INTRODUCCIÓN
La popularidad del uso de manufactura aditiva (AM por sus iniciales en inglés) o impresión 3D ha aumentado para la fabricación de productos personalizados en las industrias agrícola, automotriz y aeroespacial, en la ingeniería, en los sistemas biológicos y en las cadenas de suministro de alimentos [1] [2]. La AM es un proceso asistido por computador que fabrica objetos 3D físicos capa por capa, a partir de datos de un modelo sólido virtual (CAD), con materiales metálicos, plásticos, cerámicos, compuestos o biológicos. En la actualidad existen diversos sistemas disponibles de manufactura aditiva en el mercado, entre los que se encuentran modelado por deposición fundida (FDM por sus iniciales en inglés), deposición directa de metal (DMD), sinterización selectiva por láser (SLS), modelado por inyección de tinta (IJM) y estereolitografía (SLA), entre otros [3]. La adopción de estas tecnologías ha propiciado el diseño de piezas de libre acceso, sobre las cuales la información es limitada debido, por un lado, a la falta de conocimiento sobre el desempeño final de las piezas durante el servicio [4] [5] y por otro, a la falta de soporte para el software de diseño empleado. Las piezas construidas por AM poseen propiedades mecánicas anisotrópicas que son inherentes a este proceso de fabricación. Los datos de las propiedades reportadas por las diversas compañías que fabrican estas tecnologías no son comparables entre sí, debido a que no brindan suficiente información sobre los parámetros del proceso. Por lo tanto, el uso de partes impresas en 3D requiere el reporte público de los datos de las propiedades mecánicas finales de la pieza [6] para una aplicación específica.
Una de las tecnologías más utilizadas para la fabricación de piezas mediante AM es el FDM, ya que es una de las más económicas y posee un sistema de extrusión flexible [7]. El FDM es un proceso en el cual un filamento, generalmente de acrilonitrilo butadieno estireno (ABS) o ácido poliláctico (PLA), pasa a través de una resistencia y llega a un estado semifundido; luego, una boquilla es alimentada por este filamento y se deposita de forma entrecruzada en la pieza parcialmente construida. Los materiales extruido y recién depositado se fusionan entre sí, y luego la boquilla se mueve en el plano XY conforme deposita material según la geometría de la pieza. La plataforma que contiene la pieza se mueve de forma vertical en el eje Z para depositar una nueva capa sobre la anterior. Después de un periodo de tiempo -por lo general, varias horas-, la boquilla habrá depositado una representación física completa del archivo CAD original (figura 1) [8] [9].
La tecnología de FDM reviste interés para la academia y la industria debido a su capacidad de fabricar geometrías complejas a costos relativamente bajos, su facilidad de utilización y su compatibilidad con materiales reciclables [10] [11] [12]. La calidad y las propiedades mecánicas de las piezas construidas mediante FDM dependen de una selección adecuada de parámetros que intervienen en el proceso de impresión (figura 2). La incidencia de estas variables sobre el acabado y el desempeño de la pieza final requieren ser estudiados para obtener las condiciones óptimas durante el proceso de impresión.
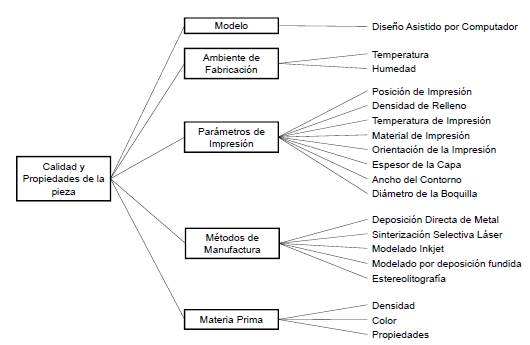
Fuente: adaptada de [9].
Figura 2: Parámetros que modifican la calidad y propiedades de la pieza en FDM
En la actualidad, el principal uso que se da a las piezas fabricadas mediante FDM corresponde a ayudas visuales y presentación de prototipos, ensambles o modelos educativos. Debido a los avances tecnológicos en la técnica de FDM y la disminución de costos, se ha incrementado el número de usuarios domésticos que utilizan esta técnica y han surgido muchos software de código libre para el uso de estas impresoras -Cura y Repetier-host, por nombrar solo algunos-, los cuales permiten modificar parámetros como los que se muestran en la figura 3; estos influyen en las propiedades mecánicas, el acabado y la calidad de la pieza final.
El diseño de piezas con FDM que involucren mejores acabados y buen desempeño mecánico, y en cuya fabricación se empleen las herramientas y ventajas de la técnica al tiempo que se minimicen sus limitaciones, es una tarea que está ganando atención por parte de la comunidad científica y académica. Además, visto que la mayoría de los usuarios domésticos no tienen forma de verificar la resistencia de las piezas que se imprimen; que tampoco hay suficiente información disponible sobre las propiedades mecánicas finales y del desempeño de las piezas impresas; y que no existen investigaciones que involucren la tenacidad de las partes fabricadas por FDM, resulta pertinente analizar la influencia de algunos parámetros de impresión que intervienen en el proceso FDM en las propiedades mecánicas de las piezas finales.
Con lo anterior, este artículo describe un proceso de análisis respecto de los cambios en las propiedades mecánicas de probetas impresas en ABS sometidas a esfuerzos de tensión, al variarse los parámetros de densidad del relleno, la orientación de la pieza al imprimirla y su ángulo ráster (ángulo de la trayectoria del filamento con respecto al eje x), lo cual implica un cambio de dirección en las fibras impresas. La orientación hace referencia a la forma en que la pieza se ubica con respecto a los ejes X, Y y Z de la plataforma; y la densidad de relleno se define como el porcentaje de polímero impreso al interior de la pieza con respecto al espacio total dentro de ella: 100 % indica que el relleno de la pieza es solo polímero y no hay ningún espacio entre las fibras. La información recolectada tiene el fin de proporcionar criterios de resistencia de los productos finales a los usuarios de impresoras controladas por programas con código abierto.
1. MATERIALES Y MÉTODOS
Para determinar las propiedades mecánicas de las piezas impresas y su dependencia a los parámetros de impresión que es posible alterar en una impresora 3D, se analizaron la incidencia de la orientación de la pieza a imprimir y el porcentaje de relleno (densidad) en la resistencia a la tracción, el módulo de rigidez y la tenacidad. Las piezas se imprimieron en dos posiciones y orientaciones específicas, -45745° (XY) y 0790° (XZ), (figura 4), y las densidades de relleno fueron 30 %, 50 %, 75 % y 100 %.
Los demás parámetros se mantuvieron constantes para todas las configuraciones de impresión. La altura de capa fue de 0,3 mm; el espesor de contorno, 1,2 mm; la velocidad de impresión, 30 mm/s; y el diámetro de boquilla, 0,4 mm (la tabla 1 muestra las configuraciones utilizadas). En total se imprimieron 101 piezas.
Se fabricó un mayor número de probetas en la posición XZ debido a que de tal modo era posible imprimir más probetas de forma simultánea. Además, se desecharon las piezas que después de haber sido elaboradas presentaban algún defecto geométrico. Para esta investigación no se tuvo en cuenta la incidencia de las condiciones ambientales en la impresión, las cuales pueden afectar levemente los resultados [13] [14].
Se utilizó una impresora Ultimaker 2 [15] junto con el software de código abierto Cura 2.4, recomendado para ese modelo. El polímero usado en las impresiones fue un filamento de ABS SKU: ABS32 natural blanco, con una resistencia última a la tensión de 33 MPa, un módulo elástico de 2,2 GPa y una elongación de 6 %. Se diseñaron las probetas conforme a la norma ASTM D638 [16]in the case of revision, the year of last revision. A number in parentheses indicates the year of last reapproval. A superscript epsilon (' tipo I: cada espécimen tenía 3,3 mm de espesor. Luego, se hizo el modelado geométrico en el programa Autodesk Inventor 2017 (figura 4) y se exportó lo anterior al formato STL (stereo litographie). La temperatura de extrusión fue de 210 °C y la cama fue precalentada a 85 °C para favorecer la adhesión del material a ella.
Los ensayos de tracción se practicaron de acuerdo con la norma ASTM D638 para probeta tipo I en una máquina Shimadzu AGX Plus; se empleó una celda de carga de 500 kg clase 1 con una resolución de 1/5000. La velocidad utilizada para el ensayo fue de 5 mm/min, y para determinar el módulo elástico del material para cada configuración de la probeta se utilizó un extensómetro axial Epsilon 3542-050M-020-ST. En la figura 5 se muestra el montaje del ensayo.
2. RESULTADOS Y DISCUSIÓN
En esta investigación se analizó la variación del módulo de rigidez con respecto al porcentaje de relleno de la probeta y de la orientación en la cama de impresión; también se obtuvieron valores para los esfuerzos de fluencia y máximos en cada uno de los casos, al tiempo que se calcularon los valores de tenacidad y se relacionaron con los valores de esfuerzos.
En la figura 6 se presentan las curvas de esfuerzo-deformación para cada orientación de impresión y las densidades de relleno de 30 %, 50 %, 75 % y 100 %. La configuración de impresión XY se representa con líneas de color azul, mientras que XZ está representada con líneas rojas. En esta figura se observa que el módulo de elasticidad y la resistencia máxima son afectados por la posición de impresión de la probeta. En esta línea, las probetas fabricadas en posición XY presentan un rendimiento a tracción inferior, es decir, poseen un esfuerzo máximo a la tensión y un módulo de elasticidad menor que en el caso de las probetas elaboradas en posición XZ, lo cual concuerda con los resultados presentados en otras investigaciones [1] [8] [9] [14].
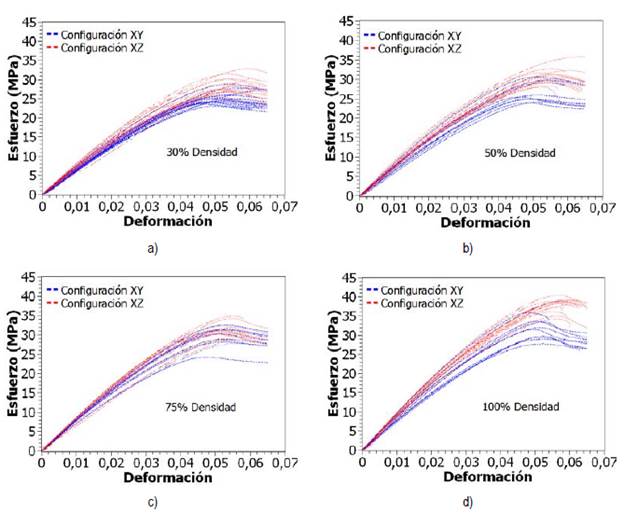
Fuente: elaboración propia.
Figura 6: Gráficas esfuerzo vs deformación según densidad: a) 30 %; b) 50 %; c) 75 %; d) 100 %
Los resultados de los módulos de elasticidad y los valores de las tenacidades se observan en la tabla 2. Respecto a las posiciones de impresión X y XZ se encontró que los valores más altos de módulo de elasticidad se presentan en la posición XZ. Además, las probetas con densidades superiores al 75 %, al margen de su posición de impresión, obtienen los valores de E más altos, por encima de 1,5 GPa, lo cual representa una disminución del 5 % con respecto al valor del módulo de elasticidad del material sin extruir; para las demás configuraciones estudiadas, esta variación llegó hasta el 14 %. Estas observaciones son similares a las reportadas por Behzad et al. [17], quienes realizaron un estudio con ABS variando la configuración de impresión y el número de capas. En otros estudios se han encontrado módulos de elasticidad para el ABS que varían de 1,0 a 1,9 GPa [14] [18]. Se observa entonces una tendencia al aumentar del valor del módulo con el incremento del porcentaje de relleno. En algunos casos se observó discrepancia en los resultados, pero esto pudo deberse a la falta de control sobre la temperatura ambiente del cuarto de impresión, por cuanto esta afecta la adhesión de la capa de material depositado por la boquilla [9] [19].
Tabla 2 Valores promedio del módulo de elasticidad y de la tenacidad para cada posición de fabricación y porcentaje de relleno
Relleno de la probeta | ||||
---|---|---|---|---|
Posición de fabricación | 30 % | 50 % | 75 % | 100 % |
Exy (GPa) | 1,44 ± 0,04 | 1,39 ± 0,04 | 1,58 ± 0,14 | 1,62 ± 0,1 |
Exy (GPa) | 1,49 ± 0,04 | 1,48 ± 0,02 | 1,78 ± 0,09 | 1,89 ± 0,12 |
T XY (MJ /m3 ) | 1,34 ± 0,33 | 1,99 ± 0,8 | 1,26 ± 0,12 | 1,31 ± 0,1 |
T XY (MJ/m3 ) | 1,61 ± 0,35 | 1,64 ± 0,52 | 1,24 ± 0,15 | 1,48 ± 0,12 |
Fuente: elaboración propia.
En la figura 7 se observan los valores promedio y las desviaciones estándar obtenidos para los valores de los esfuerzos de fluencia y máximos de los diferentes porcentajes de relleno y posiciones estudiadas; para calcularlos se empleó la metodología planteada por la norma ASTM D638 [13]. Se observa que la posición XY ostenta menores valores de esfuerzos máximos y de fluencia, lo cual concuerda con los resultados reportados por Sung-Hoon etal. [8], Wang etal. [20], Sood et al. [21] y Rayegani y Onwubolu [22] que realizaron experimentos con cambios en el ángulo raster y orientación, y Tymrak et al. [14], que experimentaron bajo condiciones ambientales reales. En estos artículos también se pudo apreciar que al aumentar el porcentaje de relleno de las probetas, los valores de los esfuerzos también aumentan. Para ninguna de las posiciones estudiadas se logró alcanzar los valores reportados para el material base (filamento) de la extrusión; como se mencionó, este es uno de los factores que causa incertidumbre frente a las piezas fabricadas mediante FDM [6], y esto se hace más notorio al fabricar piezas con un porcentaje de relleno menor.
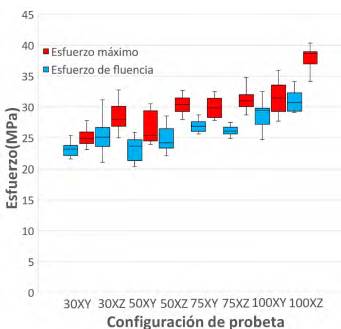
Fuente: elaboración propia.
Figura 7 Esfuerzos de fluencia y máximo para cada una de las probetas ensayadas
La relación entre la tenacidad y el módulo de elasticidad para las probetas ensayadas se puede observar en la figura 8; esta relación es importante en aplicaciones en que no solo se busca resistencia mecánica, sino la combinación de las dos propiedades. En estas relaciones se observa que, para las probetas con menor valor de módulo elástico, se obtiene más dispersión en los datos de la tenacidad, es decir, se genera mayor incertidumbre en el comportamiento global de la pieza impresa; además, se obtienen valores promedio ligeramente mayores para estas mismas probetas.
A partir de porcentajes de relleno de 75 % se puede decir que la tenacidad permanece constante, lo cual puede atribuirse a que los airgaps y la densidad de relleno determinan la dimensión de la zona de contacto entre los filamentos y las capas [23]. Por lo tanto, cuanto más densa la pieza, más juntos estarán los filamentos, lo que incrementa la resistencia de la unión de los filamentos y, por ende, la resistencia de la pieza final.
En la figura 9 se observan los modos de falla para las probetas: todas fallaron en la dirección transversal. Además, se percibe el efecto del blanqueamiento (whitening) [24] [25] [26] reportado para este tipo de materiales, causado por la deformación localizada: esta consiste en que algunas fibras se tornan de un color más claro que el mostrado por el original en la pieza fabricada. Se nota que las probetas impresas en la orientación XZ presentan una fractura frágil, mientras que las impresas en la orientación XY presentan fractura dúctil. También se observa que las probetas impresas en XZ evidencian mecanismo de retraso al crecimiento de la grieta, lo que se traduce en un aumento de la energía de fractura. Esto se aprecia en los datos de la figura 8: se observa allí que se pueden obtener mayores valores de tenacidad para las probetas con menor densidad de relleno, efecto que puede ser ocasionado por la orientación de las fibras; y que la sección trasversal efectiva de estas últimas cambia de acuerdo con la orientación de impresión, datos que guardan relación con los reportados por Sung-Hoon [8].
3. CONCLUSIONES
Como se ha dicho en secciones previas, el objeto de la investigación mostrada fue revisar la incidencia de la posición de impresión y la densidad de relleno en las propiedades mecánicas de ABS impreso por medio de FDM con dos tipos de orientaciones y cuatro densidades. El análisis de las curvas esfuerzo-deformación indicó que tanto la posición de fabricación como el porcentaje de relleno tienen un impacto en el rendimiento de las propiedades mecánicas de la pieza elaborada. La posición XZ y el 100 % de densidad presentaron los mayores valores para los módulos de rigidez y los esfuerzos; mientras que para valores de densidad inferiores al 50 % se obtuvieron los mayores registros de tenacidad.
Al elaborar piezas con porcentajes de relleno inferiores al 75 % las propiedades mecánicas de rigidez, límite de fluencia, límite último y tenacidad presentan variaciones excesivas (que pueden superar el 80 %), las cuales no permiten establecer con claridad criterios de diseño y de falla. Por tal motivo, es recomendable hacer pruebas para las piezas elaboradas por manufactura aditiva, a fin de establecer su comportamiento en el entorno real de trabajo.
RECOMENDACIONES
Se debe establecer un criterio de funcionamiento principal; es decir, si se desea una pieza con una buena relación de resistencia mecánica, es aconsejable emplear densidades mínimas del 75 % y que la fuerza aplicada sea paralela a la dirección de las fibras en la pieza fabricada. Si, por el contrario, la aplicación necesita una mayor tenacidad, se recomienda emplear densidades inferiores al 50 % y que la dirección de las fibras de la pieza sea de 45° con respecto a la dirección de la carga aplicada.