Introduction
There are different methods to control the quality of injected plastic parts based on measurements of residual stresses in the part. These methods can be classified into destructive and non-destructive testing. The former include the hole-drilling technique 1, the layer removal method, and chemical attack 2. Among the non-destructive testing techniques, photoelasticity stands out. It is implemented using clear materials (such as polycarbonate) and their the refraction indices, which depend on the polarization and propagation of the light that hits the material 3. This property is then utilized to observe (residual) mechanical stresses and anisotropy in the material 4. In addition, thermal treatments can be applied to injected parts; for instance, annealing can be used to release residual stresses in a controlled manner 5-8. However, to evaluate the mechanical performance of injected parts, laboratory testing is indispensable. In this regard, several studies have investigated the effect of injection molding conditions on the quality of the injected products, which can be defined based on mechanical properties such as tensile strength, bending, hardness, and impact strength, among others 9-14. Nevertheless, no paper so far has fully studied the use of techniques to measure or estimate residual stresses in injected parts and their relationship with the final mechanical properties of said parts. It has been proven that, in injected parts, residual stresses (measured by photoelasticity) have a direct effect on the generation of deformations 8. Photoelasticity has also been used with auto parts to measure residual stresses and reveal how they can promote the presence of cracks in this kind of parts 15. Furthermore, the combination of photoelasticity and thermal treatment has shown that a longer thermal treatment can relieve residual stresses in the material 16. Still, new studies should evaluate the direct relationship between residual stresses and the mechanical performance of injected parts. This study evaluates the mechanical performance of injected plastic parts as a function of their processing conditions, post-injection thermal treatments, and photoelasticity tests. The latter were conducted to observe areas where higher residual stresses were produced, which reveals the effect that these variables can have on the injected plastic parts.
Methodology
1. Injecting the plastic parts
Injection molding was carried out using a test specimen mold (see Figure 1). The parts were injected employing 24 different Conditions (see Table 1) that were defined based on four processing variables (remaining cooling time, packing time, packing pressure, and mold temperature). The injected material was GE LEXAN™ 144R polycarbonate. According to the manufacturer’s recommendations and the literature (17), the processing variables mentioned above were defined as follows. Two mold temperatures were used: a low one of 50°C to establish if this value could produce significant changes in residual stresses and 80°C, which is the recommended temperature for polycarbonate. The average cooling times for the experiments were determined based on the analytical equation for cooling in a rectangular section 18,19. Packing pressure and time were defined previously to obtain parts that were free from sink marks and had a good superficial appearance. Two conditions were fixed: an injection temperature of 300°C and an injection time of 1 second. A Welltec 90F2V injection molding machine was used to manufacture the specimens for subsequent annealing (thermal treatment), photoelasticity, and flexural tests.
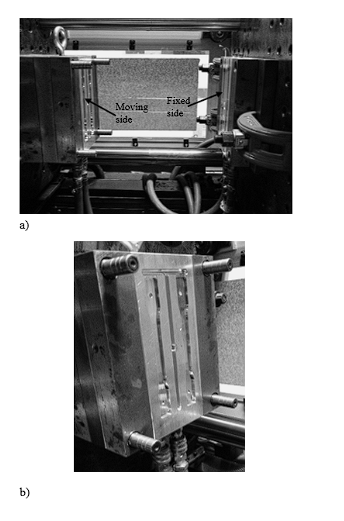
Figure 1 Mold used for injecting the specimens to be analyzed. (a) Open mold and (b) detail of the cavity in the moving side of the mold.
Table 1 Experimental design to evaluate injection molding conditions.
Remaining cooling time [s]* | Packing time [s] | Packing pressure [bar] | Mold temperature [°C] | |
---|---|---|---|---|
10 | 1.5 | 40 | 50 | Cond-1 |
15 | 1.5 | 40 | 50 | Cond-2 |
10 | 4 | 40 | 50 | Cond-3 |
15 | 4 | 40 | 50 | Cond-4 |
10 | 7.7 | 40 | 50 | Cond-5 |
15 | 7.7 | 40 | 50 | Cond-6 |
10 | 1.5 | 60 | 50 | Cond-7 |
15 | 1.5 | 60 | 50 | Cond-8 |
10 | 4 | 60 | 50 | Cond-9 |
15 | 4 | 60 | 50 | Cond-10 |
10 | 7.7 | 60 | 50 | Cond-11 |
15 | 7.7 | 60 | 50 | Cond-12 |
10 | 1.5 | 40 | 80 | Cond-13 |
15 | 1.5 | 40 | 80 | Cond-14 |
10 | 4 | 40 | 80 | Cond-15 |
15 | 4 | 40 | 80 | Cond-16 |
10 | 7.7 | 40 | 80 | Cond-17 |
15 | 7.7 | 40 | 80 | Cond-18 |
10 | 1.5 | 60 | 80 | Cond-19 |
15 | 1.5 | 60 | 80 | Cond-20 |
10 | 4 | 60 | 80 | Cond-21 |
15 | 4 | 60 | 80 | Cond-22 |
10 | 7.7 | 60 | 80 | Cond-23 |
15 | 7.7 | 60 | 80 | Cond-24 |
*Additional cooling time after the injection and packing times. The cooling time includes the injection, packing, and remaining cooling times.
2. Thermal treatment for injected parts
To observe the effect of a thermal treatment on the plastic parts, annealing was applied to some of the specimens injected under the conditions detailed above. A hot air circulation oven was used for this purpose. In the heating program, the temperature was raised gradually up to 130°C over 5 hours. This temperature was maintained for 45 minutes. Finally, it was gradually reduced to room temperature over 5 hours. These conditions were established based on recommendations provided by the polycarbonate’s manufacturer 20-22. Five replicas of each Condition selected for this thermal treatment were later used in flexural tests.
3. Photoelasticity tests
Before the mechanical tests, a photoelasticity test was conducted with the injected parts to observe the patterns of distribution of residual stresses in them. This technique (i.e., photoelasticity) is based on the phenomena that electromagnetic waves experience when they go through clear materials, in particular, the polarization of light-which occurs as a consequence of stresses present in bodies subjected to external or internal forces. The experimental setup employed two polarizing plates, a source of white light, and a HD-capable camera. Figure 2 shows the experimental setup used in this study to obtain the isochromatic fringes in the injected parts. These fringes represent the internal (residual) stresses that are generated in the parts during the injection process.
4. Flexural tests
To evaluate the plastic parts in a real application in which they are subjected to an actual load, flexural tests were conducted combining stresses and compression forces. A Shimadzu universal testing machine was used to apply a load onto the rectangular area of the plastic part according to ASTM D790 standard for molded thermoplastic parts 23. Five replicas were produced under each Condition to obtain averages and standard deviations of their results.
Results and discussion
5. Flexural tests
Flexural tests were conducted with all the parts described in the experimental design, and the results are summarized in Figure 3. In the latter, the flexural strength was higher when the mold temperature had been 80°C, which is close to the recommended temperature for this material 24. This is explained by the fact that the hotter the mold the lower the cooling rate. This condition enables a better application of the packing stage, translates into heavier products with less material shrinkage, and also facilitates a molecular relaxation of the injected plastic. In contrast, at a mold temperature of 50°C, higher cooling rates are generated. Instead of stress relaxation, these higher rates promote high molecular orientation in the solidified layers of injected plastic and high concentrations of still unsolidified areas in the part. This condition facilitates an increase in residual stresses 17,25, which can affect the external load applied during flexural tests 17,26. Specifically at a mold temperature of 50°C, the injected parts do not present a clear trend in terms of flexural strength, which could be an indication of low repeatability of the injection results under these conditions.
Usually, when the packing pressure is higher and the packing time is longer, the injected product is heavier and has less shrinkage-quality characteristics that improve the mechanical performance of the parts 27-29. Nevertheless, the standard deviations obtained in this study do not reflect this behavior. Still, the 80°C mold temperature did produce a trend: a better flexural strength was achieved with higher packing pressures and longer packing times (except for the Condition at 600 bar and 7.7 s). With a mold temperature of 50°C, the flexural behavior of the parts was highly variable without any kind of trend, which can be a reason for not recommending this temperature for polycarbonate processing.
Finally, in this case, increasing the cooling time seemed to have no significant influence on the mechanical strength of the injected products, although it enables a cooling condition with greater molecular relaxation in the injected material.
6. Flexural tests of specimens previously subjected to annealing
Figure 4 compares the flexural strength values of thermally untreated and treated parts, where the latter achieved better results (as further detailed in Table 2). The untreated parts presented similar flexural strength values at mold temperatures of 50°C (Conditions 3-6) and 80°C (Conditions 16 and 20). This situation could be explained by the interaction of variables with different packing pressures and cooling times. These combinations could produce a similar effect on the molecular orientation inside the part and the amount of injected material, which are represented in material weight and density-important variables for the mechanical performance of the injected products.
The parts injected at 50°C exhibited a greater increase in flexural strength (in percentage) after the thermal treatment, showing that this mold temperature enables a greater relief of internal or residual stresses later during annealing, thus improving the mechanical performance of the injected parts (see Table 2). In the case of the parts injected at 80°C, the thermal treatment did not produce a significant increase in mechanical strength, which can be explained because this mold temperature enables more molecular relaxation during the injection process as a consequence of a lower cooling rate.
Similar to the results of the untreated specimens, the flexural strength values of treated parts did not present significant changes as the Conditions (packing pressures and cooling times) were modified. However, in general, the specimens that were subjected to the thermal treatment exhibited a noticeable increase in flexural strength. This is evidence that the molecular relaxation of the parts produced by the thermal treatment reduces residual stresses in the parts, enabling a better mechanical performance in each case. Similar results have been obtained in other studies that have found a better mechanical performance of injected plastic parts when they have been subjected to annealing 24,30.
7. Photoelasticity tests
Figure 5 shows a summary of the pictures taken with the photoelasticity experimental setup detailed above. They represent each one of the Conditions compared in Figure 4 and Table 2. A change in the distribution pattern of residual stresses can be observed in the specimens that were subjected to the thermal treatment. Comparing untreated and treated injected parts, a change in isochromatic fringes can be observed in the latter. In particular, untreated specimens show darker shades and grays compared to their treated counterparts, which exhibit lighter tones that seem to represent areas with fewer residual stresses. Sometimes, this reduction in stresses improves the flexural strength of the parts, as it occurred with Conditions 6, 8, 10, and 12. After the thermal treatment, the specimens obtained under Conditions 16 and 20 (which included a mold temperature of 80°C) showed lighter tones. As explained above, since the moment they were injected, these parts presented fewer residual stresses than their 50°C counterparts. This could explain why the mechanical strength of these parts was not improved significantly when the thermal treatment was applied. Although this test is only qualitative, it established that there was an important change in the distribution of residual stresses, which could be reflected in a higher flexural strength of injected parts subjected to annealing compared to those injected under the same conditions but without a subsequent thermal treatment (Figure 4 and Table 2). Vargas et al. 31 conducted a quantitative analysis of this kind of injected parts using the photoelasticity technique. They determined that injected plastic flow was the most influential variable in the generation of residual stresses when there was a homogeneous distribution of temperatures in the mold.
Conclusions
The mechanical behavior of the specimens showed that those injected at a mold temperature of 80°C presented less variations in flexural strength-which could be an indication that 50°C results in a more variable injection process and greater residual stresses. For this reason, the recommended mold temperature for polycarbonate is 80°C and above. This temperature produces a slightly higher flexural strength when pressure and packing times are increased. However, the corresponding standard deviations are not evidence of a predominant effect of these processing conditions. Likewise, longer cooling times seem to have no effect on the mechanical performance of the injected parts. This opens up the possibility of evaluating higher packing pressures and longer cooling times to produce different levels of molecular contraction and relaxation, which could result in greater variations in residual stresses and the final mechanical performance of injected parts.
Annealing-the thermal treatment applied here-improved the mechanical performance of the injected specimens because it relieved residual stresses generated during the injection process. This was confirmed in the flexural tests, where the parts injected at a mold temperature of 50°C presented a greater increase in flexural strength (in percentage), which could be associated with the generation of more residual stresses under this condition that were later relieved during the thermal treatment. Said increase was also observed in the isochromatic images. Although post-injection annealing can take a long time, it can be justified for certain kinds of plastic parts. This study established that photoelasticity is a viable and easy-to-implement technique to evaluate residual stresses in a quality control system. Its qualitative results can be extended to the numerical determination of these stresses. Future studies can explore other (although destructive) quality control techniques. For instance, chemical attack can be used to reveal the behavior of residual stresses in the form of early cracks or defects in plastic pieces and how they are relieved using thermal treatments.