INTRODUCTION
Merge-in-Transit (MiT) is a logistics operation concerning different components, combined for single deliveries at the merge center, after end-customer orders arrive (Bradley, Thomas, Gooley, & Cooke, 1998; O'Leary, 2000). To compare MiT with other distribution operations, see figure 1.
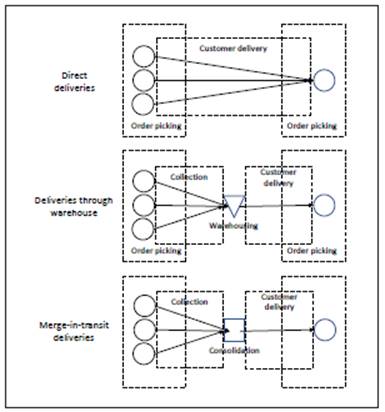
Source: Ala-Risku, Kárkkáinen & Holmstrõm (2003).
Figure 1 Activities for Different Distribution Channels
Concerning deliveries through warehouses, there are other distribution strategies also designed to maintain inventory low-levels. One well-known example is 'crossdocking'. In a typical crossdocking system, goods are moved directly from receiving to shipping through 'crossdocking centers'; the aim is the elimination of storage and excessive handling (Rohrer, 1995). Like crossdocking, MiT also involves intermediate coordination points called 'merge-in-transit centers'. Both MiT and crossdocking minimize inventory costs and decrease lead times by avoiding storage time. However, they are applied in different environments (see table 1).
MiT is a recent approach to solve some of the traditional problems associated to multi-actor distribution channels. MiT was introduced into business practice at the end of the 1990s (see table 2).
Ala-Risku, Karkkaainen & Holm-strom (2003) identify that some of the advantages obtained with MiT are, first, higher customer satisfaction is obtained by delivering multi-product orders in one event instead of making more than one delivery, one for each component or partial group of them. Second, savings are achieved by not keeping inventories in the distribution process; since merge-in-transit centers just hold order components for a short time, usually less than 24 hours, the order is all the way in transit to its final delivery point. This avoids or at least minimizes holding costs associated with warehousing operations. Finally, savings also arise by avoiding the risk of keeping obsolete inventories. MiT is normally applied to distribute orders where at least one component has been made-to-order. Those tailored components have been made for a specific need and are never kept in stock so there is no risk of keeping obsolete components.
However, literature indicates that this distribution strategy can deliver its benefits only if effective Information Systems (IS) back up MiT operations. Simchi-Levi and Kaminsky (2000) recommend manufacturers to merge centers and delivery equipment, and to link them with advanced information systems; to ensure that all pickups and deliveries are made within the required time windows. In practice, e-commerce platforms and 'build-to-order' strategies are usually put in place to respond to market fluctuations and, at the same time, avoid high inventories cost when supplying a wide range of customer requirements (Van Hoek, 2001).
E-commerce and associated IS present benefits and hindrances. Otto and Chung (2000) identify potential advantages and disadvantages in Internet Retailing and traditional Physical Retailing (see table 3).
Table 3 Advantages and Disadvantages between Online Retailing and traditional Physical Retailing
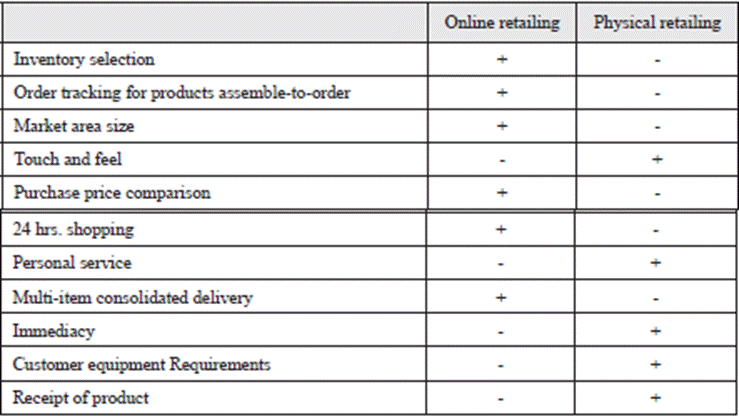
Note: advantage (+) disadvantage (-)
Source: Adapted from Otto and Chung (2000).
Some of the disadvantages presented in Online Retailing can be offset by means of MiT product delivery programs. For example:
Convenience in payment. When multi-item purchasing is required by a customer, having the convenience of paying for the group of items in a single transaction can be appreciated by customers. This means that there is a single payment from the customer to the retailer. This feature can save time to customers as they do not need to repeatedly key in payment details such as delivery address, credit card number and purchase security data as examples. This feature is well used by retailers like Amazon, as an example, that allows customers to select products to purchase in more than one visit to their web portal to later purchase them in a group of items. O'Leary (2000a) has addressed this advantage also but in the context of saving paperwork processing and invoicing time, savings that deal with the convenience for the retailer side.
Saving in transportation. Shipping a group of items to the same location allows consolidation of the transportation operation. Transportation consolidation is a well-established practice by transportation companies to realize economies of scale and therefore savings. These savings for carriers can be translated into savings in delivery fees to multi-item shoppers. Some online retailers have been successful offering the charge of delivery fees in a "per order" policy rather than a "per product" policy. This strategy has been an incentive to buy online and reduce delivery costs.
Convenience of receiving an order. Receiving orders of products purchased online can be problematic to customers that find it difficult to receive deliveries any time during the day. This issue becomes worse when the purchase is multi-items as the problem of having unattended deliveries is multiplied. The consolidation of transportation allows the consolidation of receiving operations into one delivery and potentially a higher customer satisfaction. This is the way that unattended deliveries can be potentially reduced by MiT programs.
Finally, as a point of attention, Bayles (2001) assert that payment processing, order fulfillment, product delivery, and other back-end logistics represent the messiest parts of e-commerce but they are also the most crucial challenges in building customer satisfaction and customer loyalty.
1. LITERATURE REVIEW
The amount of academic papers reflecting research work in MiT distribution seems limited. MiT has been in use since 1997 in the distribution industry (Hoffman, 1998; O'Leary, 2000a; ). Kopczac (1995) was first addressing MiT, when analyzed manufacturers' partnership, in the context of 3PL and supply chain restructuring. Logistics partnerships involve strategic alliances between manufacturers and logistics service providers (e.g. Excel, FedEx or UPS); while supply chain restructuring is the reengineering of the organizational functions in the supply chain (Kopczac, 1997). MiT is presented as a distribution system framework that requires a strongly linked operational partnership between a manufacturer and a logistic service provider. Analytical models focusing on the trade-off between inventory holding cost, planned shipment lead-time, and on-time delivery, given stochastic shipment times are used to build conclusions.
Cole & Parthasarathy (1998) developed a linear programming model to design optimal MiT distribution networks and a Decision Support System (DSS) for the same purpose. The model considers MiT costs simultaneously with production, warehousing and inventory costs. Experimental variables of the model include location, type of merge points, selection of transportation channels, and allocation of customers and retailers to merge points. In the DSS, users interact with a Geographic Information System (GIS) which functions as a user interface. The interface has access to the database and runs the optimization model to finally call the solver.
Croxton, Gendron, & Magnanti (2003) developed integer programming formulations and solution methods for addressing operational issues in MiT distribution. The models account for features including the integration of inventory and transportation decisions, the dynamic and multimodal component of MiT distribution and the specific structure of specific cost functions that arise in MiT. Their paper provides indications on how to decide which merge center to use, in a trade-off between what can appear best for different merging components. For example, while one MiT center might be optimal for a given component (if it is in a direct line between the source and the customer), it might be less costly to merge the order at another MiT center that is closer to the source for some of the other components.
Ala-Risku, Karkkaainen and Holm-strom (2003) elaborate a guideline for logistics managers on how to evaluate the applicability of MiT operations for their own business situation. This paper presents a systematic procedure for the evaluation of MiT distribution in a specific supply chain. The procedure is based on activity-based costing models for distribution operations. The paper includes a structured approach to define whether MiT is suitable for a business considering the nature of the product, current distribution costs, profitability of changing to MiT, and capabilities of current information systems; a feasibility study is also presented.
Brewer, Sloan & Landers (1999) argue that Intelligent Tracking Technologies, such as Global Positioning Systems (GPS), Geographic Information Systems (GIS), wireless telecommunications, and Radio Frequency Identification (RFID), have the potential to contribute to improvements in manufacturing and to the entire supply chain. From orders of raw materials and sub-assemblies through product assembly, testing, and distribution, intelligent tracking technologies offer opportunities for increased efficiencies and improved customer service.
Karkkainen, Ala-Risku and Holm-strom (2003) present a description of differences between MiT and crossdocking from the point of view of how operations are carried out in merging points and cross docks respectively, customer service implications and suitability for different business sectors. Additionally, the effects of MiT distribution on delivery costs are examined in a maintenance and repair distributor as a case study in Finland. The costing model used four attributes to calculate the distribution cost of a delivery: location of suppliers, number of orders per supplier, weight per shipment and location of the customer.
In O'Leary (2000a), MiT is investigated as an approach for reengineering, warehouse and billing processes for electronic commerce. MiT is defined and examples are given to illustrate its use. Processes necessary to accomplish MiT are developed, while advantages and disadvantages of Merge in Transit are studied. The paper also provides examples of successful implementations of MiT. The central part of the paper consists of comparing the traditional process flow for handling multi-item orders with a MiT approach. An interesting element of O'Leary's work is the inclusion of the simplification in the purchase order management and invoices handling. MiT consolidation reduces the number of purchase orders and invoices handled. This factor simplifies back-office operations increases office efficiency and diminishes operating costs.
Finally, Rao, Navoth and Horwitch, (1999) provide a detailed retrospective look at how Third Party Logistics (3PL) companies capitalize on the rise of electronic commerce. Rao et al. argue that by integrating virtual-world information technology and electronic commerce capabilities with real-world physical delivery of products through air and ground transportation network, global 3PL companies exploit the new opportunities emerging in the digital economy.
2. PROBLEM DESCRIPTION
MiT is usually presented as an alternative way to physically deliver multi-item orders to customers as it relies on fundamental principles from the theory of Operations Management. Three different strategies, postponement, mass customization and quick response operations, will be explored in the context of MiT and potential benefits and limitations for retailers and customers will be indicated.
2.1. Postponement
Postponement was first mentioned by Anderson (1950) as a strategy that delays product differentiation to as late as possible, with the aim to improve marketing systems' efficiency. Similarly, Bucklin (1965) suggests postponement as a strategy to speculate with the delay of operations activities (i.e. inventory holding, assembly, and manufacturing) in the distribution channel, to reduce cost and deal with competitive forces. However, over time, this concept has been redefined, as markets' needs have evolved. Van Hoek (2001) analyses postponement in a more contemporary context and develops a comprehensive analysis that reflects the evolution of the concept. Anyway, postponement remains as a speculative strategy to delay operations, even though its objectives have changed and will continue to change as markets do.
Pagh and Cooper (1998) suggest three categories of postponement: logistics, manufacturing and full postponement. Postponement in logistics involves a degree of speculation, as finished products are held in inventory until orders are placed. Manufacturing postponement considers pre-planning products assembly, in terms of which partner will process and distribute final goods. Finally, full postponement combines previous two. This strategy involves less speculation, due to less financial commitment related to components manufactured in advance, and more focus on opportunities available in specific time windows. In this context, MiT distribution implicitly involves postponement as it involves delays in individual customers' purchase orders, to be satisfied only when a multi-item order appears. Multi-item orders could be preassembled or put together with anticipation to reduce unexpected risks, even though this can lead to unwanted costs related to unnecessary inventory or incorrect demand estimations.
MiT also speculates in the geographic dispersion of potential customers. MiT distribution systems are designed to fulfil the multi-item needs of a geographical region within the same country and sometimes more than one country (Hammond, 2005). Once the delivery location wanted by the customer is identified, it is defined the optimal location for the consolidation based on item availability, sourcing and taking into consideration also the minimization of transportation costs to provide acceptable delivery times.
2.2. Mass Customization
Gilmore and Pine II (1997) suggest mass customization as a "flexible work process". It refers to a customer co-design process of products and services that matches product features to the needs of each individual customer (Piller, 2005). It allows high-volume customization of goods and services to individuals' specifications, within a fixed solution space, characterized by stable but still flexible and responsive processes. Accordingly, mass customization provides increase in variety and customization without a corresponding rise in costs, providing strategic advantage and economic value (Pine II, 1999).
Some new concepts emerged as consequence of mass customization realization. Vollmann, Berry, Whybark & Jacobs (2004) categorize different production strategies concerning mass customization. 'Make-to-Order' products (MTO) is the term used to define the products that were made under the needs of a specific customer. 'Make-to-Stock' (MTS) and Assemble-to-Order (ATO) products can be drawn from table 4.
Cruz-Mejia and Eglese (2005) suggest different forms of co-design for MiT distribution. One is the configuration of products ATO, where customers have access to web applications that allow the selection of features in the ATO contained in the multi-item order. The second form involves multi-item order, the need of the customer is integrated for the election of multiple items; they can be all MTS products or a combination of MTS products and ATO products. MiT, due to its capacity to integrate multiple items in a single order, may deliver multi-product needs that are co-designed in the selection process.
2.3. Quick Response Operations
MiT distribution not only implements mass customization and postponement strategies but it is also able to compress delivery times to customers. Quick response supply chains are an extension of the quick response manufacturing strategy developed by Japanese companies in the 1980s. This strategy is also known as 'Time-Based Competition' (TBC). Quick response supply chains rely on the use of speed to gain competitive advantage (Suri, 1998). A supply chain under quick response operation delivers products and services faster than its competitors. Lead-time analysis is a key performance indicator in quick response supply chains.Christopher, Lowson & Peck (2004) indicate that having the ability to respond to customers' requirements on a time basis is fundamental to the marketing concept. They add that current challenges to marketing and logistics involve reducing product development times, accelerate feedback from marketplace and compress replenishment times.
Quick response supply chains are time sensitive in the whole range of processes involved in the delivery of multi-item orders. In the capacity analysis of suppliers is important, to consider how they will react in the case of high fluctuations of demand, as an example. The Quick response operations that allow MiT to deliver short lead times on the delivery is heavily supported by IS within the organization. Companies like Dell Computers and Cisco Systems are examples of organizations running quick response operations. In these organizations, lead-times are closely monitored and customers informed about the expected delivery time. This estimated delivery time involves a safety buffer to increase customers' satisfaction.
3. ANALYSIS
Micro-businesses (MBs) are a fundamental force in current World economy. They represent 90% of businesses in the European (EU28) formal economy, and contribute 20% of value added to the European economy (Muller, Gagliardi, Caliandro, Bohn & Klitou, 2014). However, this is an under-researched area. The main challenge on studying MBs is the general impression that small businesses are scaled-down versions of big businesses. Accordingly, same theories are applied, even in terms of supply arrangements. However, size is not the only reason to consider MBs differently. Micro-entrepreneurs are usually the owners of micro-businesses and follow different drivers such as family-orientation, heritage, life style or prestige (Hingley, & Vi-lalta-Perdomo, 2017). In operational terms, differences also arise. For instance, Haksever (1996) suggests advantages in remaining small in terms of total quality management. He states that business size of the allows regular interactions between customers and managers, and builds personal relationships with clients.
Observing operations in manufacture-oriented MBs suggests their preference to pursue the MiT model. MBs usually follow the ATO strategy; where unfinished products or raw material are transformed into finished products and delivered only after customers put an order. The rationale behind is that typical micro-producers have limited access to resources, which constrain their financial capabilities to maintain big inventories. MBs tendency to follow build-to-order helps them to control inventory and minimise associated costs (Svensson, & Barfod, 2002). This suggests MBs to become convergence points between the original suppliers and the final customer. In other words, to play the role of merge centres. Three MiT strategies will be explored in this context: postponement, mass customisation and quick response.
3.1. Micro-businesses and Postponement
Concerning postponement, this is a traditional strategy followed by MBs. As indicated above, typical MBs follow ATO strategies because these reduce inventories and add flexibility to meet individual customer orders. Postponement concerns moving the decision point for final assembly of a product, what is known as 'decoupling point' (see figure 2). The decoupling point indicates inventory decisions related to orders being delayed by intermediaries' decisions and actions. For instance, at the point of manufacture inventories are usually constituted by components and materials; whereas, at the end of the chain inventories involve finished product (Christopher, 2000).
MBs tend to move the decoupling point as close as possible to the customer. This is achieved by means of having meeting customers on a regular basis, which allow building stronger personal relationships with their clients (Haksever, 1996). Accordingly, MBs postponement usually supports agile and responsive networks. Agility is "a business-wide capability that embraces organisational structures, information systems, logistics processes and, in particular, mindsets" (Christopher, 2000). An agile approach may equip MBs with additional flexibility, innovation, delivery speed and adaptability to the supply chain (Mattila, Huuskonen, & Hietikko, 2013).
A side-effect concerning postponement is the limited capability to answer to urgent customers' orders. As inventories of finished goods are maintain as closer as possible to zero, customers need to consider the production time incurred and plan in advance.
3.2. Micro-businesses and Mass Customization
Mass customisation aims to provide high-volumes of goods that demand customisation without an increase in cost for quality or delivery (Wang, Wang, & Zhao, 2015). To adjust production to a high variety of customers' needs demands being 'agile'. As previously mentioned one of the competitive advantage of MBs versus big corporations is their potential to become 'agile'.
However, there are limitations for mass customisation in MBs related to the high-variety of customers' requests. First, to deal with such high-variety demands reliable communication channels between customers and MBs. Internet-based interfaces are usually part of the technical solution to this. But maintaining a commercial internet platform may become a hindrance for MBs operations. Two mass customisation challenges for MBs can be identified. First, specialised human resources are limited and their provision expensive. Second, a high-variety of products may involve the need to build and maintain an extensive multi-actor network of suppliers. Specialised suppliers cannot always provide all the materials required, because they aim to rationalise the amount the SKU or the cost of distributing of products in small quantities is prohibitive.
3.3. Micro-businesses and Quick Response
Until recent years, quick response was an impossible task for MBs. Regular postage was design not for speed and multiple delivery options, but for low-cost and reliability, making global transactions very difficult for MBs. However, with the development of alternative courier firms, like DHL, UPS, etc. MBs can make use of effective distribution systems to reach a global coverage.
Quick response involves an increase in delivery costs. This limits the applicability such strategy to high-value products, which limit customers' perceived impact of additional transportation costs. However, it is important to notice that international delivery costs are becoming affordable for customers when MBs make use of 3PL/4PL solutions. Internet-based organisations such as Amazon are providing logistics support for MBs, which can then focus more on innovative products and cost-efficient manufacturing processes.
A summary of advantages and limitations of postponement, mass customization and quick response is presented in table 5.
One possible way to alleviate limitations in the implementation of MiT strategies for MBs is to collaborate with others. Different alternatives to direct marketing have been previously identified, such as being part of a supply chain, a network or a community (see table 6).
Table 6 Strategies for MBs to Collaborate with Others
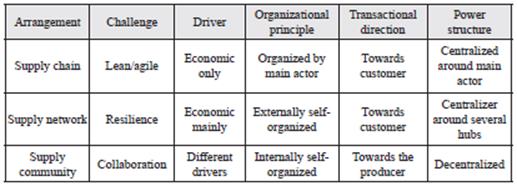
Source: adapted from Hingley & Vilalta-Perdomo (2017).
A possible way to develop sustainable MiT strategies in MBs is by means of collaboration. Groupings of MBs associated in organizations that share resources to deal with common challenges is one possible solution to MiT limitations. For instance, communities of MBs may share common resources that would not be possible to develop alone.
MBs participation in supply chains and networks involves a level of submission to the instructions developed by bigger actors. For instance, in the case of food supply chains big retailers are the ones who control operations and exert imbalanced power relations with the different participants (Burch & Lawrence, 2007; Hanf & Kühl, 2002; Hingley, 2005).
An alternative approach involves the development of micro-producers' groupings. These may take at least two forms: as cooperatives or communities. The former involves externally self-organized collaboration; the latter builds on to more democratic structures that allow MBs to follow their own drivers. There are challenges involving collaboration, but these may be made visible by looking at interdependencies between activities and coordination mechanisms (Handayati, Simatu-pang, & Perdana, 2015).
CONCLUSION
MBs are closer to MiT strategies that one may initially suspect. Their production strategy tends to be associated to ATO, and their decoupling point inclines to be nearer to final customers. MiT can be associated to agile organizations, and can be achieved by any of the three MiT strategies: postponement, mass customization and quick response. These involve advantages and in terms of cost, high-volumes and fast-paced response, respectively.
There are also barriers concerning the implementation of MiT in the context of successful agile supply arrangements. For instance, in the case of MBs limitations associated to the need of additional resources have been indicated, mainly in relation to internet-based marketing support systems and the management of complex networks of suppliers. In some cases, MBs may become slow responsive to urgent customers' demands. Finally, in some cases MiT implementation involves initial high-costs limiting it to high-value products.
It is important to recognize the existence of alternative ways to organize MBs participation in supply arrangements. Three of these have been presented in this document: supply chains, supply networks and supply communities.