Services on Demand
Journal
Article
Indicators
-
Cited by SciELO
-
Access statistics
Related links
-
Cited by Google
-
Similars in SciELO
-
Similars in Google
Share
Ingeniería e Investigación
Print version ISSN 0120-5609
Ing. Investig. vol.30 no.1 Bogotá Apr. 2010
Jaime Alberto Giraldo García1, William Ariel Sarache Castro2 y Omar Danilo Castrillón Gómez3
1 Ingeniero industrial. Ph.D., en Ingeniería, Universidad Nacional de Colombia. Profesor asociado, Departamento de Ingeniería Industrial, Universidad Nacional de Colombia, Manizales. jaiagiraldog@unal.edu.co 2 Ingeniero industrial. Ph.D., en Ciencias Técnicas, Universidad Central de las Villas, Cuba. Profesor asociado y actual vicerrector, Departamento de Ingeniería Industrial, Universidad Nacional de Colombia, Manizales. wasarachec@unal.edu.co 3 Ingeniero de sistemas. Ph.D., en Bioingeniería, Universidad Politécnica de Valencia, España. Profesor Asociado, Departamento de Ingeniería Industrial, Universidad Nacional de Colombia, Manizales. Coordinador, grupo de investigación en Innovación y Desarrollo Tecnológico. odcastrillong@unal.edu.co
RESUMEN
En el municipio de Caldas (Colombia), uno de los sectores estratégicos para la economía regional es el de las pymes metalmecánicas; de hecho, este sector, según estadísticas del DANE a 2005, participa aproximadamente con el 31% de los establecimientos industriales del departamento y con un 29% del empleo industrial, además tiene vocación exportadora hacia países andinos. Sin embargo, estudios preliminares realizados al 57% del universo empresarial de este sector (no incluye microempresas ni famiempresas), demuestran serias falencias de tipo estructural (tecnologías, procesos, instalaciones) e infraestructural (programación de la producción, sistemas de calidad, etc.) en los sistemas de producción de estas organizaciones. Mediante este artículo se espera divulgar entre la comunidad académica los resultados obtenidos al aplicar una metodología integral de mejoramiento del sistema de producción en una empresa piloto del sector. A partir de la definición y ponderación de las prioridades competitivas que la empresa debe alcanzar, y siguiendo la metodología universalmente aceptada en estudios de simulación discreta, se propone un marco de experimentación para mejorar los niveles alcanzados por el sistema en dichas prioridades empleando técnicas de bifurcación secuencial, diseño factorial en experimentación y superficies de respuesta. Al final se presentan las mejoras alcanzadas en las prioridades competitivas en términos de un índice de efectividad (IE) del sistema de producción de una empresa piloto estudiada al pasar éste de 1,84 a 2,46.
Palabras clave: empresas metalmecánicas, sistemas de producción, simulación discreta, bifurcación secuencial, diseño estadístico de experimentos, superficies de respuesta.
ABSTRACT
Metalworking companies represent one of the strategic sectors in the regional economy of the Caldas department in Colombia; in fact, this sector is involved in 31% of the departments industrial establishments and 29% of industrial employment according to DANE (Colombian State Statistical Department) statistical data from 2005. The sector also exports to Andean countries. However, preliminary studies conducted with 57% of the entrepreneurs from this sector (excluding micro companies and family businesses) have revealed serious structural (technology, processing, installations) and infrastructure weaknesses (production planning, quality systems) in these organisations production systems. It is hoped that this paper will lead to disseminating the results amongst the academic community of implementing a comprehensive methodology for improving the production system of a pilot company from this particular sector. An experimental framework for improving the levels reached by the system regarding such priorities is proposed following universally accepted methodology in discrete simulation studies; it proposes using sequential bifurcation, factorial design and response surface experimentation based on defining and weighting the competing priorities which the company should achieve. The improvements in the pilot companys production system priorities are presented in terms of an effectiveness index (EI) which rose from 1.84 to 2.46 by the end of the study.
Keywords: metal-working company, production system, discrete simulation, sequential bifurcation, statistical design for experiments, response surface.
Recibido: abril 20 de 2009 Aceptado: febrero 16 de 2010
Introducción
En el caso del sector metalmecánico de Caldas, observaciones preliminares (Sarache et ál., 2005) revelan, en lo que a la gestión de la producción se refiere, en la mayoría de las empresas de este sector, especialmente en Pymes, la inexistencia de una estrategia integral que permita mejorar el funcionamiento del sistema de producción, concebido este último en sus dos dimensiones: el sistema físico de transformación (SFT) y el sistema de programación y control de la producción (PPC). El procedimiento validado por Sarache ét al. (2007), propone un esquema de mejoramiento coherente en tres aspectos fundamentales: 1) las prioridades competitivas (P), 2), el sistema de producción (S), y 3), las palancas de fabricación (P). En otras palabras, una acción de mejora en un sistema de producción debe partir por identificar las prioridades competitivas o exigencias del mercado objetivo; a partir de éstas, se debe valorar la coherencia de la configuración adoptada por el sistema productivo y el desempeño de sus subsiste-mas o palancas de fabricación con dichas prioridades competitivas.
Sin duda, el enfoque orientado a reconocer y potenciar el papel de la función de producción/operaciones como arma estratégica para la creación de ventajas competitivas sostenibles, ha cobrado importancia en las últimas décadas, tal como lo sustentan los aportes de diversos autores clásicos, entre los que se destacan cronológicamente: (Skinner, 1974, pp. 111-120; Hayes y Schemner, 1977, pp. 105-119; Hayes y Weelwright, 1984; Domínguez et ál., 1995; Krajewski y Ritzman, 2000; Gaither y Frazier, 2000; Heizer y Render, 2001; Miltenburg, 2004).
Trabajos recientes de investigación relacionados con mejorar la función de producción en su dimensión de programación (PPC) en ambientes Job Shop apuntan a emplear un criterio mediante el cual se mide la utilización de los recursos productivos, es decir, se centran en objetivos relacionados con la eficiencia, mas no con la efectividad lograda por el sistema de producción en coherencia con el mercado objetivo al que debe responder. Así por ejemplo, Osorio et ál. (2008) proponen un modelo de programación jerárquica de la producción empleando como criterio de evaluación el tiempo de finalización de los pedidos (makespan) que se compara con el makespan arrojado por un reconocido software descheduling; Roshanaei et ál., (2009), formulan el mismo criterio para mejorar un algoritmo de programación de producción basándose en tiempos de preparación de máquinas dependientes de la secuencia; Su et ál. (1998) plantean una heurística de programación basada en reglas de prioridad cuyo desempeño se mide con el criterio tiempo de retraso (lateness); y Zhou et ál. (2009) presentan un marco de trabajo en el que integran una heurística y un algoritmo genético para programar la producción empleando como criterio de evaluación el tiempo de tardanza (tardiness).
A nivel de estrategia de producción, autores como Miltenburg, 2004; Ibarra, 2003) recalcan la necesidad de medir la mejora en un sistema de producción en términos de múltiples prioridades competitivas (múltiples criterios), en razón a que éstas últimas están relacionadas de manera más natural con un mercado objetivo. Las prioridades competitivas se hallan relacionadas con las características de los productos o servicios que los clientes consideran deseables; este concepto ha sido denominado de forma diferente según los diversos autores que han abordado la temática. Algunas denominaciones más reconocidas son: tareas de producción (Skinner, 1974)], metas de fabricación (Miller, 1983), objetivos de producción (Anderson et ál., 1989), entre otras. Las prioridades competitivas señalan la orientación dominante de la producción; sin embargo, para que las prioridades competitivas sirvan de guía en la fijación de políticas en las distintas áreas de decisión, así como para la toma de decisiones a largo y corto plazo, es conveniente su disgregación cualitativa (Garvin, 1993), así como su expresión en términos cuantitativos y mensurables (Schroeder, 2003). Corbett y Wassenhove (1993) identifican dos dimensiones en las prioridades competitivas: a) como indicador externo de la competitividad de la empresa, y b) como indicador interno del saber hacer en fabricación (o sea, de las capacidades de fabricación). Ambas están estrechamente interrelacionadas, puesto que la com-petitividad depende de la eficacia de los atributos de los productos para satisfacer las necesidades del mercado y a su vez, estos atri-butos tienen su origen en el modo como se hacen las cosas en el área de producción. El estado actual de la producción, permite constatar la existencia de siete prioridades competitivas básicas: costo, calidad, entregas, flexibilidad, servicio, innovación y respon-sabilidad ambiental (Avella y otros, 1999; Ibarra, 2003). Una des-cripción de estas prioridades y ejemplos de criterios de medida/ atributos de operacionalización puede ser consultada en (Giraldo et ál., 2008, pp. 35-36).
Un asunto importante radica en el problema de las incompatibilidades entre las prioridades competitivas de fabricación (trade-offs). Un trade-offs significa conceder a una misión u objetivo de pro-ducción un tratamiento preferencial sobre las demás, cuyo principio básico está en evitar que un sistema de producción posea más de una misión (Miller, 1983). Esta idea, tal como se desprende del trabajo de Skinner (1974), es que rara vez es posible que una planta consiga mejoras significativas en más de una o dos de las prioridades competitivas al tiempo, pues requeriría políticas de producción radicalmente distintas. Este planteamiento conlleva a que el establecimiento de las prioridades competitivas claves, se convierta en un problema no sólo de seleccionar sino también de jerarquizar. Esta jerarquización hace necesario el empleo de técnicas multicriteriales que permitan definir las prioridades competitivas que deben ser potenciadas en el mejoramiento de sistemas de producción en las empresas objeto de estudio. Tales técnicas resultan bastantes útiles para la construcción de indicadores (efectividad-eficiencia) orientados a medir el desempeño de una organización productiva o un sistema productivo en relación con sus prioridades o misiones de fabricación.
En este orden de ideas, se ha propuesto una metodología integral soportada en simulación discreta para el mejoramiento de los sistemas de producción en Pymes metalmecánicas. Se describe la aplicación de la metodología en una empresa piloto, la cual parte de lo estratégico al considerar un procedimiento para la definición y jerarquización de prioridades competitivas de fabricación (Sarache et ál., 2005) y otro para evaluar la estrategia de manufactura (Sarache et ál., 2007). Luego se modela conjuntamente mediante simulación discreta el sistema físico de transformación (SFT) y el sistema de programación y control de la producción (PPC), a partir de los conceptos expuestos en Giraldo et ál. (2008, pp. 298-315). Posteriormente, se considera la experimentación teniendo en cuenta un amplio número de factores que potencialmente pueden influir en las prioridades competitivas seleccionadas, empleando técnicas de filtrado y diseño factorial. Finalmente se hace un análisis de varianza y se prueba un modelo de optimización multirrespuesta para determinar cuáles factores y en qué niveles se deben operar estos en el sistema real para mejorar el indicador de efectividad del sistema de producción en estudio.
Metodología integral de mejoramiento de sistemas de producción
ETAPA 1. Definición de prioridades competitivas
Para tal fin se aplicó el procedimiento validado en Sarache et ál., 2005), el cual permite definir y jerarquizar el conjunto de prioridades competitivas que exige un mercado objetivo. De 15 Pymes metalmecánicas a las que se les aplico el procedimiento, se seleccionó una como piloto de experimentación, cuyos productos principales son utensilios para cocina. La autoevaluación para la empresa piloto en estudio se expone en la Tabla 1. De acuerdo con los resultados obtenidos por los expertos, la calidad, el precio y la entrega son las tres prioridades más importantes; entre estas tres se recoge el 66% de la importancia relativa. Igualmente, se aprecia en la Tabla 1 que el indicador de efectividad (IE) del sistema de producción para la empresa en estudio es del orden de 1.84, el cual se considera bajo, toda vez que empresas similares de categoría mundial ofrecen este indicador en un nivel superior a 4.
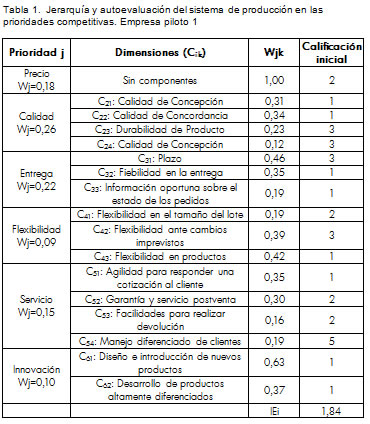
ETAPA 2. Acciones de mejoramiento. Aplicación del modelo general y las herramientas informáticas/procedimientos estadísticos
Con base en el modelo general de mejoramiento integrado para el sistema de producción que se expone en la Figura 1, se desarrolló para la empresa en estudio un modelo de simulación de eventos discretos con sus respectivas herramientas informáticas/estadísticas, que fue utilizado como medio de experimentación de las tres prioridades competitivas relevantes. Mediante la experimentación con el modelo se busca mejorar el índice de efectividad (IE) alcanzado por la empresa en las prioridades competitivas costo, plazo y calidad, al manipular simultáneamente los factores controlables relacionados con las palancas de fabricación o la configuración productiva.
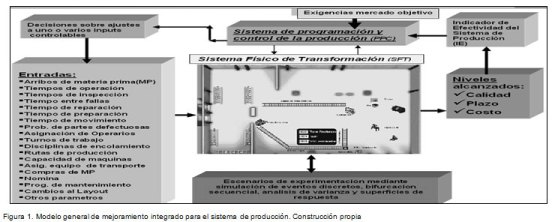
Para construir el modelo de simulación se siguió la metodología universalmente aceptada en estudios de simulación discreta (Shannon, 1988; Banks et ál., 2004; Kelton y Law, 2007), como se describe a continuación:
Paso 1. Objetivo del modelo de simulación
Desarrollar y aplicar un modelo integral soportado en simulación discreta y sus procedimientos estadísticos/informáticos asociados que, mediante experimentación, permita medir el mejoramiento del índice de efectividad (IE) del sistema de producción de la empresa piloto estudiada.Paso 2. Definición del sistema de producción
En la definición del sistema productivo se recolectaron datos sobre flujograma general del proceso de producción; locaciones de procesamiento y almacenaje, así como sus capacidades; secuencias de enrutamiento para cada materia prima; tipos de materias primas (entidades) necesarias para la fabricación del producto; cantidad y disciplina de entrada de las materias primas, etc.; recursos (personal, vehículos y equipos) utilizados en el sistema; tiempos requeridos por cada operación, recursos usados y materiales implicados; disciplina de encolamiento entre estaciones de trabajo; características de maniobra de los recursos tales como la velocidad, la distancia o el tiempo; horarios de trabajo de los recursos y descansos de éstos; costos de materias primas, insumos y utilización de maquinaria y otros recursos; tiempos relacionados con los daños en la maquinaria o bajas de recursos; información de unidades defectuosas en cada operación o en el sistema en general.
Paso 3. Construcción del modelo de simulación
Para construir el modelo de simulación se empleó el software Promodel, versión 6.2. La Figura 2 ofrece una vista del modelo de simulación en computadora. En síntesis, el modelo de simulación representa al sistema de producción en sus dimensiones física (SFT) y de gestión (PPC).
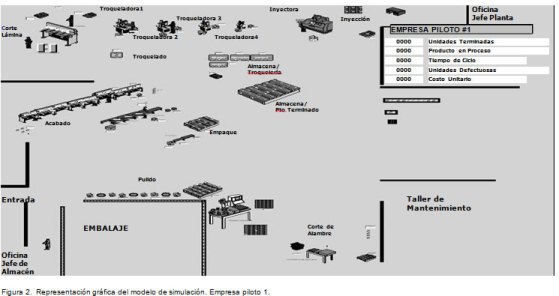
Paso 4. Validación del modelo de simulación
Para la validación se presentó el modelo al gerente y al jefe de planta, para que de acuerdo con sus conocimientos de la empresa valoraran si el comportamiento del modelo es aproximadamente similar al funcionamiento del sistema real de producción. Para tal fin, se efectuaron pruebas estadísticas empleando datos históricos de niveles de producción alcanzados en un periodo de ocho semanas, encontrándose que arroja niveles similares.
Paso 5. Experimentación
Según Kelton y Law (2007), en estudios con simulación discreta podemos encontrar, a partir de varios parámetros y suposiciones estructurales, cuáles tienen mayor efecto sobre una medida de rendimiento, o cuál conjunto de especificaciones del modelo conducen a un rendimiento óptimo.Para el caso, los términos parámetros y suposiciones estructurales (subsistema S-P), es lo que denominaremos factores, mientras que medida de rendimiento se denota como respuesta, que para la empresa piloto en estudio serían los niveles alcanzados en las prioridades competitivas: costo, plazo y calidad (sistema P). La prioridad calidad se considera en el modelo en su dimensión de concordancia (% defectuosos) como un factor que afecta al plazo y al costo. En la realización de la experimentación se aplicó la metodología de diseño estadístico de experimentos (DOE), con una longitud de corrida de ocho semanas y simulando a tres réplicas.
Determinación de los factores a estudiar
De acuerdo con el modelo de la Figura 1, los factores de experimentación que pueden influenciar el desempeño de las prioridades competitivas costoy plazose pueden agrupar entre los relacionados con el sistema físico de transformación (SFT) y el sistema de programación y control de la producción (PPC); todos ellos enmarcados dentro de las palancas de fabricación (P) y el sistema de producción (S). Para ser consistentes con el método científico, potencialmente todo lo involucrado en un sistema de producción puede influir en los niveles alcanzados por las prioridades competitivas. No obstante, en el proceso de experimentación sólo se incluyeron aquellos factores controlables (modificables) por la empresa. En la Tabla 2 se muestran los primeros 13 (de 76) factores a estudiar con sus respectivos niveles - y +. El nivel - corresponde al nivel actual de operación del factor, el nivel + correspondería al nivel modificado del factor. Obsérvese que algunos niveles corres-ponden a valores aleatorios y otros a valores determinísticos. Otros valores pueden ser cualitativos, como por ejemplo la regla de enrutamiento hacia una estación de trabajo (FIFO, LIFO, SPT, etc.). Los niveles + (propuesto) para los 76 factores controlables fueron sugeridos por la gerencia, jefe de planta y los autores de esta investigación. Son de especial interés los factores 75 y 76. El factor 75 en su nivel - lo constituye el programa de requerimiento de materiales utilizado por la empresa actualmente, mientras que el nivel + es el programa arrojado por un aplicativo informático de-nominado MRP-CRP, desarrollado en el marco de esta investiga-ción. El factor 76 en su nivel - es el programa de requerimientos de capacidad calculado manualmente por la empresa, y el nivel + el arrojado por el mencionado aplicativo informático. Las bases conceptuales del algoritmo en el cual se basa este aplicativo informático pueden ser consultadas en Giraldo et ál., (2008, pp. 103-112).

Filtrado de factores
Dado que se usará un diseño experimental 2k (k factores cada uno a dos niveles), sería impracticable experimentar con 276 puntos de diseño (escenarios). Se propone entonces emplear la técnica de fitrado bifurcación secuencial (Bettonvil, 1990), cuyo objetivo es encontrar los factores que realmente tienen efecto en las variables de respuesta (prioridades competitivas). La bifurcación secuencial se relaciona con el algoritmo de la búsqueda binaria, el cual busca un elemento en un arreglo ordenado, dividiendo el espacio de búsqueda en mitades hasta encontrar o no el elemento buscado. El procedimiento sigue una secuencia de pasos. Se comienza colocando todos los factores en un solo grupo y se comprueba si el grupo de factores tiene un efecto importante. Si lo hace, el grupo se divide en dos subgrupos y para cada uno de éstos se realizan pruebas de importancia. El procedimiento continúa desechando los grupos poco importantes y dividiendo los importantes en grupos más pequeños. Eventualmente, todos los factores que están etiquetados en los grupos con importancia se someten a una prueba individual.
Al aplicar la bifurcación secuencial se encontró que los factores20, 32, 42, 61 y 68influyen en la variable de respuesta plazo y los factores 17, 57 y 75en la variable respuesta costo. En las Tablas 3 y 4 se describen estos factores con sus respectivos niveles. Si el lector desea ver en más detalle la aplicación de esta técnica en otra empresa metalmecánica puede consultar la ponencia de Giraldo et ál., 2008).
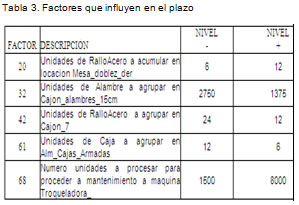
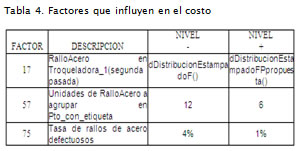
Experimentación con factores influyentes
Para desarrollar el diseño estadístico de experimentos 2k se plantearon dos diseños de experimentación. El diseño plazo, en función de los factores 20, 32, 42, 61 y 68 (cinco factores con dos niveles) y el diseño costoen función de los factores 17, 57 y 75 (tres factores con dos niveles). Para el plazo se empleó un diseño 25, lo que arroja 32 puntos de diseño. Para el costo se utilizó un diseño 23, es decir ocho puntos de diseño. La Tabla 5 contiene la respuesta de la variable plazo por cada punto de diseño (escenario) experimentando con el modelo a tres réplicas por escenario y obteniendo el promedio en horas. La Tabla 6 contiene similar información, pero aplicada a la variable de respuesta costo, obteniendo la respuesta en pesos.
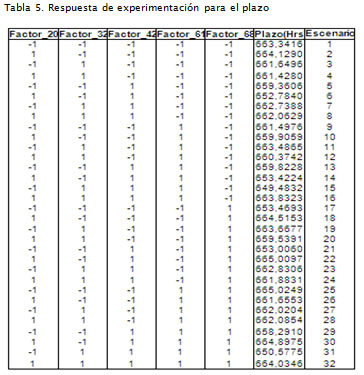
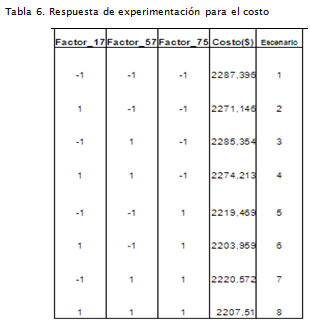
Análisis de varianza para el plazo
Para la variable plazo se procedió, partiendo de los resultados de la simulación mostrados en la Tabla 5, a validar estadísticamente los efectos que tienen los factores en ésta. La Tabla 7 muestra que el factor 42 tiene un efecto importante en la variación de la respuesta plazo, es decir, que si en vez de agrupar como lote de transferencia 24 unidades de producto (nivel -1), se hace con 12 (nivel +1) se disminuye el plazo. Igualmente, la Tabla 7 revela que la interacción de los factores 20, 32 y 61,y la interacciónde los factores20, 32 y 68, conllevan a la variación del plazo a un nivel de confianza del 95%. La Figura 3 ratifica de nuevo que el factor 42 disminuye el plazo y el factor 61 lo hace muy levemente. Sobre este último factor podrían reconsiderarse sus niveles de operación a fin de estudiar niveles para este factor que afecten al plazo. En la Figura 4 se muestran las interacciones de segundo orden. Se connota que las interacciones CD (factores 42 y 61) y CE (factores 42 y 68) tienden a bajar el plazo. Al igual que el factor 61, podrían reconsiderarse los niveles de operación para el factor 68.
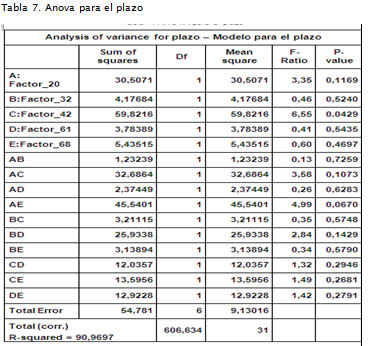
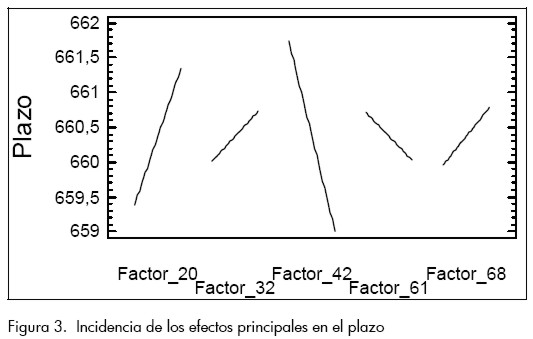
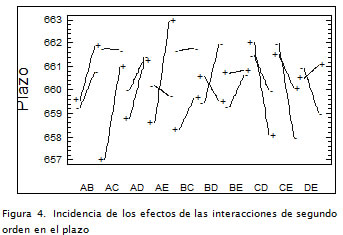
Análisis de varianza para el costo
Para la variable costo se procedió, partiendo de los resultados de la simulación de la Tabla 6, a validar estadísticamente los efectos que tienen los factores en ella. La Tabla 8 señala que los factores 17 y 75 tienen un efecto importante en la variación de la respuesta costo a un nivel de confianza del 95%, y la Figura 5, que el mayor efecto en la disminución del costo lo aporta el factor 75, seguido del factor 17, y que el costo es prácticamente insensible ante cambios del factor 57. En la Figura 6 se presentan las interacciones de segundo orden. Se connota que la interacción AB (factores 17 y 57) y la interacción AC (factores 17 y 75) tienden a bajar el costo. Igualmente, podrían reconsiderarse los niveles de operación para el factor 57 dado el efecto de la interacción AB.
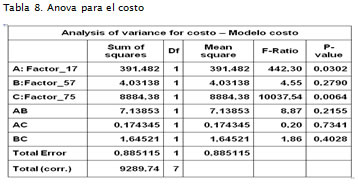
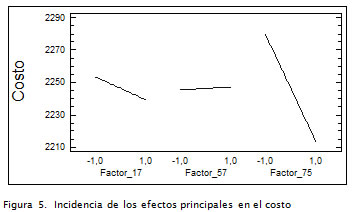
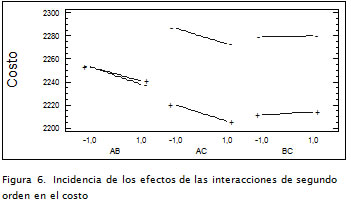
En síntesis, los factores 17, 42 y 75 influyen significativamente en la variación de las prioridades competitivas costo y plazo. Sería entonces ideal desarrollar un modelo que nos mostrara a qué nivel se deben operar estos factores para obtener un efecto de optimización combinado en estas prioridades, empleando las sugerencias planteadas por Kleijnen (2007).
Optimización
Las respuestas consideradas fueron el plazo y el costo en función de los factores que inciden en la variación de éstas: 17, 42 y 75. Para tal fin, se eligió un diseño 3k: k factores con tres niveles. Para el caso k=3 los niveles serían: -1, 0, +1. La Tabla 9 expone por cada factor los niveles con los cuales se experimentó. Los niveles del factor 17 son tiempos de operación aleatorios arrojados por una distribución de frecuencia, donde el nivel -1 representa la distribución con un muestreo de tiempos tomando el método de operación actual y el nivel +1 muestreando tiempos con el método propuesto; por lo tanto, los números 1, 3 y 2 en los niveles del factor 17 son meros identificadores de la respectiva distribución de frecuencia.
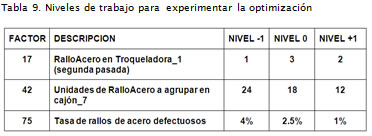
La Tabla 10 contiene la respuesta alcanzada por las variables plazo y costo por cada punto de diseño (escenario) experimentando con el modelo a tres réplicas por escenario y obteniendo promedios en horas y pesos, respectivamente. El procedimiento de optimización con el software StatGraphics exige efectuar en cada variable un estudio de superficie de respuesta.
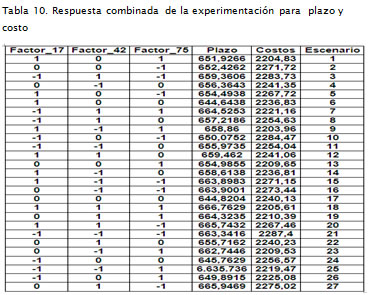
La Tabla 11 muestra la optimización de superficie de respuesta para la prioridad competitiva plazo y la Figura 7 el dibujo de la respectiva superficie. La Tabla 11 nos informa que el valor mínimo del plazo alcanzado es de 644,5 horas con los niveles de los factores registrados en la columna Optimum. La Figura 7 visualiza la respectiva superficie bajo la consideración que el factor 75 se encuentra en su nivel 0. Igualmente, se podrían visualizar superficies considerando los factores 17 y 42 en su nivel 0. La Tabla 12 expresa que el valor mínimo del costo alcanzado es de 2203,9 pesos con los ni-veles de los factores registrados en la columna Optimum. La Figura 8 visualiza la respectiva superficie bajo la consideración de que el factor 75 se encuentra en su nivel 0. También se podrían visualizar superficies considerando los factores 17 y 42 en su nivel 0.
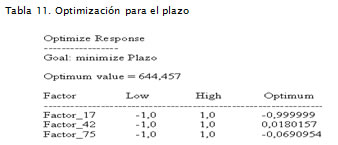
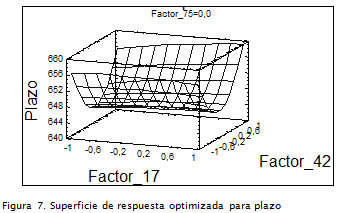
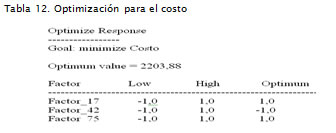
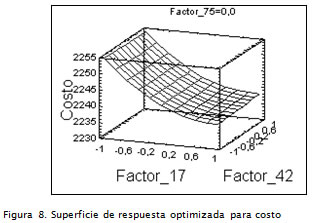
En la Tabla 13 se despliegan los resultados obtenidos al ejecutar el procedimiento de optimización para plazo y costo simultáneamente. Obsérvese en dicha tabla que los datos empleados para efectuar el proceso de optimización simultánea corresponden a los registrados en la Tabla 10. El resultado del proceso de optimización se expone en la Tabla 14, la cual reporta un plazo mínimo de 648,5 horas y un costo mínimo de 2.215 pesos simultáneamente con niveles para los factores 17, 42 y 75 de +1, -0,108 y 0,693 respectivamente. La Figura 9 muestra la superficie de respuesta de la deseabilidad del costo y plazo variando los factores 42 y 75 y manteniendo constante el factor 17 en su nivel 0.
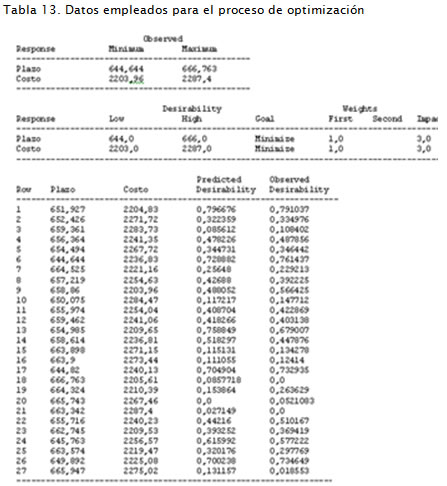
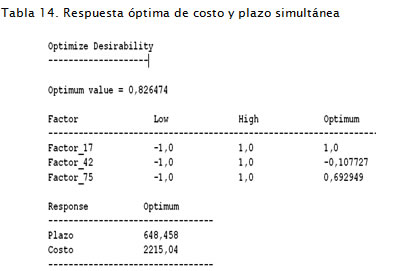
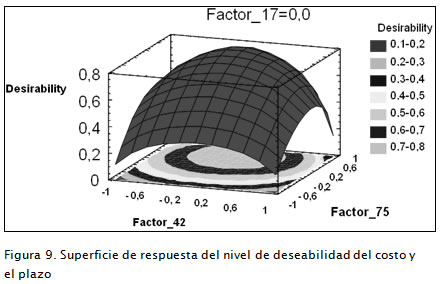
Según la Tabla 14, el valor óptimo de deseabilidad es de 0,826474, por lo que en la Figura 9 la superficie alcanza dicha altura máxima aproximadamente; el contorno de color gris señala la región en la que se deben mover los niveles de los dos factores con el objeto de mejorar (disminuir) las respuestas costo y plazo simultáneamente. Igualmente, se podrían dibujar superficies manteniendo en su nivel 0 los factores 42 y 75.
Traduciendo los niveles óptimos de los factores desde sus niveles codificados a sus valores originales, se obtienen los valores con los cuales debería operar el sistema de producción a fin de mejorar su indicador de eficiencia (IE), según se aprecia en la Tabla 15.
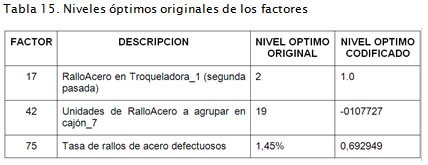
Al correr una simulación a tres réplicas bajo un escenario con los niveles de los factores 17, 42 y 75 indicados en la Tabla 15 (columna 2) y los demás factores en su nivel actual, se obtiene para el costo el valor promedio de 2.216 pesos y para el plazo 651 horas, valores muy cercanos a los arrojados por el estudio de superficies de respuesta contenido en la Tabla 14, de y 2.215,04 y 648,5 respectivamente.
ETAPA 3. Valoración de resultados
Dado que el proceso de mejora, debido a la complejidad del sistema de producción examinado y a la jerarquía de las tres prioridades competitivas más importantes, solo se centró en el costo (precio), el plazo y la calidad, el impacto en el indicador IE de la empresa en estudio debe ser revisado en esa misma vía. La gerencia de la empresa realizó de nuevo su proceso de auto-evaluación basado en los resultados de esta experimentación. En la Tabla 16 se presenta la proyección de impactos en el IE dados por la gerencia.
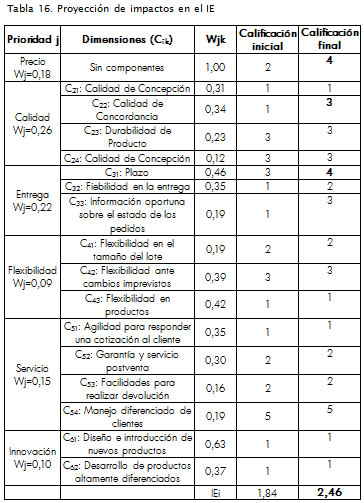
Con base en los resultados de la Tabla 16 es posible demostrar que, mediante la aplicación de los modelos conceptuales que soportan el modelo integral de mejoramiento y las herramientas informáticas diseñadas para tal fin, se puede medir el mejoramiento del IE de la empresa de un valor de 1,84 a un valor de 2.46. No obstante, aunque el resultado aún no le permite a la empresa llegar a los niveles más destacados del IE, las mejoras no son despreciables.
Conclusiones
Para solventar las debilidades estructurales de los sistemas de producción en Pymes metalmecánicas es necesario partir de una identificación plena de las prioridades competitivas que deben ser perseguidas en la estrategia de mejoramiento. Tales prioridades son la base fundamental para seleccionar el conjunto de actividades de mejoramiento en torno al sistema de producción y al ajuste en las palancas de fabricación. El primer paso dentro del propósito general de mejoramiento consiste en establecer la posición relativa de la Pyme frente a las exigencias del cliente y sus mejores competidores y a partir de ésta definir las acciones estratégicas a adoptar que permitan mejorar la posición competitiva en el mercado objetivo. En este sentido, el indicador de desempeño IE se constituye en un aporte importante que facilita el estudio de la tríada Empresa-Cliente-Competidor y la orientación de las acciones de mejora en el sistema productivo. El procedimiento que guía la construcción del IE puede ser aplicable en empresas de otros sectores industriales, con las debidas adaptaciones. Para el caso en estudio, es necesario que el conjunto de prioridades competitivas y su jerarquización estén siendo monitoreadas y ajustadas ante cambios en las percepciones por parte del mercado. De acuerdo con el indicador, para el sector metalmecánico resulta de vital importancia trabajar en tres prioridades fundamentales: costo, calidad y plazo de entrega.
Como una contribución fundamental de la presente investigación, el modelo general de mejoramiento integrado para el sistema de producción, junto con las herramientas informáticas de soporte, les permite a las Pymes metalmecánicas enmarcar su actuación a partir de un enfoque que promueve la mejora en sus dos subsistemas claves: el de programación y control de la producción, y el físico de transformación. El primero le permite a la empresa organizar los procesos de gestión relacionados con el tratamiento de pedidos provenientes del cliente y la generación de órdenes de compra hacia los proveedores, así como el establecimiento de las acciones de ejecución; el segundo, de forma integrada con el primero, es el encargado de ejecutar las secuencias de fabricación programadas. De esta manera, la empresa puede mejorar su fiabilidad y reducir sus plazos de entrega. Por otro lado, la mejora en el sistema físico, tal como se demostró en el proceso de simulación, puede generar reducciones importantes en los costos y evaluar el impacto de la tasa de productos defectuosos en estas prioridades competitivas.
Una de las herramientas de ayuda en la mejora de sistemas de producción es la simulación. Gracias a la existencia actual de paquetes computacionales avanzados es posible abordar la modelización de sistemas complejos de manufactura y probar, bajo la experimentación, el impacto de una decisión en los indicadores de desempeño. Sin embargo, el trabajo computacional que exige la construcción del modelo de un sistema productivo, aun en una pequeña empresa, puede tornarse inmanejable cuando el número de factores influyentes en las variables de respuesta es alto. En este caso, la simplificación de los experimentos de simulación a través de técnicas avanzadas, como la bifurcación secuencial, permite al investigador un ahorro importante en el esfuerzo computacional sin comprometer la confiabilidad de los resultados.
Finalmente, se considera hacia futuro iniciar nuevas investigaciones mediante el empleo de la simulación discreta como marco de trabajo en torno al mejoramiento de las demás áreas funcionales claves (ventas, financiera, etc.) de las Pymes metalmecánicas, como complemento a la metodología de mejoramiento propuesta.
Agradecimientos
Este trabajo fue apoyado por Colciencias (proyecto 1119-0817306419) y la Universidad Nacional de Colombia, mediante la financiación de la investigación "Modelo, procedimientos y soluciones informáticas para elevar el nivel de efectividad de los sistemas de producción de Pymes metalmecánicas. Aplicaciones al subsector 381 de la región Caldas".
Bibliografía
Anderson, J.C., Cleveland, G., Schroeder, R., Operation Strategy: A literature review., Journal of Operations Management, Vol. 8, No. 2, 1989, pp. 1-26. [ Links ]
Avella, L., Fernández, E., Vázquez, C. J., Proceso de planificación y contenido de la estrategia de producción., Papeles de Economía Española, No. 78-79, 1999, pp. 161-178. [ Links ]
Banks J., Carson, J., Barry, L. N., Nicol, D., Discrete-Event System Simulation., 4a Edicion, Prentice Hall, Nueva York, 2004. [ Links ]
Bettonvil, B., Detection of Important Factors by Sequential Bifurcation., Tilburg University Press, Tilburg, The Netherlands, 1990. [ Links ]
Corbett, C., Wassenhove, L. V., Trade-offs? What trade-offs? Competence and Competitiveness in Manufacturing Strategy., California Management Review, Vol. 35, 1993, pp. 107. [ Links ]
Domínguez Machuca, J. A., Álvarez Gil, M. J., Domínguez Machuca, M.,A., García González, S., Ruiz Jiménez, A., Dirección de Operaciones. Aspectos tácticos y operativos en la producción y los servicios., Editorial Mc-Graw Hill, Madrid, 1995. [ Links ]
Gaither, N., Frazier, G., Administración de la Producción y Operaciones., 8ª Edición, Thompson Editores, México, D.F., 2000. [ Links ]
Garvin, D. A., Manufacturing Strategy Planning., California Management Review, Vol. 35, No. 4, 1993, pp. 38-46. [ Links ]
Giraldo, J. A., Sarache, W., Castrillon, O., Gestion de la producción: una aproximación conceptual., 1a ed., Bogotá, Unibiblos, 2008, pp. 35-36; 298-315; 103-112. [ Links ]
Giraldo, J. A., Sarache, W., Castrillon, O. D., Mejoramiento de los outputs de fabricación plazo y costo en el sistema de producción de una pyme metalmecánica mediante simulación de eventos discretos., XVIII Simposio Colombiano de Estadística. Estadística en la industria y los negocios, Cartagena, 2008. [ Links ]
Hayes, R. H., Schemner, R. W., ¿How you should organize manufacturing?., Harvard Business Review, Vol. 55, No. 1, 1977, pp. 105-119. [ Links ]
Hayes, R. H., Weelwright, S.C., Restoring our competitive edge., John Wiley, New York, 1984. [ Links ]
Heizer, J., Render, B., Dirección de la producción. Decisiones tácticas., 5ª. Ed., Editorial Prentice Hall, Madrid, 2001. [ Links ]
Zhou, H., Cheung, W., Leung, L.C., Minimizing weighted tardiness of job-shop scheduling using a hybrid genetic algorithm., European Journal of operational Research, Volume 194, Issue 3, May 2009, pp. 637-649. [ Links ]
Ibarra Mirón, S., Modelo y procedimientos para el análisis y proyección competitiva de Unidades Estratégicas de Fabricación en empresas manufactureras cubanas.m Tesis Doctoral. Universidad Central "Marta Abreu" de Las Villas, Santa Clara, Cuba, 2003. [ Links ]
Kelton, W. D., Law, A. M., Simulation Modeling and Analysis., 3a Edicion, Ed. McGraw-Hill, Singapore, 2007. [ Links ]
Kleijnen, J.P.C., Response surface methodology for constrained simulation optimization: An overview., Modell. Pract. Theory, 2007. doi:10.1016/j.simpat.2007. [ Links ]
Krajewski, L., Ritzman, L., Administración de Operaciones. Estrategia y Análisis., 5ª Edición, Prentice Hall, México, D.F., 2000. [ Links ]
Su, L-H., Chang, P-Ch., Lee, E. S., A heuristic for scheduling general job shops to minimize maximum lateness., Mathematical and Computer Modelling, Vol. 27, No. 1, January 1998, pp. 1-15. [ Links ]
Miller, S., Make your plant managers job manageable., Harvard Bussiness Review, No. 1, January - February, 1983, pp. 69-74. [ Links ]
Miltenburg, J., Manufacturing Strategy.,. Productivity Press, Portly, Oregon, 2004. [ Links ]
Osorio Gomez, J. C., Castrillon Montenegro, O. E., Toro Cardona, J. A., Hierarchical production planning model in flexible job shop including a preemption and sequence-dependent setup times.,Ing. Investig., May/Aug, 2008, Vol.28, No.2, pp. 72-79. [ Links ]
Roshanaei, V., Naderi, B., Jolai, F., Khalili M., A variable neighborhood search for job shop scheduling with set-up times to minimize makespan., Future Generation Computer Systems, In Press, Corrected Proof, 8 February, 2009. [ Links ]
Sarache, W., Cárdenas, D. M., Giraldo, J., Procedimiento para la definición y jerarquizacion de prioridades competitivas de fabricación: aplicaciones en la industria metalmecánica.,Revista Ingeniería y Competitividad., Vol.7, No.2, 2005, pp. 84-91. [ Links ]
Sarache, W., Cárdenas, D. M., Giraldo, J., Procedimiento para evaluar la estrategia de manufactura: aplicaciones en la industria metalmecánica.,Cuad. Adm., Vol.20, No.33, 2007, pp.103-123. [ Links ]
Schroeder, R., Administración de operaciones. Toma de decisiones en la función de operaciones., 3ª Edición. Editorial Mc-Graw Hill, México, D.F., 2003. [ Links ]
Shannon, E. R., Simulación de Sistemas., 1a Ed. Editorial Trillas, México, 1988. [ Links ]
Skinner, W., Focused Factory,. Harvard Business Review (May-June), 1974, pp. 111-120. [ Links ]