1. Introduction
Concrete is known for its good performance regarding exposition to high temperatures, due to its incombustibility, low thermal diffusivity [1-3] and inability to expel gasses or smoke [1]. However, concrete suffers physicochemical changes in fire situations, which result in loss of mechanical properties, cracking and spalling [4]. This kind of deterioration derives from multiple factors, such as constitutive (aggregate and cement types, water/cement ratio, mineral additions and fiber content) and environmental features (exposure time, heating rate, load applied and relative humidity) [1,3,5,6].
Residual strength of heated structural concrete elements depends on the characteristics of the heating. In real fire situations, not all sides of the structural elements are directly exposed to heat [7]. Due to concrete’s low thermal conductivity, a temperature gradient may occur throughout the cross section of the element, causing severe damages within few centimeters [2,7,8]. Thus, compression tests must be analyzed carefully when performed on core samples extracted from fire damaged concrete structures, as the results will not be representative [7,9].
Changes in concrete properties are related to changes in microstructure [6]. Thus, residual properties of concrete can be assessed by experimental techniques that identify physical, chemical and mineralogical changes. Within this context, this research aims to investigate the potential use of scanning electron microscopy (SEM) and X-ray diffraction (XRD) for analyzing thermally damaged concrete. For this purpose, two reinforced concrete columns, each with a different concrete mix, were exposed to a controlled fire situation for 4 hours, following the standard curve of ISO 834. Reference columns were produced as well, and were not exposed to high temperatures. After natural cooling, the techniques mentioned were used to investigate microstructural changes.
This study is part of an ongoing research at the Fire Safety Laboratory of itt Performance, which regards fire behavior on reinforced concrete columns.
2. Previous studies and research relevance
High temperatures cause intense degradation to microstructures of concrete. These microstructural changes have been studied by different experimental techniques. Fernandes et al. [10] compiled a total of 35 studies that had applied techniques to investigate physicochemical changes, such as scanning electron microscopy, X-ray diffraction, thermogravimetric analysis, mercury intrusion porosimetry, colorimetry and petrography.
Handoo, Agarwal and Agarwal [11] studied the effect of temperature (up to 1000 ºC) on concrete cubes. These authors applied XRD, SEM and thermal analysis (DTA/TGA). The results showed massive deformations of calcium silicate hydrate (C-S-H) and portlandite (CH) crystals at temperatures beyond 600 ºC. [4] studied microstructures of concrete exposed to real fire by means of optical microscopy. According to results, a carbonation reaction occurred on the cement paste surface, and Portlandite was found more deeply within the samples. The images also showed heavy cracking on the aggregate-cement paste interface.
Peng and Huang [12] verified the microstructure of hardened cement paste heated up to 800 ºC by means of SEM, XRD and mercury intrusion porosimetry (MIP). C-S-H started to decompose significantly at 600 ºC along with the coarsening of its pore structure, while portlandite and calcium carbonate being strongly reduced at 500 ºC.
Menéndez and Vega [13] studied the microstructure of concrete from Windsor Building in Madrid, exposed to real fire in 2005. The authors applied SEM, XRD and thermal analysis in the post-fire investigation. XRD findings showed the absence of portlandite only on the surface of the samples (0-2.5 cm). These samples also presented microfessures and morphological alteration in C-S-H. Samples from the inner portion presented no apparent changes.
Kim, Yun and Park [14] studied the behavior of mortar specimens subjected to temperatures up to 1000 ºC by means of XRD, SEM and X-ray tomography. SEM results showed that CH and C-S-H began dissociating at 500 ºC and completely disintegrated at 700 ºC. XRD diffractograms also displayed the reduction of portlandite, but starting at 400 ºC and completely disassociating at 1000 ºC.
Lim and Mondal [15] applied thermal analysis (TGA), SEM and XRD to study cement paste exposed to temperatures up to 1000 ºC. SEM images showed degradation of C-S-H and CH starting at 300 ºC, along with the appearance of dehydrated cement particles. At temperatures above 500 ºC, microcracks started propagating on the interface of these particles, increasing porosity. XRD showed dissociation the appearance of β-C2S at 500 ºC. At this level, portlandite also began disintegrating.
Although many experimental investigations concerning heated concrete have been carried out, the evolution of microstructural changes into macroscopic ones to is not entirely explained [15]. Furthermore, most experimental researches are performed with small scale test specimens. Concrete samples used in this kind of experimental program differ from those of full scale tests, which are usually more representative. There are limited data [4,13] regarding microstructural changes of full scale concrete members and most of them are from real fire situations. This paper intends to contribute to these studies by applying microstructural analysis for assessing full scale concrete elements exposed to a standard fire.
3. Experimental procedure
3.1. Reinforced concrete column specimens
Two reinforced concrete columns were manufactured in a precast factory. The specimens had square cross section of 250 mm X 250 mm and height of 3000 mm. Four longitudinal bars were placed within each column, being 10 mm and 16 mm diameter on the heated surface and two constructive ones with 8 mm diameter on the unheated surface, with a gross concrete cover of 2.5 cm. Stirrups with 6.3 mm diameter bars with a spacing of 150 mm were used as well.
Normal strength concrete was used in each column, whereas under different mix proportions (P1 and P2). Details of the mix design are given in Table 1. The concrete was made of Brazilian CPV-ARI (high early strength) Portland cement, basaltic coarse aggregate in two sizes, and two kinds of sand - quartzitic natural sand and crushed basalt. The aggregates were from local quarries with a maximum diameter of 19mm and 9.5mm for coarse aggregates and 2.4mm for sands. The water/cement ratio was 0.45 for P1 and 0.55 for P2, and the compressive strength of the concrete at 28 days was 47.9 MPa for P1 and 40.2 MPa for P2. Small concrete columns (250 mm x 250 mm x 400 mm) were used as reference samples.
3.2. Heating process
For the heating process, a vertical furnace was used. The inside of the furnace is 2.5 m tall, 2.5 m wide and 1.0 m long. The experimental model consisted of columns embedded in a masonry wall built within a frame, so that 45% of the cross section would be exposed to high temperatures, .in three faces. Fig. 1 shows how the columns were tested, and Fig. 2 depicts the experimental setup.
The reinforced concrete columns were instrumented with type K thermocouples. They were inserted in holes prepared during concrete casting. The temperature was measured within intervals of 5.00 cm of depth, on the concrete cover and the non-exposed side. Fig. 3 presents the placement of the thermocouples on column’s cross section. The furnace temperature was controlled by 2 fixed thermocouples inside the furnace chamber. The columns were exposed to the standard fire of ISO 834 for 4 hours.
3.3. Preparation of samples for microstructural analysis
Core samples were extracted from the concrete columns after natural cooling, as well as from the reference column, which was not exposed to high temperatures. These cores were sectioned in discs with 50 mm of diameter and 15 mm of thickness, and were dried in an oven at 60 ºC for 24 hours. They were then stored in a vacuum desiccator with silica gel until the microanalysis tests. Table 2 presents a summary of the samples analyzed. Altogether, 22 samples were analyzed (14 for SEM and 8 v for XRD).
For SEM tests, the samples were fractured for a secondary electron analysis. The heated concrete surfaces were covered in gold and the analysis was carried out with the Zeiss Evo LS 15 scanning electron microscope. For XRD tests, the samples were ground into powder and the Siemens D500 X-ray diffractometer was used for analysis.
4. Results and discussion
4.1. Thermal response
Figs. 4 and 5 present the temperature evolution inside the furnace, for different depths of columns.
The furnace temperature followed the ISO 834 standard fire curve throughout both tests. The thermocouple at 2.5 cm depth on column P1 was expelled at 95 minutes. During both tests, usually 5 minutes after the start, at 100 ºC, the temperature remained constant for a period due to concrete water vaporization. This phenomenon occurred up to the depth of 10 cm in both cases.
Overall, the temperatures of column P1 were lower, but the temperature of 550 ºC was reached by the depth of 10 cm, which did not occur on P2. Concrete becomes structurally useless above 550°C [3], which is the reason why 500 ºC is the basis for one of the most used calculation methods for estimating safety of fire damaged structures [13].
4.2. Macroscopic observations
The surface of one of the reinforced concrete columns, after the fire resistance test, is shown in Fig. 6. A yellowish color is visible, indicating that the concrete surface surpassed the temperature of 900 ºC [2,16,17]. It was also noted that the color of concrete changes as depth increases, with a grey tone appearing, indicating that the concrete reached a range of 600-900 ºC [2,16]. This is also observed in Fig. 7, which shows a piece of concrete cover. Small black dots can be seen in this picture, which can be related to use of crushed basalt sand, since the mineralogical nature of the aggregate induces color changes to the concrete. As expected, the material from the concrete cover was fragile and had an intense incidence of pores (observed visually). Yet, only column P1 underwent spalling.
4.3. SEM Analysis
SEM micrographs of the reference concrete and 25 cm, 5 cm and 0 cm depth samples of both columns are shown in Figs. 8 and 9.
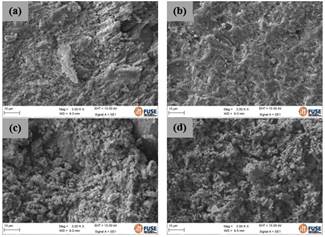
Source: Authors
Figure 8 SEM micrographs of P1 (mag. 3000X): (a) reference sample, (b) 25 cm depth sample, (c) 5 cm depth sample and (d) 0 cm depth sample
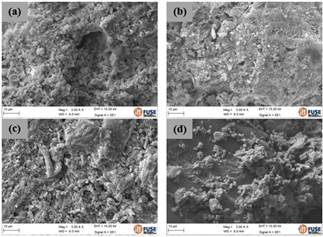
Source: Authors
Figure 9 SEM micrographs of P2 (mag. 3000X): (a) reference sample, (b) 25 cm depth sample, (c) 5 cm depth sample and (d) 0 cm depth simple
In both cases, SEM images of the 25 cm depth concrete did not present apparent morphological changes in comparison to the SEM image of the reference sample. This concerns the temperatures reached at this depth, which were 103 ºC for P1 and 114 ºC for P2. Increasing temperature at this level only causes dissociation of ettringite [18,19].
The micrograph of 5 cm of P1 showed a dense matrix, similar to the reference sample, but with coarse aspect and presence of little voids. P2 also displayed this similarity with respect to the reference sample (coarse aspect and voids), but the matrix is sparser than P1. Similar transformations that occurred in both columns were related to the dehydration of CH at temperatures above 420 ºC [6,20]. The differences between columns depended on the temperatures at this depth, which were 565.6 ºC for P1 and 701.2 ºC for P2, considering that the maximum temperature of P2 column reached the C-S-H disintegration outset point [6,20,21].
Lastly, the SEM micrograph of the 0 cm depth sample showed robust morphological changes, such as cracks and voids. The temperature reached at this point was 1128.8 ºC for P1 and 1123.6 ºC for P2, and cement paste begins melting at this temperature level [8].
4.4. XRD Analysis
XRD diffractograms of the reference concrete and 25 cm, 5 cm and 0 cm depth samples of both columns are presented in Figs. 10 and 11. The transformations observed are highlighted.
P1 diffractograms display presence of portlandite and quartz due to the fine aggregate used when making the concrete. Portlandite appeared in the reference and 25 cm samples, but was not seen in the 5 cm and 0 cm samples. The temperature reached by the depth of 5 cm was 565.6 ºC. This temperature is higher than 420 ºC, which is when CH begins disintegrating [6]. Similar results were reported by Handoo, Agarwal and Agarwal [11], Peng and Huang [12] and Lim and Mondal [15].
P2 samples displayed portlandite and quartz as well, but larnite was identified in the XRD diffractograms. Contrary to P1 samples, portlandite could be seen at the 5 cm depth, but not at 0 cm, where the temperature was 1123.6 ºC. A similar behavior was observed by Kim, Yun and Park [14]. Furthermore, larnite (β-C2S) was found at 0 cm depth, most likely as a result of the C-S-H disassociation, in accordance to what is pointed out by the literature [5,6,20].
5. Conclusions
This study assessed the thermal damages on concrete using full scale reinforced concrete columns, by the means of scanning electron microscopy and X-ray diffraction., The following conclusions may be drawn from the results:
Macroscopic observations can help determining critical damage zones, as concrete changes color. From these observations, the maximum temperature reached at certain depth can be estimated. The yellowish color indicates that the temperature of 900 ºC was surpassed, and this is confirmed by the cross section temperatures measured during the test. The small black dots that showed up can be related to physical transformations of crushed basalt. Only P1 underwent spalling.
SEM micrographs presented robust morphological changes, such as coarsening of the cement paste, cracks and voids. This signalizes a significant mechanical degradation of concrete, due to dehydration of CH and C-S-H. Microstructural changes are more visible at temperatures above 420 ºC, when portlandite starts decomposing.
XRD diffractograms showed a reduction of portlandite and the presence of larnite as depth increases. This can be useful for estimating the temperature reached and the damage level, since CH dehydrates at temperatures above 420 ºC and C-S-H decomposes into β-C2S above 700 ºC. Portlandite reduction could also be observed during the main experimental program using XRD, so CH degradation can be used as the main indicator of thermal damage to concrete.
The microstructural damages can be useful for estimating concrete strength reduction. Khoury [3] points out that concrete becomes structurally useless at temperatures above 550 ºC. The microstructural changes that occurred at the depths of 5 cm and 0 cm (surface of concrete column) indicate that the temperature level surpassed 550 ºC.
The techniques of this study are already used on small scale tests and real fire scenarios, but showed potential for evaluating damages caused to concrete exposed to elevated temperatures on full scale tests as well. Further research is needed to establish standardized tests procedures, including sample preparation and process of analysis.