1. Introduction
The economic development and the National integration of a country are influenced by the economic sector of transport, specifically by road infrastructure. Statistical data of the state of the Colombian road network made by the National Institute of Roads (INVIAS), under the sub-direction of studies and innovation, indicate that Colombia has a road network composed of approximately 9115 kilometers, which 75.11% are paved roads, 24.69% unpaved and 0.20% are in intervention states. With regard to the paved road network, 52.71% are in a good to a very good condition and 47.29% in a bad to a regular condition [1]. Given this panorama, it is important to study new material technologies, mainly rolling layers, in order to address the structural and functional aspects for new and existing pavements.
In this sense, the modification of asphalt cements and asphalt mixtures is a technique widely studied and used in the world. The objective of the modification of asphalt cements and mixtures consists in improving the behavior of the mixtures before the solicitation of loads coming from the traffic and the climatic action. Currently, around the world, there is an alert conservation and preservation of the environment. Due to the above, initiatives arise to motivate the implementation of alternative materials such as asphalt cement modifiers. The use of alternative materials can contribute to improve some characteristics and provide a form of environmentally correct disposal [2].
Polymers are considered as the main materials for modifying the asphalt due to their physical, chemical and high compatibility characteristics. These materials can be elastomers, plastics and thermoplastic elastomers. The elastomers improve the behavior of the asphalt and the mixture before cycles of loading and unloading presenting elastic return in the deformation of the rolling layer. Plastics can be of the thermoplastic or thermo-rigid type, which increase the stiffness of the asphalt mixture and entail an increase in the degree of performance in service temperatures.
Thermoplastic elastomers exhibit behavior as a function of temperature; at high temperatures they have a thermoplastic behavior and at low temperatures they exhibit elastic behavior. Polymers can modify the rheological characteristics of asphalt cement as a function of the added content and molecular weights due to possible interactions of polymer-asphalt chains (physical or chemical) [3]. Approximately, 75% of the modified asphalts are improved with elastomers to increase the stiffness and guarantee the elastic return, 15% with thermoplastics and 10% with other materials, mainly acids [3]. The additions of the polymers improve the performance of asphalt and asphalt mixtures in the laboratory and field, mainly in terms of permanent deformation, fatigue resistance, susceptibility to humidity, resistance to aging, among others [4-6].
The recycled rubber grain (RRG), a product of the used tires, is considered one of the most used elastomer polymers for pavements built with modified asphalts. The final disposal of tires from vehicles represents a great environmental problem due to the need for large areas and exposure to weather conditions. Used tires subject to climatic action may be subject to water storage causing the habitat of pathogenic microorganisms that increase the risk to health deterioration of the human population. Various policies and studies have been formulated to guarantee sustainable practices that contribute for the conservation of the environment [7,8]. In this context, the producers of the pneumatic industry recycle the used tires to give them a correct disposition that does not affect the environment [9]. Some forms of recycling consider the application of rubber in pavement works for roads, the use in the manufacture of rubber artifacts, the use of incinerators as fuel for kilns for the manufacture of cement, among others [10,11].
Since the 70s, in the United States, paving works that include the use of AC modified with RRG from used tires have been reported [10]. This practice is very popular for being a solution to the environmental problem and for increasing the mechanical and functional performance of the asphalt mixtures improving their behavior against permanent deformations and fatigue cracks [4,9], which are considered as the main mechanisms of failure in flexible pavements [4].
The incorporation of the RRG in the asphalt mixtures is done by four techniques: dry, wet, terminal and fourth generation asphalt technique. (I) The dry route consists of the substitution of the fine fraction of the mineral aggregate (through the 10 sieve) by RRG. The disadvantage of the technique lies in the manufacturing and compaction process due to the short contact time between the RRG and the AC which gives rise to the reduction of adhesion and the appearance of cracks in the performance of the asphalt mix in the field. (II) The wet way consists of the modification of the asphalt cement by means of the inclusion of RRG in percentages lower than 20% (with respect to the total content of the asphalt cement). In this case, the asphalt cement is subjected to high temperatures and the incorporation of the RRG is done by means of rotational equipment during a determined time. The disadvantages of the technique lie in the high temperatures of mixing during which, premature aging in the asphalt is induced [10,11]. (III) The third technique of incorporation of the RRG consists of the incorporation by the wet and modified oils. This technique seeks to reduce the viscosity and, consequently, the manufacturing and compaction temperatures. (IV) The fourth form of incorporation of the RRG consists of the elaboration of a compound of granulated rubber. The rubber compound results from the interaction between the RRG and a mineral filler (filler) stabilizer from phosphate mining. The fourth-generation asphalt technique incorporates a wet process and a dry process respectively. Details of this technique can be found in [10-12].
This research work focuses on the evaluation and application of rubber grain from the soles of used military boots (R). We contacted several national companies that provide shoe supplies to their employees and it was observed that one of the biggest problems of the investigation is the final obtaining of this waste material due to lack of control over the final disposal of such product. Hence, it was identified that one of the entities that most produce this type of waste elements and has control over its collection is the Colombian National Army. In 2014, a production of military footwear of approximately 923 tons was included for 461092 members. In this sense, the final disposal of the boots used by the military generates a great latent environmental problem. The above because in some cases it is covered in areas specified by the army and in other cases as any other pollutant, without going through any type of process of recycling.
At the time of publication of this work, there are no specific studies of asphalt modified with footwear waste products. However, modified asphalt works were found with different types of polymers, or additives in general that are components of the waste material analyzed [13,14]. For this reason, the aim of this study is to evaluate the mechanical and dynamic behavior of asphalt mixtures modified with rubber grain from used military boots in order to generate a final disposal alternative of environmentally safe waste and propose practices of sustainable civil engineering.
2. Materials
2.1. Asphalt cement
Table 1 shows the physical characteristics of the AC used in this study. This material corresponds to an asphalt 60-70 and meets the requirements for the manufacture of hot asphalt mixes (MDC-19) established in the regulations of the National Institute of Roads - INVIAS [15]. Table 1 presents the general properties of AC 60-70 used for this study under original conditions and after rolling thin film ovens test (RTFOT).
2.2. Aggregates
The stone aggregate for the preparation of the asphalt mixtures is from the Colombian company Concrescol. Table 2 presents the physical characterization of the stone aggregate and the specifications for use in asphalt mixes [15]. The original grain size distribution was modified to fulfill with the specifications of INVIAS [15], using as reference the average values of the range required by the specification for the preparation of the asphalt mixtures (see Fig. 1).
3. Experimental program
3.1. Preparation and evaluation of modified asphalt
The rubber-modified asphalt mixtures with the used military boots were prepared using the wet method. The mass ratios of rubber and AC of R/AC of the tested samples were 2.0%, 4.2 and 8.7%. The samples were compacted in a rotational equipment at an average mixing temperature of 150ºC during 45 minutes. The rubber residue comes from the sole of the used military boots, which were subjected to a crushing process to obtain size particles passed through the No. 200 sieve in a granulometry test. The following tests were carried out on conventional asphalt cement AC 60-70 and the modified asphalts:
Physical characterization tests such as penetration, softening point and ductility, following the guidelines of the specifications [16,18,22], respectively.
Rotational viscosity by using a Brookfield viscometer following the protocols of ASTM specification D 4402 [30]. The viscosity readings were made with splinde SP21 for the conventional asphalt and with splinde SP27 for the modified asphalt, at 20 rpm at temperatures of 105, 120, 135 and 150°R. The results were expressed in graphical log-log viscosity (cP) versus log-temperature (°Ra), in order to determine the Susceptibility Index of viscosity at temperature.
Short-term aging in rotational thin-film furnace - Rolling Thin Film Oven Test (RTFOT) according to the guidelines of the specification ASTM 2872 [23], in order to evidence the change over time of the properties of asphalt due to processes such as oxidation and volatilization.
Rheological characterization by means of a dynamic shear rheometer (DSR) of parallel plates, following the guidelines of the AASHTO T 315 specification [31]. The test was conducted on samples with circular geometry of 25 mm in diameter and 2 mm in thickness, in order to obtain the complex cutting module (G*) and the phase angle (δ). The tests were carried out at temperatures of 40, 46, 52, 58, 64 and 70°C and frequency of 10 rad/s (1.59 Hz), corresponding to the speed of operation of a vehicle of 90 km/h. With the obtained data, the isochronous curves were constructed at a frequency of 10 rad/s, varying the test temperatures.
3.2. Design of asphalt mixtures with the Marshall methodology
After conducting the physical characterization tests of the materials (aggregates, conventional asphalt cement and modified mixtures), the control sample and the three study samples were prepared. The control asphalt mixture was made with the stone aggregates previously described and the AC 60-70. The three study mixtures were made with the three wet modified asphalts in rubber and AC R/AC mass ratios of 2.0%, 4.2 and 8.7%. The evaluation was performed for each Marshall design of five probable percentages of asphalt and four briquettes for each percentage of asphalt.
A total of 80 Marshall briquettes were made (20 for each type of mixture), in order to evaluate the mechanical properties of the control mixture and the study samples with the modified asphalts. The compaction temperatures - TC and the mixture - TM were 150 °C and 160 °C for the control mixture and the study mixtures respectively, based on the viscosity method of the AC 60-70. The asphalt mixtures were fabricated with the optimum percentages of asphalt cements determined in the Marshall methodology. With these briquettes the following tests were carried out:
Dynamic modulus under cyclic loads by diametrical compression according to the standard procedure of ASTM D 3497 [32]. The briquettes were compacted to 75 blows per face following the specifications established in [33]. The tests were carried out under temperatures of 10, 20 and 40 ° C and load frequencies of 2.5, 5.0 and 10 Hz. The dynamic modulus was measured in a Universal Testing Machine (UTM) using 4 briquettes of asphalt mix. The sigmoidal model was computed to obtain the master curves of the asphalt mixtures (see Eq. (1)). This model is incorporated in the mechanistic-empirical design guide MEPDG of the AASTHO [34].
In eq. (1), G* corresponds to the dynamic modulus of the asphalt mixture, which is assessed in the laboratory using different temperatures and test frequencies. The coefficients δ, α, β, and γ correspond to constants obtained from the material. The reduced frequency can be obtained by eq. (2).
In the construction of the displacement curve, it is important to determine the displacement factors and the selection of the reference temperature. The displacement factor a(T) of the isobars curves to the sigmoidal model is determined by eq. (3).
Where the values of a, b and c correspond to the constants of the material, the value of T at the test temperatures (10, 20 and 40 ºC), the reference temperature being defined as 20 ºC. The simultaneous solution of the above equations for the four study temperatures in the frequency and temperature ranges were performed determining the coefficients δ, α, β, γ, a, b, and c of the material from the iterative process of the mathematical solution of the model with respect to the values of dynamic module obtained in the laboratory test.
4. Results
4.1. Physical characterization of conventional and modified asphalt cement
Table 3 and Fig. 2 show the evolution of the physical characteristics (penetration, softening point and ductility) with the R/AC ratio. The results of consistency are expressed through the relation of the physical characteristic of the modified asphalt cement and the characteristic of the asphalt cement 60-70. This representation allows quantifying the effect of the addition of the rubber obtained from the used military boots in the asphalt matrix.
Table 3 Physical characterization of both conventional AC and cement modified with military boot rubber
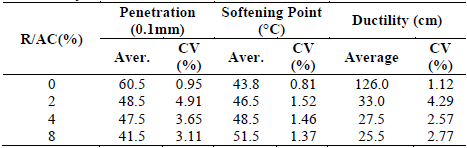
Source: The Authors.
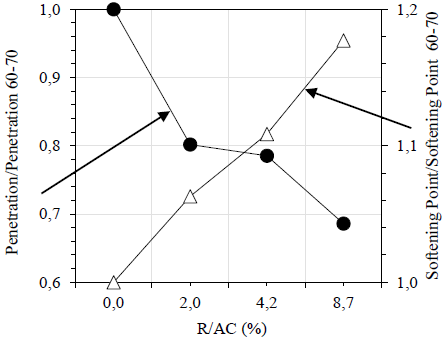
Source: The Authors.
Figure 2 Evolution of the penetration / penetration 60-70 and the softening point/softening point 60-70 with the R/AC ratio.
From test results, it can be observed that the penetration and ductility decrease, while the softening point increases as a function of the increase in R content which indicates greater stiffness in the modified asphalt. Therefore, 8% of rubber boots in the asphalt cement matrix decreases penetration and ductility by approximately 30% and 80% respectively, and increases the softening point by 18% with respect to the conventional AC sample. These variations may be associated with greater resistance of the asphalt mixture to the demands of traffic in climates of high temperatures.
Fig. 3 and Table 4 show the linear mathematical models of viscosity and the Susceptibility Index of Temperature Viscosity (ITS) of conventional asphalt cement and those modified with R. The results show an increment in the viscosity as a function of the R/AC ratio due to the increased thickness of the asphalt cement sheet due to the size of the grain particles of R. The greatest increment was observed at a temperature of 150 °C (762 ºRa), indicating at that temperature the particles of the grains of R do not dissolve in the malt oils and are attracted to the asphaltenes of the asphalt cement. The increments of the viscosity at elevated temperatures contribute to a reduction in IST and induce greater viscosity stability at 150 °C. However, the increase in viscosity in modified asphalts leads to increased manufacturing and compaction temperatures of asphalt mixtures.
4.2. Short-term aging on conventional asphalt cement and modified
When AC 60-70 is modified with R, the material undergoes mass loss reduction in the short-term aging test using the RTFOT in reference to conventional asphalt cement. The reduction of the loss of mass asphaltic cements modified with R can be attributed to the absorption of the malthenes from the AC by the grains of R during the incorporation process. In this sense, there is an increase in the oils in the asphalt cement during the short-term aging process. The chemical interaction between the asphaltic cement and the rubber grain coming from tires (35), can be used for the understanding of the modified AC with R since it is an elastomer type modifier. The incorporation of 2, 4 and 8% of R in the AC cause a reduction of the mass loss of approximately 40, 25 and 50% respectively, with respect to the conventional asphalt sample (see Table 5). The non-proportionality of mass loss as a function of the increase in the R / AC ratio may be related to the chemical interactions that occur during the process of modification and short-term aging. The maximum loss allowed per specification is 1%, in this sense, the asphalt modified with R meets the requirements for the manufacture of asphalt mixtures.
4.3. Rheological characterization on conventional asphalt cement and modified
Fig. 4 shows the evolution results of G* and δ with the test temperature (T) in the DSR on the samples of conventional asphalt cement and modified with R. There is evidence of an increase of G* and reduction of δ respectively, depending on the increase in the R/AC ratio for each temperature evaluated. The largest and smallest variations of the rheological parameters (G* and δ) were observed at temperatures of 40 and 90 °C, respectively.
The increase in G* is an indication of the increase in stiffness, as evidenced by the physical characteristics of R-modified asphalt cement. The increase in stiffness may indicate greater resistance of the asphalt mixture in service to rutting phenomena in climates of high temperature. The reduction of the δ is an indication of the elastic behavior of the asphalt cement that induces greater elastic recovery capacity of the mixture before the application of dynamic loads due to the presence of R particles that act as elastomers.
4.4. Design of mixtures of both conventional asphalt and asphalt modified with used military boot rubber
The results obtained from the Marshall test for the control asphalt mixture and the three asphalt mixes with modified asphalt in the mass ratios of rubber and R/AC of 2.0%, 4.2 and 8.7% are registered in the Figs. 5-9. From the volumetric parameters of the Marshall test it is possible to deduce that:
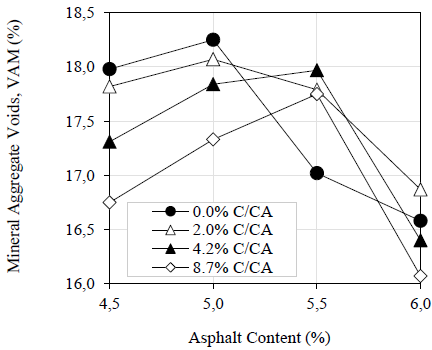
Source: The Authors.
Figure 6 Evolution of the voids in the mineral aggregate with the percentage of asphalt.
The volume of air voids (Va) in the asphalt mixture decreases as a function of the increase in the percentage of asphalt. For the asphalt content of 5.5%, it goes from the asphalt mixtures increases in reference to the control mixture.
Voids in the mineral aggregate (VMA) can be defined as the volume of air and asphalt in the mixture. To guarantee a minimum thickness of asphalt sheet for the coating of the particles, the INVIAS specification establishes a minimum value of 15% for a nominal maximum aggregate size of 19 mm. In general, the control mixture and the three study mixtures meet the minimum value of the specification.
Voids filled with asphalt (VAF) can be understood as saturation with asphaltic material in the mixture. The INVIAS specification establishes an interval between 65 and 75% for the determination of the optimum content of asphalt. In this sense, it was evidenced that the control mixture and the three study mixtures with addition of R only fulfill the minimum value of VFA with 6.0% asphalt.
From the parameters of the response to the action of the monotonic load of the Marshall test it is possible to deduce that:
Additions of R in the asphalt mixtures increase the stability value in reference to the control mixture. In this regard, it is noted that stability increases proportionally to the amount of R added by the wet process.
Asphalt mixtures with R/AC of 4.0 and 8.7% showed an increase in flow concerning the R/AC control sample of 0%. This behavior is typical of mixtures with modified asphalts of the elastomer type, which increase the deformability of the material by the asphalt sheet. However, the sample with R/AC of 2% with 4.5% and 5.0% of asphalt experienced a reduction of the flow concerning the control sample.
The E/F ratio indicates the Marshall stiffness of the material at the break. The mixtures with addition of R experienced greater increments in Marshall stiffness concerning the control mixture. However, the largest increases in E/F were recorded for the mixture with R/AC of 2%, followed by the mixtures with R/AC 4% and 8%, respectively. Higher values of S/F indicated that the material experiences greater load capacity in the rupture and less deformability.
The content of asphalt cement of 5.0% in the control mixture and in the study mixtures with addition of R guarantees the compliance of the volumetric parameters of the INVIAS specifications [13] for the layer of rolling of pavements (such as Va, VAM and VAF). However, the asphalt cement content of 5.5% in the mixtures recorded the highest values of Stability (S) and Marshall stiffness (S/F). Therefore, the optimum content of asphalt cement was defined as the average of the two values, obtaining a value of 5.3%, which guarantees compliance with the specifications of the INVIAS for the asphaltic layer.
4.5. Evaluation of the dynamic modulus
Table 6 and Fig. 10 present the parameters and the master curves for the control mixture and the mixtures with the addition of 2.0 and 4.2 R/AC, respectively. From the interpretation of Fig. 10, it can be observed that there is a significant increase in the dynamic modulus (G*) in the mixtures with the addition of R in reference to the control mixture. The increase of G* is attributed to the increase in the consistency of the asphalt cement (physical and rheological properties) by the inclusion of R. The mixture with R/AC of 2.0% presented the greatest increases in stiffness in reference to the control sample, which shows concordance with the S/F ratio obtained from the response to the monotonic charge action.
5. Conclusions
The following conclusions are drawn from the study of modified asphalt cement with rubber grain from used military boots and subsequently in the mechanical performance of asphalt mixtures:
The presence of rubber grain particles from the used military boots in the asphalt matrix increases the consistency of the asphalt mixtures. This was evidenced by the decrease in penetration, ductility and mass loss in the short-term aging, as well as the increase in the point of softening and viscosity. The variations were proportional to the increase in the R/AC ratio.
The increase of the consistency and the dynamic shear modulus of the asphalt modified with R produce an increase in the rigidity of the asphalt mixture. This is a result of the increase in the Marshall (E/F) stiffness and the dynamic modulus concerning the control sample. The increase in stiffness in the asphalt mix leads to a better performance of the tread layer in terms of the reduction of permanent deformation, mainly in zones with high temperatures. However, further studies must be carried out to evaluate the behavior of the asphalt mix with the addition of rubber from used military boots in terms of adhesion and fatigue resistance. The incorporation of rubber from used military boots in the asphalt cement matrix and later in the asphalt mixtures represents an alternative to reduce the great environmental problem of the final disposal of solid waste, contributing to generate practices in the sustainable civil engineering field.