1. Introduction
The ceramic process (clay transformation) is mainly composed of three stages: the preparation of ceramic paste, molding, and cooking. In the first stage, the composition and plasticity are modified by adding other clays or materials to obtain a homogeneous ceramic paste and can be molded. Note that in some cases, the addition of other materials could improve the mechanical or physical properties; this depends on the chemical and mineralogy of the clays or additives used. After a geometric block wet has been obtained by extrusion molding in the second stage, this block is dried under controlled conditions to avoid superficial damage [1]. Later this, the block dry is cooking to decrease porosity, increase density, and mechanical resistance in the third stage, where finally are sale such is shown in Fig. 1.
The ceramic companies have been classified according to the production capacity and technology as chircal, small, medium, and large [4]. Clays are the primary raw material for the manufacture of ceramic construction products, which appear in all rock formations [5,6]. Technological properties such as mechanical, chemical, physical, and mineralogical differ widely, even between layers of the same clay formation. Therefore, the control of the quality of the products of any ceramic company begins with the characterization and constant monitoring of the raw material used [4].
The chemical and mineralogical compositions (Characterization of the raw materials) are one of the most important tests to evaluate clay and its influence during the ceramic process [1,7,8]. Plasticity (Physical characterization) is another critical parameter to control, understood as the property that clays have of forming a plastic and homogenous ceramic paste. The granulometry distribution is another variable of high importance (Physical characterization); this depends on the degree of molding of the particles and the physic-mechanical properties of ceramics such as porosity, water absorption, and mechanical resistance principally.
Norte de Santander region is recognized nationally and internationally due to its raw materials base clay quality. The companies do not know the behavior of the raw materials used in the manufacture of products derived from clay [9]. Also, Cesar in Norte de Santander region, Colombia is another important region where the characterization of the raw material of the companies in all technological ways has taken great value to study [10,11]. In this way, it’s of great importance to add new materials, other clay, or additives to improve the mechanical and physical properties of the H-10 blocks, thus increasing the circular economy of masonry products for construction and therefore the growth of this important industrial sector [12].
In Norte de Santander, Colombia, some investigations have been carried out in companies mainly in Cucuta, where the construction blocks are manufactured on a large scale. Mainly, laboratory tests are developed to determine the physical-mechanical properties and thus define if the blocks are suitable for commercial use as non-structural masonry products for indoor use and outdoor, according to the NTC 4017 and NTC 4205 Colombian standard procedures [13-17]. However, in Ocaña, some studies on the subject are in less scale, with the principal aim of the finding of optimal mixtures in terms of ceramic paste to develop different masonry construction products that could be produced in the region (Block H-10) according to the technological capacity of the companies [18-20]; García-León et al. 2016 developed laboratory tests in blocks manufactured in Ocaña to determine some mechanical properties such as mechanical resistance and water absorption according to the guidelines NTC 4017 standard procedure. The results were analyzed and used to improve the extraction and selection of raw materials base clay and thus to optimize the economic resources of the company studied [21,22].
The dimensions of the H-10×30 blocks of the ceramic companies of Norte de Santander oscillate depending on the technology used; for the case of the block of 6 holes, the most common high values are between 28.00 to 30.50 cm, and the values of the width between 9.64 to 10.46 cm according to the investigation carried out on the Cucuta blocks [23]. In this way, blocks type H are elaborated under different configurations varying the values of the width (10, 20, 30, cm), the length (20, 30, 40, cm), and the number of holes (2, 4, 6, 8, 10, 12, cm) with a constant height of around ~20 cm.
On the other hand, the term sustainable development (SD) appears with the concept of managing the efficient and rational resources that use the companies to society, and thus provide better well-being to the current population and the life of the future generations, due to the pollution generates the industrial sector. Also, the SD aid in another way to achieving economic growth of the companies and safe the natural sources of the environment, taking into account the sustainability strategy [24]. Some investigations have identified the relationships between the dimensions of blocks, such as the concept of eco-efficiency, which seeks to unite environmental and economic improvements [25,26], the social and environmental relationship through the investigation can be carried out in higher education institutions, through the analysis of various theoretical and business models, as well as various certification standards.
Nowadays, not enough investigations have developed to determine the physical and mechanical properties of the masonry products for construction, specifically the mechanical resistance to flexion (rupture module) for the H-10 block of six holes elaborated in Colombia. For this purpose, different laboratory tests were applied, and the values obtained from the experimental tests were compared with the values established by current standard techniques such as NTC 4017 and NTC 4205 standard procedures. Finally, the SEM-EDS technique was applied on the surface of the current manufactured block to identify the main chemical elements and defects:
2. Experimental procedures
NTC 4017 and NTC 4205 (Norma Tecnica Colombiana “NTC”) were used to develop this investigation, which presents the minimum parameters and requirements of quality for the manufacture of masonry products for construction and thus avoids damage in terms of environmental sustainability production and responsible consumption. The most common tests used to measure the physical-mechanical properties of clay blocks are break module (resistance to flexion), resistance to compression, initial and final absorption. The studies carried out randomly H-10 blocks of 6 holes were selected from the ovens of the companies under study, with dimensions of 10 width × 20 high × 30 length (cm), due to being the most commercial within the Norte de Santander region and its surroundings.
Blocks H-10 of six holes of Companies from Norte de Santander in Colombia (Ocaña and Cucuta) were used as samples to develop Physical and mechanical laboratory tests. The experimental data obtained were compared with the NTC 4205 standard procedure. The methodology applied is shown in Fig. 2. During the laboratory tests, at least 5 samples of masonry units (blocks) were selected to validate the statistical behavior of the data, which were compared with the values of the NTC 4205 standard, that define the permissible values of physical-mechanical properties for units of masonry [27,28].
During the physical-mechanical tests (initial and final water absorption, morphology, compression, and flexion), the blocks were dried at a temperature of 110 °C for 24 h in the Gabrielli brand oven to remove residual humidity (Fig. 3).
The dimensions of the H-10 blocks (length, width, thickness, and partitions) were measured to observe the variability between the different samples. A conventional digital Vernier caliper (Baker equipment), an electronic balance (for water adsorption), and a universal machine model Pinzuar-50K for compression and flexion tests with a calibration certificate dated 05 August 2019 were used to measure and develop the physical-mechanical properties. The values obtained were validated statistically with the aid of the STATGRAPHICS Centurion software for the experimental set of samples and tests.
2.1. Physical tests
2.1.1 Thicknesses and partitions
This physical property is related to the transversal elements that hold the walls on one side with the opposite or separate holes within the piece. In both horizontal and vertical drilling samples, the outer holes can be substantial, perforated, or double, considering the acceptance and rejection criteria with the parameters established by the NTC 4017 and NTC 4205 standard procedures. The morphological or dimensional characteristics of block H-10 are the length, width, height of the base to the piece, thickness, and weight, as shown in Fig. 4a. The way the measurements were made with the digital Vernier caliper is shown in Fig. 4b.
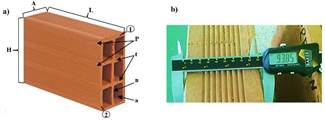
Source: The authors.
Figure 4 Dimensions of the block H-10, a) principal measurements, and b) Measurements with a digital Vernier caliper. Where: L is the length (mm), A is the width (mm), H is the height (mm), a is the hole, P is the smallest thickness of the walls (mm), T is the smallest thickness of the partitions (mm), N is the thickness of the nerve (mm), and 1, and 2 are the thicknesses or partitions (mm).
2.1.2 Initial absorption rate
This property is the capillary absorption capacity of the dry samples measured during 1 min. The water absorption is directly related to the porosity of the elements subject to test and the quality of the raw materials. When the values of absorption of water are low, this suggests a minimum capacity for collecting humidity from the environment; besides, it indicates good mechanical properties on the behavior of the clay used Eq. 1 was used to estimate the initial rate of water absorption according to the NTC 4017 standard procedure [27], where: T.I.A is the initial absorption rate, G is the difference between the initial and final weighing per min, and A is the contact area with water.
The samples previously dried in the oven were weighted before the test, and after placed on supports inside a water container that not contain more than 5 mm deep of water to ensure that the bottom surface of the block gets wet and absorbs water during 1 min of exposure according to the guidelines of the NTC 4017 standard procedure, such as shown in Fig. 5. Finally, the blocks were removed from the container, water excess was dried with a cloth, and the block wet was re-weigh during the following 120 s.
2.1.3 Final absorption rate
This laboratory analysis determines the increase in mass in the blocks submitted to immersion in water for 24 h. Initially, the block samples previously dried in an oven were weighed and immersed in a tank with water at room temperature (~20°C), as shown in Fig. 6b. Subsequently, at the end of the 24 h of immersion in water, the blocks were removed, and water excess was dried with a cloth and re-weighed (It is essential that the weighing of each specimen takes place within 300 s after being removed from the water) such as shown in Fig. 6a. According to the NTC 4205 standard procedure, the maximum final absorption values are 13% and 13.5% for indoor and outdoor use, respectively. These values are of equal magnitude for structural and non-structural use. According to his geometry, the main objective of this test is to calculate the increase in mass that the block obtains due to the porosity. The percentage of water absorption was calculated using Eq. 2 according to the guidelines of the NTC 4017 standard procedure [27], where: WS is the dry mass before immersion (g), and WSS is the wet mass after immersion (g).
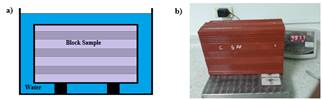
Source: The authors
Figure 6. a) Final absorption rate test (weighing block samples), and b) Representative scheme.
2.2 Mechanical tests.
2.2.1 Resistance to compression
This analysis is to put a block sample that does not present irregularities such as pores, cracks, and fissures, mainly. In this way, on the surface of one face of the block, a constant normal load was applied to compression uniformly (are used in the wall), such as shown in Fig. 7. The values of the last resistance of each block are taken by dividing between the area of the surface in compression and the value of the last effort, that is, the point where the block stops supporting the high load, and the failure occurs. Eq. 3 was used to calculate mechanical resistance to compression, taking into account the NTC 4017 standard procedure [27], where: σ is the last effort, F is the load applied, and A is the cross-sectional area.
2.2.2 Mechanical resistance to flexion (rupture module)
This analysis allows knowing the minimum value of the blocks about the resistance on two points; note that the NTC 4017 standard procedure does not present a premeditate value for evaluating this parameter. During the test, the block samples are placed on the supports, shown in Fig. 8 (The supports are solid steel bars). In this test, a constant normal load was applied to the block’s central area (Where the force will be concentrated). Eq. 4 was used to calculate the breaking module taking into account the guidelines of the NTC 4017 standard procedure [27]:
Where: MR is the sample breaking module, W is the maximum load indicated by the test machine (N), L is the distance between the supports (mm) (measured from center to center), b is the net width (face-to-face distance) of the sample in the fault plane (mm), and d is the depth, (distance from the top face to the bearing plane) of the sample in the fault plane (mm).
2.3 Chemical tests
The principal defects on the block sample were observed visually, and the topography characteristics were obtained using a scanning electron microscope with the aid of COXEM/INTEK/SEM-EDS equipment operating at 20 kV. The identification of phases of the raw materials for both companies was carried out by X-ray diffraction using a Bruker/D8-ADVANCE/XRD equipment with CuKα radiation and 2θ angles of 0°-70°, and a glancing angle of 1°.
3. Results and analysis
3.1 Morphology and water absorption results
The masonry products for construction do not present uniformity for all the samples tested for both companies studied. This behavior perhaps is due to the do not exist technical parameters of quality or an adequate technological characterization of the raw materials base clay, taking into account that exits many contractions of the drying and cooking stages of the blocks in the ceramic process thicknesses can occur. Therefore, the estimations of these physical parameters are very hard to control. Fig. 9 shows morphological values as results of experimental tests such as width, height, length, partitions, and thicknesses for each test according to the NTC standards.
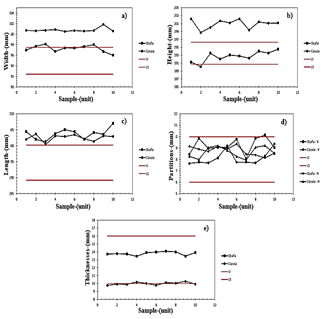
Source: The authors.
Figure 9 Thickness values for the experimental set. a) Width, b) Height, c) Length, d) Partitions, and e) Thicknesses.
Fig. 10 shows the initial absorption results for the blocks selected in the company of Ocaña and Cucuta, respectively, according to the NTC 4205 standard procedure; for this calculation, Eq. 1 was used. The charts were constructed under the assumption that the values have a normal distribution average of 0.22±0.04 % for the samples of the Ocaña Company; in this case, five (5) points are outside of the limit, indicating that it does not comply with the specifications of the NTC 4205 standard procedure. Otherwise, for the samples of company Cucuta, all the 5 points comply with the specifications of quality for the blocks H-10, presenting a normal distribution with an average of 0.05±0.16 %, indicating good processing of the raw materials during the stages of the productive process.
Fig. 11 shows the final water absorption results and presented the comparison of the two companies with respect to the NTC 4205 standard procedure, and Eq. 2 was used to calculate the values. In this way, the charts were constructed under the assumption that the values have a normal distribution with an average of 13.18±0.07 % for the samples of Ocaña Company similar results with [29], according to the parameters established by the NTC 4205 standard procedure. For the case of the samples of the Cucuta Company, the 5 points shown in Fig. 11, five (5) are outside the limits, taking into account the upper limit (LS) and lower limit (LI). Consequently, these values do not comply with the standard procedure parameters; these values present a normal distribution with an average of 9.95±0.34 %, similar results with [17]. The quality of the blocks in terms of final water absorption is related to defects during the production process, the diameter of sand particles, the properties of the raw materials, and the formulation of an optimal mixture for masonry products.
3.2 Mechanical resistance to compression and flexion results.
The compression test was carried out with 5 previously prepared block samples according to the NTC 4017 standard procedure. The minimum compressive strength for the average of the 5 samples is limited to a value of 5.0 Kgf/cm2 for horizontal drilling masonry according to the NTC 4205 standard procedure, and Eq. 3 and Eq. 4 were used. Fig 12a showed that the Ocaña Company samples present low behavior on compression and flexion with a value average of ~13.82±1.23 Kgf/cm2 and 3.60±0.30 Kgf, respectively. This attribute to big particles of sand, chemical properties, and performance in the drying and cooking stage of the raw material.
On the other hand, the Cucuta Company samples presented a high-value average of ~20.17±1.35 Kgf/cm2 for compression and 7.28±0.71 Kgf for flexion test such as shown in Fig. 12b. The Cucuta Company presents 35% and 50% better values concerning the Ocaña Company. It was observed that both companies comply with the specifications and exceed the values 2 and 3 times concerning mechanical resistance. In this way, only two samples comply with the specifications; this is associated with characteristics of the productive process and mechanical, physical, and chemical properties of the raw material. When the samples absorb a high percentage of water, these phenomena do not reduce the other mechanical properties like the resistance to compression. Notice that the blocks present a high resistance to flexion, but the NTC 4205 standard procedure does not present permissible values to consider this parameter. Therefore, these results are presented to show a global visualization of the ceramic masonry products-based clay.
3.3 Comparative of the experimental results with the values of the NTC standard procedure.
With the previous experimental results, it can be observed that for the case of morphological considerations, the Ocaña Company mostly complies with the specifications of the NTC standards, which is related to the extrusion, kneading, drying process, and chemical properties of the raw materials used to perform masonry products base clay [3]. Table 1 summarized the experimental results obtained and presented an observation according to the NTC 4205 standard; similar results have been reported by [10,23].
3.4 Chemical characterization results
The experimental test results carried out determined that the process presents inconsistencies regarding the size of the particles formed in the crushing and rolling stages of the ceramic process, obtaining samples with cracks, pores, and sand particles greater than 2 mm, as shown in Fig. 13a. Perhaps due to the wear of the machines during the crushing process, chemical properties of the raw material, lack of development of the technical test, and lack of maintenance follow-up.
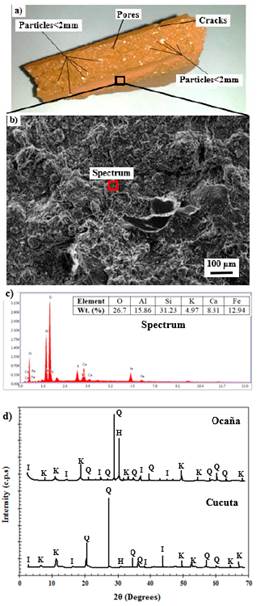
Source: The authors.
Figure 13. a) Defects on the blocks, b) characteristic microstructure via SEM, c) EDS from the principal elements on the surface, and d) XRD pattern for the raw materials from the Companies.
The SEM-EDS micrograph from the surface of the current block manufactured in one of the companies studied (Fig. 13b and Fig. 13c) indicates that the clay minerals are constituted mainly by silica and hydrated alumina-silicates with the presence of some other elements, such as Na, Fe, K, and Ca, similar results found by [30], finding typical clays of this region with the mechanical and physical properties evaluated and compared with the Norma Técnica Colombiana (NTC) [12]. These values indicate that one of the companies uses natural sediments that can be considered useful to medium quality plastic clays to prepare its masonry products for construction and is similarly used in the ceramic industries [16]. Notice that the superficial texture presents high roughness due to the main particle size, such as sands, silts, and clays. This behavior can be changed by adding other materials or improving the manufacturing process to obtain the masonry products and thus increase the mechanical properties in some cases [31]. This also could be used to improve the extraction and selection of raw materials base clay used in the production of blocks. Besides, optimize the economic resources of the companies that generate masonry products base clay that contribute to the sustainable development of the environment and ceramic sector.
The analysis by XRD pattern of Fig. 13d expose that the clay minerals of the raw material consist mainly of phases such as Hematite [H~(Fe2O3)], Illite [I~(KH3O)(AlMgFe)2(SiAl)4O10], Kaolinite [K~Al2(Si2O5)(OH)4)], and the high presence of Quartz [Q~(SiO2)], which were identified through the PDF-2 diffraction profiles database, thus, obtaining characteristic clays of the Norte de Santander raw materials for both Companies, and another region such as been reported by [12,32]. Also, is evident that the raw materials of Cucuta Company have minor impurities than Ocaña Company [7,33]. In this way, clay aid to obtain an adequate plasticity index, the Al2O3 contributes to the flux, and the SiO2 as a stabilizer [34].
4. Conclusions
The conventional statistical analysis for initial and final absorption of the blocks exposed that the low porosity is related to the compaction of the clay mixture during manufacture. The maximum values of water absorption, according to NTC 4205 standard procedure, must be less than 0.10% for indoor or outdoor use. However, for the statistically obtained values, many exceed 10% of the standard deviation, so these companies are certified in their production process but not in the product they manufacture because there is no reliability in terms of product quality in the values obtained concerning the Colombian standards.
The chemical composition and physical-mechanical characterization (Technological characterization) of the raw material within the manufacture of ceramic blocks are of utmost importance. Therefore, drying and cooking stages, the block becomes more complicated depending on the chemical properties of the raw materials (Contractions of thicknesses); notice that its physical properties also are not constant because the interstitial spaces between the particles are large (sand particles <2mm); therefore, the blocks have an excellent water absorption resistance, and thus low mechanical resistance.
Due to the difference in the raw material of the companies, the results regarding the NTC (Normas Técnicas Colombianas) differ by 30%, with the H-10 blocks of Cucuta concerning the Ocaña Company, which present the best properties and complying in greater quantity with the values according to the Colombian standards used.
On the ceramic stages is recommended to modify the quality of the raw material or the addition of others with major quality to not generate rejections of the final product due to the non-compliance with the specifications of the Colombian standards. This generates waste that not includes sustainable development companies. To improve sustainable development in the ceramic sector, actions must be taken to optimize the infrastructure and innovation of production processes to reduce emissions and production losses, which is reflected in economic implications.