1. Introduction
Los compuestos elaborados a base de arcillas caolinitas y partículas diatomáceas son usualmente utilizados en diversas aplicaciones industriales para mezclas de cemento, producción de piezas de mampostería, adsorbentes de humedad, aislantes térmicos, agentes purificadores, en forma de aditivos para fertilizantes, aerogeles, espumas, catalizadores, entre otros [1-3]. Sin embargo, uno de los mayores usos se da en la producción de filtros cerámicos [4-7], en donde se clasifican como sistemas purificadores altamente efectivos gracias a la cantidad y tamaño de poros o intersticios que se encuentran distribuidos en su matriz, lo cual permite que otros elementos se anclen de forma total o parcial dependiendo de la relación que haya entre el tamaño del poro y el tamaño del sólido a retener [8].
En comparación con otros materiales porosos, los compuestos de caolín y diatomita ofrecen varias ventajas que los diferencian de los demás: poseen excelentes propiedades mecánicas como dureza, resistencia a la corrosión y desgaste, resistencia al ataque químico, baja densidad de masa, durabilidad en ambientes agresivos y estabilidad frente a la presencia de altas temperaturas [9-14]. Lo anterior ha ocasionado que estos materiales sean objeto de investigación en los últimos años con el fin de optimizar sus propiedades y potencializar sus usos [15].
Dar estructura y forma cristalina bien definida a los materiales porosos se lleva a cabo con la adición de compuestos inorgánicos con fases cristalográficas estables [16-18]. Por tal razón, en la síntesis del material se adiciona carbonato de calcio (CaCO3), uno de los minerales más abundantes en la corteza terrestre producido por organismos vivos a través del proceso conocido como biomineralización [19]. Entre las fases cristalinas del mineral se encuentran: calcita, vaterita y aragonita; de las cuales la calcita es la fase polimórfica responsable de la alta estabilidad termodinámica y fisicoquímica [20-22]. La adición de carbonato de calcio en la matriz del compuesto juega el papel de agente poroso que en condiciones de sinterización, se disocia en oxido de calcio y dióxido de carbono. Al ser este último un gas, buscará la forma de salir hacia la superficie generando canales porosos en la estructura [23].
Para la síntesis de este tipo de compuestos cerámicos existen tres procesos de conformado: slip casting o colado, prensado y extrusión [24,25], cada técnica requiere una consistencia específica del material: plástica, fluida o seca. Una vez es seleccionado el proceso, se conforman de acuerdo a la geometría deseada y se someten a un proceso de sinterización. Sus propiedades pueden variar dependiendo del porcentaje entre sus compuestos, tamaño de partícula, rango de temperatura de sinterización y la técnica seleccionada [26].
El objetivo del presente trabajo consiste en estudiar el comportamiento microestructural, físico y mecánico del compuesto caolín-diatomita reforzado con CaCO3, bajo seis temperaturas de sinterización que varían entre 800 °C y 1100 °C. Las propiedades físicas de estudio son: densidad aparente, porcentaje de absorción y contracción lineal. Por último, el comportamiento mecánico comprende resistencia mecánica a la compresión y ensayo de flexión a tres puntos.
2. Materiales y métodos
2.1. Elaboración y caracterización de las muestras
Los polvos de caolín, diatomita y carbonato de calcio, fueron suministrados por la compañía Minerales Boyacá Ltda., ubicada en el departamento de Boyacá, Colombia. Los análisis de las materias primas y prototipos cerámicas se llevaron a cabo en los laboratorios del Instituto para la Investigación e Innovación en Ciencia y Tecnología de Materiales (INCITEMA) de la Universidad Pedagógica y Tecnológica de Colombia y en el Centro de Investigación en Ciencia Aplicada y Tecnología Avanzada (CICATA) de México.
La mezcla utilizada para la elaboración de la barbotina se presenta en la Tabla 1, allí se observan los materiales utilizados expresados en porcentaje en peso, así como las dimensiones de los prototipos las cuales variaron de acuerdo al ensayo al que fueron sometidos (ver Fig. 1).
Se utilizó silicato de sodio como defloculante en una concentración en peso de 0.5%, valor determinado por medio de la curva de defloculación del material. La homogenización de la barbotina se realizó a una velocidad de 200 min-1 en el equipo floculador E&Q referencia F6 300T. El proceso de conformado de los prototipos cerámicos fue slip casting o colado, para lo cual se utilizaron moldes de yeso. Una vez conformados los prototipos se sometieron a un proceso de secado en una estufa de circulación forzada a 110 °C por 24 horas.
Las temperaturas y tiempos de cocción se muestran en la Fig. 2. Para el proceso de cocción de los especímenes se manejó dos rampas de calentamiento de 5 °C/min cada una y dos mesas: la primera alcanzó 600 °C y se mantuvo por 120 minutos, la segunda correspondió a la temperatura final que alcanzó cada lote de probetas, a saber: 800, 850, 900, 950, 1000 y 1100 °C, con una duración de 120 minutos cada una. Las seis temperaturas de sinterización utilizadas de ahora en adelante son identificadas en el texto como: T1, T2, T3, T4, T5 y T6.
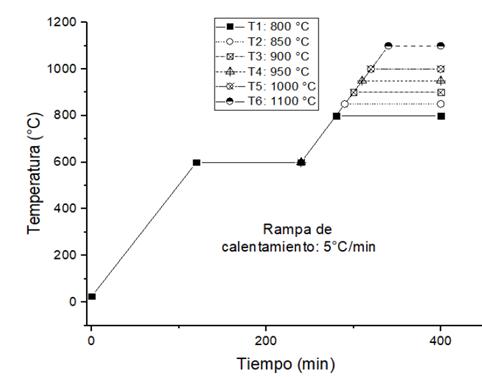
Fuente: Los Autores.
Figura 2. Curva de sinterización utilizada para cada lote de probetas cerámicas con temperaturas entre 800 - 1100 °C.
La morfología, microestructura y tamaño promedio de poro del compuesto se investigó a través de Microscopía Electrónica de Barrido (MEB) en el equipo marca Zeiss Evo MA10 con magnificaciones entre 3000X y 8000X.
Las fases mineralógicas de las materias primas y prototipos cerámicos se determinaron por difracción de rayos X, con un ángulo de incidencia de 2 grados y una velocidad de barrido de 0.5 segundos por paso. El ensayo se realizó en el equipo marca Philips X’pert Pro Panalytical; el análisis y cuantificación de fases se realizó por medio del programa X’pert High Score Plus (versión 1.0d), usando como referente los patrones de difracción del Inorganic Crystal Structure Database (ICSD).
2.2. Densidad Aparente: Método de Inmersión en Mercurio
Para hallar la densidad aparente se siguió el procedimiento descrito en la Norma E - 8B del Instituto de Tecnología Cerámica [26], el ensayo consiste en la ubicación de una probeta en un sistema de inmersión que contiene un recipiente con mercurio y una balanza de ±0.1g de precisión. Para cada temperatura se ensayaron cuatro probetas, correspondientes al tamaño de muestra mínimo requerido por norma; se utilizó la ecuación (1) para el cálculo de la densidad aparente.
Donde D ap es la densidad aparente de la probeta seca o cocida expresada en g/cm3, m es la masa de la probeta seca o cocida expresada en g, d Hg es la constante que hace referencia a la densidad del mercurio (d Hg = 13.53 g/cm 3 ) y ep es el empuje de la probeta seca o cocida sumergida en el mercurio, expresado en gramos.
2.3. Porcentaje de absorción de agua
El porcentaje de porosidad por absorción de agua se determinó según la norma ISO 10545-3 siguiendo el método de ebullición [27]. El ensayo consistió en impregnar los poros abiertos que son fácilmente rellenables por medio de la sumersión vertical de las probetas en agua a punto de ebullición, durante dos horas. El porcentaje de absorción se calculó por medio de la ecuación (2) donde se establece una relación entre las masas secas, saturadas y suspendidas de los especímenes.
Donde Abs es el porcentaje de absorción de agua, m 1 es la masa del prototipo seco y m 2 la masa del prototipo húmedo, ambas expresadas en gramos.
2.4. Contracción lineal
El estudio de la contracción se realizó en prototipos con forma cúbica, en los cuales se registró longitudes en las tres direcciones: largo, ancho y alto. El porcentaje de contracción fue calculado de acuerdo con la ecuación (3).
Donde C es el porcentaje de contracción, L p es la longitud del prototipo seco (sin cocción) y L c es la longitud del prototipo sinterizado, ambas longitudes se encuentran expresadas en milímetros.
2.5. Resistencia mecánica la compresión
Para determinar la resistencia mecánica se tuvo en cuenta lo establecido en la norma ASTM C773-88 [28], para lo cual las probetas debían mantener una relación diámetro - altura de 1:2.5. Los prototipos se analizaron en la máquina de ensayo marca MICROTEST EM 2/300 FR, en la cual se aplicó una carga axial a una velocidad constante de la celda de 10 N/s. Para cada temperatura de sinterización se ensayaron 5 probetas, el cálculo de la tensión máxima se realizó siguiendo la ecuación (4).
Donde σ c es la tensión máxima del espécimen expresada en N/m2 (Pascales), F es la fuerza expresada en Newton y A es el área de la sección de la probeta donde es aplicada la carga, la cual se encuentra expresada en metros cuadrados.
2.6. Ensayo de flexión a tres puntos
El módulo de rotura o resistencia a la flexión se determinó siguiendo el método establecido en la norma ISO 10545 - 4 [27], para cada temperatura se elaboraron 3 probetas de configuración cúbica rectangular. De acuerdo a la norma se estableció una separación entre los rodillos de apoyo de 8 cm y se manejó un punzón con diámetro de 30mm. El ensayo se realizó en la máquina marca MICROTEST EM 2/300 FR, a una velocidad de celda de 10 N/s, la cual se mantuvo constante durante la prueba. Una vez finalizado el ensayo, se halló el módulo de rotura según la ecuación (4).
Donde R es la Resistencia a la flexión o Módulo de Rotura expresado en N/m2, F es la fuerza o carga necesaria para causar la rotura de la probeta expresada en Newton, L es la distancia o separación entre los rodillos de apoyo, b es el ancho de la probeta y h es el grosor mínimo de la probeta en la sección de rotura. L, b y h se encuentran expresados en metros.
3. Resultados y discusión
3.1. Difracción de Rayos X (DRX)
Previo a la síntesis de las muestras se realizó el análisis semicuantitativo por difracción de rayos X de los polvos de caolín, diatomita y CaCO3. El patrón obtenido para la muestra de caolín se presenta en la Fig. 3, allí se identificó tres fases mineralógicas diferentes: caolinita (Al2Si2O5(OH)4), cuarzo bajo (SiO2) y magnesioferrita (Mg(Fe3+) 2O4), con porcentajes en peso de 74 %, 19.3 % y 6.8 % respectivamente. La fase caolinita se encuentra dentro del conjunto de especies conocidas como kanditas [27,28] y se caracteriza por tener baja reacción en diversos medios, lo anterior ocurre gracias a su estructura cristalina formada por enlaces Van der Waals (OH) que unen los tetraedros de sílice con los octaedros de alúmina, los cuales resisten la mayoría de los ataques ocasionados por fluidos corrosivos [29].
Según la roca de procedencia y el tamaño de partícula del mineral (inferior a 2µm) es frecuente encontrar dentro de la composición del caolín, cantidades bajas de cuarzo y óxidos de hierro [30,31]. En este caso la presencia de la fase cuarzo bajo, puede provocar problemas de abrasión e influir en las propiedades reológicas del material [32], mientras que la fase magnesioferrita también conocida como ceilonita, un óxido metálico perteneciente al grupo de las espinelas [33], es un mineral que ocasiona pigmentación en la muestra.
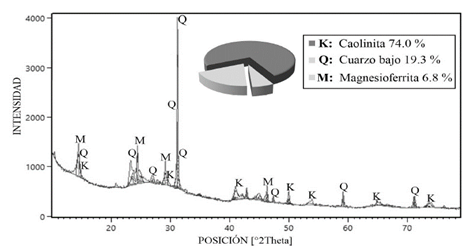
Fuente: Los Autores.
Figura 3. Patrón de difracción y porcentaje en peso de las fases que componen los polvos de caolín.
El patrón de la muestra de diatomita se presenta en la Fig. 4, este mineral reveló un alto contenido de moscovita (KAl2(AlSi3O10)(OH)2) y cuarzo entre sus fases mayoritarias con porcentajes en peso de 58.0% y 36.5% cada una. La fase moscovita pertenece al grupo de las micas alumínicas que a su vez se encuentran dentro de la clase de los filosilicatos, se presenta en forma de láminas o capas de contorno hexagonal y otorga a la muestra propiedades dieléctricas y de resistencia al calor [34-36]. Sin embargo, una alta presencia de silicatos de aluminio en forma de moscovita, refleja en la muestra cantidades elevadas de alúmina (AI2O3) y potasio (K), este último bajo la forma de metal alcalino. Por otra parte, los picos característicos de la fase caolinita son bastante débiles en la muestra, con un porcentaje en peso de 5.5% reflejando una mínima presencia de este tipo de impurezas en el mineral.
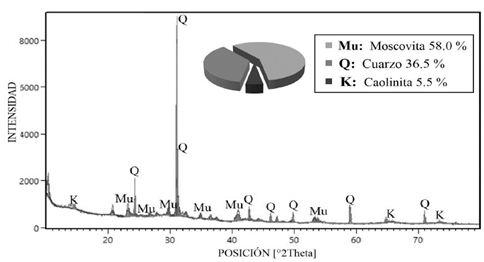
Fuente: Los Autores.
Figura 4. Patrón de difracción y porcentaje en peso de las fases halladas en los polvos de diatomita.
El patrón de difracción de la muestra de carbonato de calcio exhibió picos característicos de las fases calcita (CaCO3) con una participación de 87.1% y dolomita (CaMg(CO3)2) con 12.9 %, como se puede observar en la Fig. 5. La fase dolomita se presenta en la roca caliza debido a una sustitución por intercambio iónico del calcio por magnesio [37,38].
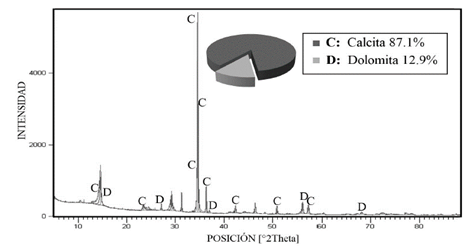
Fuente: Los Autores.
Figura 5. Patrón de difracción y porcentaje en peso de las fases que componen el carbonato de calcio CaCO3.
En la Fig. 6 se encuentran los patrones de difracción de los prototipos cerámicos así como el porcentaje en peso de las fases en cada temperatura de sinterización. La fase cuarzo (Q) está presente en todas las muestras con reflexiones localizadas en 27.316°, 27.722°, 37.189° y 38.047°, la intensidad de estos picos disminuyó conforme aumentó la temperatura de sinterización, sin embargo el tamaño de cristalita permaneció constante teniendo en cuenta que el FWHM no exhibió variaciones significativas. El porcentaje en peso inicial de la fase fue de 51.16 % a 800 °C, alcanzó su máximo a 950 °C con 55.96 % y posteriormente decreció hasta alcanzar una participación de 33.81 % a 1100 °C.
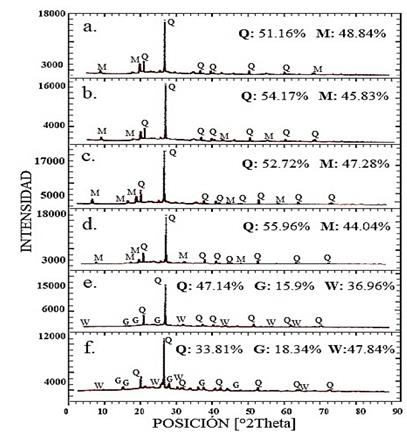
Fuente: Los Autores.
Figura 6. Patrones de difracción y porcentaje en peso de las fases presentes en los prototipos cerámicos a distintas temperaturas de sinterización. (a). 800 °C (b). 850 °C (c). 900 °C (d). 950 °C (e). 1000 °C (f). 1100 °C.
En el rango de 800 °C a 950 °C se halló la fase moscovita (M) con picos ubicados en 9.899°, 9.772°, 16.132° y 18.689°, los cuales disminuyeron en intensidad conforme aumentó la temperatura. Esta fase disminuyó su porcentaje en peso desde 48.84 % hasta 44.04 %. Sin embargo, a partir de los 1000 °C se presentó una transición en la cual se desarrollaron dos fases de alta temperatura del tipo gehlenita (Ca2Al(AlSiO7)) y wollastonita (Ca3(Si3O9)), esta última, un metasilicato de calcio que se presentó en la muestra en proporciones mayores que la gehlenita y cuarzo llegando a ser la fase predominante a 1100 °C. En este caso ambas fases son una reacción ocasionada por el aporte de sílice y calcio en los precursores, donde la sílice se difunde y avanza de forma preferente por los planos de fractura preexistentes.
3.2. Análisis microestructural
La Fig. 7 presenta las imágenes obtenidas por MEB del corte transversal de los prototipos cerámicos. En las muestras sinterizadas entre 800 °C y 900 °C (Figs. 7a y 7b) predomina una matriz de caolín con superficie rugosa homogénea y alto contenido de alúmina, este último presente en forma de escamas o láminas, concordando con los resultados obtenidos por DRX de la muestra de diatomita. En las imágenes se observan fragmentos de diatomeas constituidas por paredes celulares o frústulas de simetría central radiada, en su mayoría de forma cilíndrica donde la valva se halla dispuesta en referencia a un punto central.
Los prototipos sinterizados por encima de 950 °C (Fig. 7c ) presentaron una superficie más consolidada, sus cambios morfológicos obedecen a dos aspectos: las transformaciones de fase que suceden por encima de los 900 °C y la posterior aglomeración de partículas que origina un cuerpo cerámico mucho más denso [39,40]. Para este rango de temperaturas se observó en la superficie poros interconectados y aislados.
En las distribuciones de tamaños de poros presentadas en la Fig. 8 se corrobora lo observado en la microestructura del material, donde las frecuencias presentan un comportamiento de tipo normal, revelando una amplia gama de tamaños de poros que disminuyen conforme se incrementa la temperatura de sinterización. El ajuste gaussiano permitió identificar que los especímenes sometidos a temperaturas entre 800 y 850 °C presentaron diámetros entre 4.7-16µm (Fig. 6a) y 3.8-12.5µm (Fig. 6b); de 900 a 950 °C se exhibió una microestructura caracterizada por espacios interconectados con diámetros entre 2.7-11.6µm (Fig. 6c) y 1.9-10.4µm (Fig. 6d); por último, temperaturas entre 1000 y 1100 °C revelaron una geometría con cavidades más reducidas que oscilaron entre 0.14-7.6µm (Fig. 6e) y 0.01-3.6µm (Fig. 6f).
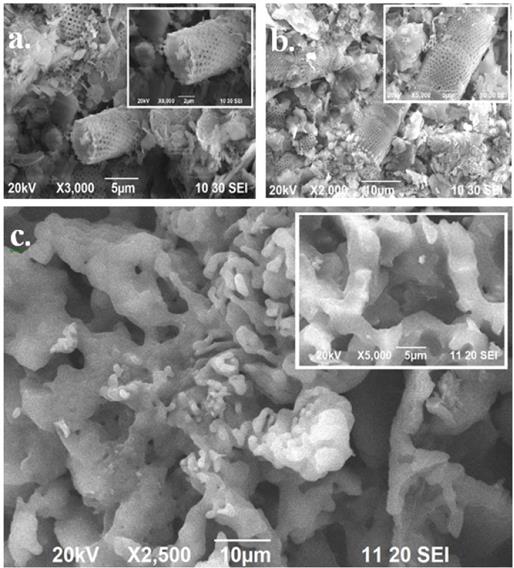
Fuente: Los Autores.
Figura 7. Microfotografías de MEB de prototipos cerámicos (a). 3000X y 6000X a 800 °C. (b). 2000X y 5000X a 900 °C. (c). 2500X y 5000X a 1100 °C.
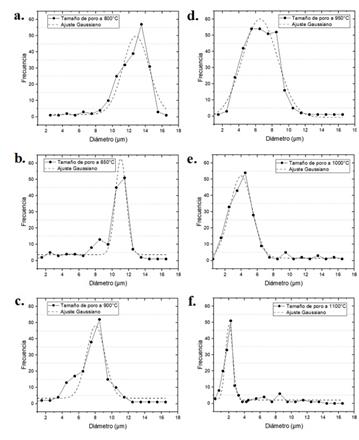
Fuente: Los Autores.
Figura 8. Distribución del tamaño promedio de poros según la temperatura de sinterización (a). 800 °C. (b). 850 °C. (c). 900 °C. (d). 950 °C. (e). 1000 °C. (f). 1100 °C.
De acuerdo a los tamaños de poros encontrados en la superficie se concluye que el compuesto combina macroporos y mesoporos distribuidos en su red interna [41], sin embargo, estos no evidencian un ordenamiento o jerarquía específica. La característica mesoporosa del compuesto facilita su aplicación en catálisis, fotoquímica, microelectrónica y como medio altamente microfiltrante [42].
3.3. Propiedades físicas
3.3.1. Densidad aparente
La densidad aparente de los prototipos se muestra en la Tabla 2. De acuerdo a los resultados, las menores densidades se hallaron en T1, T2 y T3, con valores de 1.22, 1.25 y 1.27 g/cm3, respectivamente. Sin embargo, con el incremento de la temperatura se produjo mayor densificación de las muestras, reportando para T4, T5 y T6 valores de 1.33, 1.45 y 1.75 g/cm3. Lo anterior, concuerda con lo observado en la microestructura del material para este rango de temperaturas, donde la aglomeración de partículas que ocurrió a partir de 950 °C origina una matriz más densa caracterizada por tener menores tamaños y cantidad de poros.
Además de la morfología del material, la evolución de la densidad también se atribuye a cambios ocasionados por la ruptura de los enlaces de agua que forman parte de la estructura cristalina del caolín, dando inicio a la vitrificación del material. Asimismo, el alto contenido de potasio hallado en la fase moscovita presentada en el DRX del mineral de diatomita, facilita la unión vítrea al reaccionar en forma de fundente alcalino con aquellas partículas más gruesas, dando origen a un cuerpo cerámico mucho más denso, rígido y con porosidad reducida [43].
3.3.2. Porcentaje de absorción en agua
Los porcentajes de porosidad por absorción de agua se reportan en la Tabla 2. Allí se observa en T1 y T2 los mayores valores con 74.96±2.27% y 71.04±2.52% respectivamente; para este rango de temperaturas se identificó una microestructura macroporosa que registró los mayores diámetros de poro con tamaños que oscilaron entre 12.5µm y 16µm. Lo anterior, demuestra la influencia del diámetro de poro en el aumento de la capacidad de absorción del material. Por otro lado, el menor porcentaje de absorción se presentó en T6 con 51.47±4.05%, esta reducción está relacionada con el aumento en la fase líquida conforme aumenta la temperatura y la disminución en la viscosidad [44]. En la Fig. 9 se observa dicho comportamiento, señalando la relación inversa entre la absorción del material y la densidad aparente de las muestras, en función de la temperatura de sinterización.
Tabla 2. Densidad aparente y porcentaje de absorción obtenidos para cada lote de temperaturas.
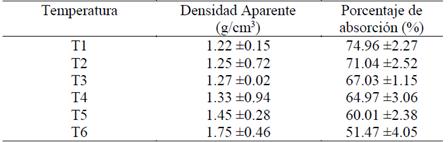
Fuente: Los Autores.
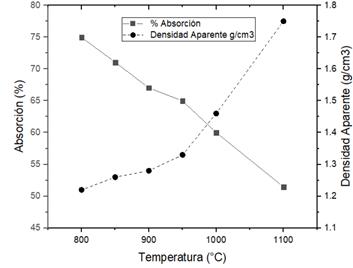
Fuente: Los Autores.
Figura 9. Efecto de la temperatura en el porcentaje de absorción y densidad aparente del compuesto cerámico.
Al comparar los porcentajes de absorción obtenidos en la mezcla propuesta, con los reportados por compuestos elaborados a partir de caolín y diatomita en composiciones de 60-40% (en peso), se observa el efecto de la adición de CaCO3 como agente formador de poros, al incrementar la capacidad de absorción en las muestras un 5% aproximadamente [21].
3.3.3. Contracción lineal
De acuerdo a los resultados presentados en la Tabla 3 e ilustrados en la Fig. 10, se puede observar que se produjo contracción en las tres dimensiones de los especímenes: largo, ancho y alto. Lo anterior es debido a la diversidad de intersticios observados en la microestructura del compuesto, lo cual ocasiona diferenciales de contracción entre las microrregiones del material.
Tabla 3. Porcentaje de contracción de los prototipos cerámicos en las tres dimensiones: largo, ancho y alto.
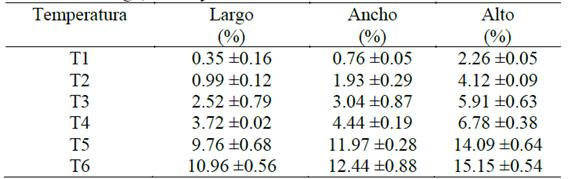
Fuente: Los Autores.
En las seis temperaturas se observa que la dimensión con mayor contracción es la altura, esto ocurre debido a que el peso del espécimen descansa sobre la cara que está directamente en contacto con la pared inferior de la mufla durante el proceso de sinterización, y por tanto, la presión ejercida en esta cara es mayor que en las demás, ocasionando que la altura del cubo cerámico sufra una contracción mayor en comparación con las dimensiones largo y ancho.
En la Fig. 10 se puede observar que la contracción del material es mayor a medida que aumenta la temperatura de sinterización, esto es producto de la reducción del tamaño de poro que se presentó en la microestructura a temperaturas elevadas.
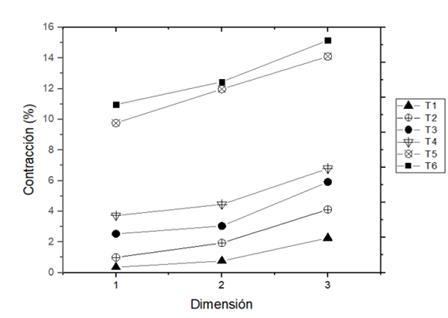
Fuente: Los Autores.
Figura 10. Porcentaje de contracción en las tres direcciones: 1. Largo, 2. Ancho, 3. Alto.
En comparación con los demás lotes de temperaturas, los especímenes correspondientes a T5 y T6 evidenciaron contracciones dos veces más altas, este aumento explica la estructura mesoporosa encontrada, donde para este rango de temperaturas se evidenció tamaños de poros del orden de 0.01µm y 0.14µm.
3.4. Propiedades mecánicas
3.4.1. Resistencia mecánica a la compresión
El ensayo de resistencia mecánica a la compresión evaluado en el compuesto presentó una gran dispersión durante cada prueba, en la Fig. 11 se observan los resultados obtenidos los cuales exhibieron variaciones significativas entre especímenes de un mismo lote de temperaturas. Sin embargo, cabe resaltar que el aumento de temperatura logró especímenes con resistencias más altas, siendo el caso de las muestras T5 y T6 con valores de 6.98 y 9.23 MPa.
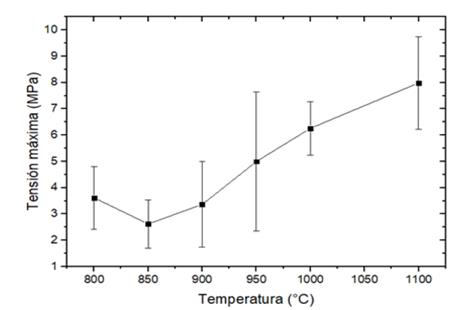
Fuente: Los Autores.
Figura 11. Media y desviación estándar de la tensión máxima hallada en los especímenes, en función de la temperatura.
Estos resultados coinciden con investigaciones reportadas por J. C. Anderson [45] donde se afirma que para compuestos cerámicos en lo que respecta a ensayos que involucran esfuerzos de fractura, se obtendrán diferencias considerables durante cada ensayo. Lo anterior se puede corroborar en la Fig. 12, donde se aprecia la dirección de fractura de dos especímenes pertenecientes a un mismo lote de temperaturas, allí se refleja las distintas orientaciones que adquirió la falla, las cuales pueden obedecer a imperfecciones internas ocasionadas durante el proceso de conformado, secado o sinterizado. Estas imperfecciones propagan la falla en diferente dirección y ubicación en relación con el esfuerzo aplicado; del mismo modo, los valores obtenidos pueden ser influenciados por los tamaños de grano en la matriz y la densificación de las muestras [46].
3.4.2. Ensayo de flexión a tres puntos
La resistencia a flexión de los especímenes aumentó gradualmente en función de la temperatura de sinterización como se observa en la Fig. 13, con valores entre 2.52 y 11.73 MPa en muestras pertenecientes a temperaturas desde T1 hasta T4. Posteriormente, se duplicó alcanzando sus máximos valores entre 23.81 y 45.70 MPa, correspondientes a especímenes de las temperaturas T5 y T6.
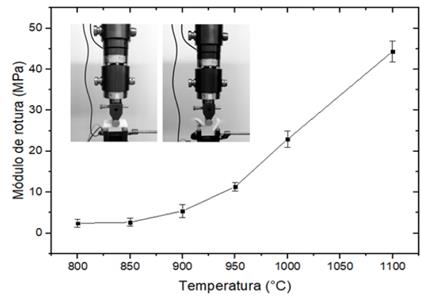
Fuente: Los Autores.
Figura 13. Módulo de rotura con desviación estándar, en función de la temperatura de sinterización.
Este aumento es atribuido a la presencia de wollastonita en este rango de temperaturas, fase .que se caracteriza por incrementar tanto la resistencia a tracción como a flexión [47]. La tendencia del módulo de rotura coincide con la reportada en trabajos de materiales porosos reportados por F. P. Knudsen y D. Liu [48,49], para los cuales este comportamiento se encuentra también relacionado con la disminución del tamaño de poro del material.
El módulo de Young o módulo de elasticidad lineal del compuesto, presentó un comportamiento creciente exponencial (R2=0.9828) conforme se aumenta la temperatura de sinterización, como se puede verificar en la Fig. 14. Teniendo en cuenta que factores como la densidad y porosidad influyen en esta propiedad mecánica [50], en la gráfica se puede observar que la densidad no afecta significativamente el módulo elástico de los especímenes, en este caso la densificación de las muestras presentó leves incrementos hasta alcanzar los 1000 °C y posteriormente presentó un ligero aumento, mientras que el módulo de Young se duplica hasta alcanzar 2.62 GPa, aproximadamente.
De acuerdo a estos resultados se concluye que el módulo de Young del compuesto es bajo en comparación con el reportado por otros trabajos realizados en materiales cerámicos similares, los cuales exhiben módulos del orden de 3 GPa hasta 278 GPa [51,52]. Lo anterior, evidencia que el comportamiento obtenido es característico en estos compuestos cerámicos y no es estrictamente una función de la porosidad, sino que a su vez depende de la morfología de poros, distribución del tamaño de poro, la microestructura y fases formadas [49,53].
4. Conclusiones
Se elaboraron prototipos cerámicos porosos a base de caolín-diatomita y refuerzo de CaCO3 por el método de slip casting o colado, a temperaturas de sinterización que oscilaron entre 800 °C y 1100 °C. De acuerdo a las difracciones de rayos X, todas las muestras evidenciaron la presencia de la fase cuarzo en su estructura Las imágenes MEB del corte transversal y la superficie de las muestras, permitieron identificar el tamaño y forma de los poros y grietas que se formaron durante el proceso de sinterización. Allí se pudo observar que la microestructura presentó macroporos y mesoporos distribuidos en toda su superficie, cuyos tamaños decrecieron conforme se aumentó la temperatura de sinterización, alcanzando diámetros entre 0.01 y 16 µm.
Por encima de 950 °C ocurrieron cambios morfológicos significativos en el material, los cuales son ocasionados por las transformaciones de fase y aglomeración de partículas. Estos factores originaron una mayor densificación en el compuesto alcanzando valores de 1.75 g/cm3 a 1100 °C.
Al comparar los porcentajes de absorción obtenidos en la mezcla propuesta con los reportados por compuestos cerámicos elaborados a partir de caolín y diatomita, se observa el efecto de la adicción de CaCO3 como agente formador de poros, al obtener un incremento aproximadamente del 5% en la capacidad de absorción del material. Este comportamiento es explicado por la reacción endotérmica que se genera durante el proceso de sinterización, donde la fase CaCO3 sólida se disocia en óxido de calcio y dióxido de carbono, este último en forma de gas que sale hacia la superficie generando canales porosos en la estructura.
Los valores obtenidos de tensión máxima en el ensayo de resistencia a la compresión y el módulo de rotura derivado del ensayo a flexión, presentaron una relación creciente con la temperatura de sinterización, esto atribuido a la formación de nuevas fases de alta temperatura como es el caso de la wollastonita. Cabe resaltar que del ensayo de resistencia a la compresión, la tensión máxima obtenida presentó altas desviaciones para especímenes de un mismo lote de temperaturas. Lo anterior, puede obedecer a imperfecciones internas producidas durante el proceso de conformado, secado o sinterizado de los prototipos.
De acuerdo a las propiedades y características morfológicas encontradas en el material propuesto facilitan su aplicación en procesos de catálisis, fotoquímica y otros procesos que requieran medios altamente microfiltrantes.