Introducción
La fricción en ortodoncia se produce por el contacto directo entre el bracket, el alambre y la ligadura. La fricción reduce la eficiencia en los tratamientos ortodóncicos debido a que del total de fuerza entregada gran parte se invierte en vencer la fricción bracket/alambre/ligadura, por lo que se requiere aplicar una mayor fuerza para lograr el movimiento dental 1.
Los brackets de autoligado son aditamentos libres de ligadura ya que poseen un dispositivo mecánico para encajar el alambre en la ranura; es decir, tienen un componente fijo y un componente móvil que sujeta el arco 2. Los brackets metálicos de autoligado reducen sustancialmente la fricción en las primeras etapas del tratamiento de alineación y nivelación 3; se presentan como una alternativa al sistema de brackets metálicos convencionales, y ofrecen una mayor eficiencia en el tratamiento al generar una significativa reducción de la fuerza friccional en la interfase bracket-alambre, y por lo tanto disminuyen la duración del tratamiento, así como el tiempo en el sillón odontológico 4-5.
Los brackets cerámicos están compuestos por cristales de óxido de aluminio, ya sea en forma policristalina o monocristalina 6. Los brackets policristalinos se componen de partículas de óxido de aluminio irregulares fusionadas a temperaturas de 1860ºC. Los brackets monocristalinos se componen en su mayoría del mismo material de los policristalinos, pero el proceso de fabricación se hace con técnicas de corte ultrasónico o corte de diamante, procedimientos más especializados y costosos. El material se fusiona por encima de los 2400ºC pero a diferencia de los policristalinos su atemperamento se produce en un medio controlado para formar un solo cristal de óxido de aluminio, sin imperfecciones y con apariencia de cristal traslúcido 7.
Los brackets cerámicos de autoligado 8 se desarrollaron con el propósito de mantener la característica de autoligado de los brackets metálicos convencionales, pero con el agregado estético que ofrece la cerámica 5,sin embargo, poco se conoce de sus propiedades físicas. En consecuencia, es necesario investigar acerca de la resistencia que ofrecen a la fricción. Teniendo en cuenta la relación entre autoligado y menor resistencia friccional, se debe establecer la diferencia en resistencia friccional de los brackets cerámicos de autoligado y los convencionales cerámicos.
El método de elementos finitos ha demostrado ser una herramienta útil en el análisis de estrés de los brackets cerámicos sometidos a diversas fuerzas. Además, esta metodología reduce la necesidad de prototipos y experimentos de laboratorio y permite más opciones de diseño para ser probado en una determinada cantidad de tiempo 9.
Por lo tanto, esta investigación tuvo como objetivo determinar la diferencia en la resistencia friccional entre los brackets cerámicos convencionales y brackets cerámicos de autoligado, cuando se utilizan diferentes inclinaciones del bracket y diversas aleaciones y dimensiones del alambre, a través del método de elementos finitos, de modo que pueda predecirse su aplicabilidad y pertinencia.
Materiales y métodos
Método Experimental
Se usaron dos tipos de brackets para dientes laterales superiores, cerámicos convencionales (zafiro monocristalino) (Inspire Ice®; Ormco, Orange, CA, USA) con ranura de 0,022” x 0,028” y brackets cerámicos (alúmina policristalina) de autoligado de torque estándar (Damon Clear®; Ormco, Orange, CA, USA) con ranura de 0,022” x 0,028”, dado que tienen características de prescripción similares (bracket convencional: torque +8o, angulación +9º, y rotación 0o; bracket autoligado: torque +6o, angulación +9o, y rotación 0o). Se utilizaron además alambres Ormco de acero inoxidable, niquel titanio (NiTi) y beta-titanio, cada aleación en las dimensiones 0,016”, 0,017” x 0,025” y 0,019” x 0,025”. Para los brackets cerámicos convencionales se utilizaron ligaduras de la casa comercial Ormco, elásticas y metálicas (0.010”).
Las combinaciones se montaron en un dispositivo reportado previamente 10, y adaptado a una máquina INSTRON 3345 con una celda de carga de 10 N ± 0.01 a cero grados, a una velocidad de 5mm/min durante 2 min. Se realizaron 810 deslizamientos en total, con 27 combinaciones posibles de alambre, bracket y ligadura. La calibración del modelo es descrita en una publicación realizada por el mismo grupo de investigación 10. Resumiendo, se midieron brackets convencionales pre-ajustados, arcos redondos de acero inoxidable, y ligaduras metálicas inoxidables usando un estereoscopio con una magnificación de 8X y 80X y una tolerancia de ± 5 mm, asistida por un programa de análisis de imagen (NIS 3.1 Element, Nikon). Se construyó un modelo asistido por computador del bracket con medidas microscópicas (Solid Edge 18). Igualmente, con un microscopio (Eclipse X20 LV100) se midió la rugosidad de superficie del slot y el arco, calculando la rugosidad promedio entre los picos y valles observados sobre la superficie de los materiales. El FEM se validó comparando su resistencia friccional con la del modelo experimental con una confiabilidad del 95% mediante una prueba Z. No se observó diferencia estadísticamente significativa entre los dos métodos (p = 0.7493). De esta manera, se validó el FEM para estudiar fuerzas friccionales en diferentes combinaciones de brackets y arcos. Las propiedades mecánicas de los brackets y alambres tenidas en cuenta en el modelo fueron 205 y 190 GPa, 200 y 193 MPa, y 0,31 y 0,3 (Poisson’s Ratio), respectivamente 10-11.
El montaje de los brackets y los deslizamientos realizados durante este estudio fueron realizados por un sólo operador, previa calibración mediante una prueba piloto de fijación del bracket, forma y fuerza de ligado. Los datos se procesaron por medio del programa Excel y se calcularon medidas descriptivas (media e intervalo de confianza de 95%, de todas las mediciones realizadas). Las pruebas estadísticas se realizaron por medio de un programa estadístico (SPSS version 24.0, Chicago, IL).
Modelación asistida por computador (CAD)
Se elaboraron modelos CAD de los brackets a partir de fotografías obtenidas por medio de un estereoscopio (Nikon, Japón) SMZ 1000 a 20X, una cámara y un software para análisis de imágenes NIS-Elements-D (Nikon, Japón). Por medio de estas fotografías, que representaron los diferentes lados de los brackets, se construyeron los modelos CAD, utilizando el software SOLIDEDGE (versión 18) como se muestra en la Figura 1. Estos modelos fueron posteriormente simulados por elementos finitos.
Simulación por el método de elementos finitos (MEF).
Cada una de las combinaciones bracket, alambre, ligadura fueron simuladas por MEF usando el software Autodesk Simulation de Multyphysics con mallas tetragonales y haciendo fijación de todos los grados de libertad en los puntos en la base del bracket (Figura 2).
La medida de la resistencia friccional se asumió como el esfuerzo cortante en las paredes y/o fondos del bracket de acuerdo con la simulación por MEF que arroja valores en megapascales (Mpa). Se aplicó el valor de la media máxima de la resistencia a la fricción (MRF) del método experimental sobre las paredes y/o fondos del slot con angulaciones de 0°, 7° y 13°.
Este estudio experimental in vitro realizado en modelos no requiere aprobación de un comité de ética institucional.
Resultados
Fase Experimental
En la tabla 1 se presentan los resultados experimentales de los deslizamientos, señalando la fuerza friccional promedio acompañada de la desviación estándar y el intervalo de confianza del 95%. La mayor resistencia friccional se encontró en la combinación bracket convencional con ligadura elástica y alambre beta-titanio 0,019” x 0,025” (0,737 N), y la menor en la combinación bracket convencional con ligadura elástica y alambre de acero inoxidable 0,019” x 0,025”. (0,002 N). En términos generales, la aleación de mayor resistencia friccional fue beta-titanio y la de menor fue la de acero inoxidable.
Angulación
En la figura 3 se presentan los resultados de simulación por MEF para cada angulación.
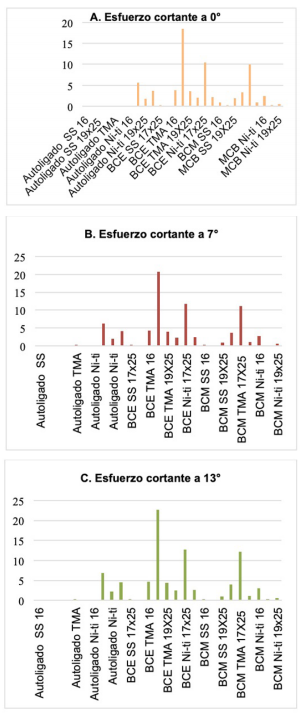
Figura 3 (A, B,C). Distribución de la máxima resistencia friccional en términos de esfuerzo cortante (megapascales) en las diferentes angulaciones y combinaciones bracket/alambre/ligadura.BCE: bracket convencional con ligadura elástica. BCM: bracket convencional con ligadura metálica.
Desde el punto de vista de las tres angulaciones (0°, 7° y 13°), la angulación de 13° fue la que presentó mayores valores de MRF, seguido por la de 7°.
En las tres angulaciones, la combinación con mayor resistencia friccional fue el bracket convencional con ligadura elástica y alambre beta-titanio 0,017” x 0,025”; en la angulación de 0°, la combinación bracket autoligado con beta-titanio 0.017” x 0.025” resultó con el menor comportamiento friccional, mientras que en las angulaciones de 7° y 13° la menor resistencia friccional se encontró al combinar el bracket convencional con ligadura elástica y acero 0,019” x 0,025”.
Calibre
De los tres calibres analizados (0,016”, 0,017” x 0,025”, 0,019” x 0,025”) la mayor resistencia friccional la presentó el calibre 0,017” x 0,025” seguido por el calibre 0,016”.
Con los tamaños 0,016” y 0,017” x 0,025” la combinación con mayor resistencia friccional fue el bracket convencional con ligadura elástica y aleación de beta-titanio a 13º de angulación. La menor fue la combinación bracket autoligado con aleación beta-titanio a 0°.
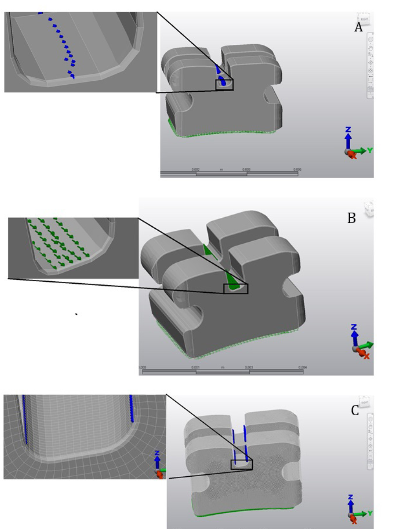
Figura 4 Puntos de aplicación de la fuerza para la simulación por MEF. A. Calibre 0,016”. B. Calibre 0,017” x 0,025”. C. Calibre 0,019” x 0,025”
Con el calibre 0,019” x 0,025” la combinación con mayor comportamiento friccional también fue el bracket convencional con ligadura elástica y aleación beta-titanio a una angulación de 13°, pero la menor fue la combinación bracket convencional con ligadura elástica y aleación de acero a 0°.
La figura 4 presenta los puntos de aplicación de la fuerza en los calibres de alambre estudiados. Se observa que un mayor calibre de alambre (0,019” x 0,025”), no es igual a mayor área de contacto entre bracket y alambre.
Aleación
De acuerdo al tipo de aleación, beta-titanio presentó la mayor resistencia friccional seguido por NiTi.
Con el alambre de acero inoxidable la mayor resistencia friccional fue encontrada al combinar bracket convencional con calibre 0,016” a 13º de angulación; y la menor se presentó con la combinación convencional, calibre 0,019” x 0,025” a 0°.
Con las aleaciones beta-titanio y NiTi el mayor comportamiento friccional fue similar; en los dos se presentó al combinar bracket convencional/calibre 0,017” x 0,025”/ angulación13°, sin embargo, la menor resistencia friccional varió entre las dos aleaciones. En la categoría beta-titanio el menor valor lo presentó la combinación bracket autoligado/ calibre 0,017” x 0,025” /angulación 0° y para NiTi el menor resultado se obtuvo al combinar autoligado/calibre 0,016” /0° de angulación.
Bracket
Comparando el comportamiento friccional entre los tipos de brackets, el mayor resultado lo obtuvo el bracket convencional /ligadura elástica, mientras que el menor fue para autoligado.
Al insertar ligadura elástica al convencional el mayor valor friccional resultó con beta-titanio 0,017” x 0,025” a 13° de angulación y el menor con acero 0,019” x 0,025” a 0°. De otro lado, cuando dicho bracket se coordinó con ligadura metálica, la mayor resistencia friccional se logró con beta-titanio 0,017” x 0,025” a 13° y la menor con acero 0,017” x 0,025” a 7°.
En la categoría de autoligado la mayor resistencia friccional resultó con Ni-Ti 0,017” x 0,025” y 13° de angulación, mientras que la menor se registró con beta-titanio 0,017” x 0,025” a 0°.
En términos generales, el mayor comportamiento friccional se observó en la coordinación bracket convencional/ ligadura elástica/ beta-titanio 0,017” x 0,025”/ 13° y la menor, en la combinación bracket de autoligado/ beta-titanio 0,017 x 0,025/ 0°.
Discusión
Los estudios que evalúan la fricción producida por brackets y alambres de ortodoncia divergen ampliamente debido a diversos aspectos: variedad en los métodos de estudio, materiales de diferentes casas comerciales, diversas combinaciones bracket-alambre-método de ligado, medios de prueba (ambiente seco, saliva o sustitutos), y la suma de angulaciones (10, 12). Esto hace que sea difícil comparar los resultados observados en el presente estudio. Además, si se trata de investigaciones “in vitro,” es difícil garantizar las mismas condiciones en cada uno de los experimentos, incluyendo la posición específica del alambre con respecto a las paredes de la ranura del bracket y que esta posición sea reproducible en cada deslizamiento, aumentando la susceptibilidad a sesgos 13-16. Todo lo anterior, dificulta contrastar detalladamente los resultados de este estudio con referentes ya publicados. Sin embargo, se realizaron comparaciones con estudios que de alguna manera tuvieran relación con los resultados encontrados en esta investigación.
Con respecto al ángulo los mayores resultados friccionales observados en el presente estudio fueron arrojados por la angulación 13°, seguida por 7°. Hallazgos similares fueron reportados previamente 17,18, señalando que el aumento en la angulación aumenta significativamente la resistencia al deslizamiento. Este concepto se fundamenta en la fricción clásica indicada por algunos autores que argumentan que cuando no hay rotaciones o inclinaciones dentales sólo se observa fricción clásica entre el alambre y el bracket 19. Cuando se introducen angulaciones en esta interfase, la resistencia al deslizamiento es el resultado de este tipo de fricción, sinergizado por la deformación elástica y la deformación plástica 20, que se reporta tres veces mayor en brackets cerámicos 21.
En el presente estudio se encontraron los menores valores de resistencia friccional en la aleación de acero inoxidable 0,019” x 0,025”, resultados similares a los obtenidos por Krishnan y Kumar 21. Este menor comportamiento friccional en la interfase bracket/ alambre se puede explicar a partir de la alta rigidez y superficie lisa del acero inoxidable comparado con otro tipo de aleaciones 22 .
En el presente trabajo se encontró mayor valor friccional para la aleación beta-titanio. Resultados similares fueron observados por Doshi y Bhad 11 cuando evaluaron la resistencia friccional de tres tipos de aleaciones (acero inoxidable, NiTi y beta-titanio) en brackets metálicos, cerámicos convencionales y cerámicos con ranura de oro paladio. Sus resultados muestran que el alambre más friccional fue beta-titanio y el de menor fricción el acero inoxidable. Estos hallazgos también son parecidos a los encontrados por Cacciafesta y colaboradores 22, quienes luego de comparar comportamientos friccionales en brackets metálicos convencionales, de autoligado, y cerámico de autoligado, reportaron mayores valores para la aleación beta titanio. Este fenómeno se podría explicar a partir de la textura superficial rugosa de la aleación, cuyos valores fueron determinantes en los deslizamientos experimentales, con consecuentes resultados en las correspondientes simulaciones por MEF.
El presente estudio muestra que de los tres calibres evaluados la mayor resistencia friccional la presentó el calibre 0,017” x 0,025” y la menor el 0,019” x 0,025”. Este resultado podría explicarse (teniendo en cuenta el MEF) a partir del área de contacto entre el alambre y la ranura del bracket, ya que en la simulación la categoría alambre 0,019” x 0,025”, sólo tuvo contacto en las paredes del slot y no con el fondo del bracket. De igual manera en un alambre redondo, la fuerza se concentró en un área relativamente pequeña del slot del bracket; mientras que el alambre 0,017” x 0,025” aplicó la fuerza sobre las paredes y el fondo de la ranura, aumentando de esta manera el área de contacto, favoreciendo el esfuerzo generado sobre cada una de las posibles combinaciones. Estos resultados pueden estar relacionados con la estructura geométrica de ángulos redondeados y el fondo de la ranura del bracket en forma de semiluna, analizados a partir de las imágenes arrojadas por el estereoscopio. Por lo tanto, se puede decir que visto con MEF, un mayor calibre de alambre (0,019” x 0,025”), no es igual a mayor área de contacto entre bracket y alambre, siendo esto último un factor determinante en la resistencia friccional resultante del sistema ortodóncico (Figura 4). En este sentido, diversos autores 23-26, a partir de pruebas de deslizamiento “in vitro,” y usando diferentes combinaciones de alambres y brackets, han logrado probar que donde existe una mayor área de contacto entre el bracket y el alambre, existe una mayor zona para el desarrollo de fenómenos asociados con la fricción como “stick slip” 5-11, que se refiere al aumento de la resistencia friccional debido al bloqueo mecánico entre las rugosidades de dos superficies en contacto durante el deslizamiento. En contraste, Voudourisa y colaboradores 27 reportaron que el tamaño del alambre asociado con mayor fricción fue el calibre 0,019” x 0,025”, seguido por los alambres 0,018” x 0,018” y 0,020”, enfatizando la indicación de los alambres redondos para biomecánica de deslizamiento de autoligado.
Con respecto al tipo de ligado, al comparar el comportamiento friccional de los brackets cerámico convencional y de autoligado, la mayor representación friccional fue para el bracket cerámico convencional con ligadura elástica y la menor para el de autoligado. Estos resultados corroboran los hallazgos de Kambay y colaboradores 26 quienes encontraron que las cifras más bajas de fricción se observaron en ligaduras de acero inoxidable en comparación con ligadura elásticas. En la literatura se encuentran diversos estudios que comparan la resistencia friccional entre brackets metálicos convencionales y de autoligado 28-30, afirmando que el grado de resistencia a la fricción es proporcional al grado de rigidez de los elementos de sujeción del alambre 30 poniendo de relieve la eficacia de los sistemas de autoligado por la sujeción pasiva del alambre al bracket, lo que se traduce en baja fricción.
Considerando que la geometría del slot del bracket puede ser diferente según la marca comercial (lo cual es determinante en el área de contacto y por ende en la resistencia friccional), los resultados de la presente investigación no son extrapolables a otras marcas comerciales de brackets cerámicos. Lo anterior pone de relieve la necesidad de nuevas investigaciones usando diferentes marcas comerciales de brackets cerámicos convencionales y de autoligado, en un esfuerzo por demostrar científicamente que sistema podría proporcionar fuerzas más óptimas sobre la base de un coeficiente de fricción bajo asociado con la estética.
La presente investigación presenta varias limitaciones. La primera de ellas se relaciona con el diseño experimental “in vitro;” sin embargo, experimentos como este difícilmente pueden ser planteados en estudios clínicos debido a consideraciones éticas. Por otra parte, las propiedades mecánicas de las ligaduras no fueron incluidas en la modelación, lo cual constituye también otra limitación del estudio.
Conclusiones
La resistencia al deslizamiento es directamente proporcional al incremento del ángulo creado entre el bracket y el alambre.
Una mayor área de contacto entre el bracket y el alambre, aumenta la resistencia friccional debido al bloqueo mecánico entre las rugosidades de dos superficies en contacto durante el deslizamiento.
Un mayor calibre no implica una mayor área de contacto entre el bracket y el alambre.
La aleación beta-titanio presenta los mayores valores de resistencia friccional