1. Introduction
The use of high range water reducer admixtures has become a common practice since the 1970s. These types of admixtures allow for the reduction of water- to-cementitious material ratio (w/cm) of the mixes, which results in stronger concretes without affecting workability. But water reducers can also be applied to increase the fluidity of mixtures, scarcely affecting strength (maintaining the w/cm ratio). This has enabled the emergence and application of self-compacting mixes.
Water-reducing admixtures are polymers with very high molecular weight, which act when they are adsorbed into the surface of cement particles, producing particle dispersion and reducing the amount of water required for a given consistency level. There are different types of superplasticizers (SPs), with varying fluidizing power and action mechanisms in the cementitious system. According to their composition, they can be based on sulfonated melamine-formaldehyde condensates, sulfonated naphthalene formaldehyde condensates, modified lignosulfonates (MLS) or acrylic polymers [1]. The first three types of superplasticizers disperse by electrostatic action, while the last kind disperses predominantly by steric action, generally with increased fluidizing power [2].
In contact with water, cement particles release a high number of ions that dilute from their surface. Due to the great affinity between water and cement, cement particles tend to form flocs that prevent particle dispersion and retain water in their structure. Retained water contributes inefficiently to cement hydration and strength development. In this sense, SPs create repulsive forces among cement particles that prevent flocculation and promote mobility. Recent studies have confirmed the influence of different types of SPs on cement hydration and the corresponding affectation of the microstructure of the hardened material [3].
SP efficiency is defined as the capacity to increase the flow of a mix and its persistence over time. It not only depends on the superplasticizer and cement compositions but also on the manner in which they are mixed (mixing capacity, mode of incorporation, mixing time) [4].
Cement characteristics, such as fineness, composition (contents of C3A, calcium sulphate, and alkalis), and types of mineral additions contained, are key factors for the interaction with SP [5,6]. Moreover, important characteristics of SP include molecular weight and distribution, length of the polymeric chain and, in the case of naphthalene-based admixtures, the nature of the counter-ion included in them [2,6].
The anhydrous phases and hydration products of cement do not adsorb the same amount of SP [5]. The C3A phase displays higher adsorption capacity of admixtures, due to its more positive zeta potential values, than C3S and C2S phases. In the presence of gypsum, admixtures and sulphates compete for adsorption on C3A, with a more favourable reaction with sulphates [5]. Therefore, more quantity of admixture remains available in the aqueous phase to exert a flowing effect on the paste. In this sense, the amount of sulphate in solution depends on both the w/cm ratio and temperature [7]. Thus, indirect influence by the amount of water on the efficiency of the admixture would be revealed. This is also helpful to explain the differences in the efficiency of admixtures with different cement types.
Nowadays, the cement market is dominated by cement types other than Ordinary Portland Cement (O). Even O itself can contain minor constituents different from clinker or setting regulator (up to 5 % of blast furnace slag according to IRAM 50000). Some of the most common blended cements are Blended Portland Cement (B), e.g. with up to 35 % admixtures (including a combination of limestone powder, blast furnace slag and natural pozzolans or at least two of them), and Pozzolanic Portland Cement (P), e.g. with up to 50 % of natural pozzolan.
Adding natural pozzolan to cement does not necessarily modify water demand for a given consistency level [8]. The effectiveness of the different types of water reducers has been previously addressed for the particular case of pozzolan-admixed cement type [9]. However, in the particular case of polycarboxylic-based SP, this efficiency has been reported to be lower for pozzolanic cements than for limestone or slag blended cements [10]. As regards SPs efficiency to increase strength by reducing w/cm ratio, similar results for O, B and P have been obtained by Erdogdu [11]. In terms of the influence of slag, it has been determined that its interparticle forces are stronger than those of Portland clinker particles [12]. However, the efficiency of SP on cement is increased with slag content, mainly due to the greater dispersing effect that slag particles have [2,13]. This higher efficiency of SP has also been confirmed by concrete workability with replacement ratios by slag of 15-20 % [14].
On the other hand, mineral admixtures do not contain C3A, and therefore they act as diluting agents of the C3A content of clinker, causing lower net adsorption by this phase and a corresponding lower admixture demand for a given consistency in comparison with non-blended cement. However, significant adsorption of naphthalene and melamine based admixtures, and vinyl copolymer on slag has been reported [15], which implies that a reduction in the demand of these admixtures is not directly related to clinker replacement ratio. Moreover, recent studies have shown that the type of SP plays a significant role in the stability of ettringite formed during hydration [16]. This affinity is affected by cement aging, depending on the C3A content of cement [17]. Then, the efficiency of SPs with aged cements would be more stable for blended cements than for OPC.
Concerning flowability loss over time, there are no reasons for which incorporation of admixtures, such as slag or natural pozzolans, should modify the efficiency of an SP. However, in order to recover flow level after a certain mixing time, while slag-containing concretes need admixture re-doses similar to those of concrete without admixtures, it has been informed that natural pozzolans may require slightly higher re-dosing [18]. On its own, limestone powder accelerates cement hydration [19] and could, as a result, accelerate flowability loss rate. On the other hand, limestone reacts partially with C3A to form new carboaluminates [20]. This in turns also contributes to a reduction in the degree of adsorption of the admixture and an increase in its efficiency. The net impact will be the result of which of the two effects is more predominant.
For optimizing SP/cement, the maximum percentage of SP to be used should be determined (once the w/cm ratio has been decided) based on the saturation point for the water-cement-admixture system. This is evaluated using the flow level in pastes or mortars. If SP dosage exceeds the saturation point, some issues such as setting time delay, segregation or increase in the viscosity of the mix, may occur, causing few significant changes in flow value but subsequently higher costs [5]. However, it is common to study system compatibility only in the fresh state and not to link it with properties in the hardened state, disregarding the fact that SP could affect strength development when used at dosages lower than the saturation point.
The aim of the present study is to evaluate the efficiency of water reducer admixture-cement systems in mortars made with different binary and ternary Portland cements. Different properties in the fresh state and their link with some properties in the hardened state are also assessed. The analysis is carried out from an engineering point of view, considering parameters which may affect the SP dosage for a target consistency.
2. Experimental
2.1 Materials and mixtures
Four Portland cement types were evaluated in this study: Ordinary (from two origins: O1 and O2), Blended (B) (containing approximately 17 % of limestone powder and 12 % of slag) and Pozzolanic (P) (containing approximately 40 % of natural pozzolan). Table 1 presents the physical and mechanical properties and chemical compositions of the studied cements. Table 2 shows the potential Bogue mineralogical compositions of O1 and O2.
The properties of the chemical admixtures under evaluation, a plasticizer (M), and three superplasticizer (S, P, and V) are presented in Table 3. Two river siliceous sands (fine and coarse) with different fineness modulus were selected (Table 4).
For comparative purposes, reference non-admixed mortars were produced for the four cement types so as to evaluate the properties in their hardened state. Then, efficiencies of superplasticizers in varying dosages and with constant proportions of reference mixes were evaluated.
Among these, the mortars that showed the best performance in the fresh state were replicated, including a combination of superplasticizer and the plasticizer (M).
Table 5 shows mix proportions for mortars. Nomenclature corresponds to the cement and type of admixture used (only a letter is indicated for reference mortars, i.e. non-admixed mortars). The mortar mixes were prepared in accordance with ASTM C305. The dose of admixtures is expressed in % w/w of cement.
2.2 Testing methods
Flow and consistency of fresh mixes were determined by the flow test (Fig. 1) and the slump test (Fig. 2), respectively. To evaluate the active period of SPs, these tests were performed immediately after mixing and 30 minutes after the cement got in contact with water.
The flow test is commonly applied to select materials, and to proportion pastes and mortars for self-compacting concretes [2, 21-24], but it has not been standardized yet. This method is applied with the aid of a frustum cone. The cone is placed on a plane, smooth, levelled and non-absorbent surface, and filled with the mortar to be tested. The mould is then lifted, and the mortar flows freely. The value of the flow is the average of the two perpendicular measurements of the diameter (Fig. 1).
The slump evaluation was carried out using an “Abrams mini cone” (Fig. 2). This is a scaled version of the standard Abrams cone, corresponding to 1/8 of its volume. The methodology used followed regulation NCh 2257/3 [25].
For assessments in the hardened state, prismatic specimens (4 cm x 4 cm x 16 cm) were moulded for each one of the studied mortar mixes. They were then cured under water saturated with lime at 23 ± 2 °C until tested.
Compressive strength at 7, 28 and 90 days as well as density and water absorption at 28 days were evaluated. The determination of density and absorption was carried out according to ASTM C642 and compressive strength was determined following ASTM C349.
3. Results and analysis
For the sake of clarity, the results are presented in two graphs: in a) mortars with SPs (S, V and D) and b) mortars with plasticizer and SPs (MV-MD).
3.1 Fresh State
Fig. 3 shows flow in relation to the admixture dose. From the comparison of the two mortars with ordinary Portland cement (O1 and O2), it can be observed that O1 shows higher fluidity than O2, in correspondence with a lower C3A/calcium sulphate (1.91 versus 2.20 for O1 and O2, respectively computed from contents of SO3 and C3A, Tables 1 and 2). Therefore, the higher flow value for O1 may be explained as the result of a higher amount of admixture available to disperse C2S and C3S phases.
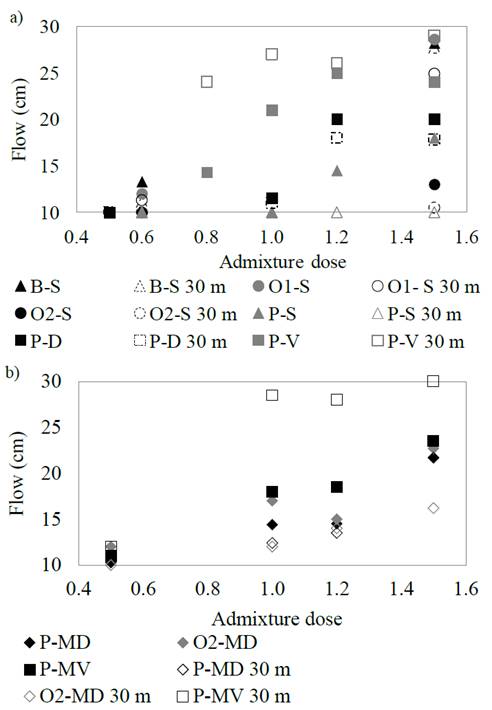
Source: The authors.
Figure 3 Initial and 30 min flows of a) mortars with SP and b) mortars with plasticizer and SP as a function of the admixture dose.
Also in Fig. 3, admixture S shows better performance with cement O1 and B, while compatibility with the other cement types is limited. This is also in agreement with the fact that the other cement types showed a higher [Al2O3]/[SO3] (however, although for blended cement an estimation of C3A content from Bogue equation is not possible, a qualitative analysis is still viable).
Therefore, the most probable reason for such compatibility is chemical composition. Moreover, some cement grinding aid admixtures are known to have an important effect on the compatibility with SPs, but this hypothesis could not be corroborated in this study as only commercial cements were analyzed and this information is not provided by manufacturers.
On the other hand, the admixture V with cement P shows increased flow values for 30-minute periods in comparison with those determined immediately after mixing, which shows excellent compatibility with cement P.
When mortars made with plasticizer and SP are compared with those made with SP only, an improvement can be appreciated in the flow parameters for the combinations P-MD (with respect to P-D) (Fig. 3). Regarding the combination P-MV, an incompatibility between admixtures is observed, as the combined action shows less efficiency than that obtained for the P-V series; this is attributed to the different origins of their compositions (Table 3).
Fig. 4 presents the results of the slump as a function of the admixture dose. It can be observed that, for mortars with plastic consistency, such as P-D, P-S, O1-S, O2-MD, and P-MV, flow values rise with increasing admixture dose. This greater fluidity of the mortars with 1 % of admixture, in comparison with those that have a lower admixture dose, was not revealed by the results from the flow test (Fig. 3). This is due to the different range of sensitivity of both methods. For the P-S series, a noticeable decline in the values of the slump is observed at 30min, which also rises with increasing admixture dose.
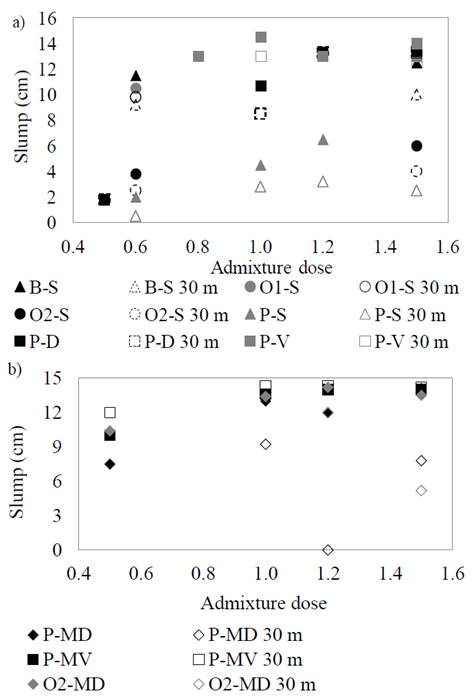
Source: The authors.
Figure 4 Initial and 30 min flow of a) Mortars with SP and b) mortars with plasticizer and SP as a function of the admixture dose.
Fig. 5 shows relative slump loss 30 minutes after mixing in relation to the admixture dose. In almost all cases, it may be observed that the smallest slump loss is obtained for a dose of admixture between 1 and 1.2 %, which indicates the saturation point for the cement-admixture systems. Negative values in Fig. 5 show that slump after 30 minutes was higher than the initial value. As observed from the fluidity tests, this is the case of P-MV mortars and, to a lesser extent, P-V mortars.
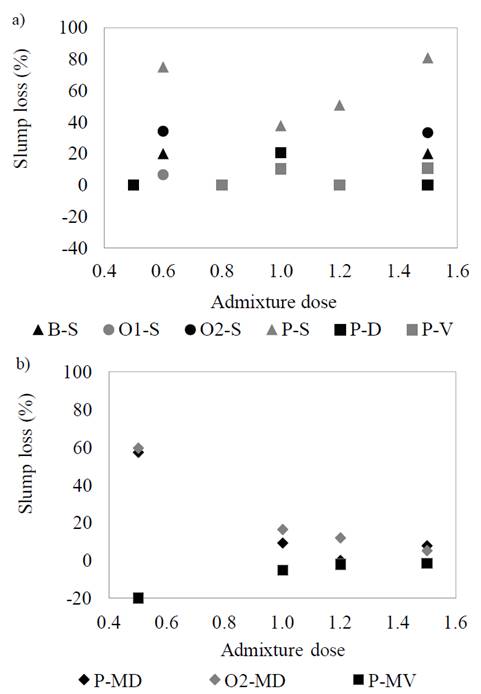
Source: The authors.
Figure 5 Relationship between of slump losses and admixture dose for a) Mortars with SP and b) mortars with plasticizer and SP.
Fig. 6 shows the relationship between the values of slump and flow. It may be observed that for most of the stiff mixes, slump reveals great differences in consistency among mortars, while lower differences for slump values are obtained for increasing values of flow.
In the case of concrete, the slump method is considered representative of the level of consistency for values up to 60 % of the cone height (18 cm). The same criterion applied to mortars leads to a maximum slump of 9 cm. As it can be noted even for the outlier points (P-S, O2-S, and B-S 30m), the results obtained can be consistently divided based on this limit. The use of Abrams mini cone is adequate for mortars with plastic consistency, as it shows higher sensitivity for differences within this range of values, and the flow test method is more appropriate for evaluating the consistency of fluid mortars.
3.2 Hardened state
Fig. 7 shows density values for hardened mortars determined at saturated surface dry condition. It is clear that the use of admixtures may cause air occlusion and originate variations in the density of mortars. It can also be noticed that, except for mortars with admixture D, in all cases the reduction in density, compared to the reference mortar (P= 2.16; B= 2.16; O1= 2.15; O2= 2.16 g/cm3), is less noticeable with increasing admixture dose. This fact can be explained by the net effect of the competing factors of improved compactability and increased air content, caused by the admixture.
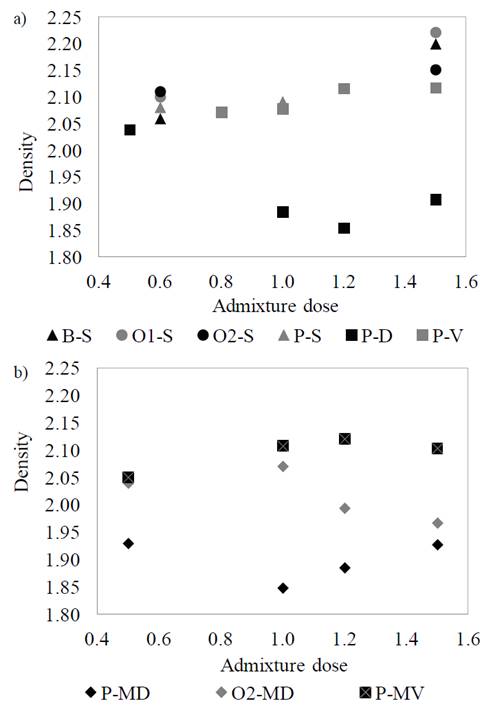
Source: The authors.
Figure 7 Density saturated surface dry condition for a) mortars with SP and b) mortars with plasticizer and SP.
Fig. 8 shows values for 24 hours water absorption. In the case of admixed mortars with cement P, water absorption increases for all mixes between 35 % and 70 % more than for the reference mortar (P= 4.94 %). Admixed mortar mixes with cement O2 increase their absorption up to 83 %, compared with the reference mortar (O2= 4.30 %), independently of the type of admixture used. As in the case of density, this is attributed to the air occlusion caused by the admixtures, which creates macropores and increases water absorption. On the other hand, for mortars with cement types O1 and B, the adsorptions values of the mortars containing admixtures were similar to or lower than those from the reference mortars (O1= 5.27 %; B= 6.12 %).
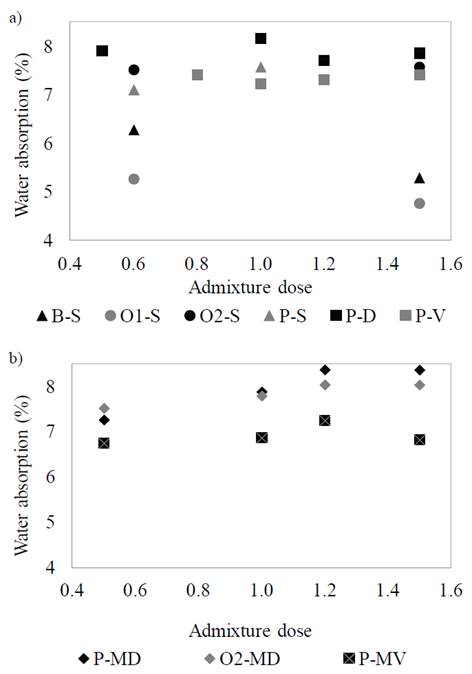
Source: The authors.
Figure 8 Water adsorption for a) mortars with SP and b) mortars with plasticizer and SP.
Table 6 shows compressive strength and corresponding standard deviations of mortars determined at 7, 28 and 90 days. Nomenclature includes the admixture dose in ‰ with respect to cement weight. Here it may be observed that series O2-S-6 shows high standard deviation for the three ages (7, 28 and 90 days), whereas mortars P-S-15, P-D-12, P-D-15, P-V-15 and P-MV-8, P-MV-12 and P-MV-15 show high standard deviation at 90 days, and P-MD-5, at 28 days.
Series O2-S-6 shows high standard deviations at the three ages. This suggests inadequate compaction of specimens. A reliable comparative analysis is therefore not possible in this case. What may be observed is that the strength of mortars O1-S is substantially higher than that of the reference mortar, with decreasing difference for increasing age. This outcome is also presented, to a lesser degree, for P-V mortars in spite of the great compatibility shown in the fresh state. Likewise, the relative strength of P-MD series decreases with test age.
For a more reliable analysis of the influence of admixtures on compressive strength, a statistical analysis through paired values (mortar with admixture - reference mortar) was done for the three ages. The p-values were determined for the null hypothesis of equal mean values for each mortar containing admixture and the corresponding reference mortar. Table 7 shows the results obtained for this analysis. It can thus be observed that mortars O1-S and P-V show a p-value <0.05 for the three ages assessed, with the same condition for P-MD at 7 and 90 days.
Table 7 p-values for hypothetical same compressive strengths for admixed and reference mortars.
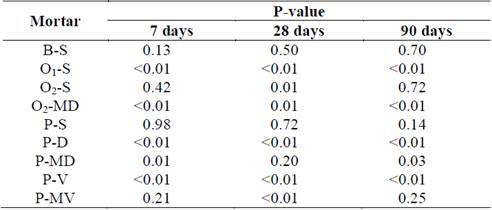
Source: The authors.
From the statistical analysis (Table 7), it can be seen that mortars O1-S and P-V show substantially higher compressive strengths than those of reference mortars at the three ages. This may be attributed to improvements in the compaction degree produced by the used admixture and also due to the possible strength accelerator effect of SPs in the cement-admixture system. Conversely, P-D mortars show significantly lower strengths with respect to the reference mortar at the three ages. This must be attributed to air occlusion in the cement-admixture system, which is consistent with the low density and high water absorption of these mortars in the hardened state. Regarding mortars O2-S, inconsistent p-values were obtained for the different ages; therefore, analysis of these results is not possible.
Finally, for the rest of the mortars, p-values do not allow one to discard the null hypothesis, i.e., no statistically significant differences in compressive strength due to the incorporation of these admixtures could actually be identified.
On the other hand, it is noticeable that in mortars where absorption increases with respect to the reference mortar, no effects on the compressive strength were found. This fact suggests the need to carry out studies that evaluate durability behavior in connection with SP doses.
4. Conclusions
The following conclusions may be drawn from the results in the fresh and hardened states of mortars elaborated with binary and ternary Portland cements (Ordinary, Blended and Pozzolanic), and using different types of superplasticizer (SPs).
First, maximum fluidity of almost all SPs was found for dosages between 1-1.2 %, independently of the SP composition and type of cement evaluated.
Furthermore, the flow method proved to be appropriate for evaluating the fluidity of mortars with fluid consistency, whereas the Abrams mini cone showed more sensitivity in the case of mortars with plastic consistency, being suitable whenever slump was lower than 9 cm.
In addition to this, an increase in water absorption of admixture mortar, with respect to reference mortars, was noticed in some cement-admixture systems. This fact needs to be considered when the cement-water reducer admixture system is set, due to the implications that increased absorption has in terms of the durability behavior of mixes.
Moreover, the compressive strength of mortars shows that the water reducer can cause increase or decrease, even when the compatibility evaluated in the fresh state is good.
Finally, although the efficiency of cement-admixture systems is commonly adjusted upon the evaluation of fresh properties, the impact of SPs on the properties in their hardened state is derived from the combined effect of air occlusion in the fresh state and the affectation of the degree of hydration of cement in its hardened state. Therefore, these properties in the hardened state provide valuable information for selecting the most convenient constituents and their proportions. This proves to be a better evaluation method in comparison with the common testing technique carried out exclusively in the fresh state.