1. Introduction
The constant necessity to find lower specific energy consumption and larger competitiveness in the production of several value-added products in the industry requires the application of technologies for efficient use of the thermal energy as well as the optimization of the operation parameters of the production equipment. The furnace geometry influence fluid dynamic parameters and thermal phenomena such as residence and heat transfer by convection and radiation. In general, saving of thermal energy in the industrial manufacturing focuses on strategies such as optimizing the air/fuel ratio in combustion systems, waste heat recovery, improving thermal insulation and preventing infiltrations of atmospheric air in heating equipment [1-3]. Other actions are related to the increased residence time of the combustion gases in the furnace, as shown in the work of Lee and Jou [4], who obtained a reduction in the pressure within the furnace by regulating damper in the chimney. This allowed a reduction of the output speed of hot gases and more time for heat transfer within the furnace was possible. On the other hand, Nicolau and Dadam [5], showed that optimization parameters such as wall insulation and preheating combustion air and load in brick kilns can lead to fuel savings of 10%.
The greater amount of heat transferred to the load on high temperature furnaces is due to the radiation mechanism [6], reaching proportions between 75 and 90% over convection [7]. The radiation intensity depends significantly on the furnace geometry, the nature of the surfaces and the combustion gases, and the relative position of the load and heat sources [8]. Furthermore, the position of the exit of the combustion gases has a strong influence on the fluid dynamics of these [9], which affects parameters such as residence time and convective heat transfer. In general, the higher the residence time of the gases into the furnace, the greater the radiation energy to the load [10].
Few studies have examined the influence of combustion systems on thermal energy efficiency of the high temperature process where melting is involved. Wang et al. [10,11] made a numerical study of the effect of burners on the aluminum melting process using the response surface method. They found that the melting time can be decreased by increasing the swirl component of gas to the burner outlet, increasing the vertical angle of the burner and increasing the air preheating. On the other hand, Kremer et al. [12] determined by a numerical study that increasing the height of the combustion chamber in a glass melting furnace, NOx emissions were reduced due to the creation of areas of gas recirculation within the furnace which dilutes O2-rich zones.
Since melting processes requires high temperatures, it is common to use oxygen as oxidizer in the burners. Combustion with oxygen can be done in two ways: oxygen enriched air in which the oxidizer is a mixture of air and oxygen, and oxy-combustion where the oxidizer is only oxygen [13]. Enriched air combustion and oxy-combustion are used in industrial applications related to melting of materials, thermal decomposition reactions and sintering. Some of such applications include glass melting and production of cement, steel, ferrous and aluminum. In these processes, production has been increased from 15 to 65%, while combustion efficiency has increased between 10 and 30% [14].
When enriched air is used in combustion, the composition of the combustion gases changes and therefore thermal properties and kinetics of combustion change too. The heat transfer to the load changes due to increased temperature and concentration of molecules such as CO2, H2O, CO, SO2, soot and ash, which increase the emissivity of the gas and radiative heat transfer [15]. The radiation pattern is modified because soot particles formed in the high temperature zone are highly radiant and they are distributed along the fuel-rich zone, while the radiant gases are after the reaction zone. This separation of sources of radiation modifies the flame temperature and NOx emissions [16]. Furthermore, when the flue gas volume decreases, the convective heat transfer decreases and causes a non-uniform temperature distribution when enrichment levels are high [17].
The use of enriched air combustion in melting processes and other high temperature processes has been studied by several authors. Golchert et al. [18] analyzed the effect of the variation of the nitrogen concentration in the fuel, with partial substitution of air with pure oxygen on the heat transfer and NOx formation in melting furnace aluminum. They found that such emissions increase with increasing temperature and N2 concentration in the fuel. Karimi y Saidi. [19] studied numerically the implementation of enriched air combustion into a furnace steelmaking and they found optimal concentrations of O2 between 21 and 45%, with fuel savings up to 18% per ton of steel.
On the other hand, in high-temperature industrial processes such as glass and metallurgy industries, oxy-combustion is a widely used technique, where high purity oxygen is used generally 99.9% instead of air during the combustion process. The flames when using this technique are characterized by fast reaction kinetics, resulting in rapid and dense chemical energy release from the short and intense flames. This technique allows to increase productivity in furnaces [20] and in recent times, the oxy-combustion has emerged as a competitive option for capturing CO2 in various industrial processes including coal boilers and power production [21]. Concentric oxy-combustion burners, flat-flame burners, low NOx burners, burners with gas recirculation and flameless combustion burners are among the technologies offered by different manufacturers to achieve oxy-combustion.
Another alternative to increase the temperature of combustion in melting process is the implementation of regenerative or recuperative heat exchangers for preheating the air combustion from waste heat. Because of the various energy efficiency programs implemented around the world, motivated by economic guidelines and rational use of fossil fuels, many technological developments that began in the second half of the twentieth century and mainly in applications and heating processes, have been based on heat recovery for preheating combustion air as a method of improving the efficiency of combustion equipment. These kinds of measures are a key to reduce fuel consumption between 13 and 51% [22] and carbon dioxide emissions (CO2).
Even though the technology for oxy-combustion is well known, few works have been directed to analyze the effect of residence time of flue gases on the energy efficiency of high temperature processes where combustion with oxygen is used. Prieler et al. [23] modeled an industrial walking hearth furnace for reheating of steel billets where oxygen enriched combustion with 25% O2 was applied. They determined 8% of fuel saving with oxygen enriched combustion. Also, an increasing in the heating rate was reached as a consequence of the increased radiative heat transfer. However, slower heating of the billets was detected due to reduction in the convective heat flux in the preheating zone of the furnace. Previously, Prieler et al. [24] had determined by numerical simulation that small oxygen enrichment levels in high temperature processes are more effective for higher temperatures and reductions in the order of 77% in lost energy through the outlet can be achieved applying oxygen enriched combustion.
Granados et al. [25] analyzed the effect of flue gas recirculation during Oxy-Fuel Combustion in a Rotary Cement Kiln by using a CFD model applied to coal combustion process. They found that convective heat transfer coefficients are higher because the thermal conductivity of flue gases are also higher when flue gas recirculation is above 35%. Recirculation ratios lower than 35% provide lower convective energy flux than the air combustion process and that this effect is mainly caused by the low Reynolds number. On the other hand, authors found higher radiation in the oxy-fuel case with lower flue gas recirculation because the CO2 emissivity is higher than that for N2 of flue gases. These contrary effects allowed concluding that an optimum FGR that maximizes the energy transfer by convection and radiation to the load can be obtained
Possamai et al. [26] reported an experimental study on the thermal behavior of a continuous-operation sodium silicate furnace with pre-heated air as the oxidizer. They found that higher amount of energy can be absorbed by the load when oxy-combustion is used due to an increasing in the radiation heat transferred. Also, authors suggested that when oxy-combustion is used, a longer residence time of the flue gas inside the furnace could contribute to a lower loss of energy through the chimney, but they emphasized that a numerical study is required to verify these suppositions.
Only one study has considered the residence time of flue gases in a high temperature process. In that study, Wang et al. [27] used CFD simulations and a response surface method (RSM) to optimize operation conditions of an aluminum holding furnace. Among variables that they considered, combustion technology and location of the chimney were considered. They determined the minimum specific energy consumption by using pure oxygen instead air as oxidizer and locating the outlet of flue gases on the same side of the burner. They commented that this location can prolong the residence time of high temperature gases. Also, cross-correlations between chimney position, oxidant type, fuel velocity and burner load ratio are significant, while air preheated temperature had a trivial effect on energy consumption per ton of aluminum.
In several industrial processes, it has been though that thermal energy efficiency depends mainly on the efficiency of the combustion and many efforts have been made to improve the performance of the burners. However, as far as has been documented, there are not enough studies which show the simultaneous influence of the oxygen combustion system and the residence time of gases on the performance of high temperature melting process. The most of these studies have been numerical studies. In this paper, an experimental study carried out in an industrial melting frit furnace is presented. The experiments include tests of several burners based on enriched air combustion, oxy-combustion and preheated air combustion and modification of the residence time of the combustion gases within the furnace. For each configuration of the combustion system, its impact on productivity, efficiency and specific consumption of thermal energy in the process was analyzed, considering the influence of the predominant mechanisms of heat transfer in combustion system. The experimental data reported here from an industrial-scale furnace are important for the development and evaluation of further numerical models applied to estimate the physical phenomena occurring inside melting furnaces. Also, the knowledge acquired from experiments enables the application of actions to increase the process efficiency leading to fuel economy and lower levels of emissions in other high temperature process where such data are still limited or restricted.
2 Materials and methods
The main energy consumption in the frits production process is the inorganic oxides melting. The combustion processes in the melting furnace is carried out generally with oxygen as oxidizer and it’s possible to obtain temperatures between 1400 and 1600 °C. The residence time of the material inside the furnace is defined by the melting rate of the raw materials and the melt material fluidity. Finally, the molten material exits the furnace for receiving a water quench at room temperature, producing a thermal shock which forms the vitreous material called frit.
Experimental tests were performed in an industrial continuous frit furnace with capacity to process 10 to 11 ton/day of raw material. The furnace worked with natural gas, whose composition is shown in Table 1. The furnace was built in refractory brick walls 30 cm thick and an emissivity of 0.93. The furnace roof has geometry in the shape of an arc in order to direct the radiation over the center of the load on the furnace bottom.
Table 1 Composition of natural gas used in the furnace for frits production. Source: the authors
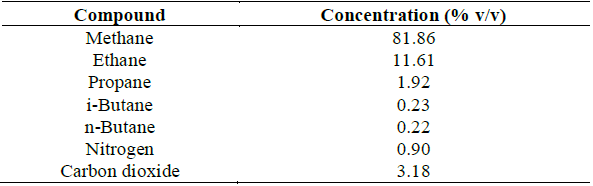
Source: the authors
Six combustion system configurations were tested in which the number and position of the enriched air combustion, oxy-combustion and preheated air combustion burners were varied, as well as the position of flue gas duct. Each setting conditions were as follows:
Configuration 1 (Fig. 1a): combustion of natural gas with enriched air was used. Air with 48% oxygen was used and none preheating was done. Four cylindrical non-premix co-flow burners were used. This configuration corresponds to the base line of furnace operation.
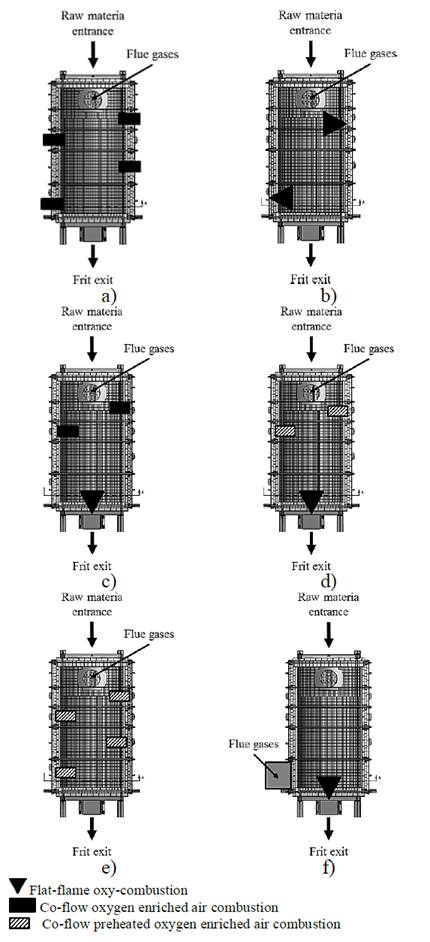
Source: the authors.
Figure 1 Scheme of the distribution of the combustión systems in the kiln a) Configuration 1. b) Configuration 2. c) Configuration 3. d) Configuration 4. e) Configuration 5. f) Configuration 6
Configuration 2 (Fig. 1b): oxygen and natural gas combustion was used in two flat flame burners with oxygen and fuel mixing downstream of the fuel injection nozzle. Each of these burners had a power of approximately 1683 kW.
Configuration 3 (Fig. 1c): oxygen and natural gas combustion was used in a flat-flame burner and enriched air combustion was used in two cylindrical non-premix co-flow burners. In the enriched air combustion burners, air with 48% oxygen was used and none preheating was done.
Configuration 4 (Fig. 1d): This configuration had the same burner types and distribution of configuration 3, but the enriched air was preheated about 350 °C.
Configuration 5 (Fig. 1e): enriched air and natural gas combustion was used in four cylindrical non-premix co-flow burners. In the enriched air combustion burners, an air stream with 48% oxygen was used and it was preheated about 350 °C.
Configuration 6 (Fig. 1f): oxygen and natural gas combustion was used in a flat-flame type burner with oxygen and fuel mixing downstream of the fuel injection nozzle. The burner was located on the opposite side to the input of the load. In this configuration, the evacuation of flue gases was at the left side of the burner, in order to increase the residence time of the gases into the furnace. Fig. 2 shows a scheme of the furnace before and after of the relocation of the flue gases duct.
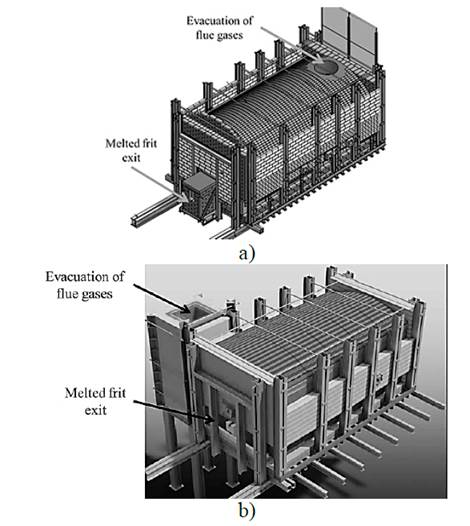
Source: the authors
Figure 2 Schematic view of the frit melting furnace. a) evacuation of flue gases on the opposite side to the melted frit exit b) evacuation of flue gases on the left-side to the melted frit exit.
For both oxygen enriched air combustion and oxy-combustion, oxygen with 99.99% purity was used. For oxygen enriched air combustion, air was supplied by a fan and it was mixed with oxygen upstream of the burner up to a concentration of 48% oxygen. For each of the configurations of combustion, performance indicators such as energy intensity (the amount of energy consumed per unit mass of frit produced) and furnace productivity (amount of frit produced per unit time) were determined. Calculation of these indicators was made from the measurement of the amount of frit produced, the consumption of natural gas and oxygen consumption. Quantity of frit produced was measured using load cells with capacity of 2000 ± 0.5 kg. Measurement of natural gas and oxygen flow was made using differential pressure cells (Bailey) with flow measurement capability up to 108 m3/h. Each configuration was tested for a week continuously.
The entire tests, the data of fuel, oxygen and raw material were taken every time a frit container was filled, which lasts about 1 hour and a half to 2 hours depending on productivity of the particular configuration. The external temperature of the furnace walls was measured with a thermography camera (Fluke). NOx emissions were determined according with the procedure specified by US EPA 7. NOx concentration was reported on a base of 11% in O2, as required by Colombian normative.
For completing the energy balance, the flow of flue gases was calculated as the summation of fuel and oxidants flows, while temperature of flue gases was measured by a K-type thermocouple. Concentration of combustion products such as CO2, CO and O2 were measured by electrochemical cells with a gas analyzer (Bacharach PCA3). Water vapor in flue gases was calculated from the stoichiometric balance according with composition and flow of fuel and oxidants. Finally, concentration of N2 was determined by balancing of the flow of flue gases.
The heat for processing raw material and production of frit was divided into two contributions: sensible heat for raising temperature of reactants from room temperature up to meting temperature around 1500 °C, and melting of the reactants. For sensible heat calculation, specific heat of raw material of 900 J/kg.K was used and latent heat for melting was assumed in 400 kJ/kg [9]. The same value of specific heat was used in order to calculate the sensible heat of the frit leaving the furnace.
Heat lost through walls was calculated by processing of thermography images using a code in MATLAB as shown in Fig. 3. Every image was split in 22 intervals of areas with a representative average temperature and heat lost by convection and radiation was calculated according with the Eqs. (1) and (2):
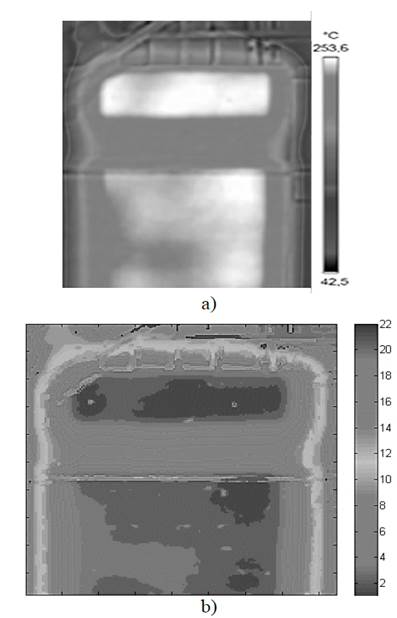
Figure 3 Processing of a thermography image for calculating the areas of the wall at representative average temperatures. a) Unprocessed image b) processed image using a Matlab code (temperature interval 1 has the larger temperature and interval 22 has the lower one).
where Q ̇conv and Q ̇rad are the heat lost by convection and radiation, respectively, h is the convection heat transfer coefficient, A is the area determined by a MATLAB code, Tw and T∞ are the representative temperature of every area and the room temperature, respectively, ε is the emissivity of the walls and σ is the Stefan - Boltzmann constant (5.68×10-8 W⁄m2.K4).
3 Results
The specific consumption of thermal energy is fundamental to compare different combustion technologies and design of heating equipment parameters. Low specific energy consumption implies an improvement in the productivity of industrial processes and a reduction in CO2 emissions. In Fig. 4 the values of specific consumption of thermal energy are shown for each of the combustion system configuration.
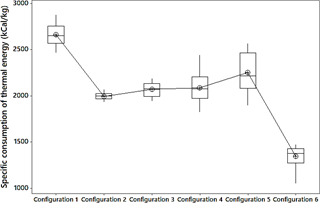
Source: The authors.
Figure 4 Thermal energy specific consumption with different configurations of the combustion system.
The results showed an improvement with regard to the base line in the configuration 1 when configuration 2 to 6 were applied. On the other hand, no significant difference on specific consumption of thermal energy was found among configurations 2 to 5, when the position and the burner technology in the production furnace frit were changed, while the evacuation of the combustion gases in the entrance side of the raw material was retained. In general, the specific consumption with the configurations using oxy-combustion (configuration 2, 3 and 4) had lower values than those using enriched air combustion (configuration 1 and 5). This is because oxy-combustion can increase flame temperatures above 10%, which enhances the radiation to the load. Furthermore, when oxy-combustion is used, the concentration of chemical species that contributes to the emission of heat by radiation such as CO2 increases. Also, it worth to note that configurations 1 and 5 have the same kind of burner and the same position, but configuration 5 works with preheated enriched air and a significant reduction in specific consumption was reached in this case. This result is because of the recovering of waste heat to preheat the oxidant in the burner.
In Figs. 4 and 5 can also be noted that configurations 2 to 4 showed a trend to reach lower specific consumption and higher productivity values than configurations 1 and 5. This slight variation is probably due to the type of flame generated in each configuration. Configurations 2 to 4 incorporated at least one flat-flame burner, which is characterized by supplying the reactants with low momentum and generate a flame with a high aspect ratio. These characteristics maximize the radiation incident on the load because the flame has a larger coverage area. This property helps to compensate for the shorter length of the oxy-combustion flame compared with the flame longer that is generated in enriched air co-flow burners.
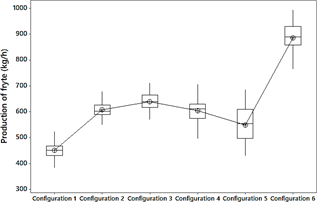
Source: The authors.
Figure 5 Production of frit with different configurations of the combustion system.
Unlike configurations 1 to 5, configuration 6 showed a decrease in specific consumption which results in a statistically significant difference with respect to other configurations, as concluded by the ANOVA and Games-Howell analysis performed. Considering that configuration 6 changed the position of the flue gases outlet, this result indicates that in the frit melting furnace, the residence time of the combustion products is more prevalent on the heat transfer to the load that the burner arrangement and the oxygen combustion technology (oxy-combustion or enriched air combustion). From the comparison of configurations 2 and 6, where oxy-combustion was used, it can be seen that even with two burners, configuration 2 had higher values of specific consumption than configuration 6, which has only one burner but more residence time of gases into the furnace.
The best performance of configuration 6 is likely associated with increased heating of the furnace walls, especially the crown-shape wall on the roof. This increased heating is due to increased contact of the combustion gases with the walls. These warmer walls increase heat transfer by radiation, which is the mechanism that accounts for about 90% of heat transfer to the frit [9]. This causes increase in efficiency fusion process. Moreover, in oxy-combustion systems, the removal of nitrogen increases the concentration of CO2 and H2O in the combustion products, which are participating species in radiative heat transfer. Therefore, it is expected that increased residence time of these species into the furnace, increase the radiation incident on the load. On the other hand, as a gas with higher specific heat at constant pressure than air, a higher concentration of CO2 in the flue gas increases its thermal inertia and this affects the heat transfer inside the furnace [26].
In this study, the minimum specific consumption was around 1346 ± 108 kcal/kg frit with a production of 887 ± 60 kg/h, which corresponds to the average specific consumption and production for configuration 6. In comparison, Possamai et al. [9] reported an experimental study of a furnace frit with two burners of natural gas and pure oxygen. One burner was directed to the input of the raw material and the other towards the exit of the product in order to maintain fluidity. The energy characterization furnace in that study showed a productivity of frit around 864 kg/s with a specific consumption of 4.375 MJ / kg (1044 kcal / kg). For the present study, the higher specific consumption is because heat loss was detected in the furnace walls, which reached temperatures up to 235 ° C, as shown in thermography images of Fig. 6. On the other hand, configuration 6 represents a significant improvement over the base of the furnace operation corresponding to the configuration 1, which had a specific consumption around 2664 ± 118 kcal/kg frit. This reduction represents a decrease of 0.302 kg of CO2 per kg of frit produced.
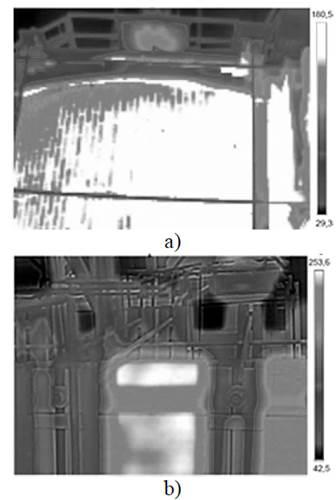
Source: the authors.
Figure 6 Thermography images of the furnace walls (Temperature in °C). a) Roof b) Side wall.
Fig. 7 shows the Sankey diagrams which represent the energy balance in each configuration of the combustion system. Highest efficiency of 39.98% was obtained with the configuration 6 which was at time the configuration with the lowest specific consumption of thermal energy.
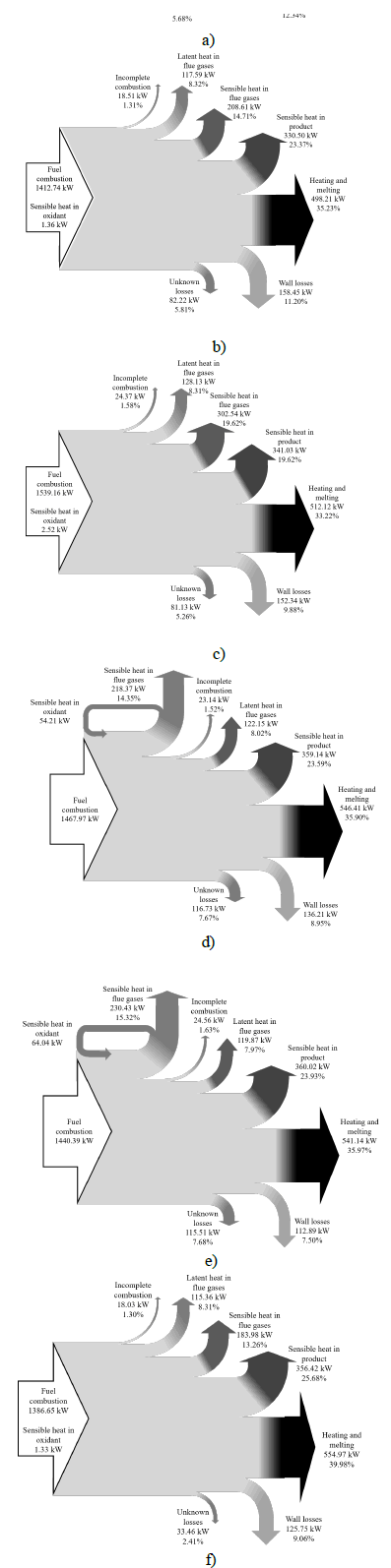
Source: the authors.
Figure 7 Sankey diagrams for energy balance in each configuration. a) Configuration 1 b) Configuration 2 c) Configuration 3 d) Configuration 4 e) Configuration 5 f) Configuration 6
This configuration had the lowest loss of sensible heat because of the reduction of flow of flue gases due to the lowest oxidant flow in oxycombustion. However, the highest productivity of frit in this configuration increases the quantity of heat which is lost through the hot and molten frit leaving the furnace. This heat is given to the water used for sudden cooling of the frit and it is not recovered. It is worth to note that the efficiency in configuration 6 was at least 4% higher than the other configurations and 9% higher than the base line (configuration 1). These improvements in efficiency are linked with a reduction of 49% in specific consumption of thermal energy in comparison with the base line and 32 - 40% with respect to configurations 2 to 5. This result suggests that every 1% of improvement in thermal efficiency of the furnace leads to 5 - 8% of reduction in specific consumption, which is a promissory figure for investment projects.
Configuration 1 had the lowest thermal efficiency which is attributable to the relatively higher loss of sensible heat since this configuration did not include neither oxycombustion nor preheating of oxidant. Even though configuration 3 had similar losses of sensible heat in comparison with the base line, it could get 3% higher efficiency approximately which implies that a reduction of N2 in the oxidant and an increasing in the concentration in radiant-participant species such as CO2 and H2O has an important effect on the heat transfer to the load.
Configurations 2, 4 and 5 had similar thermal efficiency around 35%, which is related to lower losses of sensible heat. In the case of configuration 2, the lower loss of sensible heat is due to lower production of flue gases, while configuration 4 and 5 use preheating of the air by means of recovering of waste heat in flue gases. A special comparison must be done between configuration 4 and 5 because they have same efficiency in despite of configuration 4 has an oxycombustion burner and configuration 5 does not. As it was said before, oxycombustion reduces the flue gases flow and therefore less heat is available for recovering while combustion with enriched air has more heat for transfer to the air. In this case, configuration 5 allowed recovering of 10 kW more than configuration 4 and it was enough to make equal the efficiency of both configurations. However, configuration 4 has the advantage of reducing emissions of NOx as will be mentioned later.
Losses through the walls were common for all configurations. These losses were in the range of 100 - 200 kW, which corresponds to losses around 10% of energy of the fuel. This proportion is relatively high and it offers an opportunity of improvement for the process. On the other hand, unknown losses were lower than 10% and they are likely due to leaks through walls where burners were located since some blanks were inevitably left during installation of the burners.
In Fig. 8, NOx measurements for each configuration in the flue gases are showed. Configuration 4 and 5 had the highest concentration of NOx due to the use of preheated air with only an enrichment of 40% oxygen in the oxidizer. In the literature, it has been reported that even with the reduction of nitrogen that occurs in the enriched air combustion, reducing NOx emissions is not evident until oxygen concentrations around 70% are achieved [28]. Configurations 1 and 3 had NOx emissions below the limit permitted by Colombian regulations (1000 mg / m3 at 11% v/v O2), which is due to the introduction of oxy-fuel burners and not preheating of the air. Configuration 2 and 6, meanwhile, yielded very low NOx values due to the use of oxygen as the only oxidizer. The presence of nitrogen in the combustion gases is mainly due to desorption of nitrogen compounds from raw materials for the production of frits.
Experimental results showed a strong influence of the residence time of the combustion gases on the specific fuel consumption in the production of frits. This effect needs to be understood from the standpoint of the interaction of chemical kinetics, turbulence and combustion, so a numerical simulation analysis to is required to have an approach to this phenomenology. This simulation is on execution and will be presented later.
4. Conclusions
In high temperature furnaces for frit production, technology combustion system and the residence time of the combustion gases into the furnace determine the process efficiency. This paper evaluated experimentally the effect of the burner distribution and residence time on the specific consumption of thermal energy and furnace productivity. The results showed that increasing the residence time of the combustion gases can significantly reduce the specific consumption of this type of furnace, while the change of the combustion system between oxy-combustion, enriched air combustion and preheated air combustion has no significant changes in the specific consumption, although it was noted that the oxy-combustion systems with flat-flame generated lower values of this consumption.
A longer residence time of the combustion gases produced a larger warming of the internal walls in the oven, whereby incident radiation on the load was increased. Furthermore, in the oxy-combustion system, the increase in concentration of radiation participating species such as CO2 and H2O caused a longer residence time of these species into the furnace, increasing the incident radiation on the load. In addition, the use of flat-flame burners in oxy-combustion mode allowed greater coverage of the melting area.
Moreover, oxy-combustion has the advantage of removing nitrogen from the combustion, whereby NOx emissions are substantially reduced. The only produced emissions are due to volatilization of nitrogen compounds that are part of the raw material in the process. Enriched air and preheated air combustion, in despite of reducing oxygen costs, generates higher NOx emissions due to the presence of nitrogen and to the high temperatures generated in the process. This adverse effect can be reversed if enrichment higher than 70% oxygen in the oxidizer is achieved.