1. Introduction
Methanol is an important fuel and promising energy vector, since it has an octane number of 113 and its energy density is near half of the gasoline (by volume); blends of 10%/90% methanol/gasoline can lead to an octane level up to 130 and pure methanol engines can reach efficiency close to 43% )[1]. Besides, it is an essential input for biodiesel production, participating with about 10% to 15% of the total raw materials used in the production of this biofuel[2, 3], and is a precursor for many other high-value chemical compounds, generally and industrially used, like formaldehyde, methyl-tert-butyl ether (MTBE, 20%), acetic acid and dimethyl ether[1, 4-7].Therefore, the production and use of this alcohol can be a way to reduce the fossil fuels dependence, because it could be used directly as a fuel or in fuel engine blends, with low NOx and SOx emissions, chemical energy carrier and as an input to produce synthetic fuels[1, 4, 5, 8] and omit partially or totally the use of non-renewable resources, in terms of the human time scale, because their quantities are finite, they fluctuate in prices, their use promotes global warming and damage to the environment, so it is necessary to obtain high added value products to base the economy and consumption patterns on more sustainable activities[1, 9-11].
This article aims to simulate the catalytic conversion of SYNGAS into methanol in a packed-bed reactor. The SYNGAS gas could be obtained from the gasification of renewable sources, derived from agro-industrial residues, municipal organic waste, among others [12, 13]. Also, the SYNGAS is a useful and sustainable raw material to produce fuels, chemical commodities (urea, methanol, dimethyl ether, etc.), heat and electricity, depending on the conversion route and physicochemical treatment selected[2] [4-7] [14-16].
2. Methodology
2.1 Technology and process selected to produce methanol
The processes conventionally used to produce methanol are carried out in fixed-bed multi-tubular reactors with a CuO-ZnO-Al2O3 catalyst in the form of pellets and operating in the gas phase[7, 15, 17]. The catalyst CuO-ZnO-Al2O3 is adopted, since it is the most used on an industrial scale, it allows working in a low pressure range, it has a high selectivity for methanol production, and it reaches an excellent level of CO2 conversion[1, 8, 18].
This heterogeneous process is highly exothermic[18,19]. Therefore, a cooling system must be implemented, since high temperatures affect life usefulness of the catalyst bed, due to the deactivation by thermal sintering[20]. The standard technologies used in methanol synthesis are shown in Table 1.
At the industrial scale, the Lurgi-type reactor is well-known, which functions as a kind of tube and shell exchange, where the CuO-ZnO-Al2O3 catalyst is packed in the tubes and on the shell side, it is made circulating the cooling water[13, 19]. This configuration of catalyst packaged inside a tubular reactor is used because the process can be more controlled[21, 22], with higher conversions by catalyst weight, and ensure efficient removal of heat[1]. Besides, in this type of reactor the H2: CO ratio in the fed SYNGAS should be as close as 2, to maximize efficiency and yield in methanol production[14], the operating temperature should not exceed the 570 K[22], to avoid the catalyst deactivation for sintering or aging processes, which are present at high temperatures[23]. However, some studies report loss of activity starting at the range between 463.15 and 500.15 K, and becoming more rapid and severe at temperatures between 543.15 and 573.15 K[1]. This deactivation process causes the surface area loss of the catalyst and reduction of its support area[1, 23].
Concerning pressure, this should be as high as possible, to counteract the decrease in the moles of the system by chemical equilibrium[22]. However, it should be noted, that with a high system pressure, the reactor manufacturing cost, and the energy required for SYNGAS compression are increased[23-25].
2.2 Raw material: SYNGAS
SYNGAS is a gaseous mixture obtained by gasification of carbonaceous material, such as biomass or coal. The process for SYNGAS production is called gasification, which consists in the conversion of these materials at moderate pressures and high temperatures, between 973.15 and 1473.15 K, in the presence of a gasifying or oxidizing agent, usually air, steam, or a mixture of them[26-29]. However, the quality, composition, calorific value, among other characteristics, depend on the physical and chemical properties of the biomass[30]. The characteristics of SYNGAS are shown in Table 2 and Table 3, for different types of agro-industrial biomass waste.
Table 2 SYNGAS composition (Wet basis in % Vol.) from Colombian agro-industrial flower waste at 1,123 K for different gasifying agents[28].

Table 3 SYNGAS composition (% Vol.) from Colombian agro-industrial waste at 1123 K for several values of steam/biomass ratio[31]
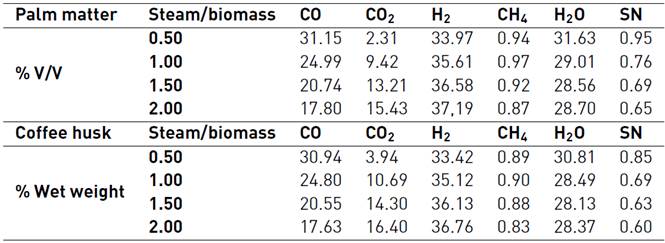
2.3 Math model and process simulation
The simulation of a Lurgi tube reactor operating in steady state condition is discussed. Besides, the following considerations and simplifications proposed by[18, 23, 24] are considered for this type of operation and reactor:
• Negligible radial diffusion: concentration and temperature profiles are assumed as constants, which leads to a one-dimensional model.
• Constant radial speed.
• Temperature and pressure profiles in the catalyst are assumed as constants (homogeneous catalytic particle).
• Secondary reactions are neglected due to the high selectivity of the catalyst.
The chemical kinetics used to model the methanol production process is proposed by Vanden[17], since it is the only one that considers the heterogeneous processes associated with the CuO-ZnO-Al2O3 catalyst, as noted in the comparative table of the different catalysts and chemical kinetics illustrated in[20]. Then, in equations (1) and (2), the chemical reactions involved in the process are shown.
Although the Lurgi technology admits pressures ranging from 50 to 100 bar, in[17] the model was developed to operate between 15 and 51 bar, and concerning temperature, this model allows working in a range between 453 and 552 K[16]. However, it has been decided to work at the maximum pressure allowed by the model, since it favors the chemical equilibrium towards the formation of methanol. Also, a 523 temperature K is used, because it is a common condition for this type of system[14] and it has been reported that catalyst deactivation occurs at temperatures above 550 K[18]. The chemical kinetics to produce methanol from catalytic conversion of SYNGAS, are illustrated in equations (3), (4), and (5). Additionally, the equations (5) and (6) are used to define the parameters
of kinetic expressions, the equations (7) and (8) denote the kinetic constants, and equations (9), (10), and (11) are the equilibrium constants involved in the methanol synthesis chemical reactions.
Where,
For this proposed mathematical model, r denotes the reaction rate, f fugacity, T temperature and R the ideal gas constant.
Since a reactive gaseous flow is present through a porous bed, the pressure drop along the length of the reactor is considered. Equation (12) represents this phenomenon:
Where, P is the pressure, z is the reactor length,
and
are, respectively, the density and viscosity of the gas passing through the bed, D
p
is the diameter of a particle forming the bed,
is the porosity of the bed,
is the specific gravity and G is the surface velocity of the mass of the gas passing through the bed.
In addition, since the average and high operating temperatures are considered, the catalyst is deactivated over time by sintering or aging processes[1, 16, 23, 31]. This process is represented by equation (13).
Where a is the term describing the deactivation, R is the universal ideal gas constant, T is the system temperature, To is the reference temperature, kd is the specific deactivation constant and is equal to 4,39x10-5 h-1 and Ed is the activation energy of the catalyst deactivation process and equals 9,1x104 J/mol[16].
On the other hand, the stoichiometric number (SN) is also evaluated, which is determined by equation (14) and allows the relationship between the composition of H2, CO and CO2 to be seen, since these compounds are directly related to the synthesis of methanol.
The efficiency and performance in the methanol synthesis process are favored for SN values close to 2, with the optimum value being 2,05[1, 7, 16]. Values of the SN <2 indicate a deficiency in the amount of H2, which causes the formation of unwanted byproducts, and an SN> 2 indicates an excess in the amount of H2 and deficiency in carbon, this occurs when a gasification with steam, which implies a higher recirculation ratio within the reactor and a less efficient and more costly plant[16].
2.4 Model validation and simulation conditions
Initially, an algorithm is constructed in MATLAB©, to simulate the production of methanol, from SYNGAS, which uses the mathematical model illustrated in section 3 of this paper. The temperature variation along the reactor is not considered, since it is assumed that it operates isothermally, thanks to it is assumed the use of water as a refrigerant[18] and because it is expected to have a constant temperature, which favors the production of methanol and not drastically affecting the activity of the catalyst.
Once the algorithm is ready, it is proceeded to validate it and compare its results with references that obtain the experimental data or simulate the catalyst (CuO-ZnO-Al2O3) methanol production, from biomass SYNGAS. For this purpose, the following data illustrated in Table 4 and reported by[22] and [18] are used.
Additionally, the methanol synthesis reactor characteristics and operation conditions, are illustrated in Table 5.
Once the model is validated, we proceed to use the compositions shown in Table 2 and provided by Sarmiento et al (2015), to feed the algorithm in MATLAB©, and thus the influence of gasifying agent in methyl alcohol chemical synthesis could be discussed. The data in Table 3 is used to determine the methanol yield production depending on the Steam/biomass ratio variation. The analysis of all results will allow establishing which of the studied residual biomasses and gasification conditions have a greater potential for obtaining a SYNGAS, according to the needs of methanol process production and the SN condition.
3. Results and discussion
3.1 Model validation
The comparison of the methanol composition profile between this model and the data reported by[22] and [18] is shown in Figure 1.
This model is suitable for the simulation for methanol production from a SYNGAS, product of the biomass gasification because the constructed model follows the same behavior as that reported by[22]. The profile of the model results and those presented by reference show a difference for reactor lengths between 0 and 3 m, where the methanol profile for a simulated case is higher than reference results. After three meters, the trends are opposite and the reference methanol production data is higher. It is important to point out that, the model used here, considers the deactivation of the catalyst by sintering processes, whereas the one used by the reference does not.
As the catalyst deactivation rate depends on the temperature and system operation time, what is expected is that the methanol molar fraction for catalyst deactivation model approaches these values, from a reactor longitude between 0 to 3 m, to the reference values, which are lower, because the catalyst activity loss increases with the time and a high temperature operation.
3.2 Gasification agent effect
Considering the most common, feasibility and favorable operational conditions, and that the simulations developed here are for a one catalyst packed tube, the results are then illustrated in the following figures.
In Figure 2, it is shown the methanol molar fraction profile for SYNGAS obtained from flower waste gasification, whose compositions are shown in Table 2, which considers several gasifying agents.
With the figure analysis, it could be said that the more adequate SYNGAS to be a raw material in a methanol synthesis process, is derived from a gasification biomass process, which considers as a gasifying agent an air-steam mixture, followed by steam and finally, by air. The SN was the highest to air-steam, but, the methanol production was the worst because the hydrogen concentration was very low, if it is compared with the other two gasifying agents considered in this study.
Although the Nitrogen (N2) acts like a pressurized agent to favor the chemical equilibrium towards the methanol production, its excess in the reacting gas mixture can lead to a low conversion of methanol, because the SN is low in these cases, as illustrated in Table 2. Additionally, the N2 is not a reactant specie, therefore, it will not participate in the methanol production process; also, due to a high calorific value, it steals heat for the gasifying process.
3.3 Steam-Biomass ratio effect
The results obtained for the methanol production process simulation using a SYNGAS from Palm matter gasification and a Steam/Biomass ratio of 2.0 and 0.5, are shown in Figure 3 and Figure 4, respectively.
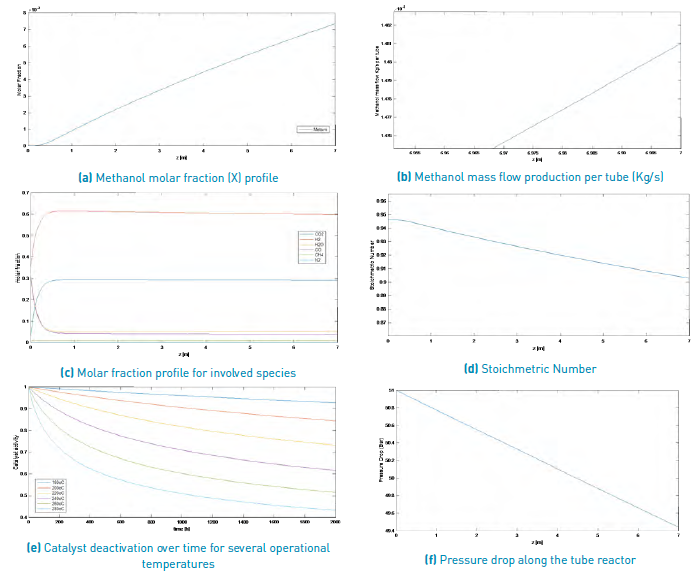
Figure 3 Simulation results for a methanol production from a palm matter SYNGAS (Steam/Biomass ratio = 2).
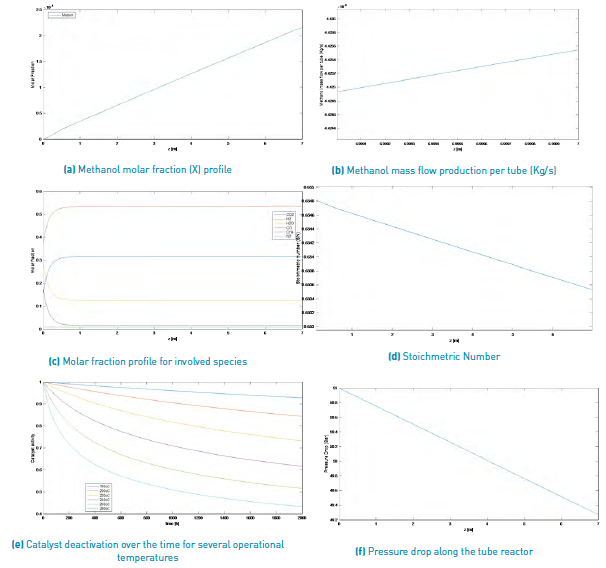
Figure 4 Simulation results for a methanol production from a palm matter SYNGAS (Steam/Biomass ratio = 2).
According to this information and comparing both results for a SYNGAS from palm matter, it can be said that with a larger Steam/Biomass ratio, smaller amounts of methanol production are reached, once the reactor longitude is achieved, with a 1.481x10-4 Kg/s for a S/B=0.5 and near 4.4253 x10-6 Kg/s for a S/B=2.0.
Because the considered deactivation catalyst mechanism is sintering, it only depends on operational process temperature; thus, this parameter does not vary for the different selected biomass sources or for any other variation of operational condition.
Figure 5 shows, the methanol profile yield, for steam/biomass ratio between 0.5 until 2 for coffee husk and palm matter.
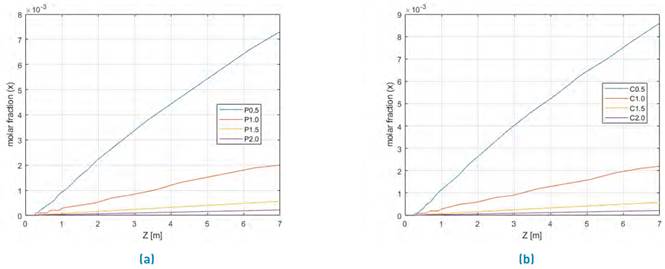
Figure 5 Evaluation of Steam/biomass ratio between 0.5 to 2.0 for two SYNGAS from Colombian biomasses steam gasification for a) Palm matter and b) Coffee husk
According to the results in Figure 5, the best methanol production to both evaluated biomasses are for the 0,5 biomass/steam ratio. Therefore, the methanol production yield is increased, while the Steam-biomass relationship value decreased.
3.4 Biomass selected effect
Table 6 shows the methanol results, using the selected biomass SYNGAS as a raw material. This information is useful to look for the best biomass for methanol synthesis.
Table 6 Methanol output molar fraction for the simulation of reference and three SYNGAS from Colombian agro-industrial waste
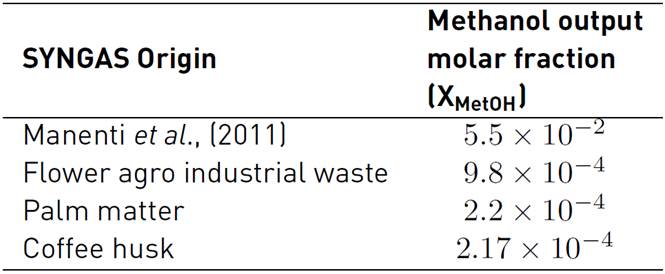
Table 6 shows that the best methanol production is for the synthesis gas from the gasification of flower agro-industrial waste. Although the flower waste has the lowest stoichmetric number, these results are achieved because SYNGAS composition does not exhibit a high content of steam, and it has a higher CO2 composition than its counterparts evaluated here.
4. Conclusions
A high value-added generation, through a SYNGAS catalytic conversion into methanol, is presented and discussed here. Likewise, this study considers a computational modelling, using Matlab©, including methanol yields, operational condition evaluation, temperature and pressure, catalyst deactivation, SYNGAS composition, gasifier agent, the origin of biomass, pressure drop, among others.
The results show that the best methanol yields are achieved for the situation where the gasifier agent is pure oxygen (O2) or steam (H2O(v)), being the first with a stoichmetric number near to 2. However, it is considered that producing pure O2 is more expensive than the steam production, and biomass gasification with H2O(v) achieves the highest low heat value of SYNGAS. This could be explained due to the hydrogen content in the steam. Therefore, at industrial scale, it will be profitable using the steam as a gasifier agent.
The temperature and pressure are important operational parameters, because these variables are directly related with the chemical equilibrium, chemical kinetics reactions and selectivity, but if increasing these two parameters, the initial investment, operational cost and useful life of catalyst will be affected in a negative way, all of this, without considering the origin of residual biomass and the gasifier agent identity, because the math and computational model characteristics of the catalytic process for the methanol production do not depend on these two gasifying operational conditions.
Regarding the syngas biomass origin, it can be concluded that SYNGAS with a H2O low content is desirable, because this condition promotes the chemical equilibrium towards the methanol production. Therefore, the biomass that shows the best results is the flower agro industrial waste, because the SNGAS steam content is the lowest, if compared with coffee husk and palm matter SYNGAS, despite its SN is not the nearest to the recommended condition (2,01). Additionally, for a good conversion of synthesis gas into methanol, it is recommended that the SYNGAS has a high hydrogen and considerable carbon dioxide amounts in the reactor inlet composition.