Services on Demand
Journal
Article
Indicators
-
Cited by SciELO
-
Access statistics
Related links
-
Cited by Google
-
Similars in SciELO
-
Similars in Google
Share
Ingeniería e Investigación
Print version ISSN 0120-5609
Ing. Investig. vol.35 no.1 Bogotá Jan.Apr. 2015
https://doi.org/10.15446/ing.investig.v35n1.46157
DOI: http://dx.doi.org/10.15446/ing.investig.v35n1.46157
C. A. Forero-Nuñez1, J. Jochum2 and F. E. Sierra3
1Carlos Andrés Forero-Nuñez. Chemical Engineer, Universidad Nacional de Colombia, Colombia. Ph.D (c), Universidad Nacional de Colombia, Colombia. Affiliation: Departamento de Ingeniería Mecánica y Mecatrónica, Universidad Nacional de Colombia, Colombia. E-mail: caforeron@unal.edu.co
2Joachim Jochum. Dr.-Ing Electrical Engineer, Department of Chemical Engineering, University of Applied Sciences Hochschule, Germany. Affiliation: School of Aerospace, Transport & Manufacturing, Cranfield Offenburg, Germany. E-mail: jochum@hs-offenburg.de
3Fabio Emiro Sierra Vargas. Mechanical Engineer and M. Sc. Mechanical Engineering, Universidad Nacional de Colombia, Colombia. Dr.-Ing., University of Kassel, Germany. Affiliation: Departamento de Ingeniería Mecánica y Mecatrónica, Universidad Nacional de Colombia, Colombia. E-mail: fesierrav@unal.edu.co
How to cite: Forero-Nuñez, C. A., Jochum, J., & Sierra, F. E. (2015). Effect of particle size and addition of cocoa pod husk on the properties of sawdust and coal pellets. Ingeniería e Investigación, 35(1), 17-23. DOI: http://dx.doi.org/10.15446/ing.investig.v35n1.46157
ABSTRACT
The continuous increase of the world energy demand, the rise of fossil fuels costs, and the strong environmental policies around the globe are some of the reasons for the wood pellets industry increase. However, there are some other available biomass feedstocks capable of being densified for energy production. Among the various options, the use of mixed biomass pellets is becoming remarkable due to the wide variety of species, although more research is needed in order to enhance the mechanical properties of these pellets. This study aims to identify the effect of particle size on the mechanical properties of sawdust and coal pellets when cocoa pod husks are used as an additive. Cocoa pod husks have a similar composition to sawdust and less sulfur and nitrogen than coal. Thus, the use of this additive might decrease the environmental impact during coal pellets combustion. Results show an attractive potential of cocoa pod husks grinds for pellet production, an increase of the durability of coal pellets mixed with this raw material, and similar performance between cocoa pod husks and sawdust pellets. The compression ratio, the compressive and impact resistance varied linearly with the addition of cocoa pod husks.
Keywords: Biomass, coal, cocoa pod husks, densification, pellets, sawdust.
RESUMEN
El incremento en la demanda de energía a nivel mundial, el alza en los precios de combustibles fósiles y las fuertes políticas ambientales son algunas de las razones del crecimiento de la industria de los pellets de madera. Sin embargo, existen otras materias primas disponibles que pueden ser densificadas para la producción de energía. Dadas las diferentes opciones, el uso de pellets mixtos de biomasa se ha convertido en una opción favorable, a pesar de que es necesaria una mayor investigación con el fin de mejorar las propiedades mecánicas de los pellets. Este estudio tiene como objetivo identificar el efecto del tamaño de partícula sobre las propiedades mecánicas de los pellets de aserrín y carbón cuando la cáscara de cacao se usa como aditivo. Las cascaras de caco tienen una composición similar al aserrín y menos contenido de azufre y nitrógeno que el carbón. Por lo tanto el uso de este aditivo puede disminuir el impacto ambiental durante la combustión de pellets de carbón. Los resultados muestran un potencial atractivo para la producción de pellets con cacao molido, un incremento de la durabilidad de los pellets de carbón mezclados con esta materia prima y un rendimiento similar entre los pellets de cacao y aserrín. La relación de compresión, la resistencia a la compresión y al impacto variaron linealmente con la adición de cáscara de cacao.
Palabras clave: Biomasa, carbón, cáscara de coco, densificación, pellets, aserrín.
Received: October 15th 2014 Accepted: November 25th 2014
Introduction
The worldwide energy demand increase, the global warming, and the stronger energy policies around the globe have intensified the research on alternative energy technologies capable of harnessing renewable resources such as wind, solar radiation or biomass. Biomass from a broad diversity of agricultural residues is a major contributor to renewable energy, occupying about 10% of the world total energy consumed (Okeh, Onwosi & Odibo, 2014). Biomass is classified as traditional and modern; it can also be utilized by many conversion technologies such as direct combustion, thermochemical, biochemical and agrochemical processes (Sanchez-Silva, López-González, Villaseñor, Sanchez & Valverde, 2012). Traditional biomass like wood, mainly used for heating and cooking, supports 9.3% of final energy consumption worldwide (REN21, 2013). On the other hand, the modern biomass, consisting of the several derivatives and biofuels obtained from biomass, i.e., bioethanol, biodiesel, syngas, biogas, pellet, or briquettes, supplies about 1% of the world total energy. There are some disadvantages that improved processes need to overcome in order to increase the penetration of biomass technologies in the energy market. As stated by Kaliyan and Morey (2009), biomass is very difficult to handle, transport, store, and utilize in its original form due to the high moisture, irregular shape, and low bulk density. Hence, biomass densification by agglomeration and pressing becomes a valuable alternative to solve these drawbacks. The product that results from densification processes is known as pellets or briquettes. In comparison to biomass in its original form, densified solid biofuels exhibit some advantages like: (1) Efficient biomass storage; (2) Uniform and controlled combustion; (3) Low moisture content; (4) Simplified fuel feeding; (5) Ease in transport and handling; (6) Marketability; and (7) Flexibility in accommodating a variety of feedstock including wastes (Erlich, 2009).
As a consequence of these benefits, wood pellets commercialization has risen exponentially in recent years, moving from 2 to 22.4 million tonnes between 2000 and 2012 (REN21, 2013). Wood pellets are mainly manufactured with residues of timber industries; nevertheless, the rapid growth of the demand is creating a necessity of identifying new raw materials for solid biofuel industry. According to Karkania, Fanara & Zabaniotou (2012), mixed biomass pellets (MBP) have a high potential in enlarging the use of biomass for energy conversion, particularly in central and south European countries. With the exhaustion of biomass residues for wood pellets production (particularly sawdust), the production of MBP is of growing concern for project developers and biomass producers. Hence, several authors have focused on the analysis of alternative raw materials for pellets production, the study of their mechanical properties, and their behavior during thermochemical conversion processes. Karkania et al. (2012) summarized the results obtained after utilization of wood-corn and wood-cotton mixtures. LHVs for these pellets were in the range of 14 to 15 MJkg-1. Kaliyan & Morey (2009) analyzed the densification behavior of corn stover and switchgrass; they studied the effect of compression/densification conditions (particle size, moisture content, and preheating temperature) on the constitutive model parameters. Munawar & Subiyanto (2014) characterized pellets made from solid wastes from oil palm industry. They used oil palm empty fruit bunch, oil palm frond, oil palm shell, and oil palm mesocarp; also, they reported adequate conditions to produce biomass pellets using these resources. Limousy et al. (2013) carried out a study using pellets made of spent coffee grounds blended with pine sawdust in a boiler. Results showed a good combustion efficiency; moreover, the use of blended pellets could be a valuable alternative to replace pure sawdust pellets. Nunes, Matias & Castalao(2014) made an analysis of the state of the combustion models for mixed biomass pellets. They emphasized the possibility to produce mixed biomass solid fuels with sufficient hardness and mechanical durability, as well as heating values close to those of wood pellets.
Cocoa pod husks form about 70% of the cocoa fruit; the husks are generated after opening the pod for removing the cocoa beans (Ofori-Boateng & Teong-Lee, 2013). Commonly, these wastes are unexploited and considered as a disposal problem. They are left to rot on the cocoa plantation producing foul odors and propagating diseases such as black pod rot (Vriesmann, Amboni & Petkowics, 2011). Projects have been performed aiming to establish alternatives for adding value to these residues. Some scientists analyzed the utilization of cocoa pod husks as green solid base catalysts for transesterification of oils (Ofori-Boateng & Teong-Lee, 2013), as a source of proteins (Serra & Ventura, 1999), pectins (Vriesmann et al., 2011) (Vriesmann, Teófilo & de Oliveira, 2012) or other useful chemicals (Mansur, Tago, Masuda & Abimanyu, 2014), and as a raw material of the densification process (Syamsiro, Saptoadi, Tambunan & Pambudi, 2012). This work aims to identify the effect of using cocoa pod husks as an additive to sawdust and coal pellets, and the incidence of particle size on the mechanical properties of mixed biomass pellets made.
Methods and Materials
Raw material characterization
The sawdust was gathered from the wood workshop located at the Universidad Nacional de Colombia; the coal was given by the Servicio Geológico Nacional staff, and the cocoa pod husks were provided by Cimitarra Santander farmers. Cocoa pod husks were air-dried until reaching low moisture content. Air-drying was needed due to the difficulties given during cocoa husks grinding. Figure 1 shows the changes of cocoa husks after drying; the biomass became more brittle making easy to pulverize. Typical dimensions of these husks were 20cm length and 10cm width approximately.
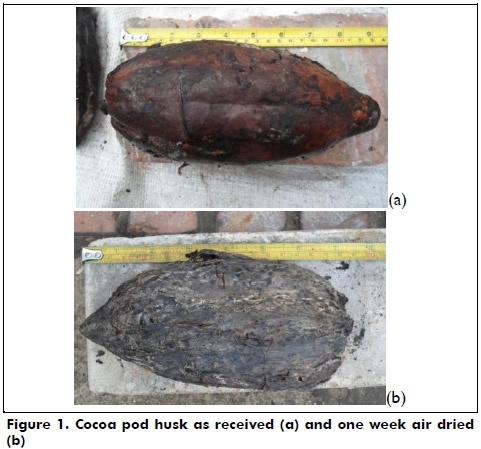
Cocoa pod husks, sawdust, and coal were ground separated using a hammer mill. Proximate analysis was carried out for each raw material; the moisture content was calculated by following the ASTM E871-82 (ASTM, 2013), volatile matter recorded in accordance with ASTM E872 (ASTM, 2013), ash content determined using a furnace as indicated by ASTM E1755-01 (ASTM, 2007), and fixed carbon calculated as balance. Meanwhile, the ultimate analysis was performed. A LECO Truspec CHN Analyzer determined the Carbon, Nitrogen and Hydrogen content according to ASTM D5373-08 (ASTM, 2014), whereas an LECO SC-32 and an S-114 DR analyzer were employed to establish sulfur content by following ASTM D4239-08(ASTM, 2014). The oxygen content was calculated by balance. These tests were performed in the coal laboratory of the Servicio Geológico Colombiano, Bogotá, Colombia.
Experimental design and statistical analysis
The analysis was based on three factors; the particle size (three levels, particles between 4.76 and 1.19mm, intermediate between
1.19 and 0.297 mm, and fines <0.297mm), the base raw material for pellets (two types, coal and sawdust), and the cocoa content in the blend (five levels, 0, 30, 50, 70, and 100%wt). Hence, a factorial design (3x2x5) was adopted as the experimental design in this study. The mean value and tolerance limits of initial and final density were calculated for a 95% confidence level using the Student´s t-distribution (Holman, 2001). Table 1 summarizes the assortment distribution employed in this experiment. The first letter exhibits the code of the particle size (B, I, or F); the second letter is the base raw material, (coal (c) or sawdust (s)). The mass ratio between the base raw material and cocoa husks (ch) is also defined; e.g., the assortment identified by code Icch-30/70 means intermediate particles with a mass ratio 30% coal and 70% cocoa pod husks.
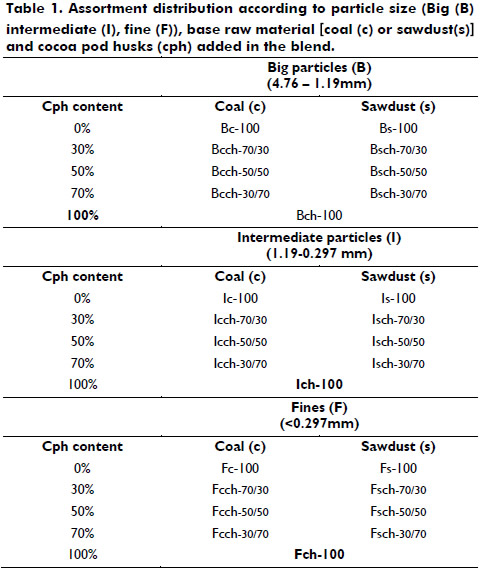
Assortment preparation, characterization and densification
Based on the experimental design, the raw materials were sieved separately using a Sieve Shaker equipped with Mesh No 4, 16, and 50; thus, the grinds were categorized in three groups according to the particle size. Big particles were those remaining between Mesh 4/16; intermediate particles were those that passed through Mesh 16 and retained by Mesh 50, and fines were those grinds remaining on the base of the Sieve shaker. Afterwards, the assortments were organized based on the raw materials combination and the mass ratio (Table 1).
The initial bulk density of each assortment was determined by filling a cubic box of known volume and weighing it at the near 0.001g. Five repetitions were carried out, and the density was then calculated as the ratio between the weight of the sample in the box and the volume of the box. The powder was densified by using a hydraulic press with a 120mm long x 21mm diameter fixed die installed at the Thermal Plants and Renewable Energy laboratory located at 4.638°N-74.084°W, 2630m above sea level. Press force was constant at 170 MPa. Biomass was densified at ambient temperature without steam injection or any heating source. Similar to Zhengang, Quek & Balasubramanian (2014), the end of the die was closed using a removable backstop. The grinds were loaded until filling the die and compressed; after holding 3s the maximum pressure, the backstop was removed, and the resulting solids were pushed out by pressure. About 25 solids were made of each assortment.
Pellets characterization
Physical parameters such as diameter and height of pellets were measured with an electronic caliper. Likewise, the solids were weighted at the near 0.001 g using a digital balance, and the final pellet density calculated as the ratio between the volume and the weight. Density was evaluated for 20 randomly selected samples (Obernberger & Thek, 2004). Meanwhile, the ratio between the initial and the final density was calculated and associated to the compression ratio; this parameter can be ascribed to the resilience, plasticity, and deformation capacity of the grinds during the compression.
Mechanical properties such as the maximum strain before failure, the impact and the compression resistance were measured for each group. The impact resistance was evaluated in accordance with Kaliyan & Morey (2009); ten randomly samples were dropped into the surface at 1,8m height, five times and the final weight of the samples were recorded. This parameter was calculated as the percentage of the final sample against the initial pellet weight. The compression resistance was evaluated using a universal compression machine Shimadzu AG-Xplus 300kN Universal Tester, and corresponded to the maximum load before failing on a stress-strain test. The samples were vertically-oriented during compression and the plunger moved down at 2.0 mm/min. This property gives a measurement of the inter-particle bonding strength.
Results and discussion
The proximate analysis summarizes the moisture content, volatile matter, fixed carbon and ash in the samples (Table 2). Each of these parameters provides elements to analyze the materials performance during either combustion or other thermo chemical process. The raw materials moisture affects not only the performance of the solid biofuels on thermochemical processes, but also the phenomena occurring during densification. The higher the moisture, the more energy is wasted when using the raw materials on thermochemical processes. Meanwhile, the moisture in the raw material affects the densification process; water acts both as a binding agent and a lubricant (Kaliyan & Vance, 2009), moisture in the raw materials enhances the gelatinization of starch, helps develop van der Waals´ forces and diffusion of water-soluble substances throughout the matrix. Nevertheless, when raw materials are so wet, water might encumber short-range intermolecular forces acting as an interface between the solid grinds. Cocoa pod husks had the highest moisture content, about 11.53%wt; which was 2% larger than that of sawdust and 9% larger than that of coal.
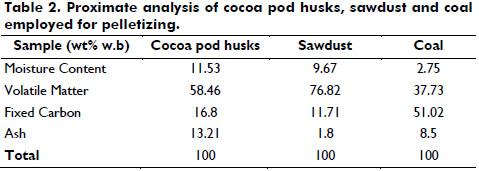
Table 3 summarizes the results of the ultimate analysis for samples of cocoa husks, sawdust and coal on a dry basis. Carbon and Hydrogen content have the closest relationship with the energy content; the oxidation of these elements releases the more quantity of energy during combustion. Coal had the highest carbon content (71.28%), which is 25% larger in comparison with cocoa pod husks and sawdust, whereas sawdust had the highest hydrogen content (9.07%). Nitrogen and Sulfur are components that should be taken into account due to their capability of forming pollutants such as Nitrous and Sulfur Oxides. While nitrogen oxidation can be controlled by maintaining low reaction temperatures during combustion, sulfur reaction with air is more complicated to control. A valuable typical advantage of biomass is the low sulfur content. Sawdust had less than 0.1% sulfur, followed by cocoa pod husks that had about 0.17% sulfur; which is lower than the sulfur content of coal (0.73%).
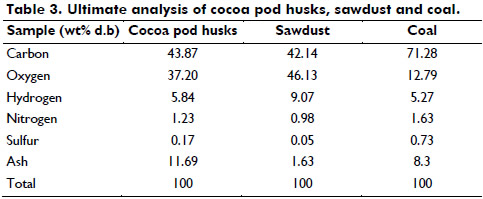
After compression, the pellets density varies depending upon the ratio of cocoa pod husks added and the particle size. Table 4 exhibits the variation of the coal-cocoa pod husks assortments density before and after densification. Table 5 gathers the changes on the sawdust-cocoa husks assortments density during the process. Regardless the particle size, coal grinds always had a higher initial density compared to cocoa pod husks and sawdust; nevertheless, the effect of the particle size on this parameter was completely opposite. The finer the grind, the lower is the coal initial density. The density decreased about 14%, from 917.98 to 788.35 kgm-3 when decreasing the particle size from big to fine sizes. This decrease can be ascribed to the relaxation of the coal intermolecular bonds increasing the volume occupied by the particle. On the other hand, the initial density of cocoa pod husks and sawdust powder rose about 119% and 45%, from 249.53 to 547.88 and from 148.22 to 215.2 kgm-3, respectively, when decreasing the particle size from big to fine sizes.
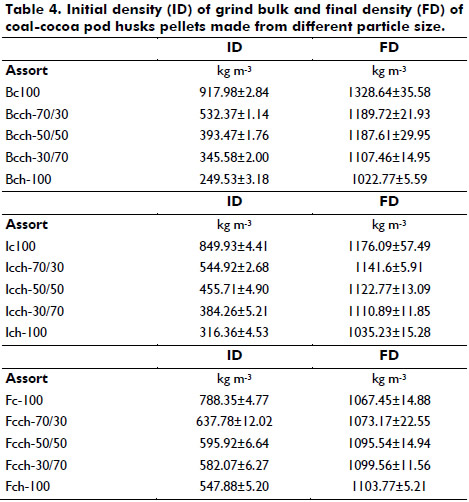
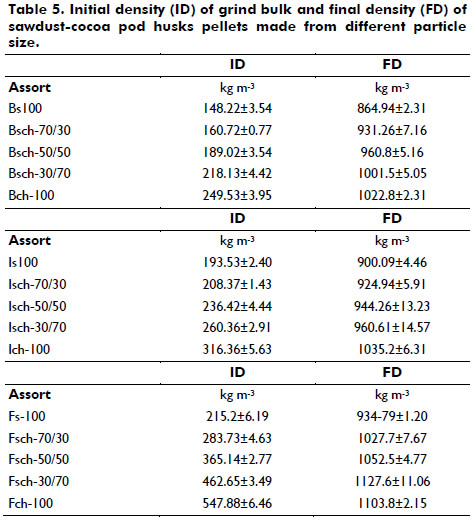
husks pellets (figure 2) fell down due to the addition of the cocoa pod husks. Nevertheless, higher final density was obtained for pellets made of finer particles. Compression ratio was always larger for mixtures with higher quantities of cocoa pod husks. This behavior occurred due to the different densification mechanisms that took place during compression, e.g., air releasing, solid particles rearrangement, fragmentation, and elastic and plastic deformation.
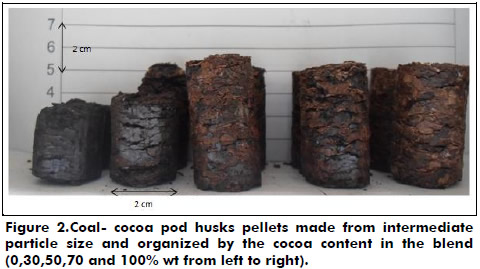
The compression ratio relates the initial and the final density; this parameter exhibits the capability that those materials have to deform with an applied stress. When coal was densified without any additive, the ratio was between 1.35 and 1.45. The more cocoa pod husks are added into the mixture, the greater the compression ratio is. Hence, pellets manufactured with 70%wt. cocoa pod husks have a 3.20 compression ratio, whereas those made with 30% cocoa husks have a lower compression ratio (2.23). Moreover, the particle size proportionally affects the compression ratio. The bigger the particle size, the greater the compression ratio. Bcch-70/30 compression ratio is about 3.22, which is higher than the value obtained for fcch-70/30 (1.89).
Likewise, the compression ratio of pellets made of different sawdust-cocoa pod husks mixtures varies depending upon the grinds size and the mass ratio. Pellets made of 100% sawdust have lower final densities and higher compression ratios than those made of 100% cocoa husks. This exhibits a higher capacity of sawdust to deform and rearrange their particles in comparison with cocoa husks. As seen for the coal-cocoa pod husks pellets, utilizing fine particles in the pellets raises their final density but decreases the compression ratio. Figures 3 and 4 exhibit the behavior of the compression ratio as a function of the cocoa content in the mixture. Compression ratio fitted a linear trend with cocoa husks content in the blend. The coefficient of determination (R2) was higher than 0.92 in all cases. The more cocoa pod husks in the mixture, the greater the compression ratio of coal-cocoa pod husks assortments is. On the other hand, for sawdust-cocoa pod husks pellets, the compression ratio decreases with more cocoa husk in the blend.
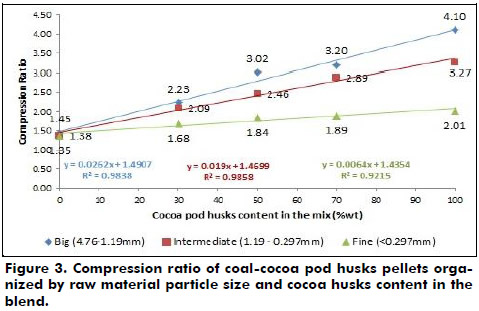
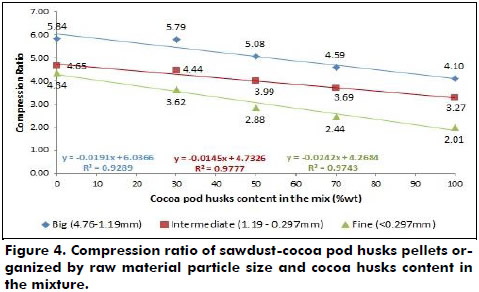
The compression ratio shows the materials capacity to deform and occupy less space due to the applied stress, but it does not relate the cohesion of the particles. An alternative to evaluate the strength of the inter-particle bonds is by analyzing the impact resistance. This parameter simulates the forces encountered while emptying of densified products from trucks onto the ground or from chutes into bins. Several authors have used the term “durability” to report this parameter (Kaliyan & Vance, 2009). Coal pellets were so brittle and instantaneously disintegrated during the tests; their impact resistance was less than 10% despite the particle size. The addition of cocoa pod husks grinds enhanced the resistance fourfold. The impact resistance of coal-cocoa pod husks pellets proportionally increased with the cocoa husks content (Figure 5); a linear trendline fitted the results with determination coefficients above 0.97. Likewise, the fine solid particles use improves the resistance (Figure 6).
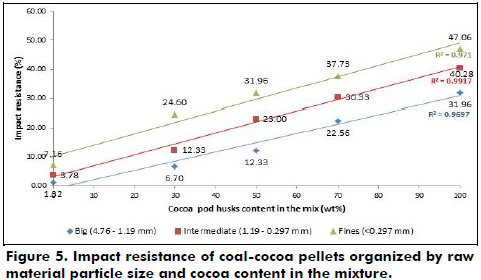
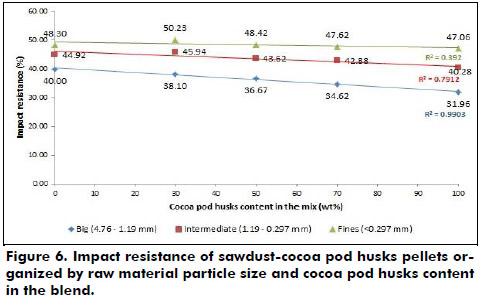
The compressive resistance determines the cohesion between particles and the maximum resistance against a compressive force. According to Kaliyan and Morey (2009), the product may fail due to tensile forces resulting from the applied compressive force or pressure. Table 6 summarizes the results of the stress and final strain before failure for the samples. Addition of cocoa pod husks onto coal pellets enhances the particles cohesion in the agglomerate; nevertheless, the effect is not similar to that of sawdust. Cocoa pod husks addition to sawdust pellets makes the compression resistance decrease. Utilization of finer particle size raises the compressive resistance as a result of the strong bonds created between particles and the large inter-particle area.
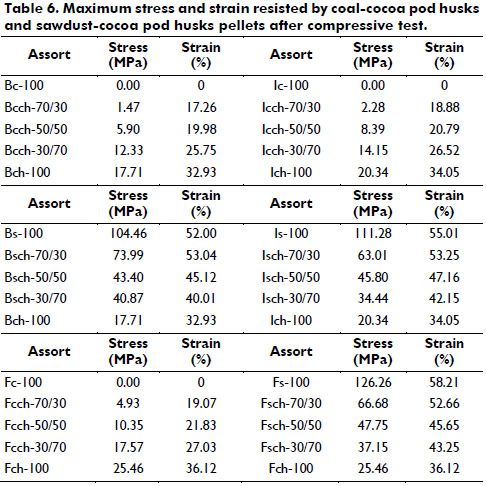
Conclusions
Effect of particle size was analyzed for mixed pellets made of coal-cocoa pod husks and sawdust-cocoa pod husks blends. Compression ratio linearly increased with the addition of cocoa husks into coal pellets; whereas, in the sawdust-cocoa pellets the behavior was opposite. Sawdust grinds exhibited better binding properties in comparison to cocoa pod husks, possibly due to the higher content of lignin in sawdust. Sawdust is more fibrous than the cocoa pod husks particles. As a consequence of that, the sawdust pellets are more flexible and resistant against an applied stress. Nevertheless, cocoa pod husks pellets showed promising results; the final density was larger than 1000 kgm-3 with compression ratio in the range of 2 to 4.2. Thus, the densification of cocoa pod husks might mitigate problems related to waste disposal, storage, transport and management. Cocoa pod husks have lower nitrogen and sulfur contents than coal, which may result in fewer environmental issues and less nitrous and sulfur oxides emitted to the atmosphere. Cocoa pod husks acted as natural binders for coal-cocoa pod husks pellets. The addition of cocoa pod husks to coal pellets improved their mechanical properties. Nevertheless, further research is needed in order to increase the binding capacity of cocoa pod husks and the mechanical resistance of the materials; preheating and steam addition could enhance mechanical properties of cocoa pod husks and coal-cocoa pod husks pellets.
Acknowledgments
The authors kindly acknowledge the Clean Development Mechanisms technical support staff, the Energy Management Research Group, and the financial support of the Research Department (DIB) of the Universidad Nacional de Colombia trough the project code 17996.
References
American Society for Testing and Materials (2013). Standard Test Method for Moisture Analysis of particulate wood fuels ASTM E871, West Conshohocken: ASTM International. Available in: http://www.astm.org/Standards/E871.htm [ Links ]
American Society for Testing and Materials (2013). Standard Test Method for Volatile matter in the analysis of particulate wood fuels ASTM E872. West Conshohocken: ASTM International. Available in: http://www.astm.org/Standards/E872.htm [ Links ]
American Society for Testing and Materials (2007). Standard Test Method for Ash in Biomass ASTM 1755, West Conshohocken: ASTM International. Available in: http://www.astm.org/Standards/E1755.htm [ Links ]
American Society for Testing and Materials (2014). Standard Test Method for Determination of Carbon, Hydrogen, and Nitrogen in Analysis samples of Coal and Carbon in Analysis samples of coal and coke ASTM D5373. West Conshohocken: ASTM International. Available in: http://www.astm.org/Standards/D5373.htm [ Links ]
American Society for Testing and Materials (2014). Standard Test Method for sulfur in the analysis sample of coal and coke using high-temperature tube furnace combustion ASTM D4239. West Conshohocken: ASTM International. Available in: http://www. astm.org/Standards/D4239.htm [ Links ]
Byoung, J. A., Chang, H. S., Lee, S. M., Choi, D. H., Cho, S. T., Han, G. S., & Yang, I. (2014). Effect of binders on the durability of wood pellets fabricated from LarixKaemferi C. and LiriodendromTulipifera L. Sawdust. Renewable energy, 62, 18-23. Available in: http://www.sciencedirect.com/science/article/pii/S0960148113003315 [ Links ]
Erlich, C. (2009). Comparative study of residue pellets from cane sugar and palm-oil industries with commercial wood pellets, applied in downdraft gasification (Ph. D. Thesis). Royal Institute of Technology, Stockholm, Sweden. Available in: http://www.diva-portal.org/smash/record.jsf?pid=diva2:272453 [ Links ]
Forero-Nuñez, C. A., Jochum, J., & Sierra-Vargas, F. E. (2012). Characterization and feasibility of biomass fuel pellets made of Colombian timber, coconut and oil palm residues regarding European standards. Environmental Biotechnology, 8(2), 67-76. Available in: http://www.environmentalbiotechnology.pl/eb_dzialy/eb_online/2012/vol8_2/ms179.pdf [ Links ]
Holman, J. P. (2001). Experimental Methods for Engineers (7th ed.). McGraw-Hill. [ Links ]
Kaliyan, N., & Vance Morey, R. (2009). Factors affecting strength and durability of densified biomass products. Biomass and Bioenergy, 33, 337-359. Available in: http://www.sciencedirect.com/science/article/pii/S0961953408002146 [ Links ]
Kaliyan, N., & Vance Morey, R. (2009). Constitutive model for densification of corn stover and switchgrass. Biosystems engineering, 104, 47-63. Available in: http://www.sciencedirect.com/science/article/pii/S1537511009001597 [ Links ]
Karkania, V., Fanara, E., & Zabaniotou, A. (2012). Review of sustainable biomass pellets production- A study for agricultural residue pellets market in Greece. Renewable and Sustainable Energy Reviews, 16, 1426-1436. Available in: http://www.sciencedirect.com/science/article/pii/S1364032111005740 [ Links ]
Limousy, L., Jeguirim, M., Dutournie, P., Kraiem, N., Lajili, M., & Said, R. (2013). Gaseous products and particulate matter emissions of biomass residential boiler fired with spent coffee ground pellets, Fuel, 107, 323-329. Available in: http://www.sciencedirect.com/science/article/pii/S0016236112008162 [ Links ]
Mansur, D., Tago, T., Masuda, T., & Abimanyu, H. (2014). Conversion of cacao pod husks by pyrolysis and catalytic reaction to produce useful chemicals. Biomass and Bioenergy, 66, 275-285. Available in: http://www.sciencedirect.com/science/article/pii/S0961953414001949 [ Links ]
Munawai, S. S., & Subiyanto, B. (2014). Characterization of biomass pellet made from Solid Waste Oil Palm Industry. Procedia Environmental Sciences, 20, 336-341. Available in: http://www.sciencedirect.com/science/article/pii/S1878029614000437 [ Links ]
Nunes, L. J. R., Matias, J. C. O., & Castalao, J. P. S. (2014). Mixed biomass pellets from thermal energy production: A review of combustion models. Applied Energy, 127, 135-140. Available in: http://www.sciencedirect.com/science/article/pii/S0306261914 00395X [ Links ]
Obernberger, I., & Thek, G. (2004). Physical characterization and chemical composition of densified biomass fuels with regard to their combustion behaviour. Biomass and Bioenergy, 27, 653-669. Available in: http://www.sciencedirect.com/science/article/pii/S0961953404001072 [ Links ]
Ofori-Boateng, C., & Teong-Lee, K. (2013). The potential of using cocoa pod husks as green solid base catalysts for the transesterification of soybean oil into biodiesel: Effects of biodiesel on engine performance. Chemical Engineering Journal, 200, 395-401. Available in: http://www.sciencedirect.com/science/article/pii/S1385894713000867 [ Links ]
Okeh C. O., Onwosi, Ch. O., & Odibo, F. J. C. (2014). Biogas production from rice husks generated from various rice mills in Ebonyi State, Nigeria. Renewable Energy, 62, 204-208. Available in: www.sciencedirect.com/science/article/pii/S0960148113003510 [ Links ]
REN21 (2014). Renewables 2013 Global Status Report. Available in: http://www.ren21.net/portals/0/documents/resources/gsr/2013/gsr2013_lowres.pdf [ Links ]
Sanchez-Silva, L., López-González, D., Villaseñor, J., Sanchez, P., & Valverde, J. L. (2012). Thermogravimetric-mass spectrometric analysis of lignocellulosic and marine biomass pyrolysis. Bioresource Technology, 109, 163-172. Available in: http://www.sciencedirect.com/science/article/pii/S0960852412000053 [ Links ]
Serra, J., & Ventura, F. (1999). Protein quality assessment in cocoa husk. Food Research International, 32, 201-208. Available in: http://www.sciencedirect.com/science/article/pii/S0963996999000885 [ Links ]
Syamsiro, M., Saptoadi, H., Tambunan, B. H., Pambudi, N. A. (2012). A preliminary study on use of cocoa pod husks as a renewable source of energy in Indonesia. Energy for Sustainable development, 16, 74-77. Available in: http://www.sciencedirect.com/science/article/pii/S0973082611000834 [ Links ]
Vriesmann, L. C., Amboni, R. D. d. M. C., & Petkowics, C. L. d. O. (2011). Cacao pod husks /Theobromacaco L.): Composition and hot-water-soluble pectins. Industrial Crops and Products, 34, 1173-1181. Available in: http://www.sciencedirect.com/science/article/pii/S0926669011001142 [ Links ]
Vriesmann, L. C., Teófilo, R. F., & Petkowic, C. L. d. O. (2012). Extraction and characterization of pectin from cacao pod husks (Theobroma cacao L.) with citric acid. LWT Food science and technology, 49, 108-116. Available in: http://www.sciencedirect.com/science/article/pii/S0023643812001892 [ Links ]
Zhengang, L., Quek, A., & Balasubramanian, R. (2014). Preparation and characterization of fuel pellets from woody biomass, agro-residues and their corresponding hydrochars. Applied Energy, 113, 1315-1322. Available in: http://www.sciencedirect.com/science/article/pii/S0306261913007319 [ Links ]