Introduction
The rapid progress of concrete technology in recent years has meant a major evolution in civil engineering, especially in the development of new types of concrete and mortars (C. Meyer, 2009). This development is evident with the appearance of new additives and reinforcing fibers that will meet the demands of today's civil engineers whilst making it more and more possible to use environment friendly materials. (Hansen T., 2004; Torres Castellanos & Torres Agredo, 2010).
One of these products used as binders in the manufacture of mortar is glass powder from glass wastes that cannot be reused because they are contaminated with papers, cork, and other substances, or from the frits from cleaning mills in the ceramic industries (Marco, 2012; Tung-Chai Linga, 2012; Tung-Chai Ling a, 2017). The use of these types of additives for the manufacture of mortars fulfills the criteria of sustainability that is demanded by society today (Atienza, 2010). This decreases the amount of cement used, thus contributing to the reduction of greenhouse gas emissions, (Marco, 2012; Mas-López M. I., 2016; Tagnit-Hamou, 2016) and also decreases the area used as landfills (Mas-López M. I., 2016; N. A. Soliman, 2016; C. Pade, 2017). Just in Spain, about 1,5 million tons of waste glass are generated annually, of which 75% is recycled and the rest, about 300 000 tons, are deposited in landfills (Ecovidrio, 2018).
Due to the positive environmental impact on the use of waste glass, many studies were carried out on the properties of waste glass used as a binder confers on mortars and cements (Y. Jani, 2014). Such studies carried out in the middle of the 20th century showed that cement made with aggregates from glass powder (R. G. Pike D. H., 1957; R.G. Pike D. H., 1960; Johnston, 1974) cracked more easily than traditional cements due to alkali-silica reactions. More recently authors such as R. Idir M. C.-H. (2011), V. Corinaldes (2005) and R. Idir M. C.-H. (2010), H. Rashidian-Dezfouli, (2017) and A.Prghi (2016) have concluded that this problem can be corrected by decreasing the size of the particles of the glass powder used as an aggregate.
To verify whether these additives are viable, one of the key factors is to verify that they meet the demands of compressive strength (Mohammadreza Mirzahosseini, 2015; M. Z. Guo, 2015; J. Chen, 2009). To know how the resistance of mortar will evolve it is important to know what the setting process consists of, what are the chemical compounds responsible for this setting and its evolution over time (G. Vijayakumar, 2013). The basic components that determine the setting process are the C-S-H gels. The kinetics of their formation and the abundance of these gels will depend, to a great extent, on the evolution of resistance over time, both for conventional mortars and those made with different conglomerates.
Hydrated calcium silicate gel (C-S-H) is the most important product of the hydration of cementitious materials, and is responsible for their setting process. With a complex nano-porous structure and a very high surface area, the C-S-H gel has a great capacity to form bonds per unit surface area and is therefore mainly responsible for the mechanical properties of cement-based materials (S. Goni, 2011).
Hydrated cement pastes consist essentially of a set of crystalline phases, (portlandite, ettringite, hydrated calcium monosulfoaluminate), by anhydrous cement grains and mainly by a hydrated calcium silicate, of quasi-amorphous nature: that is the CSH gel mentioned in the previous paragraph.
In previous studies by Marco et al. (2012) compression strengths obtained in mortars made with glass powder with different granulometries and different proportions of glass powder and it was found that the best results of compression resistance were obtained for mortars made with glass powder of 16 μ and with a percentage of glass powder of 80% in the composition of the binder. This is in the range of dimensions accepted by other authors as optimal for its use as a binder in the production of cement and concrete (Y. Jani, 2014). It was also found in this study that mortars made with glass powder presented suitable conditions to be used in the stabilization of soils, due to their resistant characteristics and self-repairing properties when faced with small fissures or differential landings. These properties of self-repairing, were produced due to the prolonged time of the reactions in setting, produced by new formations that occur in the form of gels similar to C-S-H.
For the observation and study of new formations, different mortars were made with part of the cement replaced by ground glass powder with different diameter and in different proportions. Two types of analysis were performed: X-ray diffraction analysis and Scanning Electron Microscope (SEM) coupled to the Dispersive Energy Spectrograph (EDS).
Materials and methods
The materials used to carry out the tests had the following characteristics.
Materials
Cement
The glass powder used comes from the cleaning of mills from the ceramic industry (frits) and packaging from the selective collection of garbage that due to its characteristics (high percentage of paper, cork or plastic adhered to it ...) cannot be reused. They were ground in a bar mill equipped with 15 bars of 3 different diameters and for different grinding times. The granulometry of the glass powder was established for three characteristic diameters of d10, d50, d90, which constitute the dimension of the particles of the sample for which 10%, 50% and 90% had a diameter less than that value. Table 3 shows the granulometric characteristics of the glass powder as a function of the grinding time.
Table 3 Granulometric characterization of the glass powder as a function of the grinding duration (our own preparation)
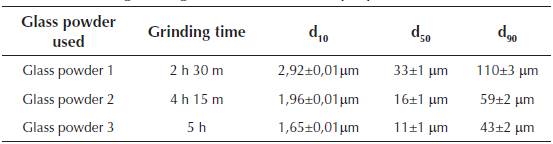
Source: Authors
During the test, glass powder batches of d50 value were used, because according to Marco L. J. et al. (2012) (Marco, 2012; Marco et al., 2012), the relationship of grinding time with the diameter of the particles represents the optimum economic profitability and sustainability. The chemical composition of the glass powder residues used in the milling is shown in Table 4.
Research Plan
Collecting the samples of glass residues and then grounding the glass until reaching the desired particle diameter. The mortar was prepared, according to standard (Comité Técnico AEN/CTN 80, 2011) UNE-EN 196-1, with sand and binder in a 2,75: 1 ratio and a water / binder ratio of 0,52, and paste with the same water / binder ratio.
To verify that the sand used did not affect in any way the setting phenomenon, some mortar specimens were prepared by replacing the sand with a lime type material with similar granulometric characteristics. In previous studies by Marco et al., (2012) the authors found that the resistances for the mortars made from the two materials are very similar, so, the hypothesis of the influence of the mortar sand is discarded as the agent responsible for the setting phenomenon.
To study the products responsible for setting and their influence on resistance, standard mortars and pastes were made with two different dosages. The first group of analysis was made for pastes and mortars with the following composition: 80% glass powder, 18% lime and 2% potash (henceforth group 1). The composition of the second group was: 80% glass powder, 20% CEM 152.5 R (henceforth group 2).
Once the paste and mortar were made, two types of analysis were carried out: X-ray diffraction analysis and scanning electron microscope analysis coupled to the Dispersive Energy Spectrograph.
Analysis and discussion
X-ray diffraction analysis
The first step of the study was to test the products responsible for getting the resistance to compression of different samples of mortars and pastes using X-ray diffraction. The analysis carried out on the pastes enabled us to obtain all the information about the gels formed in them while for the mortars we only had information on the characteristic peaks of the sand quartz. Hence, in this section we only use the results obtained for the pastes.
First we analyzed the samples with the composition identified in group 1. Figure 1 shows the graph corresponding to the analysis of the samples of group 1, after 19 days of preservation in an endogenous medium in a humid chamber at a temperature of 20 °C ± 3 and a relative humidity > 95%. The dotted line represents the bulge generated by the presence of amorphous phases. The characteristic peaks of CaCo3 calcite due to the carbonation of the lime in the air and the portlandite Ca(OH)2 from the hydration of lime can be seen, but no other crystallized hydrate can be observed.
The analysis of the X-ray diffractogram of group 2 of samples reveals the presence of amorphous phases, as in the samples from group 1.
In the analyzed samples of paste, again, we found the characteristic hump of the glass as well as all the characteristic peaks of the main constituents of the cement:
The tricalcium silicate: 3CaOSiO2 (C3S)
The dicalcium silicate: 2CaOSiO2 (C2S)
The tricalcium alumínate: 3CaOAl2O3 (C3A)
In addition, we observed the presence of quartz, (SiO2), that is found in the cement. Hydration of these powders forms a paste that eventually hardens. In the X-ray diffractogram shown in Figure 3, of the paste from group 2 measured at different times of aging (3 hours, 7 days and 28 days), we can observe the representative glass peak, including that of calcite and portlandite. In addition, the analysis shows the presence of ettringite and other calcium, silicon and aluminum hydrates. Also, we can see from the dotted lines the bulge of the baseline that shows the presence of amorphous phases.
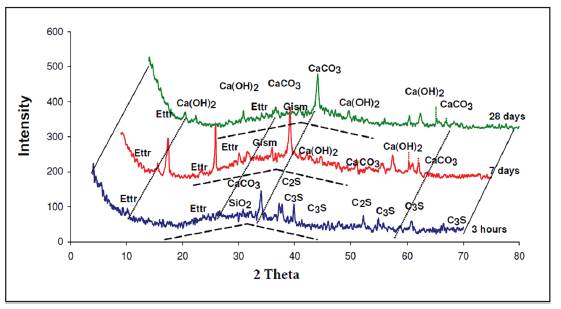
Source: Authors
Figure 3 X-ray diffractogram of paste group 2 different time points preserved in endogenous medium.
We observed that lime was consumed at the beginning of the hydration reaction and that there was a self-sustaining reaction.
Table 5 Compounds detected by X-ray diffractogram of the paste group 2 studied at different times
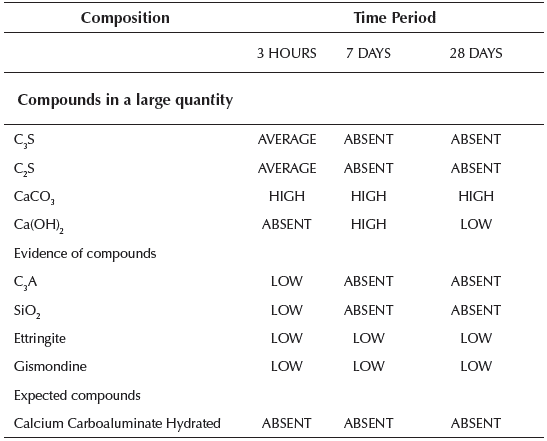
Source: Authors
Once the paste is hydrated in the early hours, we could observe the presence of anhydrous compounds of the C3S and C2S cement. The presence of calcite CaCO3 was also verified that is formed quickly at the moment of hydration from cement and ettringite.
After 7 days from hydration, the calcite always appears in larger quantities and the ettringite to a lesser extent. But no anhydrous cement compounds were present. The diffractogram reveals the presence of hydrated lime Ca(OH)2 in considerable amount, gismondine more faintly and Absent presence of hydrated calcium carboaluminate because the presence of this compound usually appears at older ages.
At 28 days, the characteristic peaks of calcite and ettringite continue to appear, similar to those detected at 7 days. In contrast, the peaks of hydrated lime are much less pronounced. This fact indicates that lime was intensely consumed during the hydration reaction, which means that, in addition to the pozzolanic reactions, there are other similar reactions that consume lime which explains the growth of the mechanical resistances in the long term.
In order to analyze the amorphous phases that are not evident in the above diffractograms, a scanning electron microscope analysis was carried out coupled to the Dispersive Energy Spectrograph (EDS), which analyzes the same pastes and mortars as those analyzed by X-ray diffraction. Samples for the SEM were prepared using the classic method of chemical fixation, dehydration and critical point drying. The coating to make the sample conductive was made with a carbon wire coating. The observed parts of each sample are sections from the fracture planes.
As in the previous analysis, we proceeded to study pastes and mortars group 1. The results obtained for the pastes (preserved in endogenous medium and observed for a period of 47 days) are shown in Figures 4 and 5.
Figures 4 and 5 show respectively different sized glass grains integrated in the paste, as well as the new formations that appear after the hydration of the pastes. The observed particle size ranged from lμ to 100μ. It is also appreciated that the pastes were constituted by particles of glass and by new formations that appear in the form of gels. These have a little closed surface and do not have preferential orientation in space.
Figure 6 shows the analysis performed on a glass bead by Dispersive Energy Spectrography, where the chemical composition of the existing glass can be seen: Silicon, Sodium and Calcium.
Figure 7 shows the composition of new formations. In this graph, it is clearly noticed that the presence of calcium is much more significant than in the observations made for the glass grains.
Standard Mortar Observations
Figures 8, 9 and 10 show photographs taken from SEM images of standard mortars whose composition corresponds to group1, preserved in endogenous medium and observed after curing 67 days.
Figure 8 shows the siliceous aggregates within the paste. Figure 9 shows an enlargement of the trace left by the aggregate in the structure, and indicates that the paste appears rather porous and poorly sealed. Figure 10 shows the paste-arid interface and the cohesion that exists between both as well as the continuity between the new formations that appear in the paste and the aggregates. It is also observed that the new formations appear well adhered to the surface of the aggregate, otherwise the observed fracture plane would follow the surface of the aggregate.
Observations of pastes and mortars from group 2
Pastes
Figure 11 shows the graph of the compounds obtained by the Dispersive Energy Spectroscopy analysis of the paste group 2.
Figures 12 to 14 show the photographs obtained from the SEM of paste with a composition of group 2 that were observed for 180 days and preserved in an endogenous medium. It can be seen that these pastes are basically constituted by glass particles of varying sizes and new formations. In the photograph corresponding to figure 13 it can be seen how the new formations adhere to the surface of the glass particles. In Figure 14, one can observe phenomena similar to the face of dissolution of some glass particles.
Figure 14 is a photograph obtained by SEM of a paste with a composition group 2 preserved and observed for 65 days. In these figures it can be seen that the paste is always formed by glass particles and new formations in the form of a gel. However, they appear somewhat different from those observed for pastes with the above composition, but appear in more fibrous forms Figures 15 to 17, shown below are the photographs obtained by SEM of standard mortars with a binder from group 2 preserved in an endogenous medium (observed within 180 days).
Standard mortars
In Figure 15 it can be seen that the existing paste in the tracks of the aggregates is quite well closed, indicating a good cohesion between both. Figure 16 focuses on the study of paste-aggregate interfaces. A good cohesion of the mortar can also be appreciated, as the paste seems well joined to the aggregate mass and the new formations also appear to be attached to the surface of the mortar. Also detected in these mortars are some crystals of calcium carbonate and ettringite in very small quantity.
The pastes that were analyzed by SEM coupled to the EDS had a structure very similar to the C-S-H gels. But unlike these gels, the pastes analyzed here had a Ca / Si ratio close to 1, whereas in the classic C-S-H this ratio is 2,7.
Conclusions
The analysis carried out throughout the study reveal the presence of new gel-like formations similar to the C-S-H of conventional mortars. They differ from these in the Ca / Si ratio, while for conventional C-S-Hs this ratio is 2,7, for these new formations it is 1. This indicates that they are much richer silicon gels. This greater amount of silicon causes the setting reactions to be prolonged over time and that the optimum of the mechanical resistances is obtained in a longer period of time than would be achieved with conventional mortars.
The new gels tend to form preferentially in the fissures because it is in these spaces, where the accumulation of water is greater, which consequently causes an increase in the concentration of the chemical elements that can precipitate and form structures of the type CSH. This preference in the formation of gels, gives to this type of mortars certain characteristics of auto-repairing before the appearance of small fissures.
The shape of these new compounds depends on the medium in which the pastes or mortars in which they are generated are preserved. If they are preserved in an endogenous medium they appear as amorphous formations, whereas if they are preserved in humid environment they acquire a fibrous form. These fibrous structures are responsible for the self-repairing of mortars made of glass powder.
The application of the new compounds in civil engineering are various, and their particular capacity of self-repairing and the longer time they take to reach their final resistance, makes them suitable for the stabilization of grounds.