Introduction
Methionine is a sulfur-containing essential amino acid required in the diet of humans, other mammals, and avian species for their growth and normal body function. It plays an indispensable role in several cellular processes and activities, including the synthesis, stability, structure, regulation of catalytic function, and post-translational modification of various proteins [1].
In recent years, the demand for methionine has progressively grown due to the fast progress of the food additives market motivated by an increment in the consumption of milk and meat products at global scale [1].
According to Willke [2] L-methionine has the following applications:
As a flavoring agent in food additives.
Used in pharmaceutical preparations and medicines to prevent liver deterioration.
As a nutritional element in milk formulas for infants, parenteral nutrition, healthy foods, and as a component of sports supplements.
As stated by Reports and Data [3], the global methionine market was USD $ 6.18 billion in 2022, and is projected to reach USD $ 13.42 million by 2032, registering a compound annual growth rate (CAGR) of 9 °%, while as reported by Data Bridge [4] the global methionine market was USD $ 4.11 billion in 2022, and is estimated to reach USD $ 6.45 billion by 2030, with a CAGR of 5.8 °%. There are two isomers of methionine, d-methionine and l-methionine, which have different chirality. L-methionine can be used directly by organisms, while most d-methionine cannot be used by mammals until it is converted to l-methionine by aminoacid oxidase and transferase [5]. Methionine can be produced through chemical or biological routes [1]. Other authors [2] indicate that methionine production can be generally classified as chemical synthesis, chiral separation, chiral resolution and fermentation. Up to now, methionine is produced at commercial scale through chemical synthesis [1], consuming acrolein, methyl mercaptan and hydrogen cyanide as raw materials, thus producing the dl-methionine racemate which can be used either directly as food or converted into the l-isomer for human consumption and subsequent processing [6]. However, the production of methionine by microorganisms using natural renewable resources and low-cost waste residues is becoming more attractive. In this sense, Zhou et al. [1] investigated the effect of the culture medium composition and the fermentation conditions in order to improve the production of l-methionine using the genetically engineered Escherichia coli MET-3 microorganism. Also, in Xiong et al. [5] a separation process of L-methionine contained in a fermentation broth of the E. coli W3110 strain was designed based on macroporous resin chromatography. Furthermore, Mari et al. [7] studied the production of methionine by the fermentative route using Bacillus cereus isolated from soil. In another study [8], a metabolic pathway study was realized to forecast the metabolic potential of Corynebacterium glutamicum and Escherichia coli for the production of l-methionine, where the theoretical optimum yield of methionine and related flows were calculated for various scenarios involving different mutants and process conditions, based on detailed stoichiometric models. In Anakwenze et al. [9], the influence of culture conditions on methionine accumulation was examined using Bacillus thuringiensis EC1. Likewise, in Ranjan et al. [10] a satisfactory mathematical model was obtained to establish the relationship that exists between cell mass production, substrate consumption and product formation during the semi-continuous submerged culture of Corynebacterium lilium to produce methionine, which can be used then in process control applications. Finally, in Li et al. [11] a highly efficient l-methionine producer was derived from E. coli W3110 using rational metabolic engineering strategies. According to Wang et al. [12], the energy balance and metabolic feedback inhibition in microorganisms limits the large-scale production of l-methionine through fermentation. Recently, a new approach for the production of l-methionine using O-acetyl-homoserine (OAH) and 3-methylthiopropionaldehyde as substrates was studied in Wang et al. [12] by catalysis over the yeast OAH sulfhydrylase MET 17. Optically pure methionine has also been obtained through enzymatic conversion processes, which, although good yields were achieved, require expensive substrates, meaning that the production efficiency of these enzymatic methods is still lagging behind compared to the commercial production scale of chemical synthesis. In Mai & Ko [13], ionic liquids were investigated as additives to carry out the enzymatic synthesis of l-methionine from o-acetyl-l-homoserine and methanethiol, because these ionic liquids present advantageous properties such as negligible vapor pressure, excellent chemical stability, and the ability to dissolve a variety of solutes. In the extensively used chemical synthesis, acrolein and methyl mercaptan are first consumed to synthesize the hydantoin analog, then the intermediate is condensed and hydrolyzed to obtain methionine [5]. These chemical routes of methionine synthesis produce a dl mixture of the amino acid. At present, all these routes are adaptations of the Strecker synthesis, and use similar raw materials: acrolein, methyl mercaptan, various sources of ammonia and cyanide, using a catalyst [14]. An alternative process consumes propylene, hydrogen sulfide, methane and ammonia, to produce the intermediates acrolein, methylthiol and hydrocyanic acid. However, the synthesis of dl-methionine by chemical methods also causes serious environmental pollution [1], because it consumes dangerous chemicals such as acrolein, methyl mercaptan, ammonia and cyanide [15], requires a large number of procedures and equipment, with a high production cost [7], and it involves the consumption of fossil resources [13]. For Reershemius [16], the most significant industrial process to produce dl-methionine is chemical synthesis, also classifying it as the most economical to date due to the fact that it is possible to use the racemic mixture for food additives, since human organisms and animals can convert d-methionine to the nutritional form l-methionine by the enzymes oxidase and transaminase. In Intratec Solutions [17] a description of a dl-methionine production process by the carbonate route was reported using 3-methylthiopropionaldehyde and hydrogen cyanide as main raw materials, and without the formation of byproducts, where the process shown is comparable to one established by Evonik Industries AG. However, the available literature related to the simulation of a dl-methionine production plant via the chemical synthesis route is null, so it is not known what is the profitability, feasibility and yield that a process of this type will have.
A certain investment company plans to build a dl-methionine production plant via the chemical synthesis, and for that it needs to know the profitability, productivity and yields of a plant like this. In this context, in the present work the techno-economic evaluation and conceptual design of a dl-methionine production process through chemical synthesis is carried out, using SuperPro Designer® v13 (Intelligen, Scotch Plains, NJ, USA) simulator, in order to calculate its main productivity and profitability indicators under current worldwide economic conditions, and thus to obtain a simulation model that is available for future studies of scale up, optimization and increment of productivity, which could serves then as a prototype to promote research related to process engineering.
Materials y methods
Physical-chemical properties of l-methionine
According to the literature [2,16], the l-methionine presents the physical-chemical properties shown in Table 1.
Description of the proposed dl-methionine production process through the chemical synthesis route
The production process of dl-methionine by the chemical synthesis route begins when 300 kg of acrolein are sent to a stirred jacketed reactor of 2,500 L capacity (Reactor 1), together with ammonium carbonate (1,000 kg), hydrogen cyanide (150 kg), methanol (40 kg) and methyl mercaptan (190 kg). Once all these chemical reagents are present in the reactor, the mixture is heated to a temperature of 80 °C using steam, and subsequently maintained at this temperature value for 90 min for the hydantoin formation reaction to occur. The temperature is controlled at 80 °C by using cooling water inside the reactor jacket, because the reaction is exothermic. The hot gases exiting the reactor, which contain certain amounts of acrolein, methanol and ammonia, are sent to a shell and tube heat exchanger (Condenser) to condense them and then send the condensate obtained to the waste treatment plant. At the end of the reaction time, the hot reaction mixture (80 °C) is pumped to a second stirred jacketed reactor of 4,000 L capacity (Reactor 2), where 600 kg of a 50 % sodium hydroxide (NaOH) solution are added to the reactor, to then proceed to heat the resulting mixture to 90 °C with the objective that the formation of the dl salt occurs from the reaction of hydantoin with water and NaOH. The reaction temperature is kept at 90 °C by means of chilled water which flows inside the reactor jacket because the reaction is exothermic. This reaction occurs for a time of 90 min. Once the reaction time has elapsed, the resulting mixture is pumped to a shell and tube heat exchanger (Cooler 1), where it is cooled to 30 °C using chilled water, and then the cooled mixture is sent to an adsorption column to remove organic impurities such as residual hydantoin, ammonium carbonate, hydrogen cyanide, methyl mercaptan, among others. The resulting Altered mixture, which is rich in the dl salt and water, is sent to a third stirred jacketed reactor of 3,000 L capacity, where 400 kg of a 45 % aqueous solution of hydrochloric acid (HCl) are added, in order to reduce the pH to 2.3, so that the reaction of formation of dl-methionine occurs, as well as the neutralization of the residual NaOH, with the consequent formation of sodium chloride (NaCl). This reaction is carried out at 80 °C for 60 min, circulating steam through the reactor jacket to control the temperature at this value. Once the reaction is complete, the hot mixture (80 °C) is pumped to a shell and tube heat exchanger (Cooler 2) to reduce its temperature to 30 °C, and the cooled stream is then sent to a rotary vacuum Alter, which removes all the NaCl and ammonium carbonate contained in the feed stream, as well as certain amounts of the rest of the chemical components with a high removal rate. The output cake of the rotary filter is sent to the wastewater treatment plant, while the product output stream of this filter, which contains approximately 32 % dl-methionine, 60 % water and 7 % hydrochloric acid is sent to a reception tank (Tank 1), where it is stored for 15 min. Next, the mixture contained in the Tank 1 is pumped to a shell and tube heat exchanger (Pre-heater) where its temperature is increased to 90 °C using steam, and then it is sent to a double-effect evaporator where 70 % of the water and 90 °% of the rest of the components (HCl, hydantoin, hydrogen cyanide and methyl mercaptan) contained in the feed stream are removed. The steam and condensate streams leaving the double-effect evaporator are sent to the wastewater treatment plant, while the concentrated mixture leaving the evaporator, which is rich in dl-methionine with certain amounts of water, is sent to a tank (Tank 2) for storage during 15 min. Next, this concentrated mixture is pumped to a continuous crystallizer (Crystallizer) where dl-methionine crystals are formed, a process that has a residence time of 2 h and is carried out at 15 °C. Then, the output stream of the crystallizer, which contains the dl-methionine crystals, is centrifuged in a decanter centrifuge (Centrifuge), where the liquor is separated from the dl-methionine crystals, which still contain a certain amount of water (~ 30 %). The outlet liquor from the decanter centrifuge is sent to the wastewater treatment plant, while the concentrated mixture of dl-methionine crystals is sent to a drum dryer (Dryer) where 99.7 %% of the water that was fed is removed. The output stream of the dryer, that is, the dehydrated crystals of dl-methionine, is sent to a final storage tank (Tank 3) for subsequent commercialization. In the process described in this study, around 478 kg of feed grade dl-methionine crystals are obtained per batch with a purity of 99.87 %, where water is the only impurity found. Figure 1 displays the block diagram of the proposed dl-methionine production process via the chemical synthesis route previously described.
Chemical reactions
Shown below are the chemical reactions that occur in the dl-methionine production process via the chemical synthesis route:
• Formation of hydantoin from acrolein (Conversion: 95 %):
Formation of the dl salt from hydantoin (Conversion: 95 %):
Formation of the dl-methionine (Conversion: 95 %):
Formation of sodium chloride (Conversion: 98 %):
Unit cost of raw materials
Table 2 shows the unit costs of the different chemicals used as raw materials in the proposed dl-methionine production process by chemical the synthesis route.
Equipment cost
Table 3 presents the free on board cost of the equipment used in the dl-methionine production process by the chemical synthesis route, which were estimated using values reported in various references [26-30]. Next, the equipment costs were updated to June 2023 using the Chemical Engineering magazine's cost index = 1,013.1 [31]. The equipment was designed and chosen according to indications and recommendations published in [27,30,32,33], while stainless steel 316 was selected as the construction material for all the equipment included in the production process.
Table 3 Cost of the equipment included in the production process, and their characteristics.
Equipment | Amount | Characteristic | Cost (USD $) |
---|---|---|---|
Reactor 1 | 1 | 2.5 m3 / 3.5 kW | 40,000 |
Pump 1 | 1 | 4.0 kW | 5,000 |
Condenser | 1 | 30 m2 | 20,000 |
Reactor 2 | 1 | 4.0 m3 / 3.5 kW | 40,000 |
Pump 2 | 1 | 4.0 kW | 5,000 |
Cooler 1 | 1 | 5.0 m2 | 7,000 |
Adsorption columns | 1 | 2.2 m3 | 20,000 |
Reactor 3 | 1 | 3.0 m3 / 3.5 kW | 40,000 |
Pump 3 | 1 | 4.0 kW | 5,000 |
Cooler 2 | 1 | 5.0 m2 | 9,000 |
Rotary Filter | 1 | 15 m2 | 50,000 |
Tank 1 | 1 | 3.0 m3 | 15,000 |
Pump 4 | 1 | 4.0 kW | 5,000 |
Pre-Heater | 1 | 5.0 m2 | 6,000 |
Evaporator | 1 | 15.0 m2 | 120,000 |
Tank 2 | 1 | 1.0 m3 | 8,000 |
Pump 5 | 1 | 4.0 kW | 5,000 |
Crystallizer | 1 | 1.0 m3 / 5.0 kW | 50,000 |
Decanter centrifuge | 1 | 5.0 kW / 5,000 L/h | 25,000 |
Dryer | 1 | 15.0 m2 | 20,000 |
Tank 2 | 1 | 0.8 m3 | 7,000 |
TOTAL | 502,000 |
Simulation of the dl-methionine production process by the chemical synthesis route in the SuperPro Designer® simulator
The dl-methionine production process was simulated in SuperPro Designer®, in order to know the productivity and profitability values that a process of this type will have under current worldwide economic conditions. For that, the mass and energy balance tools and economic calculations that this simulator contains were used. First, a plant construction time of 18 months, a start-up period of 4 months, a project lifetime of 20 years were considered, while an interest rate of 11 % was chosen to determine the net present value (NPV) parameter [30].
It was also taken into account that the plant will operate at 70 % capacity for the first four years of operation, then at 90 %% capacity for the following four years, and at 100 % capacity for the rest of the years of operation. Likewise, an annual product failure rate of 5 % was applied, with a waste material disposal cost of USD $ 2.50/kg [25]. An income taxes value of 30 %% and an annual advertising and selling expenses of USD $ 3,000 were considered. To determine the direct fixed capital of the project, the direct costs (piping, instrumentation, insulation, electrical facilities, buildings, yard improvements and auxiliary facilities); the indirect costs (engineering and construction) and other costs (contractor's fee and contingency) were taken into account. Direct costs (DC) are estimated using a method that assigns percentages to the total equipment purchase cost (PC) for each category or cost factor [34], indirect costs (IC) are determined by assigning a percentage to the calculated CDs, while the other costs item is calculated by setting a percentage to the sum of direct costs and indirect costs (CD+IC). Table 4 shows the percentages assigned to each category or cost factor according to recommendations reported in Harrison et al. [25] and Peters et al. [27].
Table 4 Percentage assigned to the cost items to calculate the direct fixed capital.
Item | Multiplier |
---|---|
Direct Cost (DC) | |
Piping | 0.45 x PC |
Instrumentation | 0.25 x PC |
Insulation | 0.10 x PC |
Electrical facilities | 0.15 x PC |
Buildings | 0.60 x PC |
Yard Improvement | 0.15 x PC |
Auxiliary facilities | 0.65 x PC |
Unlisted equipment purchase cost | 0.40 x PC |
Indirect Cost (IC) | |
Engineering | 0.35 x DC |
Construction | 0.45 x DC |
Other Cost (OC) | |
Contractor's fee | 0.05 x (DC + IC) |
Contingency | 0.15 x (DC + IC) |
The working capital was projected to cover expenditures for 10 days of labor, raw materials, utilities and waste treatment; the startup and validation cost was appraised as 20 % of the direct fixed capital [35]; while the facility-dependent costs were estimated by selecting the capital investment parameters, including maintenance option. Laboratory, quality control and quality assurance costs were estimated as 25 % of the total labor cost, an additional electricity consumption of 150 kWh was chosen per batch, and an annual expense of USD $ 5,000 was considered for process validation. The expenses related to research and development operations were not taken into account in this study.
Table 5 describes the unit cost of the auxiliary services (utilities) used in the projected production plant, which were chosen according to values reported by Harrison et al. [25] and from recommendations by the simulator itself.
Table 5. Unit cost of utilities.
Utility | Unit Cost (USD $/MT) |
---|---|
Chilled water | 0.50 |
Cooling water | 0.10 |
Glycol | 0.80 |
Steam | 32.00 |
Finally, a labor wage of USD $ 3.0/h and USD $ 6.0/h was assigned for operators and supervisors, respectively; an electricity unit cost of USD $ 0.15/kWh was chosen [25]; about 240 production batches will be carried out per year selecting a cycle time slack of 12 h; while a unit selling price of USD $ 35/kg was chosen for the feed grade dl-methionine produced in this study. The annual production capacity of the proposed plant will be 109 tons of dl-methionine crystals.
Results and discussion
Figure 2 displays the process flow diagram for the dl-methionine production process by the chemical synthesis route obtained by means of SuperPro Designer®.
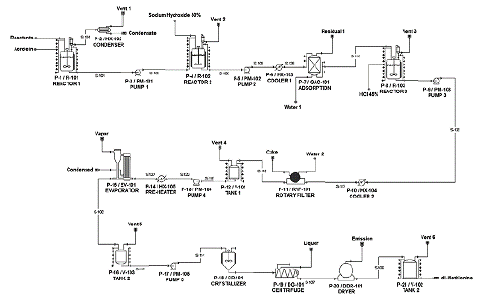
Figure 2 Process flow diagram of the dl-methionine production process created in SuperPro Designer®.
Techno-economic and profitability indicators
Table 6 shows the results of the key techno-economic and profitability indicators of the proposed dl-methionine production process, obtained by means of the simulation in SuperPro Designer®. According to Table 6, it is needed a total capital investment of USD $ 8.282 million which refers to the fixed costs that are related with a process, and is estimated as the sum of the direct fixed capital, working capital, startup and validation cost, up-front R&D cost y up-front royalties; while the direct fixed capital was of USD $ 6.838 million (represents the fixed resources of an investment, such as plant and equipment, and is determined as the sum of direct, indirect and miscellaneous costs that are related with the plant's capital investment).
Table 6 Results of the main techno-economic and profitability indicators.
Item | Value |
---|---|
Total capital investment (USD $) | 8,282,000 |
Direct Fixed Capital (USD $) | 6,838,000 |
Working capital (USD $) | 76,000 |
Startup Cost (USD $) | 1,368,000 |
Operating cost (USD $/year) | 1,323,000 |
Revenues (USD $/year) | 3,818,000 |
Unit production cost (USD $/kg) | 12.13 |
Gross margin (%) | 65.35 |
Net profit (USD $) | 1,747,000 |
Return on Investment (%) | 21.09 |
Payback Time (years) | 4.74 |
Internal Rate of Return (%) | 20.33 |
Net Present Value at 11.0% interest (USD $) | 4,436,000 |
Likewise, the working capital was of USD $ 76,000, which involves the costs required to start the operation of the plant and finance the first months or weeks, before profits from sales of the product begin, and includes investment in salary, raw materials, consumables, etc. Likewise, the startup and validation cost amounted USD $ 1.368 million, which comprises inaugural, one-time costs planned to make ready a new industrial facility for operation, while the operating cost was of USD $ 1.323 million (refer to all costs related to any productive activity that aims to offer a service or manufacture a product. They can be both fixed and variable, depending on the level of demand, and can be referred as the cost of raw materials, salaries, auxiliary services, among others). Similarly, the annual revenues due to the sale of the main output (or product) stream (dl-methionine) was of USD $ 3.818 million; while the unit production cost, which is the amount it costs a company to produce a product, and is calculated by dividing the total annual production cost by the total products produced in the same year, was of USD $ 12.13/kg, and can be considered in the range proposed by Harrison et al. [25] of USD $ 5 to USD $ 100/kg for specialty biochemical used as food supplements.
The gross margin, which is a financial indicator that represents the difference between the total revenue generated by sales and the cost of goods sold, that is, the amount of money that a company retains after subtracting the costs directly associated with the production and sale of its products or services, measured in percentage terms, was of 65.35 %%, while the Return on Investment (ROI) which refers to the profits or benefits obtained after making an investment, expressed as a percentage, and is used to analyze the performance of the company from a financial point of view, was of 21.09 %%, that is, a positive value, thus indicating that the profits or return on investment are greater than the expenses, and also demonstrates that the projected production process will be lucrative. The Payback Time (PT), which refers to the time (in years, months and days) that it takes for a business to recover the capital invested initially at present value, that is, the date on which the initial investment will be covered, thus allowing to determine whether a project is profitable or not, was of 4.74 years.
The Internal Rate of Return (IRR) had a value of 20.33 %>, which is the interest or profitability rate (expressed as a percentage) that an investment offers, as well as the percentage of profit or loss that any investment entails. It is defined as the discount rate that equates, at the initial moment, future collections with payments, generating an NPV equal to zero. The higher its value, the greater the profitability of the project. Finally, the NPV was of USD $ 4.436 million, which is an investment criterion that consists of updating the collections and payments of a project or investment to know how much will be gained or lost with that investment. It is a financial tool used to evaluate the profitability of an investment or project. This indicator calculates the present value of all future cash flows (both income and expenses) related to the investment, discounted at a specific interest rate. If the value of NPV is positive, the project will generate profits, while if its value is negative, the investment project will generate losses, so it must be rejected. Taking into account that the NPV for this project has a positive value, the IRR is greater than 20 % and the PT is less than 5 years, the dl-methionine production process simulated in this study can be defined as profitable and feasible from the economic and financial points of view [27,30]. In another study [17], the estimated capital investment of a dl-methionine plant with a production capacity of 150,000 t/year (which is about 1,370 times greater than the production capacity of the dl-methionine production plant simulated in this study) to be erected in the U.S Gulf Coast was of USD $ 390 million, with operating expenses of about USD $ 2,600 per ton of product. It's worth stating that in this study, the dl-methionine production plant is integrated with 3-methylthiopropionaldehyde and hydrogen cyanide facilities; the storage self-sufficiency is equal to 30 days of operation of methionine, aqueous ammonia and liquefied carbon dioxide; and the dl-methionine is obtained via the carbonate process analogous to that established by Evonik Industries AG, with four production areas: hydantoin production; hydantoin hydrolysis; dl-methionine production and filtration; and final drying.
Direct fixed capital
The fixed capital investment is the amount of money necessary to completely build a process plant, with its auxiliary services, and place it in a position to start producing. It is basically the sum of the value of all the assets of the plant. The fixed capital investment is important in increasing the value of a chemical process since this metric is employed in calculating operating costs and estimating depreciation, cash flow, and project profitability.
The Table 7 shows a breakdown of the items included in the estimation of the direct fixed capital of the production process simulated in this study.
Table 7 Direct fixed capital estimate summary of the process simulated in this study.
Item | Value (USD $) |
---|---|
Total Plan Direct Cost (TPDC) | |
Equipment purchase cost | 833,000 |
Installation | 374,000 |
Process piping | 375,000 |
Instrumentation | 208,000 |
Insulation | 83,000 |
Electrical | 125,000 |
Buildings | 500,000 |
Yard Improvement | 125,000 |
Auxiliary Facilities | 542,000 |
TPDC | 3,165,000 |
Total Plan Indirect Cost (TPIC) | |
Engineering | 1,108,000 |
Construction | 1,425,000 |
TPIC | 2,533,000 |
Total Plant Cost (TPC) = TPDC + TPIC | 5,698,000 |
Contractor’s Fee and Contingency (CFC) | |
Contractor’s Fee | 285,000 |
Contingency | 855,000 |
Total CFC | 1,140,000 |
Direct Fixed Capital (DFC) =TPC + CFC | 6,838,000 |
For the dl-methionine production plant simulated in this study, the total equipment cost was anticipated to be USD $ 833,000, while the installation, piping, instrumentation and insulation costs were USD $ 374,000, USD $ 375,000, USD $ 208,000 and USD $ 83,000, respectively. Also, the electrical and buildings items had costs of USD $ 125,000 and USD $ 500,000, respectively. Lastly, the yard improvement and auxiliary facilities costs amounted USD $ 125,000 and USD $ 542,000, respectively. The projected total plant direct cost (TPDC) was USD $ 3,165,000, the total plant indirect cost (TPIC) was of USD $ 2,533,000, including USD $ 1,108,000 for engineering and USD $ 1,425,000 for construction, while the total plant cost (TPC), which is the sum of TPDC and TPIC, reached a value of USD $ 5,698,000. The contractor's fee and contingency costs were USD $ 285,000 and USD $ 855,000, respectively, and the direct fixed capital for the proposed plant was USD $ 6,838,000. The cost item that influences the most in the TPDC was equipment purchase cost, with 26.32 %, due to it comprises the total cost of all the main equipment included in the simulated process flowsheet (USD $ 502,000, see Table 3) plus the unlisted equipment purchase cost (USD $ 331,000, value not shown) which account for the purchase cost of other (overlooked) equipment (i.e. pumps, tanks, vessels, heat exchangers, etc.) that are not included explicitly in the main process flowsheet. Auxiliary facilities is the second significant cost item with 17.12 %% since it includes the cost of the facilities to provide the auxiliary services to the plant such as steam, water, chilled/cooling water, energy, compressed air, fuel, etc. [30]. The third item with the largest influence was buildings (15.80 %) since it covers the cost of offices, workshops, laboratories, warehouses, control rooms, cafeteria, etc., including labor, materials, plumbing, lighting, heating, ventilation, etc. Finally, the process piping constituted the fourth largest cost item (11.84 %), because it incorporates the cost of valves, pipes, supports, steam traps, insulation, among others elements associated to equipment piping.
Since this is a plant that will handle fluids both in liquid and vapor states, including slurries and suspensions, the amount of piping required to transport these fluids among the equipment, and also to transport the utilities that cool or heat the fluids in equipment such as the reactors, crystallizer, heat exchangers, among others, should be relatively high. Because it is considered a grass-rooted, small-scale plant, the costs for auxiliary facilities, piping and buildings are considered reasonably high. The capital cost estimation performed in this study classifies as "Class 4" estimate, also known as study estimate or factored estimated according to the classification established by Sinnott et al. [30]. This type of estimate uses a list of the most important equipment used in the process, that is, pumps, compressors, turbines, columns, heat exchangers, tanks, reactors and boilers. An approximate sizing is made to calculate the cost of the aforementioned equipment and the investment capital is estimated using percentages based on those costs. A process flow diagram is needed and the estimate has an accuracy of between -25 % and +30 % [33]. The capital cost result obtained in this type of estimate is important, since it provides valuable information to choose whether the project can be continued or not, in order to carry out more accurate and precise capital cost estimates.
Operating cost
The production plant conceptually designed in this study will produce about 478 kg of feed grade dl-methionine per batch with a purity of 99.87 %, and will carry out 240 batches per year, which is equivalent to produce about 109 t/year of dl-methionine after discounting the 5 % of the product failure rate. The operating cost is defined as the expenses necessary to maintain a certain chemical plant under operation, and includes the cost of raw materials, utilities, labor, waste disposal and other facility expenditures.
Table 8 presents the breakdown of the different cost items included in the annual operating cost, together with their percentage contribution.
Table 8 Cost items included in the annual operating cost, and their percentage contribution.
Cost item | Cost (USD/year) | % |
---|---|---|
Raw materials | 1,113,000 | 84.11 |
Labor-dependent | 89,000 | 6.76 |
Facility-dependent | 53,000 | 3.97 |
Laboratory/QC/QA | 22,000 | 1.69 |
Utilities | 24,000 | 1.78 |
Miscellaneous | 5,000 | 0.38 |
Advertising/Selling | 3,000 | 0.23 |
Failed product disposal | 14,000 | 1.08 |
TOTAL | 1,323,000 | 100.00 |
The item that most contributes to the annual operating cost is raw materials, with USD $ 1,113 million (84.11 %), which is due to the relatively high consumption of the different raw materials that are consumed directly to produce the desired final product in the proposed production process, fundamentally methyl mercaptan (USD $ 684,000, see Table 9) and acrolein (USD $ 187,920). The percentage value calculated in this study is above the range proposed by Harrison et al. [25] of 1080 °%, which could be due to the relatively high unit cost and consumption of some raw materials, particularly hydrogen cyanide and methyl mercaptan. The second most important cost item was labor dependent, with USD $ 89,000 (6.76 °%), which is related to the relatively high amount of operating labor required to control, operate and supervise the production process, mostly because the hazardous chemicals handled as raw materials in the process, which need special attention and care to avoid spills, escapes and leaks that could lead to fatal accidents. It should be mentioned that the labor-dependent costs calculated in this study are below the range suggested by Harrison et al. [25] of 10-50 %.
Table 9 Cost items involved in the materials cost and their percentage influence.
Raw material | Annual Amount | Units | Annual cost (USD $) | % |
---|---|---|---|---|
Acrolein | 72,000 | kg | 187,920 | 16.89 |
Ammonium carbonate | 240 | MT | 87,600 | 7.87 |
Hydrochloric acid (45%) | 96,000 | kg | 5,669 | 0.51 |
Hydrogen cyanide | 40 | t | 99,883 | 8.98 |
Methanol | 11 | t | 5,545 | 0.50 |
Methyl mercaptan | 45,600 | kg | 684,000 | 61.47 |
NaoH (50%) | 144 | MT | 41,760 | 3.75 |
Water | 378,065 | kg | 378 | 0.03 |
TOTAL | 1,112,755 | 100.00 |
The facility dependent cost was the third higher cost item, with USD $ 53,000 (3.97 %), which is due to the high maintenance and depreciation costs that will be involved in the production process. In the case of new, grass-rooted/green-field plants, where no previous knowledge on the use of equipment exists, this is considered as the sum of the costs associated with equipment maintenance, depreciation of the fixed capital cost, and miscellaneous costs. Still, the percentage value calculated in this study for this item is below the value reported by Harrison et al. [25] of 10-70 %>. Finally, the cost of the items laboratory/QC/QA, utilities, miscellaneous, advertising/selling and failed product disposal were of USD $ 22,000, USD $ 24,000, USD $ 5,000, USD $ 3,000 and USD $ 14,000, respectively.
Materials cost
In SuperPro Designer®, the annual cost of each raw material is calculated by multiplying the corresponding unit cost (i.e., purchasing price) by the equivalent annual amount that is consumed in the production process. In this case, the user specifies the unit costs of materials, whereas the corresponding annual amounts are calculated by the program as part of the simulation. Table 9 describes the annual amount consumed by each raw material, their annual cost and the percentage contribution to the annual cost for the simulated dl-methionine production process. The item that has the largest influence to the materials cost is methyl mercaptan, with 61.47 °%, mainly because it's the raw material with the highest unit cost (USD $ 15.00/kg). In second place comes acrolein (16.89 %) because it's the raw material with the fifth highest annual consumption (72,000 kg) and the second highest unit cost (USD $ 2.61/kg), while in third place is the ammonium carbonate with 7.87 % primarily because it's the raw material with the second highest annual consumption (240 MT).
It's worth mentioning that a high number of the raw materials consumed in this production process are considered hazardous and harmful to humans. For example, the acrolein is a clear, yellowish liquid which is highly flammable and toxic; the hydrogen cyanide is a colorless to pale blue liquid below 26 °C, and a colorless gas at higher temperatures, which is highly flammable and can produce symptoms such as flushing of the face, tightness in the chest, headache, nausea, vomiting, weakness, confusion, pounding heartbeat, and difficulty breathing, and quickly lead to seizures and even death; the methyl mercaptan is a flammable gas at ambient temperatures that is extremely irritant when it contacts eyes, skin and upper respiratory tract. It can also induce headache, dizziness, nausea, vomiting, coma and death. The hydrochloric acid is highly corrosive and irritant. Due to these hazardous properties, special, meticulous and rigorous care must be taken into account when handling, transporting and processing these chemicals throughout the proposed dl-methionine production process.
Risk analysis and potential mitigation to make the dl-methionine production process by the chemical synthesis route sustainable
One of the main objectives of increasing the cost sustainability of industries is to reduce the environmental impact of production operations while maintaining or improving their economic profitability. However, industries confront different challenges and opportunities in terms of cost structure, market demand, regulatory framework and social expectations. Among the main challenges that exist to maintain and improve cost sustainability in industries are the following [36]:
Energy and resource consumption: One of the main sources of environmental impact and operating cost is the amount and type of energy and resources used by the industries. Depending on the industry, this can include electricity, fuel, water, raw materials, chemicals, packaging, etc. Reducing energy and resource consumption can help industries reduce their carbon footprint, waste generation and operating expenses. However, this may require investing in more efficient technologies, processes and equipment, which can have upfront costs and long payback periods. In addition, some industries may have limited access to renewable or low-carbon energy sources, or face high prices or volatility in energy and resource markets.
Regulatory compliance: Another challenge of cost sustainability is complying with environmental and social regulations and standards that apply to different industries. These may include emission limits, waste management, health and safety, labor rights, human rights, etc. Compliance with these regulations and standards can help industries avoid fines, penalties, lawsuits and reputational damage, as well as meet the expectations of their customers and stakeholders. However, compliance can also involve significant costs and administrative burdens, especially for companies that operate in multiple jurisdictions or have complex supply chains.
Innovation: Alast but not least cost sustainability challenge is to innovate and differentiate in a competitive and dynamic marketplace. Industries that want to achieve sustainability of their economic results and production processes need to constantly improve their products, services, processes and business models, as well as communicate their value proposition and sustainability credentials to their customers and stakeholders. Innovation and differentiation can help industries create competitive advantages, increase customer loyalty and capture new market opportunities. However, innovation and differentiation can also involve significant costs and risks, such as research and development, marketing, intellectual property, etc.
In today's industrial environment, sustainable management of its economics and productivity poses several challenges that need to be addressed. One of the key challenges is the increasing costs associated with various aspects of the production process. This includes expenses related to labor, raw materials, equipment and overhead costs. Industries must And ways to effectively manage and control these expenses to ensure the sustainability of their production processes, and thus ensure efficient and optimal management, maintenance and operation of the industrial plant once erected. From the perspective of financial and productive sustainability, industries must achieve a balance between reducing costs and maintaining the quality of their products or services. Indiscriminant cost-cutting can compromise the quality of the final product, which can negatively affect customer satisfaction and ultimately damage the reputation and profitability of the production process [36]. Among the main general strategies to be considered and implemented in the dl-methionine production process proposed in this study, in order to meet these sustainability challenges are:
Implementation of Lean principles: Lean principles focus on eliminating waste and optimizing production and waste treatment processes to reduce costs. By recognizing and eliminating activities that do not add value, the production process can optimize its operations and improve cost efficiency.
Strategic sourcing: Strategic sourcing options can be explored to categorize cost-effective suppliers and negotiate favorable contracts. This can help decrease procurement costs and guarantee viability of quality inputs at competitive prices.
Process automation: Automating manual and repetitive tasks can generate cost savings for industry by reducing labor costs and improving operational efficiency. Industry can take advantage of technologies such as robotic process automation to automate routine tasks and free up resources for higher value-added activities.
Value engineering: Value engineering involves analyzing the purposes of a product or service and identifying opportunities to reduce costs without compromising quality. By re-evaluating design choices, materials and production processes, cost-saving alternatives can be identified.
Cost tracking and analysis: The implementation of stable and efficient cost analysis and tracking systems will enable the industry to monitor expenditures, identify cost overruns and take corrective actions in an opportune manner. This helps to maintain cost control and prevent major budget slippages.
Invest in renewable energy: Investing in renewable energy is another strategy the plant can adopt to become more sustainable. This may include installing solar panels or wind turbines, or purchasing renewable energy credits. By investing in renewable energy, the industry can reduce its dependence on fossil fuels and decrease its carbon footprint. This can also help improve its reputation and attract customers looking for environmentally responsible companies.
Implementation of sustainable packaging practices. A sustainable packaging practice is another area where the plant can focus its sustainability efforts. This can include using biodegradable or recyclable materials, reducing packaging waste, and implementing sustainable packaging designs. By implementing sustainable packaging practices, the plant can reduce its environmental impact and enhance its reputation as a socially responsible industry.
Create a sustainability plan: The industry can create a sustainability plan to guide its sustainability efforts. This plan should comprise specific goals and objectives, as well as strategies to achieve those goals. By creating a sustainability plan, the plant can ensure that its sustainability efforts are focused and effective. This can also help improve its reputation and attract customers who are looking for socially responsible companies.
It is important to mention that these strategies for increasing productive and financial sustainability must be adapted and tailored to the specific needs and context of each industry. By adopting a proactive attitude to the sustainability of their financial and production management, industries can meet the challenges and tasks and thus ensure the long term viability of their production processes.
The chemical plant simulated and proposed in this study must take into account that external factors such as market fluctuations, regulatory changes and technological advances resulting from innovation, can considerably affect the sustainability of its cost management, its productivity and therefore its profitability. The dl-methionine production plant must remain agile and adapt its cost management strategies to respond efficiently to these external factors.
Conclusions
In the present work a proposed dl-methionine production process via the chemical synthesis was successfully simulated in SuperPro Designer®, with the purpose of determine its key techno-economic and profitability indicators. The simulated plant will produce about 478 kg of feed grade dl-methionine per batch (109 t/year) with a purity of 99.87 %. A total capital investment of USD $ 8.282 million is needed to build the proposed plant, with an annual operating cost of USD $ 1.323 million and annual revenues of USD $ 3.818 million. The cost item with the main contribution to the annual operating cost was raw materials with 84.11 %, while the item that influences the most in the materials cost was methyl mercaptan with 61.47 %%. It was shown that, with a dl-methionine unit selling price of USD $ 35/kg, the plant is feasible and profitable due to the values obtained of the indicators NPV (USD $ 4.436 million), IRR (20.33 %%) and PT (4.74 years). The results of this study demonstrate that simulation tools are valuable to assess, from the techno-economic point of view, the industrial production of feed grade dl-methionine. An innovative cost model was developed for the economic analysis of a proposed dl-methionine production process via the chemical synthesis, which can be further optimized to improve its throughput and economic viability.