1. Introduction
The market requires that companies make their products considering the most important factors of quality, speed, flexibility, reliability, and cost [1]. For Gagnon [2], a method of strategically managing production and operations to meet these criteria is based on the vision of production capabilities. These resources involve decisions such as product development, technology to be used, work force organization, capacity planning, and configuration of facilities. Fleischer et al. [3] emphasize that the competitiveness of manufacturing companies depends on the availability and productivity of their production lines.
The need to prioritize the rationalization of the use of a resource or another depends on the type of process and product that the company offers to the market. Mass production companies seek high efficiency of equipment and human resources, and must also consider the input materials. In the continuous process, companies need to ensure highly predictable airflow via capital-intensive technologies [4]. An example of a continuous process is wood pulp production. In Brazil, this production sector obtains high investments in the industry that, in conjunction with the economic development of the country, has generated significant impacts in wood pulp production in the last decade [5]. The segment has practically doubled the wood pulp volume in the period between 2003 and 2013, with an average growth of 7.1% per year, quite large compared to the more traditional world markets in the industry. In 2008, Brazil reached the rank of the fourth largest wood pulp producer worldwide, behind only the United States, Canada, and China.
In the cases of mass production and continuous processes, it is essential to ensure high equipment availability and reliability. To promote the company's performance through the competent use of its production resources, Jonsson and Lesshammar [6] claim that it is necessary to establish an integrated assessment system of overall manufacturing performance, because when the causes of losses in the utilization of production capacity are identified, efforts to eliminate or reduce them can be undertaken. High-efficiency equipment indexes require analysis of the various elements that may interfere in their result, whose adoption of indicators to assess the equipment and productive system performance, has been a common practice among organizations. The indicators, according to Kardec et al. [7] has the purpose to direct the necessary changes, allowing the maximization of the efficiency and improvement of the overall results.
The philosophy of total productive maintenance brought the notion that it is necessary to develop a more holistic view of the manufacturing system, and thus, it is essential to establish a more comprehensive means of measuring the productive capacity utilization. The overall equipment effectiveness (OEE), which measures the effective utilization of the equipment capacity, was then proposed as an indicator that would fulfill this managerial control function [8, 9]. This indicator provides an enlarged view of equipment life and assumes that its conditions of use are primarily influenced by its availability, performance, and quality.
A proper measurement system through the management of key parameters contributes to increased productivity [10]. OEE assists in obtaining the financial results of manufacturing, which supports management in the identification of the maximum possible efficiency. The use of indicators is the most effective means of management evaluation, where it is exhibited in the current situation, the progress over time, and a comparison with optimum performance levels [7]. In this way, this study has the main objective to implement OEE in the production of woodchips for the wood pulp industry. The specific objectives of the study are: (i) to implement processes and resources to performance data integration, (ii) to diagnose the overall efficiency of the woodchip production line, according to the performance world class of OEE, (iii) to apply actions to evaluate possible improvements for adequacy of quality indicators, and (iv) to verify the results of these actions for the quality indicators.
2. Methodology
Considering it is an analysis of a particular object and cannot extend the methods and results directly to other processes, the present study is defined as a case study [11]. It must be noted that an adequate case study requires the use of documentation, observation, and information collection directly with the main actors involved in the problem and the specific environment investigated.
For this work, the method chosen can be detailed in three steps. The first step consisted of the formulation of the problem and study planning, where the context was defined by analyzing the significance of the project in the scientific and technical field, and the evaluations criteria were defined. Subsequently, the team involved was able to align the OEE concepts, as well as for explanation of the objectives of this work. Finally, from the observation in the research environment, analysis of records, and staff suggestions, the data to be collected were defined.
In the second stage, the data collection tool was implemented to subsidize the generation of results regarding the overall efficiency of the production line, through the collection of events records of unavailability, volumes produced, and results of product quality analyses. After the tool functionality was validated, the results were analyzed from meetings to develop collaborative analyses involving members from the team and to verify the data’s adherence to the formulated indicators. Finally, based on the results, the problems and their possible impacts on the overall efficiency index in the production line were identified.
The third step comprised the proposition of actions and their applications to the results optimization, where an action plan was adapted defining the responsible subjects, deadlines and resources necessary to mitigate the deviations and optimize the OEE result of the line. The priorities were defined by the criteria of simplicity, expected results, and resources available in the period. Following the study, the results were exhibited to generate reactions, contribute to awareness and enable suggestions for a future cycle of improvements.
3. Results and discussion
3.1. Description of the company and the process analyzed
The company is a pioneer in the wood pulp and paper processing industry in Chile, and started its activities in 1920, in the city of Puente Alto. Today, it is one of the leading companies in the forestry area in Latin America and is present in more than 50 countries in five continents. With more than 25 factories, it has approximately 8,000 employees working in 5 areas of business, through the following segments: forestry products, wood pulp, paper, tissue, and paper products. The company has strong ties with its markets worldwide and has a commercialization network of diversified exportation, which reaches more than 200 customers in 30 countries. In Brazil, it started its operations in 2009 and now occupies an area of 106 hectares in the municipality of Guaiba (RS, Brazil). The company invests in the cultivation of forests in a large part of the regional territory to obtain its raw materials.
The object of study was one of the systems in the production process of woodchips, where equipment is leased for transporting and processing raw material from the forests. The system processes the wood with a predominance of eucalyptus logs and a small percentage of acacia logs. The logs intended for the wood pulp mill are peeled and sliced in the forest, with a nominal length of six meters and delivered to the wood pulp mill. These logs contain approximately 3% fiber by volume, and the system has carriers to remove these residues to achieve the standard accepted bark content in woodchips.
3.2. Practical application system
Initially, the experts in the sector consulted for the study answered two questions designed to investigate and understand which opinions and criteria are used by professionals in crucial decisions and prioritization of actions regarding interventions and maintenance during situations faced daily during their work. The justification for these questions is that, based on the answers obtained and using appropriate tools, the decisions, which are currently based on the technicians’ individual and implicit knowledge, can be replaced by consensual decisions based on collectively constructed knowledge. The transportation and chipping system of logs is composed of three production lines of equal capacity, which supports the receipt of wood by B-train trucks. Each line has a design capacity to process 500 m³/h (unit of measurement for volume of timber processed), with availability of operation designed by 70% and average performance guaranteed of 400 m³ /h.
The production lines are fed through a stationary hydraulic crane, directly on the receipt tables. From this step, the production process of the system analyzed begins with the tables dosing the material on the first belt conveyor. Next, the material is led to a roller conveyor with a washing station. After the washing station, the logs go through a metal detector installed on the second conveyor belt, which transports the material to the grinder. The logs are provided by gravity to be processed in a disc grinder by dropping the log in an entry. The woodchips produced are unloaded from the rear. Chipping line 100 was chosen for the OEE implementation, because it was the most used by production.
3.3. Team involved in OEE implementation process
The OEE implementation as a productivity indicator of one of the woodchip production lines began with a meeting to define and align the activities to be performed. The technicians responsible for the operation of process equipment for the woodchips production participated of the works, totaling 12 employees with technical training in mechanical and/or technical in wood pulp and paper. Initially the operators were given training with the following objectives: i) clarification of what OEE means, ii) explanation of the metric’s operation, (iii) the form of application of the indicator for the woodchips production line, and iv) benefits of application of this technique. Still in the first stage of the work, one of the technicians was selected to participate with greater effectiveness in the discussions and a survey of the data collection criteria for indicators compilation. During the second stage, the selected technician worked in the implementation of the data collection tool, as well as helped in the analysis for the tool validation. The rest of the team also participated actively through the daily records completion for the line’s downtime, the records of the production volumes, and the process of analysis of the quality of the woodchips with data entry into the system, using the implemented tool.
After the seventh week of implementation of the data-collection system, the analyses of the indicator results were held in conjunction with the team participant, through specific meetings for this purpose. In these meetings through methods of analysis and solution of problems, proposals for actions for adequacy of the problems were drawn up exhibited in the OEE results of the woodchips production line.
3.4. Quality of woodchips for wood pulp production
The quality of the woodchips is a relevant concept to wood pulp manufacturing, owing to the significant costs of raw materials and potential impacts on the pulping process, making this indicator of crucial importance for the sequence of wood pulp production process [1]. For Smook [13], the quality of the woodchips is measured by the uniformity of dimensions and by the lower presence of scraps. According to the same author, scraps are considered: (a) woodchips above a specified size in length or width, (b) chips with normal length, but thickness and width smaller than three millimeters, called toothpicks, and (c) very short chips or fragments that pass-through sieves with circular holes of 3 mm, classified as thin. To determine the quality of the particle size distribution of woodchips, the method described in the regulation SCAN CM 40:01 was used [14].
According to the specific technical bibliography and with the regulation of woodchips classification, the OEE quality indicator considers woodchips accepted as good products and the rest of the portions were considered as scraps.
3.5. Criteria for data collection for OEE determination
For the construction of the data-collection and -compilation tool for the analysis of productivity of woodchip production, criteria were reviewed and developed to develop the three indexes that are considered in the OEE metric. Regarding the availability (i) criteria for records of the causes of unscheduled downtime and (ii) criteria for records of the reasons for planned downtime of the woodchip production line were defined. In terms of performance, the accounting system of production was defined by volume per hour. The quality index of the woodchips produced was defined based on the parameters of the method of sample analysis of the material, complying with the plan of existing analyses in the process, universal regulation for woodchips classification, and project data concerning the level of acceptable losses.
Initially, the production of this line started to be recorded via an electronic spreadsheet in time arrangements, stored in the data directory inside the company, according to the quantity of trucks unloaded in a given period. The availability for production of this line began to be monitored also every hour, being justified the downtimes reasons in the internal data directory of the production. The quality of the product was measured according to the results of the particle size distribution of the chips produced by the woodchipper, according to SCAN CM 40:01 [14] which is universal standard for classification of woodchips for wood pulp production. The frequency of analysis is daily, in accordance with the analysis procedure plan established by the quality system from the mill.
The records relating to the performance (production) and availability are made by SDCD’s operators that control the entire production process. These records are entered into the bulletin of control process and saved in internal company directory. The data on stop of time of lines and lack of raw material supply are integrated automatically through a system called the PI System, which integrates the monitored data in SDCD into Microsoft Excel through the application Data Linck. Field operators undertake particle-size analysis, where they insert the results in an integrated system of quality data storage. These results suggest that the quality of woodchips is automatically integrated into the process control bulletin, also through the application Data Linck.
3.6. Criteria for availability determination
To diagnose the availability of the production line and consequently to stratify the reasons which give rise to the planned and unplanned downtimes of the system, items were discriminated as detailed in Table 1.
Table 1 Criteria of downtimes records.
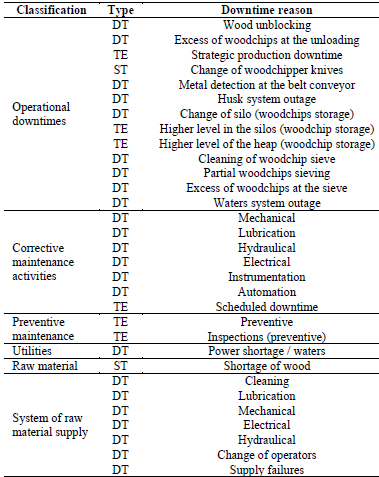
DT: Downtime, TE: Time Excluded, ST: Stop Time.
Source: The Authors.
The results were stratified on a weekly basis for the behavior of the performance indices measured by the metric implemented.The total period of data measurements was 7 weeks. Table 2 shows the values found through the record of time for the downtime reasons and of the line production, as well as for recording the results of the daily analyses regarding the quantity of woodchips produced.
It can be observed that the system is quite adjusted regarding availability. The manufacturer ensures that the process should operate for at least 70% of the operation time. The results presented in seven weeks of follow-up were satisfactory and are fulfilling the production demand, except the first week (Fig. 1). In week 1 the high level of downtime events due to mechanical maintenance problems impacted in Downtime, resulting in availability below the average.
The Pareto chart shown in Fig. 2 presents the ten main downtime causes during the first week. It should be emphasized that the downtime due to heap level is due to lack of demand, therefore is counted as time excluded, not impacting on ID. Therefore, the downtime for corrective maintenance in 1st week was the main factor that impacted in availability.
Regarding the performance, the production line presented a mean value of 93%, which indicates that in terms of small downtimes and speed losses, the process is adjusted to levels close to those cases considered as world class [10]. It is important to point out that the manufacturer ensures an average of 400 m³/h, which is equivalent to a performance of 80%, designed according to the demand of woodchips consumption of the next process. However, the data used to calculate the PI was 500 m³/h for definition of the theoretical rate, based on the production capacity of the line under study. In case the guarantee data were used as, the process would display IP results above 100%. The results showed a PI above the target established by the company, as shown in Fig. 3.
Regarding quality, the IQ had an average value of 89.8%, close to the designed objective value for quality of 90.4%, because this process allows 9.6% of scrap in the processed raw material (Fig. 4).
According to Hansen [10], the average OEE indicator of the sampling results analyzed from week 1 to week 7 in this production line classified it as unacceptable, with an OEE below 65%. Through the results obtained, it is evident that the indicator that most impacts on the OEE results of this production line is the availability. However, actions for improvements in this indicator were not examined, due to the time required for the implementation of improvements that caused positive effects for availability of the production line. Another factor that contributed, although actions were not proposed to improve it, was the observation of results that exceeded the target demanded by the company.
The largest relative standard deviation of weekly results was recorded for the availability, which denotes the need to work to obtain better result stability of this indicator. Fig. 5 shows the OEE results in the seven weeks analyzed and in Fig. 6 is presented the indicators that compose the OEE.
The quality indicator was below the target designed by the company in four of the seven weeks analyzed, which was the focus of the proposition and implementation of improvement actions. Therefore, works were directed to analysis of the factors and procedures which impact on the particle size distribution quality of the woodchips produced.
It is extremely important that the woodchips manufacturing process obtain a high index of accepted woodchips, because of the impacts in the next process and the significant cost of the raw material supplies. The results of the mean weeks of diagnosis are presented in Table 3.
According to the results of particle size of woodchips, the largest portion of the scraps is associated with the production of woodchips below the thickness limit for acceptance (toothpicks and thinner). This showed the need to evaluate the components and adjustments of the woodchipper which impact on the waste generated by the low particle size distribution. The condition of the raw material processed was also considered as a variable in the following analysis, because variations in some of its properties can have a direct impact on the quality of the woodchips produced. For example, the water content in the wood directly influences the quality of chipping because the wood properties vary with moisture. When the moisture content is less than the saturation point of fibers, the demand for energy grows, the woodchip will be thinner, and the quantity of thinner chips increases [15]. The moisture considered ideal for production to increase the quality of the woodchips is estimated at approximately 45% [16].
According to the manufacturer's manual, the increase in the generation of thin woodchips can be associated to the wood cutting geometry that can be impacted by the angle and quality of rectification of the knives, the quality of the surface of the counter knife, the integrity of the blades of the press knives support, for the integrity of the disc plates coating of the grinder and the parallelism of adjustment between knives and counter knife. The manufacturer also stresses the importance of the wood’s moisture as a variable to be analyzed.
3.7. Actions for improving the quality indicator
Owing to the existence of several variables that could impact the high production of scraps and thinner chips, an action plan was developed for the implementation of tests to assess the impacts on the particle size distribution of the chips, varying the possible items which could be correlated to the generation of these deviations. The objective of the tests was to diagnose the potential increase in quality indicator, according to the alteration of each variable, when the action plan is presented in Table 4.
Analyses of the chips were performed according to the procedures of SCAN CM 40:01 for every action implemented to assess the impact of the adequacy of each item recommended by the manufacturer on the quality indicator of the woodchips produced. The results for each parameter are shown in Table 5.
Can be observed that the woodchipper equipped with parts in the beginning of their service life combined with the supply of wood with moisture content below the level considered ideal, can produce woodchips with a percentage of good products above the expected goal. The analyses performed in step 5 of the plan of action, processing of wood with moisture content of 39%, exhibited a rate of 91.2% of good products. However, spare parts such as blades, counter knives and wear plates are items that have estimated service life of 40, 100 and 180 days, respectively, and their wears are directly associated with reducing the percentage of good woodchips. Nevertheless, the production of woodchips with the woodchipper equipped with parts in the beginning of their service life combined with the supply of wood with moisture average content of 45%, which is considered ideal, showed a greater potential for generating good woodchips within approximately 3 percentage points above the quality target. The benefits of the adequate moisture content can compensate for the impacts of wear of the woodchipper consumables on the production. Fig. 7 show the percentage of good products, associated with each step of the action plan.
4. Final considerations
The application of metrics and OEE to measure the productivity of the woodchips production line were effective in terms of the data compilation to aid in decision making in the technical management of this productive process, fulfilling the objective of this work. The implantation of a registration system, which, when compiled, accounts for the OEE indicator, was consolidated successfully. Regarding the indicator analysis, it was possible to diagnose that the system, although according to the specific literature is classified as inefficient, obtained an OEE lower than 65% during the period analyzed, is quite well-adjusted to the project and the compliance of the current production demand. Some points of attention, such as the variation in the availability of the production line, could be analyzed, revealing that the most significant impacts were originated by downtimes for corrective mechanical maintenances. Concerning the quality indicator, the diagnosis showed that its result varies below the goal the company determined for a more comprehensive analysis in the chipping system. The tests have certified the importance of working with the moisture content of the wood within the standards set by the manufacturer and described in the specific literature, and a potential increase of 3% was obtained in this category. Such scrap production deviation above the target may be appropriate with the receipt of raw materials containing this variable in the aforementioned standard.