Introduction
Global energy consumption has increased considerably in recent years due to the substantial growth of the global population and industrial development. As a result, the demand for transportation fuels has significantly increased (Bhoi et al., 2020). The development of renewable energy has played an important role in meeting demands and mitigating the dependence on fossil fuels, as they are non-renewable and unsustainable and their use increases the emissions of greenhouse gases (GHG) into the atmosphere, which causes global climate change. Residual biomass has great potential for use in the synthesis of renewable energies because it is found in large quantities, it is available and cheap, and it is ecological and sustainable (Rasid et al., 2020).
Several mechanisms exist through which biomass can be converted into renewable energy sources, such as gasification to produce gaseous fuels or pyrolysis or hydrothermal liquefaction to generate liquid fuels. Pyrolysis can be carried out at ambient pressure. As a result, biomass transformation into liquid fuels through pyrolysis has become very attractive (Hu and Gholizadeh, 2019). Pyrolysis is the thermochemical decomposition of biomass in the absence of oxygen at temperatures between 300 and 700 °C. From this process, liquid bio-oil, non-condensable gases, and solid biochar are obtained (Brassard et al., 2017). Non-condensable gases can be used to provide energy to the pyrolysis process. Catalytic Fast Pyrolysis (CFP) is commonly used to transform biomass into high-quality bio-oil, deoxygenating the H2O, CO, and CO2 vapors formed during the process (Chen et al., 2019).
Oil palm (Elaeis guineensis) is the world's main source of vegetable oil, and it is produced principally by Malaysia and Indonesia. Oil palm industry residues constitute the biggest source of biomass in Malaysia, produced in large quantities throughout the year, but only a small fraction is converted into value-added products. Colombia is the second largest producer outside Southeast Asia and the largest producer in South and Central America (Onoja et al., 2019; Rivera-Méndez et al., 2017). African Palm Husk (APH) is produced as a result of the extraction of palm oil and is a biomass available in large quantities to be transformed. Many efforts have been made to take advantage of solid waste from the palm oil industry. Some studies involve the pyrolysis of this biomass using TG-MS, catalytic pyrolysis with low-cost catalysts, conversion of oil palm biomass to hydrogen via gasification reaction in supercritical water, metal oxide-catalyzed hydrothermal liquefaction of oil palm biomass, among others (Salema et al., 2019; Ro et al., 2018; Kelly-Yong et al., 2007; Yim et al., 2017).
It has become essential to know the effect of heavy metals as catalysts in the pyrolysis of metal-impregnated biomass, as well as their distribution in pyrolysis products, in order to find a suitable way of using them (Han et al., 2018). The effect of metallic salts as catalysts in this process has been studied by several authors (Zhao et al., 2017; Cao et al., 2020). Moreover, metal (Ru/Fe) impregnated banana pseudo-stem (Kumar et al., 2019), and copper and iron salts as additives in wood pyrolysis (Edye et al., 1992) have been studied.
Due to its advantages, biomass has gained interest as a green renewable energy. Lignocellulosic biomass is composed of cellulose (32-45%), hemicellulose (19-25%), and lignin (14-26%), which usually makes for very complex thermal decomposition profiles (Kaur et al., 2018; Han et al., 2018). The combination of thermogravimetric analysis coupled with mass spectrometry (TGA-MS) appears to provide a deeper insight into the identification and quantification of devolatilization products. One of the main advantages of TGA-MS is that it can afford real-time and sensitive detection of evolved gases, which is an important and often difficult task in many thermal applications (Malika et al., 2016).
In this work, the effect of FeSO4 as a catalyst on the devolatilization kinetics of APH and its product distribution at 10 and 100 K/min heating rates were studied using the TG-MS simultaneous analysis technique, as a continuation of a previous study on APH devolatilization by TG-MS in the absence of a catalyst (Albis et al., 2018). Kinetics parameters obtained using TGA were fitted to the Distributed Activation Energy Model (DAEM).
Methodology
Materials
The APH was obtained from a biodiesel plant in the municipality of Santa Marta, Magdalena, Colombia. Biomass was ground (particle size < 200 mm) and stored in a desiccator for further use.
Sample preparation
An aqueous solution of FeSO4 was prepared by dissolving 2 000 g of the salt at 75% in 100 ml of water to obtain a final concentration of 15 mg Fe/ml. The prepared APH was added to the solution in the adequate volume, and the suspension was stirred for 2 h. Then, the sample was dried at 80 °C for 2 h, and thereafter for 2 h at 105 °C. The final concentration of FeSO4 in the biomass was 1,5% by weight.
Thermogravimetric Analysis (TGA)
Thermogravimetric analysis was performed using a TA instruments TGA 2950 thermogravimetric analyzer. Control and acquisition of experimental data were carried out via the Universal Analysis software. The procedure for this analysis was the same as that used in the previous study (Albis et al., 2018).
Distributed Activation Energy Model
The DAEM is a multiple reaction model widely used in the pyrolysis of lignocellulosic biomass. This model assumes that the decomposition mechanism takes a large number of independent, parallel, first-order, or n th -order reactions with different activation energies, reflecting variations in species' bond strengths. The difference in activation energies can be represented by a continuous distribution function (Cai et al., 2014). As described in Albis et al. (2018), in this model, the mass conversion rate is represented by several numbers of reactions that share the same frequency factor (Aj), with an activation energy distributed in Gaussian form. A media activation energy E 0 j and a standard deviation of the activation energy (oy) are part of the model represented by Equations (1) and (2).
Where, according to Albis et al. (2018):
Y
calc
represents the conversion rate of the sample or signal strength, M is the number of reactions or pseudocomponents of the sample,
C
j
is a proportionality constant, X
j
is the unreacted fraction of the material represented by the j-
th
kinetic equation, and is the rate of production or consumption of j, which can be calculated as:
where are the solution for
dx
j
/dt at time
t,
and the value of the energy of activation is E.
Equation (2) was solved using MATLAB, as described by Albis et al. (2014).
Results
Thermogravimetric Analysis (TGA)
The TG and DTG of the samples of APH and APH + 1% FeSO4 at temperature rates of 10 and 100 K/min are shown in Figures 1a and 1b, respectively. In Figure 1, four events are observed: the first is related with water release at temperatures below 393 K; the second, at temperatures between 393 and 475 K, which approximately corresponds to the first thermal decomposition; followed by the main pyrolytic event, which shows two peaks; and, finally, the last event is a slow-rate decomposition.
In Figure 1a, a displacement to the right with increased heating rate from 10 to 100 K/min is noted in the thermogram in both cases, i.e., in the absence and presence of the catalyst, related to a small increase in sample weight loss. A similar percentage of char reported in the absence of the catalyst (Albis et al., 2018) was also observed in its presence, which is within the limits of experimental uncertainty. This means that the presence of the catalyst does not affect the percentage of carbonization at either of the two heating rates evaluated.
In the main pyrolytic event, the first peak is associated with hemicellulose decomposition, and the second one with the disintegration of cellulose. In Figure 1b, a difference in the formation of peaks in the presence of FeSO4 is observed, which is related to an increase in the second pseudo-component (corresponding to hemicellulose) within the DTG peak. This peak is higher in the pyrolytic event than the hemicellulose peak for the APH pyrolysis in the absence of the catalyst at the heating rates studied.
The presence of FeSO4 leads to a hemicellulose reduction in the DTG peak temperature at heating rates of 10 and 100 K/min. This behavior suggests a catalytic effect that causes the pyrolytic process to start earlier. In previous studies, it was found that the promoting effects of FeSO4 were noticeable in the hydrolysis of microcrystalline cellulose -an 84,14% conversion was obtained. It was also found that the depolymerization and hydrolysis of biomass remains active in the presence of metals that lower the degradation temperature of the biomass (Tao et al., 2010). This shows the capability of catalysts of initiating pyrolysis reactions at lower temperatures.
Fitting to the DAEM
In Figure 2, the fitting of the DAEM in the presence of the catalyst at heating rates of 10 and 100 K/min is shown. Given the number of peaks, Figure 1b suggests the use of at least four pseudo-components. Consequently, the DAEM with four pseudo-components is used to illustrate the experimental data in this study.
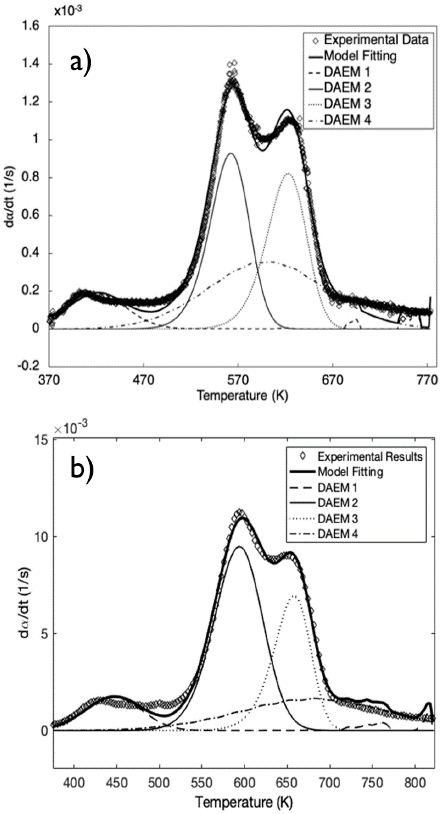
Source: Authors
Figure 2 Fitting of the DAEM with four pseudo-components for APH + 1% FeSO4 at a) 10 K/min and b) 100 K/min
The fitting of the data regarding the conversion rate to the DAEM with four pseudo-components for pyrolysis of APH with FeSO4 heated at 10 and 100 K/min is shown in Table 1. In comparison with a previous study (Albis et al., 2018), the results in Table 1 show that the catalytic effect of FeSO4 affects mainly the second and fourth pseudo-components, identified as hemicellulose and lignin, reducing their average activation energies and their corresponding standard deviations. This behavior explains the reduced starting temperature for the pyrolysis process of APH in the presence of a catalyst: reduction of the activation energy increases the decomposition rate of these compounds, and reduction in the standard deviations of the activation energy causes these components to have a narrow temperature range. For the third pseudo-component, identified as cellulose, the catalytic effect of FeSO4 enhances the standard deviation of the activation energy, which produces a broad temperature range. Moreover, the proportionality constant decreased for the first, second, and third pseudo-components, but increased for the fourth one. On the other hand, the values of the frequency factors remained within the range of values reported for all pseudo-components. Prior studies have reported the catalytic effects of FeSO4 in the decomposition of lignin in wood pyrolysis (Edye et al., 1992), as well as the catalytic effects of ferric sulfate in hemicellulose pyrolysis (Albis et al., 2018).
Table 1 DAEM parameters with four pseudo-components for APH + 1,5% FeSO4 at heating rates of 10 and 100 K/min
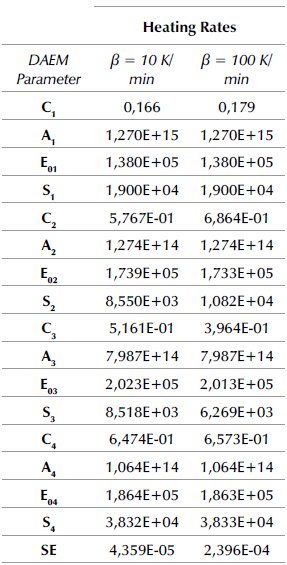
Source: Authors
It was found that, in comparison with the previous study (Albis et al., 2018), the activation energy for the first pseudo-component (Ea = 1,38E+5 kJ/mol), identified as extractives, remained the same in the absence and presence of the catalyst for the heating rates studied. The activation energy for the second pseudo-component, identified as hemicellulose, went from Ea = 1,77E+05 kJ/mol in the absence of the catalyst to Ea = 1,739E+05 kJ/mol and Ea = 1,733E+05 kJ/mol in the presence of FeSO4 at heating rates of 10 and 100 K/min, respectively. Furthermore, the activation energy for the third pseudo-component, identified as cellulose, went from Ea = 2,04E+05 kJ/mol in the absence of the catalyst to Ea = 2,023E+05 kJ/mol and Ea = 2,013E+05 kJ/mol in the presence of FeSO4 at 10 and 100 K/min, respectively. The activation energy for the fourth pseudo-component, identified as lignin, went from Ea = 1,95E + 05 kJ/mol in the absence of the catalyst to Ea = 1,864E+05 kJ / mol and Ea = 1,863E+05 kJ/mol in the presence of FeSO4 at 10 and 100 K/min, respectively. The decreased activation energy shows the catalytic effect of FeSO4 on APH pyrolysis.
A previous study on pyrolysis of banana pseudo-stem found that, in comparison with raw biomass (Ea =116,22 kJ/mol), samples impregnated with FeSO4 have a lower activation energy (Ea = 86,78 kJ/mol). The catalytic effect lowers the activation energy, thus enhancing the reaction rate with modified reaction pathways (Kumar et al., 2019).
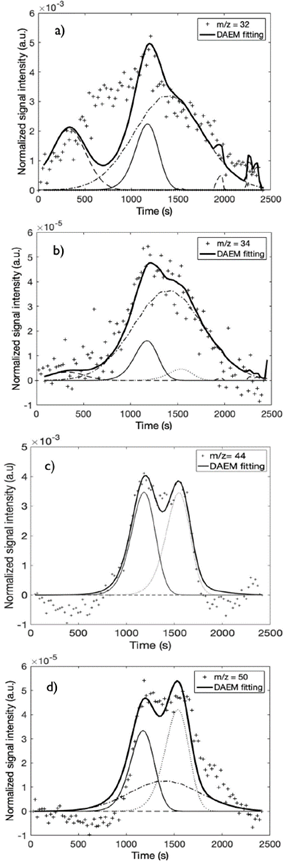
Source: Authors
Figure 3 Fitting of the DAEM with four pseudo-components of selected m/z signal intensities: a) m/z = 32, b) m/z = 34, c) m/z = 44, d) m/z = 50 of APH + 1% FeSO4 at a 10 K/min heating rate
Mass spectrometry
Figures 3 and 4 show the fitting of the DAEM with four pseudo-components for some of the m/z ratios at heating rates of 10 and 100 K/min, respectively. The fit for all the m/z curves at the heating rates studied is supplied in the complementary material.
To analyze the effect of the catalyst, the data obtained at the 10-K/min heating rate is used because, due to the high speed, very few points were obtained in the areas of interest at 100 K/min (Figure 4). Table 2 shows the mass spectrometric intensities selected for kinetic evaluation and its presence in the main thermal events at heating rates of 10 and 100 K/min.
Table 2 m/z obtained for the kinetic study and its presence in the main thermal event at heating rates of 10 and 100 K/min
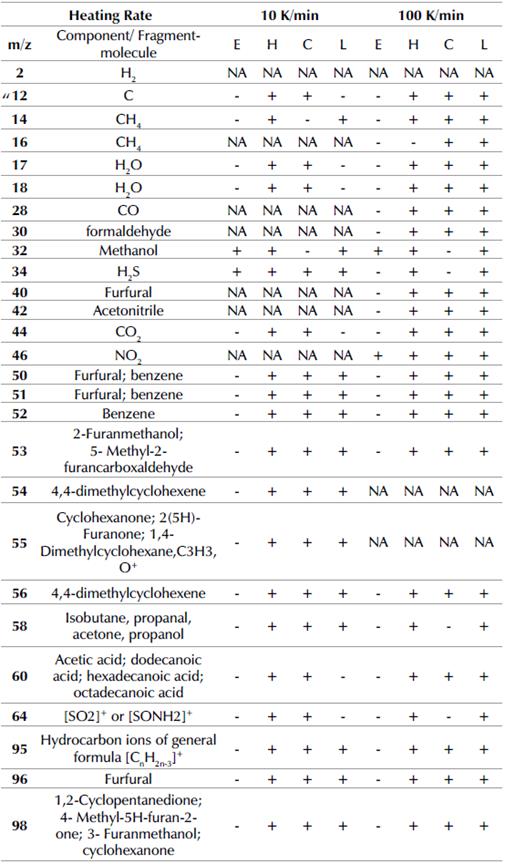
E= Extractives ; H= Hemicellulose ; C= Cellulose ; L= Lignin ; NA= Not-
Source: Authors
At the heating rate of 10 K/min, the fragments associated with m/z = 2, 16, 28, and 40 did not evolve during pyrolysis in the presence of the catalyst. The signal intensities m/z = 12, 14, 17, 32, 34, 44, 50, 51, 55, 58, 60, and 98 for APH pyrolysis in the presence of FeSO4 were lower than the signals corresponding to the absence of the catalyst (Albis et al., 2018). These signals were assigned to methane (m/z =12 and 14), water (m/z = 17), methanol (m/z = 32), hydrogen sulfide (m/z = 34), and carbon dioxide (m/z = 44). The fragments associated with m/z = 50 and 51 were assigned to furfural and benzene. m/z = 55 was assigned to cyclohexanone, 2(5H)-furanone, or 1,4-dimethylcyclohexane, C3H3O+. m/z = 58 was assigned to isobutane, propanal, acetone, or propanol. m/z = 60 was assigned to acetic acid, dodecanoic acid, hexadecanoic acid, or octadecanoic acid, and m/z = 98 was assigned to 1,2-cyclopentanedione, 4-methyl-5H-furan-2-one, 3-furanmethanol, or cyclohexanone.
In addition, the signal intensities of the m/z = 64, 95, and 96 ratios for APH pyrolysis in the presence of FeSO4 were greater than those corresponding to the absence of the catalyst. This behavior suggests that FeSO4 promotes the formation of these compounds. Signals were assigned to the production of [SO2]+ or [SONH2]+ (m/z = 64) (Kuehl and Rozynov, 2003), hydrocarbon ions of general formula [CnH2n3]+ (m/z = 95) (Mjøs, 2004), and furfural (m/z = 96) (Shen et al., 2015). It has been reported that Fe, as a catalyst, removes the oxygenated compounds from the pyrolysis process, thus, improving bio-oil quality and, consequently, increasing the formation of hydrocarbons. Also, the aqueous solution contains aldehydes (Kumar et al., 2019; Ansari and Gaikar, 2019).
Fitting mass spectrometry data to the DAEM
Tables 3 and 4 show the proportionality constant values (cj) for the DAEM with four pseudo-components for the m/z signals detected regarding the pyrolysis of APH + 1% FeSO4 at heating rates of 10 and 100 K/min.
Table 3 Proportionality constants regarding the DAEM with four pseudo-components for m/z signals detected related with the pyrolysis of APH + 1% FeSO4 at a 10 K/min heating rate
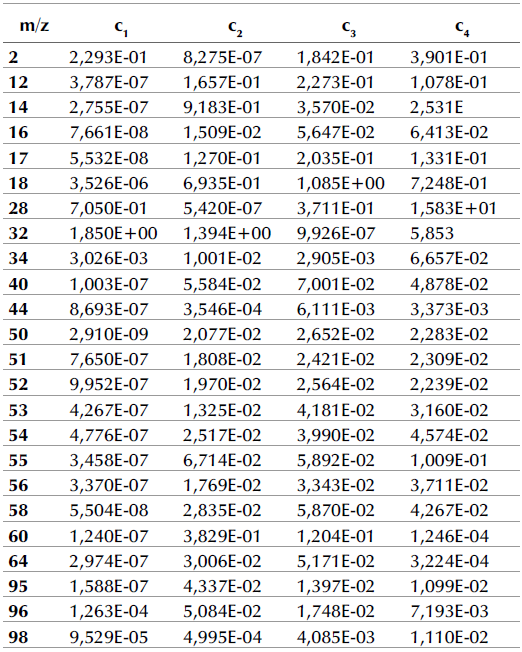
Source: Authors
Table 4 Proportionality constants regarding the DAEM with four pseudo-components for m/z signals detected related with the pyrolysis of APH + 1% FeSO4 at a 100 K/min heating rate
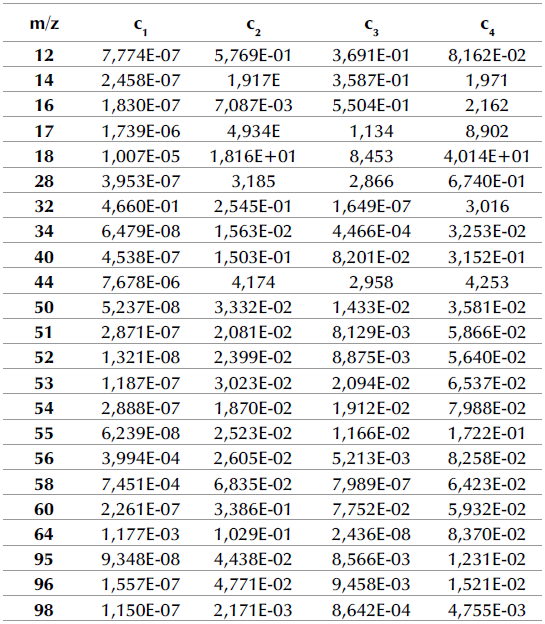
Source: Authors
When comparing these results to those of a previous study (Albis et al., 2018), several observations can be made. In the absence of the catalyst, at a heating rate of 10 K/min, the fragments associated with m/z = 12, 17, 18, 60, and 95 were associated with the thermal decomposition of hemicellulose, cellulose, and lignin. However, in the presence of the catalyst, these fragments were associated only with the thermal decomposition of hemicellulose and cellulose, with the contribution of the thermal decomposition of lignin being almost negligible. In the case of the fragments associated with m/z = 51, 55, and 96, the gases evolved were associated with hemicellulose, cellulose, and lignin decomposition with and without the catalyst. For the m/z ratios described, in the absence of the catalyst, the peak corresponding to the decomposition rate of hemicellulose is lower than that corresponding to the decomposition rate of cellulose. In contrast, in the presence of the catalyst, the peak corresponding to the decomposition rate of hemicellulose is higher than that corresponding to the decomposition rate of cellulose. This, except for m/z = 55, whose main event is associated with the thermal decomposition of lignin. This behavior coincides with the results obtained in the DTG curves described.
Moreover, in the absence of the catalyst, the fragments associated with the m/z = 14, 32, 34, 50, 64, and 98 were associated with the thermal decomposition of all major biomass components, extractives, hemicellulose, cellulose, and lignin. Similarly, in the presence of the catalyst, m/z = 32 was associated with the thermal decomposition of extractives, hemicellulose, cellulose, and lignin. However, for m/z = 64, the presence of FeSO4 changed the m/z signal intensity profiles, and the evolution of this fragment was only associated with the thermal decomposition of hemicellulose and cellulose. In the presence of FeSO4, m/z = 50, 34, and 98 were associated with the thermal decomposition of hemicellulose, cellulose, and lignin, but not extractives. Finally, the evolution of the fragment of ratio m/z = 14 was associated with the thermal decomposition only of hemicellulose and lignin in the presence of FeSO4. For the aforementioned m/z ratios, in the absence of the catalyst, the peak corresponding to the decomposition rate of cellulose is higher than that corresponding to the decomposition of hemicellulose, which was higher than the peak corresponding to the decomposition of lignin. In contrast, in the presence of the catalyst, the peak corresponding to lignin decomposition is higher than those corresponding to hemicellulose and cellulose decomposition, with the contribution of the thermal decomposition of cellulose being smaller or negligible in some cases, except for m/z = 64 for which the contribution of the thermal decomposition of lignin is negligible.
For all m/z ratios, the catalytic effect of FeSO4 on hemicellulose and lignin can be evidenced as a displacement to the left of the DAEM fit for the thermal decomposition of hemicellulose and lignin: the peaks go from being broad in the absence of the catalyst to becoming narrow in its presence. This means that decomposition occurs at lower temperatures (increasing the decomposition rate), and in a shorter period of time. Additionally, the thermal decomposition of cellulose in the absence of the catalyst occurs in a short period of time and it takes longer in its presence.
Conclusions
This work studied the effect of FeSO4 on the APH pyrolysis process. It was found that the catalyst mainly affects the thermal decomposition of hemicellulose and lignin and that FeSO4 promotes the formation of compounds for ratios m/z = 64, 95, and 96 -corresponding to fragments of molecules, such as SO2, hydrocarbon ions of general formula [CnH2n3]+, and furfural, respectively- due to the iron deoxygenation effect, which improves hydrocarbon formation. The m/z ratios of the gases evolved in the presence of the catalyst were compared with the signals corresponding to its absence. A difference in the formation of peaks shows an effect on the rate of production in the presence of FeSO4, thus increasing the decomposition rate in the case of hemicellulose and lignin, and decreasing it in the case of cellulose.