1. Introduction
Organic deposits such as asphaltenes can cause several problems in the production and processing of oil. During the oil production, asphaltenes can precipitate in the reservoir, pipes, pumps, and storage tanks, for example. They also contribute to the stabilization of the water-in-oil (w/o) emulsions produced by shearing imposed during lifting. The crude oil containing emulsified water presents high viscosity, hindering the flow. Besides, the presence of water can cause corrosion in the transportation pipes. Therefore, phase separation must be executed when the fluids achieve the surface. The crude oil demulsification process requires specific equipment and additives. Incompatibility of oils coming from different reservoirs, which can provoke asphaltene precipitation [1-3] in separators reducing its performance.
Asphaltenes are soluble in aromatics compounds (for example, toluene and benzene) and insoluble in short n-alkanes (for example, pentane, hexane and heptane). Its chemical composition, structure, molecular weight and content depend on each oil. Asphaltenes consist of molecules with one or more aromatic rings, aliphatic chains, heteroatoms like oxygen and sulfur and traces of metal. It contains functional groups, for example, carboxyl, ether, ester, hydroxyl, aldehyde, acetone, amine and amide. Asphaltene phase behavior has been studied by several authors [4-9]. In oil mixtures, the big challenge is to know the reasons that provoke the asphaltenes precipitation and the changes in emulsion stabilization. To understand the asphaltene precipitation is necessary to know the oil composition. The composition is often given by determination of SARA (Saturated, Aromatic, Resin and Asphaltenes). The presence of resins in oil plays an indispensable role in the stabilization of asphaltenic fractions. The resins keep the asphaltenes disperse. Without which, under normal operating conditions, asphaltenes would precipitate. Saturates provoke asphaltene precipitation and aromatics help the asphaltene solubilization [3,10,11]. Instead of oil composition, other factor that affect the stability of asphaltenes and lead to precipitation is the solvent solubility parameter. The greater the difference between the solvent solubility parameter and asphaltene, the greater the asphaltene precipitation. [12,13].
To avoid the asphaltene deposition it is necessary to predict the start and the amount of deposition. Determining the starting point of asphaltene precipitation (also known as the onset point) is a widely used analysis to help with prevention methods [14]. Solubilizing the oil in toluene and adding n-heptane is often used to check the stability and precipitation of asphaltenes. The solubility of asphaltenes is altered by the proportions of heptane and toluene [7,15].
The determination of the solubility parameter leads to the interpretation of oil stability and also of oil compatibility of mixtures. Oil compatibility is widely studied in the petroleum industry because many fields produce oils from different reservoirs. With different compositions, when mixed, is concluded that the solubility parameters are different and therefore asphaltene precipitates. Oils that do not show asphaltene precipitation under pressure, temperature and composition conditions are classified as stable; when this precipitation occurs, they are considered unstable. Oils are considered compatible when during their mixture there is no precipitation, otherwise they are considered incompatible. [12,13,16]. Incompatibility between oils can cause emulsion stabilization. There are studies that show that asphaltenes as well as resins are natural oil emulsifiers because they act at the water-oil interface, stabilizing the emulsion and can be considered a surfactant [14,17,18].
A qualitative test widely used to check oil stability and compatibility of oil mixtures is the Spot Test [19,20]. The oil contained in its paper must be qualitatively evaluated for any evidence of precipitation. If the spot is homogeneous without a ring in the center, the oil is considered stable. Likewise, the mixture is considered compatible. And if the spot shows a ring in the center, the oil is considered unstable. If it is a mixture of oils it is considered incompatible. There are many indexes that are studied by several authors to verify the stability of asphaltenes by analyzing the composition of the oil [3], some of them are the resin/asphaltene (R/ASP) ratio, colloidal instability index (CII), Stankiewicz graph, Gaestel Index (Ic). Usually, the interpretation of these indexes requires additional experimental analysis or field data to be conclusive. The present work studied these indexes, spot test, asphaltenes precipitation onset and emulsion stability to verify the influence of asphaltenes precipitation on emulsion stability.
This study is aimed at presenting a relevant contribution to industrial and academic sector. Offshore process units in petroleum companies receive oils from different reservoirs, the reason why many different combinations of reservoir fluids can occur. As mentioned before, oil incompatibility can provoke the precipitation of asphaltenes in separation equipment and hinder its performance [13]. However, the association of such precipitation to emulsion stability it is still a matter of research. Therefore, a systematic study must be done, to evaluate the kinetics of emulsion separation and correlate it to the residence time in the process units and electrostatic treater. Using oil composition to correlate oil incompatibility with emulsion separation kinetics is a new contribution to thermodynamic models that attempt to predict precipitation and aggregation of asphaltenes in industrial units [5].
2. Materials and methods
2.1. Chemicals
The oils called A, B e C, and their respective SARA values (Table 1), were provided by Rio Petroleo, Rio de Janeiro, Brazil, a Brazilian engineering company specialized in services for oil producing operators. The oils come from an offshore production platform. They were collected from the riser before the treatment station and were received hydrated.
Table 1 SARA values for crude oil samples A, B and C
Sample | Oil Composition (%m/m) | |||
---|---|---|---|---|
S | AR | R | ASP | |
A | 32.80 | 45.67 | 17.66 | 3.87 |
B | 33.70 | 47.83 | 16.36 | 2.11 |
C | 59.87 | 30.57 | 9.35 | 0.21 |
ABC* | 42.12 | 41.35 | 14.45 | 2.06 |
* 1:1:1 v:v:v%. Calculated values by arithmetic average.
Source: own authorship.
Sodium chloride PA, calcium chloride PA and n-heptane 99.5% were supplied by Isofar Prod. Quim., Duque de Caxias. Karl Fischer reagent was supplied by Carvalhaes Prod. Lab., Campo Limpo Paulista. Milli-Q water was used to prepare synthetic emulsions. A commercial demulsifier was donated by Petrobras.2.2 Methods
2.1.1. Correlation of oil composition (SARA) to evaluate asphaltene instability
Colloidal instability index (CII) and Gaestel Index (Ic) were determined by eqs. (1)-(2), respectively. Resins/asphaltenes ratio (R/ASP), and Stankiewicz graph, that plots the Saturated/Aromatic versus Asphaltenes/Resins ratios, were also calculated and analyzed.
2.1.2. Spot Test to check the stability and compatibility of the oils
To check the oil stability by Spot Test, 0.2 g of oil was added to 5 mL of n-heptane and left to rest for a few hours. An aliquot of each oil immersed in n-heptane was filtered and the stain was observed. The test was carried out for the three crude oils under study, A, B, and C. To check the compatibility of the oils, the same procedure was adopted, with 0.2 g of the mixtures of the oils (A + B, A + C, B + C, at 1:1 m:m, and A + B + C, at 1:1:1 m:m:m) in 5 mL of heptane.
2.1.3. Dehydration of oils
The oils were dehydrated by homogenizing and heating in a water bath at 60 °C for 30 minutes. Then approximately 400 ppm of demulsifier were added to the crude oil, homogenized, and kept at 60 ºC for one more hour. The oils were left to rest for a week to further remove water. These oils will be called herein as dehydrated oils A, B and C.
2.1.4. Water content by Karl Fischer
The water contents of the hydrated and dehydrated oils were determined by titling with Karl Fischer reagent. The oil sample was weighed and homogenized with the reagent. The measures were done in triplicate.
2.1.5. Synthetic emulsion preparation
A saline water (NaCl:CaCl2 10:1) at 55000 mg/L was prepared to incorporate into the oil and prepare the synthetic emulsions. Water in oil emulsions (20:80 v:v) were prepared using Ultra Turrax IKA T25 at 8000 rpm for 4 minutes.
2.1.6. Emulsion separation kinetics by bottle test
The emulsion stability was performed for the hydrated oils and the synthetic emulsions prepared with dehydrated oils. The emulsions were placed in the graduated conical flasks and heated for 30 minutes. After this time, the demulsifier was added shaking the flasks manually for one minute and the test was performed at 60 °C for one hour, measuring the volume of separated water at every 5 min. The test was carried out for the three crude oils under study, A, B, C and mixtures of theses oils (A + B, A + C, B + C, at 1:1 m:m, and A + B + C, at 1:1:1 m:m:m). The results were obtained for the emulsions without and with adding 200 ppm of demulsifier. The stability tests of the emulsions containing demulsifier were done in duplicate and compared with the emulsion without demulsifier.
3. Results and discussion
3.1. Correlation of the oil composition (SARA) to evaluate instability
Indexes CII (colloidal instability index), resins/asphaltenes ratio (R/ASP), Ic (Gaestel Index) were calculated (Table 2) from the SARA analysis. Stankiewicz graph (Fig. 3) was also determined from the SARA analysis, whose data S/ARxASP/R are also seen on Table 2.
Table 2 Index to verify asphaltene stability.
Sample | Indexes | |||
---|---|---|---|---|
CII (S+ASP/R+AR) | Ic (ASP+R/S+AR) | R/ASP ratio | S/AR x ASP/R | |
A | 0.58 | 0.27 | 4.56 | 0.72 x 0.22 |
B | 0.56 | 0.23 | 7.75 | 0.70 x 0.13 |
C | 1.51 | 0.11 | 44.52 | 1.96 x 0.02 |
AB | 0.57 | 0.25 | 5.69 | 0.71 x 0.18 |
AC | 0.94 | 0.18 | 6.62 | 1.22 x 0.15 |
BC | 0.92 | 0.16 | 11.08 | 1.19 x 0.09 |
ABC | 0.74 | 0.20 | 7.01 | 1.02 x 0.14 |
Source: own authorship.
To assess the stability of asphaltenes of different oils and its mixtures it is not enough to analyze the content of asphaltenes, it is necessary to consider the contents of the other components, especially resins, since they can form a resin-asphaltene complex which can also act strongly at the water-oil interface and stabilize an emulsion. Larger aggregates can precipitate, and Rio Petroleo has reported that these deposits are often found in the equipment of the process plant. We have concluded that the presence of deposited asphaltenes is occurring either due to the instability of the oils but also due to the incompatibility of their mixtures. They can form stable emulsions which can impair the performance of separators and electrostatic treaters.
According to the literature, the CII index is adequate for colloid stability analysis. If the colloid is stable, this probably happens because resins help stabilize it. Maybe this resin-asphaltene complex can act at the water-oil interface and stabilize the emulsion. When the CII index is less than 0.7, it indicates more colloid stability and greater than 0.9 indicates colloid instability. Values between 0.7 and 0.9 indicate uncertainty in stability. As shown in Table 2, the CII found for oils A and B are less than 0.7, within the colloid stability range. C oil has an CII of greater than 0.9 and can be considered an unstable colloid. According to CII index results, oil A and oil B are more likely of stabilize an emulsion while the oil C is less. It is possible noted that the presence of oil C in the mixture with A or B leads to a content greater than 0.9. The mixture with oil C makes it less likely to stabilize an emulsion. The CII of comingled oil is in the margin of uncertainty for colloid stability.
Ashoori et al. [10] studied oils with CII indices similar to oils A and C. The oil with low asphaltene content had a high CII value (1.47), similar to the CII of C oil, and less chance of precipitation, while the oil with high asphaltene content showed a low CII value (0.85), close to the oil A CII and more likely to precipitate.
As to the Gaestel Index (Ic), which verifies the dispersion capacity of maltenes (saturated, aromatic and resins) against asphaltenes, increasing the Ic, the asphaltene can precipitate. The Ic can be seen in Table 2 and in Fig. 1.
As to the resin/asphaltenes ratio (R/ASP), the higher this ratio, the lower the chance of asphaltene precipitating, consequently the lower the R/ASP ratio, the greater the chance of precipitating. The oil C despite having a low resin content (Table 1) which is indicative of precipitation, it has a very high resin/asphaltene ratio (Table 2), that is, very low asphaltene content. The high saturated content in oil C is not sufficient to precipitate asphaltene, perhaps due to the high R/ASP ratio. The resin/asphaltene ratio (R/ASP) can be seen in Table 2 and in Fig. 2.
A Stankiewicz graph (Fig. 3), that plots the Saturated/Aromatic versus Asphaltenes/Resin ratios was done with data from SARA (Table 1). The graph shows the asphaltene stability region (Fig. 3a), assuming that unstable oils are those where asphaltenes grow and can precipitate. And stable oils do not precipitate. The oils A and B are at the

Source: own authorship.
Figure 3 Stankiewicz graph: Saturated/Aromatic (S/Ar) ratio versus Asphaltenes/Resin ratio (ASP/R).
limit of instability. While the oil C is in the stability area. The graph was also plotted for oil mixtures as shown in Fig. 3b. The oil mixtures are on the limit of stability, without much certainty if asphaltene precipitates. The analysis of the Stankiewicz graph confirms the interpretations of the Gaestel index and the resin / asphaltenes ratio.
These indexes show that oil A can precipitate asphaltenes and these asphaltenes can cause an emulsion stabilization.
3.2. Spot Test to check the stability and compatibility of the oils
The Spot Test was performed to check the stain on the filter paper. According to the literature, a stain homogeneous means stable oil when the analysis is do in oil pure or compatible oils when the analysis is do in oil blend. A ring in the center of filter means unstable oil when the analysis is do in oil pure or incompatible oils when the analysis is do in oil blend. The results to the oil A, B, C and their blends AB, AC, BC and ABC can be shown in Fig. 4.
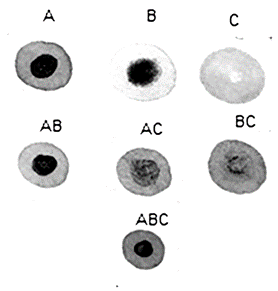
Source: own authorship.
Figure 4 Spot Test for the pure oils (A, B and C) and their mixtures (AB, AC, BC and ABC).
Analyzing the stains, we can say that oil A and B are unstable, they presented a dark stain in the center possibly due to asphaltene precipitation. Oil C is stable because the stain is homogeneous. In the mixture of oils, we can say that AB and AC are incompatible, and BC is almost compatible. ABC is incompatible. Mixtures with oil A, which is the most unstable, tend to be incompatible. And the mixtures with oil C, which is stable, tend to be compatible. The results of the spot test were more conclusive than those of the Stankiewicz graph, which presented uncertainty regarding the asphaltene precipitation.
Dehydration of oils and verification of water content by Karl Fischer titration before and after dehydrating
The dehydration of the oils is important since this allows the preparation of synthetic emulsions containing different brine contents and understand the phase behavior of the w/o emulsions in function of their compositions.
The Karl Fischer results show high amount of water in oils A and B (respectively, 59.4 and 40.9 %), and very low water content in oil C (1.1 %) (Table 3). These water contents emulsified in the oils agree with the asphaltenes content (Table 1). Oil C, containing a very low asphaltenes content (0.21 %m/m), present a very low amount of water emulsified. On the other hand, oils A and B, containing higher percentage of asphaltenes (respectively, 3.87 and 2.11 %m/m) produced stable emulsions containing higher amounts of water.
Table 3 Water content in the hydrated and dehydrated oils obtained by Karl Fischer titration
Oils | Water content (%m/m) | Oils | Water content (%m/m) | Oils |
---|---|---|---|---|
Hydrated | Hydrated | |||
A | 59.42 | 1.20 | 10.45 | 0.70 |
B | 40.94 | 1.20 | 11.32 | 0.26 |
C | 1.08 | 0.07 | 1.08 | 0.07 |
Source: own authorship
The amount of water in oil C is already very low (1.08 %m/m, Table 3) so that, it was not possible to separate or visualize the separation of this water content. Therefore, the curve related to oil C matches the x axis.
After the procedure to dehydrate the oils, the percentages of water phase in the oils A, B were reduced to 10.4 and 11.3 %m/m, respectively. The optimum concentration of the demulsifier required to achieve these water contents was 400 ppm, since by using 600 ppm the results was very similar. Such water content will be taken in account when preparing the synthetic emulsions using brine as aqueous phase.
3.4. Emulsion separation kinetics of the hydrated oils and the synthetic emulsions prepared with dehydrated oil and brine
3.4.1. Hydrated oils
The emulsion stability of the hydrated oils was accompanied by bottle test. The volume of separated water without adding demulsifier was equal or very close to zero mL for all oils samples and their mixtures, evidencing the stability of the emulsions of the oils A and B. The behavior of separated water against time obtained for all oil samples and their mixtures containing 400 ppm of demulsifier is shown in Fig. 5. Table 4 shows the final percentage of separated water in relation to the total amount of water in oil, determined by Karl Fischer Titration (Table 3).

Source: own authorship.
Figure 5 Emulsion stability of the hydrated oils and their mixtures containing 400 ppm of demulsifier, using bottle test at 60 °C.
Table 4 Final percentage of separated water in relation of the total amount of water in oil determined by Karl Fischer Titration (Table 4-3).
Oils samples and their mixtures | Percentage of separated water related to the total content of water in the oil (Table 4 3) (%v/v) | |
---|---|---|
Experimental determined | Theoretical calculated | |
A | 84.99 ± 0.89 | - |
B | 53.74 ± 2.44 | - |
C | 0.00 ± 0.00 | - |
AB | 68.75 ± 0.99 | 69.36 |
AC | 84.30 ± 4.96 | 84.99 |
BC | 57.12 ± 14.28 | 53.74 |
ABC | 65.06 ± 2.96 | 69.36 |
Source: own authorship.
Although oil A presents a larger amount of water than oil B, it is less stable under the demulsification action: at the first 5 minutes oil A separated 85 % of its amount of water, while oil B started the phase separation only after 5 minutes achieving a total amount of separated water of 54 % in relation of its amount of water before the bottle test.
The oscillation in the curve of oil A is a consequence of the difficulty in reading the water-oil interface, due the characteristic of this oil.
When mixing oils A and B (1:1 v:v), the kinetic of phase separation became slower than the pure crude oils, suggesting some kind of interaction or interference from each other. The influence of oil B on oil A provoked a less oscillation in the readings. However, the final percentage of separated water was almost the same as the expected theoretical value for an average behavior.
When mixing oil A and C (1:1 v:v), it is possible to notice that oil C did not interfere on oil A. The phase separation started in the first 5 minutes, and the same percentage of water separated at the end of the test, related to oil A, was observed (~85 %).
On the other hand, the addition of oil C in oil B, provoked a higher instability when comparing with pure oil B, since the phase separation started in the first 5 minutes. As observed for oil A, the percentage of water separated was similar as that for pure oil B. Nevertheless, the visualization of phase separation was affected, becoming more difficulty, as we can see in the standard deviation of the result. It means that somehow oils B and C affect their behavior when comparing to the pure oils. In fact, the standard deviation of the mixtures increases when adding oil C.
The mixture of the three different oils presents a mixture of the behaviors observed for the binary mixtures, prevailing the stability in the first 5 minutes, observed for oil B and its mixture with oil A, and the percentage of separated water was lower than that expected for an average of theoretical value do not considering any interference from each other.
3.4.2. Dehydrated oils
In order to compare the oils under the same emulsification conditions, the dehydrated samples were used to prepare synthetic emulsions at the 20/80 %v:v (w/o), using brine at 55000 ppm of salts (NaCl: CaCl2 10:1) as aqueous phase.
Fig. 6 shows the separated water volume as a function of time for the emulsions prepared with oils A, B and C and their binary and ternary mixtures, after adding 400 ppm of demulsifier. The emulsions prepared with oils A and B and its binary mixture are more stable than the mixtures containing oil C, for the same reason discussed above.
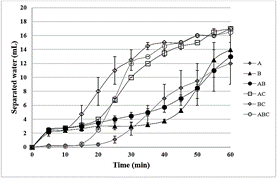
Source: own authorship.
Figure 6 Stability (bottle test at 60 °C) of the synthetic emulsions of the pure crude oils and their mixtures, after adding 400 ppm of demulsifier. Emulsions prepared using the dehydrated oils and brine as aqueous phase.
Table 5 shows the final percentage of separated water in relation to the total amount used to prepare the emulsion, without (blank) and with the addition of 400 ppm of demulsifier. The stability result for the emulsion prepared with oil C is not in Fig. 6 nor Table 5 because it was very unstable, exhibiting total water phase separation just under heating (60 °C). This behavior can be, probably, related to the low asphaltenes content in oil C, making it difficult to stabilize of the synthetic emulsion. In fact, as discussed previously, oil C presented very low content of water for the same reason.
Table 5 Final percentage of separated water in relation to the total amount of water used to prepare the synthetic emulsions, with and without (blank) adding 400 ppm of demulsifier.
Oils samples and their mixtures | Percentage of separated water related to the total content of water (%v/v) | |
---|---|---|
Without demulsifier | With demulsifier | |
A | 0.8 | 60.0 ± 15.0 |
B | 4.0 | 70.0 ± 10.0 |
AB | 60.0 | 65.0 ± 0.0 |
AC | 85.0 | 85.0 ± 0.0 |
BC | 75.0 | 85.0 ± 0.0 |
ABC | 75.0 | 82.5 ± 2.5 |
Source: own authorship.
Without adding demulsifier, all oils mixtures exhibited high percentage of separated water compared with the emulsions prepared with the pure crude oils (A and B). The emulsions prepared by mixing oils A and C presented the same percentage of separated water without and with the addition of demulsifier, evidencing the high instability of this emulsion. The emulsions prepared with the pure crude oils (A and B) were stable without the demulsifier, and only 60 % and 70 % of water was separated by the addition of 400 ppm of demulsifier. As discussed before, these emulsions with pure crude oil separated a lower percentage of water, by adding demulsifier, than those prepared with the mixture of oils containing oil C.
By comparing the kinetic of phase separation (Fig. 6) with the spot test results (Fig. 4), slower kinetics is observed for oil A and ABC mixture which presents lower asphaltenes stability and lower compatibility, respectively. On the other hand, mixture BC presents a faster kinetic and the highest compatibility among the other mixtures. It can be suggested that the tendency to asphaltenes precipitation can contribute to decrease the water-oil phase separation kinetic.
The interpretation of the results agrees with the results found in the literature. Suilamon et al. [3] worked with some oils with characteristics similar to oils A and C. An oil with 0.6% of asphaltene, close to the content of oil C, presented a high R/ASP ratio, without precipitated asphaltene. They also worked with another oil with 3.85% asphaltene and a low R/ASP ratio, similar to oil A, which can precipitate asphaltene. Guzman et al. [19] also worked with R/ASP ratio oils similar to A and C oils and correlated with the Spot Test results. The oil with an R/ASP ratio of 40 (close to the C oil value) was an oil with a homogeneous stain. And another oil with an R/ASP ratio of 4.6 (close to the value of oil A), was an oil with a stain in the center. We can verify that the ratio R/Asf is also an indication of the kinetics. Oil C and mixture BC had higher R/ASP ratio and had faster water separation kinetics. As well as oil A, which presented the lowest R/ASP ratio, it also presented a slower kinetics. Although the AC mixture has a lower R/ASP ratio than the ABC mixture, the ABC mixture had slower kinetics, which suggests that the greater incompatibility of the ABC mixture led to this result.
4. Conclusions
The calculated values of R/ASP for oils A, B and C were 4.56, 7.75 and 44.52, respectively and the water content in the hydrated oils were almost 60, 40 and 1 %m:m. A good correlation between the resins/asphaltenes ratio (R/ASP) and the water content in the oil was confirmed, that is, higher R/ASP ratios are related to more unstable oils with lower water contents. Spot test analyzes proved to be more conclusive for evaluating the stability of asphaltenes and oil compatibility than the Stankiewicz graph. The stabilities of the emulsions were A > B > C and has a good correlation with the asphaltenes contents in the oils A, B and C (3.87, 2.11 and 0.21 %m:m, respectively). From synthetic emulsions containing the same w/o ratio, obtained from the dehydrated oils, it was possible to suggest a correlation between the stability of asphaltenes/oil blends compatibilities and the w/o phase separation kinetics in the bottle test: Kinetics is faster for the samples most compatible (BC). And slower kinetics is observed for oil A and the ABC mixture which present lower asphaltenes stability and lower compatibility, respectively. Despite the relevant contribution given by this work, further studies are required because the several differences among the crude oils produced by the petroleum industries and their combinations.