1. Introduction
The scarcity of natural aggregates for making concrete is an increasing concern for the industry in certain regions. The consumption of natural aggregates for making concrete was about 2500 millions of tons in 2016 in the European Union [1]. This demand alerts on the availability of natural aggregates in the near future. In particular, the scarcity of natural sand in many countries leads to the need of finding alternative sources of fine aggregates. In this regard, manufactured sand is a byproduct of the coarse aggregate production that has been successfully used for making concrete. Although it has been concluded that angular shape of fine aggregates increases compressive strength in comparison with rounded shapes [2-4], the detrimental impact on fresh properties is the main limiting factor to increase its use. However, increasing the content of manufactured sand in new concrete involves environmental benefits since lower quantities of natural sand would be required.
Although the literature well establishes the influence of aggregates characteristics, such as maximum particle size, particle size distribution, shape, surface roughness and angularity, on the consistency of concrete [5-9], in many cases there is a remarkable absence of an explicit reference to the mechanisms by which this influence occurs. For example, there is consensus that spherical shape and smooth surfaces contribute to the fluidity of mixtures, in contrast with angular shape and rough surfaces (typical of manufactured aggregates). This former type of particles also required a greater water content for a given consistency level. Nevertheless, a standard quantification method of this difference is lacking. There are several proposed methods with varying complexity for the assessment of shape, angularity and surface texture [10-16]. However, studies linking the impact of each parameter to the properties of the cementitious mixtures are still lacking.
Aggregates are only a part of the mixture, and their influence on the fresh properties of concrete decreases with the increment in cement paste content. The minimum influence of aggregates is obtained when the aggregate/cement ratio is less than 2 or 2.5 [17-18]. As a rule, cement paste lubricates aggregate particles and provides mobility and cohesion to the mixture. However, with increasing paste content interaction between aggregate particles is reduced, and a large relative volume of paste causes that flowability being mainly ruled by the rheological parameters of the paste itself. In this regard, some authors [19] found that there is good correlation between the flowability of mortar and the paste/solids ratio (in volume) when this ratio is higher than 1.1 times the maximum voids ratio (determined according to [20]), independently of the characteristics of the aggregate.
In consequence, the void volume in the granular skeleton can be used as a design parameter. Cabrera et al. [21] related the specific void volume (Vv) for different types of fine aggregate to the fluidity of mortars made with them. They found a relationship between the Vv and the amount of water required to achieve a specific flow level. They also concluded that once the Vv between fine aggregate particles is filled with paste, any increase in the volume of the paste over the Vv has an equivalent impact on flowability, regardless of the shape and roughness of the fine aggregate particles.
On their own, Jarvenpaa [22] studied 21 different types of aggregates and found that their shape and porosity influence the fluidity of concrete to a similar extent or more than the cement content. The generalization of this finding should take into account that the influence of particle shape also depends on its size. In this sense, angular particles with sizes between 2.36 and 9.5 mm worsen the mixture fluidity than other size ranges [23].
Due to the aforementioned detrimental effects of manufactured aggregates on the fresh properties of concrete, there are recommendations for limiting the content of flaky and elongated particles in concrete. For example, the Argentine Regulation CIRSOC 201-2005 [24] sets the maximum percentage of manufactured sand at 30% of the total fine aggregate content, while the limit for elongated coarse aggregate particles is 40% wt. For the aggregate package as a whole, contents below 15% wt have been recommended [25]. However, the increase in the use of manufactured sand is environmental favorable as this aggregate is a byproduct of the production of crushed coarse aggregate. Then, a convenient valorization is required for it. Natural sands are very scarce in many geographical areas with a long history of exploitation, so their use can be avoided at the same time.
1.1. Mixture proportioning methods: background
The aim of increasing the relative content of manufactured fine aggregate in optimized concrete mixtures requires correlation studies between aggregate characteristics and the properties of fresh concrete. In other words, a rational proportioning method of aggregates needs to be in connection with their geometric characteristics. Otherwise, solutions for dealing with the poor fresh performance of concrete containing manufactured fine aggregates are solely based on the use of a higher dose of plasticizer or water content [26-27]. This procedure commonly indicated in the guidelines of general design methods can lead to less stable mixtures.
For example, traditional proportioning methods (ACI 211 [28]; ICPA [29]), determine mixing water content on the basis of the maximum aggregate size and required consistency level. Subsequent provisions are made for adjusting the amount of mixing water or using water reducing admixtures depending on the shape of aggregate particles. This sequence hardly results in optimized mixes. Other proportioning methods such as the Bolomey method [30] are based on the optimization of the aggregate package. In this case, the focus is put on the best particle size distribution, with coefficients that considers the aggregate nature and the required consistency of the mixture. That is, it accounts for the shape of aggregate particles by using one or another coefficient value according to whether a natural or manufactured aggregate is used. It is noteworthy to mention that according to the type of crushing process, the shape of aggregate particles can vary from cubic to elongated. The manner in which these design methods take into account the aggregate shape and surface roughness is still somehow simplistic. In fact, they do not optimize the mixtures, but it merely solves the issue of an increased harshness of the mixture due to the type of aggregates.
Although it was concluded that Vv of aggregates determines water demand in concrete [31-32], and that denser granular packings produce concretes with lower requirements of paste content [33-34], there is no standard guideline for using these variables as design parameters.
Special interest arises for the Compressible Packing Model Method [35]. It allows optimizing the mix design through parameters of the granular skeleton, such as shape, surface roughness and particle size distribution of the aggregates. All these parameters are globally correlated according to their packing capacity. However, the complexity of the method and the need for calibration of the model for the mix of constituent materials make difficult its universalization and application in the field.
In this paper, an approach for a proportioning method based on the minimum Vv of mixes with manufactured sands, natural or recycled, is presented and linked with the fresh and hardened properties of mortars with aggregate/cement varying between 3 and 1.5.
2. Materials and methodology
2.1. Materials and methodology
Four coarse sands were selected (CSs): three manufactured sands (quartzite (Q), granite (G) and recycled (R)) and a coarse river siliceous sand (S). Each one of these sands was used in combination with a fine river siliceous sand (Sf). Recycled sand was obtained from crushing waste concrete from a ready-mix plant,
Fig. 1 shows the images of the four CSs obtained with stereomicroscope. Sands differ in shape and surface roughness with S being the most spherical and with smoother surface, and the R the one with the highest surface roughness and the most angular. Physical properties for the sands are presented in Table 1.
Table 1 Physical properties of sands.
Properties | R | Q | G | S | Sf |
---|---|---|---|---|---|
Density | 2.30 | 2.55 | 2.69 | 2.65 | 2.65 |
Absorption (%) | 10.35 | 4.09 | 0.62 | 0.62 | 0.30 |
Material finer than 75µm (%) | 1.26 | 8.13 | 2.8 | 0.59 | 1.50 |
Fineness Modulus | 3.55 | 3.82 | 3.59 | 3.41 | 1.20 |
Source: The Authors.
For the design of mixtures, mortar was optimized for maximizing the use of manufactured sand with minimal increase in cement demand. The scheme of the proposed rational proportioning method is as follows:
Determination of the proportions for the blend of fine aggregates that corresponds to the minimum void content (ASTM C 1252) of the granular skeleton computed from the unit weight (UW). For this, combinations with variable contents of CS-Sf are prepared, and the optimal mix is defined as the combination with the lowest Vv.
Determination of the minimum paste content that allows the targeted level of consistency, quantified by the slump or flow methods depending on the level of fluidity. With the optimal mix defined previously for each CS, mortars with water/cement ratio (w/c) 0.50 and fine aggregate/cement ratios (A/C) 1.5, 2, 2.5 and 3 were prepared. Water absorption of all aggregates was compensated by adding 50% of the 24h-water absorption to the mixing water.
Each mortar was evaluated in the fresh state by means of the slump test [36], spread, flow, entrained air and unit weight. The spread value corresponds to the relative increase in diameter measured after removing the truncated cone mold, resulting from the deformation of the mixture by the action of its own weight. The table is then given 10 free fall strokes in 10 s, in accordance with ASTM C1437 [36], and the flow value is determined as the relative increase in diameter of the fresh sample.
Additionally, in order to establish the influence of the sand particle shape and surface roughness on the Vv, the particle size distributions of G, R, and S coarse sands were modified to reproduce the one of the quartzite sand (Q), which originally had the lowest Vv. Thus, CS-Sf combinations with the same particle size distributions were analyzed through UW and Vv, with shape and surface of the particles as the only variables.
3. Results and discussion
3.1. Aggregates
Variations in the compacted UW from different CS-Sf combinations are presented in Fig. 2a. Each point is the average of at least three determinations. Representative sampling was applied in all cases. The absolute percentge difference between the three determinations was below 0.5% in all cases. The maximum UW was obtained for 40, 60, 70, and 80 % contents of R, Q, G, and S, respectively. Minimum Vv was obtained for combinations of 50, 60, 70, and 80% of R, Q, G, and S, respectively (Fig. 2b). Small differences between the combinations for the maximum UW and minimum Vv are due to differences in densities of CSs and Sf (which is most evident for the case of R). Therefore, the optimal mixing ratio R-Sf changes depending on if it based on the UW or Vv values (40% for maximum UW and 50% for the minimum Vv).
The nomenclature includes indication of the percentage in which each coarse sand was used (which corresponds to the lowest Vv of each CS-Sf blend). For example, Q 60 indicates 60% quartzite manufactured sand, by weight.
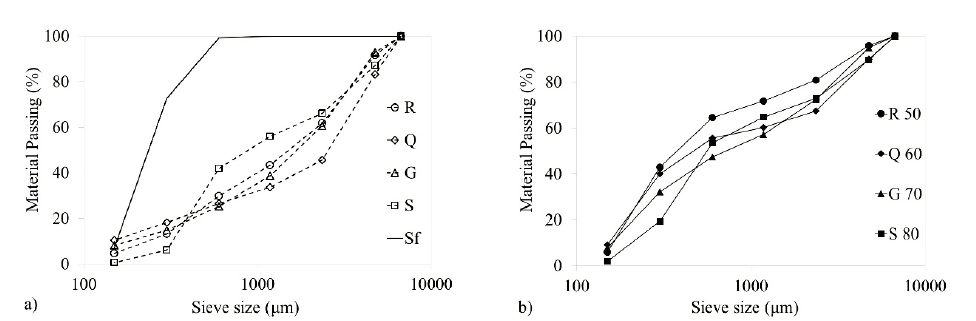
Source: The Authors.
Figure 3 Particle size distributions: a) Individual aggregates, b) CS-Sf blends.
This implies that blends made with this sand result in increased discontinuity of the particle size distribution with increasing Sf content. Due to the reduced particle sphericity of CSs, this discontinuity involves an increase in the value of Vv only when the content of Sf is higher than the minimum volume of Sf required to fill the space among CS particles, not as consequence of their particle size distribution but of their shape.
Fig. 4 shows the internal friction angle for each optimum combination of CS-Sf. The internal friction angle was measured from the ratio between the height and diameter of a cone of 10 cm in diameter formed by free fall of the material from a minimum height. Aggregate S 80 has the lowest internal friction angle because of its rounded shape, followed by the aggregate R 50, with 50% of Sf. Mixtures Q 60 and G 70 have similar values of the internal friction angle. This is unexpected as the mix G 70 has a higher content of manufactured particles, which have also lower sphericity than Q particles (see Fig. 1). Therefore, the higher than expected internal friction of Q 60 could be due to its rough surface rather than to its shape and to the higher content of particles lower than 75 μm, which in terms increases the internal friction angle [27].
Clearly, internal friction due to the texture of particles requires a smaller volume of paste to achieve mobility in the mixture than that due to the shape of particles, since a smaller volume of paste is required to form a lubricating film of a rough surface than to compensate for the lack of sphericity of a particle with equivalent size.
As it was mentioned above, the particle size distribution of Q was reproduced with each one of the other coarse sands (G, R, and S), in order to establish the influence of the particle shape and surface roughness on the Vv, Figs. 5a) and b) show UW and Vv, respectively, for the same particle size distribution of the CSs-Sf blends. From the results, it appears that there was no change in the proportions for which the maximum UW and minimum Vv are obtained when the same particle size distribution of CS is applied. Furthermore, from the comparison between Vv for 100% content of CS in Fig. 3b and 6b, it arises that the quantitative influence of particles shape and texture is less than that caused by the particle size distribution. In this sense, for low contents of CS, the curves differ less in the Vv values when the particle size distribution is the same, due to a reduced presence of coarser particles which have little incidence when surrounded by particles of Sf. In these cases, Sf particles only compensate gaps caused by the particle size distribution of the coarse sand. CS texture starts showing significance only with CS contents over the optimum proportion. In addition, a small reduction in the Vv values for R and G blends is noted in Fig. 5.b), respect to those in Fig. 2b, but a significant decrease is produced for S aggregate instead. In this case, particle shape and texture influence the Vv of the blends more than the particle size distribution. The same tendency can be observed for UW when comparing Fig. 2a and 5a.
3.2. Mortars
Fig. 6 shows the results of slump a) and flow b) as a function of the paste volume to Vv ratio (Pv/Vv) for mortars made with CS-Sf blends maintaining the original particle size distribution of each CS. For the four CS-Sf blends, slump and fluidity increase with increasing Pv/Vv due to the increase in the thickness of lubricating film and the lower incidence of aggregate due to its lower relative content. The same cause leads to fluidity of the mixtures to tend to the same value with increasing relative volume of paste, regardless of the type of aggregate used. However, contrary to what is indicated in the literature [21], increasing the volume of paste over Vv did not caused proportional increases in fluidity of mortars with independence of the shape and texture of the granular skeleton. In this matter, the lower fluidity of mortars made with Q 60 aggregate can be attributed to the higher content of material finer than 75µm in this aggregate.
In Fig. 7, spread values as a function of Pv/Vv are presented. The comparison among mortars with different types of aggregate reflects that the behavior for spread resembles those earlier described for slump and flow for values of Pv/Vv above 2.5. However, differences for spread are larger. This is, in agreement with [31], where different impact of Vv on different consistency test methods is also reported. This fact indicates the greater sensitivity of slump for the evaluation of plastic mixtures, whereas spread corresponds better with consistency of fluid mixtures. The different sensitivity of each method is based on the mechanisms on which each one is based for measuring the deformation of the fresh mixtures. Slump measures the drop due to the weight of the sample (plastic behavior), whereas spread measures the expansion of the base (fluid behavior). Flow also measures spreading out, but with the aid of freefall strokes. Such a provision of energy progressively turns slump into spread, when it decreases the incidence of internal friction among particles.
Figs. 6 and 7 also show that for a given fluidity level, the aggregate with less paste requirement is S followed by R, G, and Q. This behavior is in general consistent with the respective friction angles of each blend (see Fig. 4). The similar friction angle between Q60 and G70 mixtures was due to the rougher surface of Q60. A lower flowability of G70 mortar was therefore expected. However, Q60 showed significant higher consistency than G70. This fact could be attributed to higher content of particles between 2.36 and 4.75 mm (32.6 and 27.6, for Q60 and G70, respectively) which exert a larger influence on the flowability than other particle size ranges [23], also Q60 shows higher content of particles lower than 75μm which increase specific surface and consequently water demand [25].
In Fig. 8, entrained air as a function of Pv/Vv is presented. The content of entrained air decreases with increasing Pv/Vv. This can be explained by the increase in the fluidity of the mixtures and consequent decrease in the viscosity, which allows entrained air to be released more easily. For Pv/Vv lower than 3.0 entrained air is higher in mortar with manufactured sand in comparison with those made with rounded sand (S80), while for Pv/Vv higher than 3.0 entrained air is similar for all mortars. It is well known that particles with angular shapes tend to occlude more air [25].
However, for the same level of entrained air and Pv/Vv lower than 3 in mortars with Cs, no correlation with the internal friction angle could be obtained in this work. According to the literature [17], it is possible that the content of particles between 600 and 150 μm (39.6, 46.4 and 58.6 for G70, Q60 and R50, respectively) exerts higher influence in the entrained air than the internal friction angle. In general, the results are a consequence of the fact that air is occluded in the paste, and for higher Pv/Vv, the properties of the paste dominate and the relative influence of aggregates decreases.
In Fig. 9, UW is presented in terms of Pv/Vv. Unit weight decreases as Pv/Vv increases for Q 60, G 70, and S 80, while it remains the same for R 50. This is because R density is more similar to the paste than the rest of aggregates, and the increase in paste content offsets the decrease in air content with decreased aggregate content. For the rest of the aggregates, the decrease in UW due to the increase in the content of paste is greater than the increase in UW due to reduction in the air content. That is, the indirect effect of paste content through the entrained air has greater impact than the direct effect of the lower density of the paste.
In Table 2 the values of compressive strength determined at the age of 28 days, together with the corresponding standard deviation, are presented. There is no clear trend for the compressive strength according to the A/C ratio. The compressive strength values of mortars with G and Q aggregates are in general higher than those for R and S mortars for the same A/C ratio. This can be due to the internal friction angle of aggregates (Fig. 5), as the influence decreases with the decrease in the aggregate content. From Table 2, it emerges that the amount of manufactured fine aggregate can be increased with no detrimental effect on the compressive strength compared with mortars with rounded sand, furthermore, with no increase in cement content.
4. Conslusions
This study presents the evaluation of properties of three manufactured fine aggregates compared to a natural aggregate, and mortars made with them. The experimental design tended to the verification of a rational procedure for optimizing the proportioning of manufactured fine aggregates in mortar. From the results, the following conclusions are drawn:
The particle size distribution has greater influence on the void content of the granular skeleton than the shape and texture of manufactured aggregate. Therefore, the determination of the aggregate bulk void volume allows an initial quantification for optimizing the granular skeleton composed by a mix of aggregates. Cement content for a targeted consistency level is therefore minimized.
The internal friction angle is shown as a useful parameter, complementary to the particle size distribution. It allows to comparatively establish the differences in shape and texture of the different aggregates. However, it was found that this influence is also partially included in the bulk unit weight.
Consistency and air content of mortar decrease with increasing paste volume to void volume ratio (Pv/Vv). This is attributed to a thicker lubricating film on the aggregate particles that promotes mobility and it consequently eliminates entrained air. However, these values are not likely to have a direct application to predict the air content of concrete, due to the additional modification of the granular skeleton caused by the coarse aggregate.
It was not possible to define a single paste demand to comply with the paste film thickness that allows a certain targeted consistency level. Moreover, the effect of exceeding paste volume over the void volume on the flowability of mixtures was not proportional to this exceeding volume. This is indicative of the influence of the shape, texture, and particle size distribution of each aggregate on the required film thickness.
The relative influence of the Vv of the aggregate on the consistency of mortar was experimentally determined. As it was expected, the slump method was more sensitive to changes in the consistency due to variations in Vv for plastic mixtures, whereas the spread method was more convenient for fluid mixtures.
The density of aggregate is also an important parameter for defining the proportions. The unit weight of mortar decreases with increasing Pv/Vv for aggregates with higher specific gravity than the paste, and it increases for the opposite case. This suggests the need of considering methods that include volumetric relationships for blends of aggregates with significant differences in specific gravity.
The compressive strength for different fine aggregate to cement ratios was similar. The type of aggregate showed a greater impact in this regard. The proposed methodology for mix proportioning demonstrated that the content of manufactured sand can be maximized without detrimental effect on the compressive strength.