1. INTRODUCTION
The climate emergency cannot be ruled out to allow the transition for a clean energy future. This is a timely topic that required immediate attention to accomplish the emission policies imposed, for example, by the Paris Agreement [1]-[3]. The continuous and rapidly increasing demand for energy has resulted in more innovative, efficient upgrading and valorization of renewable feedstocks such as biomass [4], [5]. Although all the potential, there are several challenges to develop cost-efficient and large-scale processes to apply renewable resources for sustainable energy development [6]. Particularly, special attention should be placed on the production of fuels and value-added chemicals. The synthesis of chemical products using fossil fuels is expected to continuously increase at least until 2023 which is the main factor contributing to the increase in oil consumption [7].
The utilization of the most abundant biomass resource, lignocellulosic biomass, represents an attractive and promising strategy for green and sustainable energy production due to due to its low cost, carbohydrate-rich constitution [6], [8], [9]. Moreover, the utilization of lignocellulosic biomass avoids the food-versus-fuel debate and can significantly reduce the emissions of the major greenhouse gas, CO2 [10]. Lignocellulose is mainly composed of three main components, cellulose (35 %-50 %), hemicellulose (20 %-35 %), and lignin (10 %-25 %) [6],[11], [12].
The conversion of lignocellulosic biomass to various "building blocks" molecules via biological and chemical pathways has aroused greet attention [11], [13]. Furfural (FAL) is one of those "building blocks" molecules that deserves special attention since it is a potential platform for biofuels and value-added compounds making it one of the key platform chemicals in lignocellulosic biorefineries. Furfural and its derivatives have been extensively used as transportation fuel, gasoline additives, lubricants, jet fuel blends, and also in agrochemical (e.g. soil enhancers and organic fertilizers, fungicide and nematicide) and pharmaceutical industries [10], [14], [15].
Furfural is a heterocyclic aldehyde with a density of 1160 kg/m3 and a boiling point of 161.7°C (at 1 atm). It is colorless but turns quickly darken when exposed to air. Its molecular formula is C5H4O2 and can also be named as 2-furancarboxaldehyde, furaldehyde, 2-furanaldehyde, 2-furfuraldehyde, fural and furfurol [14], [16], [17]. Traditionally, furfural is synthetized by hydrolysis and dehydration reactions of pentoses (mainly xylose/xylan) presented in biomass in severe acid media (HCl and/or H2SO4). This is a well-explored industrial process first implemented by Quaker Oats Company in 1921 [18]. The mechanism route of furfural production is well described but this process is yet limited by low yield of furfural, high energy consumption, and high environmental and safety risks associated to the use of corrosive homogenous acid catalysts [10], [14]. Hence, many efforts are being adopted to update and improve the existing technologies that encompass the use of more selective heterogeneous catalysts and turn the process cleaner and greener to accomplish the targets of green chemistry and sustainable production. Westpro-modified Huaxia Technology and Supra Yield processes are two examples of improved processes where high furfural yields, recovery of the catalysts and high purity on target product are obtained [19]-[21].
The global furfural market size is growing reaching USD 551 million in 2019 with an annual production around 340 tons. It is expected to grow until USD 700 million by 2024 with an annual production around 424 tons at a compound annual growth rate (CAGR) of 4.9 % during that period (2019-2024) [16], [22], [23]. The production of furfural is mainly concentrated in China, the Dominican Republic and South Africa [14], [22], [23]. This market growth is primarily driven by the demand for furfural derivatives from the pharmaceutical and oil refining industries. More than 80 chemicals are directly or indirectly derived from furfural. The majority of furfural market ( > 50 %) is used for furfuryl alcohol production, but other potential derivatives are produced including furoic acid, methylfuran, tetrahydrofurfuryl alcohol, tetrahydrofuran and methyltetrahydrofuran [21], [24]. These products are obtained by several catalytic processes such as hydrogenation, oxidation, reduction, hydrogenolysis and decarboxylation [10], [24].
The hydrogenation of furfural is one of the most versatile reactions from where furfuryl alcohol (FFA) can be obtained. Its production represents approximately 65% of the overall furfural production [10] and it can allow the upgrading of furanic components to biofuels [24]-[27]. This reaction can be accomplished in gas or liquid-phase but the gas-phase is the preferred route. The liquid-phase reaction is limited by high operational costs of using batch reactors, expensive equipment to achieve high-pressure conditions and the time between successive reactions [15]. Cu-based catalysts have been extensively used in this reaction and copper supported in asbestos catalyst was used in the first report of this gas-phase reaction, in 1929 [15][26]. Thus, copper-chromite (Cu-Cr) has been widely used on the hydrogenation of furfural but due to its high toxicity new Cr-free catalysts have been developed [28]. Both homogenous and heterogeneous catalysts have been used to catalyze this reaction, including noble metal catalysts (Pd, Pt and Ru) and transition metals (Ni, Cu and Fe) supported on silica and alumina. Thus, to improve the performance of the monometallic catalysts, bimetallic catalysts such as Pt-Cu, Pd-Cu, Cu-Co and Ni-Cu have been used [15], [26], [29]. There are other methodologies for catalyst design that are being proposed such as a simple, easy, inexpensive method for the production of noble-metal free catalysts [10][26]. However, some advances are still needed to look forward new alternatives for the reduction of the severe reaction conditions (e.g. high temperatures) and to improve the catalyst performance.
Furoic acid (FA - C5H4O3) is another important furfural derivative obtained through the oxidation of furfural. FA is commonly transformed in furoyl chloride which has a market in the agrochemical and pharmaceutical industries [30], [31]. FA is traditionally produced through the Cannizzaro reaction where furfural reacts with a stoichiometric amount of NaOH used as BrØnsted base catalyst. However, the FA yield is limited up to 50% [15], [31]-[33]. To optimize the FA selectivity, different catalysts have been examined including noble metal catalysts, bimetallic catalysts [30], [34]-[36] and more recently metal-free carbon catalysts [32].
Biocatalysis is a practical and environmentally friendly approach for the synthesis of furfuryl alcohol and furoic acid which use different microorganisms and enzymes to degrade the furanic compounds of biomass [37]. Using all the potential of modern biotechnology, protein engineering and the efficient DNA sequencing, interest genes in-volved in processes including the FAL conversion into furanic compounds can be identified [38] [37]. Biocatalysis in on track in the production of building blocks molecules from renewable resources and the market of bio-based products is expected to reach € 3.2 billion by 2030 [39]. The degradation pathway of FAL by some microorganisms such as Cupriavidus basilensis [40], Saccharomyces cerevisiae, Escherichia coli, Corynebacterium glutamicum has been established [41]. However, there's no information about the metabolic pathways in which the furanic compounds are degraded. Although all major efforts done using modern tools, it's still necessary to improve and optimize the actual biocatalyzed processes.
The current review focuses on the catalytic conversion of Furfural to furfuryl alcohol, furoic acid and other by heterogeneous catalysis and biocatalysis. First, the recent progress on furfural conversion to target products using heterogeneous catalysts is reviewed by focused on hydrogenation and oxidation reactions. Then, the state-of-the-art advances in the biocatalytic production of furfuryl alcohol and furoic acid is reviewed.
1.1. HETEROGENEOUS PROCESSES
1.1.1 Hydrogénation
The nature of the products from hydrogenation of furfural is determined by the catalysts composition and reaction conditions (temperature, pressure and reactants concentration). Primary reactions occur by reducing the C=O group or the furan ring. Secondary reactions can occur by hydrogenolysis of the C-O bond, decarbonylation and hydrogenation of the furan ring [42].
Generally, most hydrogenation catalysts are capable of hydrogenating the C=C and the C=O bonds. The control of hydrogenation process of these bonds has been one of the most important subjects in study for development of catalysts. [43]. The addition of hydrogen to the C=C bond is more thermodynamically and kinetically favorable compared to the C=O bond. Thus, is required a selectively hydrogenation performing by specific catalysts and suitable reaction conditions [44], [45].
Hydrogenation can be carried out in both liquid phase and gas phases. Liquid phase hydrogenation achieves better results when compared to the gas phase process. The selectivity towards furfuryl alcohol is strongly dependent on the solvent, which can inhibit an unwanted polymerization [46]. In addition, in this condition the range of catalysts that generate yields of FFA close to 100% is greater. Although this vantages of liquid-phase its application in the large-scale is hindered due operating cost. Therefore, the gas-phase hydrogenation is preferred in industry [38].
The main reason for the continuous study of furfural hydrogenation is the search for a selective catalyst that controls the reaction route, as well as the degree of furfural hydrogenation. [47]. Industrially, catalysts based on copper and chromium are used, but new catalysts formulations are still of interest. Recently, Babu and coworkers [48] evaluated Cu-Cr-Zn mixed oxide as catalysts for selective vapor phase hydrogenation of FAL to FFA. In this study was compared the effect of catalysts synthesis (conventional and y-irradiation prepared methods) as the Cr content. First difference was noticed even prior of hydrogenation reaction, once gamma radiation exposition led to Cu reduction, discarding activation step.
According to catalytic tests results, the oxides prepared by gamma radiation were active and stable catalysts and presented higher activity compared to the conventional catalysts. The selective hydrogenation ability of catalysts depended on the copper metal surface area and dispersion. These parameters are improved by small amount of chromium. The catalyst with 0.4 molar percentage in Cu/ZnO presented the better results, achieving 84% of furfural conversion with 100% furfuryl alcohol selectivity [48].
Despite of good performance of Cu-Cr catalysts, the high toxicity of the chromium-containing catalyst incites the development of new Cr-free catalytic systems. Figure 1(a) presents the main metals used as an active phase for FAL hydrogenation catalysts, while figure 1(b) summarize the oxide materials that are typically used as supports or dopants in these systems. These images graphically represent the search for the term "furfural hydrogenation" in the Scienfider database, comprising works available from 1942 to 2020. The evaluations were limited to data published as papers (excluding reviews) and patents.
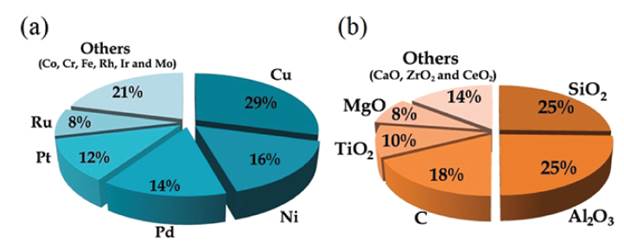
Figure 1 Typical active phases (a) and oxides supports or dopants (b) applied for catalytic hydrogenation of furfural in published papers and patents.
From figure 1(a) is noticeable that copper is still the most employed metal in furfural hydrogenation reaction studies, which is understandable due to its good activity and low cost. In order to obtained a copper Cr-free catalyst, Yang and co-workers [49] evaluated Cu/ZnO catalysts derived from aurichalcite. The precursor effect was investigated by preparing catalysts with different Cu/Zn molar ratios (0.4, 0.6, 0.8, and 1.1). In this series of catalysts the size of Cu nanoparticles and Cu-ZnO interactions were determinant for their catalytic activity for FAL hydrogenation to FFA. The catalyst with a Cu/Zn = 0.8 provided the highest TOF value (17.1) while the selectivity to furfuryl alcohol did not significantly varied with catalysts' composition and was around 98% for all catalysts.
Yang and co-worker proceeded the study of Cu-ZnO aurichalcite derived catalysts [50]. In this new approach, the researchers prepared Cu/ZnO-Al2O3 composites and investigated the role of aluminum for FAL hydrogenation in a fixed-bed reactor. The introduction of this component considerably influenced the catalysts' activity, resulting in an increase of furfural conversion from 84.9% to 98.0% (at 120°C) and 51.4% to 72.1% (at 100°C), with a high selectivity of furfuryl alcohol (around 98%). These results were attributed to superior copper surface area and improvement of Cu-ZnO interaction due Al presence that acted as structural and electronic promoter.
Alloys formation also influence at selectivity and activity of catalysts for furfural hydrogenation. Recently, was suggested an alloy chemistry strategy to modify the d-band center of Ni by Cu incorporation [51]. These catalysts were prepared by pyrolysis of a metal-organic framework (MOF) precursor containing cooper and nickel (NiCux-BTC). Theoretical calculation determines that Cu introduction lead to a downshifted of Ni d-band center. This change can improve catalytic activity by promoting desorption of hydrogen from Ni surface. And also favor the selectivity to furfuryl alcohol due transformation of adsorption orientation of furfural. NiCux/C catalysts exhibited enhanced activity and selectivity for FFA compared to pure Ni and Cu, been NiCu0.33/C catalyst the most promising at 120°C, obtained 96.7% and 93.8% of conversion and selectivity, respectively.
Li and coworker [52] also applied nickel and MOF materials in their study on catalytic hydrogenation of furfural. Ni-P-MOFs were employed as precursor to prepare Ni-P@C catalyst with graphitized carbon-covering structure. This carbon □ covering structure was able to protect the active components of Ni2P, granting stability and good reusability to the catalysts. The performance of Ni P@C catalyst was influenced by calcination temperature in preparation step. Increasing the temperature from 773 K to 973 K, the furfural conversion increased from 76.6% to 99.9%. However, another increase to 1073 K caused a decrease in the convection to 95%. Despite of minor FAL conversion the catalysts calcined at mild temperatures (773 K and 873 K) achieved better FFA selectivity.
In another recent study of nickel applicability as active phase for the catalytic hydrogenation of FAL, a series of C-rich nickel nitride nanoparticles supported on silica catalyst were prepared by the urea glass route [53]. Ni3N/C/SiO2 (10 wt.% Ni) catalysts exhibited higher conversion and stability in the gas-phase hydrogenation of FAL, when compared to Ni/SiO2 catalyst with similar Ni content. The main product was FFA when reaction occurred at 170°C, 190°C and 210°C. The temperature increasing progressively reduced the selectivity towards furfuryl alcohol and at 230°C furan was the major product.
Despite provide catalysts a higher cost, noble metals are also widely used as active phases due to their high activity in hydrogenation reactions. Pd/Ni/Ni(OH)2/C catalyst was prepared under mild conditions by hydrazine hydrogen reduction and galvanic substitution methods [54]. This catalyst had superior conversion from furfural and selectivity to furfuryl alcohol than monometallic catalysts, like Pd/C or Ni/C. Pd/Ni/Ni(OH)2/C presented high selectivity toward FFA (90.0% or 92.4%) at very low reaction temperatures (5°C or 10°C). The better performance of this catalyst was attributed to the formation of Pd tiny islands supported on nickel/nickel hydroxide nanoparticles which improves the synergy effect between Pd, Ni and Ni(OH)2 related species. The catalytic performance of this novel material did not decrease significantly after being used for 5 cycles.
Still regarding studies that combined palladium and carbon for catalysts elaboration, a recent paper present a series of 1wt% Pd/C materials as possible catalysts for hydrogenation of FAL in the liquid-phase [47]. These systems were prepared by the sol-immobilization method using different capping agents, like Polyvinyl alcohol (PVA), polyvinylpyrrolidone (PVP), and poly (diallyldimethylammonium chloride) (PDDA). It was observed that the choice of capping agents could influenced the initial activity of the catalysts due differences in amount of available Pd surface sites, but it did not significantly change the Pd particle size. PdPVA/C was the most active catalyst followed by Pd PDDA/C and PdPVP/C. However, with regard to selectivity to furfuryl alcohol, the opposite trend was observed. PdPVP/C exhibits better selectivity towards FFA (64% at 25 °C and 56.7% at 50°C) compared to PdPVA/C (45.2% at 25 °C and 49.6% at 50°C) and Pd PDDA/C (52.8% 25°C and 49.0% at 50°C) catalysts.
Furfural hydrogenation over silica-supported Co@Pd and Cu@Pd bimetallic overlayer catalysts was studied by Liu and coworkers [55]. Both systems exhibited enhanced reactivity compared to pure Pd in all evaluated pressure (1 bar, 10 bar and 20 bar). Langmuir-Hinshelwood kinetic study revealed that this result could be attributed to the decreased of hydrogen coverage on Co@ Pd and Cu@Pd catalysts surface during reaction, in contrast to pure Pd. This means that there are more active sites available for surface reaction or FAL adsorption.
Co@Pd and Cu@Pd performances were also compared to copper or cobalt catalysts and the overlayer catalysts achieved higher furfural conversion and selectivity towards furfuryl alcohol than their monometallic corresponding. Being Cu@Pd the most selective catalysts, reaching more than 90% in all studied pressures. In this study was also observed that product selectivity could be enhanced by increasing the concentration of oxygen vacancies, after the concentration is higher than a threshold value [55].
The liquid phase hydrogenation of furfural was catalyzed by Pt nanoparticles supported on SiO2, ZnO, y-Al2O3, CeO2 [56] In addition to the effect of oxide support were also evaluated the influence of solvent and reaction temperature. Methanol and n-butanol were excellent solvents for achieving high FFA yields over Pt/MgO, Pt/ CeO2 and Pt/y-Al2O3 catalysts, with uniform Pt nanoparticles dispersion. For these catalysts, mild conditions (ambient hydrogen pressure and 50°C) were sufficient to occurred FAL hydrogenation with high conversion and above 99% of selectivity to FFA. The support choice appears important to improvement platinum dispersion for achieve high FFA yields. SiO2 support begotten large and broad particle size distributions which resulted in poorer activity and selectivity.
Knowing that supported acid-materials are suitable choices for furfural hydrogenation reaction, Jouve and coworkers [57] prepared Pt catalysts supported on niobia, producing bifunctional catalyst, and modified the acidity of this oxide by incorporation of dopants (W6+ and Ti4+). The incorporation of theses cations induced alterations in the surface acidity of the support, mainly modifying the Lewis acid sites. The W6+ introducing increased the amount of Lewis acid sites, whereas the addition of Ti4+ decreased this characteristic. Was observed that the supports acidity influenced catalysts performance in distinct ways. While an increase in acidity led to greater FAL conversion, being the Pt on W-modified Nb2O5 the most active catalyst. A decrease in surface acidity improved the selectivity to FFA, making Pt on Ti-modified Nb2O5 the most selective in these series of Pt-Nb catalysts.
Bimetallic catalysts based on Pt are another approach in recent studies of furfural hydrogenation. For example, was noticed that PtSn systems were more active than monometallic catalyst. Merlo and coworkers [58] evaluated Pt/SiO2 catalysts containing different amounts of tin (Sn/Pt molar ratio of 0, 0.3, 0.6, 0.8 and 1). All the studied systems allowed obtaining furfuryl alcohol with high selectivity (96-98%). However, the bimetallic catalysts archived higher reaction rates than monometallic catalyst, being the system with lowest Sn/Pt atomic ratio the most active one.
A similar conclusion was reached when applied PtSn/SiO2 catalysts with Sn/Pt atomic ratio of 0.2, 0.4 and 0.6 [59]. The TOF obtained for the hydrogenation of furfural decreased with increase of Sn content, indicating that there is an optimum Sn/ Pt ratio and that the higher presence of Sn could block Pt sites, which are active for the hydrogenation. The researchers determined that bimetallic catalysts were more selective towards FFA due the architecture of active sites resulting of Pt particles dilution effect. This configuration favored the hydrogenation of the C=O group, allowing the preferential formation of FFA.
Bimetallic Pt-Sn nanoclusters confined in the pores of a Zr-based MOF acted as suitable catalysts for FAL hydrogenation to FFA [60]. In this study the Pt-Sn interaction was investigated by DRIFTS analysis of adsorbed CO to probe the bimetallic surface. The results indicated the formation of a Pt-Sn interface that presents different electronic surface property compared to only Pt. Moreover, CO desorption experiments using variable-temperature IR indicate that the Pt atoms on the Pt-Sn surface are spatially isolated compared to the monometallic Pt surface, which is desirable, once isolated Pt sites on the bimetallic surface appear to avoid the activation of C=C double bonds and increase the C=O bond activation.
Ru/Carbon nanotubes (CNTs) catalysts modified with Fe3O4 were applied to perform the catalytic hydrogenation of furfural to furfuryl alcohol, using alcohols as the solvent as also hydrogen donors [61]. In addition to effects of Fe3O4 loading the influence of different hydrogen donors and reaction parameters (temperature, N2 pressure, furfural concentration and catalyst amount) were also evaluated. The Fe3O4 inclusion promoted the formation of Ru0 species. Moreover, this addition facilitated catalysts recovered from the reaction mixture due the magnetic property of this oxide. Ru-Fe3O4/CNTs catalysts presented higher activity and selectivity towards FFA than Ru/CNTs catalyst, especially at the Fe3O4 loading of 5 wt%. The resulting Ru-5%Fe3O4/CNTs showed 99.4% FAL conversion and 100% of FFA selectivity using i-propanol under 453 K and 0.1 MPa (N2) for 4 h. The reaction mechanism over Ru-Fe3O4/CNTs proceeds through metal-mediated hydrogenation (Ru metal) and Lewis acid-mediated intermolecular hydride transfer (RuOx-Fe3O4 Lewis acid).
The relationship between structure and activity for catalytic hydrogenation of FAL in liquid phase was verified by evaluating ruthenium catalysts supported on fumed silica and SBA-15 and varying the size of the Ru nanoparticles (2-25 nm) [62]. It was observed that the furfural conversion was directly proportional to the surface fraction of Ru, indicating an apparent sensitivity of the structure. The competing reactions that produce furfuryl alcohol (hydrogenation) and furan (decarbonylation) presented opposite structure sensitivity. While the hydrogenation of C=O is favored by Ru nanoparticles larger than 17 nm, decarbonylation occurs preferably in particles smaller than 10 nm, regardless of the textural properties of the support. These trends correlate with the apparent diverging activation energies for hydrogenation contrasted with decarbonylation. The increase in hydrogen pressure from 10 bar to 25 bar promoted the hydrogenation of C=O. The selectivity for FFA reached 98% at 100°C and 25 bar, decreasing slightly at higher temperatures due to a small degree of ring-opening to 1,2-pentanediol.
Ru/Al2O3 was also used in the liquid phase catalytic hydrogenation of FAL in a recent study [63]. These catalysts were modified with phosphorous to improve Ru stability against leaching. Phosphorous addition was made by impregnation with ammonium hypophosphite and varying the next step (reduction or calcination). The addition of phosphorus increased ruthenium dispersion and its reducibility. I addition the catalysts acidity was changed to a more Brensted-based material than a Lewis-based material that was an original characteristic from Al2O3 support. The catalysts that experimented reduction step achieved more activity and selectivity. Despite of phosphorus inclusion did not led to significantly alterations in catalyst activity and selectivity, it affected the stability. The extent of activity loss of P-free catalyst was significantly higher than P-promoted catalyst, after six consecutive recycling tests.
It is evident from the studies presented that the hydrogenation of furfural is a very complex reaction that involves several variables in relation to the catalyst as well the reaction medium. Regarding the catalyst design, different factors were presented that can affect its performance. Like the effect of preparation method, precursor and presence of dopants. As well as the influence of support properties, the result of active phases combination and of alloys formation. That is why research related to furfural hydrogenation is quite extensive and involves the employment of classic materials, such as supported catalysts and typical oxides and supports such as alumina and silica. But also, the use of advanced materials, such as MOF and structured catalysts.
1.1.2 Oxidation
As mentioned above, the furfural has many applications in the chemistry industry. It can be employed to produce biofuel to aviation (kerosene) from the oxidative condensation reaction with alcohol. Ton and coworkers [64] studied the oxidative condensation between furfural and ethanol employing Au/FH, Pt/FH, and Co/FH catalysts. They obtained furfural conversions major than 90% and high selectivity. The main products of reaction were 3-(furan-2-yl-)-2-methylacrylaldehyde and furan-2-acrolein. In this reaction, K2CO3 and KOH as promotor are used; however, taking into account that the reactions should be carried out in clean systems, the oxidative condensation is still a challenge.
In the same way, recently, Gao and coworkers [65] prepared Au catalyst supported, which were used in the oxidative condensation of furfural and ethanol with O2 molecular under mild reaction conditions. Au@CaO catalyst raised higher furfural conversion (85.9%) and of furan-2-acrolein selectivity (81.8%). The results indicated a synergistic effect between the golden nanoparticles and the calcium oxide, which favors the furan-2-acrolein production.
In another study, Signoretto and coworkers [66] tested Au/ZrO2 catalysts in the oxidative esterification of furfural and studied the calcination of temperature. They found that the calcination at 500° produces Au nanoparticles of 3 nm that can dissociate the molecular oxygen. This calcination temperature was also to eliminate the organic residue from both Au active sites and ZrO2. The main product of the reaction was the furoate ester. Besides, Pinna et al. used Au/ZrO2 and Au/TiO2 systems in the oxidative esterification of furfural with oxygen and methanol. Au/ZrO2 was calcined at 600°C and 250°C under O2 flow. When the sample was calcined at 650°C, the Au nanoparticles showed particles above 4 nm, which were detected by CO chemisorption and HRTEM studies. This fact caused low activity and selectivity in the reaction. However, the Au/ZrO2 catalyst calcined at 250°C was more active and selective that Au/ TiO2, and there was not acetal formation [67]. Menegazzo and coworkers [68] analyzed the support effect in the oxidative esterification of furfural. Au/ZrO2, Au/CeO2, and Au/TiO2 catalysts were studied. The best system was Au/ZrO2 followed by Au/CeO2 and Au/TiO2. The zirconia showed good chemical and morphological properties that allowed obtain high dispersion of Au particles, adequate specific surface area, and acid-base properties. This behavior caused a high selectivity to methyl furoate.
The furfural can also be oxidized to produce maleic acid with hydrogen peroxide and a solid catalyst. Alonso-Fagundez and coworkers [69] used titanium silicalite as catalysts and studied the effect of temperature and of the concentration of H2O2. The catalyst was characterized by different techniques, and it found that the titanium was incorporated within the silicalite framework. Two furfural types (pure and derived from biomass) were used in the reactions. When in the reaction was used pure furfural, the catalysts raised six runs without deactivation. Still, when the furfural was derived from biomass, the system deactivated quickly due to the presence of organic compounds. The maleic acid can be dehydrated and produce Maleic anhydride. These compounds have many applications in the industry. They can be used in the manufacture of polymers, resins, pharmaceuticals, biofuels, each other. The oxidation of the furfural into maleic acid involves two steps; decarbonylation, which carries out 423-453 K, and oxidation. A noble metal catalyst is necessary for the two steps that help to avoid deactivation. They conclude that the titanium silicate is an excellent catalyst to obtain maleic acid from furfural.
Besides, V2O5/Al2O3 also was used in the gas phase oxidation of furfural to maleic anhydride. In this reaction was studied the temperature effect and an increase in the temperature of reaction contributed to the rise to maleic acid yield. The catalyst was characterized by different techniques; however, the solid is deactivate due formation of maleate and resins as a consequence of an increase of temperature. In this case, the yield of maleic anhydride was near 30%. Regeneration is carried out at high temperature (773 K). The best conditions of reaction were at 573 K using 1 vol.% furfural and 20 vol.% O2, to obtain 60% of maleic anhydride yield after 15 of reaction. Therefore, the high oxidizing potential of the reaction mixture favor the selective transformation to maleic acid and to prevent resin and maleate formation and subsequent deactivation [70].
In a recent study, Rezaei and coworkers [71]. used vanadyl pyrophosphate and zirconium pyrophosphate particles in the oxidation of furfural to maleic acid. The authors demonstrated that the synthesis of a mixture of vanadyl pyrophosphate and zirconium pyrophosphate supported on well-ordered mesoporous KIT-6, which favors the oxidation of furfural to maleic acid. The reaction conditions were 0.25 Zr/V ratio-loading at 70 °C with 3:1 (H2O2: furfural mole ratio), using acetonitrile as solvent. The solvent was chosen due to good solubility and polarity. In this case, the furfural conversion was 81.2 %, and the yield to maleic was 29.2 % at 1h of reaction. In the reuse test, the solids showed activity after four runs; however, the solid showed slight leaching of zirconium and vanadium, which was determined by ICP-AES analysis.
The support effect was also studied in the partial oxidation of furfural to maleic acid. Santander et al. prepared, characterized, and evaluated V2O5/SiO2, V2O5/ZrO2, V2O5/TiO2, and V2O5/y-Al2O3 solids in the gas phase reaction. V2O5/SiO2 and V2O5/y-Al2O3 catalysts exhibited the best catalytic performance, achieving a yield maleic acid of 50%. In this case, V2O5/y-Al2O3 was more selective to maleic acid that V2O5/SiO2. This behavior was attributed to good vanadium dispersion on y-alumina [72]. However, V2O5/ ZrO2 and V2O5/TiO2 increase the activity with the decrease in the oxidative conditions. In this case, these catalysts oxidized the furfural entirely to CO2 and H2O, and the maleic acid production was scarce. In spite that the performance of V2O5/ZrO2 and V2O5/TiO2 was not excellent, the oxidation potential of the reaction feed was decreased, and the maleic acid yield increased like V2O5/SiO2 and V2O5/y-Al2O3. On the other hand, the furfural can also be to furoic acid, another essential value product. Palombo Ferraz and coworkers [73] used the Au/MnO2 catalyst to obtain furoic acid form furfural at 110°C. This catalyst was prepared with different morphologies such as nanoflowers and nanowires. The systems were characterized and evaluate catalytically. Au/MnO2 nanoflowers showed a higher selectivity to furoic acid. The authors attributed this behavior to the presence of surface Aua+ species detected by XPS analysis. This catalyst also exhibited high surface area and pore volume, which contributed to excellent performance in this reaction. Roselli and coworkers [74] carry out the furfural oxidation in the liquid phase using pure oxygen and Au/hydrotalcite with Mg: Al ratios. Au/hydrotalcite system with 4:1 showed the total furfural conversion and the higher selectivity to furoic acid. This study also performed the stability tests and found that the Au/hydrotalcite showed leaching of Mg2+ cations.
Douthwaite and coworkers [75] prepared monometallic catalysts (Au/Mg(OH)2 and Pd/ Mg(OH)2) and bimetallic catalysts (AuPd/ Mg(OH)2) and were evaluated in the furfural oxidation. AuPd/Mg(OH)2 systems showed an excellent performance in the reaction. However, it was reused around five runs, and the TEM results indicated that the particles formed agglomerated. The catalysts contributed to the formation of furoic acid in two ways; direct oxidation to produce the acid and via aldehyde to acid furoic. Sometimes occurred parallel reactions such as polymerization, which conducted to form humins. Search for the term "furfural oxidation" in the Scienfider database, comprising works available from 1963 to 2020. The evaluations were limited to data published as papers (excluding reviews) and patents.
1.2 Bio CATALYTIC PROCESSES
An option to replace and improve the chemical methods is the oxidation or reduction biocatalytic. In biocatalysis the enzymes from microbial cells or whole cells are used for chemical transformations [37] even to obtain furan compounds or high-value molecules aggregate coming from biomass. The most important of this process is that the molecules obtained can be easily separated and produced under mild reaction conditions with high yield and selectivity, while maintaining high chemical purity and low or negligible by-product formation [30]. Although the furanic aldehydes are highly toxic to microorganisms [15], some microrganisms have developed a wide variety of defense mechanisms to degrade these compounds. The oxidation/ reduction reactions constitute the initial steps of the biological pathways for the degradation of FAL, which in turn produce alcohol and furan acid. These products are valuable in polymer chemistry, because these are renewable monomers. Furans can be oxidized following the Trudgill cycle.
Furoic acid enters the cycle of tricarboxylic acids (TCA) [40], and FAL can be reduced aerobically and anaerobically, generating furfuryl alcohol.
The whole cells are more used for transformation processes than isolated enzymes because these are economical, more stable and do not require complex regeneration systems [76]. The modern biotechnology and efficient DNA sequencing [38] have allowed for example, incorporate the bioinformatic analysis to identify possible genes involved in processes of interest, propose metabolic networks based on overexpress genes that encode a specific enzyme. In this sense, the search of microorganisms capable of tolerating FAL and transforming it into alcohols or acids furanic as the identification of the possible genes that encode the enzymes that microorganisms use to metabolize aldehydes furanic are the basis for possible large-scale production.
Successful industrial enzymatic examples using microorganisms in bioremediation strategies increasingly better for biorefinery [37] [39] are reported. Also, pathways of degradation of HMF/FAL have been established in some microorganisms such as Cupriavidus basilensis [40], Saccharomyces cerevisiae, Escherichia coli, Corynebacterium glutamicum [41]. However, information on metabolic pathways by which the furanic compounds are degraded is almost null. The genomes sequencing of some of these microorganisms has been used to broaden the understanding of the metabolic pathways involved in the regulation of these processes. For example, unifying the hydrolysis and fermentation of biomass in a single microorganism was performed, although the yields are not entirely successful [37]. At the biological level, studies using microorganisms and specific enzymes produced by them as catalysts for reactions of agro-industrial interest. Several oxidoreductases have been identified as the key enzymes in Saccharomyces cerevisiae, in enteric bacteria, or in consortia of microorganisms to oxidize or reduce compounds derived from biomass. Also, biochemical pathways have been postulated to explain the metabolism of furans. Enzymes such as oxidoreductases (dehydrogenases and oxidases) and decarboxylases have been identified in these routes [40] [77]. High concentrations of furan aldehydes have been evaluated in different strains; expression of genes related to tolerance and adaptation to general stress, central metabolism, transport and degradation of damaged proteins regulated positively, indicating a stress response throughout the system [78] [79]. Besides, genes encoding enzymes with furoyl-CoA dehydroge-nase activities were found [80].
With respect to isolated microorganisms, Boo-pathy et al. in 1993 [81], they evaluated the ability to transform furfural and 5-hydroxymethylfurfural from seventeen strains of enteric bacteria that included Enterobacter, Klebsiella, Escherichia, Citrobacter among others, the enteric bacteria were able to transform furfural to furfuryl alcohol or acid furoic if they followed an aerobic route, in the same way, the strains that grew in a glucose-peptone medium transformed approximately 95% of the furfural present in the medium in 24h. Subsequently, Sarvari Horvath et al., In 2003 [82], studied the effect of furfural on the aerobic metabolism of the yeast Saccharomyces cerevisiae during respiratory growth in the presence of glucose; the results obtained provided the basis for a metabolic flux analysis that was carried out under different substrate conditions, product formation, metabolic energy, and additionally, the effect that furfural has on the aerobic and anaerobic metabolism of yeast S. Cerevisiae In 2004, Mitsukura et al. [83], used aromatic aldehydes for the production of furoic acid using strains of Acetobacter and Serratia; and demonstrated with the batch-fed strategy, that the whole cells were able to oxidize the aldehyde and transform it into furoic acid with a conversion rate of 95% and 97% with Acetobacter and Serratia respectively, using commercial furfural. For this reason, Lopez et al., In 2004 [84], isolated and identified new microorganisms for the biological treatment of lignocellulosic hydrolysates, and selected some microorganisms according to their potential for the degradation of toxic compounds of acid hydrolysates. The fungal strain C. ligniaria C8 (NRRL30616), isolated and identified in the study, presented appropriate characteristics for the biological treatment of lignocellulosic hydro-lysates. In this process there are advantages over other detoxification treatments that include the complete elimination of furfural and 5-HMF, the minimum nutrient requirements and the possibility of performing detoxification in one step without additional manipulation, however it could not be proven if the substrate was completely metabolized by the whole cell or only transformed into a compound less toxic to it. This is why in 2012, Zhang, Han, and Ezeji [85], studied the ability of Clostridium acetobutylicum 824 to tolerate furan aldehyde inhibitors (furfural and HMF) and improve the bioconversion of lignocellulosic biomass hydrolysates to fuels and chemicals, and demonstrated that furfural and HMF were converted to furfuryl alcohol and 2,5-bis-hydroxymethylfuran, respectively. However, Zhou, Zhou, and Chen in 2016 [86] used a strain of Gluconobacter oxydans (ATCC621H) that catalyzed the oxidation of furfural and furfuryl alcohol to produce furoic acid; this transformation was carried out with a fed-batch strategy, optimizing the fed-batch process until obtaining furoic acid concentrations greater than 40 g/L with a productivity of 0.167 g/Lh and yield of almost 100%. In turn, Kudahettige Nilsson et al. in 2016 [87] studied the effects of inhibitors of phenol, levulinic acid, HMF (hydroxymethylfurfural) and furfural on the growth and enzymatic activity of different microorganisms, demonstrating that microorganisms can grow and degrade lignocellulosic inhibitors. Recently, in 2017, Singh et al. [76] isolated a soil bacterium (Bordetella sp. BTIITR) that showed the ability to degrade furfural (100%) and HMF (80%) present in a hydrolyzed lignocellulosic liqueur. Thus, Wang et al., In 2018 [41], used the long-term adaptive evolution of the strain Coryne-bacterium glutamicum S9114 to make it tolerant to the inhibitor, by means of the continuous transfer every 24h to the inhibitors present in a corn stubble hydrolyzate.; after 128 days the strain showed a high conversion rate of the typical inhibitors of lignoce-llulose derivatives, where from 1 g/L of furfural in the medium converted 0.9 g / L in 2h.
According to the above, the toxicity triggered by the FAL on the different microorganisms is reason to study, optimize and improve the processes of oxidation, where the metabolic capacity of the microorganisms can be improved for the production of the corresponding alcohol or carboxylic acid, generating economic viability in the process; Likewise, most of the described organisms also inhibit or rapidly consume the products formed, this causes that it is often not clear to what extent the furanic compounds are actually metabolized.
With respect to the enzymes involved in the furfural degradation process, in 2002, Modig, Liden, and Taherzadeh [88] evaluated in vitro the kinetics of furfural inhibition of the alcohol dehydrogenase (ADH) enzymes, aldehyde dehydrogenase and the complex pyruvate dehydrogenase (PDH); where the inhibition caused by HMF of ADH was very similar to that caused by furfural. The effects of inhibition on the three enzymes could well explain previously the effects caused by furfural and HMF on the global metabolism of S. cerevisiae, suggesting a critical role since inhibition was observed in these enzymes. Petersson et al. in 2006 [89], an alcohol dehydrogenase VI (ADH6) was overex-pressed in yeast strains, observing a substantially higher in vivo conversion rate of HMF and furfural in both aerobic and anaerobic cultures [90]; in addition, by overexpressing ADH6 with a cofactor, preferably NADH, the degradation activity was 3.9 times higher than in the control strain. Gutiérrez et al. in 2006 [91] they purified and characterized a furfural reductase enzyme (FFR), in the strain Escherichia coli LYO1; that catalyzed the reductive detoxification of furfural to furfuryl alcohol; the activity exhibited by this enzyme was maintained at the same level (60% of its Vmax) when it was in reaction with furfural concentrations of 5 and 10 mM. However, it was reported that increasing concentrations of furfural (5-20 mM) affected the growth and metabolic rates of the LYO1 strain in Luria Bertani medium. Almeida et al. in 2008 [92], they used Pichia stipitis xylose reductase (Ps-XR) to transform strains of S. cerevisiae that can ferment xylose and showed that strain TMB3400 not only converts xylose but also shows a greater tolerance to lignocellulosic hydrolyzate, as well as 3 times greater in vitro reduction activity of HMF and furfural than the control strain; it is also important to note that the overexpression of Ps-XR increased the conversion rate of HMF in vivo by approximately 20%, thus improving the tolerance of the yeast towards HMF.
Liu & Moon in 2009 [93], reported the cloned gene of an aldehyde reductase enzyme in S. cerevisiae, which proved to be dependent on NADPH in reduction activities and was also able to survive at different concentrations of furfural and 5-HMF in comparison with the strain without gene insertion. Moon & Liu in 2012 [94], improved the aldehyde reductase activity of the GRE2 gene of S. cerevi-siae towards HMF and furfural using the mutation of the enzyme; in this study, the enhanced activity of aldehyde reductase in yeast strains was shown by overexpressing mutated GRE2. Additionally, Wang et al, in 2015 [95] identified Aldo-ketoreduc-tases, aldehyde reductases and aldehyde dehydro-genases responsible for the degradation of furfural and HMF to the corresponding alcohols and acids in A. resinae ZN1 and provided important information to understand the mechanism of degradation of furfural and degradation of HMF[96]. Tsuge etal., In 2016 [97], studied an alcohol dehydrogenase enzyme involved in the process of reducing furfural to furfuryl alcohol in Corynebacterium that accelerated the detoxification of furfural by its conversion to furfuryl alcohol and 2-furoic acid. Recently, Yee et al. 2018 [98] studied the degradation of furfural and 5-hydroxymethylfurfural using recombinant manganese peroxidase produced by the yeast Pichia pastoris and demonstrated that the treatment based on Manganese peroperoxidase (MnP) was able to detoxify the solutions of furfural and HMF for subsequent fermentation with microorganisms [99]. Besides, the enzymes that have been found in the degradation pathway of furfural for some microorganisms among which are Cupriavidus basilensis, Saccharomyces cerevisiae, Escherichia coli, Pichia stipitis, Amorphoteca resi-nae, Corynebacterium glutamicum, among others; It is very important to emphasize that the genetic and biochemical characterization of the microbial metabolism of enzymes capable of degrading furans has great potential for industrial applications from lignocellulosic hydrolysates.
CONCLUSIONS
The utilization of lignocellulosic biomass represents an attractive and promising strategy for green and sustainable energy production due to its low cost and abundance. Furfural is considered a building block molecule that takes significant attention due to their applications as biofuels and value-added compounds. Furfural and its derivatives have been extensively used as transportation fuel, gasoline additives, lubricants, jet fuel blends, and in agrochemical and pharmaceutical industries. The hydrogenation of furfural is one of the most versatile reactions from where furfuryl alcohol can be obtained. This reaction can be carried out in gas or liquid phase. The furfural hydrogenation is performed at different reaction temperatures, hydrogen pressures, metal, and supports that allow study and understanding of furfuryl alcohol. The furfural can also be used in oxidation and oxidative esterification reactions to produce maleic acid, furoic acid, and methyl furoate. In these reactions sometimes are employed H2O2 and pure oxygen. The conventional catalysts are golden supported catalysts and mixed oxides, which favor the catalytic performance and the interest products. However;Bio catalytic transformation of Furfural could be considered a degradation alternative with great potential for industrial applications with a possible large-scale production of different derivatives.