1. Introduction
Today, for the exploitation of hydrocarbons a large amount of fossil fuels is needed, where these are scarce every day, so we want to find a method by which we can supply them. Currently, the possibilities of using clean energy are being generated, where great interest is being shown because, in recent years, they have been generating successful results. Through this article, it is intended to implement concentrated solar energy (CSP) to supply the recovery method by vapor injection to a Colombian field, where it will be developed in three parts.
Initially, based on a previously published article "Selection of Fields for the Implementation of Solar EOR as an Improved Thermal Recovery Process in Colombia", the most suitable Colombian fields for said implementation were determined according to various parameters, mainly as their location; which are Teca-Cocorna, Nare, Jazmín, Moriche, Girasol, Chichimene and Quifa, where analysis of oil production was carried out between the years 2015 to 2019, it was observed that the TECA field maintains a stable oil production; Besides that, it should be noted that it is one of the oldest fields and has been implementing cyclical steam injection for several years; therefore, the TECA field was chosen to implement Concentrating Solar Power (CSP). [1]
After this, the System Advisor Model (SAM) program was chosen, which is a software that has a wide range of solar energy technologies for the generation of electricity, the energy of Concentrating Solar Power in Parabolic Through - Physical was chosen. , because this is one of the most used energies at the moment, for this simulation a capital cost of $ 5000, a space of 800 meters since generally in the fields there is not an extensive space, for modules such as SCA collectors, Siemens Sunfield 6 was used because of its availability in the market and because it is a universal brand, and also in HCE receivers always UVA 2010; Since it was sought that the two modules were of the same brand, in such case of presenting a guarantee or any inconvenience only one supplier is taken into account; Finally, was calculated the total electricity production of a system in kilowatt-hours, from hourly meteorological data for a specific place, and the physical specifications of the power components of the system, obtaining as a result of a Levelized Cost of Energy (LCOE) from $ 0.40 / kWh.
Finally, an analytical model was performed in to predict the behavior of the reservoir, the TECA field currently implements a cyclical injection of steam. In this case, the Boberg & Lantz model was used, since it is one of the most used models, for the realization the necessary data to carry it out was collected, a two-cycle analysis was decided to see the rate of oil production in a two-year projection.
2. Methods
2.1 Simulation in SAM
Through the System Advisor Model (SAM) software, the Levelized cost of energy (LCOE) was calculated, using the data in Table 1, where the energy Solar Concentrating Solar in Parabolic Through - Physical is used.
The simulation in the SAM software consisted initially in the configuration of the location and resource. Latitude, longitude, and elevation were entered into the simulator. Due to the location of the study field, the sector of Puerto Nare, Nariño, was selected.
Then, the system design was proposed. It consisted of the simulation of the installation of two parabolic troughs. 2 heat exchangers and 2 thermal energy storage tanks, occupying about 800,000 m2. The temperature was maintained between 293°C (loop inlet) and 391 (loop outlet). The system is shown in Fig. 1.
Among the most important design parameters is total tracking power of 1000W, a collector spacing of 15m, and a current field thermal power output of 3.45861 MW/t. The collector orientation was maintained with a stow angle of 170 deg and a deploy angle of 10 deg.
Regarding efficiency settings. A ratio of 8 single loop configuration (SCA) per receivers (HCE) was maintained. As can be seen in Fig. 2.
For the project, a solar collector of the reference Siemens Sunfield 6 was evaluated, which has a reflective aperture area of 545 m2, a total structure of 6m, length of collector assembly 115m, an average surface-to-focus path length of 2.15m, and a dimensionless mirror reflectance of 0.93.
The selected receiver was the Siemens UVAC 2010. The same supplier as the collectors was retained to facilitate the purchase of spare parts and maintenance throughout the life of the project. The receiver consists of parameters such as an absorber tube inner diameter of 0.115, a glass envelope inner diameter of 0.12, an absorber flow pattern in tube flow, and an absorber material type 304L.
Concerning to power cycle of the system, an estimated gross net conversion factor of 0.9, a cycle thermal efficiency of 0.356, a cycle thermal power of 311.798HWT, HTF hot temperature of 391°C, and HTF cold temperature of 293°C were calculated.
The system connection works with a built-in Rankine cycle with parameters such as a boiler operating pressure of 100 Bar, an ambient temperature at the design of 42°C, a condenser pressure ratio of 1.0028, and a cooling system part-load level of 8 units. Fig. 3 shows the curve of condenser pressure vs ambient temperature of the power cycle of the system.
Furthermore, the thermal storage is composed of a tank height of 12 m; with operational conditions of cold tank heater capacity by 25 MWE, cold tank heater temperature ser point at 350°C, and hot tank heater temperature set point 365°C.
Moreover, the weekday schedule (Fig. 4) and the weekend schedule (Fig. 5) were programmed. Each of the numbers and colors corresponds to the turbine output fraction.
Finally, the financial and operational parameters were configured. A system capacity of 99,900 kW, a capital cost of 5000 USD/kW, and a fixed operating cost (annual) of 66 US/kW were sized. For the calculation of the LCOE (Levelized Cost of energy), 25-year financing was assumed with a rate of 2.5% per year and a nominal internal rate of return of 13% per year.
2.2. Cyclical vapor injection
The application of cyclical vapor injection is in the group of thermal oil extraction processes. These processes are subdivided into those that involve the injection of hot fluid into the reservoir (hot water injection, continuous steam injection, and cyclical steam injection) and others that generate heat directly in the reservoir (in situ combustion) [2]. In addition to being a fluid injection process, the cyclic steam injection process is also known as a reservoir treatment through thermal stimulation, which consists of heating only the reservoir area that is close to the producing wells, reducing the resistance to the flow of oil by means of heat transfer between the vapor injected and the rock together with the fluids present in the reservoir. [3]. The cyclical steam injection process has been related to hydraulic fracturing, only that instead of increasing the flow capacity of the reservoir, its focus is directed to reducing oil viscosity. [4].
For vapor injection, it must be taken into account that not all the heat that is injected will be the same that reaches the tank; This is due to the heat losses that occur during the process, which are classified into surface heat losses, heat losses in the formation and heat losses in the well. In the following Fig. 6, these losses can be seen; It is very important to take these losses into account, otherwise, the heat transfer efficiency will not be adequate and there may be a waste of the well to produce since it does not have a good displacement.
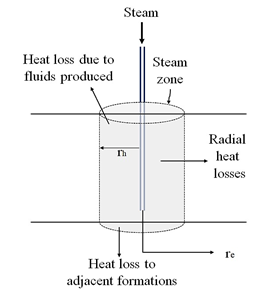
Source: The authors
Figure 6 Vapor Zone and Heat Losses are assumed in the model of Boberg and Lantz.
The Boberg & Lantz model is one of the models used for cyclical steam injection, it was decided to do it for this model due to its assumptions, which are:
Start using the Marx & Langenheim model (to estimate the radius of the hot zone.
It considers the distribution of temperatures in the reservoir in time after the injection of vapor, which is represented as a step function, that is, it considers a gradual drop in temperature.
The sand is invaded uniformly and radially by the injection of vapor.
If several producing grains of sands are stimulated in a well, the sands will be invaded by vapor at the same radial distance, that is, the advanced front of vapor in the two grains of sands moves the same distance.
The pressure drop in the reservoir is negligible.
A gas-oil interface is assumed, with no transition zone between these two.
It assumes that before stimulation, the reservoir must have sufficient energy.
To produce oil at the initial reservoir temperature, using some of the primary energy supports, simply put, the reservoir had to initially produce cold. [6]
A flow diagram was proposed to perform the cyclical steam injection as can be seen in Fig. 7 and with their respective equations in Table 3. In the Table 2 was exposed the convention of the flow chart in the Fig. 7.
The data collection of the characteristics of the TECA Field was carried out as can be seen in Table 3, since these were necessary to carry out the analytical model of cyclic steam injection.
Having the aforementioned, we proceed to the realization of the analytical model. The procedure for the vapor cycle was initially carried out with the estimation of the initial steam temperature taking into account an average as shown in Eq. (1), then the heat is removed from the formation by the oil and gas produced with Eq. (2) was calculated taking into account the previously calculated initial vapor temperature, then with Eq. (3) the vapor pressure was calculated, the enthalpies of the water were calculated taking into account the reservoir temperature and the estimated vapor temperature, with Eq. (4) and (5) respectively; then with Eq. (6) the latent heat of vaporization was calculated. Taking the results of the enthalpies of the water previously, the sensible and latent heat removed from the formation by the water and the vapor produced with the Eq. (7).
With the latent heat of vaporization previously calculated, the heat injection rate is calculated for each time until the established projection, where it is calculated with Eq. (8). Then we proceed to the calculation to the dimensionless time, the dimensionless factor, the vapor area, and the radius heated by vapor injection, where the Eqs. (9), (10), (11), and (12) respectively. To calculate the rate of hot and cold oil, Eqs. (16) and (17) are used respectively. First, the constants a and b will be calculated through Eq. (13) where, having two viscosity values and two different temperatures, we can obtain the results by means of a system of equations. Second to determine the cold and hot viscosity using Eq. (15) and (14) respectively the constants calculated above will be used, finally, having these values, the rate of production of hot and cold oil is obtained.
Finally, to calculate the vapor temperature of Eq. (25), initially, the Energy removed by produced fluids will be needed, which is calculated with Eq. (24), but for this, it is necessary to have the Increased thickness of formation that is calculated with Eq. (18) and the rate of heat removed by produced fluids which is calculated with Eq. (23). Then the variables x and y are calculated with the Eq. (19) and (20), respectively; these variables are used to calculate the terms are the unit solution of the heat equation in the radial direction and the vertical direction with the Eq. (21) and (22). This procedure must be carried out as many times as necessary until the difference between the calculated temperature and the previous estimate is equal to zero. When this is achieved, it is because the principle of the model has already been fulfilled.
The calculations for the cycles following the first are carried out similarly, with the difference that the residual heat in the reservoir during the preceding cycle must be taken into account. The remaining energy in the oil sand can be calculated by Eq. (26). An approximate way of taking this energy into account is by adding it to the heat injected during the following cycle, assuming that the reservoir is at the original temperature Tr. This, however, assumes that the supra and underlying layers are at the original reservoir temperature. As a consequence, the calculated heat losses will be greater than the true heat losses. [5]
For this case, a second cycle and a third were performed with the same parameters considering previously, in addition to its remaining heat.
3. Results and discussion
After performing the simulation in the SAM software, a Levelized Cost of Energy (LCOE) of 0.40Cents/kWh could be established, which means that generating 1-kilowatt hour of energy has a value of approximately 1/3 of a dollar. Ratifying an appropriate energy production cost for the project. Other results of vital importance correspond to the annual water use of 248 cubic meters a power cycle gross electrical output of 175.722 kWh-e.
As can be seen in Figs. 8 and 9, in the months of February and March there were dips in the system's energy dispatch curve. This is attributed to the rainy season that occurs in the region during these months. On the other hand, in the other months evaluated there is an increase in the load curve due to the thermal and climatic characteristics of certain days. October 7 and December 13 stand out. These irradiation peaks are used for energy storage in the system.
As for the CSP operating time-of-use value, it can be seen that in June, July, August, and September there is a decrease of 3 units concerning the other months due to the injection procedures and soaking time of the project.
On the other hand, the variation of the parameter at the end of the first 6 days of the month is due to the heat requirement necessary for the steam injection process of the field. (As seen in the Figs. 10 and 11)
Also, in Figs. 12 and. 13, the field collector cosine efficiency can be observed, where it is clearly shown that in the month of February there is a reduction in efficiency that is due to the scheduling of predictive maintenance of the system.
On the other hand, for this work, it was decided to perform 3 cycles with an injection time of 5 days all three, in a projection of three years, with the previously mentioned methodology, and the following Fig. 14 was obtained as a result.
To carry out the cycles, the remaining heat from the previous cycle was taken into account, as the Boberg & Lantz model does, assuming that the reservoir is at the original reservoir temperature; It can be seen in Fig. 14 that the general behavior of each cycle is that its production rate increases for a short time and then falls rapidly, in the first cycle it increases for five and a half months, the second cycle approximately 3 months and in the third cycle in a month and a half; if it wanted to carry out more cycles, its time would be much shorter and in the same way their production rate would be lower. Additionally, it is observed that when it already declines, it returns to its original production rate, this behavior is typical of this model since it is due to the decrease in temperature and the increase in viscosity.
4. Conclusions
According to what has been simulated in this article, it can be concluded that solar collectors are an ecological and efficient proposal for the generation of steam for later injection into an oil reservoir.
More than three cycles are not recommended since the performance of more cycles is not favorable because its production will not increase in large proportions and will only last for a short time.
The Boberg and Lantz analytical model is suitable for estimating the performance of a vapor injection cycle for single sand, although this model can be considered for multiple sands.