1. INTRODUCTION
Crude oil is a complex mixture of hydrocarbons, consisting of non-polar n-paraffins and polar components such as asphaltenes. When the density of crude oil is equal to or less than 20 API, it is categorized as heavy crude oil (Gerez & Pick, 1996). However, once the density drops to 10 API or less, it becomes extra-heavy oil or bitumen, weighing more than water. Its high viscosity, density, and impurity content, including sulfur and metals, hinder natural surface flow, requiring pumping techniques for extraction (Rahmes & Nelson, 1948; Anhorn & Badakhshan, 1994). According to the International Energy Agency (IEA), heavy crude oil represents a significant portion of the world's recoverable oil resources (Strelets & Ilyin, 2021). The Llanos Oriental basin, located in central eastern Colombia and spanning approximately 87.105 square miles, contains heavy and extra-heavy crude oil reserves (Ruiz et al., 2014). Electro-submersible pumping equipment is highly regarded for efficiently handling viscous fluids and suspended solids (Salah et al., 2023). These devices offer various benefits in heavy oil production, including:
Viscous fluid handling: Electro-submersible pumping equipment is designed to operate effectively with high-viscosity crudes, making it well-suited for heavy oil wells.
Improved energy efficiency: The ESP electric motors render superior efficiency compared to other motors in the oil industry, leading to reduced energy consumption and operational costs.
Versatile configuration: ESP equipment can adapt to diverse production conditions, allowing for adjustments in flow rate and pumping pressure according to well requirements.
Reduced surface footprint: As these devices are placed within the well, electro-submersible pumping equipment requires less surface infrastructure, resulting in reduced surface costs compared to other pumping systems.
During the initial exploitation of the San Fernando formation, several challenges emerged, including organic and inorganic compound precipitation, strong emulsions, higher rates of electro-submersible equipment failure due to motor overstressing, and elevated wellhead pressures. The production of heavy crude oil increases viscosity, leading to greater resistance to flow and decreased production rates (Shu, 1984; Hénaut et al., 2001).
To maintain the integrity of the ESP equipment, the main challenge is the tendency of San Fernando formation fluid to cause scaling. As a result, the electrical submersible pumping equipment is designed with a capillary to chemically treat the bottom to prevent the formation of scale. However, recent issues have arisen, including increased bottom pressure and operational instabilities such as pump inlet pressure, pump discharge pressure, motor temperature, pump inlet temperature, and vibration due to the high production of heavy crude oil. Consequently, there is a need to enhance the mobility of crude oil through bottom chemical treatment, which requires an additional capillary in the ESP design (Shuler et al., 2010). This is due to the oil-based fluidity improver and the water-based scale inhibitor being incompatible for application within the same capillary.
This technical article presents a case study conducted in the Apiay Field. It focuses on the downhole application of a fluidity improver and a scale inhibitor using a single capillary. The results show improved production, energy efficiency, and cost optimization.
2. STATE OF THE TECHNIQUE
The use of electro-submersible equipment is an attractive option for wells with high production rates, especially in heavy and extra-heavy oil wells located in deep reservoirs.
In the Apiay field, water-soluble scale inhibitors, including barium sulfate, calcium carbonates, and calcium sulfate, commonly found in oilfield production systems, are used to prevent scale deposition. These inhibitors contain an active compound, a slightly acidic anionic phosphonate, and are stable in solutions down to -4°C. They also have significant calcium tolerance (50.000 ppm). Continuous application through a capillary is essential to ensure inhibition in producing wells.
Additionally, the flow improver reduces turbulent eddies, interacting with fluid molecules to minimize deviations in velocity and channel hydraulic energy to propel the fluid stream through the pipe more efficiently. This reduces frictional pressure losses, empowering pipeline operators to lower operating pressure or increase fluid flow rates.
Since 2020, many wells have been equipped with a single capillary, which has made initiating downhole flow improver treatment challenging. To address this, ChampionX developed a flow improver that can be administered via a single capillary alongside the scale inhibitor, dispersed in the aqueous phase to avoid chemical incompatibility issues and enable concurrent application with the scale inhibitor via capillary.
The testing methodology involved the following steps:
Establishing baseline information including equipment operating conditions, fluid characteristics, and oil production volume.
Evaluating the performance of two chemical products (scale inhibitor and fluidity improver) at concentrations of 30 ppm and 1.000 ppm, respectively; these concentrations were made based on technical recommendations for each chemical product (Barton, 2017). The application was carried out using a single downhole capillary at the equipment sensor's level.
Monitoring trends in operating variables, stability of the electro-submersible equipment, chemical dosing, measurement of scale inhibitor residuals at the wellhead, characterization of water's physical chemistry, production fluid tests, and measuring energy consumption of each piece of equipment.
The test was conducted in five producing wells of the San Fernando formation, each equipped with a single capillary. Operating variables of the electro-submersible equipment and production fluid tests were closely monitored to comprehensively evaluate the pilot test outcomes.
3. RESULTS
The first part of the analysis involved establishing the baseline for the test. The selected wells had shown no operational issues or drastic changes in their chemical characteristics over the past six months. These data (Fluid production, energy consumption, and operational parameters) were stored for comparison in subsequent stages. Due to confidentiality agreements between the companies involved in this pilot, the baseline information cannot be shared in this paper.
The following step implied conducting laboratory tests to ensure the two alternatives' chemical compatibility, and avoid any adverse effects on crude dehydration treatments and water clarification.
1. A solubility test was performed, evaluating the mixing of the two alternatives in different proportions (20:80, 50:50, 80:20) to avoid formation of precipitates or undesired phases. Results (Figure 1) indicated no precipitates or undesired phases formed, suggesting excellent solubility and compatibility between the two chemicals. The mixtures remained homogenous and transparent in all tested ratios, confirming that the alternatives could be mixed in any proportion without compromising their solubility.
2. A compatibility test with base fluids (crude oil and water) was carried out to observe any changes in the fluid's color or other physical properties. The tests showed no significant alterations in the color, viscosity, or other physical properties of crude oil and water (Figure 2). This indicates that the chemical alternatives do not adversely interact with the base fluids, maintaining their original properties, and ensuring their efficacy in direct emulsion treatment and scale inhibition processes.
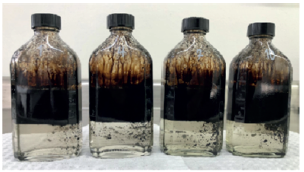
Figure 2 From left to right, White bottle (production fluid without additives), bottle with 500 ppm scale inhibitor + flow improver, bottle with 1000 ppm scale inhibitor + flow improver, bottle with 1500 ppm scale inhibitor + flow improver and bottle with 1500 ppm scale inhibitor + flow improver.
3. Thermal stability tests implied exposing the mixtures to different temperatures representative of downhole conditions (250°F, 300°F, and 350°F), and observing any changes in the stability and composition of the chemical alternatives, as shown in Figure 3. The mixtures exhibited excellent thermal stability across all tested temperatures, with no observable degradation or changes in composition. This suggests that the chemical alternatives can withstand high-temperature conditions that are typical in downhole environments, maintaining stability and performance.
4. Emulsification tests were conducted with the mixture of the two products to assess their ability to form emulsions and their stability. The results demonstrated that the mixtures did not form stable emulsions. This is favorable for direct emulsion treatment in crude oil, as it indicates that the chemical alternatives do not promote emulsion stability, thus aiding in the separation processes and improving overall treatment efficiency.
After conducting a chemical compatibility test, it was determined that the combination of the two chemical alternatives successfully passed all evaluations outlined herein.
The third part of the analysis of the results initially focused on examining the performance of variables and production tests conducted on the selected pilot wells. All wells exhibited stable behavior, with discernible enhancements in oil production ranging from 12% to 79%, as detailed in Table 1.
During the application of the mixture of the two chemical products, an average dosage of 600 ppm for the flow improver and 25 ppm for the scale inhibitor was maintained. In terms of efficiency, an average increase of 17 barrels of crude oil per gallon of chemical product applied was achieved. Residual measurements of the scale inhibitor were conducted, ensuring 5 ppm at the wellhead.
Due to the increased production from these wells, the additional earnings amounted to approximately 25.436 USD per day, substantiating the efficacy of the chemical treatment interventions in facilitating improved flow dynamics for heavy crude oil.
In the context of energy efficiency assessment, the ESP equipment's kilowatt-hour consumption was meticulously evaluated before and after applying the chemical product.
The UPME (Mining-Energy Planning Unit of Colombia) provides specific guidelines for calculating the emission factor in the oil and gas sector. However, in general terms, the emission factor Is calculated by relating the amount of greenhouse gas (GHG) emissions to the system's energy consumption. Nevertheless, the UPME also considers the origin of the consumed energy in this equation, thus assigning specific emission factors depending on whether the energy was sourced from the national electricity grid or a power generation plant. For this project, the emission factors used were provided by the Energy Savings Department at Ecopetrol for BES systems, Efficient Energy (E2, 2022).
The assessment focused on data from wells 1 and 2, as other wells faced unrelated operational challenges and were, therefore, not representative of typical cases for this evaluation According to the data in Table 2, wells 1 and 2 show a significant decrease in kilowatt-hours (KWh) per month, with a reduction of 28-29% per well, as well as a corresponding decrease in emissions within the same range of 28-29% per well. These findings clearly demonstrate the effectiveness of the chemical treatment strategy in reducing the motor's workload and lowering energy consumption
Table 2 Energy consumption and emissions before and after the test.
In terms of cost optimization, incorporating a single capillary into the design of electro-submersible pumping equipment results in substantial savings. Current market prices are approximately 5,85 USD per foot of capillary, and the wells in the Apiay field extend to a depth of around 9.500 feet. Hence, by avoiding the installation of a second capillary, the cost savings amount to approximately 55.575 USD per well.
CONCLUSIONS
After conducting the pilot test, it was definitively established that the concurrent use of the scale inhibitor and flow improver within the same capillary does not lead to any incompatibility or compromise in the effectiveness of either product.
The observed results show a significant increase in crude oil production ranging from 12% to 79%, attributed to the improved mobility of heavy crude oil facilitated by the chemical intervention There is a noticeable decrease of 28-29% in the energy consumption required for the electro-submersible equipment, along with a corresponding reduction in emissions.
From an economic perspective, utilizing a single capillary configuration results in substantial savings of 55.575 USD per well, eliminating the need for a second capillary. Additionally, due to the ncreased oil production from these wells, daily earnings amount to approximately 25.436 USD.