Services on Demand
Journal
Article
Indicators
-
Cited by SciELO
-
Access statistics
Related links
-
Cited by Google
-
Similars in SciELO
-
Similars in Google
Share
CT&F - Ciencia, Tecnología y Futuro
Print version ISSN 0122-5383On-line version ISSN 2382-4581
C.T.F Cienc. Tecnol. Futuro vol.4 no.5 Bucaramanga Jan./June 2012
ABSTRACT
This study used two Colombian petroleum pitches (an asphalt and a precipitate) to determine their capacity as precursor of carbonaceous materials. In order to obtain the mesophase, pitches were oxidized at temperature of 350°C and oxidation times of 2; 3 and 5 hours. Oxidized pitches were fractioned with toluene using a ratio of 20 mL Toluene/g of oxidized bitumen. Insoluble material in Toluene (IT) and Tetrahydrofurane (ITHF) were carbonized with nitrogen at 400°C. For the identification of the mesophase, specimens were fabricated with the material obtained from carbonization. For the quantification of the mesophase, a microscope with polarized light filter was used. A total of 500 points were counted. The results showed that the asphalt treated with the longest oxidation time, contained higher concentration of mesophase. By contrast, the precipitate treated with the shortest oxidation time produced higher concentration of mesophase.
Keywords: Pitch, Oxidation, Asphalt, Characterization, Precursor, Carbonization.
RESUMEN
Este trabajo usó dos breas de petróleo colombianas (un asfalto y un precipitado) con el fin de determinar su capacidad como precursor de materiales carbonosos. Para la obtención de la mesofase, las breas se oxidaron con aire a la temperatura de 350°C y a tiempos de oxidación de 2; 3 y 5 horas. Las breas oxidadas se fraccionaron con tolueno usando una razón de 20 mL Tolueno/g de brea oxidada. El material Insoluble en Tolueno (IT) y en Tetrahidrofurano (ITHF) se carbonizó en atmósfera de nitrógeno a 400°C. Para la identificación de la mesofase se fabricaron probetas con el material obtenido de carbonización. Para la cuantificación de la mesofase se utilizó un microscopio con filtro de luz polarizada. Un total de 500 puntos fueron contados. Los resultados mostraron que el asfalto presentó alta concentración de mesofase usando altos tiempos de oxidación. Por el contrario, el precipitado produjo altas concentraciones de mesofase a bajos tiempos de oxidación.
Palabras clave: Brea, Oxidación, Asfalto, Caracterización, Precursores, Carbonización.
RESUMO
Este trabalho usou dois breus de petróleo colombianos (um asfalto e um precipitado) com a finalidade de determinar a sua capacidade como precursor de materiais carbonosos. Para a obtenção da mesofase, os breus se oxidaram com ar na temperatura de 350°C e a tempos de oxidação de 2; 3 e 5 horas. Os breus oxidados se fracionaram com tolueno usando uma razão de 20 mL Tolueno/g de breu oxidado. O material Insolúvel em Tolueno (IT) e Insolúvel em Tetrahidrofurano (ITHF) se carbonizou em atmosfera de nitrogênio a 400°C. Para a identificação da mesofase se fabricaram provetas com o materia obtido de carbonização. Para a quantificação da mesofase se utilizou um microscópio com filtro de luz polarizada. Um total de 500 pontos foi contado. Os resultados mostraram que o asfalto apresentou alta concentração de mesofase usando altos tempos de oxidação. Pelo contrário, o precipitado produziu altas concentrações de mesofase a baixos tempos de oxidação.
Palavras chave: Breu, Oxidacao, Asfalto, Caracterizacao, Precursores, Carbonizacao.
1. INTRODUCTION
One of the prevalent problems in the processing of heavy crudes is the production of isotropic bitumen/pitches, which are by-products of heat treatment and distillation of both oil and coal liquid extracts. The isotropic pitches represent the main contributor to the formation of coke and produce some difficulties in the processes of hidro rupture and hidro refining (Verkoczy, 1993). At high temperatures, the isotropic pitches are polymerized and cause clogging of the catalytic beds, piping and equipment. Colombia is not immune to this problem because it processes some heavy crudes from fields such as San Fernando, Rubiales and Castilla (Barraza, Camargo, Bermudez & Velasco, 2009). Due to the difficulties stated above, alternatives must be found to eliminate, reduce or give added value to those isotropic pitches before entering the refining process or after they are produced.
The isotropic pitches are widely available and economically represent a promising raw material in the production of carbonaceous materials with high added value such as fibers, activated carbons, anodes for the aluminum industry and electrodes for lithium ion batteries, among others. (Ozel & Bartle, 2002; Diefendorf & Riggs, 1980). The pitch are usually composed of four fractions: 1) aliphatic saturated components of low molecular weight similar to that of wax; 2) naphthalene aromatic compounds, which have low molecular weight with saturated rings; 3) polar aromatics compounds of medium molecular weight with some heterocyclic molecules and 4) asphaltenes of high molecular weight and degree of aromaticity. It is known that desired pitch to produce high performance carbon mesophase must be thermally stable and exhibit high proportion of asphaltenes and high softening point (Ozel & Bartle, 2002).
Before producing the value-added carbon materials, the isotropic pitches must be thermally processed to obtain a non-isotropic (anisotropic) material called mesophase or mesophase pitches, which is composed of molecules having aromatic structure to acquire forms of liquid crystals optically sorted by their molecular interactions. This treatment is done because the isotropic pitches do not present optically aligned molecules, where by the fibers produced by these pitches are inferior to those of mesophase pitches. Several papers have been published about producing mesophase starting from different raw materials and processes. Machnikowski, Machnikowska, Brzozowska and Zieliński (2002) used mixtures of petroleum pitches with various polymers and found that the presence of the polymers modifies the kinetics of the conversion and the development of the morphology of the mesophase. McHenry (1995) and Perez, Granda, Santamaria and Menendez (2003), mixed petroleum pitches with liquid coal pitches achieving growth of mesophase particles of spherical shape. In addition to them, Mora et al. (2003) studied the carbonization of mixtures of petroleum pitches and coal liquids focusing on the formation and development of the mesophase and the role of quinolone insolubles.
Various treatments have been used to modify the composition and properties of the pitch looking for increase carbonization yields and mesophase production. Mochida et al. (1975a) used carbonizations of aromatic hydrocarbon with alkali metal type catalysts. Mochida, Nakamura, Maeda and Takeshita (1975b) carbonized petroleum pitches using aluminum chloride catalysts. Meanwhile, Kanno et al. (1994) evaluated the effect of adding black carbon on the carbonization of mesophase. In most of the mentioned studies, the insoluble materials in solvents are carbonized once they are separated. This leads to a decrease in yields in the production of material with mesophase because volatile components are released at high carbonization temperatures. An approach that is being taken presently is to pre-concentrate the carbonaceous material from the insoluble material using oxidation processes at low temperatures (Oh & Park, 1999). In our country, some work has been done in the area of producing mesophase. de López (1990) study must be highlighted where mixtures of mesophase pitch were prepared with isotropic pitches of naphthalene and anthracene at l0 and 30% w/w looking for improve the softening point and the stabilization time of the threading. Rincón, Carvajal and Pacheco (1985) studied the anisotropic development of a low rank coal from the Cerrejon mine induced by a heavy crude or anthracene oil at 500°C. In this study, the effect of using the oxidation process in two Colombian isotropic pitches on the properties and the production of carbon mesophase was evaluated.
2. EXPERIMENTAL DEVELOPMENT
Materials
Two pitches from the Ecopetrol S.A. company were used: bottom of the distillation column (Asphalt, A) acquired commercially, and an insoluble material from the crude from Castilla with the Apiasol solvent (Precipitate, P) provided by the Instituto Colombiano de Petróleo (ICP). Toluene and Tetrahydrofuran (ITHF), analytic grade, were used as solvents for the oxidized pitch and epoxy resin was used for the optical microscopy analysis of the mesophase produced. Suspensions of alumina of 0,05; 0,30 and 0,50 microns were used for the polishing of the specimens.
Equipment
A glass reactor with three nozzles was used: for air feeding, measuring the temperature of oxidation and evacuating volatile matter produced. The reactor was fitted with a heating mantle to obtain the desired temperatures, and with a rotameter to measure the airflow. Filtering of the insoluble fraction in solvents was performed on a Buchner vacuum system. Carbonization and the obtaining of the mesophase were conducted in a muffle. For the preparation and polishing of the specimens a Labopol-5 machine was used fitted with adhesive discs and polishing cloths. The mesophase obtained was identified and characterized in a metallographic microscope Eclipse LVD 100 under light reflected with a polarized light filter and objective with a magnification of 50X.
Experimental Procedure
Initially the two pitches were characterized according to their softening point (Sp). The Sp was determined by adding 1 g of sample pre-asphaltene and asphaltene independently in a Petri PYREX box, then the sample was placed on the hot plate and a temperature increase of 5°C every 2 minutes was performed. This procedure was performed until the solid material took on a liquid appearance. The temperature at which this change of phase was observed corresponds to the softening point of the sample.
Toluene Insoluble fractions (IT) and Insolubles in THF (ITHF) were determined by taking 20 mL of solvent per gram of pitch, and were subjected to reflux and filtration in a vacuum. The results of Sp, IT and ITHF are presented in Table 1.
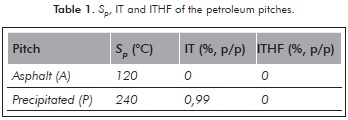
The results of Table 1 showed there was no production of insoluble fraction using toluene and THF. Therefore, the two pitches were initially subjected to an oxidation process, then to an extraction process with solvents and finally, to a carbonization process. This procedure differs to that used by Srivastava et al. (2008) who oxidized pitch as a previous step to the carbonization. It is highlighted that the treatment of the two pitches to form mesophase without any prior oxidation was not performed because it was not considered in the experimental design.
During the oxidation process, 40 g of each pitch was charged to the reactor by passing an air flow of 20 mL/min at a temperature of 350°C. Three oxidation times were used: 2; 3 and 5 hours. The yield of oxidation was calculated on the basis of the amount of volatile matter that was removed during the reaction.
Subsequently, the oxidized organic material produced was macerated in order to increase the contact area with the solvent and then subjected to a reflux system at a temperature of 115°C using a ratio of 20 mL Toluene/gram of pitch during 1 hour. Then, the mixture was filtered and the insoluble material was taken to the drying oven at a temperature of 110°C to ensure all the toluene was evaporated, leaving the insoluble to constant weight. The amount of insoluble matter in toluene was calculated by the ratio insoluble weight after drying (Bs)/weight of pitch fed (Bi). The process of carbonization of insoluble oxidized material in toluene was performed in a muffle with inert atmosphere, which was achieved with a nitrogen flow of 40 L/h. The muffle worked at 400°C with a heating rate of 2,5°C/min for 1 hour. 3 g of samples of ITHF and IT, solvent free, were used in the carbonization.
The samples obtained from carbonization were prepared for later analysis of the mesophase produced in the microscope. The epoxy resin where the polymerized sample was embedded it was prepared by mixing 1mL of resin with 1mL of hardener and mixed until it was homogeneous. Then the resin was mixed with 2 g of pitch to be analyzed until it was a uniform mixture, which was then placed in a vacuum system during 5 minutes to remove the bubbles present. Once it was completely dry and hard, the specimen was roughened with sandpaper No. 150; 600; 1000 and 1200. Finally a polishing machine was used with polishing cloths using alumina of 0,50; 0,30 and 0,05 microns.
The insoluble oxidized and carbonized material was analyzed under a microscope to identify and count the mesophase. This was carried out using a light polarizer in the microscope, as the mesophase have anisotropic properties, i.e., reflecting different characteristics depending on the direction of incidence of light. Counting was performed with an eyepiece setting of 10x and an objective lens of 50X (total magnification of 500). Mesophase content in the specimens was determined using an analysis of 500 effective points selected in an orderly manner to 0,5 mm from a point to point. The microscope has an adapted capture image system using the software LUCIA 5.3, which facilitated the identification and counting, in order to determine the volume content of mesophase in the pitch.
Finally, to ensure the presence of mesophase in the carbonized samples, several specimens were analyzed in a microscope with polarized light equipped with a retarder plate of 1/4 λ wavelength, located in the petrography laboratory of the Penn State University (State College, U.S.A.) The specimens were examined optically and photographs of the mesophase were taken.
3. RESULTS AND DISCUSSION
Oxidized Pitch Yields
Figure 1 shows the yields of the carbonaceous material obtained during the oxidation process at 350°C. The yield of the oxidized pitch was calculated using Equation 1.
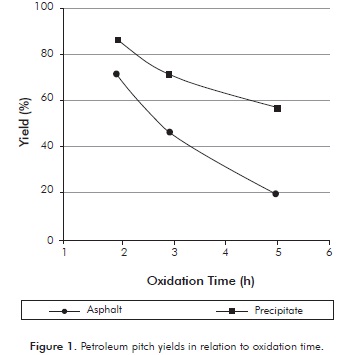
Where, R represents the mass yield of oxidation, %; mf the final mass of oxidized pitch in g, and mi, the initial mass of pitch charged to the reactor, g.
The results show that in general for both pitches, the longer the oxidation time the mayor decrease in production of carbonaceous material. This may be caused because the links of the light components are destroyed in their entirety and there is higher release of volatile material. The asphalt obtained after 2 hours of oxidation showed a yield of 72 and, 19% was obtained after to 5 hours, indicating a large difference in the final mass. This may be because the initial amount of volatile matter in the asphalt is high. This effect does not occur in the precipitate, since the variation in yield is of 30,2% between the highest and lowest oxidation time, suggesting that the insoluble precipitate in Apiasol can have high concentrations of heavy asphaltenic and pre-asphaltene compounds. Oxidized pitch yields obtained at different times do not imply that there is a greater or lesser production of mesophase. However, those results are important in the mass balance of the production of mesophase and to show that the precipitate has more heavy components than asphalt.
IT and ITHF Content of Oxidized Samples
The contents of IT and ITHF from the two oxidized pitches are shown in Figure 2. Toluene is a solvent with high capacity to solubilize the asphaltenes and lighter components, such as oils or saturated components, as well as the aromatic components of naphthalene, and has no ability to solubilize the heavier asphaltenes, pre-asphaltenes and the residue. Meanwhile, the ITHF is a solvent that presents a solubility parameter greater than toluene, as it can solubilize the majority of components present in the pitch, leaving in the insoluble fraction the residue and some pre-asphaltenes.
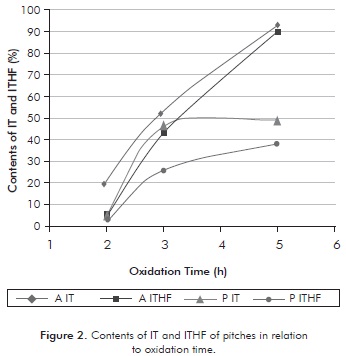
The data of Figure 2 show that in general for all times of oxidation and types of pitch, the content of THF was lower than toluene, which ensures that the THF has a higher solubility parameter. Tests to 5 hours (A5H) with oxidized asphalt using toluene and THF, produced the highest percentages of insoluble material, indicating it is an oxidized bitumen rich in heavy compounds. However, in these operating conditions the difference between IT and ITHF was low (2,9%); showing that most of material could be residue with a very low percentage of pre-asphaltic material.
Comparing the behavior of insolubility of the two pitches, it is observed that in general at all times of oxidation, the oxidized precipitate produced a lesser amount of IT and ITHF compared to the oxidized asphalt. This behavior is probably due to the fact that the amount of asphaltene present in the precipitate is greater than that of the oxidized asphalt, also, because the amount of pre-asphaltenes is greater in the latter. It was also observed that the lowest percentage of insolubility of all runs is presented in the test with the precipitate at 2 hours of oxidation (P2h), indicating that oxidation had no major impact and the components of low and medium molecular weight remained present. Figure 2 indicates that the solubilization with oxidized precipitate to 3 hours (P3h) showed the greatest difference (20,1%) between the IT and ITHF, indicating strong presence of pre-asphaltenes in the treated precipitate, which have high percentages of components of high molecular weight and high degree of aromaticity.
The most favorable operating conditions of reaction for the insolubility of the pitches treated was a reaction time of 3 hours, which showed a high degree of insolubility desired, and an appreciable difference between the IT and ITHF, ensuring the presence of pre-asphaltenes in the treated pitch. As seen in Figure 2, the asphalt and the oxidized precipitate have different trends of solubility, since the behavior of asphalt treated is almost linear and the precipitate tends to form a treated asymptote in the range of 40-50% of insolubles after the third hour of reaction. This difference is due to the nature of each of the pitches. Meanwhile, the curves of insolubility of IT and ITHF of oxidized asphalt show the same linear tendency with the time of oxidation. However, there is very little difference between them, which is harmful because a considerable amount of asphaltenes in the oxidized bitumen to be polymerized cannot be ensured.
IT and ITHF insolubility curves of the precipitate treated both have the same shape but with a wide range of difference, particularly in the zone of oxidation time of 3 hours. This indicates that one could get good amount of pre-asphaltenes with the oxidized precipitate. In the production of mesophase the material that polymerizes corresponds to the insoluble part of the toluene of the oxidized petroleum pitch. This implies that the material has very heavy components, such as residue and pre-asphaltenes, and very few asphaltenes.
Optical Texture of Oxidized Carbonized Pitch
Production of mesophase was carried out during carbonization, which was undergone under the same conditions for all runs. The identification of the mesophase in the carbonized was conducted in the microscope using a light polarizer. The isotropic pitch shows no change when polarizing the light and on the other, anisotropic pitch (mesophase) shows different behaviors when the light was reflected from different angles of polarization. Figure 3 shows particles of mesophase, isotropic pitches that showed no change in color and resin.
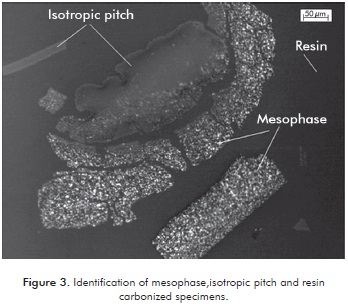
The mesophase is visible under certain direction of incidence of light, therefore, for the characterization of each pitch the microscopes polarizer is rotated so that the full effect of the direction of light may be seen there by identifying the pitch of the mesophase from the isotropic pitch. Figure 4 shows the effect of the angle of polarization on reflection of light of the particles. In Figure 4a, all the particles show the same behavior due to the fact that the polarization plates are fully open (higher angle of incidence). When rotating the polarizer (lower angle of incidence or plates partially open), there were changes in the reflection of light as seen in Figures 4b to 4d, which shows that some particles that shine correspond to a formed mesophase.
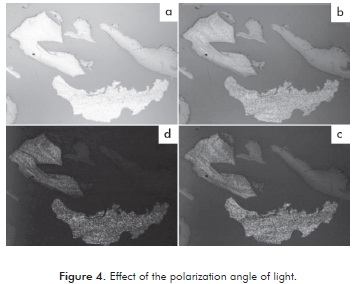
Figures 4b to 4d shows that, despite having produced mesophase they have no sphere form. Possibly the particles of the asphalt pitch and precipitate subjected to carbonization and oxidation process, had a sphere formation in a shorter time of carbonization, which rapidly coalesced. Machnikowski et al. (2002) found that the formation of mesophase spheres occurs in a period between 0,5 to 2 hours.
Mesophase Count on Carbonized Elements
The mesophase count was made taking only effective points into account, i.e., points where the intersection of the two axes (center point) indicates mesophase or isotropic pitch. If the point falls in resin it is not taken into account for counting. Figure 5 shows examples of the counted points. Figures 5a, 5b and 5c correspond to points of mesophase, isotropic pitch and resin, respectively. As seen in Figure 5b, some particles do not produce mesophase. However, they have been partially oxidized, as presented at the outer edge thereof. This behavior may be due to the resistance to diffusion of O2 into the interior of the particle.
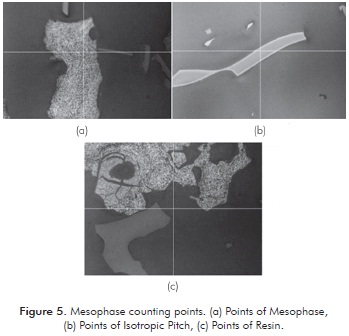
Figure 6 shows the percentage (% v/v) of mesophase in the carbonized samples, obtained for the two oxidized pitches in relation to different oxidation times and at the same temperature. As seen in Figure 6, there are differences in the production of mesophase from both carbonized pitches. Increased production of mesophase (61%) was obtained using oxidized asphalt for 5 hours, which can be explained by the high presence of pre-asphaltenes and residue present in the asphalt. For its part, the oxidized precipitate contained a high concentration of mesophase (55,8%) at low oxidation times (2 hours), which is related to the high presence of asphaltenes favor the production of mesophase.
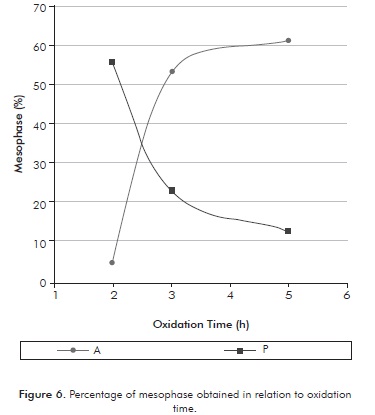
On the other hand, Figure 6 shows that the concentration of mesophase from the asphalt and the precipitate shows contrary behavior. An increase of oxidation time favors the production of mesophase coming form the asphalt, but discourages the production of mesophase from the precipitate. These behaviors are related to the chemical composition of the pitches, because, as shown in IT and ITHF testing, there is a difference in the concentration of asphaltene, pre-asphaltene components and residue between the pitches used. It was also observed a significant change in mesophase production in the runs between 2 to 3 hours of reaction in both pitches. However, after 3 hours of reaction, the production of mesophase tends to be constant.
To ensure the presence of mesophase in carbonized samples, several samples were analyzed in a microscope with polarized light containing a retarder plate of 1/4-λ wavelength located in Penn State University (U.S.A.). This was done in order to find major differences and details in color compared to images obtained in black and white taken in the petrography laboratory of the Universidad del Valle. The photographs of mesophase from asphalts are shown in Figure 7.
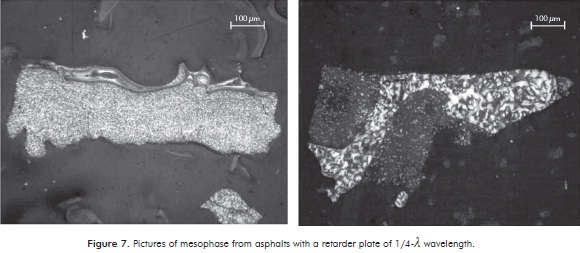
4. CONCLUSIONS
-
Carbon mesophase was obtained from two Colombian petroleum pitches. Oxidized asphalt to 5 hours produced the highest concentration of mesophase (61% v/v) while the precipitate of oxidized crude to 2 hours produced a mesophase with concentration of 55,8% v/v. The two pitches presented different behaviors in relation to oxidation time towards the conversion of mesophase. The asphalt is favored by using oxidation times greater than 3 hours, while the precipitate is favored by low oxidation times (close to 2 hours).
-
It was also found that the oxidized asphalt at 5 hours showed the highest value of IT (93%), indicating that this pitch is favored by the amount of pre-asphaltenes and residue present for the conversion of mesophase. The oxidized precipitate to 2 hours showed low values of IT (4%), indicating that this pitch is favored by the amount of asphaltenes and pre-asphaltenes present for the conversion of mesophase.
-
Mesophases produced do not have spherical characteristics, which may be due to the nature of the pitch or operating conditions. ITHF values and softening temperatures are high but are in the ranges of operation of the carbon fibers.
ACKNOWLEDGMENTS
The authors wish to thank Professor Semih Eser of Penn State University (State College, USA) for his help in the mesophase optical analysis of samples processed in the Petrography laboratory of this University. Thanks to the Instituto Colombiano de Petróleo (ICP) for the donation of precipitated samples with Apiasol.
REFERENCES
Barraza, J., Camargo, R., Bermúdez, V. & Velasco, F. (2009). Análisis termogravimétrico de concentrados resino-asfalténicos procedentes de crudos colombianos. VIII Congreso colombiano de carbón y energías alternativas, Universidad Nacional, Bogotá. [ Links ]
de López, H. (1990). Modificación de brea de mesofase. Revista Colombiana de Química, 19 (1), 115-122. [ Links ]
Diefendorf, R. & Riggs, D. (1980). U.S. Patent Num. 4,208,267. Forming optically anisotropic pitches. [ Links ]
Kanno, K., Yoon, K., Fernández, J., Mochida, I., Fortin, F. & Korai, Y. (1994). Effects of carbon black addition on the carbonization of mesophase pitch. Carbon, 32 (5), 801-807. [ Links ]
Machnikowski, J., Machnikowska, H., Brzozowska, T. & Zielinski, J. (2002). Mesophase development in coal-tar pitch modified with various polymers. J. Anal. Appl. Pyr., 65 (2), 147-160. [ Links ]
McHenry, E. (1995). Coal-tar /petro industrial pitches. Light Metals: Proceedings of Sessions, TMS Annual Meeting (Warrendale, Pennsylvania), 543-548. [ Links ]
Mochida, I., Kudo, K., Fukuda, N., Takeshita, K. & Takahashi, R. (1975a). Carbonization of pitches-IV: Carbonization of polycyclic aromatic hydrocarbons under the presence of aluminum chloride catalyst. Carbon, 13 (2), 135-139. [ Links ]
Mochida, I., Nakamura, E., Maeda, K. & Takeshita, K. (1975b). Carbonization of aromatic hydrocarbons-III: Carbonization catalyzed by alkali metals. Carbon, 13 (6), 489-493. [ Links ]
Mora, E., Santamaría, R., Blanco, C., Granda, M. & Menéndez, R. (2003). Mesophase development in petroleum and coal-tar pitches and their blends. J. Anal. Appl. Pyr., 68-69: 409-424. [ Links ]
Oh, S. & Park, Y. (1999). Comparative studies of the modification of coal-tar pitch. Fuel, 78 (15), 1859-1865. [ Links ]
Ozel, M. & Bartle, K. (2002). Production of mesophase pitch from coal tar and petroleum pitches using supercritical fluid extraction. Turk. J. Chem., 26 (3), 417-424. [ Links ]
Pérez, M., Granda, M., Santamaría, R. & Menéndez, R. (2003). Preventing mesophase growth in petroleum pitches addition of coal-tar pitch [2]. Carbon, 41 (9), 1854-1857. [ Links ]
Rincón, J., Carvajal, R. & Pacheco, L. (1985). Measurement of anisotropic development in a low-rank coal using e.s.r. spectroscopy and optical texture. Fuel, 64 (1), 119-122. [ Links ]
Verkoczy, B. (1993). Factors affecting coking in heavy oil cores, oils and SARA fractions under thermal stress. J. Canadian Petrochemical Tech., 32 (7), 25-33. [ Links ]
Srivastava, M., Singh, R., Manoj, K., Agarwal, U. & Garg, M. (2008). Influence of oxidative and non-oxidative conditions on petroleum pitch properties. J. Scientific & Industrial Research, 67: 616-621. [ Links ]