INTRODUCTION
In restorative dentistry, metal-ceramic systems have been regarded for decades as the golden standard for restorations like individual crowns and fixed partial dentures.1 However, the increased interest of clinicians and patients in esthetic results and in materials with higher biocompatibility has enabled the emergence of all-ceramic restorative systems with better aesthetic and biological properties.2
The all-ceramic systems currently available on the market are lithium disilicate, infiltrated ceramics, and zirconia (Y-ZTP). Among these, zirconia has the greatest mechanical properties suitable for producing restorations of three or more units in the posterior sector. However, Y-ZTP has a polycrystalline layout that reduces its esthetic properties, requiring the use of ceramics with high content of silica, such as feldspar, in order to achieve aesthetically successful restorations.3
Despite the high mechanical properties of zirconiabased restorations, controlled clinical trials have found a higher percentage of complications (such as chipping of the ceramic veneer) in restorations with zirconia structures compared with metalceramic restorations.4 Concerning the causes of such complications, the authors suggest that inappropriate structure design,5 differences in the ceramic material′s coefficient of thermal expansion,6 and rapid cooling of the ceramic veneer cause excessive residual tension of it, generating micro-fissures or detachment of the ceramic veneer in the presence of masticatory forces.7 In order to control this residual pressure, it has been suggested to conduct slow cooling protocols during the firing process,8 as well as ceramic coatings measuring less than 1.5 mm in thickness.9 However, the high opacity of zirconia reduces its use in restorations in the anterior sector, where it would affect appearance when using ceramic coatings with smaller thickness than those previously described.10 Having this clinical situation on mind, it has been proposed to conceal the Y-ZTP structures by adding a liner on them, allowing better optical properties of restorations.11 However, the effect on bonding strength as a result of liner application to a zirconia structure that is to be covered with feldspathic ceramics is still unclear.12)(13
The purpose of this study was to determine whether the use of a liner affects the ceramic veneer bonding strength to zirconia when using a slow cooling protocol.
MATERIALS AND METHODS
Preparation of zirconia blocks
Twenty blocks of Y-TZP pre-synthetized ceramics were fabricated and sectioned with an Ultrathin® disc: 10 (IPS e.max ZirCAD (Ivoclar vivadent®) and 10 (Ecco Amann Girrbach Zirconio®) measuring 12 mm x 11 mm x 4 mm (Figure 1), and polished with sandpaper #600 and #1000; they were later sintered in a Zircomat-Vita furnace increasing temperature during 60 min until a final temperature of 1530°C for a period of two hours (this process included the cooling phase to 200°C in 6.0 hours). Then the blocks were rinsed with water and measured, and the samples were carefully examined with magnifying lenses (bio-art MAGNIFYN LENSES) to verify the absence of fissures.
Preparation of ceramic veneer on zirconia blocks
Each of the twenty zirconia blocks was applied a ceramic veneer (IPS e.max) of 5 mm x 11 mm x 4 mm (Figure 1) as follows:
Application of liner
Groups one and three (with liner) were washed with abundant water and cleansed with isopropyl alcohol; the IPS e.max Ceram ZirLiner was mixed with fluid IPS e.max Ceram ZirLiner Build-Up until obtaining a creamy texture, and applied on the zirconia surface to achieve a uniform green color. Thickness of the veneer after firing was approximately 0.1 mm. It was left to dry for five minutes and brought to the furnace according to specifications (Table 1).
Application of ceramic veneer
The ceramic veneer (IPS e.max Ceram Ivoclar Vivadent, Schaan, Liechtenstein) was applied on the surface of each sample of sintered zirconia. The standardization process included a silicon array (Elite Zhermack) measuring 5 mm x 11 mm x 4 mm long in order to standardize the ceramic veneer dimensions.
The IPS e.max Ceram ceramics was prepared with a solution recommended by the manufacturer (IPS e.max Ceram Build-Up Liquid) (Table 2). The layering technique was used14 condensing the ceramic material layer by layer; excess moisture was removed with absorbent paper towel and the silicon mold (Elite Putty - Zhermack) was carefully removed. The samples were brought to the ceramic furnace (Programat P 300, Ivoclar Vivadent), firing at 750 °C-keeping this step until achieving the desired size of 5 mm x 11 mm x 4 mm.
Table 2 Materials under evaluation: Zr (zirconium), Y (yttrium), Hf (hafnium), Al (aluminum), Si (silicon), Zn (zinc), Na (sodium), K (potassium), Ca (calcium), P (phosphorus).

During the last fi ring cycle, the ceramic veneer was subjected to a slow cooling protocol; when the furnace (Programat P 300; Ivoclar Vivadent) reached a temperature of 500° C, the sample remained on the furnace for fi ve minutes with the muffl e partially open to about 30% (Figure 2). The room was free of any condition that could affect the slow cooling protocol (such as air conditioning, fans, or windows).8
Bond strength test (shear)
Samples were placed in a universal machine (Model 3366, INSTRON Corp., Norwood, MA, USA) and stabilized with a stainless steel clamp made to measure for proper and fi rm position during testing (Figure 3). A load was applied parallel to the axial axis of the sample, placing the tip of the cutting instrument as close as possible to the ceramic/ zirconia interface, at a speed of 1 mm/min until fracture and recording the load in Newtons (N). Bond strength in MPa was calculated by dividing the load (N) at the time of fracture by the bonding area.
Bond strength (MPa) = Load (N) / Area (mm)2
The ANOVA statistical test was used to verify any statistically signifi cant difference in bond strength among the four study groups.
RESULTS
Shear bond strength test (SBS): the mean (SD) of bond strength values obtained in laboratory testing was as follows: 15.22 MPa for the Ecco group with no liner (EX); 15.33 MPa for the Ecco group with liner (EL); 16.36 MPa for the Ivoclar group with no liner (IX), and 13.54 MPa for the Ivoclar group with liner (IL) (Table 3). The greatest ceramic veneer bond strength to zirconia was obtained in the IX group, that is to say, the Ivoclar zirconia blocks without liner application; however, the ANOVA test yielded no statistically significant differences among the four study groups when running the bond strength test (p = 0.662) (Figure 4).
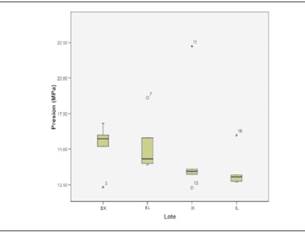
Figure 4 No statistically significant difference may be seen; all the groups showed extreme values off the field.
Analysis of fractured surfaces
There was a combined type of failure in all samples (Figure 5), characterized by fracture at the zirconiafeldspathic ceramics interface (adhesive failure) and fracture of ceramic veneer (cohesive failure) (Figure 6).
The results of this study confirmed our null hypothesis: "there is no difference in evaluating ceramic veneer bond strength to zirconia with and without the application of liner using a slow cooling protocol".
DISCUSSION
Clinical studies report delamination or fracture of the ceramic veneer as the main complication in restorations with zirconia structures.4
For this reason, researchers have tried to understand and improve the ceramic veneers bond strength to zirconia by evaluating not only their mechanical properties15 but also the manufacturing processes of zirconia structures,16 treatments on the zirconia surface,12)(17 and the behavior of veneering ceramics with different coefficients of thermal expansion on a particular brand of zirconia.17)(18
The present study evaluated and compared a ceramic veneer bond strength to zirconia blocks by different manufacturers (Ecco Amann Girrbach Zirconia - Ivoclar e.max ZirCAD) and the convenience of using a liner through a slow cooling protocol as suggested by some authors.8)(9)(19)(20)(21
The use of liners has been proposed to improve the aesthetic characteristics of restorations with zirconia structures.11 However, some authors suggest that using a liner can affect the bond strength of the ceramic veneer to zirconia.12)(22 In the present study, the application of a liner on the zirconia blocks did not affect the ceramic veneer bond strength to zirconia. These results are consistent with research conducted by Fischer et al13 and Aboushelib et al,23 who indicate that using a liner does not affect the bond strength of the ceramic veneer to zirconia.
Slow cooling protocols have been described in the production of restorations with zirconia structures. .8)(9)(19)(20)(21 These protocols significantly reduce the residual stress generated on the ceramic veneer with zirconia structures.24)(25 Some authors suggest that excessive residual tension on ceramic veneers subjected to occlusal loads could be one of the factors favoring the emergence of chipping or delamination of ceramic veneers with zirconiabased structures.7)(21)(26 The literature has described a relationship between the use of slow cooling protocols and decreased bond strength of the ceramic veneer to zirconia20 -a finding that may explain the results of the present study, where maximum bond strength was 16.36 Mpa-. These results are lower than those of studies conducted without the use of slow cooling protocols and which averaged bond strength from 20 to 35 Mpa.6)(13)(17)(22)(23
In evaluating failure type among all the samples in the present study, we found out that all showed a combined type of failure (adhesive/cohesive). This result may be connected with the ceramic veneer thickness (4 mm) used in this study, since it is bigger than suggested by the manufacturer (1.5-2 mm). This may be associated with an increase in residual stress, and with a decrease in the ceramic′s fracture strength.27)(28 On the other hand, the method used to evaluate bond strength is associated with a crack in the area of load application, no matter the reason for adhesive/cohesive failure; this type of failure should not be interpreted as a too fragile ceramic veneer, as suggested by some studies.13)(17)(23)(29
It is recommended to keep in mind that during the process of manufacturing a zirconia restoration, manipulating the ceramic veneer7 and considering the thermal properties of the material, especially its coefficient of thermal expansion (CTE),6)(13)(30 as well as a suitable structure design to support the ceramic veneer,5 is more important than using or not using a liner.
CONCLUSIONS
With the limitations of this study, we may conclude that application of a liner did not alter bond strength between ceramic veneer and zirconia blocks using a slow cooling protocol.