1. Introducción
La técnica de fotolitografía ha contribuido al desarrollo de dispositivos con base en los semiconductores, en las últimas cuatro décadas han alcanzado un alto nivel de sofisticación, permitiendo el desarrollo de la micro/nano electrónica, MEMs (Sistemas microelectromecánicos) NEMs (Sistemas nanoelectromecánicos), microfluídica, entre otros [1-3].
Las primeras técnicas de fabricación de circuitos integrados por la baja complejidad y costo son por contacto y proximidad con radiación UV, obteniéndose resoluciones de 1-10 µm. Pero se reemplazarían debido a las exigencias en la industria de los semiconductores [4]. Luego surge la técnica por proyección mejorando la resolución de los patrones impresos hasta el orden de los nanómetros, calidad de los micro/nano dispositivos y alta tasa de producción.
Mejoras en las fuentes de radiación, sistemas de lentes y resinas fotosensibles, se han dado por el esfuerzo de la industria, centros de investigación y la academia, con el fin de seguir lo planteado por la ley de Moore, donde el número de transistores en un circuito integrado se duplicará cada dos años [2].
Reducción en el tamaño de unidades lógicas (transistor) en un circuito integrado ha representado desafíos tecnológicos y económicos [4-7]. A cada reducción se le ha denominado “nodo” y está relacionado con la dimensión crítica (CD), parámetro que mide la calidad de las estructuras fabricadas a partir de su grosor, rugosidad y altura y determina el límite en la resolución de los sistemas de fotolitografía [5,6]. En los últimos 10 años se han desarrollado nodos que van desde los 45-10nm y se prevé que en el 2020 se alcanzará el nodo de 5nm [6]. De ahí la importancia de controlar todos estos parámetros que son operacionalmente imprescindibles. Por lo tanto, la producción de un nuevo nodo, implica cambios en instrumentación, materiales e infraestructura ocasionando un aumento en los costos de producción [6,8].
La instrumentación de mayor costo en los sistemas de fotolitografía son las fuentes de radiación, sofisticados arreglos de lentes, sistema electromecánicos para alinear la fotomáscara, equipos de esparcimiento de fotoresina de alta precisión, sistemas de metrología para inspeccionar las etapas de producción y la infraestructura donde se controla la temperatura, humedad, flujo y cantidad de partículas en el aire [3].
Por tal razón, el acceso a sistemas de fotolitografía e infraestructura a pequeños y medianos laboratorios de investigación es limitado debido a su elevado costo, imposibilitando la investigación en las disciplinas de micro/nano fabricación y otras áreas de ingeniería [9]. Para abordar este problema se ha desarrollado instrumentación adaptable a los recursos económicos e infraestructura como son fuentes de radiación basadas en LEDs UV [9,10] y equipos de esparcimiento de fotoresina [11,12]. Sin embargo, a la fecha no se han reportado sistemas de fotolitografía que integren esta instrumentación y dado que la industria de los semiconductores y centros de investigación continúan desarrollando nuevas técnicas de fotolitografía, es necesario acceder a instrumentación especializada y así contribuir al avance de la próxima generación de micro/nano dispositivos.
En este artículo se presenta el diseño e implementación de un sistema de fotolitografía, siguiendo el proceso de diseño y desarrollo de productos donde se identifica materia prima y módulos de equipo que conforman el sistema, se determina las condiciones óptimas de fabricación de microdispositivos, se realiza caracterización con microscopía óptica para determinar la calidad de los microdispositivos, se muestran los resultados, discusión y conclusiones.
2. Técnica de fotolitografía
Consiste en transferir un patrón a la superficie de un sustrato o película delgada, a través del proceso: 1) limpieza del sustrato para eliminar compuestos orgánicos y partículas de polvo. 2) Esparcimiento de fotoresina sensible a la radiación UV en la superficie del sustrato. 3) Calentamiento suave, para mejorar la adhesión de la fotoresina en la superficie del sustrato. 4) Irradiar con UV la superficie de la capa de fotoresina sobre el sustrato a través de una fotomáscara con los patrones a imprimir mediante las técnicas: por contacto, donde la fotomáscara se presiona sobre sustrato, proximidad donde la fotomáscara está separada del sustrato o proyección donde se usa un sistema de lentes (Fig. 1). 5) Revelado donde se elimina las regiones que fueron irradiadas con UV. 6) Grabado de la superficie del sustrato en las regiones donde el material fotorresistente fue removido con el proceso de revelado, por medio de técnicas húmedas (solución ácida) o secas (plasma). 7) Remoción de fotoresina residual de la superficie del sustrato por técnicas húmedas o secas. 8) Inspección de la calidad de los patrones grabados con alguna técnica de microscopia [4,13].
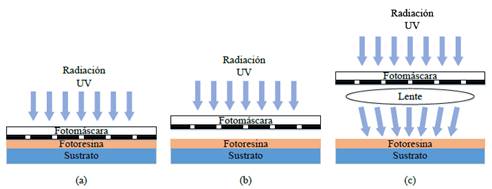
Fuente: Modificado de [4].
Figura 1 Técnicas de exposición UV. a) Contacto. b) proximidad. c) proyección.
3. Diseño e implementación del sistema de fotolitografía
Para diseñar e implementar el sistema de fotolitografía se sigue el proceso diseño y desarrollo de productos, ampliamente usado en el sector industrial para la fabricación de nuevos productos, que ha implementado distintas herramientas que dan seguimiento continuo a las actividades que realiza una empresa en el proceso de creación o mejora de un producto [14], a través de tres funciones: mercadotecnia, diseño y manufactura, integradas a la cadena de producción, que van desde la planeación del producto hasta su fabricación e inclusión en el mercado [14].
Se resalta la etapa diseño, ya que demanda más coordinación entre funciones y actividades, donde se usan recursos cognitivos como la solución de problemas, toma de decisiones, creatividad, máxima optimización de materia prima y tiempo [15]. Permitiendo desarrollar un artefacto, sistema o servicio, con características técnicas, funcionales y estéticas, que cumplen las necesidades planteadas por el cliente. Los recursos se organizan en actividades que facilitan acciones a ejecutar por el diseñador (Fig. 2).
Las actividades de desarrollo de concepto usadas para la implementación del sistema de fotolitografía son:
3.1. Identificar necesidades
El objetivo de esta fase es recopilar y determinar cuáles son las necesidades del cliente respecto al sistema de fotolitografía (Tabla 1).
3.2. Establecer especificaciones objetivo
Las necesidades identificadas se transforman en enunciados con un valor y métrica (valor numérico y unidades respectivas) [16], para identificar las especificaciones técnicas (Tabla 2). La importancia relativa se define en función de las necesidades recogidas en la generación de la idea (donde 1 es el valor de mayor relevancia y 5 el de menor).
Es fundamental analizar el error en las dimensiones de las microdispositivos, es decir, cuanto pueden variar propiedades como la rugosidad y homogeneidad, sin que afecten sus propiedades eléctricas y mecánicas. Por lo que se adoptó el criterio sugerido por la ITRS (International Technology Roadmap Semiconductor) para controlar la calidad de los circuitos integrados y la repetibilidad del proceso de fabricación [4,17,18].
3.3. Selección del microdispositivo caso de estudio
Se seleccionó como dispositivo caso de estudio un mP, usado en el estudio de propiedades de transporte eléctrico (Fig. 3) [19,20].
3.4. Generación de conceptos
Se utilizó el diagrama de caja negra (Fig. 4) [14], que opera con flujos de material, energía y señales, para identificar problemas y subproblemas (Fig. 5). Las líneas finas y continuas denotan la transferencia y conversión de energía, las gruesas y continúas el flujo y transformación del material y la línea discontinua denota las señales de control y realimentación. Se enfocó en los subproblemas de esparcir fotoresina e irradiar con UV por su complejidad.
3.5. Selección de conceptos
Para dar la solución más óptima a los subproblemas, se hizo la búsqueda y selección de conceptos mediante la revisión en la literatura, búsqueda y comparación de instrumentación existente en el mercado.
Para el subproblema esparcir fotoresina se plantearon dos conceptos: un spray para depositar la fotoresina en la superficie de la película delgada, este proceso es sencillo de implementar pero el espesor de la capa de fotoresina depositada es variable y no homogéneo [21], afectando la repetibilidad en la fabricación de los microdispositivos.
Otro concepto es el spincoater donde se deposita la fotoresina sobre la película delgada, se hace rotar en el rango 1500-6000 rpm y por fuerza centrífuga esparcirla hasta el borde de la película delgada creando una capa fina y uniforme [2,3]. La fotoresina tiene características definidas, obteniéndose precisión en el espesor en la capa de fotoresina en función de la velocidad de rotación. Así el concepto más apropiado para el subproblema esparcimiento de fotoresina es el spincoater.
Para el subproblema irradiar con UV se plantea tres conceptos: la técnica de radiación por proyección, constituida por un arreglo de lentes, fuente de radiación UV y alineador de fotomáscaras. Actualmente es el sistema más utilizado para la fabricación de micro/nano dispositivos por su versatilidad, rendimiento en la producción y resolución de los patrones impresos [2,3]. Sin embargo los costos de implementación son elevados. La técnica de radiación por proximidad, consiste de una fuente de radiación UV y una fotomáscara separada de la película delgada con la fotoresina, no obstante la calidad y resolución en las microestructuras disminuye por efectos de difracción [2,3]. La técnica de radiación por contacto consiste en una fuente de radiación UV y una fotomáscara en contacto con la fotoresina sobre la película delgada. Se obtiene buena calidad en las microestructuras de los dispositivos ya que los efectos de la difracción son mínimos, la instrumentación no es compleja y los costos de implementación son bajos respecto a las técnicas anteriores [3,4]. Por lo tanto el concepto más apropiado para el subproblema irradiar con UV es la técnica por contacto.
3.6. Prueba e implementación de prototipos
Para el spincoater se diseñó e implementó un control de velocidad PID de un motor DC marca Pololu [22], en el rango de 500-6000 rpm, con error menor al 5% en el control y medición de velocidad y un módulo de potencia para su alimentación. Para el concepto de radiación con UV por contacto (Fuente de radiación UV) se usaron LEDs UV de 380nm con una potencia de radiación de 20mW/cm2 de la empresa superbrightleds [23]. Se implementó una matriz de 10x10 LEDs y el control de potencia y tiempo de exposición. Cada concepto posee una interfaz de usuario constituido por teclado y pantalla LCD para programar y visualizar los parámetros de operación. El diseño electrónico se realizó en el entorno de desarrollo KiCad, la implementación sobre la plataforma de desarrollo electrónico arduino uno, fabricándose PCBs (Printed Circuit Board) para disponer los componentes electrónicos. Las especificaciones técnicas de los dos equipos se muestran en la Tabla 3. El diseño mecánico de los prototipos se desarrolló en el entorno Solid Edge versión estudiantil y se fabricaron prototipos en lámina y acrílico (Fig. 6).
3.7. Selección de fotoresina y película delgada
Se adquirió un kit de fotolitografía de la empresa Transene, está compuesto por fotoresina positiva (PC800), revelador (PC1800), rinse (PC2800), stripper (PC3800) y tiner (PC4800) [24].
Se utilizaron películas delgadas de cobre crecidas sobre sustrato de silicio por la técnica de sputtering DC [25].
3.8. Fabricación de la fotomáscara
Para fabricar la fotomáscara se considera las condiciones: 1) Patrón geométrico un mP en campo claro (el patrón es negro con fondo claro) puesto que la fotoresina es positiva. 2) Que los mPs en la fotomáscara no excedan el área de 10x10 mm2 ya que las películas delgadas crecidas sobre sustratos de silicio son menores a 10 mm de lado. 3) mPs con distintos anchos. Así se planteó el diseño de una fotomáscara con 6 mPs de 0.30-0.105 mm de ancho, 3 mm de longitud y nodos de 0.75 mm de ancho por 0.85 mm de alto, como contactos eléctricos (Fig. 7). El diseño se realizó con el software L-Edit versión estudiantil y se imprimió sobre acetato con impresión láser de alta resolución (25400dpi), en la empresa CAD/Art Services Inc [26].
3.9. Integración de equipos
El spincoater y la fuente de radiación UV se integraron al sistema de fotolitografía, que se ha denominado SysMicFUV-FB (Fig. 8) y está constituido por: (1) Soplador de aire, (2) Limpiador de ultrasonido, (3) Spincoater, (4) Plancha de calentamiento, (5) Medidor de temperatura, (6) Fuente de radiación UV, (7) Cuatro beaker, (8) Dos tarros de enjuague, (9) Mortero de ágata, (10) Pinzas, (11) Lámpara. Estos se organizan en 7 sistemas: limpieza, esparcimiento de fotoresina, calentamiento, radiación UV, revelado, transferencia de patrones y remoción de fotoresina.
4. Resultados y discusión
Para verificar la repetibilidad en la fabricación de microdispositivos con el sistema SysMicFUV-FB y dar cumplimiento a las especificaciones de diseño, se obtuvieron las condiciones de producción (Tabla 4) a partir de los parámetros sugeridos por el fabricante de la fotoresina [24], lo reportado en la literatura [27,28] y pruebas experimentales. Con lo cual se fabricó cuatro lotes de seis mPs cada uno sobre películas delgadas de cobre usando la fotomáscara de la Fig. 7.
4.1. Caracterización de los microdispositivos
La caracterización de los mPs se realizó con un sistema de microscopia óptica constituido por: microscopio óptico marca NIKON 80i, cámara digital marca DS-MV-U2, computador marca Dell, fuente variable de iluminación y el software NIS-Elements F, para configurar los parámetros de la cámara, captura y almacenamiento de las imágenes.
Con el software ImageJ [27] se realizó el procesamiento digital de imágenes determinando el área de las mPs y el ancho siguiendo los pasos:
Paso 1: Reconstrucción digital de la imagen. Se ha etiquetado a los lotes con L1-L4 y a la fotomáscara con FM1 (Fig. 9). Paso 2: Establecimiento de escala.
Paso 3: Conversión a escala de grises.
Paso 4: Segmentación.
Paso 5: Identificación del área de interés (ROI).
Paso 6. Medición del área de las mPs.
Paso 7. Medición del ancho de los mPs.
Se obtuvo el área de los mPs y la fotomáscara (Tabla 5), donde cada fila se ha etiquetado desde mP1-mP6 asociado a cada micropuente y las columnas hacen referencia a las medidas del ancho de cada mP en los 4 lotes fabricados.
Tabla 5 Medida del área en los mPs para los 4 lotes de microdispositivos y la fotomáscara.

Fuente: Los autores.
Se calculó la repetibilidad del proceso de fabricación con el error relativo porcentual, planteando como medida patrón (valor teórico) el área de los mPs impresos en la fotomáscara (Tabla 6).
Se evidencia errores por encima del 3% en el área de los mPs P1, P2, P3 de MD1 y P1, P3 de MD3. También se determina que los errores son mayores para los mPs de áreas menores (P1-P3). Este comportamiento se debe a que la transferencia de patrones sobre la superficie de la película delgada de cobre se hace en un medio ácido, presentándose regiones donde el ataque químico es más selectivo. Además factores como la temperatura, agitación y procesos de interacción acido-superficie afectan las condiciones de grabado [4], [28-30]. Otra causa del error se atribuye a la oxidación de la superficie de los mPs por el contacto con el medio y por otro lado a la presencia de pequeños residuos de fotoresina en los bordes, lo que aumentaría el área de los micropuentes.
Se agruparon las mediciones de ancho en los mPs que comparten las mismas características, calculándose el valor promedio, desviación estándar, doble de la desviación estándar y lo diferencia entre los valores más bajos y altos medidos respecto al valor promedio (Tabla 7).
Tabla 7 Cálculo de promedio, desviación estándar y los valores más bajos y altos medidos en la agrupación de mPs.
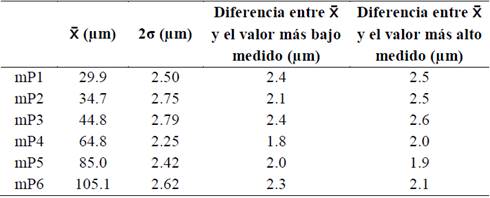
Fuente: Los autores.
La diferencia entre el valor promedio y los valores máximos y mínimos en las mediciones de los mPs, así como la desviación estándar es mayor para mP1, mP2 y mP6. No obstante, la variabilidad en la anchura de los 6 mPs para los 4 lotes es menor al criterio de dos veces la desviación estándar. Con base en lo anterior se verifica que el sistema SysMicFUV-FB permite fabricar microestructuras con alto grado de repetibilidad y por tanto satisfacen las necesidades planteadas.
5. Conclusiones
En este trabajo se diseñó e implementó un sistema de fotolitografía por contacto aplicando el diseño y desarrollo de productos, lo que permitió la identificación de los módulos de equipo, especificaciones de diseño, generación, selección y prueba de conceptos y fabricación de dos prototipos: un spincoater basado en el control de velocidad de un motor DC y una fuente de radiación UV con base en un arreglo de LEDs UV con longitud de onda de 380nm. Se fabricaron cuatro lotes con 6 mPs cada uno, a partir de películas delgadas de cobre crecidas sobre sustrato de silicio, con la técnica de sputtering DC. La repetibilidad del proceso de fabricación se determinó a partir de la medición del área y el ancho de los micropuentes usando la técnica de microscopía óptica y procesamiento digital de imágenes. Donde se obtuvo que el error relativo porcentual en el área de los micropuentes es de 1-4%. Además, se determinó que la variabilidad de las microestructuras en los micropuentes es menor a 2σ. Los resultados sugieren que el sistema de fotolitografía desarrollado, permite la obtención de micropuentes y microcircuitos con alta tasa de producción, repetibilidad y calidad óptima y por lo tanto da cumplimiento a las especificaciones de diseño.