1. Introduction
The continuous deterioration of materials has become one of the major problems faced by the industrial sector. Therefore, time and money have been invested throughout generations to mitigate the consequences, as Asrar et al. [1] state when explaining that, from the beginning, the Chinese and Roman civilizations used bitumen, lead-based paints, and copper sulfide coatings to eliminate the destructive action on metallic materials. However, for the British, this effort was insufficient because the corrosion rate of the bolts that secured their ships increased due to an augmentation of biological incrustations.
In an analysis of the spread of corrosion in materials, Michael Faraday proposed a mathematical relationship between the chemical action of corrosion and electric current. Companies in the United Kingdom pointed out the importance of prevention and control because the side effects would imply a higher cost [1]. Nowadays, scientific and technological advances have been implemented, among which thermodynamic and kinetic protections, protective barriers, structural design, environmental control, and metallurgical designs stand out, to extend the useful life of structures and instruments, using qualitative and quantitative tools to know the evolution of the destruction and speed of corrosion [2], so that resources can be allocated to problems that require higher priority such as starvation or simply the generation of savings [3].
Salazar and Vallejo [4,5] define corrosion as a natural process of deterioration, wear, or destruction of a metal or material, which, when in contact with a corrosive environment, changes its physicochemical properties, allowing it to return to the natural state in which it was found in the ore; it experiences a dissipation of energy and abandons the state for which it was transformed, i.e., the constructions and engineering works that use this material are affected. Failures in the internal structure are mainly due to the surface condition, the temperature of the environment, as it is a variable that accelerates the oxidation-reduction reactions, the difference between oxidation potentials between two metals of different chemical nature, the environment surrounding the material (for example, oxygen and water vapor), the time elapsed since the metal surface has been used for a certain function, etc. [6]. In chemical terms, corrosion is produced by oxidation-reduction type reactions, in an electrochemical environment, where the metal is in contact with an electrolyte and simultaneously both (metal and electrolyte) exchange electrons, i.e., give or gain ions, becoming positively (cation) or negatively (anion) charged. The one with the lower oxidation potential will tend to give up more electrons (anode) and thus corrode [4,7]. Anodic or reactive metals have a lower electrochemical potential (zinc, steel, aluminum, magnesium, and tin) compared to cathodic or inert metals (brass, copper, bronze, silver, and gold) [8].
An electrochemical environment consists of a conductive metal, an electrolyte in charge of transporting electrons all over the metal surface, and the presence of oxygen for the development of the reactions [9]. Corrosion is an inevitable process in which materials return to their natural primitive state and abandon the transformation given by human beings. The previous can be affirmed physicochemically, since it is demonstrated that, being a natural process, it is spontaneous, so the variation of Gibbs free energy (ΔG) will be negative. If this value (ΔG) is compared with a group of metals, the one that obtains a more negative value will be the one that will tend to corrode more, which does not mean that it will be the metal with a higher corrosion rate. It is worth mentioning that the Gibbs free energy is an independent variable of the reaction kinetics [10].
This phenomenon is affected by temperature since as it increases, the movement of molecules augments [11]. Thermodynamically this implies an increase in the disorder of the system, i.e., in entropy (ΔS), hence in a spontaneous process ΔS > 0 [11]; in this type of transformations it is determined that the reactants are less stable than the products [11], so in corrosion, the metal reacts with oxygen and with the corrosive environment until it reaches its natural state, i.e. the products of that particular reaction will be more stable, which implies better resistance to deterioration and, consequently, a positive electrochemical potential [4].
Corrosion has been labeled as undesirable for local and foreign companies, especially for those that treat metallic, ceramic, polymeric, and composite materials, because it can generate effects like the interruption of manufacturing activities, production loss, environmental pollution, reduction in the efficiency of processes and maintenance, costly designs, affectation of chemical plants, or the collapse of structures (bridges, buildings, roads) [12]. The corrosive phenomenon has not only caused operational failures but also catastrophes that take the lives of many, and end up in the respective industrial implications that involve a high expenditure of resources and the constant search for retardant solutions to this massive waste. Therefore, it is estimated that the corrosion industry demands a series of high costs, and attempts to estimate their total value vary according to the study method used.
According to the study Impact, by the National Association of Corrosion Engineers (NACE), in 2013, it is estimated that the costs attributed to corrosion damage represent 3.4 % of the world gross domestic product (GDP), translated into a sum of USD 2.5 trillion, not including costs for individual safety or environmental impacts. Of this amount, about 15 to 35 % can be saved i.e., between USD 375 and 875 billion per year if adequately distributed, as proposed by the Corrosion Management System [13]. Industrialized countries have in common that their annual corrosion costs range between 1 and 5 % of GDP, where 3 to 5 % come from corrosion of steel and its derivatives [12, 14]. In the United States, corrosion costs are estimated to be around 500 billion dollars, equivalent to 3.1 % of the GDP; a high figure, because although the annual costs due to climatic events are equivalent to 87 billion dollars, the economic effects of corrosion exceed six times those of natural disasters caused by climatic conditions. This fact suggests a better use of funds, as experts estimate that 25 to 30 % of corrosion costs could be avoided by including prevention strategies [1].
The US oil and gas industry spends billions of dollars annually as follows: storage (7.0), tankers (2.7), pipelines (7.0), production (1.4), distribution (5.0), and refining (3.7), totaling 26.8 billion, as refining together with processing and transportation (i.e., production, pipelines, and tankers) make up 41 % (11 million/year), that show how the amounts in the oil sector due to corrosion are distributed and approximately how much they are equivalent to [1].
Although the above are industrialized countries, it should be noted that corrosion also occurs in underdeveloped economies such as Mexico and Colombia, where metallic materials deteriorate, forcing an increase in expenses, either for maintenance, protection, or replacement of metallic parts [15]. For example, in Colombia, the disbursement for corrosion has been calculated between 1 to 4 % of the GDP, indicating that more than three billion pesos are lost in the Colombian industry [16,17] distributed in several costs: technical support, reduction of the productive process, health; in control costs: resistant materials, replacement equipment, maintenance, and in opportunity costs: production paralysis, customer neglect, loss of customers and bad image [18]. According to appendix A of the Impact study, by NACE in 2013, the GDP in Colombia has been evaluated at USD 369.20 billion, and corrosion costs are distributed in such a way that 6.6 % (USD 24.37) corresponds to the agricultural sector; 37.8 % (USD 139.56) represents the industrial sector, and 55.6 % (USD 205.28) is directed to services [13]. In short, it is essential to promote the development of techniques that extend the useful life of materials to reduce the economic impact of corrosion.
The corrosive phenomenon lacks a solution. Therefore, the principal achievement has been to mitigate it. Namely, the integrity of metals exposed to extreme environments has been prolonged so that the corrosive action is limited for specific periods. The aim is to reduce the economic impact generated in the industry and, more importantly, to safeguard the lives of those who have direct or indirect contact with this process (profitability and safety). That is why monetary resources have been allocated: to study preventive methods that contribute to partially stop the wear factors, taking into account an adequate selection of the process because it is linked to the type of material, environmental conditions, economic circumstances, exposure time, among others. The Eiffel Tower is a real case of mitigation. Since its construction and once every seven years, it has been painted nineteen times to restore the most corroded areas of the infrastructure and extend its use [19], which requires a rigorous preparation, since the life of the painters and specialists in metallic carpentry, as well as those of the tourists who visit it, are exposed.
Other alternatives to control the corrosion would be the design and media modifications such as inhibitors, whose definition is reduced to a chemical substance that hinders the continuity of the oxide-reduction reaction, so that, as stated by Pizarro [20], when added moderately in the corrosive medium, the rate of deterioration in the metal is reduced.
Currently, the use of green technologies has been promoted to produce sustainable and biodegradable chemical products, thus maximizing raw materials and reducing pollution in the production process. For example, green or eco-friendly inhibitors, whose manufacture implements "clean" alternatives, are proof of this. The present research is structured with the first phase of a collection of the most important data on the elaboration of a green or eco-friendly inhibitor, that is, techniques that prove its effectiveness by recognizing those organic and inorganic molecules adsorbed on the surface of a metal; to later study, analyze and understand the essential information of each article, and reach a conclusion.
2. Methodology
For this article, information was collected through specialized search engines such as Google Scholar, Researchgate, EBSCO Host, or Science Direct. A classification was then made according to the number of citations and the relevance of the information on green inhibitors. Most of the sources consulted correspond to scientific articles, business or organizational reports, management reports, and associations or government documentation.
3. Development
To establish the impact of corrosion it is necessary to document real cases whose main suspicion is the presence of this degradative phenomenon since, through these documents, it is possible to study the different causes and take advantage of such experience to minimize mistakes in future projects: whether the wear is favorable, protecting the material, or unfavorable, affecting its physical integrity. The experiences include the accident in Aloha and the explosion in Guadalajara.
The generalities of corrosion control inhibitors are discussed. In this section, the phenomena of physisorption and chemisorption, very important to understand the type of corrosion inhibitor, are taken into account. Subsequently, the types of inhibitors are defined and characterized: organic, inorganic, synthetic, and green. The latter is obtained from the plant material and is intended to replace the synthetic ones.
Two case studies related to corrosive failures are mentioned below.
3.1 Aloha Accident
April 28, 1988, Aloha Airlines Flight 243, a Boeing 737 aircraft, was traveling from Hilo bound for Honolulu, Hawaii [12,21]. At 24 000 ft altitude, the cabin ceiling in the first-class section detached. The pilot immediately took control, started the descent, and managed to land on an island, preventing a worse catastrophe [21]. After the investigation, it was concluded that the rivets joining the fuselage plates were corroded, leaks, and water obstruction were observed in these plates (crevice corrosion) [12,22].
3.2 Explosion in Guadalajara
On April 22, 1992, in Guadalajara, Mexico, a series of explosions collapsed 1600 buildings and injured 1500 people; a total of nine separate detonations were heard along a road of approximately 2 km adjacent to the city's sewer line, and large craters formed, sinking vehicles [14]. After the event, studies were carried out stating that a steel water pipe leaked over a zinc line carrying gasoline, and had been cathodically protected, but unfortunately had a hole immersed in a cavity (pitting corrosion), where oxidizing agents stagnated, leading to wear of the passivation layer in an eroded area, and caused the gasoline leakage, and subsequently the release of gases into the sewer system, as a spark caused the blasts [14].
The rupture of a pipe elbow in an oil refinery plant caused a large explosion in South Philadelphia, the Prestige ship sank off the coast of Galicia, Spain, spilling crude oil that caused catastrophic environmental consequences, and the greenish rust layer (patina) that forms on the Statue of Liberty are other events that stimulate corrosion prevention and control technologies in the industry [23-25].
4. Overview of inhibitors for corrosion control
Chemical inhibitors are used as the first protection option to reduce the speed of the phenomenon in oil and gas extraction and processing. According to Asrar et al. [1], they have a superior capacity to form protective layers in the presence of hydrocarbons, so laboratory tests that establish optimal conditions, fluid tolerance, stability, effectiveness, and layer persistence are relevant. Likewise, it is to highlight that they work under an adsorption principle, characterized as a surface phenomenon where liquid and gas molecules, in a low state of aggregation (adsorbate), adhere to the surface layer of the solid, in a higher state of aggregation (adsorbent) [26,27]. The adsorption process depends on the aggregation state of adsorbate and adsorbent, either gas-solid, liquid-solid, or gas-liquid, respectively [27]. The most important functions of this chemical additive are to form a barrier against air or moisture, to neutralize alkalinity or acidity, and to physically and chemically coat the metal surface [28].
According to Gómez [29], the method of action consists of creating a metal-inhibitor-solution interface, after adsorption of the ions or molecules of the inhibitors on the metal surface. A protective barrier, capable of delaying the process, is built up against the corrosive medium. At the metal-electrolyte interface, an electrical double layer is formed, which generates a potential difference depending on the nature and composition of the two phases, i.e. when one phase acquires a positive charge and the other a negative one [30]. This process may occur by physisorption or chemisorption, so that Table 1 highlights its main characteristics [31-33]:
Table 1 Differences between chemical adsorption and physical adsorption.
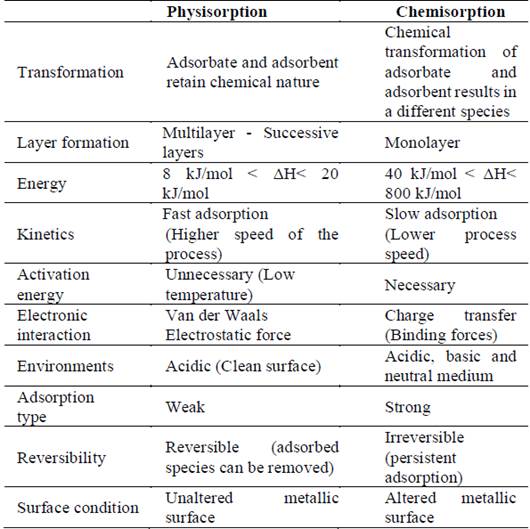
Source: Elaborated by the authors.
The mechanism of action, chemical composition, and form of application are different ways of classifying this type of alternative that controls corrosion; within the mechanism of action are anodic inhibitors, whose purpose is to modify the electrochemical potential of the metal allowing it to behave as a more noble one (corrosion resistant) due to the formation of a passivation layer (in the Pourbaix diagram) in the anodic areas of the cell where the corrosive agent is going to accumulate after generating an increase in surface potential, and thus blocking the active sites, however, application concentrations should be considered to be high enough for the good performance of such inhibitors so that the passive protective layer does not develop temporarily, which implies that after a certain amount of time the material would be exposed to localized corrosion phenomena; the most commonly used passivating agents are sodium hydroxide, sodium borate, carbonates, silicates, nitrates, nitrites, chromates, phosphates and molybdates [34-36].
In the classification there are also cathode inhibitors, which prevent the reduction reaction from being performed spontaneously so that it does not allow the release of hydrogen or oxygen, after generating variations in cathode potential, either by increasing the impedance of the metal by precipitating in cathodic areas (usually composed of magnesium carbonate and calcium), by sequestering oxygen which in turn also reduce the presence of aerobic microorganisms (mainly sulfur dioxide, sodium sulphite and ammonium bismuth) or behaving as cathode poison (such as magnesium ions, zinc and calcium), the biggest advantage is that, unlike a anodics, they do not depend on concentration which makes them safer [34-37]. Finally, there are mixed inhibitors, which act on both sides of the semi-reactions (anodic and cathodic) decreasing the reaction rate in both parts of the electrochemical cell by delaying the hydrogen reduction of the cathode and oxidation in the anode, where there is interaction between the surface of the active metal and the inhibitor, which mostly contains organic compounds such as amines or organic sulfides, and which by means of physisorption, i.e. electrostatic forces or Van der Waals, achieve the formation of the film, these are widely used in the oil industry [37-39].
On the other hand, within the classification of chemical composition, there are organic and inorganic inhibitors, the former adsorbed on the surface layer of the metal, and within their composition, there are amines, amides, benzoates, organic phosphates, among others; on the other hand, inside the inorganic inhibitors, there are crystalline salts, where the anions are responsible for reducing the corrosion of the metal [34].
In order to ensure that the chemical additive meets the standards required for its use, the appropriate physicochemical characteristics are mainly analyzed through foam, demulsifying and compatibility tests [37]. One factor to consider for the formulation of the delay catalyst is whether the efficiency of this alternative for corrosion control is relevant or not, which is obtained through the ratio of corrosion rate to and without inhibitor [36]. At the same time, the evaluation of this parameter is important for the selection of the inhibitor, so techniques are performed that estimate its behavior in corrosive environments, such as gravimetric methods (measurement of gain or weight loss), electrochemical tests, among which are, electrochemical impedance spectroscopy (EIS), infrared spectroscopy (FTIR), potentiodynamic polarization (Tafel), resistance to polarization, electronic scanning micrograph (MEB), in addition, are the volumetric methods (measurement of detached hydrogen or oxygen consumed in cathode processes), analytical methods (measured the concentration of metal components in the solution), the chemical study of electrochemical dissolution and the surface of the metal part [35,40,41].
4.1 Inorganic and organic inhibitors and current requirements
Inorganic and some organic inhibitors are mostly chemical substances that, although added in very low concentrations on the surface of metals, are highly polluting, toxic, and capable of altering the integrity of living beings and even the environment. For this reason, environmental legislation such as the Toxic Substances Control Act of the Environmental Protection Agency (EPA) of the United States and the European Union's Restriction of Hazardous Substances are currently being evaluated, proposing inhibitors capable of retarding corrosion and free of heavy metals or other toxic elements, with minimal hazards generated in comparison with others. The objective is the production of green or eco-friendly corrosion inhibitors based on extracts of seeds, leaves, shells, fruits or roots, abundant in nature and, in essence, made up of chemical compounds that, according to existing studies, inhibit efficiently; they are not very toxic and are also biodegradable [42,43]. Consequently, in recent decades they have replaced traditional inhibitors because they decompose into natural chemical elements by the action of biological agents and reduce the emission of pollutants by using waste from agroindustrial processes. Since these chemical additives are obtained with antioxidant properties from plant matter, it has not been exposed to the use of synthetic chemical products, such as fertilizers and pesticides that can be harmful to health [44,45], which promotes preservation and awareness of the environment.
4.2 Synthetic inhibitors
Synthetic inhibitors are known for containing compounds such as phosphates, vanadates, chromates, dichromates, and arsenates, which, although they are effective in controlling metal corrosion due to their inhibition properties, affect the environment and are costly to produce [31].
4.3 Green inhibitors
Green inhibitors have been studied to replace synthetic inhibitors, because they are substances that decrease corrosion by having secondary metabolites such as phenolic compounds, alkaloids, flavonoids, steroids, tannins, vitamins, amino acids, volatile oils, among other organic compounds that contain in their chemical structure long carbon chains with a polar end, consisting of heteroatoms of oxygen, sulfur, nitrogen, phosphorus, OH radicals or multiple bonds with unpaired π free electron pairs. They can provide these molecules with negative charges and increase the electron density, favoring the adsorption of the inhibitor on the metal surface and the transfer of electrons from the inhibitor to the metal. They also allow a higher efficiency of the inhibitor by forming a protective layer that delays the corrosive phenomenon [33,42,46-48].
However, it is important to emphasize that from the collection of the plant material to the elaboration of the green inhibitor, different factors must be considered, such as the mechanism of the corrosive phenomenon, the metal to be protected, the active principle of the inhibitor, the toxicity level (it must be low), the harmful effects that alter the health of living beings and the conditions of the environment where it will be applied, such as temperature, humidity, pressure, agitation, and pH; geometry of the system, nature of the metallic surface, type of metal, the type of product (oil- or water-based), its components, concentration, thermic stability and solubility in the system, also of storage methods (packaging or shipment), application mechanisms (immersion, spraying, or brushing), desired thickness, removal methods, and interactions with subsequent processes (if it is decided not to be removed), and finally, the protection time, i.e., if during the process the inhibitor has been chemically altered, are also reviewed [29,32,49]. A chemical inhibitor can be affected in its effectiveness by the interaction with the surface, composition, chemical structure, and temperature; as the latter increases, a decomposition process in the chemical additive is accelerated or the thickness of the inhibitor on the surface can be decreased, causing an increase in the corrosion rate of the metal [49,50].
4.4 Research on the use of green corrosion inhibitors
To demonstrate how green inhibitors are employed in today's industry, studies looking into the effect of plant extracts on metal surfaces in different environments have been selected to determine the efficiency of the inhibitor in slowing down the corrosion rate.
Abiola and James [51] evaluated the inhibitory activity of aloe vera on zinc in hydrochloric acid (2M HCl) solution through weight loss. Reviewing the corrosion rate, it was established that the inhibitory molecules of the extract follow the Langmuir isotherm, and the inhibitory property was directly proportional to the concentration of the extract; finally, the efficiency was 67 % at 10 % v/v HCl concentration.
Obi-Egbedi, Obot and Umoren [52] oriented their studies towards the elaboration of an inhibitor based on plum mango extract (Spondias mombin L.), capable of reducing the corrosive phenomenon on aluminum subjected to sulfuric acid (H2SO4 0.5 M), and whose effectiveness was evaluated using the standard gravimetric technique in a temperature range of 30 to 60 °C. It was obtained that the inhibitory action is more efficient as the concentration of the S. mombin L. extract increases and the degree of temperature decreases; likewise, it augments synergistically with the addition of potassium iodide (KI). According to these characteristics, this inhibitor can be widely used in the anodized coating of metal parts and other industrial surfaces.
The extract of Indian bamboo (Bambusa arundinacea) was studied as a green inhibitor against the corrosion of mild steel in the presence of hydrochloric acid (1M HCl), through the weight loss technique, in which the adsorption of the inhibitor molecules located on the metal surface followed the Langmuir adsorption isotherm and this, in 72 hours at 25 °C, with a maximum efficiency of 72.84 % at 10 % v/v. Therefore, since it does not present an efficiency value of 80 %, it is not recommended [53].
Another inhibition option was studied by Loto [54], who proposed to elaborate an extract based on tea (Camellia sinensis) to interrupt the corrosive activity caused by sulfuric acid (H2SO4 0.2 and 0.5 M) in mild steel; this through techniques such as weight loss/corrosion rate and potential measurement at room temperature. Once the tests were concluded, inhibition efficiency values of 94 and 79 % were deduced in sulfuric acid at 0.5 M and 0.2 M, respectively. The concentration of the extract was equal to 100 %, thus considered an effective inhibition.
The corrosion inhibition of apricot juice extract was studied on mild steel subjected to a phosphoric acid environment (H3PO4 at 1M), using weight loss techniques, adsorption, and activation parameters. In the adsorption test, it was shown that the inhibitor conformed to the Langmuir isotherm, forming a monolayer on the metal surface. In turn, the variance analysis indicated that the corrosion rate depended on temperature and inhibitor concentration. Apricot juice yielded an efficiency percentage of 75 at 30 °C; therefore, it is recommended for corrosion inhibition of mild steel [55].
The research developed by Prabhu and Rao [56] studied the inhibition activity of coriander extract (Coriandrum sativum L.) in a solution of phosphoric acid (H3PO4 at 1M) for corrosion protection of aluminum using potentiodynamic polarization (Tafel extrapolation) and electrochemical impedance spectroscopy (EIS) techniques. The adsorption degree of the inhibitor extracted from C. sativum L. behaved according to the Langmuir adsorption isotherm. It was found that the efficiency of the inhibitor is directly proportional to its concentration and inversely proportional to the temperature of the medium, thus acting as a mixed inhibitor in cathodic and anodic reactions.
A case was studied in which the extract to be evaluated was compared with a common green inhibitor such as tobacco, so the Persea americana extract was tested as a potential inhibitor on carbon steel and aluminum metal surfaces in an environment of hydrochloric acid (HCl at 0.5 M and 1 M). In this case were performed the weight loss test, which helps to evaluate the corrosion rate; the polarization test, which establishes the corrosion reaction in the presence of avocado pulp extract, and the phytochemical test, where the composition of avocado and tobacco as inhibitors was determined. Finally, the efficiency percentage for carbon steel was 98.06 % and for aluminum 17.08 %, making it a highly recommendable inhibitor for carbon steel [57].
In Franco's research [58], a sustainable alternative for corrosion in carbon steel with AISI 1045 standard subjected to a hydrochloric acid solution (HCl 0.5M) was proposed. It was based on the elaboration of a green inhibitor based on different extracts from the leaves of the noni tree plant (Morinda citrifolia), but using acetone, ethanol, water, and hexane as solvents. Then, it was sought to determine which of the extracts provides a more active adsorption mechanism, that is, a more effective inhibitory action, through electrochemical impedance spectroscopy EIS, Tafel approximation, and RP polarization resistance. As a conclusion of the exploration, it was discouraged to use noni extracts with hexane and acetone in the industry, since they have high individual corrosive effects and low polarity, which hinders the total dissolution of organic compounds belonging to the MC leaf in these chemical substances. In parallel, handling water and ethanol, the corrosion rate decreases markedly as the extract concentration increases; however, the efficiency was close to 66 % and the inhibitory action was appreciable for four hours.
Hexanic and methanolic extracts of turmeric powder (Curcuma longa) were tested for corrosion inhibition on 1018 steel exposed to a saline environment (NaCl 3 % wt.). Through the electrochemical impedance spectroscopy (EIS) technique, tests of C. longa extracts were developed at different concentrations 0, 10, 20, 20, 50, 100 ppm, and different immersion times; so that the methanolic extract had an inhibition efficiency of 93.68 % at 20 ppm, compared to the hexane extract, whose maximum inhibition efficiency was 72.04 % at 100 ppm. Therefore, by presenting an efficiency higher than 80 %, the use of the methanolic extract of C. longa as a potential inhibitor in 1018 steel in saline solution is recommended [59].
The inhibition action of watermelon (Citrullus lanatus) peel extract as corrosion protection of A36 structural steel in acidic (HCl 0.5 M) and saline (NaCl 3, 5 %) media was studied by electrochemical and weight loss (Tafel extrapolation) methods. The results of the process evaluated for 24 days showed that the efficiency of the inhibitor in a saline medium is 94 % and, in an acid, medium 77 %. Thus, exceeding an efficiency of 85 %, the C. lanatus inhibitor in a saline medium is recommended for the protection of A36 structural steel, since it creates a passive layer that separates the metal surface from the environment [60].
In most cases, the inhibition efficiency is at 80 % (some exceed this percentage), which reaffirms the potential of plant extracts and their organic derivatives as primary products for the elaboration of green inhibitors, in favor of counteracting the massive deterioration of metals in the industry, in an eco-friendly and cost-effective way. The use of natural extracts as inhibitors and the techniques to evaluate the corrosive phenomenon reveal a wide field of technology and research still unexplored, which motivates to continue searching for new methods and resources to eliminate corrosion.
5. Conclusions
Corrosion is an undesirable phenomenon for all companies that treat metallic materials since it prevents them from fulfilling their function, altering their intrinsic properties, and generating breaks in their surface. Even if progress continues to be made in this respect, the useful life of the materials will only be definitively prolonged. Therefore, although corrosion is a spontaneous event, it is inevitable that sooner or later such materials will be replaced.
The industry is aware of the impact that corrosion has on both the economy and the production of the organization. For this reason, and to help reduce the negative effect of this phenomenon, it is necessary to integrate control methods through green inhibitors that work mostly exposed to any environment recognized as harmful to the metal to be protected.
Cases that demonstrate the negligence of companies and the engineering branch, since they have implemented late and wrong controls, monitoring, and protection methods, ended with accidents and losses in industrial processes of great importance.
Physical methods should be implemented which, although not as accurate, allow direct measurement of corrosion, easier analysis of the results and corroboration of the conclusions obtained by electrochemical methods, such as gravimetric (measurement of weight gain or loss), analytical (measurement of the concentration of metallic components in solution) and volumetric (measurement of hydrogen released or oxygen consumed in cathodic processes) methods.
Although stationary and non-stationary electrochemical techniques are used (electrochemical impedance spectroscopy EIS, polarization resistance RP and Tafel approximation) based on polarization resistance methods, polarization curves, critical potentials, potential-time curves, impedance techniques, and potentiodynamic methods -effective for their sensitivity and safety in the measurement of potentials and current densities, for the rapid information on corrosion progress and because a single sample provides comprehensive data on the evolution of the phenomenon-, disadvantages must also be considered, such as disturbances of the system under study due to the polarization applied, indirect estimation of corrosion, poor knowledge of the mechanism interpreting the results and low reliability when used incorrectly.
In short, green inhibitors have excellent compositional characteristics because, being purely natural, they do not have secondary or negative effects on the environment compared to synthetic inhibitors, which are mostly made up of chemicals.
Although care for the environment and its preservation lead to the research of plant resources as green inhibitors to mitigate the effects caused by corrosion in metals, it should be ensured that these plant extracts do not come from essential food sources for living beings, but from organic wastes that, even today, some industries consider dispensable within their manufacturing activity. They are useful in different sectors and affordable.