted with acetone, and, finally, completely dried by applying temperature on a watch glass to eliminate all the humidity. Figure 1 shows an outline of the method.
Synthesis method 2
Figure 2 shows an outline of the second synthesis method where we used a mechanical stirrer with a polymer impeller and a temperature plate to maintain a constant temperature of 80 to 90°C in the mixture throughout the stirring process. The 66x10-3 M solution of FeSO4 7H2O was prepared in distilled water and mixed with two previously prepared solutions: the first one with 56.05x10-3 M de KNO3 and the second one with 1.485 M de KOH, both in distilled water. Then the beaker with the mixture was placed on the preheated plate, the temperature was quickly stabilized between 80 and 90°C, and, then, the mixture was stirred at 1000 rpm. When we started the mixing of the three solutions, the color was green which later turned to black due to the reactions produced by the agitation and the temperature. After this color was reached, we continued agitating for 20 minutes and, finally, we checked the alkaline pH of the product at a range between 12 and 14. Then the NPMs were separated using a neodymium magnet and decanted with acetone for their subsequent drying (Toma, et al., 2016).
Synthesis method 3
For the development of the third method, a lance was used as the main precursor, which was kept immersed in a beaker with vinegar for a period of 24 hours to obtain an iron solution. This precursor was selected and used as recommended by Toma, et al. (2016) for non-conventional materials potentially suitable to obtain NPMs. After the 24-hour period, the medium had elapsed and we separated the lance and the iron solution obtained: one third in one beaker and the remaining two thirds in another one. Then, we slowly added 10 volumes of hydrogen peroxide to the beaker containing two-thirds of the iron solution until it changed from yellow to black. Subsequently, the black solution obtained was mixed with the remaining iron solution and a 5 M solution of NaOH in distilled water. The final mixture was stirred with a glass mixer to homogenize it until the black color was obtained again in the final product. The resulting NPMs were then separated using a neodymium magnet, decanted using acetone, and, finally, dried to remove the moisture. Figure 3 shows an outline of this synthesis method.
We analyzed the morphology of the three totally dried nanoparticle samples by scanning electron microscopy in a Vega3 Tescan electronic microscope and we measured their size by implementing the free version of the Image J computational tool (Schneider, et al., 2012).
The elemental characterization of the samples was performed using a Bruker XFlash® 410-M EDS probe coupled to the scanning electron microscope.
The structural characterization was carried out by X-ray diffraction (XRD) in a PANalytical X'Pert Pro diffractometer with a Co anode, a wavelength of Kα=1,789 Å, a current of 40 mA, and a voltage of 40 kV using the Bragg Brentano configuration with an angular step of 0.013° and an exposure time of 10 s.
Results and discussion
Morphological characterization
Figure 3. Simplified scheme of synthesis method 3
Figure 4a, obtained by scanning electron microscopy at 8.72 kX, shows the results for the synthesis method 1 revealing a random distribution of particles of different sizes with irregular granular formations of the particles and an average size of 2.31 ± 1.05 μm. Grey tones corresponding to the elements present in the sample Na, S, Cl, and Fe are evident in the image of backscattered electrons.

Figure 4 SEM micrographs of the samples. (a) Synthesis method 1, (b) Synthesis method 2, (c) Synthesis method 3
The results from the scanning electron microscopy at 70 kX for synthesis method 2 (Figure 4b) showed a spherical and uniform morphology. We calculated the average particle size obtaining a value of 104 ± 27 nm. These results are similar to those obtained by Mohamad, et al. (2020) where the glutathione catalyzed nano-magnetite particles appeared as scales and spheres with a particle size in the range of 50 to 100 nm. These results are also similar to those obtained by other researchers (Shahid & Choi, 2020; Nurlilasari, et al., 2020).
Synthesis method 3 (Figure 4c) at 8.72 kX showed particles of irregular morphology with an average size of 4.03 ± 1.95 μm, which evidences that this method can produce micrometric particles due to the low speed of agitation used during the obtention process and the nature of the precursor elements.
Composition
In the spectrum of figure 5a, we observed a marked presence of Fe and O from which the possible formation of iron oxides can be inferred, as explained by Rodríguez-López (2012) in his doctoral work on the study of the synthesis and characterization of magnetite nano-particles where he pointed out that this is the typical elemental composition of iron oxide particles. The appearance of elements such as Cl, S, and Na as residual traces of the precursors used in this method is evident as it has been reported in other studies by Rodríguez-López, et al. (2012) where they obtained magnetite particles using electrochemical methods.
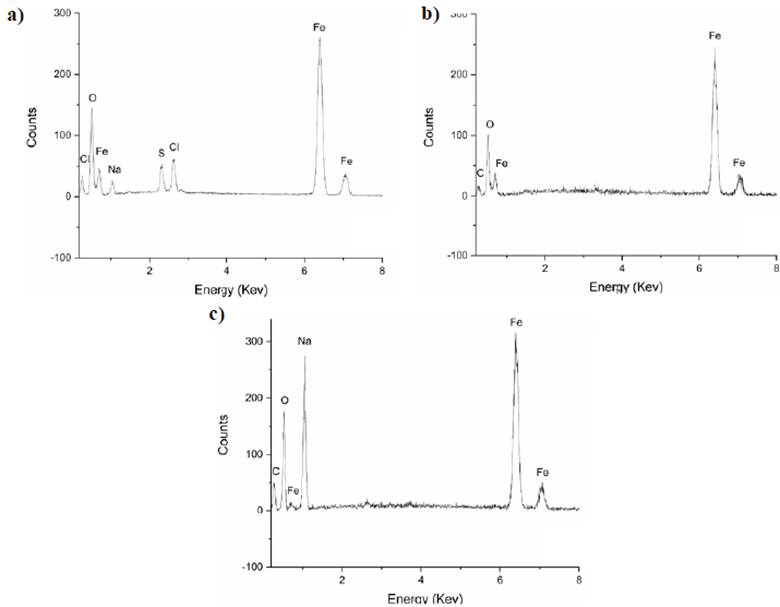
Figure 5 Elemental composition by EDS of the samples. (a) Synthesis method 1, (b) Synthesis method 2, (c) Synthesis method 3
The elemental composition shown in figure 5b corresponds to the sample obtained by using synthesis method 2, which presents a high purity since no peaks different from those of Fe and O are evident. However, the C, corresponding to the graphite tape used for the positioning of the powder in the scanning electron microscope camera, can be identified. Since the elements detected are Fe and O (as in method 1), we can infer that these particles correspond to iron oxides. This result is consistent with the investigations by Yuan, et al. (2020) where magnetite coatings were characterized.
The results of Method 3 are shown in figure 5c with the EDS spectrum showing a high presence of Fe, which indicates that these particles may be iron or iron oxides due, again, to the oxygen peak detected. The presence of Na, a product of the precursors, is strongly marked.
Structural characterization
Figure 6a shows the diffractogram obtained for the sample synthesized by method 1 where the peaks corresponding to the crystalline structures of iron oxides are clearly observed. We also detected that the presence of magnetite was consistent with the diffraction pattern identified in the databases under ICDD No. 01-075-0449 and the magnetite identified under ICDD No. 00-025-1402. In Shahid & Choi's (2020b) study, the presence of these structures was evidenced in the samples obtained from industrial waste by inverse coprecipitation in the open air. Those samples showed magnetic behavior and structural results equivalent to those obtained in our study for the maghemite and magnetite phases.
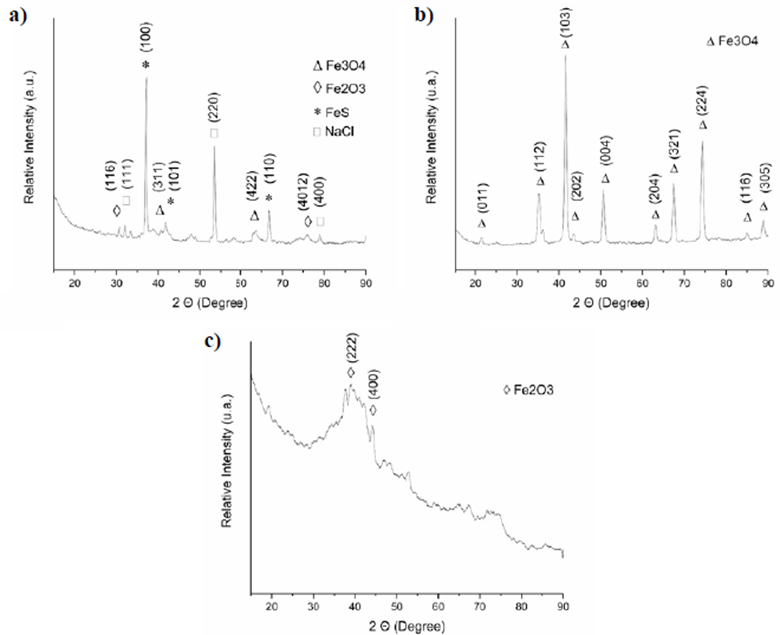
Figure 6 Diffractograms of the samples. (a) Synthesis method 1, (b) Synthesis method 2, (c) Synthesis method 3
As observed in the EDS, this sample had additional elements such as S, Cl, and Na, which formed crystalline salt structures such as NaCl matching the diffraction pattern identified by ICDD reference No. 00-002-0818 and FeS identified by ICDD reference No. 00-049-1632 in the process of obtention.
The diffractogram in figure 6b (synthesis method 2) allowed the identification of the formation of a single orthorhombic crystal structure present in the sample corresponding to the characteristic peaks of magnetite (Fe3O4). Those peaks matched with the diffraction pattern identified as ICDD reference No. 01-075-1609, an iron oxide known as magnetite with ferromagnetic behavior (Noval, et al., 2017). This result is similar to the diffraction pattern obtained in the study conducted by Singh, et al. (2020) where they obtained and characterized magnetite-ZnO nanocomposites in which the magnetite had an equivalent diffraction pattern. In this sample, a greater definition of the diffraction peaks was observed due to the temperature used in the process, a similar behavior to that obtained by Picasso, et al. (2012) using low and high temperatures during the process for obtaining magnetite particles by sol-gel and coprecipitation.
The diffraction pattern in figure 6c corresponds to the sample obtained with synthesis method 3: A mostly amorphous structure and two peaks corresponding to the iron oxide known as maghemite (Shokrollahi, 2017) coinciding with the diffraction pattern identified with the ICDD reference No. 00-039-0238. Patra, et al. results (2019) were similar, as they obtained amorphous maghemite by direct solid-state synthesis. This type of structures, especially amorphous nanoparticles, have different physicochemical properties showing weaker magnetization responses than those shown by the same nanoparticles with a defined crystalline structure (Hoang & Ganguli, 2012).
Our results using methods 1 and 2 are consistent with those reported in the literature in terms of morphology and particle size, meaning they are easily accessed and developed to obtain maghemite and magnetite nanoparticles.
Conclusions
The elemental composition of the samples analyzed by EDS primarily included Fe and consistent with results reported in the literature regarding the composition of magnetic iron nanoparticles.
Method 2 did not present traces of any element other than Fe and O, however, methods and 3 had traces of elements such as Na, S, and Cl, which are products of the precursors.
The samples obtained by method 2 showed crystalline magnetite structures while those obtained by synthesis method 1 showed structures of magnetite, maghemite, iron sulfide, and sodium chloride, and synthesis method 3 was characterized by the formation of an amorphous structure with small maghemite spikes.
These results showed that the obtention method has a great influence on the morphology and particle size with the sample obtained by method 2 being the most suitable in terms of its homogeneous, spherical, and nano-sized shapes up to 80 times smaller than those achieved by method 3 and up to 40 times smaller than those from method 1. These results open up a range of possibilities regarding the size, structure, and magnetic properties of the particles for future applications.
The physicochemical properties, particularly the magnetic ones, are affected by the presence of elements other than Fe and O, as well as the presence of an amorphous structure, a property that will be studied in future studies.