1. Introduction
Ductile iron arises from the modification of grey iron. Its most important and distinctive microstructural characteristic concerning the flakes typical of grey iron is the presence of graphite nodules, which reduces the stress concentration effect generated in the flakes. Since its commercial introduction, it has been a very striking alternative due to its manufacturing cost, its versatility in terms of part design, and the properties achieved like no other type of casting. The significant reduction of weight and its redesign for high quality and better performance makes it competitive with some steels in the manufacture of engineering components. An application of nodular (or ductile) cast iron is the manufacture of various components of the automotive industry for the construction of different parts such as axles, brake discs, cards, or connecting rods for engines, due to the wide range of mechanical properties related to the microstructure of the matrix and the characteristics of the graphite nodules present in the cast iron [1].
It is also noteworthy the progress in the development of austempering heat treatment through which a microstructure of acicular ferrite and austenite (ausferrite) has been achieved. Together with the graphite nodules, it has given rise to a microstructural condition with better mechanical properties that allowed a better balance of mechanical strength and ductility. This is known as Austempered Ductile Iron (ADI; [2-6]). Besides, an improvement in wear resistance can be achieved by adding carbide-forming elements to the chemical composition (CADI) [7,8]. In the search to improve its surface characteristics of resistance to corrosion and wear, a whole series of surface technologies have been generated [9-14] and one of them is precisely ion nitriding, to which this work is directed.
In the field of thermochemical treatments, conventional nitriding is a surface hardening process in which, through nitrogen absorption, extraordinary hardness is achieved on the periphery of the parts. This process increases wear and fatigue resistance, improves corrosion resistance and maintains a constant hardness, even at temperatures in the order of 500 °C, and it does not produce deformations in the piece. Conventional nitriding is carried out at temperatures between 490 and 580 °C, where the percentage of nitrogen that can be diffused is very low. However, at higher temperatures, a negative effect is obtained, thus obtaining layers of solid nitrogen solution, which are of no industrial use. The alloy elements most closely related to nitrogen and, therefore, more capable of forming nitrides are Al, Cr, Mo, V and Ti, which provide greater hardness and the resulting nitride layer is more uniform and compact [15].
More recently, within the alternatives of thermochemical processes, surface treatments with plasma have been developed, using an ionized gas that generates a chemically active medium. The so-called thermal plasmas or high energy density plasmas allow materials to be melted or vaporized in volume with applications in welding processes, thermal spray and processing of materials at high temperatures. This technology also makes it possible to perform surface hardening of metal components, thus obtaining functional, tribological, corrosion-resistant, high-temperature and fatigue-resistant coatings, both on cutting or machining tools and on engine or machinery components. These modification processes are of interest in sectors such as the automotive, tooling, food packaging and protection, textile, biomedical and aerospace industries.
Ion or plasma nitriding is currently the most modern procedure for performing nitriding. In this case, the introduction of nitrogen comes from the plasma generated by a luminescent discharge. After obtaining a high vacuum in a reactor, gaseous hydrocarbons are introduced at a pressure usually ranging from 0.1 to 10 Torr. A potential difference is applied between the walls of the reactor, which acts as the anode, and the parts, which act as the cathode. A plasma is then generated, which dissociates the treatment gas and the ions generated are projected onto the parts to be treated.
During treatment, the structure of the first layers of the material is conditioned by the elements in the gas mixture. If the mixture is free of carbon, a single-phase layer is formed (γ). If 0.5 % of carbon is added to the treatment atmosphere, a single-phase layer is obtained (ε). Therefore, it is possible to obtain the most suitable layer for loads of the part to be treated, depending on the appropriate conditions, i.e., it is possible to obtain nitrided layers exempt from the combination layer, consisting only of a diffusion zone. This type of coating confers a high surface hardness and also a great toughness against possible problems of fragility in edges and cutting edges.
The control of the process parameters is highly complex, as well as its relationship to the characteristic parameters of the plasma. This complexity is one of the main difficulties for scaling at the industrial level the reactors developed at the laboratory level, but it is also the origin of the versatility of plasma processing.
Ion or plasma nitriding has been applied for a long time with special emphasis on stainless steels and tool steels, in general with quite success, which has allowed its application at an industrial level in different countries [14,16-18]. In these works, the formation of iron nitrides of different types generates modifications in the properties of the treated steels, which present a greater reactivity of the nitrogen ions generated. This can happen at lower temperatures; therefore, it turns out to be a process with lower energy expenditure and more environmentally friendly than the conventional nitriding.
Recently, the nitriding process has begun to be used in the surface treatment of cast iron materials. In particular, there is a small number of reports that the application of conventional nitriding to grey and nodular cast iron has been particularly successful in improving the wear and fatigue resistance of these groups of materials [19-21].
About plasma nitriding of casting iron materials, there are also few papers reported in the scientific literature on this subject. For example, on grey castings, it has been applied [22-25] to increase fatigue, wear and corrosion resistance. In particular, in the case of nodular castings [22,26], these objectives have not always been achieved [26], even, in some cases [27], the reduction of fatigue life (of a certain type) of components treated by plasma nitriding is reported. This behavior is mainly attributed to the reduction in hardness caused by the long exposure of the material to the nitriding temperature. In this work, a procedure is developed to generate iron nitrides through ion nitriding, from a ductile iron material.
2. Materials and methods
The materials used in this investigation (ductile iron cast) were manufactured in the Departament of Metallurgical Engineering of the School of Chemistry at Universidad Nacional Autónoma de México (UNAM). The configuration of specimens of ductile iron are 7 mm in diameter and 12 mm in thickness.
Fig. 1 shows the general configuration of a nitriding system for a low-pressure plasma including the gas supply system, the vacuum system, a power source and a treatment chamber, to perform the process. Fig. 2 shows a greater detail with the equipment for plasma nitriding treatment. This equipment is located at the High Vacuum Laboratory of Experimental Physics Department of the Physics Institute of UNAM.
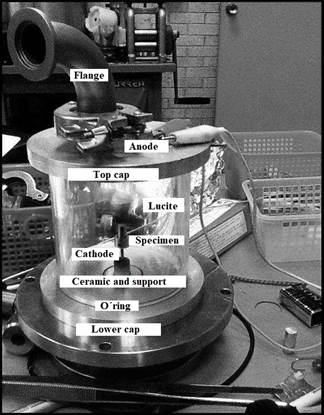
Source: The authors.
Figure 2 Detail and identification of the components of the ion nitriding chamber.
A Each part of the equipment used will be described below: (Fig. 1 and Fig. 2).
1. Vacuum System: It is connected to the process chamber through a vacuum pump, with which a maximum pressure of 1x10-3 Torr can be reached. For lower pressure, it is necessary to use a turbo vacuum pump, which generates a vacuum of 1x10-6 Torr.
2. Gas supply: The gas flow condition for the experiment was a mixture of N2-H2 and Ar-H2 and a percentage of H2 in the mixture, not exceeding 10%, was determined to be optimal.
3. Absolute pressure gauge brand Varian: It checks the pressure-vacuum of the system during the experiment.
4. Power source: It provides the voltage of at least 600 V DC, a current of 100 mA and an approximate power of 200 W.
5. Treatment chamber: (Fig. 2) It is a vacuum chamber with the following approximate measurements: 5 cm high and 13 cm diameter. This element is manufactured in stainless steel and is composed of the following elements.
A lucite tube. This material is transparent, very light, resistant to impact and a good thermal insulator.
Two stainless steel covers that allow diminishing the heat transfer by conduction.
Top cover, on which a flange is placed to make the connection between the process chamber and the treatment chamber.
Lower cover. In this cover, a copper element was placed in the central part to act as a support for the material to be treated, as well as a ceramic tube that covers the fastener to avoid electric arcs during the process.
6. The function of orienting the ionization of the gas mixture near the target is due to the proper polarization of the system. The anode is connected to the upper lid of the treatment chamber and the cathode is connected to the lower lid of the chamber. The treatment chamber is assembled to the process chamber with the help of the flange on the top lid of the treatment chamber and to the vacuum pump. Fig. 3 shows a detail of the camera assembly.
Once the chamber reaches a stationary vacuum state, the process is stabilized within an appropriate waiting time and the nitrogen and hydrogen gases are allowed to enter. Voltage is applied between the electrodes of the system (processing chamber) and the gas discharge and, if the processing conditions are appropriate, an ionized gas (plasma) is obtained.
In particular, after a series of experiments, to be able to adjust the different process parameters, the nitriding was carried out under the conditions shown in Table 1. This experimental development to find an adequate combination of variables depending on the deposition of a layer is recorded in [28].
To know the microstructure of the materials studied, a metallographic evaluation is carried out. This metallographic preparation before and after ion nitriding process is carried out using conventional sanding and polishing techniques [29], [30]. Its observation was carried out in a JEOL JSM-5600 LV scanning electron microscope which is equipped with an EDS probe. The surface characteristics of the sample were evaluated in a JEOL JSPM-4210 atomic force microscope.
The mechanical property of hardness was evaluated by using Vickers microhardness and a Leitz Wetzlar Germany 8068 microdurometer, with a 50 g load for 20 s, and making 20 measurements in various areas of the treated samples.
The structural evaluation of materials was made using X-ray diffraction. These studies were carried out in a Brucker model D-8 Advanced diffractometer. The diffractograms of the samples before and after the applied treatment were obtained under the following scanning conditions: 2θ range from 4° to 109°, scanning step of 0.039° and in a time per step of 54 seconds, using Cu radiation with a Kα=1.5405 Å.
3. Results and discussion
Table 2 shows the elemental composition of the substrate. Elements such as Mn in this cast iron allow increasing the mechanical strength, hardness and the penetration of hardening. The same happens with the Si that increases the hardening capacity of the material.
Fig. 4 shows the initial microstructure of the sample used. The predominant presence of graphite nodules in a ferrite matrix is distinguished. These graphite nodules act as a lubricant and inhibit the formation of cracks, thus improving their tribological properties. Combined with the ferrite matrix, they provide high ductility to the material.
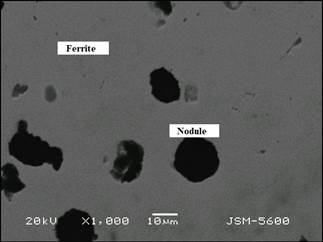
Source: The authors.
Figure 4 Microstructure of ductile iron in its initial state. The presence of ferrite and graphite nodules can be distinguished. SEM with BSE at 1000X.
In the atomic force microscopy (AFM) image (Fig. 5), the graphite nodules that protrude from the sample can be identified, thanks to the contrast changes generated. An adequate distribution of these nodules is also observed throughout the sample.
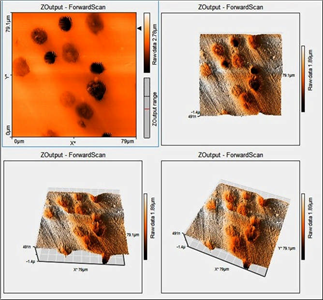
Source: The authors.
Figure 5 AFM microstructure of ductile iron in its initial state, in which the presence of a ferrite matrix (clear fields) and protruding graphite nodules (more intensely colored fields) can be distinguished.
The EDS spectrum shown in Fig. 6 and taken on ductile iron as a whole for the semi-quantitative composition shows the presence of a Fe peak of greater intensity, followed by a Si peak and a C peak of less intensity. These elements are characteristic of a ferritic type ductile iron ans this distribution of the peaks denotes what is found in the elemental composition.
The diffractogram in Fig. 7 corresponds to the ductile iron before the ion nitriding treatment. The presence of a BCC crystalline structure is evident with network parameters a=b=c 2.866 Å, and α=β=γ=90° with spatial group Im-3m (229). This group corresponds to Fe and, according to the AMCSD 000670 database, a maximum in the peak of diffraction with the highest intensity is located in 2Ɵ=44.68 °, followed by peaks of lesser intensity located in the positions 44.67°, 65.03°, 82.34°, and 98.96 °.
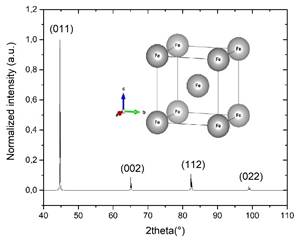
Source: The authors.
Figure 7 Diffractogram of the ductile iron sample prior to the application of the ionic nitriding treatment.
The SEM image presented in Fig. 8 shows the evidence of how the graphite nodules have been modified by the ionic nitriding treatment. The interaction of nitrogen ions on the surface is such that it manages to tear off some nodules. The luminous halo also shows this behavior and is given by the high accumulated load around them. This is also described in [30].
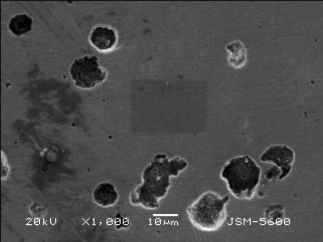
Source: The authors.
Figure 8 Micrograph of the surface of the ductile iron after the plasma nitriding treatment A halo can be observed around the graphite nodules. SEM. BSE. 1000 X.
The results of X-ray diffraction after nitriding (Fig. 9) show the formation of Fe3N crystalline structures, with the appearance of a phase with a hexagonal structure and another with an epsilon hexagonal structure (ε), both of them with space group P6-322 (182). The appearance of diffraction maxima on Feα corresponds to the substrate. Phase ε has a compact hexagonal structure, with nitrogen atoms occupying the octahedral holes. In addition to forming this compound, nitrogen diffuses from the surface of the treated sample and reaches a certain depth, which depends on time, temperature and the nitrogen potential used in the process. The beginning of the formation of a layer of compounds, consisting essentially of iron nitrides type ε, is a sign of the presence of metal ions that are released from the cathode and react with the ions of the gas-forming compounds, in addition to being implanted on the surface of the material. In other works, for example [22], where grey cast iron was ion nitrided, it is reported that the amount of hydrogen used in the nitriding mixture influences the formation of nitride phases in the layer. In fact, it is detailed that the intensity of the phases formed decreases with increasing hydrogen content in the nitriding mixture. From the above, it can be inferred that the process used, with the mixture employed and the operating conditions used, achieved its purpose of forming iron nitrides, even if in a limited way, since only the presence of iron nitride Fe3N was detected. A first reflection leads to the idea of the need to increase the processing time in order to allow the formation of other iron nitrides phases.
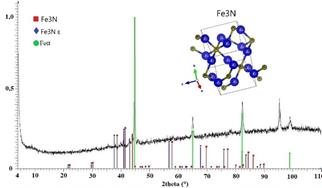
Source: The authors.
Figure 9 Diffractogram of ionic nitrided ductile iron. The presence of iron nitride epsilon (Fe3N) stands out as evidence of the result of the nitriding process.
Fig. 10 shows the microhardness results of the ion nitrided material. As for this property, the average value of untreated ductile iron was 370 HV, which represents 18.6% more than that reported by Agredo et al. [1]. The average value of treated pieces was 482.2 HV, which corresponds to an increase of about 30 % in the microhardness value and is consistent with the values reported in [23], although lower than those presented in other articles [16-19]. This behavior is associated with the different compositions of the substrate. In some cases [16-18], when dealing with steels, the presence of diverse alloys such as chrome (strong formers of nitrides) influences the obtaining of greater microhardness. Another vital variable is the experimental conditions used (longer times, for example), which can lead to the formation of other nitrides such as Fe4N or Fe0.09 N. According to the reports in [16-19,23], an improvement in the tribological properties of nodular iron would be expected, which would coincide with results in other works [23,24].
4. Conclusions
Given the operating conditions studied in this research (gas mixture, temperature and voltage), it was possible to achieve nitride ferritic matrix smelting, which allowed obtaining an increase in the mechanical properties of the material at the surface level.
Diffraction analysis identified the formation of hexagonal Fe3N crystalline structures, with the presence of an epsilon iron nitride phase, which achieved an increase in the original microhardness of the order of 30%. This increas would be expected to improve the wear behavior of the ferritic ductile iron.
In a future study, tests will be carried out to assess the effects of this treatment on the wear resistance of the treated material.