I. Introduction
Most of the world's copper production (80-90 %) comes from sulfured ores that require high temperature oxidation; however, this pyrometallurgical processes produce a large amount of residue, which is one of the main byproducts of the metal extraction industry. A primary copper residue is commonly composed of 30 % to 40 % iron, 35 % to 40 % silica, less than 10 % alumina and oxidized calcium, and lastly 1 % copper [1]. Copper slag is produced during pyrometallurgical production of copper from copper ores. For every ton of metal production, about 2.2 t of slag is generated [2]. It is estimated that each year 4.5 million tons of these residues are produced, therefore, the historical accumulated volume (in Chile) could reach about 50 million tons [3].
Several studies have been carried out in the area of slags and copper mattes. Johnson et al. [4] investigated the behavior of minor-elements (As, Sb, Bi, Se and Te), and their interaction in the copper matte-iron silicate slag system. They concluded that a better understanding of minor-element behavior in copper smelting systems could improve the recovery of minor elements and the efficiency of copper extraction, in addition to have a healthier and safer workplace, and less hazardous situations. In other study, Herreros et al. [5] analyzed the effects of stirring speed, temperature, initial chlorine and chloride concentrations, particle size, reactants addition order, and slags in the copper and iron dissolution from reverberatory and flash furnace slags. This study found that for particle sizes less than 20 um, practically all of the sulfide phases were liberated, and copper extraction reached 80-90 % by chlorine leaching, with iron solubilization between 4-8 %. It was also concluded that chlorine leaching of the sulfide phases is very fast (less than 5 minutes) in the range 10-2 to 10-3 M CI2. Banza et al. [6] used three different tests (sulfuric acid leaching, leaching at constant flow rate of hydrogen peroxide, and leaching at constant potential Eh) to analyze copper smelter slags with fayalite structure. They demonstrated that approximately 80 % Cu, 90 % Co, and 90 % Zn can be recovered using the sulfuric acid leaching method. Arslan and Arslan [7] focused on the recovery of copper, cobalt, and zinc from copper smelter and converter slags by roasting with sulfuric acid. This study used leaching experiments to investigate the effects of roasting time, acid/slag ratio, and roasting temperature on the dissolution extents of metals, achieving a total of 88 % Cu, 87 % Co, 93 % Zn, and 83 % Fe in 2 h of roasting at 150 °C and 3:1 acid/slag ratio. Moreover, increasing the roasting time to 4 h increased Cu extraction to 95 %.
The present work considers the white metal copper roasting, produced in fluidized bed, using a conventional melting furnace operated with temperature range between 750 and 820 °C, in order to produce a calcine that essentially contains cupric oxide (CuO), hematite (Fe2O3) and cupric ferrite (CuOFe2O3). First, the calcine was leached to dissolve the copper oxide producing a residue that mainly consisted of hematite and cupric ferrite, in addition to an amount of noble metals such as gold (Au) and silver (Ag). After that, the calcine recirculated through the melting furnace, where the ferrite discomposed to form copper matte; the concentration of noble metals increased during each cycle.
Regarding the recovery of noble metals contained in the residue, such as gold and silver, they usually can be recovered using the same mineral reduction processes due to their similar physicochemical properties [8,9]. Nowadays, cyanidation is the most important and frequent method used to extract gold and silver, due to its convenient ratio cost/efficiency. The cyanidation process is based on the lixiviation, or dissolution of noble metals in an alkaline solution of cyanide [10,11]. The most interesting aspect of cyanide leaching process is the reaction of selective dissolution of gold and silver in an aqueous solution to form auriferous and argentiferous metallic complexes. The main progress in understanding the chemistry of gold cyanidation was made by Kudryk and Kellog [12], who demonstrated the electrochemical nature of gold cyanidation. The gold dissolution reaction, known as Elsner's equation [13,14], can be written as:
One can mention that the reactions for the dissolution of silver are analogous to the reaction equations for the dissolution of gold. The ores of copper, iron, zinc, manganese, nickel, arsenic, antimony, among others, and their respective metals also react in alkaline cyanide solutions. These reactions may occur to some extent, thus consuming cyanide and oxygen, and producing a variety of species in solution, which can reduce the efficiency of noble metals leaching process and subsequent recovery processes [15].
II. Experimental procedure
The experimental procedure followed is summarized in the flow sheet shown in Figure 1.
The studied material is a calcine produced by oxidized roasting of white copper metal. To chemically analyze this calcine, atomic absorption spectrophotometry for copper, iron, gold and silver was carried out, using the Thermo Scientific iCE 3000 Series equipment. To reduce the amount of copper present, the calcine was pre-treated using sulfuric acid at a concentration of 25 g L-1, at room temperature for 50 h. This hydrometallurgical pretreatment procedure is commonly applied to ores containing gold and silver [16]. The residue obtained after the acid lixiviation was rinsed with distilled water, and then dried at a temperature of 80 °C for 48 h; subsequently, it was granulometrically analyzed using a series of sieves to determine its characteristic grain size, and chemically analyzed using atomic absorption spectrophotometry. Sulfur analysis was performed using the LECO HF10 model equipment.
The residue was characterized by X-ray powder diffraction (XRD), on a Rigaku Geigerflex D/Max-C, using iron radiation (due to high copper content), operated at 35 KV and 15 mA in a 2e range between 4° and 70° with a step of 0.02°, and an accumulation time of 56 seconds. To determine the phases, we used a JEOL JXA 8600 electron probe micro-analyzer (EPMA), equipped with three wavelength-dispersive spectrometers (WDS) and an energy-dispersive spectrometer (EDS), with analyzing crystals (LDEI, TAP, LIF and PET), using a take-off angle of 45 degrees and Beam Voltage of 20 V.
The cyanidation tests for the extraction of Au and Ag were performed using the following elements: a Pyrex Erlenmeyer flask, a K type thermocouple connected to a Syscon International temperature data recorder, a Nuova Thermoline heating plate, an IKA Labortechnic stirring motor, a pH meter VWR Scientific 8005 model, and glass stirrers with Teflon blades to avoid wear contamination.
The analytical reagents used for the preparation of solutions were: 97 % potassium cyanide (KCN), 99 % silver nitrate (AgNO3), and 98 % sodium hydroxide (NaOH). Distiller water was used for all tests.
For the cyanidation process, a mass of dry residue was taken and placed in an Erlenmeyer flask reactor, adding water to the cyanide solution, considering 170 g of dry residue and 500 ml of water. Then, the reactor was placed on the heating plate, connecting the thermocouple and the stirrer. The pH of the suspension was modified by adding analytical grade NaOH. When the solution reached the working temperature and the defined pH for each test (10, 10.5 or 11), the cyanide solution was added. Cyanide concentration monitoring was performed periodically by titration with silver nitrate, and the reactor was always kept open (aerobic conditions).
III. Analysis of results
A. Characterization
1) Chemical analysis of the calcine: Elemental analysis of the calcine gave concentrations of gold and silver of 29.2 and 746 g t-1, respectively (Table 1). The analysis also showed that 48 % of iron is present as hematite (and possibly some magnetite), and 52 % as cupric ferrite [16].
Eventually, three species can be assumed in the calcine [16]: cupric oxide (CuO), hematite (Fe2O3) and cupric ferrite (CuO·Fe2O3). Thus, 27.48 % of the total copper would be as cupric oxide, and the remaining 6.72 % as cupric ferrite. This calcine was leached by using sulfuric acid, aiming to dissolve all the cupric oxide, and to obtain a residue with a very high percentage of cupric ferrite.
2) Chemical analysis of the residue: With the acid pretreatment applied to the material (studied residue), in contrast to the calcine, an average mass loss of 34.38 %, and a higher content of gold and silver were achieved. This indicates that non-lixiviated copper is present yet as cupric ferrite [16], which is the main focus of this study. Results of the elemental chemical analysis of the residue are shown in Table 2, where the amount of copper, iron and sulfur, in addition to gold and silver tenors containing the residue can be observed.
3) Sieve analysis of the residue: The sieve analysis showed that nearly all the material size is less than 300 µm, 56 % is less than 75 µm, and 38 % is less than 38 µm (Figure 2).
4) Mineralogical analysis of the residue: The XRD analysis showed that by Rietveld refinement the cupric ferrite (CuO.Fe2O3) and fayalite (Fe2SiO4) represent most of the phases; and that significant amounts of iron oxides (Fe2O3 and Fe3O4), lead sulfate (PbSO4), copper oxide (CuO), and calcium oxide (CaO) are contained in the residue (Figure 3).
5) Compositional analysis of the residue: To analyze the composition of the residue, an electron probe micro-analyzer (EPMA) was used, and the results are shown in Figures 4 through 7. Figure 4 shows the backscattered electronic image (BEI) of a particle mainly composed of iron and silicon oxides (fayalite), with iron and copper oxides (cupric ferrite) observed at the bottom of the image.
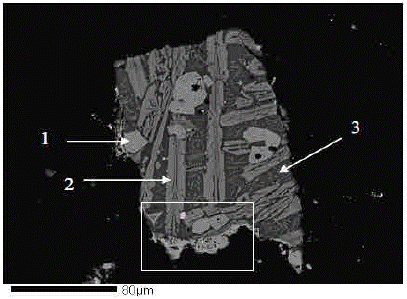
Fig. 4 BEI images of a residue particle, (1) Fe and O majority elements; Ti, Al and Zn traces, (2) Si, Fe and O majority elements; Mg and Ca traces, (3) Si, Fe and O majority elements; Al, Ca and K traces.
Enlarged images of the residue particle (Fig. 4) are shown in Figure 5. Figure 5a shows the compositional BEI image, where a grain of cupric ferrite (1), and a grain of copper sulfide (2) can be observed. Figures 5b, 5c and 5d show X-ray images for copper, iron and oxygen, respectively. From the analysis of figures 4 and 5, one can verify that the residue under study is mainly composed of three phases: the first phase is composed of cupric and iron oxides, present as cupric ferrite; and the second and third phases are composed of iron and silicon oxides, respectively, present as fayalite.
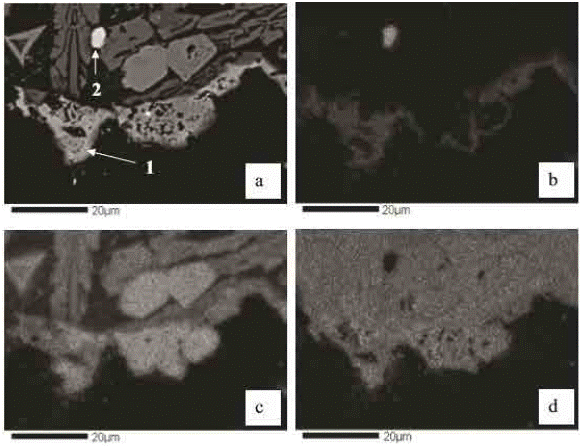
Fig. 5 Enlarged images of a residue particle. a: BEI image. b: X-ray image of copper Kα. c: X-ray image of iron Kα. d: X-ray image of oxygen Kα.
A gold particle belonging to the residue under study is shown in Figure 6. Figure 6a shows the compositional BEI image, where a grain of gold (1), and a grain of cupric ferrite (2) can be observed. Figure 6b, shows an enlargement of the compositional BEI image. Figure 6c, shows the X-ray image of gold Kα.
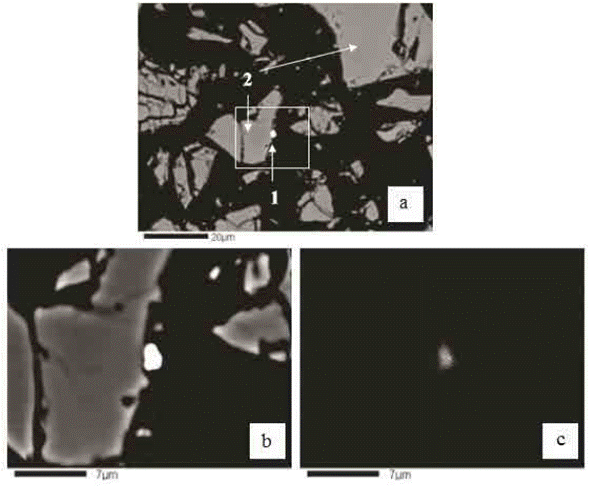
Fig. 6 a: BEI image, (1) particle of gold and (2) particle of cupric ferrite. b: Enlargement of BEI image. c: X-ray image of gold Kα.
A BEI image and X-ray analysis of a residue particle containing silver and sulfur are shown in Figure 7. Figures 6 and 7 show the presence of noble metals in the studied residue. Because the gold is found in free form, it is possible to recover it using conventional cyanidation. Silver, on the other hand, is present in the residue as sulfur-silver alloy, which may produce refractoriness during conventional cyanidation.
B. Cyanidation tests
The second part of this research was devoted to study the recovery of gold and silver present in the residue previously characterized, by applying cyanide leaching. The first experimental test was carried out to analyze the influence of pH on the cyanidation of gold present in the residue (Fig. 8). This test was conducted for three different pH values, at room temperature (25 °C), and with a 0.06 g 1-1 of KCN solution. The highest recovery percentage of gold (78.4 %) was always obtained with a pH of 10.5 in 48 h. The second test was carried out to evaluate the influence of room temperature on the effectiveness of the cyanide leaching process. This test was done for low concentration of KCN and pH of 10.5, under four different temperature conditions (25, 45, 65 and 75 °C), as shown in Figure 9. Results showed that gold recovery higher than 95 % can be obtained in only 6 hours at a temperature of 75 °C. At lower temperatures (i.e., 25, 45 and 65 °C), longer leaching process times are required to obtain similar results.
The lowest effectiveness of cyanide leaching was obtained at 25 °C. Accordingly, at higher temperatures an increase of the activity and velocities of diffusion of the reactive elements is expected, increasing the noble metals rate of dissolution. It should be noted that as temperature increases, the amount of dissolved oxygen in the water decreases, therefore, in very slow reactions, a temperature increase does not always imply increased leaching rate.
In order to identify the effect of the potassium cyanide (KCN) concentration on the metal recovery percentage for gold, silver and copper, a third experimental test was carried out. The results of this test showed that the highest percentage of gold recovery corresponds to the lowest concentration of KCN (0.06 g 1-1) used in the test (Fig. 10). The increase in the KCN concentration resulted in a decrease in the recovery of gold, from 95 % (using 0.06 g 1-1 of KCN) to 66 % (using 1.2 g 1-1 of KCN). On the other hand, high KCN concentrations are required to improve the recovery of silver and copper, due to their high content in the residue (Fig. 10).
For leaching silver, the best concentration of KCN was 1.2 g 1-1, corresponding to 30 % of silver recovery (Fig. 10). This low recovery percentage can be due to having silver ore dissolved in a copper-sulfur matrix, in amounts ranging from 1 % to 50 %. Furthermore, for KCN concentration levels higher than 0.6 g 1-1, there is a linear relationship between the extraction of silver and the concentration of KCN. This might be due to the high concentration of cyanide that dissolves the Ag-Cu alloy without preference for the noble metal. In summary, high concentrations of KCN cause leaching of cyanide metals, such as copper (i.e., cupric ferrite).
IV. Conclusions
The characterization of copper slag using compositional analysis provides valuable information related to the size and phase distribution of metals present in each particle of copper residue. The analysis showed that iron is found in all residue phases, as both cupric ferrite and fayalite, along with copper and silica, respectively. This study also found that gold was located close to the grain boundaries of the residue, while silver was always found forming alloys with sulfur. Based on this characterization, one can predict good recovery of gold but not silver. After acid pretreatment of the residue to dissolve all the copper in oxide form, cyanidation results indicate that the recovery of noble metals present in the slags from copper industry is possible. The recovery of gold present in the residue was up to 95 % under conditions of room temperature and KCN concentration of 0,06 g 1-1, during 80 hours of leaching. However, similar results can also be obtained in only 6 hours, but at a leaching temperature of 75 °C, KCN concentration of 0.06 g 1-1, and pH of 10.5. In the case of leaching silver, the recovery was less than 30 %, with a KCN concentration of 1.2 g 1-1, pH of 10.5, leaching temperature of 45 °C, and a residence time longer than 72 hours. This low recovery percentage can be due to having silver as sulfur-silver alloy, which may produce refractoriness during conventional cyanidation.