1. INTRODUCCIÓN
Con la continua producción y demanda de automóviles y motocicletas alrededor del mundo y especialmente en los países latinoamericanos, la disposición final de las llantas usadas se ha convertido en un problema ambiental y de salud pública de primer interés [1]. Métodos convencionales, tales como quema y enterrado bajo tierra liberan una gran cantidad de dióxido de carbono y otras sustancias tóxicas que causan cambio climático y graves problemas de contaminación [2]. Por otro lado, las llantas convertidas en basura sin control constituyen focos de infección al promover el anidamiento de fauna nociva, particularmente mosquitos, ratas, arañas y demás especies que buscan lugares oscuros y protegidos para reproducirse. Es bien conocido el hecho de que se tienen dos especies de mosquitos que predominan en los lugares destinados para el acopio de llantas, (Aedes aegypti y Aedes albopictus) que son los principales vectores de la fiebre amarilla y el dengue [3].
Acorde a la compañía MEAM (mediciones del medio ambiente consultoría, Belo Horizonte, MG, Brasil), especialistas en monitoreo ambiental, alrededor de 32 millones de llantas son producidas en Brasil y se estima que de 10 a 15 millones de unidades son desechadas cada año [2]. Países como Colombia y México producen entre 5.3 y 40 millones de llantas que cumplen su vida útil por año, las cuales terminan en andenes, separadores, parques, humedales e incluso junto a las casas [4], [5]. Frente a esta problemática, la atención se ha desplazado a la reutilización de los residuos de llantas con menos contaminación secundaria [6].
En la literatura se pueden encontrar algunos métodos para uso de los residuos de llantas en desuso, a las cuales se les ha extraído el caucho que posteriormente ha sido molido o pulverizado; acerca del uso de las partículas de caucho de neumático, en los estudios realizados podemos encontrar el uso de las partículas de caucho de neumático como un agregado en el concreto, en la fabricación de alfombras, como aislantes de vehículos y campos de juegos [2], [7]. Por otro lado, se pueden encontrar trabajos relacionados con el dopaje de la red polimérica, ya sea con algún tipo de ferrita o mediante la fabricación de compuestos de cauchos magnéticos a través de microondas asistida en la modificación de superficie in situ y procesos de semi-desvulcanización [6].
Polímeros termoestables como la resina epoxi son materiales económicos que curan a temperatura ambiente. Además, son materiales dieléctricos que presentan buena resistencia mecánica, química y a la humedad. Propiedades que varían dependiendo del tipo de resina base, agente de curado, como de los distintos modificadores que pueden añadirse y de las condiciones de polimerización [8]. El uso de este tipo de polímeros ha sido diverso, por ejemplo, la utilización de resina polimérica en la formación de nanopartículas magnéticas de una matriz de sílice, el dopaje de resina epoxi con ferritas de bario y estroncio para la obtención de resinas magnéticas y, por último, se pueden mencionar mecanismos de blindaje electromagnético a través del dopaje de matrices de resina epoxi con uno de los principales elementos de refuerzos en la fabricación de neumáticos como es el negro carbón (CB) [9], [10], [11], [1].
Los métodos más comunes para la fabricación de los compuestos de matriz de plástico y ferritas varían de acuerdo con la naturaleza de los materiales a mezclarse. Los materiales compuestos de matriz de resina epoxi presentan procesos de fabricación más sencillos, donde el material particulado se dispersa en moldes junto con el material termoestable. Por otro lado, la ferrita constituye uno de los mejores materiales magnéticos para ser empleados junto con matrices poliméricas [11].
Por lo anterior, el objetivo de este trabajo es reportar el proceso de producción de un material compuesto con matriz de resina pre-acelerada, reforzada con magnetita y ripio de llanta, con el fin de buscar un método económico y práctico para la reutilización de las llantas en desuso. La caracterización del compuesto obtenido se llevó a cabo mediante DRX, MEB y estudio de la respuesta magnética.
Con el material fabricado se puede realizar objetos de forma compleja con un excelente comportamiento ante la corrosión ambiental, que pueden ser utilizado en aplicaciones, donde las piezas tienen que moverse o mantenerse en posiciones mediante imanes externos, o en aplicaciones donde el compuesto debe ser fácilmente detectable [12].
2. PARTE EXPERIMENTAL
2.1 Preparación de las muestras
Para la elaboración del compuesto se emplea resina epoxi como matriz polimérica, la cual previamente fue mezclada con 2 % de catalizador en peso de resina, con el fin de iniciar una reacción química que conlleva a un proceso de curado. El porcentaje de catalizador usado en la matriz polimérica se determinó por medio de experimentos previos, los cuales evidenciaron que este porcentaje en peso era el adecuado para la fabricación de los compuestos. Posteriormente, dicha mezcla entre catalizador y resina es reforzada con dos materiales: caucho pulverizado procedente de llantas en desuso y, como relleno magnético, magnetita pulverizada (Fe 3 O 4 ). Como regla general, conviene mantener lo más bajo posible el contenido de carga en la matriz polimérica [10], por lo cual se utilizó un porcentaje en volumen de carga que se acoplara a esta condición como se observa en la Tabla 1.
El término carga hace referencia a la mezcla entre caucho pulverizado y magnetita en polvo. Las densidades utilizadas para determinar el porcentaje de volumen son: caucho pulverizado , resina epoxi,
, magnetita
valores que fueron suministrados por Gestión y Reciclaje Integral de Neumáticos (GRIN) y ficha técnica de resina epoxi. El proceso de curado y pos-curado de las muestras se realizó a temperatura ambiente durante 3 semanas.
2.2 Caracterización
La estructura y las fases presentes tanto en los precursores como en el compuesto fueron identificadas por medio de DRX, utilizando un equipo Panalytical X-Pert PRO MPD, del Departamento de Física de la Universidad Nacional de Colombia, sede Bogotá, el cual usa una radiación Cu-Kα de (=1.54 Ǻ. Durante el experimento se definió un intervalo de medición de 10-800 en la escala de 2θ, con un paso de 0.02o y un tiempo de 2 s.
El análisis de tamaño y morfología de los precursores y de las muestras se efectuó mediante MEB, utilizando un Microscopio de Barrido Vega 3 TESCAN, del Departamento de Física de la Universidad Nacional de Colombia.
Las propiedades magnéticas fueron estudiadas en curvas de magnetización. La estructura y las fases presentes tanto en los precursores como en el compuesto fueron identificadas por medio de DRX, utilizando un equipo Panalytical X-Pert PRO MPD, del Departamento de Física, de la Universidad Nacional de Colombia, sede Bogotá, el cual usa una radiación Cu-Kα de (=1.54 Ǻ. Durante el experimento se definió un intervalo de medición de 10-800 en la escala de 2θ, con un paso de 0.02o y un tiempo de 2 s. El análisis de tamaño y morfología de los precursores y de las muestras se efectuó mediante MEB, utilizando un Microscopio de Barrido Vega 3 TESCAN, del Departamento de Física de la Universidad Nacional de Colombia. Las propiedades magnéticas fueron estudiadas en curvas de magnetización en función del campo aplicado, a través de un equipo VersaLab, Cryogen-free PPMS (Physical Property Measurement System) de Quantum Design, el cual permite la aplicación de campos magnéticos hasta 30000 Oe. en función del campo aplicado, a través de un equipo VersaLab, Cryogen-free PPMS (Physical Property Measurement System) de Quantum Design, el cual permite la aplicación de campos magnéticos hasta 30000 Oe.
3. RESULTADOS Y DISCUSIÓN
3.1 Estructura
La evaluación del patrón de difracción obtenido en las mediciones de DRX se realizó por medio del programa High Score Plus, usando la base de datos COD_2013, que permite determinar las fases presentes en cada una de las muestras con diferentes proporciones de magnetita en polvo, y de igual forma a los precursores que constituyen los especímenes.
Se estableció que la magnetita en polvo está constituida por dos fases diferentes identificadas como magnetita y hematita, con un porcentaje en peso de 90,2 % y 9,8 % respectivamente. La magnetita posee una estructura cristalina cúbica centrada en las caras, mientras que la hematita pertenece al sistema cristalino hexagonal [13]. Así mismo, se identificó que la resina epoxi está compuesta en un 100 % de styrene, perteneciente al sistema cristalino ortorrómbico.
El refinamiento Rietveld de los datos experimentales de DRX permitió establecer que el ripio de llanta en polvo está compuesto de dos fases que pertenecen a un sistema cristalino tetragonal. En primer lugar, la fase con fórmula química Si64.00O128.00N4.16C45.44H66.24 fue identificada con el nombre de compuesto 4107507, y asociada al código de referencia 96-410-7508, con un porcentaje en peso de fase del 65.9 %. En segundo lugar, se obtuvo cristobalite, en un porcentaje en fase de 34.1 %, con fórmula química Si4.00O8.00 asociada al código de referencia 96-900-8230, con grupo espacial P 41 21 2. Cabe señalar que el precursor ripio de llanta en polvo posee otras fases que no son descritas en este trabajo, como las mencionadas en [1], las cuales no fueron posibles identificar mediante esta técnica. Además, las fases no identificadas son muy pequeñas en proporción, por lo cual la contribución magnética de estas fases minoritarias dependerá exclusivamente del porcentaje de elementos magnéticos que posea cada fase. Pero como se observa en [1], las proporciones de estos elementos son muy bajas para afectar las medidas magnéticas.
Los compuestos presentaron cinco fases: cristobalita, styren, hematita, magnetita y por último la fase con fórmula química Si64.00O128.00N4.16C45.44H66.24. El método utilizado para determinar la estequiometria química de los compuestos como de los precursores fue a través de la comparación de las pdfs ubicadas en la base de datos COD_2013 por medio del software X´Pert Highscore plus elaborado por Panalytical B. V. Los porcentajes de las fases presentes en los especímenes fue determinado por medio de refinamiento Rietveld (ver Tabla 2).
Tabla 2 Fases pertenecientes a los compuestos en función del porcentaje de (Fe 3 O 4 ) en la matriz polimérica.

Fuente: [1]
3.2 Comparación de los patrones de difracción
En la Fig. 1 se presenta el análisis de los difractogramas experimentales, tanto de los precursores como de las muestras, el cual fue efectuado con el fin de observar el comportamiento de dichos precursores después de ser conformados en un compuesto.
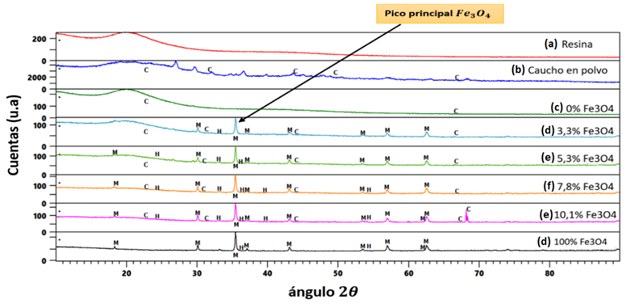
Fuente: [1]
Fig. 1 Patrones de difracción de los precursores: a)100 % de resina b) 100 % de caucho en polvo y h) 100 % magnetita en polvo. Patrones de difracción para todas las muestras con diferentes porcentajes en volumen de magnetita en polvo; c) Comp 1 con un 0 % de magnetita, d) Comp 2 con un 3.3 % de ferrita, e) Comp 3 con un 5.3 % de ferrita, f) Comp 4 con un 7.8 % de ferrita, g) Comp 5 con un10.1 % de ferrita h) 100 % Fe3 O4.
Los patrones de difracción de cada una de las muestras se pueden ver en la Fig.1. De las Figuras 1a y 1b se ve que la resina y el caucho pulverizado presentan perfiles similares.
En muchos casos, no tenemos una estructura de cristal disponible, el estado de la materia puede inferirse de la apariencia del patrón. En la Fig. 2c, los patrones de polímero consisten en múltiples picos agudos consistentes con la «difracción» de una red cristalina. En la Fig. 2a, los patrones tienen características muy amplias consistentes con la «dispersión incoherente» de un sólido amorfo. Los patrones de la Fig. 2b son más complejos, exhibiendo una mezcla por lo cual el material se comporta como un material semi-cristalino [14]. Con base a lo anterior, se puede decir que al mezclar la resina epoxi con el ripio de llanta en polvo, la difusión es muy completa, es decir, todo lo que era cristalino en el ripio de llanta se difundió y se transformó en amorfo (ver Fig. 1a y 1b).
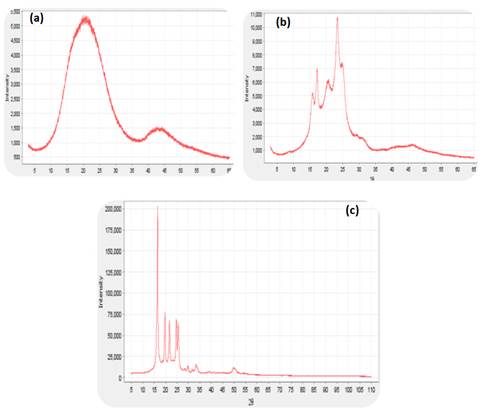
Fuente:[15]
Fig. 2 patrones representativos de DRX: a) patrón de difracción de un polímero amorfo b) patrón para un polímero semi-cristalino c) patrón de difracción para un polímero cristalino.
Por otro lado, los difractogramas de las muestras cuyo contenido de ferrita varía de un 3.3 % a un 10.1 % en volumen de magnetita, revelan que al combinar resina epoxi, magnetita en polvo y ripio de llanta se conforma un compósito semicristalino, donde hay una matriz amorfa y unas partículas cristalizadas, identificadas como magnetita y hematita. De la misma manera, se observa una progresiva disminución de la zona amorfa que hace parte del relieve comprendido en la región 2𝜃 de 15.770 y 23.090. A partir del 5.33 % de relleno de magnetita en la región amorfa se evidencia un incremento paulatino de picos bien formados pertenecientes a la fase cristalina (magnetita y hematita) ubicados en la región 2𝜃 de: 30.090, 35.440, 53.420, 56.940 y 62.520.
Se puede inferir, entonces, que hay una transición amorfo-cristalino entre las muestras al ir aumentando el contenido en volumen de magnetita. Esto ocurre debido al agregado de la fase cristalina Fe3 O4 que emigra en la fase amorfa del material, reduciendo así los dominios amorfos de la muestra Comp1 (ripio de llanta en polvo-resina epoxi). El difractograma también indica que la estructura de Fe3 O4 se mantiene [15].
A partir de los difractogramas queda en evidencia que la resina, ripio de llanta en polvo y la magnetita nunca reaccionan entre sí conformando una nueva fase y por ende no se observan nuevos picos de difracción [13].
3.3 Caracterización morfológica
Con el fin de evaluar la morfología del compuesto, se tomaron imágenes de MEB tanto a las muestras con diferentes porcentajes en volumen de magnetita como a los precursores. En la Fig. 3 se observan micrografías de la magnetita en polvo, la cual fue usada como material de refuerzo en la matriz polimérica. De las imágenes se distinguen diferentes rangos de tamaño de partícula de irregular forma y con una baja relación de aspecto, los resultados anteriores son similares a los reportados en [14].
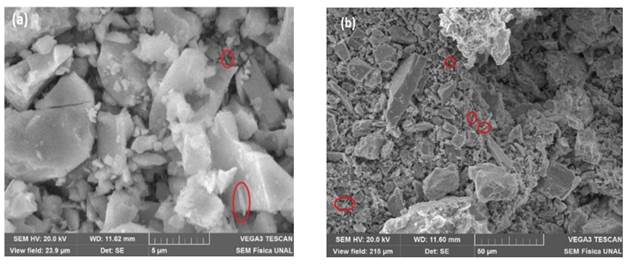
Fuente: [1]
Fig. 3 Imágenes MEB del precursor magnetita (Fe3O4) tomadas con diferentes escalas de longitud a) 𝟓 𝝁𝒎 b) 𝟓𝟎 𝝁𝒎, en círculos de color rojo los cristales laminares de hematita.
A partir del análisis se estableció que los granos presentes en la figura 3 procedentes de la magnetita en polvo poseen tamaños entre y
𝜇𝑚. Por otro lado, las imágenes muestran las diferencias entre la hematita y la magnetita, ambas fases presentes en el precursor en polvo. La hematita se caracteriza por su morfología laminar tipo aguja y su color rojo brillante, aunque la morfología de los granos se puede ver influenciada por el método de obtención del material, mientras que la magnetita presenta una morfología más volumétrica que se aproxima a un tipo de grano esférico de forma irregular de color negro [13].
En las imágenes MEB de la Fig. 3, pertenecientes al precursor magnetita en polvo, se puede observar algunos granos en forma de aguja encerrados en un círculo rojo, esta forma característica de grano hace referencia a presencia de hematita en el precursor magnetita en polvo, lo cual concuerda con los resultados encontrados por difracción de rayos x para este precursor.
La Fig. 4 ejemplifica la morfología superficial del ripio de llanta en polvo. En las imágenes se observa que la morfología del caucho pulverizado es irregular con rugosidad superficial y con zarcillos o riso que se proyectan desde la superficie formando cavidades en la superficie del material [16]. Por el método de los interceptos se determinó que el tamaño promedio del grano se encuentra entre 1.4 μm.
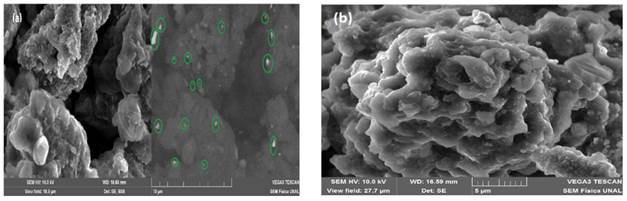
Fuente: [1]
Fig. 4 Imágenes MEB del precursor ripio de llanta en polvo tomadas a dos escalas diferentes de longitud a) 5μm y b) 10μm. En recuadro derecho de la imagen a), se observa cristales de hierro encerrados en círculos de color verde.
Cabe recalcar que se presentan partículas brillantes dentro del material, como se observa en la parte derecha de la imagen de la Figura 3a, las cuales, de acuerdo con la caracterización por fluorescencia, se sugiere que están constituidas por hierro. Dichas partículas son consideradas impurezas, debido a que en la literatura no se encuentra reportado que el caucho pulverizado procedente de llantas en desuso posea estas partículas, por lo cual un posible origen de estas partículas se encuentra en el proceso de obtención del caucho en polvo, debido a que el método es mecánico. De manera que en el desarrollo de molienda pudo haber contacto con el enmallado que poseen las llantas y de esta manera quedaron elementos de hierro en el caucho obtenido en forma de polvo.
La Fig. 5 presenta las imágenes MEB pertenecientes a las muestras. En las mismas no se puede distinguir claramente la fase perteneciente al ripio de llanta y la resina epoxi, ya que estas se interceptan entre sí. Además, se observa que las muestras presentan una microestructura no homogénea de forma irregular. Por otro lado, se evidencia que las incrustaciones de partículas de magnetita tienen una gran superficie, lo cual aumenta el contacto con la matriz caucho epoxi (ver Fig. 5c). Esto a su vez puede aumentar la resistencia del caucho epoxi debido al enclavamiento mecánico que surge del aumento del contacto entre las partículas del refuerzo y la matriz epoxi-caucho, por lo cual la interface entre la matriz y el refuerzo están bien creadas [17].
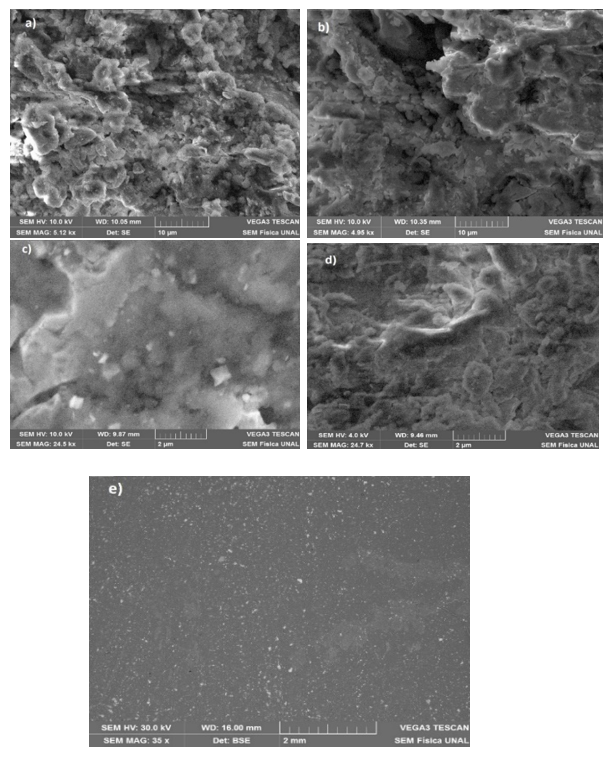
Fuente: [1]
Fig. 5 Imagen MEB de las muestras estudiadas con diferentes % vol de Fe3O4 (Comp 1-Comp 5), tomadas a una escala de longitud de 2𝜇𝑚: A) 3.3 % a 5.1 kx, B) 5.3 % a 49 kx, C) 7.8 % a 24 kx, D) 10.1 % a 24 kx E) 3.3 a 35x.
Se estimó que el tamaño del grano para las muestras se encuentra entre y
𝜇𝑚, lo cual indica que los tamaños del grano de las muestras no son uniformes. Además, algunas de las partículas se vieron más grandes que su tamaño real, que es una consecuencia de la aglomeración en ciertas áreas [17].
Al igual que en [18], se observa que los granos de magnetita en polvo penetraron profundamente en la matriz polimérica sin dejar vacío (ver Fig. 5c y 5d). La ausencia de huecos implica que no se produjo oxidación dentro del ripio de llanta en polvo durante la formación de las muestras. Se debe agregar que las distribuciones de los granos de magnetita en polvo son uniformes en los compuestos (ver Fig. 5e), lo cual asegura que el flujo magnético fluya uniformemente a través del compuesto [18].
3.4 Caracterización magnética
A las muestras Comp 1, Comp2, Comp 3, Comp 4 y Comp 5 se les realizó curvas de histéresis magnética a 50 K,120K y 300K, bajo la aplicación de un campo magnético externo comprendido entre -30000 Oe y 30000 Oe.
Los ciclos de histéresis en función del porcentaje de volumen de magnetita para diferentes temperaturas para las muestras obtenidas se presentan en las Fig. 5. Los parámetros magnéticos característicos Magnetización de saturación (Ms), Magnetización de remanente (Mr) y Campo coercitivo (Hc) de los compuestos se muestran en la Tabla 3.
Tabla 3 Parámetros magnéticos de las muestras a diferentes temperaturas: Magnetización de saturación (Ms), Magnetización de remanente (Mr), Campo coercitivo (Hc).
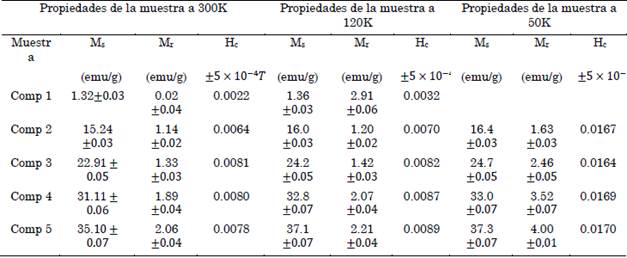
Fuente: [1]
Las curvas de histéresis para las temperaturas 50,120 y 300k que presentan las muestras Comp 1 hasta Comp 4 son curvas características de un material ferrimagnético (ver Fig. 6). En el caso de la muestra designada como Comp 1 (0 % vol. magnetita) para temperaturas comprendidas entre 120 y 300K, el espécimen se comporta como un material ferromagnético, debido a los elementos presentes en el precursor ripio de llanta como lo son el Zinc y el hierro, elementos determinados por fluorescencia (ver Fig. 6).
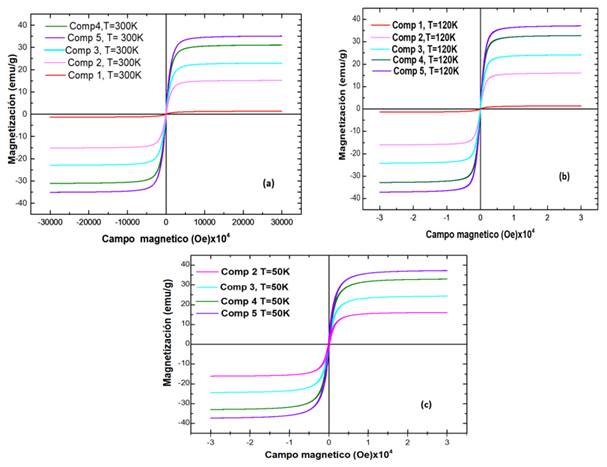
Fuente: [1]
Fig. 6 Curvas de histéresis tomadas a diferentes temperaturas en función de un campo magnético para cada una de las muestras: a) 300 K, b) 120 K, c) 50 K.
Cabe señalar que la muestra Comp1 presenta valores de magnetización remanente y magnetización de saturación pequeños, tanto para 120K como para 300K, debido a las propiedades magnéticas de las impurezas presentes en el material, las cuales han sido nombradas con anterioridad en este documento.
A partir de la Tabla 3 se puede inferir que con el incremento en %vol de Fe 3 O 4 tanto los valores de magnetización remanente como la magnetización de saturación se hacen mayores. Estos resultados coinciden con los obtenidos en [13], y se puede explicar a través de la interacción probable entre las propiedades magnéticas de las partículas de magnetita dentro de la matriz polimérica caucho-epoxi, como de las impurezas presentes en el ripio de llanta pulverizado. Además, se determina que la magnetización de saturación del compuesto es linealmente dependiente de la fracción de masa de relleno según la relación: MS = MF x WF, donde MF y WF son la magnetización de carga y la fracción de peso de carga en el compuesto [19].
Es importante decir que el área bajo la curva del ciclo de histéresis para materiales ferromagnéticos corresponde a la energía disipada o perdidas por histéresis; en el caso de los materiales magnéticos blandos esta energía de perdida es baja, por tanto, se produce menos calor para disipar [21].
Un material magnético blando es aquel que es fácil de imanar y desimanar, a diferencia de un material magnético duro. Para que un material ferromagnético sea blando, su ciclo de histéresis debe tener una fuerza coercitiva tan pequeña como sea posible, lo cual permite que el material se imane fácilmente y tenga una alta permeabilidad magnética [22].
Los valores de coercitividad para los compuestos a temperatura ambiente disminuyen con el incremento de ferrita en el compuesto. Estos valores son similares a los reportados en [18]. Por consiguiente, el aumento en Hc en las muestras con menor contenido de relleno indica que la matriz polimérica es resistente a la alineación del momento magnético de la carga. Por lo tanto, los compuestos con menor contenido de relleno apenas se desmagnetizan en comparación con aquellos compuestos con mayor carga de relleno [15]; caso contrario ocurre a temperaturas bajas donde la coercitividad aumenta con el incremento de Fe 3 O 4 en la matriz plástica.
Se debe agregar que la fuerza coercitiva en las muestras disminuye con el incremento de la temperatura en razón del tamaño de grano que disminuye, ya que la coercitividad se incrementa cuando el tamaño de grano crece, debido que los defectos introducidos por la frontera de grano disminuyen por unidad de volumen [20].
Además, se debe anotar que las curvas de histéresis para las muestras a diferentes temperaturas manifiestan que los compuestos son materiales magnéticos blandos, debido a que poseen ciclos de histéresis estrechos con pequeñas fuerzas coercitivas (ver Fig. 6).
La gama de aplicaciones de los materiales magnéticos crece con la mejora de sus propiedades magnéticas, mecánicas, eléctricas y térmicas. En comparación con los materiales magnéticos blandos clásicos, los materiales magnéticos blandos modernos tienen una tecnología óptima de fabricación al obtener las propiedades asumidas que permiten miniaturizar, simplificar y reducir los costos de los dispositivos. Por eso, es de gran importancia optimizar el proceso tecnológico de obtención de materiales [23]. De ahí que métodos como el presentado en este trabajo se hacen significativos, las aplicaciones sugeridas para los compuestos magnéticos obtenidos en esta investigación son multiplicadores de flujo, los transductores de otras propiedades (núcleos de sensores) [24], y entre otros como los mencionados en la referencia [23].
Al realizar gráficas entre temperatura y magnetización remanente y de magnetización de saturación, se observa de estas gráficas, que la magnetización remanente (M𝑟) y la magnetización de saturación (𝑀𝑠) disminuyen con la elevación de la temperatura, como indican las Fig. 7a y 7b.
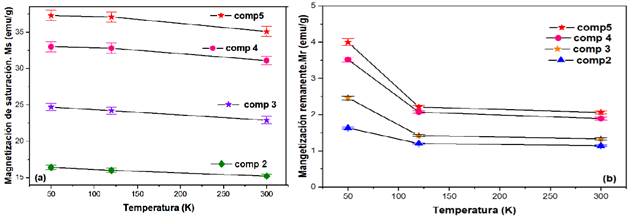
Fuente: [1]
Fig. 7 a) Magnetización de saturación para las muestras a diferentes % vol de Fe 3 O 4 vs temperatura b) Magnetización remanente para las muestras a diferentes % vol de Fe3O4 vs temperatura.
Lo anterior se debe al hecho que al incrementar la temperatura el número de partículas en estado superparamagnético se aumentan y en consecuencia la medida de los valores de 𝑀𝑠 y M𝑟 disminuyen. En muestras que poseen partículas multidominio, los valores de 𝑀𝑠 y M𝑟 tienden también a disminuir, dado que las configuraciones geométricas de los momentos magnéticos tienden a disminuir la energía total del sistema [25]. Cabe resaltar que las propiedades magnéticas evidenciadas en este trabajo son similares a los reportados en [12]-[30], donde se trabaja con materiales idénticos a los utilizados como precursores en este trabajo.
4. CONCLUSIONES
El método utilizado permitió la fabricación del compuesto a base de ripio de llanta en desuso y magnetita en polvo, usando resina epoxi como matriz polimérica. El análisis por DRX permite concluir que el ripio de llanta posee impurezas de hierro debido al método de obtención del material. Con el incremento de la magnetita en polvo en la matriz plástica, la zona amorfa perteneciente al polímero caucho-epoxi disminuye, de esta manera se pasa de un material amorfo a un material semicristalino. Frente a las pruebas magnéticas realizadas a los compuestos, se puede deducir que las curvas de histéresis en función del campo aplicados a diferentes temperaturas exhiben que las muestras Comp 2 a Comp 4 son curvas características de un material ferrimagnético. Todas las muestras a diferentes temperaturas se comportan como materiales magnéticos blandos, debido a que poseen ciclos de histéresis estrechos con pequeñas fuerzas coercitivas. Con el incremento de magnetita en la matriz se presenta un incremento de la saturación. Con el aumento de la temperatura las muestras presentan una disminución en magnetización de saturación. Con el aumento de la temperatura las muestras presentan una disminución en magnetización de saturación. La fuerza coercitiva presenta una respuesta independiente de la carga de ferrita presente en la matriz caucho-epoxi.
El material fabricado se puede realizar objetos de forma compleja con un excelente comportamiento ante la corrosión ambiental, que pueden ser utilizado en aplicaciones, donde las piezas tienen que moverse o mantenerse en posiciones mediante imanes externos, o en aplicaciones donde el compuesto debe ser fácilmente detectable.