Nomenclatura
A a | Área activa sobre la bandeja | m2 |
A d | Área del tubo de b/ajada | m2 |
A h | Área total del hoyo | m2 |
A NH3 | Amoníaco absorbido | kg/s |
A t | Área total de sección transversal | m2 |
|
Parámetro | - |
|
Relación del área del hoyo de vapor con el área activa de la bandeja | - |
C | Constante empírica | m/s |
C F | Factor | m/s |
C G | Densidad molar de la mezcla gaseosa | kmol/m3 |
C l | Parámetro | - |
C L | Densidad molar del líquido | kmol/m3 |
C o | Coeficiente del orificio | - |
d 0 | Diámetro de perforación en la bandeja perforada | cm |
D | Diámetro de la torre | m |
D E,G | Difusividad de remolino del gas | m2/s |
D E,L | Difusividad de remolino del líquido | m2/s |
DG | Difusividad de la mezcla gaseosa | cm2/s |
D L | Difusividad del agua | cm2/s |
E | Arrastre fraccional | - |
E MG | Eficiencia de la bandeja de Murphree | - |
E MGE | Eficiencia de la bandeja de Murphree corregida por arrastre | - |
E OG | Eficiencia puntual de la bandeja perforada | - |
f | Acercamiento fraccional a la inundación | - |
F F | Factor de formación de espuma | - |
F HA | Parámetro | - |
F ST | Factor de tensión superficial | - |
Fr o | Número de Froude del orificio | - |
g | Aceleración debida a la gravedad | m/s2 |
h d | Pérdida de carga de la bandeja seca | cm |
h l | Carga equivalente del líquido claro en la bandeja | cm |
h t | Pérdida total de carga por bandeja | cm |
h w | Altura del vertedero | cm |
h σ | Pérdida de carga debido a la tensión superficial | cm |
h 2ϕ | Altura de la región bifásica en la bandeja | m |
K s | Parámetro de capacidad | m/s |
l | Espesor de la bandeja | cm |
L | Caudal másico del líquido | kg/s |
L' | Caudal másico del líquido a la salida del absorbedor | kg/s |
L e | Caudal másico de arrastre | kg/s |
L w | Longitud del vertedero | m |
m | Pendiente de la curva de equilibrio | - |
M | Peso molecular | kg/kmol |
N | Parámetro | - |
p' | Paso | cm |
P e | Número de Peclet | - |
P G | Presión en el fondo de la torre | kPa |
ΔP G | Caída de presión del gas por bandeja | kPa |
q L | Caudal de líquido a través de la bandeja | m3/s |
Q | Caudal volumétrico | m3/s |
rw | Distancia desde el centro de la bandeja hasta el vertedero | m |
R | Constante del gas ideal | J/mol.K |
R NH3 | Porciento de remoción del amoníaco | - |
ReF e | Número de Reynolds fraccional | - |
t | Espaciado de la bandeja | cm |
T G | Temperatura en el fondo de la torre | K |
v a | Velocidad superficial del gas basada en el área activa de la bandeja | m/s |
v GF | Velocidad superficial del gas | m/s |
v o | Velocidad del hoyo | m/s |
V | Caudal másico del gas | - |
V m | Caudal molar de la mezcla gaseosa | kmol/s |
X | Parámetro | - |
y | Fracción molar | - |
Símbolos griegos
α | Parámetro | - |
β | Parámetro | - |
λ | Parámetro | - |
ρ | Densidad | kg/m3 |
μ | Viscosidad | Pa.s |
ϕe | Densidad relativa efectiva de la espuma | - |
σ | Tensión superficial | dyn/cm |
θ | Ángulo del tubo de bajada | rad |
k | Constante | - |
Introducción
El proceso de transferir un material desde una fase gaseosa hacia una fase líquida se denomina absorción. El dispositivo en el cual el proceso de absorción tiene lugar se denomina torre de absorción, columna de absorción o absorbedor. Las torres se clasifican de acuerdo a la función realizada (destilación, separación o extracción) y también mediante el tipo de dispositivo instalado en su interior para que la torre pueda efectuar la operación deseada. Los dispositivos internos de la torre pueden ser bandejas o empaques [1].
En la absorción (también llamada absorción gaseosa o lavado de gas) una mezcla gaseosa es puesta en contacto con un líquido (el absorbente o solvente) con el objetivo de disolver selectivamente uno o más componentes a partir de su transferencia desde el gas hacia el líquido. Los componentes transferidos hacia el líquido se denominan solutos. La operación de absorción puede categorizarse sobre la base de la naturaleza de la interacción entre el absorbente y el soluto dentro de los siguientes tres tipos generales: (1) absorción física; (2) reacción reversible; y (3) reacción irreversible.
En el caso de la absorción física, el componente que está siendo absorbido es más soluble en el líquido absorbente que en los demás gases en los cuales está mezclado, pero no reacciona químicamente con éste. Como resultado, la concentración de equilibrio en la fase líquida es principalmente una función de la presión parcial en la fase gaseosa y la temperatura [2].
Generalmente el propósito comercial de los procesos de absorción puede ser dividido en purificación de gas o recuperación de producto, en dependencia de si la porción absorbida o no absorbida del gas de alimentación tiene el mayor valor. Entre las aplicaciones típicas de la absorción para la purificación del gas se tienen la remoción de amoníaco utilizando agua como absorbente, la absorción de dióxido de carbono y sulfuro de hidrógeno usando mono- y di-etanolamina diluidas en agua, la remoción de cloruro de hidrógeno utilizando agua y la remoción de tolueno usando tolueno como absorbente. Por su parte, entre las aplicaciones típicas de la absorción para la recuperación de producto se pueden mencionar la absorción de acetileno usando dimetilformamida, la absorción de urea mediante una solución de carbamato de amonio, así como también la absorción de acrilonitrilo, anhídrido maleico, ácido nítrico y ácido sulfúrico usando agua como material absorbente [2]. Todas estas operaciones están siendo constantemente mejoradas mediante el desarrollo de nuevos solventes, configuraciones de proceso y técnicas de diseño.
El principio clave de los diferentes absorbedores industriales es el de asegurar una elevada área de transferencia de masa gas-líquido, y crear condiciones tales que se logre una alta intensidad de transferencia de masa. Aunque los procesos a pequeña escala utilizan la operación en forma de lotes (batch) donde el líquido es ubicado en el equipo y solamente fluye el gas, el método continuo de absorción se aplica usualmente en procesos industriales a gran escala. Existen varios criterios para clasificar absorbedores, siendo el más utilizado el que toma en cuenta cuál de las fases (gas o líquido) está en forma continua o dispersa. Usando este criterio, los absorbedores pueden clasificarse en los siguientes grupos [3]:
Absorbedores en donde ambas fases son continuas (columnas empacadas).
Absorbedores con una fase gaseosa dispersa y una fase líquida continua (columnas de bandejas, columnas de burbujeo y columnas de burbujeo empacadas).
Absorbedores con una fase líquida dispersa y una fase gaseosa continua (columnas de aspersión).
Las torres o columnas de bandejas son cilindros verticales en el cual el líquido y el gas son puestos en contacto entre sí por medio de etapas utilizando bandejas o placas ( Figura 1) [4,5]. El líquido entra por el tope y fluye hacia abajo por medio de la gravedad. En su paso, este fluye a través de cada bandeja y pasa hacia la próxima bandeja inferior mediante el tubo de bajada. El gas transita hacia arriba por medio de las aberturas de un tipo u otro ubicadas en la bandeja, y entonces burbujea a través del líquido para formar una espuma, y a continuación se aleja de esta espuma y pasa hacia la bandeja superior. El efecto total es un contacto múltiple a contracorriente entre el gas y el líquido, en donde cada bandeja está caracterizada por un flujo cruzado de ambos. Cada bandeja de la torre se considera una etapa, debido a que en la bandeja los fluidos se ponen en contacto íntimo, ocurre la difusión entre fases, y luego los fluidos son separados [6].
Las columnas de bandeja son particularmente utilizadas para aplicaciones en grandes instalaciones y con tasas de flujo de líquido de bajas a medianas. En general ofrecen una opción de operación más amplia para los flujos de gas y líquido que las columnas empacadas a contracorriente. Esto es, son capaces de manejar elevados caudales de gas y bajos caudales de líquido lo cual pudiera ocasionar inundación en una columna empacada. Las columnas de bandeja son también preferidas en aplicaciones que tienen grandes efectos térmicos debido a que pueden instalarse serpentines de enfriamiento en éstas, y el líquido puede ser extraído con relativa facilidad de las bandejas para su enfriamiento externo en comparación con los empaques. Además, son ventajosas para efectuar la separación que requieren columnas altas con un elevado número de unidades de transferencia debido a que no están sujetas a la canalización de las corrientes de vapor y líquido, lo cual pudiera ocasionar problemas en columnas empacadas. Las principales desventajas de las columnas de bandejas son su elevado costo de capital, especialmente cuando se emplean bandejas con capuchas de burbujeo o diseños especiales patentados, así como también su sensibilidad a producir espuma [2].
Las bandejas pueden dividirse en dos categorías principales: bandejas de flujo cruzado y bandejas de flujo a contracorriente. Las bandejas de flujo cruzado obtienen su nombre debido a que el líquido flujo a través de la bandeja hacia un ducto de bajada mientras que el vapor sube a través de las perforaciones en la cubierta de la bandeja. Existen cuatro tipos de bandejas de flujo cruzado comúnmente usadas actualmente, las cuales son la bandeja perforada, la bandeja de capucha de burbujeo, la bandeja tipo válvula (flotante) y la bandeja tipo válvula (fija) [7]. En la actualidad se disponen de varios diseños diferentes de bandejas patentados por compañías, que involucran válvulas tanto Ajas como flotantes, cuyos detalles de rendimiento y operación pueden ser obtenidos a partir de catálogos de los fabricantes [7]. En este sentido se pueden mencionar la bandeja activa trapezoide combinada, la bandeja Concap, la bandeja de empaque guiada por el flujo, la bandeja monolítica de espuma SiC y la bandeja perforada de flujo giratorio tridimensional [8].
Las bandejas perforadas han sido utilizadas desde alrededor de cien años y constituye una de las bandejas más estudiadas hasta la actualidad. Pueden ser adaptadas fácilmente a diferentes escenarios de diseño (caudales) usando diferentes perforaciones, no necesitan ninguna herramienta especial en su producción y por tanto son baratas de fabricar [9]. Consisten de una placa perforada a través de la cual el vapor sube desde la bandeja inferior, un vertedero para mantener un nivel de líquido en la bandeja, y un ducto de bajada que actúa para dirigir el líquido hacia la bandeja inferior. La operación de la bandeja perforada depende de que la velocidad del vapor a través de las perforaciones sea lo suficientemente alta para mantener el líquido fluyendo a través de la bandeja, y no hacia abajo mediante las mismas perforaciones por las cuales el vapor sube, fenómeno denominado vertimiento. La desventaja de la bandeja perforada es que tiene un rango de operación estrecho comparado con las de capucha de burbujeo y la de tipo válvula. Una velocidad menor del vapor ocasionará que el líquido caiga a través de los huecos hacia la placa inferior. Una velocidad del vapor muy alta producirá que el vapor no burbujeará a través del líquido en la bandeja. En su lugar, el vapor empuja al líquido lejos del hueco ocasionando que no ocurra un contacto eficiente liquido-vapor [1].
La transferencia de masa en las columnas de bandejas ocurre principalmente en la espuma a medida que el líquido fluye sobre la bandeja y el vapor sube a través de los orificios de esta. El área del límite de fase para la transferencia de masa está disponible debido a las pequeñas burbujas de vapor dispersadas en el líquido fluyendo sobre la bandeja. Por tanto, los regímenes de la burbuja y la espuma son los regímenes de flujo preferidos para la operación de las columnas de bandejas [10,11].
Varios autores han estudiado la operación y diseño de torres de bandejas perforadas. En este sentido, [12] llevó a cabo la evaluación de métodos para el diseño y estimación del rendimiento de bandejas perforadas y columnas de bandejas, generando un programa de computadora que puede establecer rápidamente los parámetros necesarios, con un grado deseado de velocidad operacional.
El procedimiento computacional presentado en este trabajo también ofrece una herramienta conveniente para el dimensionamiento rápido de varias alternativas o la evaluación de la capacidad de una columna existente para funcionar eficientemente con las condiciones de operación impuestas. Los métodos suplementarios de diseño, adecuados para bandejas perforadas u otros tipos de bandejas, pueden ser fácilmente acomodados en este programa. También, en [13] estudiaron la remoción de CO2 mediante el lavado con amoniaco en una torre de bandejas perforadas, donde el material de las bandejas es de acero inoxidable, con un espesor de 3 mm y un diámetro de agujero de 3 mm. Adicionalmente, en [14] desarrollaron un modelo riguroso general basado en la tasa de flujo para estudiar la absorción de NOx en columnas de bandejas y empacadas. El modelo obtenido está basado en la teoría de película y permite describir la fuerte interacción de la reacción, transporte de masa y calor. Un aspecto considerado de forma adicional fue la influencia de la reacción en fase gaseosa en la composición del gas en las secciones vacías de la columna de bandejas. Adicionalmente, el modelo incluye la descripción de los efectos de enfriamiento mediante el empleo de serpentines de enfriamiento instalados en la columna de bandejas. El modelo fue implementado en el ambiente de simulación de Aspen Custom Modeler 0 y validado mediante comparación con los datos experimentales obtenidos en una columna empacada de escala piloto y una columna de bandejas perforadas de escala industrial equipada con serpentines de enfriamiento. En [3] se efectuó el diseño de una columna de bandejas perforadas para efectuar la absorción física de etanol, considerando varios parámetros tales como el diámetro de la columna, caída de presión del gas por bandeja, flujo másico de arrastre y la eficiencia de la bandeja corregida para arrastre. Asimismo, en [15] se diseñó una columna de absorción de bandejas perforadas para separar dióxido de azufre (SO2) de una mezcla aire-SO2, mediante el empleo del software MATLAB0. Las dimensiones optimas obtenidas para la columna diseñada fueron: diámetro de 1 m, altura de 9 m, eficiencia de 25 % y un número actual de etapas de 12. Similarmente, en [16] se condujo un estudio experimental en una columna de bandejas perforadas para investigar la influencia del caudal del gas en las características hidrodinámicas de la bandeja perforada, tales como caída de presión total por bandeja, caída de presión húmeda por bandeja, caída de presión seca por bandeja, altura del líquido y altura de la espuma. Los fluidos usados en este estudio fueron una mezcla gaseosa de 30 %> CO2 y 70 % de aire, así como agua líquida como solvente. Los autores [17] desarrollaron modelos dinámicos y de estado estacionario para estudiar la transferencia de masa y la hidrodinámica de una columna de absorción gaseosa de bandejas perforadas, en donde se modela un proceso real de absorción de etanol contenido en una corriente de CO2 gaseoso proveniente de un proceso de fermentación. Los modelos desarrollados fueron programados en el software MATLAB y SIMULINK aplicando las funciones S estándar. En otro estudio [18] se desarrolló un modelo matemático bidimensional para la remoción de gases ácidos (H2S y CO2) mediante metil-dietanolamina en una columna de bandejas perforadas comercial. El modelo obtenido en este estudio considera las distribuciones de temperatura, concentración y velocidad durante el proceso de absorción sobre las bandejas perforadas, el cual se basa en la teoría de dos películas y considera la aceleración del transporte de masa debido a la complejidad del sistema de absorción estudiado. En [19] se implementó y comprobó un modelo Euleriano-Euleriano con transferencia de masa basado en el coeficiente de transferencia de masa global en fase líquida para sistemas de absorción reactiva CO2-MEA en una columna de bandejas perforadas con tres etapas, con un diámetro de 0,35 m y una distancia entre bandejas de 0,5 m. En este estudio los coeficientes de actividad para la transferencia de masa fueron modelados usando UNIQUAC para predecir mejor la solubilidad de CO2. Además, se condujo un estudio de validación previo en un sistema aire-agua, adquiriendo los datos experimentales de caída de presión y comparando sus resultados de simulación con dos métodos de cálculo de fuerza de arrastre. En [20] se reportó la primera caracterización hidrodinámica a fondo de una columna de bandejas perforadas de gran escala usando perfilador de flujo multi-sonda basado en la conductividad, reportando por primera vez la distribución de la acumulación de líquido en 3D, la distribución del tiempo de residencia y la distribución de altura de espuma efectiva para varias cargas de gas (aire) y líquido (agua) en una alta resolución espacio-temporal. La columna empleada en este estudio tiene un diámetro interno de 0,8 m, un espaciado de bandejas de 0,365 m y un espesor de la bandeja de 15 mm. Por último, en [21] se investigó la influencia de las propiedades físicas del gas sobre el arrastre mediante el empleo de gases (aire, CO2 y SF6) con propiedades físicas notablemente diferentes a las del aire, empleando para ello una columna de bandejas perforadas rectangular y utilizando los líquidos agua, etilenglicol y n-butanol con el fin de lograr el amplio rango de propiedades físicas del líquido. En este estudio se obtuvo una base de datos de alrededor de 500 puntos de datos experimentales con el fin de describir la influencia de las propiedades físicas del gas y los caudales gas-líquido sobre el arrastre.
Las columnas de bandejas perforadas han sido estudiadas también para procesos de destilación, específicamente en cuanto a la modelación y simulación de la destilación de un sistema ternario acetona-butanol-etanol tomando en cuenta la influencia de la etapa de alimentación, relación de reflujo y número de bandejas sobre la pureza y recobrado del butanol, en donde la modelación matemática se efectuó usando un modelo basado en el equilibrio con el método Hang-Wanke modificado obtenido en MATLABÒ R2020a, y los resultados fueron comparados con aquellos obtenidos mediante el simulador Aspen PlusÒ V9 [22]; la propuesta de un modelo de transferencia de masa en un proceso de destilación de una mezcla metanol/etanol en una columna de bandejas perforadas a escala piloto compuesta por 4 bandejas, donde el modelo matemático fue solucionado en MATLABÒ R2013v, obteniendo también los perfiles de composición y temperatura [23]; la aplicación del diseño de experimentos para estudiar el comportamiento de la destilación trifásica en una columna de bandejas perforadas, con el objetivo de deshidratar glicerina a presión atmosférica, comparando los valores experimentales con los resultados de simulación obtenidos usando modelos de equilibrio y no equilibrio [24]; el estudio del comportamiento dinámico de un columna industrial equipada con 16 bandejas perforadas, un diámetro de la torre de 1,5 m y un espaciado de la bandeja de 0,45 m, para efectuar la separación de una mezcla binaria de etilenglicol y agua, en donde se estudió el modelo dinámico implementado para diferentes regímenes de flujo, calcular la eficiencia de bandeja de Murphree e investigar la interacción entre el régimen de flujo de líquido, las eficiencias de la bandeja y el rendimiento de separación [25]; así como también el estudio del proceso de destilación de una solución amoníaco/agua para obtener vapores de amoníaco de elevada pureza, escogiendo para ello una columna de bandejas perforadas debido a su diseño simple, baja caída de presión y su amplio rango de aplicación. En este estudio se empleó el método de Ponchon-Savarit en donde las ecuaciones constitutivas y de conservación fueron solucionadas usando el software comercial Engineering Equation Solver, específicamente para el sistema no lineal de ecuaciones acopladas y para el cálculo de las propiedades termodinámicas y de transporte [26]. También se ha efectuado el diseño mecánico y análisis hidráulico de bandejas perforadas en columnas de paredes divididas [27].
En la actualidad la mayoría de las plantas industriales modernas utilizan sistemas de tratamiento de gases para reducir las emisiones de contaminantes dañinos originados en el proceso productivo. Particularmente, el amoníaco gaseoso es uno de los contribuyentes claves de la contaminación del aire, el cual conduce al deterioro del medioambiente atmosférico [28]. El amoníaco gaseoso es soluble en agua por lo que puede ser fácilmente removido del aire usando agua líquida corriente [29]. Debido a que las torres de absorción se consideran efectivas desde el punto de vista económico, las columnas de absorción amoniaco-agua están ganando popularidad hoy en día para eliminar los problemas asociados con las emisiones de amoníaco [30,31].
Existen pocos estudios publicados en la literatura referidos al estudio de la absorción física de diferentes componentes gaseosos en columnas de bandejas perforadas, mientras que el estudio relativo al diseño de columnas de bandejas perforadas para efectuar la absorción de amoníaco gaseoso, usando agua como solvente, es muy limitado y escaso. Para el conocimiento de los autores una investigación de este tipo no ha sido publicada aún.
Considerando estos antecedentes, el presente artículo reporta el diseño de una columna de bandejas perforadas para efectuar la absorción física de amoníaco usando agua como solvente, con el fin de darle solución a una problemática operacional que ocurre en planta química en Cuba. Varios parámetros de diseño son determinados tales como el diámetro de la torre, la caída de presión del gas por bandeja, la influencia del vertimiento y arrastre, y la eficiencia de bandeja. Para lograr este objetivo fue empleada la metodología descrita en [3].
Materiales y métodos
Definición del problema
En una planta química instalada en Cuba se genera una mezcla gaseosa proveniente de un proceso de fraccionamiento de amoníaco consiste de hidrogeno (H2) y amoníaco (NH3), conteniendo 3 %> molar de NH3. Se desea recobrar el amoníaco mediante un lavado del gas a contracorriente con agua, utilizando una torre de bandejas perforadas. Los caudales másicos disponibles de las corrientes de gas y líquido son de 0,7 y 6,0 kg/s, respectivamente, mientras que las condiciones en el fondo de la columna son:
Utilice un diámetro de perforación en la bandeja de 0,475 cm con un paso equilátero-triangular de 1,25 cm entre los centros del agujero, perforado en una placa de acero inoxidable de 0,2 cm de espesor, y un espaciado de las bandejas de 50 cm. Utilice además una altura del vertedero de 4 cm. Considere un acercamiento a la velocidad de inundación del 80 %%, y un porcentaje de remoción del amoniaco del 95 %>. Diseñe una torre de bandeja perforada de flujo cruzado adecuada para este servicio, y reporte los resultados relativos al diámetro de la torre, longitud del vertedero, caída de presión del gas por bandeja, arrastre del gas y también verifique si ocurre vertimiento excesivo. Finalmente, calcule la eficiencia de la bandeja corregida para arrastre. La caída de presión del gas por bandeja y el caudal de arrastre no deberán exceder los 0,8 kPa/bandeja y 0,3 kg/s, respectivamente.
Datos iniciales
Condiciones en el fondo de la torre:
Otros datos:
Viscosidad del hidrógeno a T G (μ H2 ): 0,0000090 Pa.s [32].
Viscosidad del amoníaco a T G (μ NX3 ): 0,0000103 Pa.s [32].
Fracción molar del hidrógeno en la mezcla gaseosa: (y H2 ) = 0,97.
Fracción molar del amoníaco en la mezcla gaseosa (y NH3 ) = 0,03.
Peso molecular del hidrógeno (M H2 ) = 2,02 kg/kmol.
Peso molecular del amoníaco (M NH3 ) = 17,03 kg/kmol.
Peso molecular del agua (M H2O ) = 18,0 kg/kmol.
Difusividad de la mezcla gaseosa (DG) = 0,230 cm2/s [3].
Difusividad del agua (DL)= 0,0000242 cm2/s [3].
Caudal másico del líquido (L) = 6,0 kg/s.
Caudal másico del gas (V) = 0,7 kg/s.
Aceleración debida a la gravedad (g) = 9,8 m/s2.
Acercamiento fraccional a la inundación especificado (/) = 0,80.
Factor de formación de espuma (F F ) = 1,0 [10].
Tensión superficial del líquido (σ L ) = 68 dyn/cm [32]
Espaciado de la bandeja (t) = 50 cm.
Espesor de la bandeja (l) = 0,2 cm.
Diámetro de perforación en la bandeja perforada (d 0 ) = 0,475 cm.
Paso, distancia entre los centros de las perforaciones en la bandeja perforada (p΄) = 1,25 cm.
Altura del vertedero (h w ) = 4 cm.
Porciento de remoción del amoníaco (R NH3 ) = 0,95.
De acuerdo con [3,4] para soluciones diluidas, la mezcla agua-amoníaco sigue la ley de Henry y a 303 K la pendiente de la curva de equilibrio es m = 0,85.
Para una mejor comprensión de la geometría de la bandeja y del tubo de bajada refiérase a la Figura 2 [3].
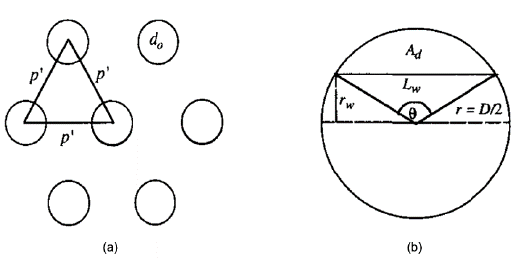
Figura 2 Geometría de la bandeja [3]: (a) Arreglo equilátero-triangular de las perforaciones en una bandeja perforada; (b) Geometría del área del tubo de bajada.
Diámetro de la torre
En el diseño de bandejas perforadas tiene que escogerse el diámetro de la torre para acomodar los caudales de los fluidos involucrados, tienen que seleccionarse los detalles de la disposición de la bandeja, tiene que estimarse la caída de presión y el acercamiento a la inundación, y debe establecerse un aseguramiento contra un vertimiento y arrastre excesivo [3]. El cálculo del diámetro de la torre involucra un proceso iterativo: (a) se escoge un valor inicial del espaciado de la bandeja (usualmente t = 0,4-0,6 m); (b) se calcula el diámetro de la torre basado en el valor escogido de este espaciado de la bandeja; (c) el valor de t es modificado según sea necesario de acuerdo con las recomendaciones de la Tabla 1 [4], y el estimado actual del diámetro de la torre; (d) el procedimiento es repetido hasta que se logre la convergencia.
Paso 1. Densidad del agua líquida (ρ L ) a T G . Según reporta [32], el agua líquida presenta una densidad ρ L de 996 kg/m3 a 303 K.
Paso 2. Peso molecular de la mezcla gaseosa (MG):
Paso 3. Densidad de la mezcla gaseosa (ρ G ):
Donde R = 8,314 J/mol.K [32].
Paso 4. Parámetro (X):
Paso 5. Relación del área del hoyo de vapor con el área activa de la bandeja (
):
Paso 6. Parámetro (α):
Donde t está dado en metros.
Paso 7. Parámetro (β):
Donde t está dado en metros.
Paso 8. Factor (C F ):
Nota: Si el valor de X determinado en la ecuación 3 está en el rango de 0,01 - 0,1, un valor de X = 0,10 deberá utilizarse en la ecuación 7 [3].
Paso 9. Parámetro (F HA ):
Paso 10. Factor de tensión superficial (F ST ):
Paso 11. Constante empírica (C):
Paso 12. Velocidad superficial del gas (v GF):
Paso 14. Caudal volumétrico del gas (Q G ):
Paso 15. Diámetro de la torre (D):
Paso 16. Verifique el valor asumido del espaciado de la bandeja (t) contra los valores recomendados del diámetro de la columna (D ) presentados en la Tabla 1 [4].
Tabla 1 Espaciado de bandeja recomendado [4].
Diámetro de la torre (D) m | Espaciado de la bandeja (t) m |
---|---|
1 o menos | 0,50 |
1 - 3 | 0,60 |
3 - 4 | 0,75 |
4 - 8 | 0,90 |
Paso 17. Ángulo del tubo de bajada (θ):
Paso 18. Longitud del vertedero (L w ):
Paso 19. Distancia desde el centro de la bandeja hasta el vertedero (r w ):
Caída de presión del gas por bandeja
La caída de presión típica por bandeja para el flujo de vapor está en el rango de 0,3-1,0 kPa/bandeja [3]. La caída de presión (expresada como pérdida de carga) para una bandeja perforada se debe a la fricción para el flujo de vapor a través de las perforaciones de la bandeja, acumulación de líquido en la bandeja y la pérdida debida a la tensión superficial. En la mayoría de los casos existe una caída de presión máxima permisible de la torre, por lo que tiene que asegurarse que la caída de presión por bandeja no exceda un determinado valor. Esto conduce a una curva limitada en el diagrama de operación [9].
Paso 20. Área total de sección transversal (A t):
Paso 21. Área del tubo de bajada (A d):
Paso 22. Área activa sobre la bandeja (A α):
Paso 23. Área total del hoyo (A h ):
Paso 24. Velocidad del hoyo (v o ):
Paso 25. Coeficiente del orificio (C o ):
La ecuación (24) es válida solamente si se cumple que
≥ 1,0 [3].
Paso 26. Pérdida de carga de la bandeja seca (h d ):
Donde ρ W es la densidad del agua líquida a la temperatura del líquido = ρ L
Paso 27. Velocidad superficial del gas basada en el área activa de la bandeja (v α ):
Paso 28. Parámetro de capacidad (K):
Paso 29. Densidad relativa efectiva de la espuma (altura del líquido claro/altura de la espuma) (ϕ e ):
Paso 30. Caudal de líquido a través de la bandeja(q L )
Paso 31. Parámetro (C l ):
Donde h W está dado en cm.
Paso 32. Carga equivalente del líquido claro en la bandeja (h l ):
Dónde L W está dado en metros y h W está dado en cm.
Paso 33. Pérdida de carga debido a la tensión superficial (h σ ):
Donde d 0 = 0,00475 m y se asume que el tamaño máximo de burbuja puede tomarse como el diámetro de perforación d 0 .
Paso 34. Pérdida total de carga/bandeja (h t ):
Paso 35. Caída de presión del gas/bandeja (ΔP G ):
Vertimiento y arrastre
El arrastre mecánico de las gotas de líquido en la corriente ascendente de gas constituye una dificultad real usualmente encontrada en absorbedores. A elevadas velocidades, cuando el gas se desprende de la espuma, pequeñas gotas de líquido son transportadas por este gas hacia la bandeja superior. El líquido transportado por esta vía hacia el tope de la torre afecta de forma adversa la transferencia de masa y, consecuentemente, la eficiencia de la bandeja. Por otro lado, el vertimiento ocurre a bajas velocidades del vapor [3] lo cual resulta en un descenso de líquido a través de las perforaciones de la bandeja hacia la bandeja subyacente [11] y/o elevados caudales de líquido, fallando por tanto en obtener el beneficio de un flujo completo a lo largo de la bandeja [3].
Paso 36. Número de Froude del orificio (Fr o ):
Dónde h l está dado en metros.
Bennett et al. [33] reporta que el vertimiento no degrada sustancialmente el rendimiento de la bandeja siempre y cuando se cumpla que el número de Froude del orificio Fr o ≥ 0.5.
Paso 37. Constante (k):
Dónde tanto h l y d 0 están dados en cm.
Paso 38. Altura de la región bifásica en la bandeja(h 2ф )
Dónde tanto h l y d 0 están dados en metros.
Paso 39. Arrastre fraccional (E):
Dónde tanto t y h l están dados en metros.
Paso 40. Caudal másico de arrastre (L e):
Eficiencia de la bandeja
La eficiencia de la bandeja es el acercamiento fraccional a una etapa en equilibrio que es alcanzada por una bandeja real [3]. Bajas velocidades de líquido conducen a situaciones en la cual no existe suficiente líquido fluyendo sobre la bandeja, conduciendo a una distribución dispareja del líquido y, por tanto, al decrecimiento de las eficiencias. En la práctica es usual asegurar una altura del líquido en el vertedero de 0,05 m. El punto de diseño dentro del rango de operación puede ser influenciado por las variables de diseño y operación de la columna, y dependen de la tarea de separación, así como también de la capacidad necesitada, la cual está limitada a su vez por la dinámica del fluido. Adicionalmente, existe una solución de compromiso entre la eficiencia y capacidad [11].
Paso 41. Viscosidad de la mezcla gaseosa (μ G ) a T G :
Paso 42. Número de Reynolds fraccional (Re Fe ):
Donde h l está dado en metros.
Paso 43. Densidad molar de ambas corrientes:
• Mezcla gaseosa (CG):
• Líquido (C L ):
Paso 44. Eficiencia puntual de la bandeja perforada (E OG ):
Paso 45. Número de Peclet del vapor (Pe G):
Dónde en [34] se recomienda utilizar un valor de la difusividad de remolino del gas D
E,G
= 0,01 m2/s, y t está dado en metros. El vapor puede considerarse no mezclado si el número de Peclet del vapor Pe
G
> 50 [3]. La ecuación (45) es válida solo si se cumple que
< 1 [3].
Paso 46. Difusividad de remolino del líquido (D E,L ):
Paso 47. Número de Peclet del líquido (Pe L ):
Donde h i está dado en metros.
Paso 48. Parámetro (N):
Paso 49. Caudal molar de la mezcla gaseosa (V m):
Paso 50. Amoníaco absorbido (A NH3 ):
51. Caudal másico del líquido a la salida del absorbedor (L΄)
Paso 52. Parámetro (λ):
Paso 53. Eficiencia de la bandeja de Murphree (E MG):
Válida solamente para λ < 3.0 [33].
Paso 54. Eficiencia de la bandeja de Murphree corregida por arrastre (E MGE ):
Resultados y discusión
Diámetro de la torre
La Tabla 2 presenta los resultados obtenidos durante la determinación de los parámetros incluidos en los pasos 2-15.
Tabla 2 Resultados de los parámetros incluidos en los pasos 2-15.
Paso | Parámetro | Símbolo | Valor | Unidad |
---|---|---|---|---|
2 | Peso molecular de la mezcla gaseosa | Mg | 2,47 | kg/kmol |
3 | Densidad de la mezcla gaseosa | ρ g | 0,196 | kg/m3 |
4 | Parámetro X | X | 0,120 | - |
5 | Relación del área del hoyo de vapor con el área activa de la bandeja |
|
0,131 | - |
6 | Parámetro α | α | 0,0489 | - |
7 | Parámetro β | β | 0,0302 | - |
8 | Factor C F 1 | c f | 0,075 | m/s |
9 | Parámetro F HA 2 | F HA | 1,0 | - |
10 | Factor de tensión superficial | F st | 1,277 | - |
11 | Constante empírica C | C | 0,096 | m/s |
12 | Velocidad superficial del gas | v gf | 6,84 | m/s |
13 | Parámetro |
|
0,102 | - |
14 | Caudal volumétrico del gas | Q g | 3,57 | m3/s |
15 | Diámetro de la torre | D | 0,962 | m |
1 Debido a que X > 0,10, un valor de X= 0,120 fue usado para determinar C F .
2 Debido a que
3 Debido a que 0,1 < X < 1,0, entonces
Paso 16. Verificación del valor asumido del espaciado de la bandeja t = 0,5 contra el valor calculado de D .
A causa de que el valor calculado de D < 1,0 m, , = 0,5 m constituye el espaciado de la bandeja recomendado de la Tabla 1, por lo que no es necesario efectuar iteraciones posteriores [4]. La Tabla 3 muestra los resultados de los parámetros determinados en los pasos 17-19.
Tabla 3 Resultados de los parámetros determinados en los pasos 17-19.
Paso | Parámetro | Símbolo | Valor | Unidad |
---|---|---|---|---|
17 | Ángulo del tubo de bajada | θ | 1,6397 | rad |
18 | Longitud del vertedero | L w | 0,703 | m |
19 | Distancia desde el centro de la bandeja hacia el vertedero | r w | 0,328 | m |
El diámetro de la bandeja fue de 0,962 m, mientras que el ángulo del tubo de bajada, longitud del vertedero y la distancia desde el centro de la bandeja hacia el vertedero tuvieron valores de 1,6397 rad, 0,7036 m y 0,328 m, respectivamente. El parámetro principal que determina el valor calculado del diámetro de la torre es el caudal del vapor, el cual es relativamente elevado para este proceso de transferencia de masa (3,57 m3/s). Esto está en concordancia con lo reportado por [7], el cual también describe que la velocidad del vapor tiene que estar por debajo de aquella que pudiera ocasionar un arrastre de líquido excesivo o una elevada caída de presión, mientras que el diámetro estimado de la columna debe redondearse hasta el tamaño del cabezal estándar más cercano, para que se puedan emplear cabezales preformados como cierres del equipo. El diámetro de la torre, y, consecuentemente, su área de sección transversal, tiene que ser lo suficientemente grande para manejar los caudales de gas y líquido dentro de la región de operación satisfactoria de las bandejas perforadas. En [3] el diámetro de la torre calculado para un absorbedor de etanol de bandeja perforada fue de 0,989 m, mientras que en [15] el diámetro óptimo fue de 1 m para una columna de absorción de bandejas perforadas diseñada para separar SO2 de una mezcla aire- SO2
Caída de presión del gas por bandeja
La Tabla 4 describe los resultados de los parámetros determinados en los pasos 20-35.
Tabla 4 Resultados de los parámetros determinados en los pasos 20-35.
Paso | Parámetro | Símbolo | Valor | Unidad |
---|---|---|---|---|
20 | Área total de sección transversal | A t | 0,726 | m2 |
21 | Área del tubo de bajada1 | A d | 0,074 | m2 |
22 | Área activa sobre la bandeja | A α | 0,578 | m2 |
23 | Área total del hoyo | A h | 0,076 | m2 |
24 | Velocidad del hoyo | v o | 46,97 | m/s |
25 | Coeficiente del orificio2 | C o | 0,760 | - |
26 | Pérdida de carga de la bandeja seca | h d | 3,75 | cm |
27 | Velocidad superficial del gas basada en el área activa de la bandeja | v α | 6,18 | m/s |
28 | Parámetro de capacidad | K s | 0,087 | m/s |
29 | Densidad relativa efectiva de la espuma | ϕ e | 0,258 | - |
30 | Caudal de líquido a través de la bandeja | q L | 0,006 | m3/s |
31 | Parámetro C l | C l | 50,30 | - |
32 | Carga equivalente del líquido claro en la bandeja | h l | 2,37 | cm |
33 | Pérdida de carga debido a la tensión superficial | h σ | 0,880 | cm |
34 | Pérdida total de carga por bandeja | h t | 7,00 | cm |
35 | Caída de presión del gas por bandeja | ΔP G | 0,683 | kPa |
1 Debido a que 0,1 <X< 1,0,
2 Se empleó la ecuación (24) para determinar C
o
ya que
De acuerdo con los resultados presentados en la Tabla 4, el valor calculado para la caída de presión del gas por bandeja fue de 0,683 kPa/ bandeja. Este valor se encuentra dentro del rango típico establecido por [3], el cual está entre 0,3 hasta 1,0 kPa/bandeja, y está por debajo del límite Ajado por este servicio de transferencia de masa (0,8 kPa/bandeja).
La pérdida de carga individual que más influye en la pérdida total de carga por bandeja es la pérdida de carga de la bandeja seca (3,75 cm) con alrededor del 54 % del total. Esto se debe al valor relativamente elevado que presenta la velocidad del hoyo (46,97 m/s) y el valor más bien pequeño obtenido para el coeficiente de orificio (0,760). Según describe [3] una elevada caída de presión puede conducir directamente a la inundación, esto es, con una elevada diferencia de presión en el espacio entre bandejas, el nivel del líquido que sale de una bandeja a una presión relativamente baja y entra a otra con mayor presión, tiene que asumir necesariamente una posición elevada en los tubos de bajada. A medida que la diferencia de presión se incrementa debido a una tasa de flujo de gas aumentada, el nivel en el tubo de bajada subirá aún más para permitir que el líquido entre a la bandeja inferior. A la postre, el nivel de líquido en el tubo de bajada puede alcanzar aquel de la bandeja superior y el líquido llenará el espacio entre bandejas. La torre estará entonces inundada, la eficiencia de la bandeja caerá hasta un valor muy bajo, el flujo de gas es errático, y el líquido pudiera salir forzado por la tubería de salida del gas en el tope de la columna. En caso de que la caída de presión del gas exceda el límite establecido por el proceso, varias medidas deberán tomarse en cuenta, entre las cuales se incluyen las siguientes [9]:
a) Reducir la velocidad del gas mediante el agrandamiento del área del hueco.
b) Usar huecos menores, debido a que huecos pequeños tienen una caída de presión menor que los huecos más grandes basados en la misma área de hueco absoluta.
c) Reducir la altura de la espuma en la cubierta de la bandeja mediante la reducción de la altura del vertedero o la altura de la cresta del vertedero.
d) Agrandar el área activa (para más huecos) mediante la reducción del área del tubo de bajada o inclinar los tubos de bajada.
En [3] la caída de presión del gas de un absorbedor de etanol de bandejas perforadas fue de 0,817 kPa/ bandeja.
Vertimiento y arrastre
La Tabla 5 exhibe los resultados de los parámetros determinados en los pasos 36-40.
Tabla 5 Resultados de los parámetros determinados en los pasos 36-40.
Paso | Parámetro | Símbolo | Valor | Unidad |
---|---|---|---|---|
36 | Número de Froude del orificio | Fr o | 1,368 | - |
37 | Constante k | k | 0,020 | - |
38 | Altura de la región bifásica en la bandeja | h 2ϕ | 0,333 | m |
39 | Arrastre fraccional | E | 0,145 | - |
40 | Caudal másico de arrastre | L e | 0,102 | kg/s |
Tomando en cuenta los resultados presentados en la Tabla 5, debido a que se cumple que Fr o > 0.5, el vertimiento no constituye un problema bajo las condiciones operacionales encontradas en este sistema de transferencia de masa [33]. También, el caudal de arrastre fue de 0,102 kg/s, el cual está por debajo del límite Ajado por el proceso (0,3 kg/s) y puede clasificarse como bajo [3]. En este resultado influyó el bajo valor obtenido del parámetro h 24 (0,333 m). Puede establecerse entonces que la bandeja perforada operará a una elevada eficiencia debido a que el vertimiento de líquido a través de las perforaciones de la bandeja será los suficientemente pequeño comparado con el flujo sobre el vertedero y hacia el tubo de bajada, mientras que el arrastre de líquido por el gas no es elevado o excesivo. En [3] el valor del caudal másico de arrastre fue de 0,110 kg/s para un absorbedor de etanol de bandejas perforadas, en donde también se verificó que el vertimiento no es un problema bajo estas circunstancias.
Eficiencia de la bandeja
La Tabla 6 muestra los resultados de los parámetros determinados en los pasos 41-54.
Tabla 6 Resultados de los parámetros determinados en los pasos 41-54.
Paso | Parámetro | Símbolo | Valor | Unidad |
---|---|---|---|---|
41 | Viscosidad de la mezcla gaseosa | μ G | 9,24x10-6 | Pa.s |
42 | Número de Reynolds fraccional | Re Fe | 91 523,64 | - |
43 | Densidad molar de la mezcla gaseosa | C G | 0,079 | kmol/m3 |
Densidad molar del líquido | C L | 55,33 | kmol/m3 | |
44 | Eficiencia puntual de la bandeja perforada | E OG | 0,727 | - |
45 | Número de Peclet del vapor1 | Pe G | 1 591,59 | - |
46 | Difusividad de remolino del líquido | D E,L | 0,060 | m2/s |
47 | Número de Peclet del líquido | Pe L | 3,14 | - |
48 | Parámetro N | N | 2,57 | - |
49 | Caudal molar de la mezcla gaseosa | V m | 0,283 | kmol/s |
50 | Amoníaco absorbido | A NH3 | 0,137 | kg/s |
51 | Caudal másico del líquido a la salida del absorbedor | L' | 6,137 | kg/s |
52 | Parámetro | λ | 0,706 | - |
53 | Eficiencia de la bandeja de Murphree2 | E MG | 0,845 | - |
54 | Eficiencia de la bandeja de Murphree corregida por arrastre | E MG E | 0,796 | - |
1 El vapor puede considerarse no mezclado debido a que el número de Peclet del vapor Pe
G
> 50 [3] y resulta válida de usar ya que
2 La ecuación es válida de usar debido a que λ < 3,0 [33].
Según se describe en [7], la eficiencia de la bandeja de Murphree es la relación entre la separación real lograda con aquella que pudiera lograrse en una etapa de equilibrio, o también se define como la relación entre el cambio real en la composición del vapor para una etapa de equilibrio [2], y oscila generalmente entre 0,4 y 0,8, con un límite superior de uno [6]. Este parámetro se especifica para suministrar una medida de la desviación de la suposición de una bandeja en equilibrio ideal, y se emplea para determinar el número de etapas ideales requeridas para lograr la separación deseada. Éste parámetro depende de la resistencia de la transferencia de masa de cada componente en cada fase, e incorpora la influencia adicional del vertimiento y arrastre. Según se indica en la Tabla 6, la eficiencia de bandeja de Murphree corregida por arrastre determinada en este proceso fue de 0,796, la cual puede considerarse aceptable y relativamente elevada [3]. Benitez [3] obtuvo un valor de 0,811 para la eficiencia de bandeja de Murphree corregida por arrastre para un absorbedor de etanol de bandejas perforadas.
Conclusiones
Se diseñó una torre de bandejas perforadas para llevar a cabo la absorción física de amoníaco usando agua como solvente y mediante el empleo de la metodología reportada en [3]. Se calcularon varios parámetros claves tales como el diámetro de la torre (0,962 m), la caída de presión del gas por bandeja (0,683 kPa/bandeja), caudal másico de arrastre (0,102 kg/s) y la eficiencia de bandeja de Murphree corregida por arrastre (0,796). Los valores determinados de las variables caída de presión del gas por bandeja y caudal másico de arrastre son menores que los límites Ajados por el proceso; consecuentemente la columna de bandejas perforadas diseñada en este estudio puede ser aplicada satisfactoriamente para el servicio de transferencia de masa demandado.