1. Introduction
Norte de Santander is known for being a clay region par excellence and one of the regions with the best clays in the world, it is for this reason that 70% of its economy revolves around companies that are engaged in the transformation of this material in coating products but above all in masonry products (bricks, tiles and blocks), being the extrusion formed the type of ceramic process most used in this region, this is why only one of 60 companies legally constituted currently is dedicated to the manufacture of pressed ceramic tiles [1,2].
It is for this reason that it was necessary to study an alternative to improve the pulps used in these extrusion processes as the manufacturing companies have begun to detect an increase in the percentage of breaks and defects in their final products, which is why today there is more interest in the search of materials that increase the mechanical strength of the ceramic pieces and thus increase their productivity and decrease the maximum manufacturing costs [3]. One feasible solution that has been investigated is the incorporation of industrial waste in clay bodies. In particular, the use of these is investigated through their addition to natural raw materials used to manufacture ceramic products [4-7].
In works and articles published previously, it was found that aluminum oxide shows in pastes of ceramic products for pressing an excellent behavior serving as an effective substitute for any existing degreaser. To date it has not been studied the mechanisms of action of this material used in furnaces of ceramic companies, nor have studies been found in the literature on the use in this type of compositions in extrusion processes [8]. For this reason and in view of the need to increase the mechanical strength of the products this research has been proposed in order to verify the efficiency of the aluminum oxide in pastes used in the extrusion forming process and to analyze the effects of the change in the formula and the possible modifications in the behavior of the composition in the different stages of the process, as well as in the properties of the tile.
2. Materials and methods
The materials used in this research were a clay from the Guayabo formation of the Norte de Santander region (Colombia) usually used in the manufacture of blocks, bricks and tiles; aluminum oxide (corundum) powder of ASTM 200 mesh (75 μm) of white color at 99% purity from the enterprise Cerámicos Asociados.
Both natural materials were initially dried at 110 °C before obtaining the representative samples by quartet. The clay was then analyzed by X-ray fluorescence (FRX), particle size distribution and plasticity index. The particle size distribution of the clay was determined by sieving and sedimentation according to ASTM D422-63, where it calculates the equivalent spherical diameter of the materials using Stoke's law.
The chemical composition was obtained by X-ray fluorescence in an equipment brand Panalytica, model Axios Max. The plasticity (IP) of the clay material was determined by the Pferfferkorn method, which determines the consistency value of a material to be formed by the extrusion method, exerted by the compression of the clay material when hit with a pylon hammer which runs a fixed path.
For the research, pure clay was used as the standard reference; the mixture was prepared with an amount of 10% by weight of aluminum oxide added to the clay, these were referenced as P0 and P10 respectively throughout the investigation. Prism specimens of 13 cm × 8 cm × 1 cm were molded with a percentage of extrusion water of 37.5% for pure clay (P0) and 28.6% for the mixture (P10) using a laboratory extruder with vacuum New Wave model with rectangular mold and a gauge pressure of 35 mmHg. From each composition, a specimen was taken and subjected to a dilatometric analysis (DIL) which was developed in a Dil 402 C dilatometer, where the coefficient of thermal expansion and the characteristic temperatures of glass transition and softening were determined (Tm and Tg), the equipment was operated with a heating rate of 10 °C/min to a maximum temperature of 1000 °C using a 25 mm × 6 mm probe. The other specimens were dried at room temperature (±30 °C) for 96 h and then subjected to convection drying at 110 °C for 24 h in a drying oven.
The cooking process was carried out in a laboratory electric muffle with final temperatures of 900 ºC, 1000 ºC, 1100 ºC, 1150 ºC and 1200 ºC, the first four temperatures are normally used in the manufacture of clay tiles and bricks in the region. The heating rate for cooking was 3 °C/min without heating table at maximum temperatures. The cooling was performed by natural convection inside the oven after it was turned off. Technological properties were evaluated using four specimens per composition, properties such as bulk density, linear shrinkage, water absorption, flexural strength and deep abrasion were calculated using the mean values in each analysis. The bulk density was measured by dividing the mass by the external volume of each specimen. Linear shrinkage was obtained by varying the length of the samples using a calibrator precision ±0.01 mm . Water absorption was determined according to the standard procedures of standard NTC 4321-3. The flexural strength was obtained using the standard procedures of standard NTC 4321-4. Finally, the tribological property or wear resistance of ceramic tiles was determined according to norm NTC 4321-6. This property was determined by the wear resistance by calculating the length left by the constant pressure of a rotating disk of a 200 mm diameter and an abrasive material (alumina F80) on the surface of the specimen at a rotation speed of 75 rpm (the development of testing is performed by wearing the specimens during 150 turns).
3. Results and discussion
3.1. Physicochemical characterization of clay
Table 1 shows the chemical composition of the clay material in which it can be observed that it presents SiO2 and Al2O3, as the most predominant oxides [9,10]. These oxides are mainly associated with the kaolinite structure. The contained silica is associated with the quartz particles and the high percentage of alumina is associated with gibsite. The value of 3.81 molar ratio (SiO2/Al2O3) in the clay indicates a high presence of kaolinite [9,11]. Fe2O3 is the main oxidant that gives the clay a red hue and according to the data in Table 1, the clay presents a high percentage of this oxide, which will give it after cooking an intense red hue, this is an important technological aspect because with this material, products cannot be made with clear shades [12].
Another important aspect to consider in clay is its high percentage of K2O which will generate a material with a low cooking range, since this oxide is considered the main flux in the clay materials [13,14]. In the same way it can be detailed that the value of LoI is high, this indicates a loss of mass in enormous cooking due mainly to the dehydroxylation of clay minerals, to the oxidation of the organic matter but especially to the decomposition of carbonates, hydroxides and sulfates, the latter associated with the high value of SO3 which during cooking can generate not only contamination in the furnace atmosphere but also contamination in the material causing aesthetic problems such as veils, blooms or stains in its structure or changing the color of the product darkening even more its hue as seen in Fig. 1 [15-18].
Fig. 2 shows the distribution of the particle size of the clay made by the method of the 152H hydrometer, within the graph it is shown the fraction of clay, silt and sand [19]. The clay fraction is associated with fine minerals (<2 μm) which are responsible for the plasticity of the material, as described, the material has a high percentage of clay fraction of 90.23% and a low fraction of silt and sand of 8.45% and 1.32% respectively, this is the reason for the high plasticity index (40.3%) and the large amount of extrusion water used to make clay molding as can be seen in Table 2 [20].
This is an important aspect to take into account as the addition of corundum affects in a tangible way the decrease of this high amount of extrusion water reducing it by 23.7%, generating not only a control in the percentage of water of tempering or of rehydration, the main cause of breakage and deterioration of the material in the drying but also the decrease in the formation of defects during molding, in addition to a lower economic cost in the process window during the wetting stage of the material, all directly influenced by a progressive increase of the concentration of clay minerals in the structure of the clay.
3.2. Process parameters in wet and dry conditions
As seen in Table 2, the addition of the aluminum oxide to the clay significantly improves the working parameters and properties of the material under wet and dry conditions. As mentioned, the amount of extruded water is significantly reduced, helping to reduce differences in the drying of the parts, controlling serious problems such as cracks and deformations, speeding the drying process (decreasing time and costs), etc., all this without affecting other properties such as density, which is directly related to the molding conditions and the volume of water added [21,22].
It is detailed that the density of P10 increases in 11.0% and in 4.9% in wet and dry respectively, in comparison with clay, generating that the material is more resistant, controlling its dry shrinkage and increasing its mechanical resistance, typical behavior when the density is improved. The reduction in linear shrinkage results in a lower percentage of breakages in the products by cracking, especially those that appear in the last phase of the drying cycle and the increase in mechanical resistance guarantees the manufacture of parts for coating or parts of large masonry because as it is shown, it gives values of 45.5 kgf/cm², when required for dry products at international level for this type of products values are between 25 kgf/cm2 and 30 kgf/cm² with the aim of avoiding breaks of the pieces at this stage of the process [23,24].
It is important to note that with the reduction in shrinkage and the increase in dry strength by the addition of aluminum oxide it will provide the possibility of using only this type of residue in pastes formulations for construction products since it will not be necessary to add high percentages (between 20% and 30%) of degreasing materials, which is what is normally used to increase porosity and reduce drying shrinkage especially in plastic materials with fine granulometry and with large specific surfaces such as the material investigated; This is an important contribution to the process because it reduces time in the preparation of these degreasers and reduces the final costs for the acquisition of non-plastic raw materials [25].
3.3. Thermal and dilatometric behavior of the clay by the addition of corundum
Regarding the thermal behavior, the sample P0 has a glass transition temperature (Tg) of 621 °C and softening (Tm) of 691 °C. The sample P10 presents Tg of 637.8 °C and a Tm of 710.4 °C, with these results it is observed that the material to add the residue has a better performance in the resistance to high temperatures since its softening point increases by 2.81% by improving in the cooking step the time of appearance of the liquid phase and controlling the sintering which decreases the viscosity of the material and the deformation thereof [26,27].
Fig. 3 shows the dilatometric curves of P0 and P10 while Table 3 shows the values corresponding to the linear coefficients of thermal expansion. As shown, the two curves have a similar behavior with the difference that the coefficient of expansion is lower in P10 indicating that the corundum will generate a control in the dimensions developed by the high plasticity in the clay which gives us the idea of a reduction in the stress differences that produce cracks in the heating stage [13,28].
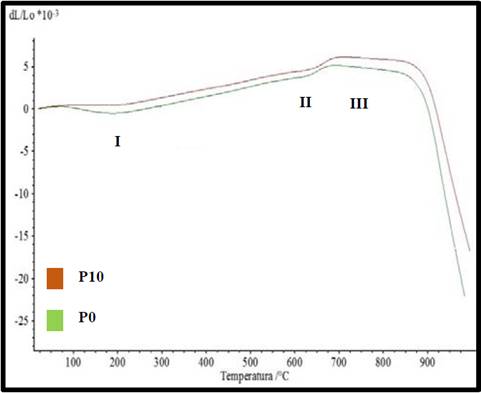
Source. Center for Research of Ceramic Materials - CIMAC.
Figure 3 Dilatometric curve of the investigated samples.
Table 3 Coefficient of thermal expansion of the samples.

Source. Center for Research of Ceramic Materials - CIMAC.
It is observed initially a rectilinear section which is interrupted in the peak I when arriving approximately to the 200 ºC, possibly it is in this point where the water of constitution completely evaporates of the structure of the specimens; It is explained that the coefficient of expansion (α50-300) is higher in P10, possibly because the corundum generates an increase between the reticular spaces of the clay material causing the water to evaporate rapidly and generating an increase in its dilation from the starting point up to 200 ºC, it is recommended that around this temperature a decrease in the cooking time is exerted to avoid high tensions differences that occurs in this phase of the process, especially in materials as clayey as the one studied.
From point I another straight section with a progressive increase in the slope up to 600 °C (Point II) is initiated, it is in this area where the allotropic change of quartz develops, the most problematic turning point in the whole cycle of cooking of any ceramic material, at this point the values of the coefficient of thermal expansion of P10 decreases up to 6.9% with respect to P0, generating a greater control in the formation of microcracks, characteristic defect in this phase.
Finally, the curve reaches a horizontal section, which reaches point III, it is here where the slope begins to decrease and the softening of the material is indicated beginning the contraction. It is important to note that the low coefficients of expansion generated by the addition of corundum will generate the possibility of sintering the material at high temperatures, as this will control the increase in the liquid phase content of the specimen and improves the densification thereof, which will be reflected in the improvement of mechanical properties due to the decrease in porosity [29].
3.4. Technological behavior as a function of temperature and addition of corundum
Figs. 4 to 8 show, respectively, bulk density, linear shrinkage, water absorption, flexural strength and deep abrasion in the baked condition of P0 and P10. It is observed in Fig. 4 that the apparent density for P10 decreases between 900 °C and 1100 °C with respect to P0, which indicates that the mechanisms of consolidation of the particles at the cooking temperatures typical for ceramic processes in the region are not efficient to increase this property but that are improved when corundum is added to the material, as an increase is observed above 1100 ºC, this is probably a consequence of the refractoriness of the corundum, developing this behavior in the clay material at elevated temperatures being a significant contribution as it contributes to control the porosity at elevated temperatures, increasing mechanical and tribological properties as detailed later [30,31].
The linear contraction in cooking is detailed in Fig. 5; this is influenced by the cooking temperature. These results indicate moderate changes between 900 °C and 1000 °C. However, above 1100 °C significant changes can be observed in P10 since linear shrinkage decreases in comparison with P0, this is associated to the sintering mechanisms and is generated by the densification of the samples as observed in Fig. 4, the importance is that as the temperature increases the control in the contraction does not change since it continues to decrease, this indicates a good behavior in any temperature range [32].
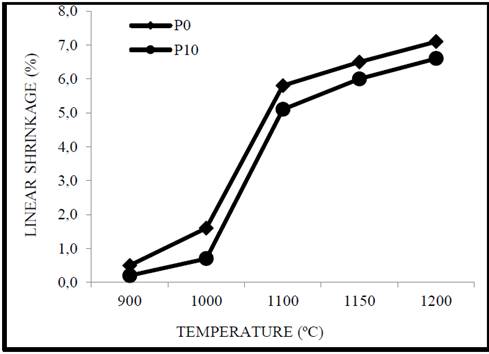
Source. Authors.
Figure 5 Graph of the linear shrinkage of the clay as a function of the addition of corundum and the cooking temperature.
In Fig. 6, it is observed that the water absorption is elevated between 900 °C and 1000 °C in P0 and P10 but decreases markedly above 1100 °C. The obtained values of water absorption at low temperatures indicate that the mechanisms of particle consolidation were not effective, as it has been mentioned during the investigation and can also be attributed to the high percentage of alumina in the clay that generates a refractory behavior as well as aluminum oxide [32,31]. It should be noted that P10 shows a significant decrease, this is associated with the increase of dry mass density. In general, the samples show a decrease in the water absorption above 1100 °C which generates the manufacture of products with a higher added value, in addition to complying with Colombian standards for the manufacture of masonry products and coating without the need to reformulate the pulp with other materials that would increase the cost of the final product [30].
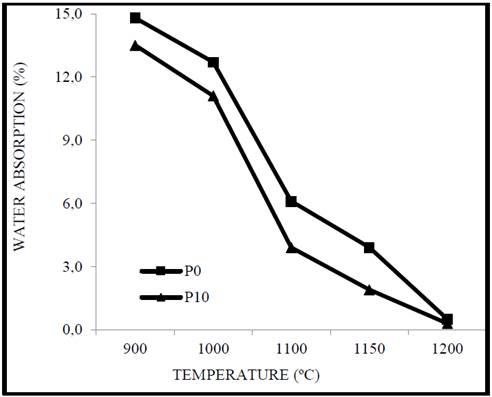
Source. Authors.
Figure 6 Absorption of water from clay as a function of corundum and cooking temperature.
In ceramic processes the sintering contributes to improve the flexural strength considering that optimizing the cooking temperature it is possible to densify the material better and decrease the porosity which in turn reduces the formation of cracks, defects that generate the reduction of the mechanical resistance of the products. As shown in Fig. 7, this property increases as the temperature increases generating more resistant materials and improving the final use of the products. Thus the presence of aluminum oxide helps to increase the modulus of rupture in the pulp at temperatures between 900 °C and 1200 °C in 25.4%, 34.1%, 50.3%, 52.2% and 58.7% respectively, being progressive and controlled increases of P10 with respect to P0 [33].
The tribological characterization was carried out by means of the deep abrasion test, the results obtained for P0 and P10 are shown in Fig. 8, comparing the wear resistance (volume removed of material) exerted by the abrasive agent on the surface of the specimens; In both cases the reduction of the volume removed is observed as the temperature increases, this can be attributed to the increase in the densification and the reduction in the porosity, as this property is related to the open porosity of the material [34-36]. Thus the addition of aluminum oxide minimizes wear resulting in an improvement in the protection of construction products and increasing its use especially in coating products where abrasive agents attack with greater force.
Finally, it can be said that the mixture of natural clay materials with residues such as aluminum oxide is effective and promising helping not only to the increase in the technical characteristics of the products but also to the reduction in the pollution of the planet, as well as minimizing cost of production that will ultimately be reflected in the final value of the product and generating a trend product with technical and decorative characteristics superior to the ceramic, with higher added value, which in many cases can greatly exceed the price of the traditional pottery [22,37,38].
4. Conclusions
The pure clay is composed of 90.23% of materials with a particle size of less than 2 microns, being this the reason why it has an extrusion behavior that is not acceptable for the processing of the clay body. The problem is solved with the addition of oxide of aluminum to the paste generating not only the reduction of cracks and deformations but also the addition of this residue to improve its workability.
Aluminum oxide effectively controls the liquid phase content and the viscosity of the paste in the cooking step above 1000 °C, since a more compact and more dense product is observed, as evidenced by the minimal alterations in the linear contraction and the water absorption.
The addition of aluminum oxide to the clay produces a very compact and resistant material, essential for building materials, as it has a low porosity, which gives it excellent mechanical and chemical properties, which makes it useful for use as a pavement or external cladding in cold areas.
The results show a high resistance against wear exerted by the abrasive agent during the development of the abrasion resistance test, which facilitates its use in environments of intense pedestrian traffic or in industrial environments, making this paste essential to manufacture materials suitable for the paving of high-traffic spaces and environments such as schools, commercial centers, airports, industries, etc. In addition to having low open porosity, manufactured products are effective for placement in open (exterior) environments such as facades being more resistant to the inclemencies of the environment (humidity,
Ttemperature and resistance to wear). An environmentally important aspect is that aluminum oxide begins to generate excellent structural, mechanical and tribological properties at temperatures above 1000 °C, which makes feasible to manufacture masonry products (products of higher consumption in the region) without requiring too high temperatures, helping to reduce the energy consumption during the cooking stage, generating in turn less consumption in fuel and greater profitability in the processes.