1. Introduction
The petroleum industry produces large amounts of wastewater. According Khatib and Verbeek [1] the ration between oil and water productions can reach 1:3, depending on the well maturation. that needs to be properly treated before being discharged or reused. In particular, the water produced during extraction of oil and gas has varied composition in function of the different types of geological formations and additives used during production [2,3]. Likewise, the wastewater from refineries contains a wide range of compounds, since low solubility hydrocarbons until nitrogen molecules, besides chemicals added to break down oil-in-water or water-in-oil emulsions during the refining or extraction process, to enhance extraction and refining [4]. Therefore, both produced water and refinery wastewater contain contaminants that can cause negative impacts on the environment, such as fish mortality and eutrophication in aquatic environments, and soil contamination, in the case of terrestrial environments, even in small quantities [5-8]. One of these contaminants is ammonium [9].
In the environment, ammonium is responsible for causing eutrophication, which is the process of exhaustion of oxygen in water due to the accumulation of nutrients, principally nitrogenated ones, causing the death of aquatic animals and posing risks to human health [10,11]. To control the environmental discharge of harmful substances such as ammoniacal nitrogen, Resolution 357/2005 from Brazil’s National Environmental Council (CONAMA) defines a maximum of 20 ml of ammonium per liter of wastewater discharged in water bodies [12]. However, in the state of Rio de Janeiro, the State Environmental Institute (INEA) sets a limit of 5 mg of ammonium per liter of liquid waste, including treated sewage, discharged directly or indirectly into surface water, groundwater or seawater [13].
Various processes are used to treat effluents containing ammonium. The processes employed depend on: (i) the total concentration of ammonium present in the wastewater, since some processes are more suitable for treatment of diluted solutions and others are better to treat concentrated solutions; and (ii) the type of effluent to be treated. When the ammonium concentration is high (greater than 500 ppm mg/L) [14], the main treatment methods used are biological processes [15], extraction with solvents [16] and electrolysis [17]. In turn, when the concentration is low (less than 200 mg/L) [18], the chief processes used involve adsorption by ion exchange. This type of treatment is applicable when the need is to “polish” previously treated water to decrease the concentration of ammonium below the maximum level of 5 mg/L, as required in the state of Rio de Janeiro. Zeolites [19] and polymeric resins [20,21], both containing acid groups in their structure, can be used as adsorbents. The advantages of using porous polymeric resins are variously based on the facility of desorption, enabling the reuse in other treatment cycles, the selectivity established by the choice of the monomers forming the resin, and/or the reactions to subsequent chemical modifications to insert acid or basic groups to increase the chemical affinity for the ions to be adsorbed, and consequently the adsorption efficiency [22,23].
Considering that the choice of the monomer for synthesis of a determined porous crosslinked polymeric resin and its subsequent chemical modification directly influence the efficiency of removing ammonium from water, and that according to the literature the polymeric resin used most often in the ion exchange process for adsorption de ammonium is synthesized from monomers of styrene and divinylbenzene [23], it is important to investigate new resins that can be modified for this purpose. With this, the aim is to reduce the production costs and attain suitable ammonium adsorption efficiency for polishing aqueous solutions with low ammonium concentration. Besides this, the development of a multifunctional resin would enable removal of other contaminants, such as heavy metal cations and/or aromatic hydrocarbons, also present at low concentrations.
Therefore, in this study we synthesized three base resins for subsequent submission to sulfonation reactions. These resins were composed of divinylbenzene (DVB), glycidyl methacrylate and divinylbenzene (GMA-DVB) or styrene and divinylbenzene (STY-DVB). In the resins based on glycidyl methacrylate (GMA) and styrene (STY), the divinylbenzene acted as crosslinker. The materials obtained were submitted to sulfonation reactions, for various time periods, to learn and evaluate the effect of the duration of the reaction on the porosity and adsorption capacity. The modified substances were then assessed regarding their efficiency in removing ammonium from water, to reduce the concentration of ammonium of the aqueous solution to the level required by the standard INEA (NT 202, R-10) [20,24,25]. This efficiency evaluation was carried out in a batch regime, with synthetic water samples containing ammonium ions. The results were analyzed by applying two thermodynamic adsorption models (Langmuir and Freundlich), considering the quantity of adsorbed ammonium cations in function of the variation of resin mass.
2. Materials and methods
2.1 Chemicals
Toluene, 99% heptane, hexane (mixture of isomers), dichloromethane, isopropyl alcohol, ammonium chloride, 98% sulfuric acid, acetic anhydride and sodium chloride, all analytical grade, and synthesis grade benzoyl peroxide were supplied by Vetec Química Fina - Duque de Caxias. Gas chromatography grade glycidyl methacrylate was supplied by Sigma-Aldrich Brasil - São Paulo, commercial grade styrene was donated by Petroflex Indústria e Comércio - Duque de Caxias, commercial grade divinylbenzene (55%) was donated by Dow Chemical Company - São Paulo, and bovine gelatin was acquired from Theoberg Importações e Exportações - Rio de Janeiro, all chemicals were used as received.
2.2 Adsorbent materials synthesis
Five polymeric resins were obtained through suspension polymerization, three based on glycidyl methacrylate (GMA) and divinylbenzene (DVB) and one containing only DVB. In all cases, the crosslinker was DVB. Bovine gelatin was used as suspension agent and benzoyl peroxide as initiator. Mixtures of heptane (HEP) and toluene (TOL) in different proportions were used as porogenic agent. We also used a previously synthesized resin based on styrene (STY) and DVB [26]. These resins are identified in Table 1. In all the synthesis reactions, a pre-polymerization step was conducted with the monomers and initiator (1% mol in relation to the monomers) at 50 ºC for 30 minutes under magnetic stirring in inert atmosphere (N2). In the copolymers, the ratio between the divinylbenzene (DVB) and the comonomer (STY or GMA) was maintained constant at 30:70. This ratio was chosen based on other syntheses carried out previously in other studies. After the pre-polymerization step, the mixture of toluene and heptane (solvent and non-solvent diluents, respectively) was added in a volume equal to that of the mixture of monomers (100% dilution). The aqueous phase was prepared separately, composed of water, suspension agent and sodium chloride (both at 2% by mass of the aqueous phase), so that the volume of that phase was three times the volume of the organic phase. The organic phase was then poured into this aqueous phase under mechanical stirring at temperature of 80 ºC under inert atmosphere (N2) and the mixture was left to stand under these conditions for 24 hours. The resin obtained was washed successively with hot water and ethanol, filtered and dried in a forced-air oven at 60 ºC for a further 24 hours.
2.3 Adsorbent materials synthesis
The resins obtained were modified by incorporation of sulfonic acid groups, according to the method described in the literature [21-24,28], where the dried resin was reacted with concentrated sulfuric acid (98%) for a determined time at 90 ºC. Then the sulfonated resin was washed with abundant deionized water until the residual water was clear. The resin was then purified by washing with water at room temperature and commercial ethanol, and was dried for 24 hours in a forced-air oven at 60 ℃. Table 1 reports the designations of all the synthesized and modified resins used in this study.
2.4 Characterization of materials
The porosity of the unmodified resins was measured by the nitrogen adsorption-desorption technique (Micromeritics ASAP 2020 physisorption analyzer) after pretreatment of the resins in the device at 120 ℃ for 2 hours. The morphology of all the resins (before and after the sulfonation reactions) was observed by optical microscopy (Carl Zeiss Axio Lab microscope) and by Fourier-transform infrared spectrometry (Varian 3100 FTIR spectrometer). All the sulfonated substances were characterized regarding the ion exchange capacity by neutralization volumetry. For this purpose, 1 gram of resin was kept in contact with 50 mL of a standard solution of NaOH 0.1 mol/L for 24 hours. Then 10 mL of the supernatant was titrated with a standard solution of 0.1 mol/L of HCl until endpoint of the phenolphthalein indicator, in 5% ethanol. The difference between the number of mols of NaOH before and after contact with the resin supplied information on the number of sulfonic groups present in the resins.
2.5 Obtaining the analytical curve of the concentration of ammonium ions in water by potentiometry
We initially prepared a stock solution containing 1000 mg/L of NH4 + ions by dissolving 2.971 g of ammonium chloride in 1,000 mL of deionized water. The concentration of 1000 mg / L of the stock solution was chosen in order to avoid relative errors, for example, when weighing the salt containing ammonium ions. Then we produced serial dilutions of 10, 25, 50, 75 and 100 mg/L to plot the analytical curve using data obtained with a potentiometer (Metrohm 781 pH/Ion Meter). Once the maximum disposal limit established by CONAMA is 20 ppm [12], for the adsorption assays, we used water containing 20 mg/L of ammonium ions, also obtained from the stock solution (pH 5). The adsorption experiment aims to reduce the ammonium concentration of the aqueous solution to the level required by the INEA standard (NT 202, R-10) [20,24,25].
2.6 Batch tests of ammonium adsorption
To conduct the batch tests of ammonium adsorption for each of the resins, we used five centrifuge tubes, respectively containing 0.05 g, 0.1 g, 0.3 g, 0.7 g or 1.0 g of resin followed by 50 mL of the solution containing ammonium ions. The tubes were kept for 5 hours at 25 ºC in a Thermo Haake SWB25 shaker operating at 100 rpm. Tests at higher temperatures were not conducted due to loss of ammonium during the test. Next, 10 mL of the supernatant was collected from each tube and analyzed with the potentiometer to determine the concentration of ammonium ions in solution with the aid of the analytical curve. The concentration of ammonium ions in equilibrium (q e ), in mg/g of resin, was calculated with Equation (1):
where C0 and Ce are the initial and equilibrium adsorbate concentrations (mg/L); V is the volume of solution (L); and m is the mass of adsorbent (g).
The adsorption equilibrium data were analyzed according to the Langmuir and Freundlich models in their linearized forms.
According to the Langmuir model, the adsorption of a substance is due solely to the formation of a monolayer, where all the adsorption sites are equivalent and the ability of a molecule to be adsorbed in a determined site is independent of the occupation of neighboring sites since no interaction exists among the adsorbed molecules [30-32]. The linearized form of the model is described by Equation (2):
Where: qe is the mass of the adsorbate per mass unit of the absorbent (mg/g); qm indicates the maximum quantity of adsorbate that can be removed from the adsorbent; KL is the Langmuir constant, related to the adsorption enthalpy; and Ce is the concentration of the solute in equilibrium (mg/L).
In turn, the Freundlich model indicates the relationship between the quantity of material adsorbed and the concentration of the material in the solution, where the adsorption of the solute increases exponentially with the increase of the concentration [31,32]. The Freundlich isotherm is often used to explain the adsorption equilibrium in heterogeneous adsorption systems. It is defined in its linearized form by Equation (3):
Where: qe is the mass of adsorbate per unit of mass of the adsorbent (mg/g); K and n are the Freundlich constants, the first related to the relative capacity of the adsorbent (mg/g) and the second related to the intensity of the adsorption process (dimensionless); and Ce is the concentration of the solute in equilibrium (mg/L).
3. Results and discussion
3.1 Synthesis, chemical modification and characterization of resins
3.1.1 Optical microscopy
The optical micrographs of Fig. 1 show the spherical morphology of the polymeric resins DVB(7:3), GMA-DVB(7:3) and STY-DVB(7:3) before submission to the sulfonation reaction. The milky appearance of the beads suggests porosity.
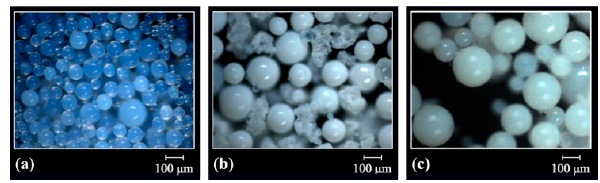
Source: The authors
Figure 1 Optical micrographs of the resins (a) DVB(7:3), (b) GMA-DVB (7:3) and (c) STY-DVB(7:3).
In turn, the resins GMA-DVB(6:4) and GMA-DVB(8:2) (Fig. 2) have distinct morphologies in function of the ratio of diluents used during their synthesis. The beads of GMA-DVB(6:4) have a less milky appearance than those of GMA-DVB(7:3), indicating, in a qualitative aspect, smaller pores, resulting from the lower concentration of heptane in the mixture of diluents. This is coherent with the fact that heptane is a non-solvent diluent. On the other hand, a greater concentration of heptane was used to synthesize the resin GMA-DVB(8:2), seeking to obtain material with a larger number of pores, but the micrographs indicate that well-defined spheres were not always obtained, with part of the sample being in powder form [20].
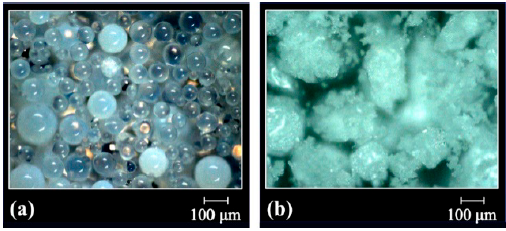
Source: The authors.
Figure 2 Optical micrographs of the resins based on glycidyl methacrylate: (a) GMA-DVB(6:4) and (b) GMA-DVB(8:2).
The morphology of the resins modified by direct sulfonation reaction with sulfuric acid was examined again because of the drastic conditions to which the beads were submitted (concentrated acid medium and heating). Figs. 3, 4 and 5 present the optical micrographs of the resins based on DVB, STY-DVB and GMA-DVB, respectively. The yellowish appearance is characteristic of sulfonated material [21,28]. The resins, which originally had spherical shape, maintained the same morphology, indicating that despite the drastic conditions used in the sulfonation reactions, there was no impairment of this characteristic.
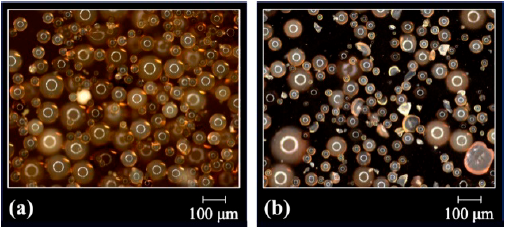
Source: The authors.
Figure 3 Optical micrographs of the resins (a) DVB(7:3)(2)S and (b) DVB(7:3)(24)S obtained by direct sulfonation with sulfuric acid.
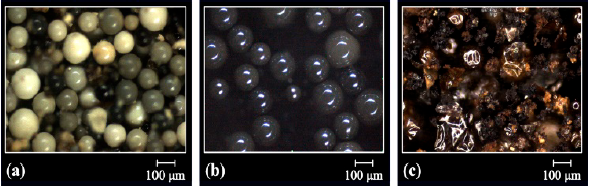
Source: The authors.
Figure 4 Optical micrographs of the resins (a) GMA-DVB(7:3)(2)S, (b) GMA-DVB(6:4)(2)S and (c) GMA-DVB(8:2)(2)S obtained by direct sulfonation with sulfuric acid.
3.1.2 Porosity
All the base resins were analyzed regarding porosity. The results of surface area, pore volume and pore diameter are presented in Table 2.
Table 2 Data on porosity of the polymeric resins before and after the chemical modification reaction.
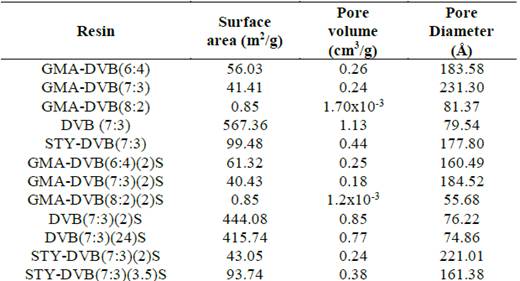
Source: The autors.
To synthesize the GMA-DVB resins, we used a mixture of heptane and toluene as diluent, where heptane acted as non-solvent diluent (porogenic agent) and toluene as a solvent diluent (non-porogenic). We expected the porosity to increase with rising content of heptane in the mixture [24]. We varied the HEP:TOL ratios with the aim of obtaining samples with varied porosities. However, there was no significant variation in the porosity of the resins obtained with 6:4 and 7:3 HEP:TOL ratios. The resin obtained with HEP:TOL ratio of 8:2 had very low surface area, despite the greater content of the porogenic agent (HEP) used in relation to the other two resins. This result can be explained because the porosity was so high that the structure was fragile and brittle, with irregular morphology and powdery appearance, as observed by optical microscopy. As expected [33], for a single type of resin, smaller average pore diameter was associated with greater surface area, with the exception of the resin that lost its spherical shape and exhibited a powdery appearance.
In general, the sulfonation reactions did not cause a significant variation of the surface area. However, for some samples, in particular DVB(7:3)(24)S and STY-DVB(7:3)(2)S, the area decreased after the sulfonation reaction, which can be attributed to the insertion of voluminous groups in a cohesive and highly crosslinked structure.
3.1.3 Infrared spectroscopy
The infrared spectra were obtained to investigate the effects of the sulfonation reactions of the resins GMA-DVB (7:3), DVB(7:3) and STY-DVB(7:3). The appearance or modification of bands in the spectrum of the base resin indicates structural alteration due to the chemical modification. Since the objective of the infrared analysis was only to verify the occurrence of a sulfonation reaction, we expected identical results for these resins as for the other materials with the same composition. This expectation was borne out because the coloration observed through optical microscopy corroborated the previous results.
Fig. 6 presents the spectra of the resins based on glycidyl methacrylate (GMA). The increased intensity and widening of the band at 3450 cm-1 can be attributed to the elongation of the O-H bond. The appearance of this band can be the result both of the opening of the epoxide ring during the sulfonation reaction and the presence of hydroxyl in the sulfonic acid group. The bands at 811 and 910 cm-1 are associated with the symmetric and asymmetric deformation of the epoxide ring. It can be noted, albeit with some difficulty, that these bands were preserved in the spectrum after sulfonation, despite the intense overlap of other bands.
The spectrum of the resins based on styrene and divinylbenzene (Fig. 7), basically composed of aromatic rings, had the same shape as the spectrum of the resin based on GMA, with the presence of an intense band at around 3450 cm-1, attributed to the hydroxyl groups present in the sulfonic acid. It is also possible to observe two sets of bands, one at 1130, 1170 and 1230 cm-1 and the other at 1037 and 1010 cm-1, attributed to the sulfonic group. The first set, with three bands, refers to the symmetric axial deformation of the S(=O)2 group, while the set with two bands corresponds to the asymmetric axial deformation of this group [34,35].
3.1.4 Cation exchange capacity
One of the ways to measure the number of sulfonic groups incorporated by a modification reaction is by measuring the cation exchange capacity via neutralization volumetry [33]. Table 3 presents the results for the sulfonated resins.
The resin DVB(7:3)(2)S incorporated fewer sulfonic groups than the STY-DVB(7:3)(2)S during reaction time of two hours, and only reached similar exchange capacity after reaction of (DVB(7:3)(24)S) for 24 hours. The structure of the chains can explain this difference. DVB is more crosslinked, and according to the porosity data, it had smaller average pore diameter, so it took longer for the sulfonation agent to diffuse inside these pores and cause the reaction. Another explanation for the longer reaction time is related to the steric hindrance of the aromatic rings of the DVB, where all of them are disubstituted, in contrast to the monosubstituted rings of the styrene portion of the STY-DVB resin. The structure of DVB is more rigid and cohesive, requiring distinct sulfonation times to obtain equivalent exchange capacities. Fig. 8 depicts the structure of a STY-DVB resin, where the monosubstituted aromatic ring can be observed. DVB is composed of only the first mer, i.e., it has disubstituted rings and a chain with strong crosslinking degree.
This relationship between the structure and sulfonation capacity can be better noted in GMA-DVB, which has a surface area only one-tenth that of DVB, i.e., 56.03 m2/g of the former versus 567.36 m2/g of the latter (Table 2). Considering that both resins were submitted to the same sulfonation reaction time (2 hours) and obtained ion exchange values on the order of 2.75 mmol/g (Table 3), it is possible to propose that the efficiency of the sulfonation reaction is more closely related to the resin’s structure than the surface area.
3.2 Batch adsorption tests
The unsulfonated resin GMA-DVB(7:3) was evaluated in terms of efficiency of ammonium ions adsorption (Fig. 9) and did not observe good performance, confirming the need for anionic groups in the resin’s structure to promote interaction with the ions in solution. For this reason, we did not analyze the efficiency of adsorption of ammonium ions for the other unmodified resins.
Beside this, the adsorption tests were not performed for GMA-DVB(8:3)S resin due to the structural damage and its low surface area (0.85 m2/g).
We evaluated the efficiency of the sulfonated resins in terms of the influence of the resin composition, surface area, pore diameter and ion exchange capacity. The tests were conducted at room temperature (25 ºC). The results of the efficiency of ammonium ions adsorption of all the resins tested are presented in Fig. 9. The relative error of each test was set at 5%. The resins based on DVB presented the best results, with 95% and 93% adsorption efficiency levels for DVB(7:3)(2)S and DVB(7:3)(24)S, respectively (resin mass = 1 g). The results obtained for these two resins suggest that the efficiency, in this case, was more closely related to the resins’ surface areas (Table 2) than their ion exchange capacities (Table 3), not only when comparing these two resins with each other, but also when comparing them with the other resins.
Based on the results presented in Fig. 9, it was possible to estimate the quantity of solute adsorbed by the mass of resin through Equation (1). The data are plotted in graphs of qe in function of Ce.
For the sulfonated DVB resins, the adsorption isotherm graph in Fig. 10 again shows that DVB(7:3)(2)S had better adsorption capacity than DVB(7:3)(24)S, since its ion exchange capacity was greater (as reported in Table 3). With respect to the porosity of these two resins, the surface area values were very close (444 and 415 m2/g), suggesting that for this resin, the adsorption capacity is directly related to its surface area.
Comparison of the three curves of the resins based on GMA (Fig. 11) showed that the unmodified resin had very low adsorption capacity values. This was expected, due to the shortage of sites able to interact favorably with the contaminant. In turn, for the sulfonated resins, in the comparison between GMA-DVB(7:3)(2)S and GMA-DVB(6:4)(2)S, the first presented better adsorption capacity. Despite the greater exchange capacity and surface area of GMA-DVB(6:4)(2)S, its adsorption capacity was lower. This effect can be attributed not to the surface area, but instead to the dimensions of the pores. GMA-DVB(7:3)(2)S presented larger pore diameter (184.52 Å), permitting better diffusion of the solution with contaminants into the pores, favoring adsorption.
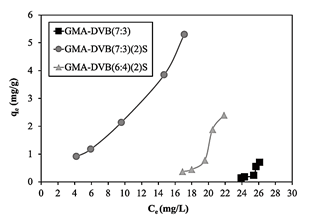
Source: The authors.
Figure 11 Adsorption isotherms of GMA-DVB(7:3), GMA-DVB(7:3)(2)S and GMA-DVB(6:4)(2)S.
The same behavior was observed for the STY-DVB(7:3)(2)S and STY-DVB(7:3)(3.5)S, as shown in Fig. 12, where the first resin had lower ion exchange capacity and larger pore diameter. Although STY-DVB(3.5)S had considerably larger surface area than STY-DVB (2)S, the latter’s pore diameter was substantially greater, favoring the diffusion of the solution with the contaminant and consequently the adsorption capacity.
Fig. 13 presents the graphs of qe versus Ce of the three resins obtained under the same conditions of diluent ratio and sulfonation time. As can be seen in Table 3, the exchange capacities of DVB(7:3)(2)S, GMA-DVB(7:3)(2)S and STY-DVB(7:3)(2)S were 2.70 mmol/g, 2.75 mmol/g and 3.35 mmol/g, respectively, while their surface areas were, in the same order, 444.08 m2/g, 40.43 m2/g and 43.05 m2/g. Fig. 13 shows that DVB(7:3)(2)S had the highest adsorption capacity. Although this resin had similar ion exchange capacity as the resin based on GMA, its surface area was much greater, allowing greater contact with the contaminant and the resin’s surface, modified with sulfonic groups, able to interact better with the contaminant.
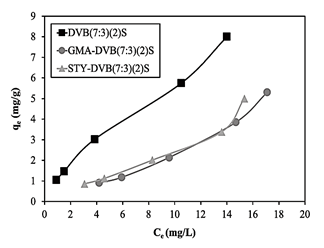
Source: The authors.
Figure 13 Adsorption isotherms of DVB (7:3)(2)S, GMA-DVB(7:3)(2)S and STY-DVB(7:3)(2)S.
On the other hand, the adsorption capacities of the resins based on STY and GMA were very close, but much lower than that of DVB. The former two resins had similar surface areas but different exchange capacities: 3.35 mmol/g for STY-DVB(7:3)(2)S and 2.75 mmol/g for GMA-DVB(7:3)(2)S. Therefore, the resin containing STY, due to the greater number of regions for insertion of sulfonic groups (aromatic rings) than the resin containing GMA, had better absorption of ammonium ions.
Another important aspect is the fact that the resins and respective masses used for treatment of water containing ammonium for compliance with the standard INEA NT 202. R-10 (concentration ( 5 mg/L of ammonium present) would be in the following order: (i) DVB(7:3)(2)S using mass of 0.3 g; (ii) DVB(7:3)(2)S using mass of 0.7 g; (iii) STY(7:3)(2)S using mass of 0.7 g; and (iv) GMA-DVB(7:3)(2)S using mass of 1.0 g.The adsorption equilibrium data were analyzed by employing the linearized forms of the Langmuir and
Freundlich models. The results are reported in Table 4. According to the Langmuir model (Equation 2), all the resins presented good correlation coefficients. However, with the exception of DVB(7:3)(2)S, DVB(7:3)(24)S and STY-DVB(7:3)(2)S, all the other resins had negative values of the parameters k and qmax, confirming that the Langmuir model did not represent the systems studied well.
According to the Freundlich model, the sulfonated resins showed correlation coefficients near 1, indicating that the data obtained can be well represented by this model. Of the parameters determined, n is related to the interaction between adsorbent and adsorbate. Since the values were below 1, except for DVB(7:3)(2)S, DVB(7:3)(24)S and STY-DVB(7:3)(2)S, it can be said that the interactions between resin and ammonium were weak for all the systems. The strongest interactions were achieved by the resins based on DVB. This can represent an economic drawback considering the possibility of regeneration for reuse in more than one water treatment cycle. The parameter k is related to the adsorption capacity, and indicated that the resin without chemical modification had low adsorption capacity, while once again, the resin based on DVB performed the best.
4. Conclusions
The sulfonated polymeric resins obtained were efficient in removing ammonium from wastewater, using the batch process. The resins DVB(7:3)(2)S, DVB(7:3)(2)S, DVB(7:3)(24)S, STY(7:3)(2)S and GMA-DVB(7:3)(2)S managed to reduce the ammonium concentration below the threshold allowed by the relevant technical standard [12] (<5 mg/L) for polishing water previously treated containing 20 mg/L of ammonium. The substances tested presented the following order regarding ammonium removal efficiency: DVB(7:3)(2)S, DVB(7:3)(24)S, STY(7:3)(2)S, GMA-DVB(7:3)(2)S, STY(7:3)(3.5)S, GMA-DVB(6:4)(2)S and GMA-DVB(7:3). Therefore, it was possible to attribute the ammonium adsorption capacity not only to the ion exchange capacity, but also to the surface area and pore diameter.
The data from all the sulfonated resins obtained fit the Freundlich isotherm model better than the Langmuir model, as indicated by the graphs of qe (concentration of solute adsorbed per mass unit) versus Ce (concentration of solute adsorbed in equilibrium in mass per unit of volume). Furthermore, the values obtained for k and qmax by means of the Langmuir model were negative, indicating that this model did not well represent the experimental data. With regard to the Freundlich model, the parameters k and n indicated that: (i) the resins DVB(7:3)(2)S, DVB(7:3)(2)S, DVB(7:3)(24)S, STY(7:3)(2)S and GMA-DVB(7:3)(2)S had the highest adsorption capacities; and (ii) the resins based on DVB had stronger interaction with ammonium, which can hamper the regeneration process of this resin. In general, this kind of material could be used in several cycles saturation-regeneration-resaturation without significant efficiency loss. However, this is an aspect that needs to be carefully evaluated from an economic perspective for use of these resins to treat water containing ammonium ions. Thereby, its industrial application becomes both economic and environmentally viable.